
16 minute read
The heavy truth about hydrogen sulfide
Due to its weight compared to oxygen, hydrogen sulfide can accumulate close to the ground or in confined spaces and becomes a threat to humans and animals.
by Robert Meinen
Advertisement
Hydrogen sulfide (H2S) is undoubtedly the most dangerous gas associated with manure storage and handling. The United States Occupational Safety and Health Administration (OSHA) lists acceptable exposure concentration limits for H2S as 20 parts per million (ppm) with a 10-minute exposure maximum peak over an 8-hour shift as 50 ppm. OSHA lists concentrations as low as 700 ppm as the level that can cause immediate collapse and death within minutes, and 1,000 ppm is the level that can cause nearly immediate death.
An unfortunate by-product
Hydrogen sulfide can be produced as a microbial by-product of manure degradation, with production of the deadly gas exacerbated when anaerobic manure storage conditions favor proliferation of sulfate-reducing bacteria. Higher levels of H2S can be produced in manure when sulfur inputs into the manure are elevated from sources such as gypsum bedding, by-product feed ingredients, or sulfur-containing water sources. Temperature also impacts H2S production, since microbial activity increases in warmer manure. Higher H2S concentration will lead to greater emissions.
Emissions can occur one molecule at a time when H2S moves across a gradient from concentrated solutions at the manure surface to low concentrations in the air above the manure. However, since H2S is only slightly soluble in water, the molecule “wants” to come out of solution as concentrations grow.
In deeper anaerobic areas of a manure storage, where microbial production continually supplies H2S, concentrations of gas can elevate beyond their solubility limit and escape the solution by coming together to form bubbles and release from manure through ebullition processes.
Other gases produced from microbial degradation of manure, such as methane and carbon dioxide, also form bubbles. Bubbles can contain a mixture of different gases.
Disturbing manure with processes such as agitation are expected to intensify H2S release. Violent manure movement brings higher concentrations found in the depth of manure to the
Heifer barn NORTH
This dairy’s heifer barn blocked air movement when winds shifted to the southeast during agitation, elevating hydrogen sulfide to a dangerous level between the manure storage and the barn.
surface, and shifting concentration gradients favor release of the poorly soluble molecule.
Worried about the weight
A characteristic that makes H2S dangerous is that it has a molecular weight of 34 grams per mole (g/mol), compared to the weight of dry air at 29 g/mol. The weight of air decreases with moisture, since water weighs just 18 g/mol. This means that certain atmospheric conditions and locations can raise the risk of H2S accumulation close to the ground, in low areas, or in confined spaces.
If air is still, the gas that leaves the manure surface may not be carried away, and since H2S is heavy, continual release can accumulate gas just above the manure surface. Such pooling of H2S can lead to deadly concentrations.
A report from the Centers for Disease Control and Prevention highlights how all these factors led to the 2016 death of a worker and 13 cattle at a Wisconsin farm. The farm’s ration included a distillers syrup that contained sulfur above dietary recommendations, and the manure storage was deep and anaerobic. The incident occurred in mid-August when summer temperatures promoted microbial proliferation. Atmospheric circumstances enhanced the pooling characteristics of H2S because there was no wind. Humidity was high, thermal inversion conditions existed, and the worker had performed manure agitation.
In Pennsylvania, studies were conducted that compared H2S emissions during agitation at dairy farms that either used or did not use gypsum bedding and provided practical recommendations concerning manure handling. Gypsum bedding (CaSO4), derived from recycled drywall material from the construction industry, was shown to elevate H2S emissions during manure storage agitation.
On one dairy that used gypsum bedding, the ability of heavy H2S gas to pool provided a great learning opportunity. At this farm, measurements were made around the perimeter of a circular concrete manure storage (see photo). During agitation, when wind moved from the west, the maximum downwind H2S monitor reading was 64 ppm, a level above OSHA standards but not deadly. When the wind shifted and moved from the southeast, the downwind H2S monitor measured 500 ppm, the maximum reading the monitor could register.
What was the difference between these positions during this agitation event? We believe that as the breeze moved over the heifer barn seen at the top left of the aerial photo, a dead space was created, much like an eddy in a stream, that allowed the heavy gas to settle, pool, and become concentrated.
Areas such as this may not appear dangerous, but people should avoid working next to structures, like this heifer barn, that can provide obstruction to free air movement. When possible, manure handlers should position themselves so that wind travels across their position before crossing the manure storage. This can be phrased as “keeping the wind at your back.”
Avoid these spaces
Low-lying areas and confined spaces where H2S may pool should always be avoided. There are three characteristics OSHA uses to define areas that are confined spaces: 1. Large enough to enter 2. Limited means of entry and exit 3. Not designed for continuous worker occupancy
These traits pertain to nearly every manure storage since none are designed for continuous worker occupancy. This includes any uncovered, open-air, outdoor storage. For this reason, consider any space inside of a manure storage fence as a confined space and never enter such spaces without proper entry equipment, ventilation, and precautions. Always pull equipment outside of the manure storage area for maintenance.
Hydrogen sulfide is a deadly gas. Agricultural professionals, including manure system designers, nutritionists, farmers, manure handlers, agency personnel, and university employees, should work together to ensure worker and livestock safety. ■
The author is a senior extension associate with Penn State University’s Department of Animal Science.
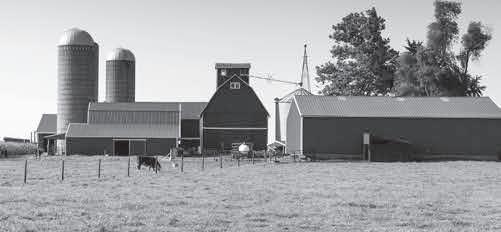
Low disturbance application opens doors
For some farmers, low disturbance manure application, cover crops, and other conservation practices go hand-in-hand.
by Abby Bauer, Managing Editor
aron Augustian said he and his brother, Todd, were looking to try something different with manure application when they were asked to join the Great Lakes Demonstration Farms Network a few years ago. Since then, the pair has switched to low disturbance manure application and introduced the use of cover crops, and for the past two years, they have used both of those practices on 100% of the fields on their farm in Kewaunee, Wis.
“It’s been working great, as long as we don’t have another extremely wet year like we did in 2019 that made things more challenging,” Augustian said during a panel discussion at the Wisconsin Discovery Farms annual conference.
Splitting the application
For manure hauling, he said they used to do a majority of their application in the fall, putting on 14,000 to 16,000 gallons per acre, but Augustian felt that wasn’t good for soil health.
“How do we put on less manure, yet get the correct amount of nutrient?” Augustian and his brother asked themselves. “Low disturbance manure application fit into that equation very well,” he noted.
Now they will typically apply 6,000 to 10,000 gallons to an established cover crop, and then, depending on soil conditions, come back with another application in the spring.
Barry Bubolz, Great Lakes Restoration Initiative area coordinator for the Natural Resources Conservation Service (NRCS), said they don’t have an official standard for low disturbance manure application, but he offered a few criteria during the panel discussion.
For starters, low disturbance application is not full width tillage, and the goal is no more than 30% of row width disturbance. Ideally, he said this application is done into a living crop or cover crop, and it is also preferable if it can be followed up with no-till planting, as that is an indicator that the level of soil disturbance was low.
“Low disturbance manure application has really opened up the door for utilization of some of these conservation practices,” Bubolz said, pointing to winter rye establishment, planting green, and interseeding.
Augustian said it can be hard to convince some custom applicators to apply less manure and return to the

Jesse Dvorachek, Aaron Augustian, Barry Bubolz, and Jacob Brey discussed low disturbance manure application during the Wisconsin Discovery Farms annual conference.
same fields multiple times. However, they have enjoyed success with this method so far.
“Last spring, Mother Nature cooperated with us, and we could plant 100% into green using no tillage tools,” Augustian said. He noted that in a rainy spring, they would use tillage if ruts were created and had to be leveled out.
Augustian shared that along with the successes came some failed attempts. For example, they tried to use one applicator tool that continued to plug up due to the high solids content (12% to 18%) of their manure. They switched to a different machine, and it has been working great ever since.
With low disturbance application, they have been able to incorporate several cover crops. A multi-species mixture is planted following the harvest of fourth crop alfalfa, and rye is planted after corn silage is harvested. He said about 15% of their corn is interseeded into a grass and clover mix, a practice that works well for them since some of their farmland is as close as 50 yards from Lake Michigan.
“I think the cooler weather helps establish these grasses and clovers,” Augustian shared about their location. Interseeding also alleviates some of the challenges of trying to get rye planted the same time corn silage is being harvested. He said they are planning to interseed 40% to 45% of their corn next year.
While low disturbance manure application can get a sideways glance from other farmers, the public has also questioned why the manure is sometimes not incorporated. For Augustian, this has been a teaching opportunity.
“When they see manure on the ground, there are questions,” he said. “We have been more proactive in letting our neighbors know what we are doing it and why we are doing it.”
Capture the most nutrients
Fellow dairy farmer Jacob Brey also noted the importance of education.
“It’s not their fault; they just don’t know,” he said of neighbors that might question their manure application processes. “We really don’t have anything to hide. We just need to tell the public what we are doing.”
He continued, “We need to do our job as farmers to tell the public all the good things we are doing to show them
farming can be a vital part of the economy and community going forward.”
Brey, who farms with his brother, Tony, near Sturgeon Bay, Wis., said it was just five years ago when he attended his first cover crops conference and all this was foreign to him.
Over the past three years, Brey said they have moved to a double cropping system on nearly all of their acres, thanks to the use of low disturbance manure injection and cover crops.
After corn silage comes off in the fall, those fields are immediately seeded down with either winter triticale or winter rye. They will plant triticale first, in September, as they found it needs to be in the ground sooner, and then they move to rye.
“After corn silage harvest, our number one priority is to get the cover crop established first to capture those remaining growing degree days we sometimes get in September,” Brey said.
They use a manure tool bar borrowed from a nearby county’s land and water conservation department and apply 9,000 gallons per acre to the growing cover crop. They let the crop grow and soak up the nutrients, and then harvest it for forage the next spring. Triticale is usually of higher quality, so they feed it to dairy cows as a replacement for alfalfa, while the rye is used as heifer feed.
Once the forage is harvested, typically at the end of May, they go through with another pass of low disturbance manure application. Last spring, right around Memorial Day, they applied 10,000 to 12,000 gallons, Brey said.
Then, after making some modifications to their corn planter, they no-till plant corn. They have found it works
best to let the manure dry a few days but not too long, as the soil can get very hard in a hurry.
Their goal is to have a living crop on all their ground throughout the year and to get manure to the crops when they can best utilize it.
“Especially with the high fertilizer prices, we want to maximize every gallon of manure we have. As a dairy farm, that is a big asset for us,” Brey said.
Especially with the high fertilizer prices, we want to maximize every gallon of manure we have . . . that is a big asset for us.
Each farm is different
While the nutrient value of manure is undeniable, there is no one-size-fits-all approach to application. Jesse Dvorachek, who operates a custom application business based in Brillion, Wis., pumps 250 million gallons of dairy manure annually and has tried many styles of manure applicators.
“What I have learned over the years, when it comes to low disturbance manure application, is that there is no perfect tool,” he said. It really comes down to each individual farmer’s preference and situation.
Bubolz reiterated that thought.
“There is not one tool bar that fits every circumstance. You have to have the tool box loaded, because every year can be different,” he said. To find what might work best, Bubolz encouraged farmers to take opportunities to learn and visit other farms to see different practices in action. ■
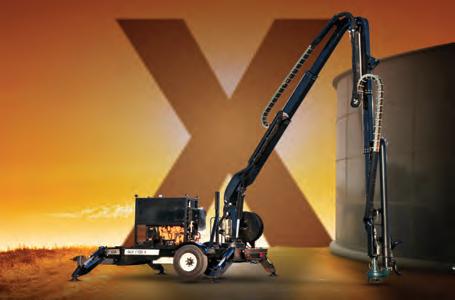
PUCK INTRODUCES THE LONG REACH AGI
There is no denying that effective agitation is the key to regaining lagoon capacity and ensuring an even application of nutrients in the field. Agitation trailers tackle deep pits and hard-to-reach places. The first-ever telescoping agitation trailer takes things to the next level. This low-maintenance, high-efficiency agitation trailer features 50 feet of reach in a compact and user-friendly package. Some of the features of the Long Reach Agi are: • A LightSpeed operating system • Heavy-duty 25-inch slewing drive • High and low agitation nozzles with 180 degrees of rotation • Ability to switch from agitation to transfer mode without shutting down
For more information, call 712-655-9200 or visit puck.com.
DIGESTED ORGANICS CONSTRUCTING LARGE DIGESTATE TREATMENT FACILITY
Digested Organics, based in Plymouth, Mich., has begun construction of the BC Organics Nutrient Concentration and Water Reclamation (NCWR) facility in northeast Wisconsin. This state-ofthe-art treatment plant utilizes unique membrane filtration equipment to process nearly 1 million gallons per day of digested dairy manure and return over 400,000 gallons per day of clean water to the environment. The NCWR facility is part of a large anaerobic digestion project called BC Organics, which is designed, owned, and operated by Dynamic. Raw manure from numerous dairy farms will be pumped and trucked to the facility for digestion in 16 aboveground tanks, capturing methane, which is purified and injected into nearby natural gas pipelines as renewable natural gas (RNG).
By removing nearly half of the digestate volume as clean water, the facility helps reduce the number of trucks moving digestate and minimizes the volume of material participating farms have to lagoon store and then land apply each year. Since the farms receive back more concentrated liquid digestate, they save money on land application, can use the liquid fertilizer in a more targeted fashion when needed (thereby helping to reduce runoff), and haul it to fields further away that traditionally receive less manure-based fertilizer.
Dan Nemke, partner and chief technology officer, said, “We have been working with Digested Organics and the farmer community near Greenleaf, Wis., for about three years to bring this project to fruition. We are excited that this project will provide substantial environmental benefits to this multi-generational farming community while also creating about a dozen local jobs for operators and plant staff.”
For more information, visit www.digestedorganics.com.
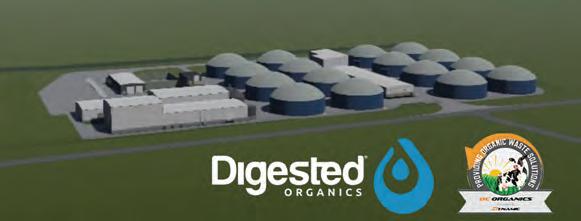
SMART SOAKER IMPROVES COW COOLING EFFICIENCY AND SAVES WATER
The Smart Soaker is a new tool available for controlling the process of cooling dairy cows at the feedbunk. It improves cooling efficiency while using only 60% to 70% of the water consumed in conventional soaking systems.
With more and more restrictions on water use and, in turn, waste disposal, reducing the amount of water that goes into the dairy waste and nutrient stream is critically important. Until now, the only way to save water was to reduce the soaking cycle duration and/or frequency. The Smart Soaker solves that problem without sacrificing any cooling benefit for the cow. Using ultrasonic sensors and “smart” technology, feedbunk soakers are individually controlled and programmed to only operate when the environmental conditions warrant, and only if cows are present. This results in a huge water savings without reducing comfort for the cow.
Research has shown that cows only spend approximately 23% of their daily time at the feedbunk. This means that 77% of the time when the environmental conditions warrant soaking, the soakers do not need to be active. A massive reduction in water usage can be achieved by simply turning off individual units when cows are not in range. This technology does that.
The Smart Soaker technology was developed and is marketed by Agpro. For more information, you can visit their website (agprousa.com) or call 903-785-5531.
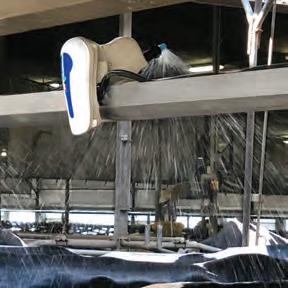
ANAEROBIC DIGESTER SERVICES
Agricultural Digesters LLC
88 Holland Ln. #302 Williston, VT 05495 802-876-7877 info@AgriculturalDigesters.com www.AgriculturalDigesters.com
Future Enviroassets LLC
513-349-3844 LF@futureenviroassets.com www.futureenviroassets.com
ENVIRONMENTAL SOLUTIONS
Hall Associates
23 Evergreen Dr. Georgetown, DE 19947-9484 302-855-0723 hallassociates@mediacombb.net
Tomorrow Water
1225 N. Patt St. Anaheim, CA 92801 714-578-0676 info@bkt21.com tomorrowwater.com
Trident Processes Inc.
1-800-799-3740 frank.engel@tridentprocesses.com www.tridentprocesses.com
COATINGS
Industrial Solutions
5115 S. Rolling Green Ave. Ste. 211 Sioux Falls, SD 57108 605-254-6059 www.isusananoclear.com
DEWATERING EQUIPMENT
Press Technology & Mfg. Inc.
1401 Fotler Street Springfield, OH 45504 937-327-0755 dberner@presstechnology.com
WASTE HANDLING EQUIPMENT
R Braun Inc.
209 N. 4th Ave. St. Nazianz, WI 54232 920-773-2143 www.RBrauninc.com
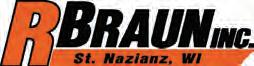
R Braun Inc.
Don’t see your company listed? Send your company name, key contact, mailing address, telephone number, email, and website to marketing@jofnm.com with Professional Directory in the subject line.
Journal of Nutrient Management
Visit us online at: WWW.JOFNM.COM
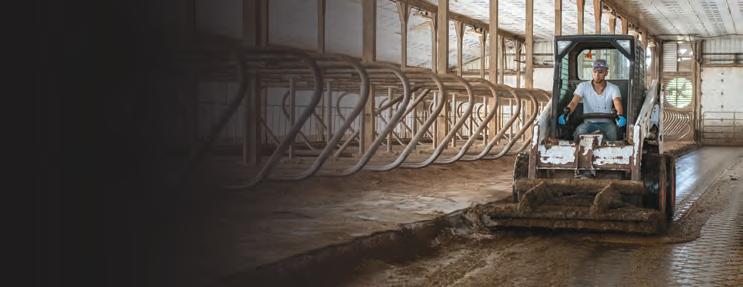
World Pork Expo June 8 to 10, 2022 Des Moines, Iowa Details: worldpork.org
National Pork Industry Conference July 10 to 13, 2022 Wisconsin Dells, Wis. Details: porkconference.com
Wisconsin Farm Technology Days July 12 to 14, 2022 Loyal, Wis. Details: wifarmtechdays.org
North American Manure Expo July 13 and 14, 2022 Chambersburg, Pa. Details: manureexpo.ca
Empire Farm Days August 2 to 4, 2022 Pompey, N.Y. Details: empirefarmdays. leetradeshows.com
Texas Animal Manure Management Issues Conference August 10 to 11, 2022 Fort Worth, Texas Details: texasmanure.org
U.S. Poultry and Egg Association’s Environmental Management Seminar September 22 to 23, 2022 Destin, Fla. Details: uspoultry.org/programs/ education/seminar
World Beef Expo September 22 to 25, 2022 West Allis, Wis. Details: worldbeefexpo.com
World Dairy Expo October 2 to 7, 2022 Madison, Wis. Details: worlddairyexpo.com
If you would like us to include your event on our list, please send details to info@jofnm.com.