
17 minute read
Sidedressing manure deserves another look
This corn is being sidedressed with liquid swine manure using a dragline hose system.
On-farm research demonstrates there’s an alternative time to get manure applied to corn. by Melissa Wilson
Advertisement
In recent years, the window of manure application in the Upper Midwest has been limited by wet or unseasonably cold weather. Additionally, farmers with older-style hog barns have deep pits that fill up faster than they did in the past, so they no longer have a full year of storage and often look for somewhere to apply manure in the summer.
Sidedressing into a growing crop opens up an alternative window of opportunity. Studies of sidedressing swine manure into corn in Ohio have shown promising results, so we wanted to test it in Minnesota.
Trials in the field
In on-farm experiments near Le Sueur, Minn., we tested several nitrogen sources for sidedressing corn over two different growing seasons in 2018 and 2019. Our primary goals were to see if finishing swine manure could be used and if it could be applied with a dragline hose system.
Why finishing swine manure? A large proportion of the nitrogen is in the plant-available form right away, similar to commercial fertilizers. Unlike commercial fertilizers, however, which are generally 100% plant-available shortly after application, a small
portion of nitrogen in manure is in the organic form, which acts as a slow-release fertilizer.
Both years, we set up the experiment in second-year corn in a corncorn-soybean rotation in a conventional till system. The corn was planted in early May with approximately 40 pounds of nitrogen applied with the planter. We sidedressed the corn in early June in large strips (about 24 rows) when the corn was at about the fourth leaf collar stage (V4 growth stage). Each treatment had four of its own strips randomly placed across the field. We aimed to get it applied before the growing point of the corn emerged (around V6).
T he sidedressed nitrogen sources included anhydrous ammonia and liquid urea-ammonium nitrate. The third source, finishing swine manure, was applied at around 3,500 gallons per acre with a drag hose system and a 12-row applicator (see photo on previous page). For all three nitrogen source treatments, we aimed to apply 140 pounds of nitrogen per acre (in addition to the 40 pounds of nitrogen applied with the planter). For the swine manure, we assumed 75% of the total nitrogen would be plant-available in the first year.
In addition to these three treatments, we also included strips where no nitrogen was sidedressed (the control plots). This was so that we could see if our nitrogen sources did, in fact, make an impact on the corn.
Both years were wetter than normal during the growing season, and we applied in slightly wetter conditions than we would have liked. Despite the issues, yield was similar across nitrogen sources in 2018 (see Figure 1).
In 2019, after finishing the manure application, we realized that we had applied a slightly lower rate than intended. Based on our calculations, we applied about 90 pounds of first year N instead of the 140 pounds that we had aimed for. We also observed in the field that more soil clumps had been thrown up on the corn plants during applicaFigure 1. Influence of sidedressed nitrogen source on corn yield
Corn yield (bushels/acre) 250
200
150
100
50
0 a a a
c a
c a
d
AA Dragline UAN Control AA Dragline UAN 2018 2019 Treatment within years Control
The treatments in 2018 and 2019 were anhydrous ammonia, dragline liquid swine manure, liquid urea ammonium nitrate (UAN), or a control that didn’t have any sidedressed N. Yield is shown with a letter above the bar. If the letter is the same as the letter above a different bar, then the yield was not significantly different.
tion than the previous year, likely due to the wetter soil conditions.
These two factors were reflected in the yield that fall, though we suspect the low nitrogen rate was more problematic. The swine manure plots had a significantly lower yield compared to the anhydrous and liquid UAN plots.
The only boat in the industry that can be pulled down the road, no trailer needed! JT BOAT Manure Agitator
GPS available
MADE IN USA
Skidloader agitator attachment

NEW to the INDUSTRY
Propeller is able to move 45 degrees either way. Able to slide in pump out hole at an angle to miss barn overhang. Easy skidloader maneuverability around buildings. Working depth for pits: 6-10 feet Fits through “pump out” holes and reaches pits under barns
visit our website, or call us to find your nearest JT dealer (507) 429-4364 • www.manureagitators.com
Figure 2. Impact of dragline manure hose on corn yield
Corn yield (bushels/acre) 300 250 200 150 100 50 0
None a
V1 V2 V3 V4 Corn growth stage when dragged Hybrid A Hybrid B
b c
e d
V5 V6
This figure shows the impact of dragging a manure dragline hose over corn at various growth stages on corn yield. Hybrid A was Pioneer P0339R and Hybrid B was Pioneer P0306AM. Yield is shown with a letter above the bar. If the letter is the same as the letter above a different bar, then the yield was not significantly different.
All three sidedressed nutrient sources were significantly higher than the non-sidedressed control, though.
Rates and conditions mattered
What can we conclude from this research? When the liquid swine manure was applied at a similar nitrogen rate (first year available nitrogen) as the commercial fertilizers, the yields were similar. Therefore, we may have found an alternative window of opportunity to apply manure in Minnesota.
In the second year, however, results showed that application rates and field conditions matter. More research is needed to fine-tune the practice, and more experience will help with more consistent application across a variety of field conditions.
Deciding when to drag
After conducting the on-farm research in 2018, we had more questions. Is there a limit to the size of the corn that can be dragged with a dragline hose? Would this be impacted by corn hybrids?
In 2019, we started a small-plot research trial at a University of Minnesota research station in St. Paul, Minn., to answer these questions. The plots were four corn rows wide by 40 feet long, and each treatment was replicated four times.
We chose two different corn hybrids, one that tends to be more resistant to green snap issues in high wind (Hybrid A) and one that tends to be less resistant (Hybrid B). Green snap typically occurs between development stages V5 (fifth corn leaf collar is present) and tasseling due to rapid stalk growth making corn plants brittle. Corn is usually sidedressed at earlier growth stages, but it was thought these corn traits might be important for the crop when a hose is dragged over it.
Dragging treatments used a waterfilled, 6-inch drag hose to mimic an application with slurry, pulled behind a tractor over corn at development stages V1 to V6. We also had a control plot that was not dragged with the hose. The photos to the right show the process and what the corn looked like later in the season.
In the fall, yield was collected (see Figure 2). This initial study suggests that corn can safely be dragged up to the V4 growth stage and that hybrid did not seem to make a difference up to that point. At the V5 and V6 growth stages, however, yield was significantly reduced. We also saw that Hybrid A tended to be impacted more by dragging than Hybrid B because yields were lower at V5 and V6.
We will continue the small-plot study for a second year. We are also starting a new, on-farm project to evaluate manure sidedress application The setup used for dragging corn with a dragline hose at various growth stages.

An aerial photo of the plots where corn was dragged at various growth stages from V1 to V6. The photo was taken in mid-July.
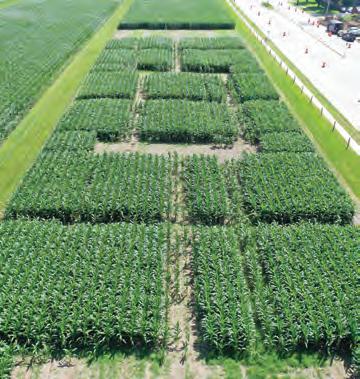
timing. This spring, we used a tanker applicator to apply finishing swine manure at V1, V3, and V7 and will compare it to anhydrous ammonia sidedressed at V3. Keep an eye out for future updates! ■
We appreciate the partial funding for this study from the Minnesota Soybean Research and Promotion Council and the Minnesota Pork Board. We are also thankful to Bazooka Farmstar for lending us the toolbar for sidedressing and to Minnesota Valley Pumping Service for applying the manure.
The author is an assistant professor and extension specialist in manure management at the University of Minnesota.
BANDS OF LITTER WORK BEST FROM A DISTANCE
Manure and used bedding from poultry farms can be a valuable fertilizer source. This litter meets corn’s nitrogen needs while having a liming effect on acidic soils, adding organic matter to fields, and supporting beneficial bacteria.
When surface-applied, up to 60% of the total nitrogen can be lost through ammonia volatilization. Subsurface application can reduce nutrient loss, but research has shown that planting directly into bands of spread poultry litter can result in stunted growth and poor stand establishment.
To better utilize the poultry litter, a team at the USDA Agricultural Research Station in Booneville, Ark., developed an implement for subsurface band application of dry poultry litter. A study found that the implement reduced volatilization by 88%.
Then, to determine the appropriate corn seeding distance from the poultry litter bands, another study was conducted on three sites in Arkansas and Alabama. The researchers planted corn 5, 10, and 15 inches from subsurface banded poultry litter, surface applied poultry litter, inorganic nitrogen, and a control (no application).
According to the results that were published in the Agronomy Journal, the 5-inch distance produced the greatest grain yield, which was similar to the inorganic fertilizer plots. Grain neutral detergent fiber, crude fiber, phosphorus, and potassium fractions were all favorable for the 5-inch band distance treatment. These researchers determined that subsurface banding poultry litter 5 inches away from corn rows may be a comparable, and sometimes superior, replacement for inorganic fertilizers.
Service is #1 here at CentriTEK Industrial Centrifuge Specialists. Along with the high quality service on all brands of centrifuges, CentriTEK supplies a line of decanter centrifuges and systems which are Made in the USA and well suited to handle the requirements for all sizes of dairy farms looking to improve their overall manure management processes.
Fiber Recovery for Bedding
Nutrient Recovery and Phosphorous ReducƟon
ReclamaƟon and Reuse of Water for Flushing
High Solids Removal to Reduce Loads on Lagoons
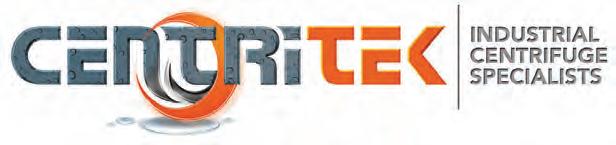
CENTRITEK IS PROUDLY REPRESENTING TRIDENT PROCESSES IN CALIFORNIA
FOR COMPLETE AND TURNKEY MANURE MANAGEMENT PROCESSES
866-769-3900 sales@centritek.com














www.centritek.com
CAPTURING MORE FROM MANURE
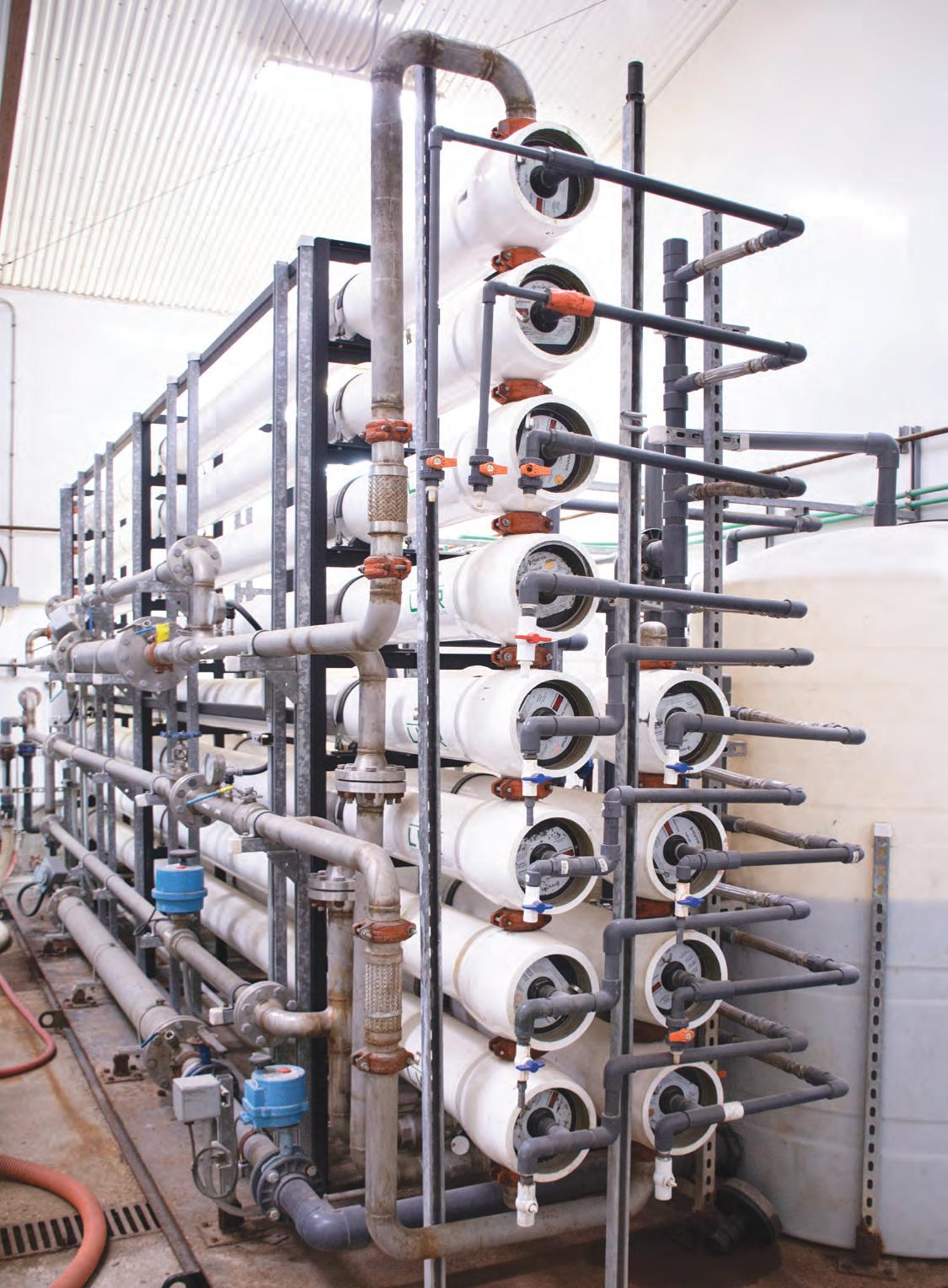
Manure from the cows at Robinway Dairy moves through a treatment system that creates concentrated nutrients and usable water.
At Robinway Dairy, the opportunities to recycle nutrients and water continue to grow.
by Abby Bauer, Managing Editor
When Jay Binversie was a freshman in high school, he traveled to California with his father to visit Maddox Dairy. That trip confirmed his desire to farm, but he wanted to do it on a larger scale than their current 200-cow operation located near Kiel, Wis. “I decided I wanted to manage people and manage a business,” he said.
Seven years later, Binversie graduated with a bachelor’s degree in dairy science from the University of Wisconsin-Madison, and he and his wife, Pam, immediately purchased the farm from his parents, Robert and Janet. “I knew what I wanted to do,” he said.
As was Binversie’s plan, he started to grow the herd and expand the farm. Some of the most recent additions came in 2014, when they built a new parlor, feed center, feed pad, and a cross-ventilated freestall barn. Currently, they have 1,760 cows in the milking herd and average 87 pounds of milk per cow per day. They also farm 1,750 acres of cropland. The Binversies do their own field work and planting, and then custom hire their harvesting and manure hauling.
Binversie is a partner with seven other dairies in a heifer rearing facility in Colorado. Right now, all their heifers are custom raised there; soon, calves will also make the trip West to be grown. That will leave more room on the home farm to expand the number of steers that can be raised. Right now, they feed out 700 steers annually to sell as farm-to-table beef.
Reduce, reuse, recycle
As the farm grew, “sustainability became even more of a priority,” Binversie said.
While Binversie identified the switch to sand bedding in 2007 as his number one best investment, it is closely followed by the installation of their pivot irrigation system the next year. By improving the productivity of his crop fields, the return on investment for the irrigation system was just 2.5 years.
Another decision to make the farm more efficient and environmentally friendly came a few years later, when herd size reached a level that maxed out their current manure storage capacity. Binversie explained that adding another 10 million or 12 million-gallon lagoon would mean more surface area and more odor, and he wasn’t eager to go down that path. More manure stored on-farm would also require nutrients to be trucked farther to be field-applied, raising hauling costs and requiring the purchase of expensive land in a competitive market.
That led Binversie to install the state’s first Livestock Water Recycling (LWR) manure treatment system in 2015. He said the system extracts up to 70% of the water from manure while concentrating and segregating the nutrients.
Prior to entering the system, manure is cleared from the freestall barns using a flush system. Manure then travels to
A MANURE TREATMENT YOU CAN ACTUALLY GET PUMPED ABOUT
Pit-king
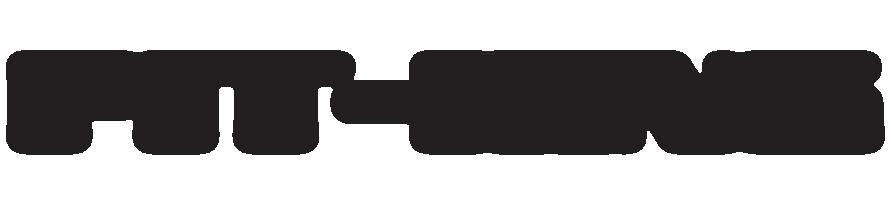
MANURE DIGESTANT PRODUCT
“...had results in the first week of application. The manure smelled different and was very easy to pump.” -- East Wisconsin dairy
“The manure hauler commented he never had a pit of manure that was pumpable without agitation.” -- East Pennsylvania dairy “The smell and the air quality has improved dramatically.” -- Northeast Iowa dairy
(800) 435-9560 AGRIKING.COM
Dairyman Jay Binversie made investments to minimize the amount of manure stored on farm and make better use of his nutrients and water.

the treatment building, where the solids are mechanically removed. The first wave of the system removes 95% of the phosphorus from their manure.
Binversie explained that these solids, which are obviously high in phosphorus, can be trucked to fields farther away from the farm that are in greater need of the nutrient. One load of the micro material is equivalent to 10 loads of manure and reduces the number of trucks that must travel on the country roads each fall.
Using the liquids
From June to mid-September, Binversie stores the remaining liquid manure portion in an old slurry store and is able to irrigate that liquid, which contains nitrogen, potassium, ammonia, and other micronutrients, on his crop fields. This adds even more value to the irrigation system investment.
He found that they could apply this nutrient-filled liquid on corn once a week from when it is knee high until it tassels, resulting in a 3- to 5-ton yield bump per acre. In addition, the risk of leaching is eliminated since the product is distributed in small amounts. “We found agronomic advantages we weren’t expecting,” he said.
During the remainder of the year, the removed liquid portion of the manure continues on through the complete treatment process. First, it travels through screens to remove the fine solids, and then goes through further filtration and purification with the use of polymers and reverse osmosis. Finally, the dissolved solids are removed, creating a concentrated nutrient product containing potassium and ammonia and clean, reusable water.
Binversie uses this recycled water on the dairy in many ways, such as cleaning equipment, washing the milking parlor floors, mixing footbath solutions, filling the polymer tanks for the treatment system, and more. The farm has been using recycled sand for bedding for more than a decade, and now they use this water to wash the sand, too.
The piece of equipment that has given the farm its fastest payback was the bedding dryer Binversie installed 2.5 years ago. Binversie said this addition dropped their somatic cell count from 200,000 to 125,000 somatic cells per milliliter and paid for itself in just one year.
Binversie also uses the dryer to remove moisture from the micro product, condensing its volume even further. The dried sand and dried micro are stored in an old feed bunker until used.
By recycling the water found in manure, Binversie creates an estimated 16 million gallons of clean water a year. That is 16 million gallons of water that doesn’t need to be drawn from the well, and nearly 3,000 fewer truckloads of manure that need to be hauled. “It’s very environmentally friendly,” Binversie said. “That’s the best part of the story.”
A side enterprise
The opportunity to improve the environment and give farming a good reputation guided him to the manure treatment system, but it also opened another door for Binversie. A chat with a friend one evening led to an idea that spurred a side business, and Bucky Organics was born.
Using the nutrients removed from the manure, they created an organic fertilizer product that can be used in nurseries, by gardeners, and by other farmers. In the company’s third year, Binversie sells both dried fertilizer and bottled liquid concentrate in gallon containers and larger totes. They also sell a hand sanitizer product.
Binversie said their products are shipped all over the country, and they have become very popular with hemp farmers as an organic nutrient source.
“It’s not the main reason we put in the manure treatment system,” Binversie said, “but it has been a fun thing.” He sees more growth opportunities for Bucky Organics and is eager to build upon this part of his operation.
Opportunity in the future
Binversie is the general manager of Robinway Dairy, and his wife, Pam, does the bookwork and landscaping for the farm. They have a solid team of managers, including someone who oversees manure separation and water recycling on the farm.
Some of the recycled water is stored prior to being irrigated onto growing crops.

Longevity is important to Binversie, and eight of their 28 employees have been with the farm for more than 12 years. He looks for people with positive attitudes, he said, because that helps create positivity all around the farm.
What does the future look like for Robinway Dairy? Binversie isn’t sure yet. He and his wife have three daughters who are all pursing careers off of the farm, but maybe that will change someday. Or, perhaps Binversie will bring in another partner.
For now, Binversie is excited to find more ways to recycle nutrients on the farm, maintain positive neighborhood relationships, and grow the Bucky Organics business. “There’s a lot of opportunity here,” he said. ■