
14 minute read
Use the four R’s to guide your application strategy
to guide your application strategy
Achieve nutrient management success the right way by focusing on the source, rate, timing, and placement of manure.
Advertisement
by Deanne Meyer
For farmers, local geography and climate determine the limiting nutrient for manure application. That being said, for much of the United States, phosphorus or nitrogen limit manure nutrient application.
A guide to manage manure nutrients is to use the four R’s: the right source, the right rate, the right time, and the right place. This also assumes there is a target crop yield and nutrient composition.
Why do people care about these four R’s? Efficient and sustainable livestock production relies on them. For many, feed nutrients are imported to farms. Nutrient management is an iterative process that allows you to more efficiently use residual feed nutrients for crop production.
Nutrient composition varies Let’s start with a review of the four R’s.
Right source. Manure solids, slurry, and liquids have different concentrations and ratios of organic and plant (ammoniacal) nitrogen. Organic nitrogen requires soil microbes to mineralize the nitrogen to ammonium. Much research focuses on better prediction of mineralization rates. Animal diet, housing and manure collection, storage, and treatment all influence the composition of manure that is applied.
For all animal facilities, manure from replacement animals will have a different nutrient composition than that of the mature animals. Testing manure sources provides farm specific nutrient composition to predict plant availability.
Identify sampling protocols for soil and manure. Your local or state Cooperative Extension Service or Natural Resources Conservation Service office may have established recommendations for sampling and plant nutrient application guidelines.
Correct laboratory methods for analyses is essential for results to be useful. Consult your water quality permitting agency to be sure your analyses are compliant. For us in California, wet chemistry is required and labs need to meet a specific certification.
The old adage “Test, don’t guess” is essential to use manure nutrients. Consult with your nutrient management specialist to discuss concerns you may have related to using your various manure sources.
Right rate. Nutrient budgets provide a road map for application. The targeted crop nutrient removal is the starting point. Biological availability and losses are considered. Monitoring nutrient conservation is important to document nutrient stewardship.
Calculations require knowing the nutrient composition of manure and being able to deliver known amounts of manure to each field as uniformly as possible. It is important to be able to measure how much manure is applied. It is also necessary to track when and where manure is applied.
How much nitrogen or phosphorus needs to be applied to meet your crop goal yields? Your water quality permit may establish target application rates. For dairies in much of California, the rate of nitrogen application is targeted at 1.4 times the estimated crop nitrogen removal.
All nutrient applications are recorded. Nutrients applied divided by nutrients removed are compared at harvest. Annual reports to the regulatory agency include a crop by field summary of actual practices. Targeting the right amount of plant-available nitrogen may be equally important in your watershed.
In other parts of the country, phosphorus is the limiting nutrient. Phosphorus application rates are based on anticipated available soil phosphorus. A Bray, Mehlich, or Olsen test is conducted, depending on soil type, and application recommendations are based on test results. Your local Cooperative Extension Service or Natural Resources Conservation Service office should be able identify which test best suits your soil type.
Where it belongs
Right time. Timing manure nutrient applications with plant nutrient needs helps utilize nutrients efficiently. Solid and slurry manure applications usually are limited by local cultivation practices.
Use manure testing to determine the specific nutrient composition of the material that will be applied to the field.
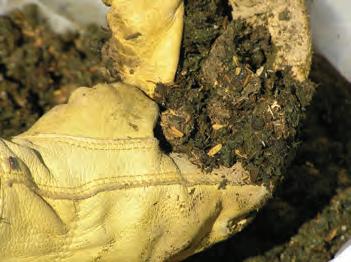
Manure spreaders and slurry tanks transfer manure from storage to fields. This often occurs before crops are planted. Liquid manure applications can be water run in irrigation systems. This allows applications once crops are planted.
Flood, pivot, or drip line irrigation systems may incorporate diluted liquid manures. Adequate filtering of particles is essential to minimize clogging of these systems. In some pivot systems, paired nozzles allow for delivery of liquid manure and rinsing of plants after liquid manure application.
Weather is another key factor. Timing of application requires the ability to get into fields as well as the ability of manure to stay where it is applied.
Frozen or saturated soils don’t lend themselves to optimum manure management. You’ll want to be sure you know your permit restrictions if you live in a state that prohibits manure application on frozen soil or if you have restrictions on application to saturated soils.
California doesn’t have frozen soils where dairies reside. However, it can have intense rains in winter, leaving some fields inundated with water. Application of manure to these fields when saturated is not allowed.
Right place. Different cultivation practices are used for permanent crops, pastures, and forage production. Nutrient application in orchards targets areas where tree or vine roots reach and band application of nutrients occurs.
Pasture or alfalfa fields provide longterm ground cover. Surface application with minimal incorporation occurs on these fields.
Annual crops often require more cultivation. Application with direct (shank injection) or partial (irrigation) incorporation of nutrients can be done. Surface application with direct incorporation (tillage) is also possible. The objective is to place nutrients near plant roots and keep them there as long as possible for plants to use.
Soil type and water holding capacity are important factors associated with keeping nutrients near plant roots. Soil management remains key in a nutrient management strategy.
Nutrient budgets take into consideration local conditions to identify targeted nutrient applications. Matching manure nutrients to crop nutrient needs helps use nutrients more efficiently. It also improves your bottom line to use nutrients you have already imported as feed and minimize the need for importing other nutrients to the farm.
If your animal operation does not have sufficient crop production capacity for the manure generated, you may have already identified off-site prospects for manure. On-farm practices to make nutrients more dense for export may be in place. No doubt, you are already paying close attention to new, potential on-farm manure utilization technologies. These technologies, paired with the four R’s, can help maximize delivery to your crops. ■
The author is a livestock waste management specialist with the University of California, Davis Department of Animal Science.
FUTURE FOR A BETTER FARMING

Rob Stout and his stepson, Alex Zimmerman, raise hogs and grow corn and soybeans at their Washington, Iowa farm.
Farmers often serve as the ultimate stewards of the land, and hog producer Rob Stout would certainly fit that description.
by Abby Bauer | Managing Editor
t a young age, Rob Stout discovered his passion for animals and decided to become a farmer. Early in his career, he also became passionate about protecting the land for himself and for generations to come.
Stout’s agricultural roots run deep. He is a ninth-generation farmer and is the fifth generation to grow crops and raise hogs in Iowa. At one time, their family raised beef cattle, too, but today, Stout and his stepson, Alex Zimmermann, focus on feeding out hogs on their Washington, Iowa, farm. At any one time they have 3,600 feeder pigs in their barns, finishing out 9,000 hogs per year.
After graduating from Iowa State University in 1978 with an agricultural degree, Stout returned home to farm with his dad. About 10 years later, Stout began renting the land that now serves as the main location for the current farm. Back then, they used the facilities on that property to calve out beef cows, but when lightning struck and burned down that barn in 1997, they decided to sell the beef cattle.
A few years prior to that, in the early 1990s, Stout invested in a sow cooperative with nine other owners. They started with 1,200 sows. The cooperative is 8 miles north of Stout’s farm, with a nursery facility located at another site.
Twenty-five years later, there are six owners of the cooperative with 2,400 sows. They meet monthly to make decisions about animal care, breeding, and facilities.
Stout receives pigs from the cooperative when they are 9 or 10 weeks old. They are fed for around 18 weeks, and once finished, they are sold on the open market.
The pigs are housed 25 to 34 per pen, and there are about 600 pigs per barn. The barns are mechanically ventilated, and sprinklers turn on at 84°F to cool the animals in hot weather.
Stout works with a nutritionist to formulate 22 different diets — 11 for barrows and 11 for gilts. The females receive a higher level of protein in their rations. The automatic feeders are run on sensors, delivering small amounts of fresh feed multiple times per day.
Stout carefully observes water consumption and records the daily water intake for each barn. He uses these numbers to monitor animal health, noting that water consumption typically goes down a day before pigs become sick, indicating a problem.
Once a group of pigs is sold, the barn is pressure washed and sanitized before the next group of pigs move in.
Even though Stout has farmed all his life, his philosophy is to seek out opportunities for continuous learning. “This business changes so fast, you have to keep up or you’re falling behind,” the thoughtful farmer said.
For better soil health
When it comes to the land on their farm, Stout said, “I believe in soil health,” and he has certainly taken steps over the years to support that statement.
In addition to the hog operation, Stout and Zimmerman also have 1,100 acres used to grow corn and soybeans. They have been no-tilling the fields since 1983, after Stout attended some no-till tours put on by their extension director and encouraged his dad to give it a try.
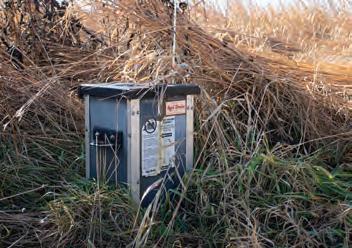
The bioreactor on Stout’s farm was one of the first to be installed in the area. He tests the water monthly for nitrate levels.
“When I talked to my dad about it, he wasn’t so sure of the idea. He said, ‘You buy a planter, and we’ll give it a go,’” Stout explained. “And we never looked back.”
Over time, Stout has learned a lot about successful no-till. For example, he said it’s important to get residue out of the rows with row cleaners to
prepare the seedbed. “The art of no-till is an evolving process,” he said. “I try to keep an open mind and attend a lot of continuing education.”
Stout commented that their view of manure has also changed over the years. “Manure was once considered a waste product, but then we became more aware of the value.” Complementing the no-till, they started injecting manure in 1996. Older low-disturbance injectors left the ground bumpy, he said, but the last two they have owned allow him to plant right after manure injection.
By injecting the manure, the odor is really minimized, Stout said. Still striving to be a good neighbor, he will avoid spreading manure on holidays and when the wind is blowing directly at someone else’s property.
To make the best use of the nutrients, Stout carefully tests his soils every four years in 2.5 acre grids. He uses that data to determine fertilizer needs, and manure is part of that package. Using manure saves Stout thousands of dollars in fertilizer costs and improves soil health.
Manure is stored in pits underneath their hog barns, and they try to get them completely emptied in the fall. Swine manure contains a lot of water, so it is less concentrated than some other manure forms. Stout tests his manure every fall, and it typically contains about 55 pounds of nitrogen (N), 22 pounds of phosphorus (P), and 35 pounds of potassium (K) per 1,000 gallons.
Stout complements the manure with variable-rate applications of commercial fertilizer, which is done by a hired applicator. Stout does this to fine-tune N, P, and K application.
He also delivers nutrients to the field several times per year, through manure application, fertilizer applied with the planter, and by sidedressing growing plants, so that crops don’t get a full dose all at once.
“Spreading it out through the year is environmentally better,” he explained.
They also do the stalk nitrate test on growing corn to monitor nitrogen levels. “We are trying to do the right thing to make sure there isn’t too much
Low disturbance injectors make a groove for the manure, then kick some soil over it. Stout and Zimmerman apply all of their own manure, about 1 million gallons each fall.

nitrogen on a field,” he said. “I’m always open to improvements.”
Watching the water
Careful application means more nutrients stay on the fields where they belong. For the past eight years, Stout has been testing the water and working diligently to reduce nitrates in their area.
He belongs to the West Fort Crooked Creek Watershed Group, and it was through that organization that he initially received funds to do water nitrate testing. When he started testing, nitrates were at 14 to 18 parts per million (ppm).
He began planting cover crops to reduce nitrates and phosphorus in water. He said he started small but plants covers on all his acres now.
He also installed a subsurface bioreactor on a tiled field in 2014. The bioreactor intercepts drainage from about 70 acres. As water passes through the bioreactor, denitrifying bacteria in the wood chips convert nitrate into dinitrogen gas.
Stout tests the water at the inlet and outlet of the bioreactor monthly, and over the past five years, he has seen a nitrate reduction of 70 percent. Aside from one really rainy month, their nitrate levels now stay below 10 ppm.
The bioreactor is 30 feet wide, 90 feet long, and 6 feet deep. It contains 4 feet of wood chips, with 2 feet of dirt over that. Pollinator flowers are planted on top of it. In all, the bioreactor takes up about one-tenth of an acre.
Even with cost sharing through the watershed group, the bioreactor was a significant financial investment, Stout explained. Still, he was pleased they installed it as he felt they were “doing the right thing.”
Stout’s bioreactor was the first one installed in their area. So far, it is working well, and he hopes it lasts the 20 years it is expected to before the wood chips need to be replaced.
To further prevent runoff, Stout has also planted some native grass buffer strips to slow the flow of rainwater, snowmelt, and nutrients. “We do what we can to keep nutrients on the farm,” he said.
Open to improvements
Solar panels are another environmentally friendly aspect of the Stout farm. The first rooftop solar panels were placed six years ago, with more added over time. Stout works with Alliant Energy on a net metering system, and the panels cover the electrical needs of the pig barns year-round.
Again, this was an expensive project to complete, with an anticipated payback period of six years. However, Stout was happy to do it and said, “Environmentally, it is a good thing to do.”
Much of what Stout does is to leave the land in better shape for those who farm after him, and he feels many other farmers are doing the same.
“There are a lot more regulations now than when I started farming,” he said. “But things that are happening are good. We are taking better care of our hogs. We are taking better care of our manure. We are all doing better at taking care of the environment.”
Stout plans to continue raising hogs and crops with his stepson. Maybe one day, one of his young grandsons will follow in his footsteps and farm the land he has worked so hard to preserve. ■

POULTRY SYMPOSIUM PRODUCTION & PROCESSING
The poultry symposium hosted by The Poultry Federation of Arkansas, Missouri and Oklahoma will take place on April 15-16, 2020 at the John Q Hammons Convention Center in Rogers, AR
Live production and processing personnel as well as suppliers who support live production and processing of turkeys, breeders and broilers are encouraged to register and attend. Agenda includes a general session with five breakout sessions focused on: breeder, broiler, hatchery, turkey and processing.
The poultry symposium vendor tradeshow runs for two days and is a prime outlet for allied industry members to showcase their products and/or services to attendees. Attendees of the Symposium will include top level decision makers in live production and processing.