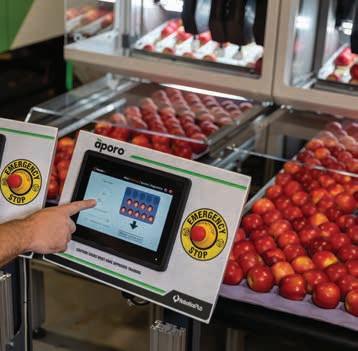
5 minute read
Labour-saving robotic packer’s timely arrival
Laboursaving robotic packer’s timely arrival
Elaine Fisher
The launch of Aporo II, a New Zealand invented intelligent robotic fruit packing machine, may seem timely given today’s tight labour market, but its arrival is no coincidence, says Cameron McInness of Jenkins Group.
“The reality is that this type of commercially proven technology doesn’t appear overnight or even in a few years. This was about foresight and early investment to have the right solution ready when the crunch came. Covid-19 has certainly exasperated the labour issue, however it was building quickly prior to this.”
Developed and manufactured in Tauranga by Robotics Plus (RPL), the Aporo II builds on the proven technology of the original Aporo I Produce Packer, first developed in 2018. The latest model has twice the throughput, packing 240 fruit per minute, saving between two and four labour units per double packing belt. “The team at Robotics Plus acknowledged an emerging challenge around labour long before anyone was talking about it, and once the issue had built to a crescendo there was a decade of development completed and a commercial product on the market,” says Cameron who is a director of Jenkins Group – a New Zealand-based company which co-founded Global Pac Technologies (GPT) with United States-based Van Doren Sales Inc as a joint venture to sell the technology to the global market. “We have been rolling out this new machine with some key customers globally and the results have been dramatic. One of our Australian customers built a new packhouse and installed three of our Aporo IIs. That increased their packhouse production by 30 to 40 percent and reduced their labour by 50 percent.” Cameron says the key benefit of any labour-saving technology to a post-harvest facility is the redeployment of labour into higher value roles and tasks instead of menial ones. “This obviously is a win-win with employees getting a more engaging role in the facility and operators getting better value out of their scarce labour pool.” The technology is now being used in France, the United Kingdom, Sweden, Belgium, the United States, Australia and New Zealand – primarily to pack apples, and now stonefruit like peaches and nectarines. Steve Saunders, chief executive and founder of Robotics Plus says development of Aporo l began in 2014 and the first pre-production machines were released in 2016.
The touch screen interface for the Aporo II robotic fruit packing machine is very intuitive and easy to use
“In 2018, production machines were released and we formed our distribution partnership with GPT. In 2018 we began work on Aporo ll and shipped the first six pre-production machines in late December 2020. Since then we have shipped a number of production machines globally and have been fine-tuning the technology leading up to the official release (in April 2022). “The machine uses suction to pick up the fruit after it has been through its orientation and blush-side-up process which uses advanced algorithms and vision systems. The technology handles the fruit very gently, if not more so than humans.” With minimal alterations, Aporo has the ability to pack other fruit too. “This past year we have developed stonefruit packing capability on the Aporos and packingtray-in-box capability for both apples and stonefruit. We are now exploring further opportunities such as avocados.” Steve says the company was pleased that GPT used this year’s Fruit Logistica expo in Berlin to showcase the Aporo ll. “Fruit Logistica is one of the global premier events for the fruit trade and showcasing of current packing technologies. The benefits of being there for New Zealand are many. The Aporos are manufactured in New Zealand creating opportunities for our outsourced manufacturing partners,
creating higher skilled and paid jobs, and putting New Zealand on the global agritech stage. “At RPL we have taken on a number of university graduates over the years across many disciplines such as mechatronics, engineering, electrical and software.” Cameron says New Zealand has long been looked at as an incubator for clever solutions to industry problems and the Aporo machines are world leading. “Other options from overseas for automating the placement of fruit into trays are less mature and still proving their reliability and return on investment. This Kiwi invention is well ahead of the pack and has the world’s attention. “Aporo II can be retrofitted across two packing belts instead of one, so it has effectively doubled the throughput and the labour saving that Aporo I could deliver. “What’s unique about Aporo I and Aporo II is they are designed for really simple autonomous packing. The machine is very intelligent. It looks at the fruit, orientates the fruit and doesn’t need to be told what type of trays you’re using – it just looks and finds the pockets. It’s really powerful technology. “Its internal vision system or ’neural network’ is continuously learning to adapt to different fruit varieties and improve performance over time. It features automatic tray pocket recognition for any tray type and the touch screen interface is very intuitive and easy to use. Not only will it orientate and place fruit the right way on the tray, you can also ask it to find the best colour on the apple and spin that side up. It’s very clever.” The Aporo machines can be retrofitted to existing packhouse infrastructure within a matter of hours in some cases. It straddles existing conveyors and is available in configurations for both single and double packing belt layouts. Since Aporo I’s initial launch in 2018, over 100 packing belts have had the technology deployed on them around the world, and a strong pipeline of orders have already been received for Aporo II. “We have a couple of big growth opportunities in California right now. “We are the market leaders in this space and our customers are having real success. The global apple market is worth approximately US$80 billion, and automation is key to over-coming the worldwide labour shortage that all post-harvest operators are experiencing. The beauty of Aporo I and Aporo II is they can be installed on both new and existing packing lines, making this technology accessible to everyone.”

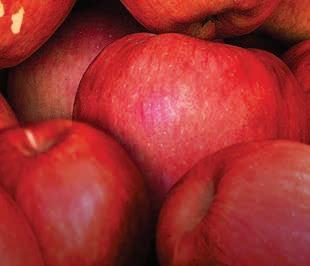

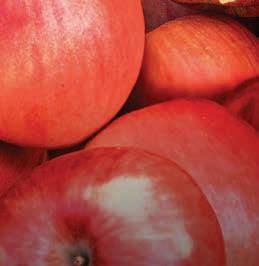