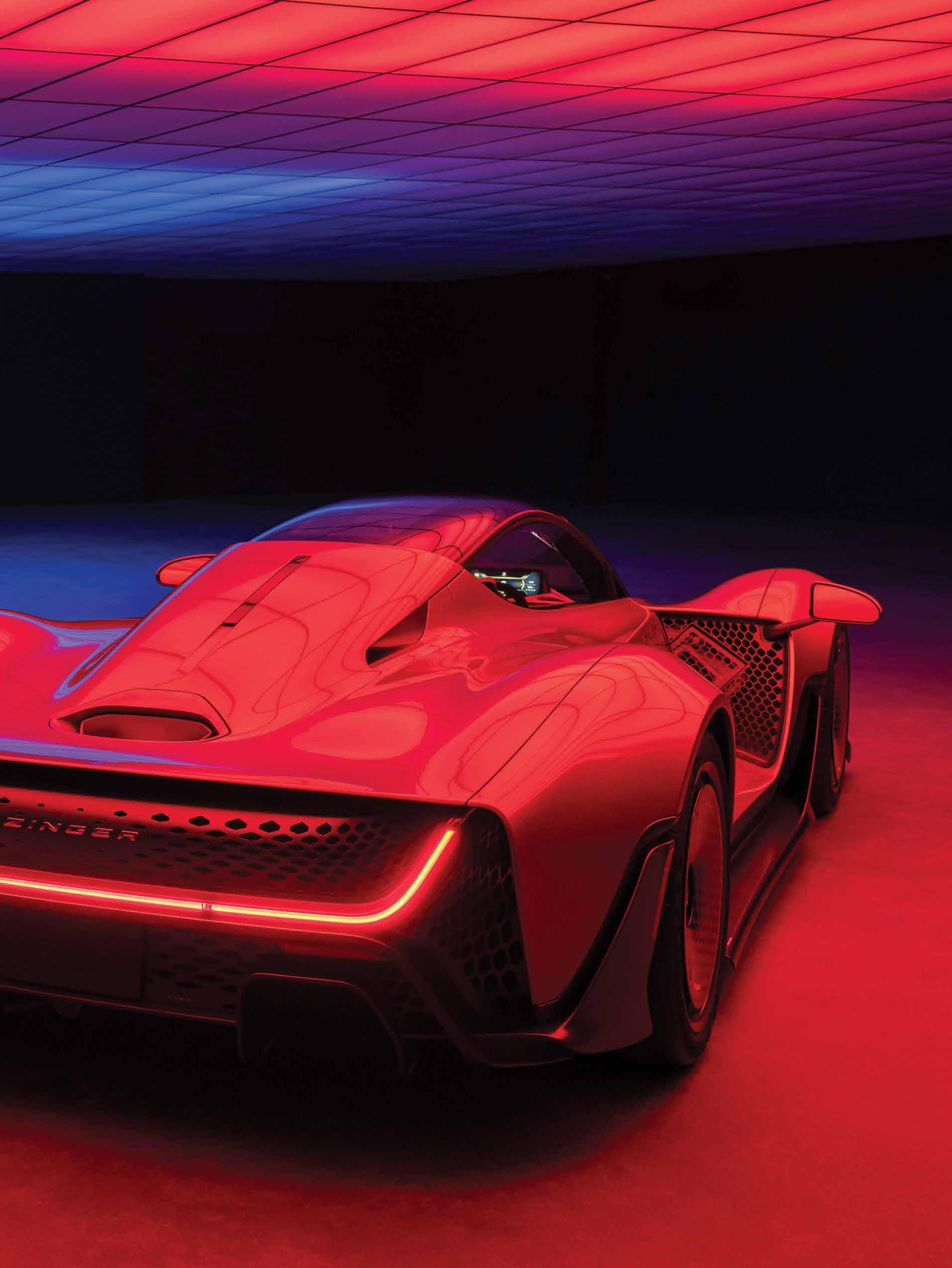
3 minute read
The Fine Print
How Czinger Vehicles aims to turn automotive manufacturing on its head with the world’s first human-AI designed and 3D-printed hypercar
WORDS: CHRIS ANDERSON
Advertisement
Imagine walking into the car showroom of the future. You would choose the model, the extras you needed, and the body colour, then once payment was made the salesperson would simply press a button. In a nearby assembly room, a 3D printer would come to life, start churning away, and a short while later your new car, to your exact specifications, would arrive on the forecourt. No waiting lists, no sourcing parts, no stock shortages. And a car company in California is already heading in this direction.
Czinger, a Los Angeles-based start-up, actually grew out of another company, Divergent, which specialises in AIdriven design software, 3D printing and automated assembly. And with the fatherand-son team behind it, Kevin and Lukas Czinger, also fans of superfast, limitededition hypercars, using their technology to make one became the next logical step. “The 21C is our first vehicle,” explains Lukas Czinger. “We’re leveraging our own proprietary design and manufacturing system, DAPS (Divergent Adaptive Production System), which is the world’s first digital manufacturing solution, with over 550 patents, and the potential to transform the automotive industry.”
No ordinary manufacturing process, and no ordinary car. With its smooth, ultra-lightweight aluminium and carbon-fibre chassis, fighter jet-inspired cockpit, and scissor doors, plus a hybrid powertrain consisting of a twinturbocharged 2.88-litre V8 engine and an 800V electric drive system, the 21C produces a combined 1,250hp, with a 0-100km/h time of 1.9 seconds and a top speed of around 407km/h – a more powerful 1,333hp version is available too. Needless to say, the car has already broken lap records at the Laguna Seca Raceway and Circuit of the Americas. “It’ll even run on net zero fuels, such as carbon-recycled methanol,” adds Lukas. Talking about the look of the 21C and its unusual cockpit seating, Lukas cites the SR-71 Blackbird jet as inspiration, with the pilot at the front, and the co-pilot or wingman behind. He’s also very proud of the digital manufacturing system. “Our cars are the first to use anything like this,” he says. “It’s all supercomputing, machine-learning, new materials and architectures, additive manufacturing and robotics, allowing you to create vehicles previously impossible or unthinkable, both in terms of looks and how efficient they are. We’ve gone further in terms of weight-saving, for example, which increases performance and improves sustainability, using fewer materials.”
Lukas talks about the printed gearbox casing used, which allowed Czinger to integrate function, reduce mass, and enable rapid design improvements throughout the development process. According to Lukas, artificial intelligence and laser-metal 3D printing allowed Czinger to drastically cut the design and production times, and make almostunlimited changes to their prototype.
“The BrakeNode, which combines the brake calliper and suspension components into a single unit, was another benefit of this process,” says Lukas. “We could significantly reduce the mass, increase the stiffness, and reduce the part count, with a marked improvement to the ride handling and overall performance.”
In production, the 12-piece rear subframe is assembled in around five minutes, with other components placed on top, and once the specification has been entered, an identical car can be reeled off at the touch of a button — handy for scaling up production if a particular model becomes popular. With production maximised, energy and material waste are minimal. “This is a vehicle defined by iconic design, ground-breaking technology, dominant performance, and harmony with nature,” explains Lukas.
“It’s a manufacturing revolution.”
The plan is to make just 80 examples of the Czinger 21C, with each carrying a price tag of more than $2 million. It also comes in two variants, both road legal and perfect for the track, but with the 21C V Max offering a longer rear for optimal GT performance. “There’s also a storage compartment in the 21C V Max for a bespoke luggage set, providing endless customisation options for owners to match their taste,” Lukas adds.
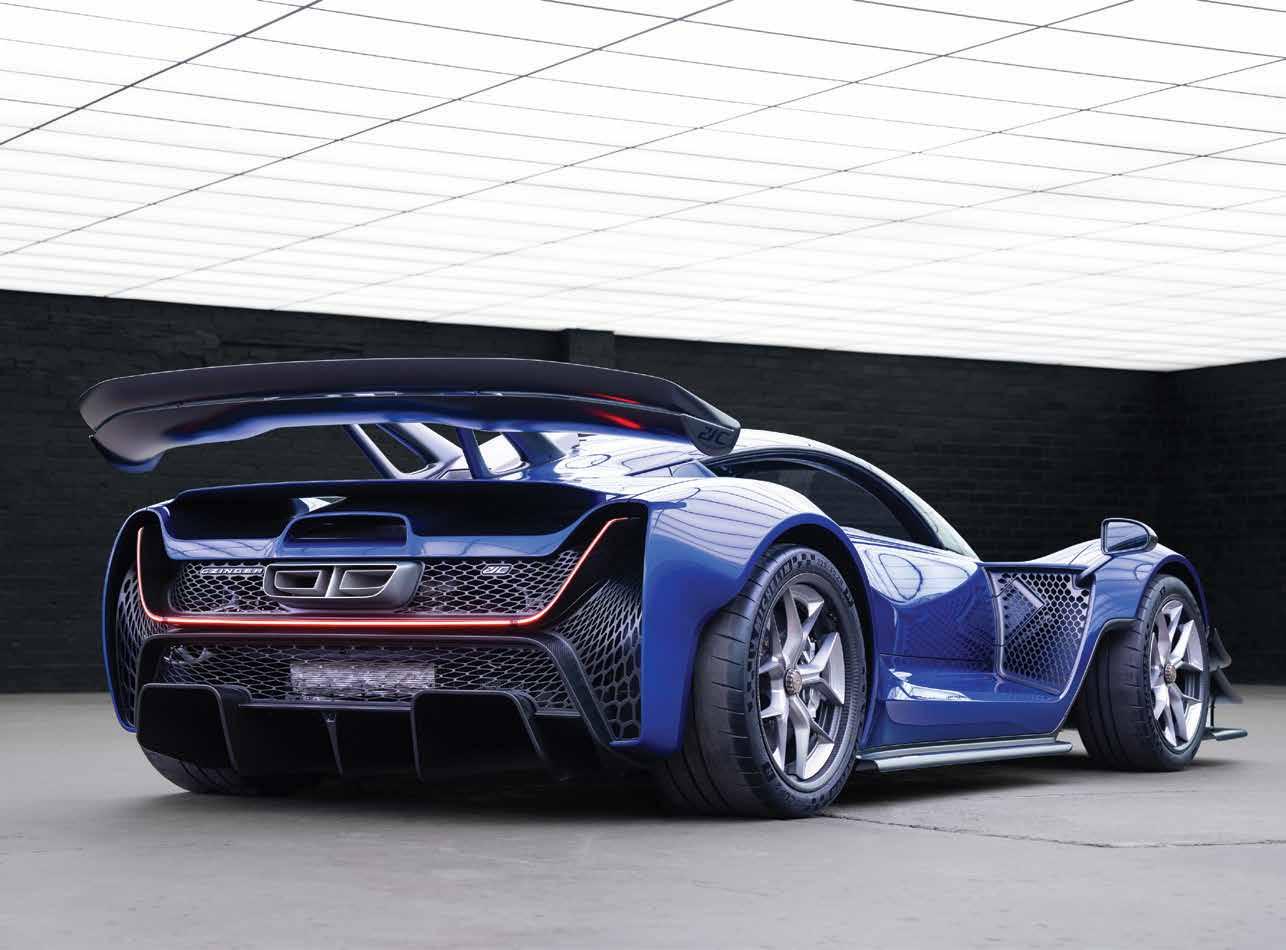
It seems that both the car and the technology behind it are garnering attention. Lukas claims that many of the planned 80 examples have already sold, with customers awaiting delivery later this year, and Aston Martin asking for 3D-printed aluminium subframes for its DBR22 speedster, which will arrive from Divergent already assembled. A relief for Lukas and his team, as he says the initial stage, getting everything up and running, creating all of the new software, hardware and processes, was easily the biggest challenge.
Czinger says it also plans to expand its customer network, with dealer locations in the UAE and Saudi Arabia. Surely the right places for such a forward-thinking company.
“We’ve built our business to leverage digital manufacturing from day one,” Lukas concludes. “It means we can move at a pace not seen by the automotive industry before, with sustainability and fewer materials used among the advantages we offer.”
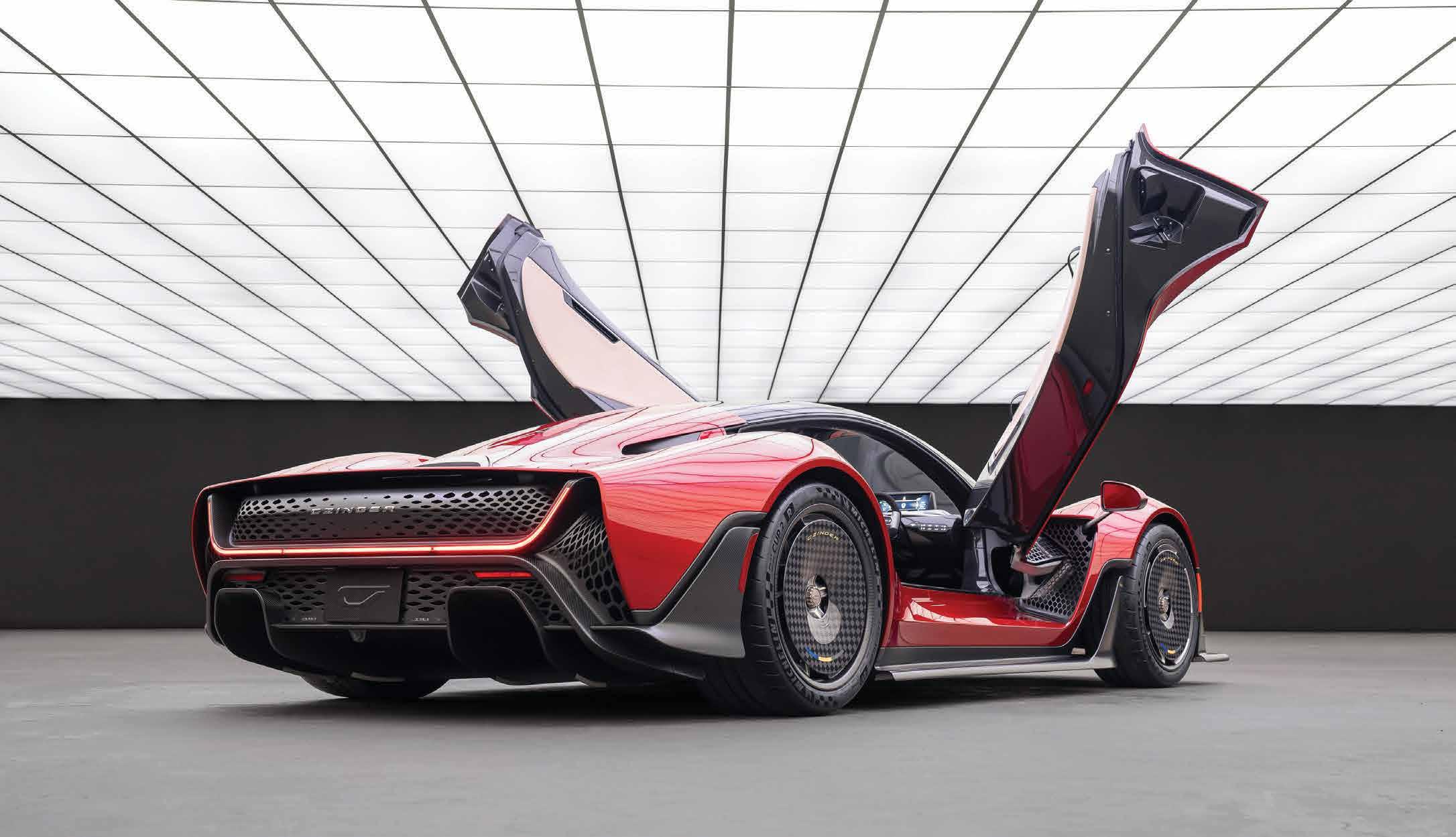
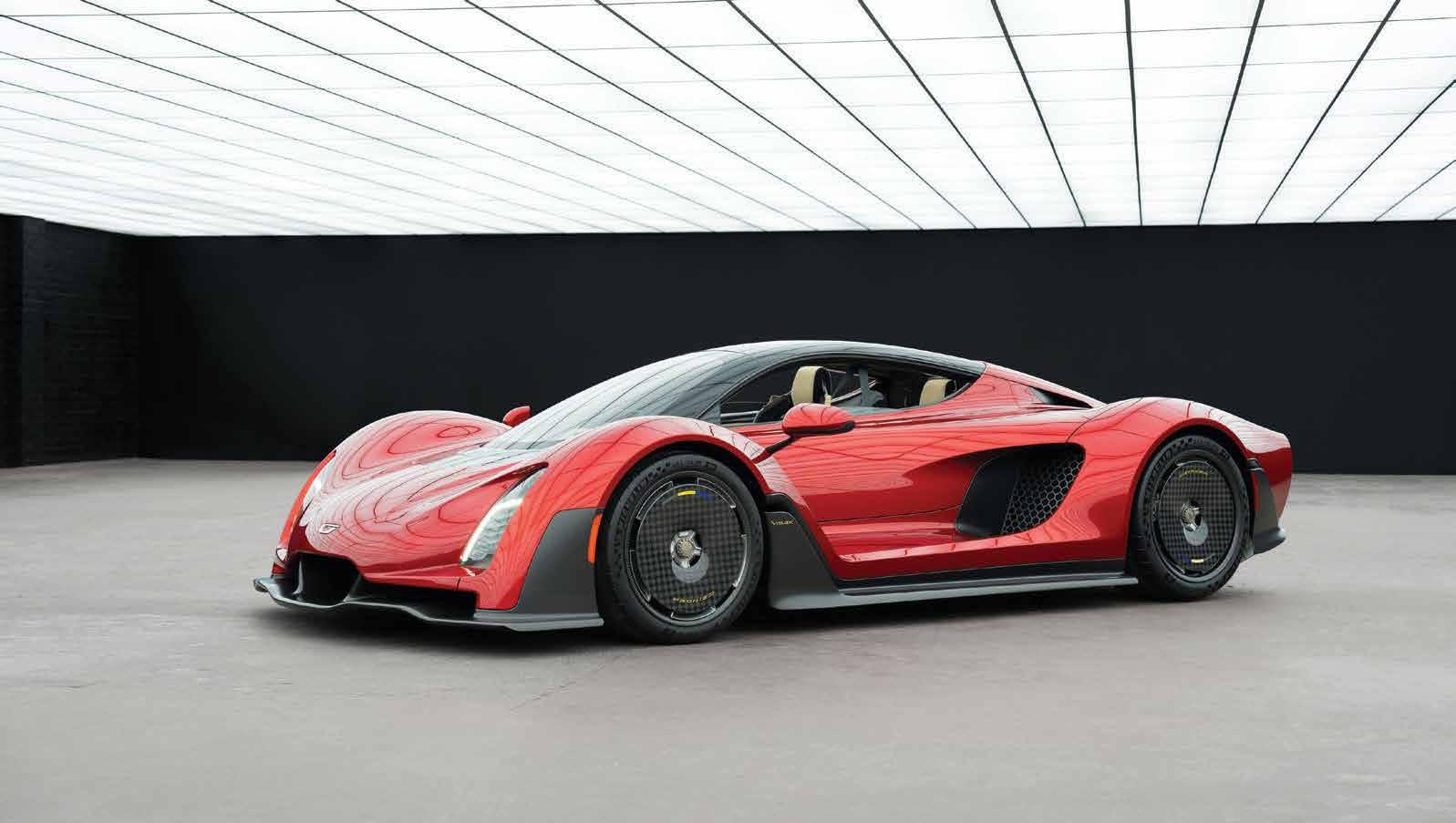
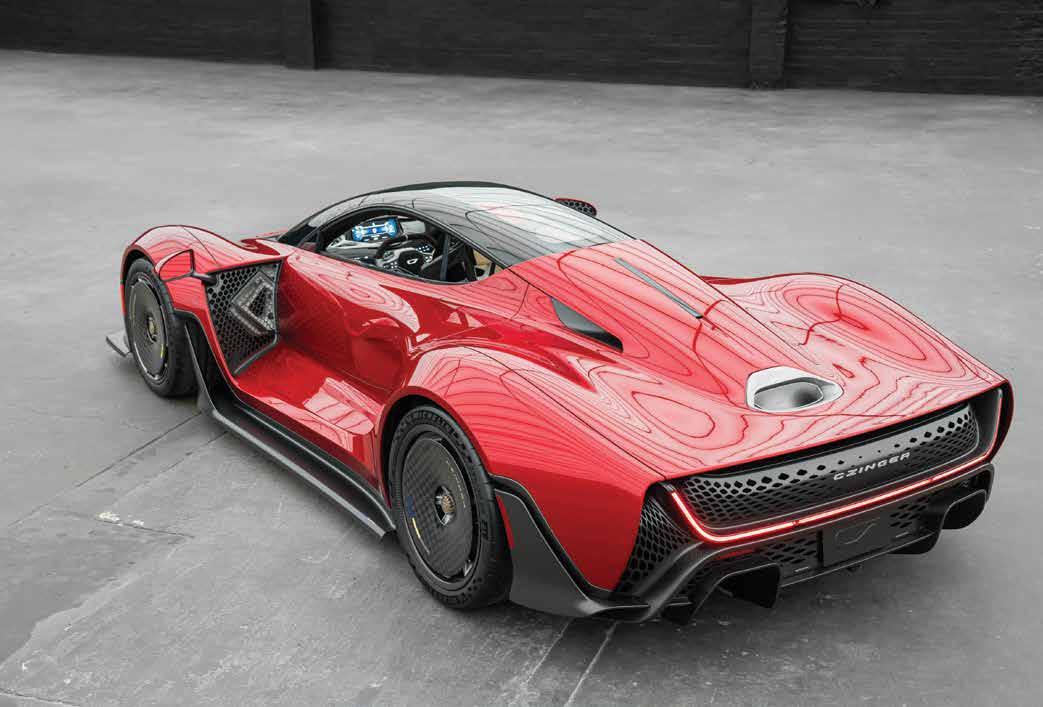
