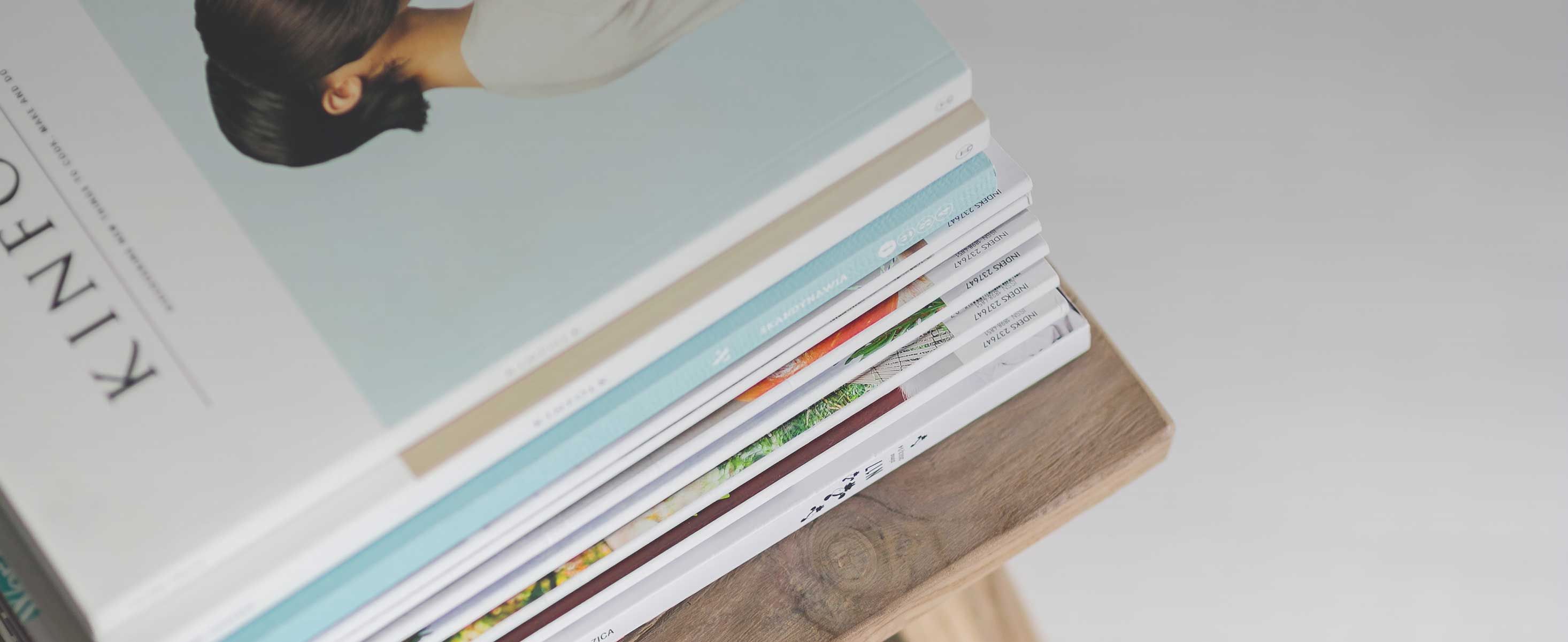
10 minute read
Digitization: How the ‘Internet of Things’ changes industry and our company
Are we ready for the Internet of Things?
The digitization of the world continues persistently. As physical objects and the virtual world of data become increasingly connected, the automation industry faces a real challenge. This raises the question: is Endress+Hauser prepared for the fourth industrial revolution?
Advertisement
JS: Bitte Wortwiederholung vermeiden. Digitization is changing our personal and work lives at lightning speed. Across a swathe of industries including travel, book retailing, transportation and communication, business models are changing. Even social interaction is taking place more and more on electronic displays. No wonder: every 18 months, computer chips are doubling in power and the price of information is cut in half. Nowhere is the pace of development so fast as in the world of bits and bytes. And in no other industry is the next trend so difficult to forecast.
What does that mean for Endress+Hauser? The digital transformation has long since impacted the industrial sector. As automation and information technologies converge, experts predict this will lead to radically different production flows. The boundaries between production, warehousing and administration will be transparent and the systems for production, sales, customer and supplier management will grow more tightly meshed. Exactly where this development will lead to is anyone’s guess, but one thing is certain: it will alter the entire value chain. And it’s in our own best interest to have a hand in this transformation. Open systems But hasn’t digital technology been part of the automation industry for 30 years? Hasn’t Endress+ Hauser used highly automated production systems for a long time now? Doesn’t every measurement point have a chip that captures, stores and forwards information? What is so new about the much-vaunted ‘Internet of Things’ and what causes ‘Industry 4.0’ to be hailed as revolutionary?
Two things, actually. For one, connectivity is reaching beyond enterprise borders for the first time. It’s penetrating every business, production and automation process, from The Internet of Things: how manufacturing and digital information technologies are converging
Raw material pricing/ stock exchange
Raw material storage
Smart supply network Continuous optimization of the product flow in line with supply and demand Raw material storage
Traffic flow
optimization Optimized energy supply and consumption
Supplier
Raw material storage Self-monitoring inventory Smart Grid
Intelligent transportation units
the field device to the customer’s ERP system (SAP). Whereas today’s information flow remains heavily fragmented due to system boundaries and with some tasks still being completed manually, the Smart Factory of the future will automatically collect and analyze all of the marketing and operations data and distribute it to the right places (see graphic).
Secondly, connected devices supply enormous amounts of data that, when intelligently analyzed, open the door to a world of new possibilities. “The question at the moment is, how do we take this data and generate information from it that creates a benefit which the customer is willing to pay
The Internet of Things: how manufacturing and digital information technologies are converging
Cloud Information about the entire value chain – data is available to everyone at all times Office/Management Continuous information flow, extensive data analysis Material planning (availability) Production planning (time, costs)
Asset monitoring Raw material costs Availability
Delivery costs
Controlling Marketing Logistics optimization (delivery time) Production optimization (efficiency)
HR ERP System Customer Tailored products, integrated engineering
Order processing Resource planning Life Cycle Management
Smart Factory Manufacturing system organizes production, maintenance and logistics on its own Data capture
Intelligent components Products communicate Production planning and quality management (MES)
with the system and visualization (SCADA)
Mobile workforce
Predictive maintenance
Modular system with intelligent sensors and actors Higher efficiency due to flexible, self-operating production processes Transportation Intelligent logistics maximize on-time delivery
Warehouse Softwaresupported warehouse logistics
for,” says Matthias Altendorf, CEO of the Endress+Hauser Group. Sensors and software not only provide information about the status of a process, they can also calculate when is the best time to perform maintenance, or explain why more resources are being used on a certain day.
The instrument data and the customer’s operational data can be coupled with external information. That means upto-date consumer data could control the product inventory, stock market prices could help optimize purchasing, or an intelligent logistics system could incorporate current transportation costs and a road condition report directly into the order processing system. Opportunities and hurdles Is all of this only a future vision? Hardly. Much of the necessary technology already exists: wireless networks, low-cost sensors, apps and intelligent industrial software. Innovative enterprises as well as government-funded pilot projects are currently working to gauge what the factory of the future might look like. It’s a place where machines accept orders, request resources, call the service technician when needed, make documents available to the right system at the right time and independently determine which product has to be manufactured next so that all orders are processed as quickly, efficiently and cost-effectively as possible. As a result, products are
Michael Ziesemer, COO of the Endress+Hauser Group
manufactured more flexibly and in smaller batches, delivery times are reduced and equipment is better utilized.
All of this can happen only if the linear manufacturing chain is transformed into a sort of production community, communicating via a ‘cloud’ that ensures every piece of information is always available to every participant at the same time. There are still plenty of hurdles to overcome in the areas of interfaces, data security and standardization. And this is where Endress+Hauser is not the only organization looking up to higher powers.
Easy integration “The automation industry is not big enough to establish its own standards,” admits Matthias Altendorf. “The much bigger IT industry is charting the course here, for example with wireless LAN, Bluetooth and Ethernet standards. Our focus must be on providing the can be easily and securely integrated into the digital landscape.”
The more measurement points are installed, the more value an integrated approach brings. “No customer wants to set about analyzing 500 signals. They want us to make their lives as simple as possible,” is how Matthias Altendorf puts it in a nutshell. This requires software that not only converts signals into individual information, but also links the data from every level of the process and integrates it directly into the customer’s ERP system via interfaces.
More intense cooperation is needed to deepen and expand the acquired information. “Our very long and productive cooperation with SAP illustrates how valuable such a partnership can be,” says COO Michael Ziesemer. Our specialized know-how is a good foundation, but it offers no guarantee best, most innovative measurement instruments, which
for sustainable success. “Google is already probing the field of building automation,” says Michael Ziesemer who adds that “it’s not because they could build a furnace. It’s because they know how to make money from data! We have to examine this area more closely and learn a lot more.”
Knowledge from data The goal is to generate even more information from the data and use it to develop new services. “It should not come to the point where our instruments are busy collecting data while others build a business around
Industry 4.0: The fourth milestone in the evolution of production
First industrial revolution Water- and steam-driven mechanical manufacturing systems Second industrial revolution Mass production through the division of labor with the help of electrical power Third industrial revolution Utilization of electronics and IT for further manufacturing automation Fourth industrial revolution Cyber-physical systems, Internet of Things
1784 First mechanical weaving loom
1800 1870 First assembly line, meat packing industry in Cincinnati, Ohio 1969 First programmable logic controller (PLC), Modicon 084
1900 2000 Today
analyzing it,” says Michael Ziesemer. Data is considered the gold of the digital world and with standard interfaces, even third-party providers can prospect these virtual mines with their own services.
Michael Ziesemer confesses: “We can’t prevent this from happening. We have to be faster and unafraid to drive forward the development of new technologies, even if some of them don’t pan out right away.”
Where does Endress+Hauser stand today? Our products are already becoming more Internet-capable and some measurement instruments have had built-in Ethernet/IP communications for years. With SupplyCare, CompuCal and W@M for instance, Endress+Hauser has already developed important building blocks capable of exchanging information with peer systems. With the goal of integrating sub-systems into a single overall platform, we also developed the Business Process Integration (BPI) concept, which takes over the responsibility for processing and managing data flows.
Other innovations are in the pipeline, such as ‘Power over Ethernet’ for two-wire technology or the advanced physical layer technology developed in cooperation with Pepperl+Fuchs: a plug-and-play approach that automatically and seamlessly configures the software environment for a device, without a mouse click, as soon as it is plugged in. “Compared to existing digital buses like Profibus or Fieldbus, this is a major step forward,” adds Michael Ziesemer.
Step by step Given that digital technology will continue to gain importance in the field of measurement and automation technology, additional steps will follow. Where will this lead to? Will Endress+Hauser gradually migrate away from process automation with these data and information services? Michael Ziesemer doesn’t think so. “I see these services becoming more like another aspect of automation technology. After all, we are still serving the same customers and the same systems, but it’s our services profile that will undergo a significant change.”
As a leading full-range provider, Endress+Hauser has no reason to fear the future. A solid foundation is in place so we can excite customers with quality and innovation, even in the Smart Factory. “We have advanced relatively far with digital communications and I’m convinced we can effectively manage the digitization of our device world,” says Matthias Altendorf. “The more difficult part of the challenge is developing a new business model and making use of the data so that our customers will be able to manage their businesses even better.” What does the Internet of Things mean for …
… production? Digital technology established itself in the Production Centers long ago. Nevertheless, becoming more linked-in to customers and suppliers will lead to increased flexibility and efficiency. The transition from development to production will also become faster and simpler. The product – configured on-screen – knows from the start what it eventually wants to be. It controls its own manufacture and organizes all of the necessary work steps. To some extent, this is already in place today. Calibration once required reading the serial plate on the device. Today it only requires scanning the barcode.
… sales? This area will undergo a change in the coming years as well. The Salesforce.com platform is already bundling customer data in a new way, so that the data generates information which is accessible around-the-clock from anywhere in the world. The significance of sales channels like E-direct is also on the rise. Customers have a growing interest in being able to select and individually configure increasingly complex products. “Personal customer service is one of our strengths and that's our success model,” says Matthias Altendorf. “In the future we also have to create digital intimacy like Amazon and Apple are doing.”
… the employees? Does everyone have to become an IT specialist? Certainly not, but continuous training and education and lifelong learning are important topics. It’s a matter of give and take. Training and education programs must be made available, but they also have to be taken advantage of. A good working atmosphere also helps. Those who are satisfied with their jobs are also happy to support changes. Creativity and responsibility will become more important in a digital and connected workplace.
… the services business? Every Endress+Hauser instrument must be capable of communicating with the Internet. The web-based system allows us to make all information and documentation available to everyone who needs it. The data we acquire can be used to optimize the life cycle of a system or a device, which at the end of the day leads to better system availability. Matthias Altendorf: “We must position our services business so that we can offer customers more information in the future they are willing to pay for.”
… the Endress+Hauser brand? The brand stands for quality and in a digital world it will take on additional importance. Wherever customer contact shifts to a virtual space, a good name counts even more. Matthias Altendorf: “When people move around the Internet anonymously, a trusted brand or provider plays an enormously important role.” Because the information flow is so rapid, data and information must be handled with the utmost care.