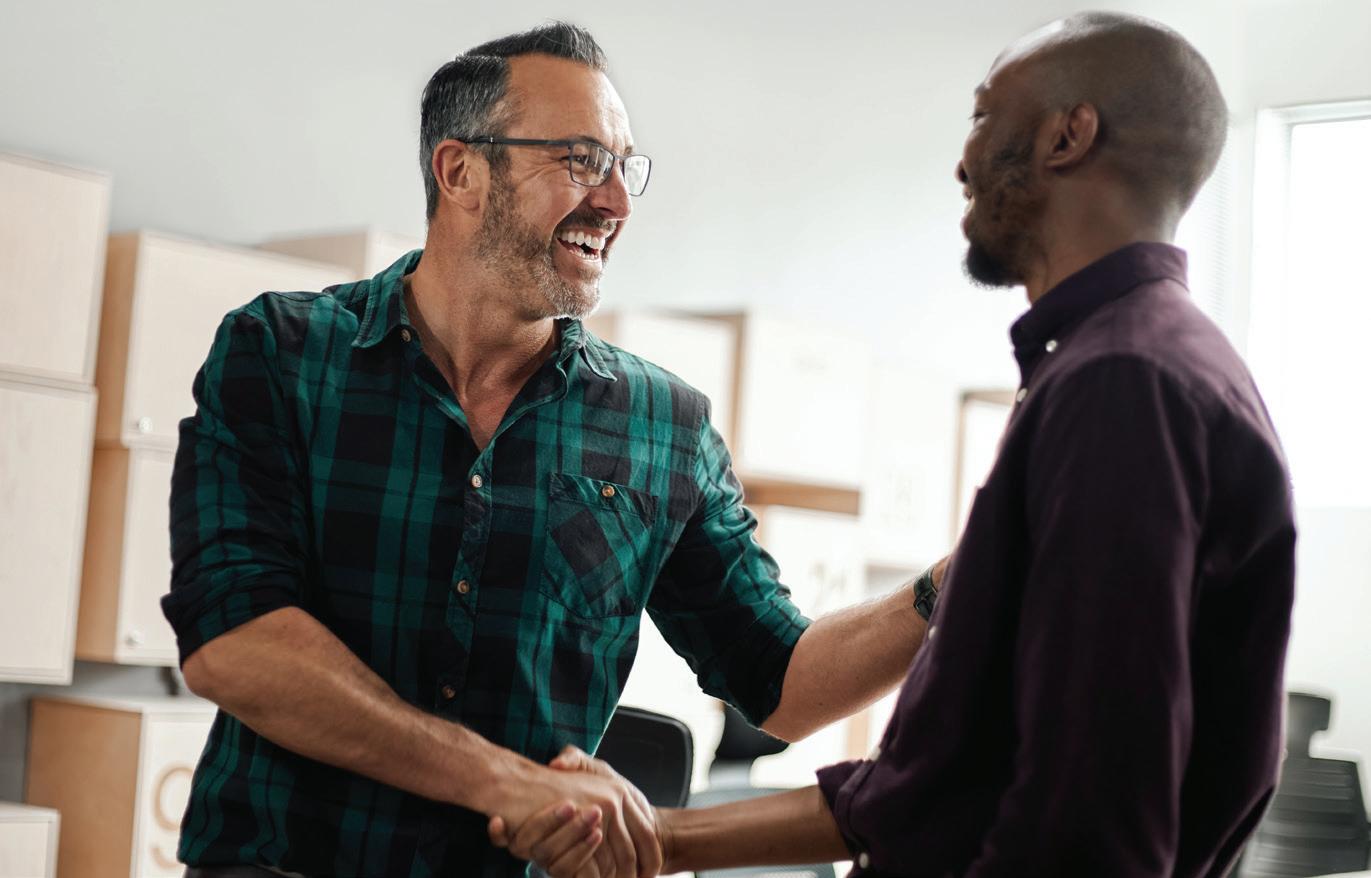
12 minute read
Rajan Rajendran
Recruit the next generation of HVACR professionals and end the workforce shortage.
BY RAJAN RAJENDRAN
Among the many challenges facing the HVACR industry today, perhaps none poses a more significant threat than the growing shortage of qualified service and maintenance technicians. According to recent statistics, 80,000 HVACR technician jobs are currently unfilled — representing 39 percent of the total industry workforce. At the same time, the industry is losing an estimated 20,000 technician jobs per year due to the retirement of an aging workforce or basic career attrition rates.
In an era of emerging system architectures, technologies and refrigerants with low global warming potential (GWP) — especially within the commercial refrigeration sector — the need for qualified technicians is greater than ever. Emerson has long been a champion of looking for ways to reverse the technician shortage, collaborating with vocational schools, helping to shape curriculum, and supporting students along their HVACR career journeys.
But solving this problem is an industry-wide obligation that will require the participation of all stakeholders — not only the input of contracting companies, manufacturers, end users, wholesalers and trade associations, but also the perspectives of educators, adjacent industries and government agencies. Fortunately, awareness of the problem’s scope continues to grow as our industry looks for new ways to solve it.
LOCAL SUPPORT
Industry stakeholders agree that one of the most effective strategies for recruiting the next generation of HVACR technicians and beginning to change perceptions is to engage locally by supporting vocational schools and technical colleges.
Combined with incentives from state governance, industry-sponsored scholarship programs and preapprenticeship opportunities, we have seen tangible examples of how this local model can inspire a lifelong passion in HVACR careers.
Emerson’s Helix Innovation Center located near the University of Dayton campus, often interacts with students enrolled in nearby Ohio vocational schools. It recently offered a pre-apprenticeship opportunity to Nicholas Didier, a student attending the Miami Valley Career Technology Center (MVCTC) near Dayton.
His experience demonstrates how private companies, industry and local governance can combine to inspire, educate and support our youth in the discovery of HVACR careers.
As a high school senior enrolled in the Heating Ventilation and Air Conditioning (HVAC) Program at the MVCTC, Didier was interested in learning more about the basics of refrigeration and getting hands-on HVACR field experience.
But what he got from his time at The Helix was a much more in-depth understanding of the challenges facing our industry, a greater overview of the service profession and the desire to explore system design.
His responsibilities at The Helix included building, prototyping and developing products, but he was particularly inspired by listening to staff conversations about current industry challenges and learning new information about the opportunities available in HVACR-related professions.
“I love to learn the mechanical aspects of a trade, and my time at The Helix reinforced my decision to pursue a career in HVACR,” Didier said. “The heartbeat of our country is in skilled trades, and the HVACR technician shortage provides an opportunity for students like me to have an exciting career.”
Didier’s passion and accomplishments also helped him to win a new Ford Ranger truck and a $1,000 scholarship from the Today’s Opportunities Offering Lifetime Skills (TOOLS) program — a scholarship sponsored by the Ohio Valley Chapter of the Associated Builders and Contractors (ABC). Didier said he plans on using the money to purchase tools for the HVACR technician trade and further his education.
In addition, Ohio Lieutenant Governor Jon Husted, who serves as the director of the Governor’s Office of Workforce Transformation, recognized Didier’s exemplary efforts when he recently visited local career centers.
Husted took the time to speak with students in various programs about their decisions to attend vocational school and/ or achieve college credits. He emphasized the career paths available to these students — with and without a college education — and then detailed the state’s upcoming initiatives to promote career, technical and vocational schools.
BRIGHTER FUTURE
Helping to solve the HVACR technician shortage is just one way to ensuring a brighter future for our served industries. Promoting science, technology, engineering and math (STEM) educational programs can help prepare the next generation of critical thinkers and problem solvers.
Today, the urgent need for skilled technicians requires the type of local level engagement to raise awareness of not only the growing problem, but also present evergreen opportunities for young people seeking a viable long-term career in lieu of a four-year college education.
Dr. Rajan Rajendran is the vice president, systems innovation center and sustainability at Emerson. He has worked at Emerson since 1990 in various capacities: first as a research engineer; later as manager in the scroll compressor product development group; and as a director for 10 years prior to his current role. Dr. Rajendran is also the director of The Helix, Emerson’s research and innovation center located on the University of Dayton’s campus. He represents Emerson in its communications with various policy and industry organizations, such as the U.S. Environmental Protection Agency and the U.S. Department of Energy, among others. For additional information, visit climate.emerson.com.
Although it’s difficult to pinpoint the cause of the declining interest in HVACR professions over the past decades, industry insiders attribute it to a variety of misperceptions and preconceptions, namely: HVACR professions are unglamourous and/ or not important. Workers within HVACR professions do not utilize cutting-edge or state-of-the-art technologies. There is an overall cultural devaluing of trade professions compared to the more widely accepted value of a traditional four-year college education. Some Americans believe that HVACR professionals do not make a competitive wage or have long-term career path opportunities. For high-school aged students considering a career path or adults pursuing a career change, there’s no question that these long-held misperceptions have gotten in the way of recruitment. And with potential young entrants inundated with social media streams that often present unrealistic, idealized views of professions (and the four-year college experience), it can be difficult to change these perceptions. But upon closer inspection, it takes relatively little effort to dispel these myths. In fact, HVACR technician jobs check important boxes for many professionals that four-year college degrees simply cannot. It’s important for all industry stakeholders to understand, highlight and promote these differentiating factors in order to paint a more realistic — and positive — picture of modern HVACR professions. These proof points not only form effective counterarguments to common misperceptions but could inspire students and those currently in the labor pool to reconsider a career in HVACR: Have a meaningful career that makes an impact — HVACR professionals are on the front line implementing new environmentally friendly solutions and technologies that will play an integral role in making the world a better place to live. Work with cutting-edge tools and technologies — Modern refrigeration and AC applications utilize advanced controls, software and remote diagnostics capabilities. Achieve job security — With little competition for available jobs, HVACR professionals are virtually guaranteed employment and enter into a field with both long-term security and growth potential. Earn while you learn — HVACR technicians can earn a competitive wage with a two-year vocational certification and have the option to augment the certification process with on-thejob training in apprenticeship programs.
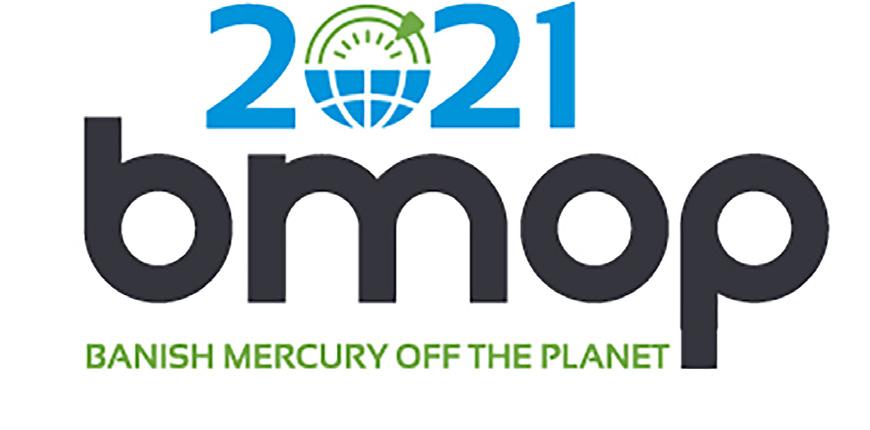
Calling all TRC/HARDI Wholesale Members. The 10th annual BMOP competition is going on now! Return your filled recycling containers by October 31 to compete. Learn more at thermostat-recycle.org/bmop
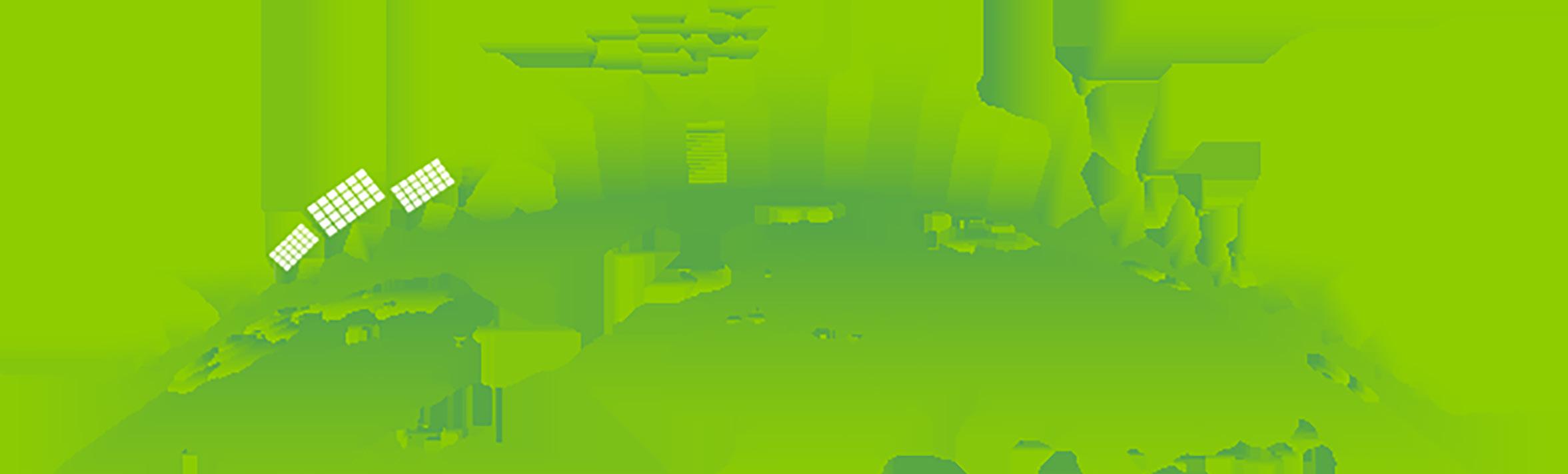
BY RUTH KING FINANCE
One Easy Way Your Technicians Can Steal from You
On Friday afternoons you should get a weekly cash flow report from your bookkeeper. Attached to the weekly cash flow report should be an aged receivables and aged payables report.
Assuming the invoicing and entering of supplier bills is current, the weekly cash flow report should take less than 15 minutes to compile (a sample report is shown in Fig. 1).
Here’s the easy way a technician can steal from you:
A contractor was looking at the aged receivables report and noticed several service customers who, according to the report, hadn’t paid for the service at their homes. This was strange because the company’s residential service policy was COD, and the technicians were supposed to collect at the end of each call.
The company owner called the customers who were on the receivables report. He first made sure that the service was performed properly and the customers’ systems were keeping their homes cool. He then asked, “Did you pay the technician at the end of the call?”
Please notice he did not ask, “Why didn’t you pay for the service?”
Every customer he called said yes, they paid the technician at the end of the call.
He then asked how they had paid for the calls. All said by credit card. He explained that the company didn’t have a copy of the receipt. He asked if the customer would be willing to send the receipt to him.
All the customers sent their receipts.
When he looked at the receipts, he noticed they all had his company’s name on it. What he also saw was that the credit card was not being processed by his normal credit card company.
He continued the investigation and found that one technician had performed all these service calls.
What had the technician done?
He applied for and got approved for a Square credit card in the company’s name, with the company’s Federal ID number and his bank account. So, the technician swiped the card in the field using his Square rather than the company’s credit card swipe device.
The owner called the police who investigated and arrested the technician. The technician was charged with seven counts of Federal crimes including money laundering, ID theft and more.
The amount the technician stole? Around $4,000. Imagine being in jail for a $4,000 theft.
The company owner was thankful he reviewed the weekly cash flow reports and the aged receivable and payable reports each week. He caught the thief quickly before a lot of cash was stolen.
I’m not saying that $4,000 is insignificant. What would have happened if this technician had stolen for months rather than weeks? The theft could have been tens of thousands of dollars more.
Here are seven things you can do to help prevent this theft from happening to you: 1. Get a weekly cash flow report and the aged receivables and aged payables reports to back up the report. Look at the aging reports and see if things don’t look right. 2. If the aging reports don’t look right, investigate immediately. 3. Assign a person, preferably not your bookkeeper, to ensure that all credit card receipts match the customers’ invoices. 4. Match the receipts against the daily reports from your credit card company.
If some are missing find the missing credit card receipts. 5. Have the same procedure for checks.
It’s also easy for a technician to tell a customer “I’ll fill out the company name” and put his own name in the
“Pay to the order of” line. And, if he deposits the checks through an ATM, this is almost never caught by a bank. 6. If a technician is stealing from you with their own personal credit card device, have that person arrested. If you don’t, that technicians will find another job and steal from another contractor. 7. Remember that it is easy to get your company’s Federal ID number — it is on the W-2 statement that the employee receives each year. If someone calls to verify your Federal ID number, however, it is probably a scam.
Never give that information out!
Thankfully this theft was caught quickly and because of the weekly cash flow report review. This is one thing that you can do to keep the honest people honest and catch thieves quickly. u

Ruth King has more than 25 years of experience in the HVACR industry and has worked with contractors, distributors and manufacturers to help grow their companies and become more profitable. Contact Ruth at ruthking@hvacchannel.tv or call 770-729-0258.
The Next-generation R-22 Drop-in Refrigerant Blend.
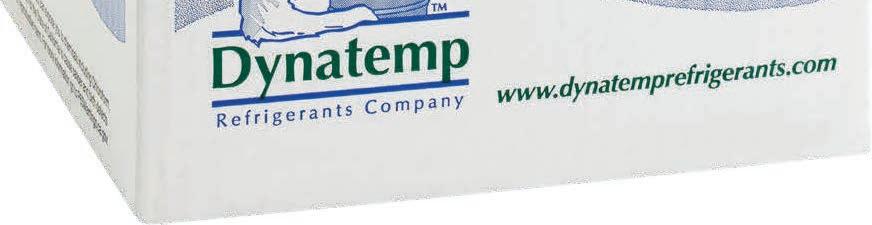

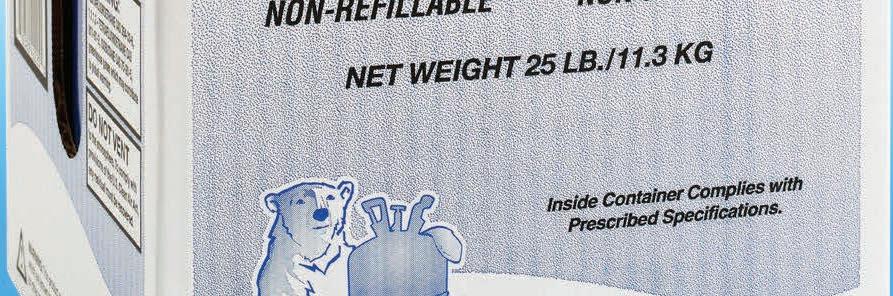

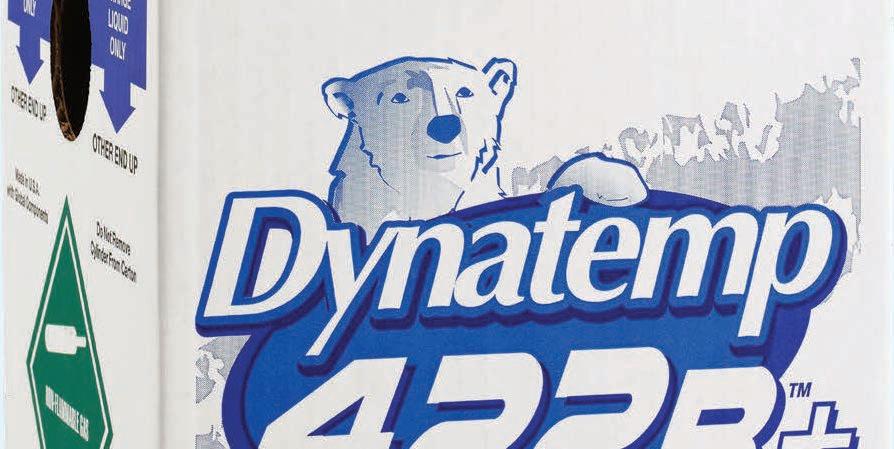
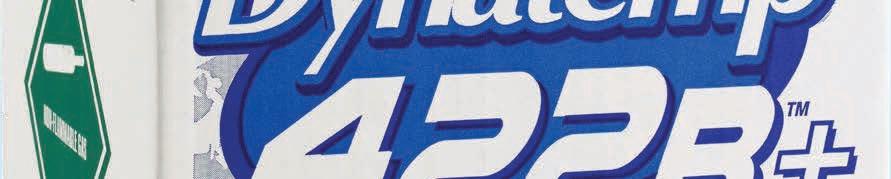
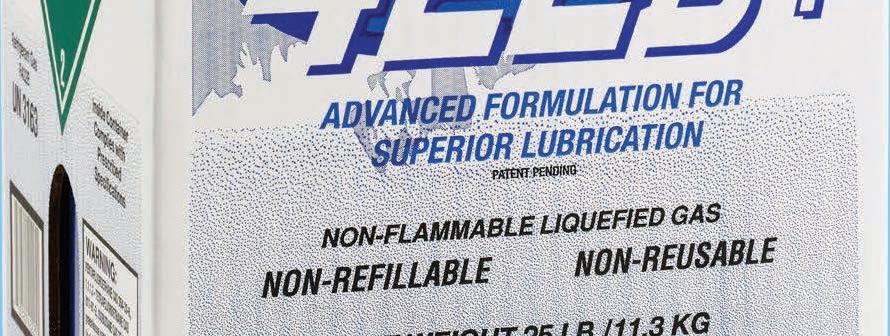

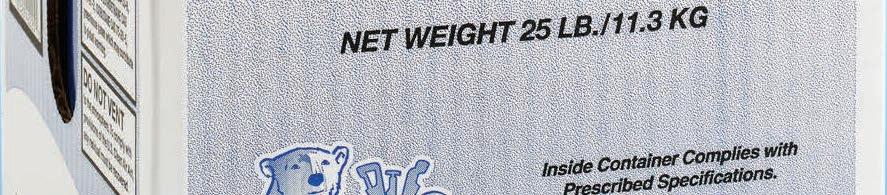
R-422B+TM is the superior R-22 replacement on the market today. An exclusive patent-pending formula, superior compatibility, lower price point, and manufacturing in North Carolina makes this the
Gold Standard for R-22 substitutes.


FEATURES & BENEFITS
The Dynatemp Advantage
Dynatemp complies with all EPA Regulations under the Montreal Protocol and Clean Air Act.
All Dynatemp refrigerants are analyzed to ensure AHR-700 specifications. n Dynatemp 422B+™ is the superior, low-cost, next-generation R-22 substitute manufactured in North Carolina, USA.
n Dynatemp 422B+™ is built with lubrication technology that enhances the miscibility and circulation of lubricants found in existing R-22 equipment.
n The pressure-temperature characteristics of Dynatemp 422B+™ are nearly identical to R-22, R-421A, and R-422B.
Contact us today, or visit our website for additional details on EPA regulations, trade matters and product specifications. n Dynatemp 422B+™ is a Universal Substitute that can replace R-22, R-421A, R-422B, R-422D, R-438A, and R-407C without an oil change-out or equipment modification, in most applications. n Dynatemp 422B+™ is an EPA SNAP approved, non-flammable, low-cost R-22 alternative.
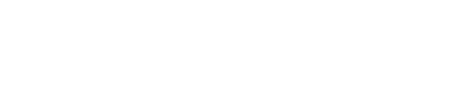
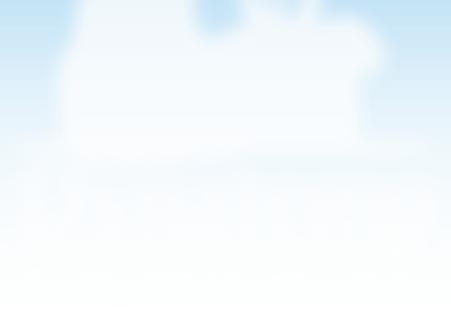
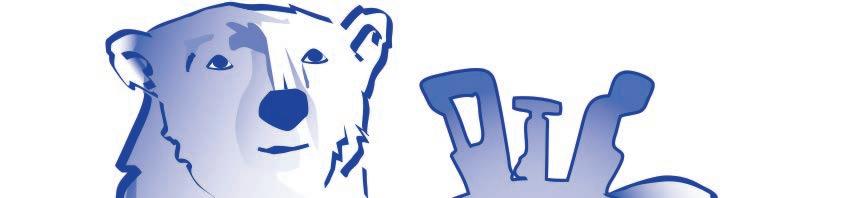
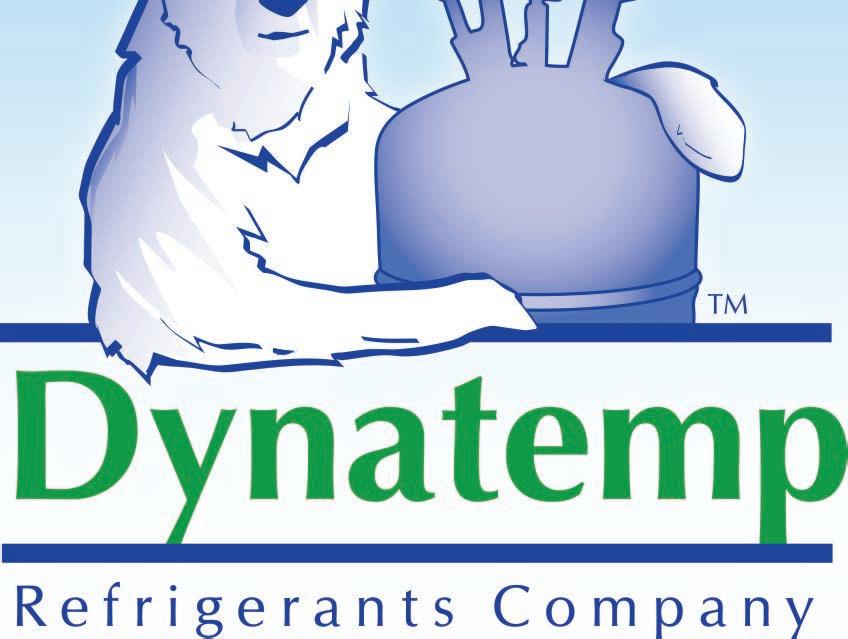
www.DynatempRefrigerants.com
P.O. Box 1206, Clayton, NC 27528-1206 Phone: (717) 249-0157 Toll Free: (800) 791-9332 Fax: (717) 249-9043