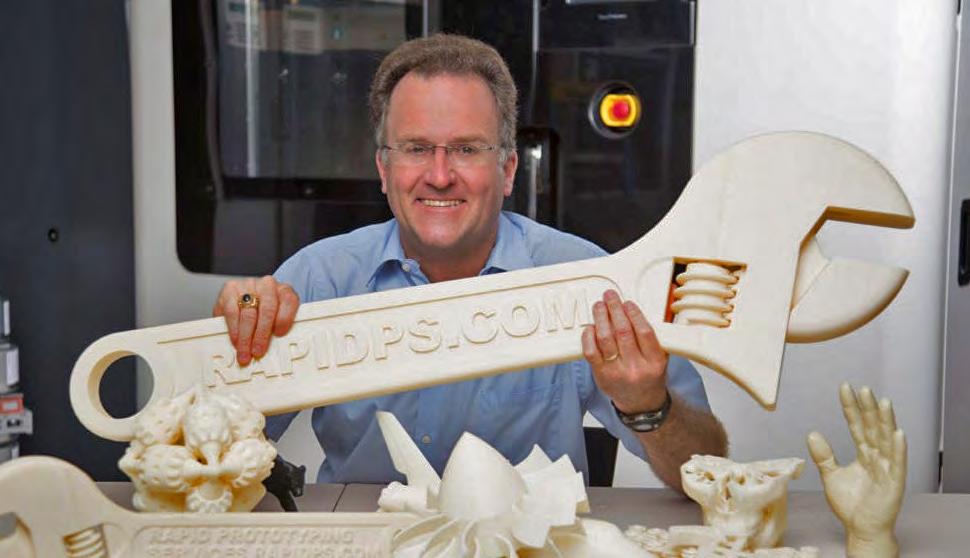
6 minute read
3D WIZARDRY
3D Wizardry Rapid Prototyping Services Gives Businesses Secret Superpowers
BY MEAGHAN BRANHAM
Advertisement
When the Scarecrow, the Tin Man and the Cowardly Lion set off on the Yellow Brick Road with Dorothy, they didn’t know exactly how the wizard would grant their wishes — they just had faith that the man behind the curtain would make it happen. When clients come to the door of Ken Brace’s 2,500-square-foot studio, they must feel that same excitement and hope — only the wizard behind the curtain here doesn’t keep his methods a secret, and he always delivers.
The truth is, 3D printing might be capable of more than what even the great and powerful Oz could dream up. From printing with biomaterials in the medical field, to revolutionizing manufacturing by making processes more affordable, to printing structures in space that couldn’t survive the stress of a launch, those behind the scenes in the 3D printing industry are turning visions into realities every day.
In Central Florida, as the owner of Rapid Prototyping Services, Brace is granting those wishes out of his Satellite Beach-based studio, where, with just one employee staffing $1 million worth of equipment, the machines on the floor run each day, sometimes 24/7, to propel industries and business in our own backyards and beyond.
Medical
While the medical industry is still exploring and discovering the possibilities of 3D printing, those at the forefront have already made advancements so incredible they seem to come straight from the pages of a science fiction book.
Bioprinting, for instance, allows the use of biomaterials like living cells to print everything from living tissue to blood vessels and even whole organs. In September, it was reported that scientists from Saga University and Kyoto University in Japan were able to 3D print cartilage using stem cells, according to 3DPrintingIndustry.com. Recently, researchers at the Complex Materials Group at ETH Zurich developed a tool to print custom heart valves using silicon, making a usually expensive and laborintensive process possibly more efficient and affordable.
Brace is bringing those advancements to Central Florida, working with everyone from doctors and surgeons to nonprofits. He has previously worked with Limbitless Solutions, a nonprofit based out of the University of Central Florida (UCF) that creates bionic limbs for children, and Brace has donated his older machines for use in its projects.
He also works with doctors on tools used during their surgeries and procedures. “In one case, I worked with a surgeon who was working on a nasal cavity and wanted to better understand it,” Brace said. “I used the CT scan they had taken of the patient to then create the model of the nasal cavity, and printed that out and sterilized it. He was able to keep that on the table during surgery to help guide him. In cases like that, it’s so rewarding because I’m not just making a part, I’m making a part that helps someone in such an incredible way.”
— Ken Brace
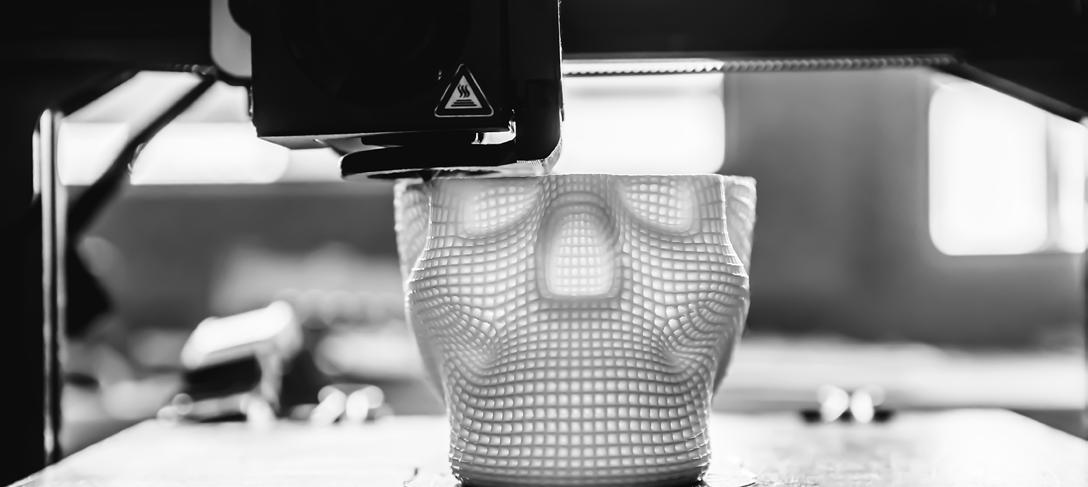
Education
In addition to donating older printers to nonprofits based out of universities, Brace often donates them to the local school district for use in classrooms and labs. During summers, he dedicates some of his time to training teachers on how to use the equipment in their classrooms.
The equipment can have far-reaching effects in schools. Since each design must start with a 3D CAD (computer-aided design) file, the use of the technology in class encourages students to be more actively involved in science, technology, engineering and mathematics (STEM). And when it comes to the subjects that can be enhanced with 3D printing, the possibilities are endless. Chemistry students can print out and study models of molecules, and history students can replicate and study ancient artifacts.
“And now, since the teachers all know me,” he laughed, “they’ll call me up and send their students over when they need pieces created for their science projects.” Each year, when science fair season gets into full swing, Brace allows students to use the equipment at his shop to help them go above and beyond with their projects.
“Some of them are thinking pretty outside the box,” he said. “One of the groups I’m working with is designing a robotic hand, and working on programming it to open and close. One student is doing the mechanical part, the other is doing the electrical.” Brace even introduced the students to Limbitless in the hopes that the company can help the next generation find new solutions. Manufacturing
The machines used in the process and on Brace’s floor don’t require constant supervision or multiple handlers like some manufacturing methods. At Rapid Prototyping Services, Brace often operates them overnight, only checking in if the machines alert him to an issue. That reduction in cost and labor means using 3D printing as part of the manufacturing process allows for far more freedom and flexibility. In fact, the machines are often used for a process called “low-volume manufacturing,” creating small quantities of a product.
Brace has jumped in for clients like this before. While working for local company FARO Technologies, RPS became an integral part of a new product launch. After the product was designed by the team and prototyped by Brace, things took an unexpected turn.
“The marketing team was getting orders for the product before they even had time to make it,” Brace said. “And when they realized they couldn’t get the parts they needed for six weeks, they came back to me. The materials I was using for that prototype were identical to the materials in the product. We were delivering 500 to 600 pieces as the orders came in, and I was running the machines 24/7 until they could get where they needed to be to mass produce. The technology is at a stage where we can make really high-quality parts when it’s needed for projects like this.”
Aerospace
Even with the impressive amount of ground already covered in Brace’s portfolio, there are still some wishes of his own he hopes to grant someday soon.
He’s already had a hand in some extraterrestrial projects, including work done with Lockheed Martin on the Orion capsule launched in 2014. As of 2021, and with space travel and space tourism taking off more quickly than most could have expected, he is ready to delve further into the possibilities of 3D printing in space.
“I’m really excited about commercial space and what they’re doing at the Cape,” he said. “I hope once that starts going, I can be more involved with SpaceX and Blue Origin. I think there are a lot of possibilities for us to service them really well.”
Whether in Central Florida or far above it, the businesses Brace services are taking off thanks to his work. It’s a privilege, Brace said, to be a part of so many exciting and innovative projects in so many realms. No one can say for sure just what the parts produced in Brace’s studio could one day look like, or one day do for the people they reach — a new way to learn, a closer look at the cosmos or maybe even, like the Tin Man always wanted, a real beating heart.