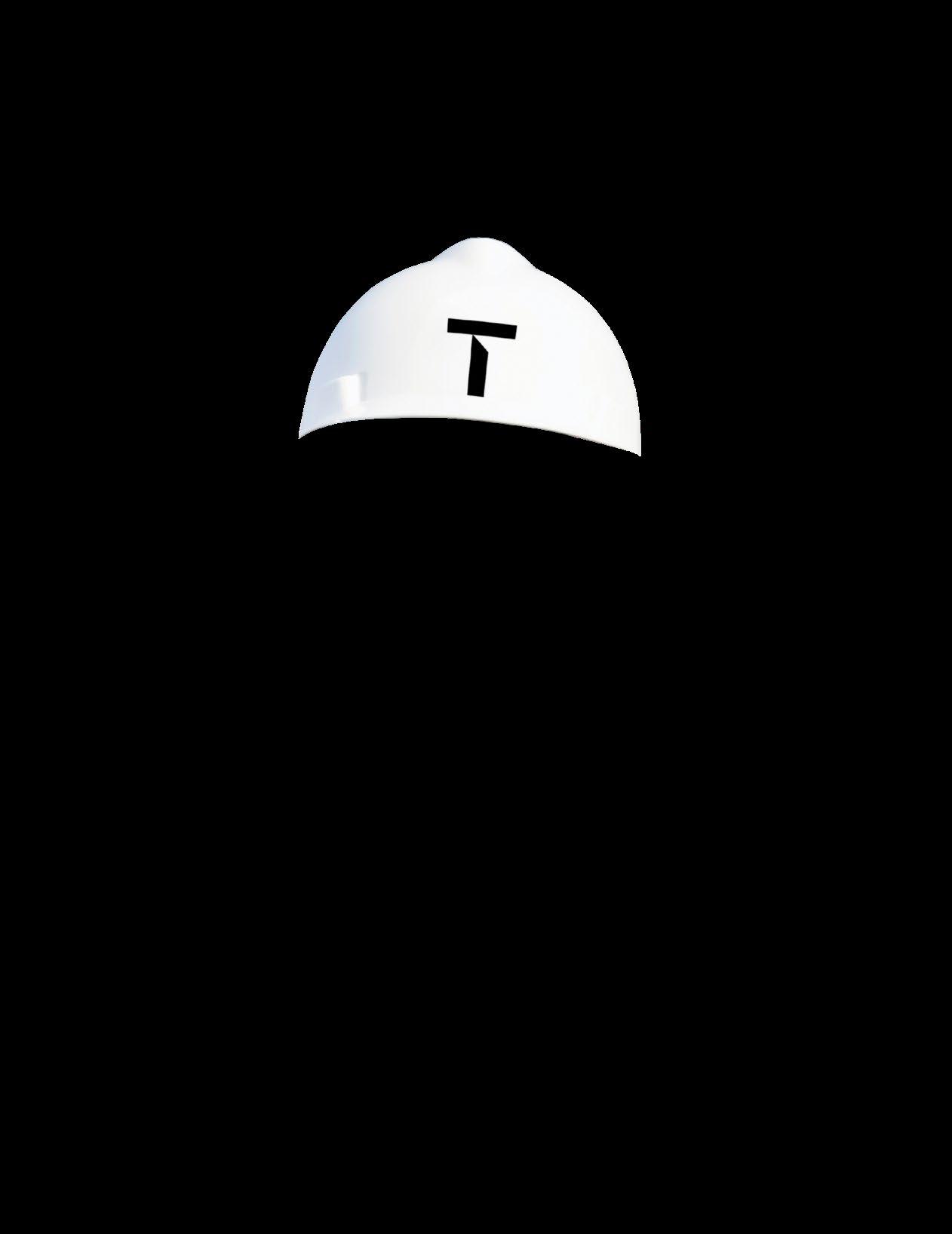

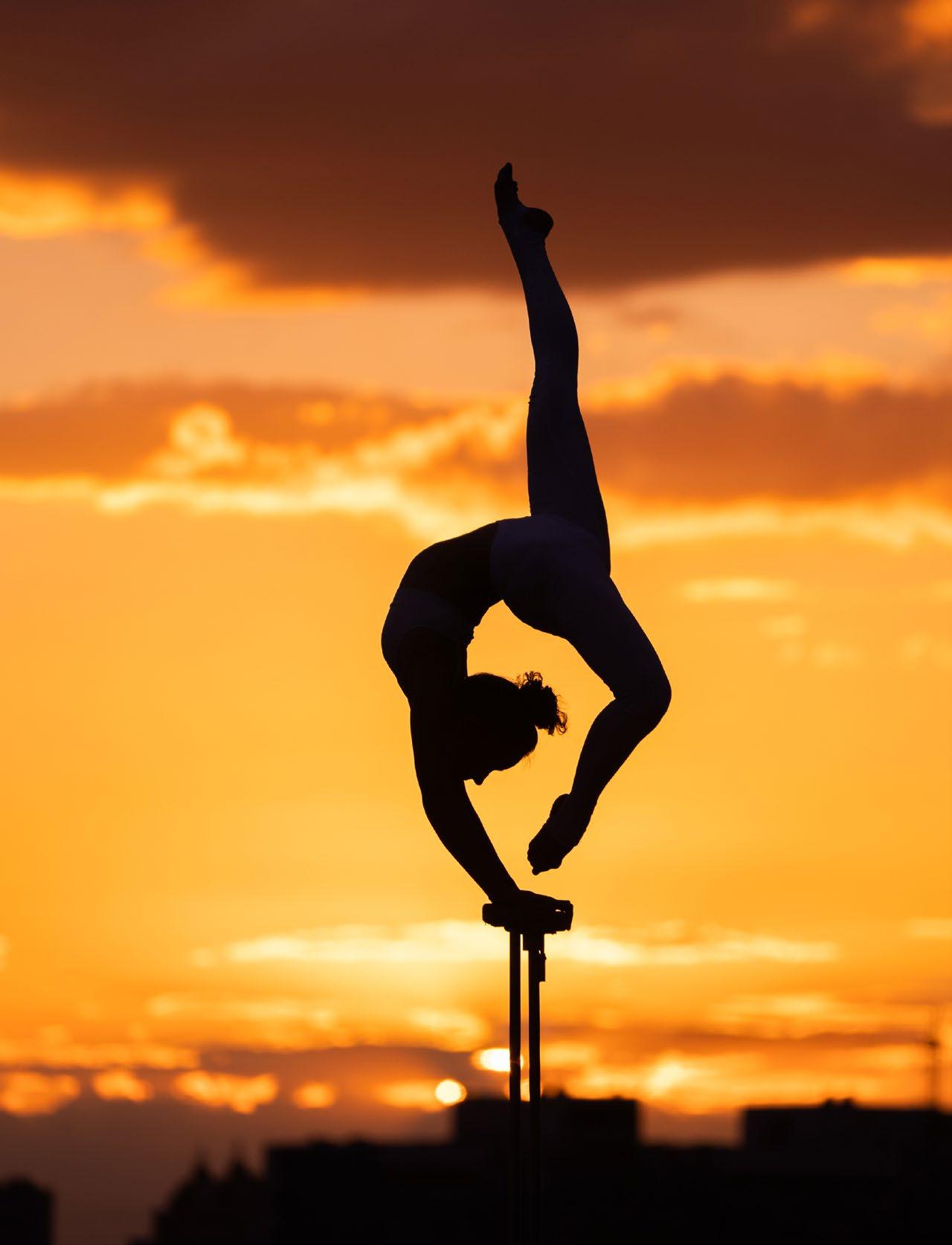
CynerSorb®, Celite® and Harborite® Our range of mineral filter aids and filterable adsorbents allows dirtier fats and oils to meet feedstock specifications of renewable diesel, biodiesel and other olechemical plants.
ANY QUESTIONS? Contact us at: www.imerys.com marketingna@imerys.com Linkedin/@imerys
Headquarters and manufacturing in China with a global presence.
Oleo-X’s technical differentiation and advanced chemistry produces the industry’s highest quality feedstocks that are so pure and so clean, our customers call it “liquid gold.” To learn more, visit www.oleo-x.com Contact us at oleoxinfo@backbaycommunications.com
Discover the forefront of renewable fuel feedstock production with Oleo-X’s exceptional facility located in Pascagoula, Mississippi. Utilizing state-of-the-art technical innovation, advanced chemistry, and rigorous testing protocols, we are leading the industry in delivering premium-grade renewable fuel feedstocks. Our impact in the renewable fuels industry is transforming poultry fat and other difficult-to-treat oils into the industry’s purest feedstocks.
Our advanced process generates bright and clear oil for premium quality you can see.
Laboratory testing of our product confirms that our feedstock has the lowest phosphorous, metals, and catalyst-damaging reactive siloxanes on the market. Our feedstocks have wider cold flow handling characteristics and do not degrade in storage.
The benefits of Oleo-X’s premium-quality feedstock ultimately accrue to our customers, who enjoy longterm cost savings and enhanced returns through:
• Substantially reduced equipment maintenance
• Adding several years to RD/SAF unit catalyst life and enhanced liquid yields during operation
• Reducing revamp costs for RD/SAF units due to feedstock compatibility with metallurgy used in legacy petroleum hydrotreaters and hydrocrackers
• Creating low carbon intensity-score RD/SAF
ADVERTISERS:
For advertising sales please call 218-745-8347, email editor@biobased-diesel.com or visit our website at www.biobased-diesel.com.
EDITOR AND PUBLISHER:
Ron Kotrba editor@biobased-diesel.com
GRAPHIC DESIGN:
Doug Conboy
Raised Brow Productions
MAGAZINE PRINTING:
Century Publishing
By Bárbara Sánchez González and Dario Altera
Biobased DieselTM is published by RonKo Media Productions LLC. Subscriptions are free of charge to those in the United States and Canada. To subscribe, visit biobased-diesel.com and fill out the contact form in the website footer. For subscribers outside the United States and Canada, a digital version of the magazine will be emailed. For those located outside the United States and Canada who wish to have a print version of Biobased DieselTM mailed, please email editor@ biobased-diesel.com with the request. A nominal postage fee may be required. For mail correspondence, write to: RonKo Media Productions PO Box 86 Warren, MN 56762
All rights reserved. No part of this publication may be transmitted or reproduced in any form without written permission from the publisher. The information contained within has been obtained from sources believed to be reliable. Neither the publisher nor
Appropriate
By Maria J. L. Perez and Milica Folic
Brandon Day
Kristof Reiter
Welcome to the largest edition yet of Biobased Diesel™. Upon launching in Summer 2021, the magazine featured 40 pages and five editorial contributions. Today, I am proud to say the issue you hold in your hands is 64 pages with more than a dozen articles from the top experts in their respective fields. This growth is not unlike that of the industries and markets this publication serves.
As I was putting this issue together—specifically the Information section on U.S. biobased diesel trade—I discovered an unwelcomed surprise. Certain biodiesel-export data on the U.S. Energy Information Administration website has been dramatically revised down. I am particularly referring to U.S. biodiesel exports to Singapore in 2022.
Based on EIA data, last year I reported that the U.S. exported 76.1 million gallons of biodiesel to Singapore in 2022. When I saw this isn’t what the agency reports for that same 12-month period now, I had to scratch my head. Thankfully I saved the data set from the year before. While I didn’t have room on this page to list the monthly figures, which are quite interesting, the yearly total of U.S. biodiesel exports to Singapore has been changed from 76.1 million gallons to just over a quarter-million gallons—a whopping 99.7 percent decrease.
I asked EIA about this and the agency said it uses data from the U.S. Census Bureau. At press time I awaited an explanation from the bureau. Meanwhile, I recalled an unsubstantiated rumor I heard in August 2022 about biodiesel tankers coming from Asia, docking in a U.S. port, clearing customs but not unloading, and then sailing back to Southeast Asia where, somewhere at sea, the fuel was transferred to a Europe-bound ship. At the time, I reached out to a contact at the U.S. Customs and Border Protection. We corresponded several times but nothing was uncovered.
For those of you who have been in this business for 15 to 20 years, this may sound reminiscent of the splash-and-dash days. I’ve reached out to several others on this and await more information. Suffice it to say, however, that when you see the 2023 trade data on pages 16-17, total U.S. biodiesel export figures for the prior year used for comparison have been inexplicably and significantly revised downward. Stay tuned to Biobased Diesel Daily® (biobased-diesel.com) for any developments on this topic.
Ron Kotrba Editor and Publisher
The U.S. government issues unpopular SAF tax-credit guidance while global project development continues.
The U.S. Department of the Treasury issued guidance April 30 on the sustainable aviation fuel (SAF) tax credit (40B) passed in the Inflation Reduction Act. Updates to the GREET model were also unveiled. The new model and guidance followed initial approval in December to use GREET once updates were made. The new guidance was criticized for a pilot program requiring SAF made from crop feedstocks to utilize so-called “climate-smart agriculture” (CSA) practices—no till, cover cropping and, in the case of corn-based SAF, enhanced-efficiency fertilizer—to be eligible for additional credit beyond the base $1.25 per gallon. The incentive allows for an extra penny per percentage point of greenhouse-gas reductions beyond 50 percent, up to a maximum of $1.75 per gallon. IRA was signed into law in 2022. The SAF credit is only good for 2023-’24, after which the clean fuel production credit (45Z) goes into effect.
Sen. Chuck Grassley, a Republican from Iowa, said the late and restrictive guidance means crop farmers won’t be able to participate in the SAF market, adding that the GREET model update is a “stupid approach.” Sen. Sherrod Brown, a Democrat from Ohio, said the rule “misses the mark and falls well short of the goal of jumpstarting this new homegrown industry.” Industry stakeholders are working to ensure the 45Z-credit guidance is less prescriptive, more expansive and issued in a timely manner. [BBD]
Valero Energy said a $315 million SAF project at the Diamond Green Diesel plant in Port Arthur, Texas, is progressing ahead
of schedule. DGD is a joint venture between Valero and Darling Ingredients. The SAF project is now expected to be operational later this year. Once complete, the plant will have the optionality to upgrade half its current 470-million-gallon-per-year (mgy) renewable diesel capacity to SAF. [BBD]
Topsoe has signed an agreement for its first SAF project in China with Guangxi Hongkun Biomass to provide its HydroFlex™ technology to produce SAF at the company’s plant in the Qinzhou Port Area Free Trade Pilot Zone of Guangxi. The facility will process 300,000 tons of feedstock per year once complete in 2026. [BBD]
LanzaJet received a $20 million investment from Groupe ADP, enabling continued deployment of its SAF process technology globally. ADP’s investment comes as LanzaJet recently opened Freedom Pines Fuels, the world’s first commercial-scale ethanolto-SAF plant in Georgia [BBD]
Swedish energy company Preem has entered into a loan agreement totaling approximately $262 million with the Swedish Export Credit Corp. and Crédit Agricole Corporate & Investment Bank. The loan falls under the National Debt Office’s “green-credit guarantees” program and is intended to partially fund Preem’s $505 million investment at its Lysekil refinery for renewable diesel and SAF production. Conversion will begin this year and is scheduled for completion by 2027. [BBD]
Haffner Energy is developing a new SAF project at the ParisVatry airport in the Grand Est region of France. Initial production capacity is slated for approximately 10 mgy using the company’s feedstock-agnostic SAFNOCA® technology. [BBD]
Several projects move forward around the world, but one in the U.S. reversed course.
Vertex Energy announced in May that it is pausing renewable diesel production in Mobile, Alabama, in order to pivot back to petroleum refining in the second quarter. The company is using a planned turnaround to load conventional catalyst and bring the unit back into conventional service. The news comes as the company reported its renewable diesel operations generated a gross loss of $10.5 million during the first quarter while its conventional petroleum refining in Mobile generated a gross profit of $37.5 million for the same period. The first-quarter loss follows Vertex Energy missing its renewables output and yield targets in the fourth quarter of 2023 and losing $8.5 million in the third quarter last year. The unit began operations in spring 2023, shortly after which it ran into operational problems during start up. [BBD]
process of starting up. Management expects operations to return to normal by the end of June. [BBD]
The Gothenburg biorefinery, a joint venture between the Nordic energy group St1 and Swedish forest-products company Svenska Cellulosa AB, officially opened in Sweden April 10. Following an extensive start-up phase since the beginning of the year, the $372 million biorefinery is now producing renewable diesel, sustainable aviation fuel (SAF), bionaphtha and bio-LPG. Production capacity is approximately 65 million to 68 million gallons per year (mgy). The plant can use a range of feedstocks including used cooking oil, animal fats and tall-oil fatty acids, the latter from SCA’s pulp-and-paper mills. [BBD]
Repsol began large-scale production of renewable diesel and SAF in April at its industrial complex in Cartagena, Spain. The $271 million plant is capable of producing more than 80 mgy. The company first announced the project in late 2020. [BBD]
As of April, Phillips 66’s Rodeo Renewable Energy Complex in California, near San Francisco, is processing only renewable feedstocks and producing approximately 1.26 million gallons of renewable diesel per day. The site is on track to increase
Plant closures are juxtaposed with increased use and adoption of higher blends.
Chevron Renewable Energy Group recently closed two of its biodiesel plants—a 30-million-gallon-per-year (mgy) facility in Ralston, Iowa, and a 20 mgy refinery in DeForest, Wisconsin—due to what the company described as “poor market conditions.” [BBD]
Across the pond, Argent Energy said in late March it planned to stop production at its biodiesel plant in Motherwell, Scotland. The company said market conditions—imports, regulatory issues and more—have put severe economic pressures on biodiesel production facilities in the U.K. over the past two years. [BBD]
In Bolivia, a start-up ceremony was held March 26 in Santa Cruz de la Sierra for the first biodiesel plant built by state-owned oil company Yacimientos Petrolófilos Fiscales Bolivianos. The 21 mgy facility is located in the Guillermo Elder Bell Refinery. A similar biodiesel plant is being built in El Alto [BBD]
Growmark is partnering with Optimus Technologies through 2027 to test biodiesel in five semi-tractors in Growmark’s Manito Transit fleet as a potential pathway for transitioning the entire fleet to low-carbon fuels. Since the pilot began last summer, thousands of gallons of biodiesel have been used in the five trucks. [BBD]
The Northeast heating-oil industry is on track to achieve goals set forth in the 2019 Providence Resolution to voluntarily reduce greenhouse-gas (GHG) emissions. According to a new analysis by Tom Butcher of the National Oilheat Research Alliance, the industry has surpassed its goal of reducing GHGs 15 percent by 2023, achieving a nearly 26 percent reduction in GHG emissions through a combination of energy-efficiency improvements and increased use of Bioheat® fuel. [BBD]
The Detroit/Wayne County Port Authority in Michigan revealed details on Earth Day of a program to dramatically improve air quality and the health of residents by cutting carbon emissions to net zero by 2040. Immediate actions highlighted in the plan to significantly reduce the port’s carbon footprint include the introduction of biodiesel, which is compatible with most of the equipment used in the terminals today. [BBD]
In Illinois, implementation of a bill to encourage the use of higher blends of biodiesel took effect April 1. The B20 bill raises the bar on biodiesel use by increasing the minimum biodiesel blend level eligible for tax exemption from B11 to B14 and, in subsequent years, B17 and eventually B20. [BBD]
Iowa Gov. Kim Reynolds signed legislation May 10 to increase annual funding for the Iowa Renewable Fuel Infrastructure Program from $10 million to $14 million beginning July 1. The revised program guidelines include an increase in the cap for retail biodiesel projects, now set at $1.75 million compared to the previous $1.25 million. As of January, there were 35 biodiesel retail applications on hold totaling $1.7 million. A new report found a record 68 million gallons of
A long-term trial, more “firsts” and major partnerships top the headlines.
The Global Centre for Maritime Decarbonisation has teamed up with NYK Line to launch Project LOTUS (long-term impact of continuous use of biofuels on vessel operations). This six-month project will trial the continuous use of a 24 percent blend of biodiesel (B24) onboard a short-sea vehicle carrier that will call at multiple ports. While its compatibility with existing engines and bunkering infrastructure makes B24 an attractive drop-in green fuel, NYK Line said concerns about the impact of its extended use on vessel operations remain. Project LOTUS aims to address this knowledge gap by establishing industry guidelines for monitoring engine and equipment performance when using biofuels. This pilot will also evaluate the total cost of ownership of using biofuels. Additionally, it will identify potential challenges and recommend mitigation strategies. [BBD]
Brazilian agribusiness and biodiesel producer Amaggi obtained Brazil’s first authorization to use marine biofuel in a vessel. After receiving approval from the National Petroleum Agency (ANP) this spring, the company planned to use B100 in a river vessel between Porto Velho, Rondônia, and Itacoatiara, Amazonas, traveling along the Madeira and Amazon rivers, consuming nearly 40,000 gallons of B100. Amaggi is expected to request
ANP’s approval for continuous use of B100 made at its biodiesel plant in Mato Grosso [BBD]
Kawasaki Kisen Kaisha Ltd. (K Line) has conducted its first trial use of marine B100 biodiesel supplied by World Fuel Services to the car carrier Apollon Highway operated by K Line. The marine B100 was delivered March 31 to the vessel at the port of Zeebrugge in Belgium and the trial was completed April 30. [BBD]
Tata Steel became the first Indian steel company to undertake a full-laden leg voyage from the east coast of Australia to India powered by a B24 marine biofuel blend. The cape vessel MV Cape XL departed from Gladstone port April 17 after loading coal. It successfully berthed at Kalinga International Coal Terminal Paradip Private Ltd. port May 8 to discharge 148,500 tons of coal. During its laden leg from Gladstone to Paradip, MV Cape XL used B24-grade marine biofuel, which was loaded from its ballast port in Guangzhou, China [BBD]
Scan Global Logistics and Hapag-Lloyd entered a partnership with a multimillion-dollar marine biofuel initiative to integrate biofuel into their shipping operations. The companies aim to establish a long-term partnership for the further upscaling of sustainabletransport solutions. Hapag-Lloyd also entered a cooperation with IKEA Supply Chain Operations to decarbonize the Hapag-Lloyd container shipments originating from Asia. From March 2024 to February 2025, both companies have agreed to use Hapag-Lloyd’s highest product option for biofuels, “Ship Green 100,” which relies on waste- and residue-based biofuel instead of conventional marine fuel oil. The expected result for IKEA during this period is a CO2emission reduction of around 100,000 metric tons. [BBD]
Gary Wheeler Executive Director
2
(Comparisons to 2022 Data)
Total combined U.S. imports of biobased diesel up 68%.
U.S. imports of renewable diesel up 38%.
U.S. imports of biodiesel up 100%.
Combined U.S. imports of biobased diesel in 2023 second highest on record behind 2016.
U.S. imports of German biodiesel up 127%.
U.S. imports of Spanish biodiesel up 310%.
U.S. imports of Italian biodiesel up 260%.
U.S. imports of biodiesel second highest on record behind 2016.
U.S. imports of renewable diesel second highest on record behind 2021.
Germany was the No. 1 source of U.S. imports of biodiesel for the first time, surpassing Canada.
U.S. imports of combined European biodiesel up 178%.
Total U.S. biodiesel exports up 5%*.
European share of U.S. biodiesel imports hits 63%, up from 46% in 2022, 27% in 2021 and just 3% in 2016.
863,142,000 gallons
Biobased Diesel Imports 611,898,000 gallons
We are excited to announce a significant step forward in renewable fuel technology with the new terminal in Fontana, a collaborative project by Baker Commodities’ subsidiary New Leaf Biofuel, and MHX LLC. This facility stands out for its dedication to low-CI feedstocks, promising a substantial reduction in biofuels’ carbon intensity and offering specialized storage for a vast array of biofuels. It’s a pivotal development for the region, designed to meet growing demands for cleaner, sustainable fuels. This facility boasts a yearly capacity of over 120 million gallons, equipped with the latest in autonomous truck loading technology and dual rail service, setting new standards for efficiency and sustainability in the fuel industry.
The agriculture committees of Congress might want to look at what is happening on the tax-incentive side of the scale regarding climate-smart practices.
By John Campbell
The Inflation Reduction Act is supercharging the race to decarbonize the transportation sector. Farmers might soon have a way to be paid for greenhouse-gas (GHG) reductions by passing their crops through low-carbon biofuels plants. The U.S. Department of the Treasury’s rules determining how GHG-saving practices on the farm might count toward further decarbonizing renewable fuels could have a greater impact on land use than all the previous farm bills put together—or not, depending on the details.
Carbon pipelines have become a political lightning rod dampening the possibilities for zero-carbon biofuels. Creatively implemented, the IRA could incentivize regenerative agricultural practices that have the potential to reduce as much GHGs as the sequestration pipelines. And, as a bonus, once a farmer retools for regenerative practices on a portion of their farm, they will likely flip the whole farming operation. Thus, there is a 3-to-1 acreage gain driven by the portion of crops going to biofuels.
Farm programs administered by USDA as part of the farm bill attempt to influence farmer behavior, but those programs are commodity by commodity—different programs for different crops on the same farms and a myriad of underfunded conservation programs.
Every once in a while, Congress enacts momentous farmpolicy changes. One was in 1985, when it approved Sodbuster, Swampbuster and Conservation Compliance for Highly Erodible Land rules as reasonable restrictions on what farmers could do with their land in exchange for price and income support (as well as subsidized crop insurance in 2014).
Today, there are more stakeholders involved in farm-bill debates. These new players are searching for ways to make the farm bill more environmentally oriented. There has traditionally been a red line for the farm lobby, however, when it comes to the big money in the commodity and crop-insurance titles of the legislation. Nobody dares cross that line.
Change on a large scale requires that the line be crossed though. There is not enough money in the discretionary conservation title to compete with the mandatory commodity and crop-insurance titles that drive farmer behavior.
Congress may want to look to the 1985 and 2014 farm bills when the red line between the commodity titles and conservation goals were crossed. Farmers were required to comply with environmental rules to get payments. While those rules leaked over time, there is a new urgency to do what we can where we are now. The greatest beneficiaries will be the
rural communities that support farmers and their families.
Farmed soils have enormous capacity to reabsorb carbon lost over the past couple of centuries. We know that regenerative practices build soil carbon, but it is a slow and complex process that takes time and can be reversed if those practices are abandoned. Voluntary carbon markets to compensate farmers for changing practices are still in their infant stages.
Farmers know that yields pay and so they push the land as hard as possible. Fifty percent of land is short-term rental so there is little incentive to make long-term changes. Corn-yield contests show that 600 bushels per acre are possible but national yield averages are only around 170 bushels per acre. The difference is “seed and feed.” More seed, more fertilizer and more water. Farmers have done an excellent job of reducing the amount of fertilizer per bushel but total fertilizer use is still high.
The biggest environmental culprits are nitrogen and phosphates. In the case of nitrogen, only 50 percent applied is used by plants. The rest is lost to the air and water. Avoiding nitrogen waste has an almost immediate GHG benefit far larger than sequestered carbon. As a GHG, nitrous oxide is 300 times more potent than carbon. Unused phosphates end up fouling waterways and lakes and eventually fueling the dead zone in the Gulf of Mexico. Nutrient management might be the most important and immediate environmental need.
Recoupling commodity payments and crop insurance to regenerative and climate-smart practices could broaden support for a food system that is under growing scrutiny. Making payments for doing good on all farms—not just small tracts of highly erodible land—seems like a commonsense evolution of commodity and crop-insurance subsidies.
Ironically, the IRA could be the first step to truly reward farmers for climate-smart practices through biofuel programs. The agriculture committees of Congress might want to look at what is happening over on the tax-incentive side of the scale and begin to funnel some of the mandatory commodityprogram money toward better environmental outcomes like the IRA regardless of the end use for those crops.
Author: John Campbell Managing Director, Ocean Park 402-680-7111 jcampbell@oceanpk.com
Editor’s Note: John Campbell is a former agribusiness executive, U.S. deputy undersecretary of agriculture, and U.S. Senate agriculture committee staff member. Campbell also served on the bipartisan Commission on 21st Century Production Agriculture.
LCAs are the foundation for regulatory compliance in many carbon markets and tax incentives, including the new 45Z clean fuel production credit.
By Jim Ramm
Understanding and implementing lifecycle analysis (LCA) is more critical than ever for organizations striving to stay ahead of regulatory requirements, consumer expectations for sustainability, and the competitive landscape shaped by environmental accountability.
The most recent example is the inclusion of LCAs in determining eligibility for the biodiesel, renewable diesel and sustainable aviation fuel (SAF) clean fuel production tax credit under Section 45Z of the U.S. Inflation Reduction Act of 2022, which applies to fuels sold from 2025 through 2027. Under Section 45Z, these biomass-based diesels are eligible for tax credits with a carbon-intensity (CI) score 50 percent lower than petroleum-based diesel, and LCAs are the foundation for regulatory compliance.
To assist the industry in understanding LCA and to take advantage of these tax credits and other revenue-generating carbon-credit initiatives, EcoEngineers (Eco) is launching a new program, the LCA Academy, June 25-26 in Des Moines, Iowa, and Sept. 4-5 in Houston, Texas. The LCA Academy is designed to help biomass-based diesel producers and traders grasp the essential role of LCA in reducing environmental impact and to engage with key government officials who are determining how LCAs are incorporated into tax policies and other incentive programs.
Eco’s LCA Academy offers industry leaders and producers the opportunity to gain insights and significantly impact the field. In this one-and-a-half-day program, participants will learn about LCA concepts; methodologies and the role of LCA in environmental, social and governance (ESG); compliance and conservation.
The first day focuses on the importance of measuring the impact of products on the environment, the principles of LCA and carbon accounting, and insights into the regulations shaping the global marketplace, including the U.S. Renewable Fuel Standard, the U.S. IRA, Canada’s Clean Fuel Regulations, California and British Columbia’s Low Carbon Fuel Standard programs, Oregon and Washington’s Clean Fuels Programs, the Greenhouse Gas (GHG) Protocol, U.S. DOE grants, and Environmental Product Declarations, as well as European standards such as the Renewable Energy Directive (RED III), and participation in voluntary carbon markets (VCMs).
In addition, participants will learn to interpret LCA results and use various assessment techniques for corporate and product reporting. The LCA Academy will address differences between LCA and scope reporting, data relevance and dataset selection, incorporation of ISO quality standards, and review and comparison of LCA tools.
The second day offers two tracks:
• The Practitioner Track provides an immersive, hands-on workshop for all levels of experience. Participants will
learn how to collect, quantify and analyze CI scores using leading LCA technologies like GREET and ISO standards, and learn the basics of utilizing LCA models and creating an LCA model from scratch.
• The Executive Track focuses on developing and deploying climate-friendly technologies and operational improvements in manufacturing, dependent on their performance as measured by an LCA. This session includes a forum for influencing industry trends and regulations to work towards a consistent LCA approach in policies. It will also include key representatives from leading agencies focused on regulations and climate change.
LCA is a systematic and comprehensive method for evaluating the environmental impact of a product, service or system from its inception to end-of-life. This analysis examines energy usage, rawmaterial extraction and processing inputs and outputs throughout the various lifecycle stages, including coproducts and waste.
Typically, LCAs assess a functional unit’s global-warming potential or carbon footprint but can also encompass other impact categories such as land use, eutrophication, acidification and water use.
At Eco, we are dedicated to helping our clients navigate the complexities of carbon emissions and climate change. We are an industry leader in performing LCAs, with a team of renowned scientists performing more than 1,000 carbon LCAs since 2015. Our team is adept at utilizing all available LCA tools to bring the right strategies and solutions to help you reach your carbon-management and ESG goals.
We use LCAs to assist our clients in reducing their CI scores and help them find innovative ways to generate additional revenue from their offsets. We recently helped North Dakota-based Red Trail Energy become the first ethanol producer to enter the VCM and the largest carbon-removal project registered to date.
Join us at the LCA Academy and be part of the movement to reduce environmental impact and drive sustainable growth by registering at eventcreate.com/e/ ecoengineers-lcaacademy.
Author: Jim Ramm
Vice President, U.S. Biofuels EcoEngineers 515-985-1260 jramm@ecoengineers.us
June 25 - 26
Des Moines, Iowa
September 4 - 5
Houston, Texas
New “technology-neutral” federal regulations are designed to drive automakers toward electric vehicles, but there is skepticism whether the U.S. will be ready or if consumers even want this.
By Allen Schaeffer
Fire, aim, ready—that’s one assessment of the playbook for how climate and energy policy are being made in the U.S. as the shift to a clean-energy economy picks up full steam.
Three new regulations issued by U.S. EPA will mark what will be remembered as the most consequential three-month period in regulatory history because of their cost and impact on society. The rules establish new emissions and efficiency standards for light- and medium-duty vehicles, commercial vehicles and power plants. All of the rules are driven by efforts to reduce greenhouse-gas (GHG) emissions and fundamentally they are driving the economy away from fossil fuels. The target sectors have been identified and the rules have been launched, but there is growing skepticism about whether the U.S. is or will be ready for this transformation.
New automobile tailpipe-emissions standards were announced as “technology neutral,” according to EPA, but in reality they are designed to drive manufacturers toward zeroemission—and preferably electric—vehicles (ZEV); 30 percent to 56 percent of new light-duty vehicle sales and about 20 percent to 32 percent of new medium-duty sales would be battery electric by 2032. As for heavy-duty trucks, about 40 percent of Class 8 tractor-trailer size trucks would likely be ZEV by 2032. Power plants are likely to see the end of coal-fired generation with the new rules. EPA backed off moving fully away from natural gas but applied extremely stringent rules requiring carbon capture for any new power plants.
There are many common features of these three rules. They were scaled back from initial proposals in time and expectations for achieving the switchover to lower- or zerocarbon fuels and technologies. In the case of the automotivesector rules, if you read between the lines there is a continued, and likely dominant, future role for advanced internalcombustion vehicles. The automotive and power-plant rules have been characterized as unrealistic in timeframes and certainty of market conditions. Both are heavily dependent on the development of a completely new fueling infrastructure (solar, wind, electric) in record time and consumers willing to adopt new lifestyles for their new technology.
In the case of heavy-duty trucks, to meet the envisioned ZEV goals, one industry association estimated that 1,995 heavy-duty electric chargers must be installed nationwide each and every month between now and the rule’s effective date in 2032. Is our grid even able to realistically deliver clean electrons from renewable power sources in a timeframe that makes this work? Probably not.
Where are renewable fuels in these new carbon-cutting policies? Regrettably they are mostly on the sidelines. EPA’s tailpipe rather than lifecycle emissions approach diminishes the opportunity for carbon reductions from renewable fuels. Renewable fuel producers and suppliers are making
IMAGE:
RICH KASSEL, AJW INC.
investments for more capacity while also expanding feedstocks. What is missing is a correspondingly progressive and growthoriented policy from government.
And then there’s the money. The Biden administration delivers a near constant flow of funding for all aspects of electrification: $900 million for electric-vehicle (EV) charging stations; $623 million in grants to build out the EV-charging network; $46 million to boost EV-charging performance, to name just a few. The New York Times captured the total for EVs at $174 billion.
You don’t need an accounting degree to see the stark differences between that $174 billion and the mere fewhundred million for renewable fuels, even considering the December 2021 $800 million in post-pandemic restoration funds for biofuel producers and infrastructure. The heralded Inflation Reduction Act puts just $500 million to increase the availability of domestic biofuels. This year, just $9.4 million was provided to spur development of advanced biofuels (February) and then in April USDA announced $43 million in grants under the Higher Blends Infrastructure Incentive Program.
Using more biofuels now helps reduce emissions immediately and leverages everything that we know works— our internal-combustion engines, our fueling and distribution systems, and the fuel producers. Many of the Biden administration’s clean-energy investments in electrification won’t see any benefits for years or decades to come, and that is if they stay on track, if they are accepted by end users, and if they are successful at the scale envisioned. That’s a lot of “ifs.”
There are many ways to get to a reduced-carbon future. We’ll get there faster by using more proven renewable and available biofuels. More progress in the near term means less severe actions in the future. And that is something we should all get behind.
Author: Allen Schaeffer Executive Director Engine Technology Forum 301-668-7230
info@enginetechforum.org
enginetechforum.org
A four-pillar concept from Chevron REG’s Rajani Modiyani is an intelligent way to establish a framework for adopting low-carbon fuels.
By Paul Nazzaro
The renewable fuels industry stands at a pivotal juncture, where challenges and opportunities abound for stakeholders across the supply chain—from biodiesel and renewable diesel producers to petroleum terminals, wholesalers and fuel jobbers. Introducing new products and services, particularly low-carbon liquid fuels, is burdened with uncertainty. Yet, for nearly three decades, the biodiesel industry has demonstrated remarkable resilience, overcoming countless obstacles to succeed and advance.
The introduction of renewable diesel marks a significant milestone, with the petroleum industry embracing cleaner fuels that align with growing environmental sensitivities. This shift represents a renaissance in the energy sector, one that resembles a marathon rather than a sprint. Leading this transformation requires visionary leaders who think forward and embrace disruption constructively.
The energy sector must continuously innovate to meet the world’s insatiable energy demands. The development of biodiesel, renewable diesel and sustainable aviation fuel are commendable strides toward a cleaner-energy future. This transition, however, does not mean abandoning petroleum altogether. The world’s energy appetite necessitates an all-of-the-above approach. Both renewable diesel and biodiesel have roles to play, and the industry must ensure that the former’s transitional ease does not sideline the latter. With a production capacity of 2 billion gallons per year, domestic biodiesel production remains a crucial component of our energy landscape.
In a recent collaborative discussion with Rajani Modiyani of Chevron Renewable Energy Group, she shared with me an intelligent way to establish a framework for companies seeking adoption of low-carbon fuels. She calls this the four-pillar concept.
Technology scalability is essential for the low-carbon liquid fuels industry, encompassing the ability to expand and adapt on a large scale without significant losses in performance or economic feasibility. For biodiesel and renewable diesel, this means ensuring efficient production and widespread distribution. The goal is to maintain or improve efficiency as the industry scales up.
Infrastructure readiness is crucial for a seamless transition. Evaluating whether existing physical systems can reliably accommodate (store, blend and distribute) new fuels is essential, as is considering new infrastructure investments. This readiness includes ensuring facilities for heating biodiesel, transloading for rail deployment, and necessary amendments from production to consumption.
Operational integration focuses on how well low-carbon liquid fuels can assimilate into the existing supply chain. This involves the adaptability of current operations within the petroleum supply chain and the ability of downstream users to manage the transition effectively. Key aspects include personnel
training, equipment modifications and overall operational efficiency. The industry’s ability to support this transition and its preparedness to adopt these changes are critical.
Economic justification is paramount as users evaluate the shift to clean energy and how it can be monetized effectively. This includes cost-benefit analyses comparing new technologies to fossil fuels, electrification and other options. It’s important to consider direct costs and externalities like environmental and health impacts associated with scope 1, 2 and 3 emissions. Ensuring biofuels are environmentally and economically viable without substantial subsidies is a significant challenge.
Each of these pillars addresses a fundamental aspect of transitioning to a low-carbon future. The relevance and importance of maintaining biodiesel plants as ready, willing and capable contributors to U.S. energy independence cannot be overstated. These valuable assets play a key role in the broader energy platform. We frequently hear about new renewable diesel capacity being considered or acted upon. Due to economic challenges, however, it’s not uncommon for biobased diesel producers to take their assets offline at their discretion. Our success will be compromised if we fail to maximize the existing production assets of both sectors.
When a company takes barrels offline, it can negatively impact supply into markets that took years—sometimes decades—to build. This also affects markets under review for expansion like marine, rail, aviation and mining. Who will supply all these sectors? It’s not a matter of either renewable diesel or biodiesel but rather leveraging all available resources. Our existing infrastructure has immense value, and we must ensure that it’s ready to service the burgeoning demand.
Scalability and reliability are critical. We need to focus on developing and advancing as many clean technologies as possible, working together to meet the demand that will likely continue to grow. This approach will ensure we can optimize the system without dismantling the infrastructure and the products it delivers without calculating the gains.
In this marathon of industry transformation, the key to success lies in collaboration and continuous advancement. By working together, stakeholders can develop and advance clean technologies to meet the ever-growing energy demand. The goal is to optimize the system, leveraging the strengths of both renewable and traditional energy sources to create a sustainable and robust energy future.
As we look ahead, it’s essential to keep an open mind and embrace innovation. The biofuels industry has demonstrated its resilience and capacity for growth. Now, it’s time to harness that spirit to navigate challenges and seize the opportunities ahead.
Author: Paul Nazzaro President
Advanced Fuel Solutions Inc. 978-880-5338 paulsr@yourfuelsolution.com
CUSTOM FORMULATED BIOBASED COMPATIBLE LONG-TERM RELIABLE
O.P.T. IS AN ADVANCED FAMILY OF FUEL ENHANCERS DEVELOPED TO ENSURE YOU NEVER STOP RUNNING. FORMULATED TO WORK SEAMLESSLY WITH BIOFUELS, OPT IS CUSTOM-TAILORED FOR OPTIMAL EFFICIENCY AND BIOBASED COMPATIBILITY. SUPPORTED BY INDUSTRY-LEADING FUEL QUALITY PROFESSIONALS, OPT DELIVERS ONGOING OPTIMIZATION FOR LONG-TERM RELIABILITY. THIS INNOVATIVE CHEMISTRY REPRESENTS THE GOLD STANDARD IN FUEL ENHANCERS, ENSURING PEAK PERFORMANCE FOR THE MARATHON AHEAD.
O.P.T. IS REVOLUTIONIZING PERFORMANCE FROM PRODUCTION TO CONSUMPTION.
DESIGNED, DEVELOPED AND DELIVERED BY
Leverage Plasma Blue technology to create the
By Tom Slunecka
Plasma Blue is a revolutionary technology that creates lowcarbon biodiesel at significantly lower production costs while seamlessly integrating into existing renewable fuel plants or those being built.
With recent changes in U.S. federal and state policies, reducing the carbon-intensity (CI) score of biofuels is imperative. By using electricity instead of natural gas, Plasma Blue requires much less energy because it doesn’t require preheating and creates flexibility in operations. The ability to lower energy costs while simultaneously reducing biodiesel’s CI allows plants to take greater advantage of government incentives for clean, renewable energy—coupling lower production costs with greater tax benefits. An additional 35 cents per gallon, for example, may be attributed to the per-gallon value of your plant based on a reduced carbon score.
Plasma Blue technology can be powered through wind or solar energy because of its ultra-low electricity requirement. And by utilizing farm-grown feedstock such as soybean oil and ethanol—another ag-based product—instead of methanol, along with wind or solar power, the ultimate low-carbon renewable liquid fuel can be achieved. In addition, Plasma Blue uses a less-intensive catalyst that is significantly more affordable than traditional ones, which could further improve a facility’s CI score and dramatically reduce production costs.
Through years of rigorous testing, this design—which has received a certificate of analysis—has been scaled from a simple benchtop design to our current 5-million-gallon capacity unit. Scaling the technology is easy and, regardless of plant size, a plasma unit can be custom built to suit your needs.
Plants that have operated our technology have achieved consistent ASTM-spec biodiesel. And because of the plasma unit’s ability to complete reactions, biodiesel produced with Plasma Blue possesses superior properties on par with more expensive distilled biodiesel, such as cold flow.
More importantly, Plasma Blue is the only technology that ethanol plants can use to produce biodiesel with their own alcohol. Typically, the biodiesel production process only allows for the use of methanol, but Plasma Blue can effectively convert fats, oil and grease into biodiesel using ethanol. The use of ethanol has long been known as a possible alternative but has never been done cost effectively—until now. For a 50-million-gallon ethanol plant, creating biodiesel using your own corn oil and ethanol could create an additional $600,000 in revenue each year. Furthermore, there is a potential California Air Resources Board score improvement that may affect both the biodiesel value and increase the value of the interplant’s production. And, because of the Plasma Blue unit’s compact size, ethanol refineries can easily add the technology to their current process.
To prove Plasma Blue’s effectiveness, we have developed a self-contained mobile testing unit. This unit allows plants to see the technology firsthand in the comfort of their own facility. The mobile testing unit exists in an enclosed trailer, allowing multiple feedstock product samples to be run on site and tested in the plant’s laboratory for comparison.
The future of biodiesel has arrived, and it’s time to invest in today’s technology. Plasma Blue is a gamechanger for the biofuels industry and we are confident that this technology can expand your plant’s possibilities. For this industry in which every cent matters, Plasma Blue will help your biofuel manufacturing plant boost profitability through lower costs and greater production.
To learn more about Plasma Blue, send me an email or give me a call. I look forward to discussing in greater detail the myriad benefits our technology can offer you and your facility.
Author: Tom Slunecka CEO, Plasma Blue 507-720-4052
tom@plasma-blue.com
Verification of biogenic-carbon content in biofuel blends can be used to maintain compliance with regulations and provide access to tax incentives.
By Jordan Turner
As alternatives to traditional fossil fuels, biofuels and renewable diesel are processed from renewable, biomassderived sources including vegetable oils, animal fats and recycled cooking grease. Fuel-industry professionals interested in verifying the biomass content of their diesel blends can benefit from the easily understood, reliable results achieved via biogenic-content testing. Biogenic-content testing is based on ASTM D686622 and EN 16640 analytical standards and harnesses the accuracy of carbon-14 analysis to validate the biogenic-carbon content of biodiesel and other renewable fuels. This testing is applicable to samples in liquid form, such as diesel fuels, as well as solid and gaseous samples. Carbon-14 analysis measures the percentage of biogenic (or biomass-derived) carbon versus fossil-derived material in a biofuel blend. Testing results provide valuable data that can be applied to monitoring progress toward carbon neutrality and can also be used to comply with regulatory requirements and obtain tax benefits.
The ASTM D6866-22 and EN 16640 analytical standards recognize biogenic content as material containing organic and inorganic carbon from renewable sources, or biomass, including plant, animal, agricultural and marine materials. Biomass-derived materials contain the radioactive isotope carbon-14, which can be measured to identify the fraction of biomass (biogenic content) in renewable fuels and other products made from biomassderived materials and feedstocks. During the lifecycle of a plant or animal, carbon dioxide, which contains the carbon-14 isotope, is exchanged with the atmosphere via photosynthesis and the food chain. Carbon-14 concentrations in the atmosphere exist at known levels, maintaining balance in biomass and allowing it to be accurately measured. When a plant or animal dies, it stops exchanging carbon dioxide with the atmosphere. The carbon-14 in the remaining organic matter begins undergoing the process of radioactive decay. Carbon-14 analysis has a detection limit of approximately 43,500 years. Once the decay process is complete, a material will no longer contain carbon-14. For this reason, fossil fuels will not contain any carbon-14.
Carbon-14 analysis is performed using an accelerator mass spectrometer (AMS) instrument. Results are clear and easy to understand, indicating the amount of biogenic content in a given sample representing the ratio of biomass-derived and fossilderived material. The biomass fraction of the result is reported as a percentage of biogenic content. A sample that is formulated completely from biomass will result in 100 percent biogenic content while a traditional fossil fuel will have zero biogenic
content. A mixture that is made in full or part of biomass-derived feedstocks such as soybean or palm oil can have its carbon-14 fraction accurately detected, making this method a highly valuable tool for measuring the biogenic content.
Biogenic content measurement is widely applicable to biodiesel, renewable diesel/hydrotreated vegetable oil (HVO), sustainable aviation fuel (SAF) and other biomass-based renewable energy sources like ethanol and renewable naphtha, as well as feedstocks such as used cooking oil, palm-oil mill effluent, cashew-nutshell oil, municipal solid waste and more.
Biogenic testing is recognized by renewable fuel industry professionals as a reliable and highly accurate third-party verification tool for measuring the biogenic content of their biodiesel and biofuel blends. Carbon-14 analysis is widely used, with applications extending to refineries for the determination of biofuel-blend ratios originating from bio-oil as an alternative to petroleum feedstocks. Several key benefits of biogenic-content testing for the fuels market exist. Verification of biogenic-carbon content in biofuel blends can be used to maintain compliance with regulations and provide access to tax incentives. Additionally, data gained from testing can be used to monitor progress toward decarbonization and reaching net-zero goals as well as offering research and development teams a tool for measuring biogenic-content optimization. When it comes to compliance, several regulatory programs recommend or require ASTM D6866 biogenic-content testing. The data obtained via carbon-14 analysis can be used to ensure renewable fuel manufacturers comply with current regulations to qualify for tax credits or carbon credits for carbon-intensity reduction. North American programs include the U.S. Renewable Fuel Standard, California’s Low Carbon Fuel Standard, Canada’s Clean Fuel Regulations, and Oregon’s Clean Fuels Program. ASTM D6866 testing is also applicable to a number of European standards including the Roundtable on Sustainable Biomaterials’ standard for advanced fuels, the EU’s Renewable Energy Directive and Emissions Trading System, and the Netherlands’ HVO regulation.
In conclusion, the renewable carbon sources from biomass used to develop biobased diesel fuel make it an ideal candidate for ASTM D6866 carbon-14 testing. Biogenic content is measured as a fraction of biomass and fossil-derived material. This is an accurate and easily understood method for validating biofuel blends. Results offer additional benefits for research and development as well as for companies seeking to reduce their carbon intensity and comply with current regulations.
Author: Jordan Turner Marketing Coordinator Beta Analytic info@betalabservices.com
Low RIN and LCFS credit prices coupled with massive UCO imports are causing hurdles, but demand for biobased diesel from emerging markets is high.
By Jonathan Martin
2023 was a year of incredible growth for biomass-based diesel (BBD) and for feedstocks that support its production. Consumption of BBD and sustainable aviation fuel (SAF) reached a record in 2023 at just under 4.6 billion gallons consumed. BBD consumption was about 8 percent of the total diesel fuel consumed in the United States, a significant growth from recent years. Biodiesel production capacity has remained relatively steady at 2.1 billion gallons per year (bgy), while renewable diesel capacity has expanded up to 3.9 bgy. States with low-carbon fuel standards (LCFS) remain the main drivers for BBD consumption, with California leading the charge with approximately 60 percent of the entire diesel pool in the state being BBD.
BBD growth does come at a cost. First, this unprecedented growth eclipsed what U.S. EPA forecasted was possible, greatly exceeding the set rule for 2023 under the Renewable Fuel Standard. When the set rule was released in June 2023, it was readily apparent that BBD would easily outpace the D4 set rule. The only question is whether it would completely fill (and possibly overfill) the D5 and D6 pools as well. When this happened, we saw a sharp decline in renewable identification number (RIN) credit prices. Many things drove this decline, but it is clear that markets have decided to revert to pricing the D4 RIN off of the bean-oil/heating-oil (BOHO) spread. The BOHO spread indicates a market-generalized necessity to fill a price gap between the cost of a producer’s feedstock (soybean oil in this case) and the producer’s final product (heating oil or diesel). Soybean-oil prices have fallen while diesel prices have increased, which has narrowed the BOHO spread—and the D4-RIN price. RIN prices seem to have found a floor at around 40 cents/RIN, and it will be interesting watching these markets to see if RINs rebound.
To add insult to injury, LCFS credit prices across the West Coast are also down from recent highs. While the RFS sets a mandated volume, LCFS markets set an overall carbon-intensity (CI) reduction target trying to balance deficit generation (petroleum/ natural gas) with credit generation (renewables, electricity, etc.) at those target levels. Recently, there has been a huge growth in credit generation led by BBD, renewable natural gas and electricvehicle adoption. There are currently over 20 million metric tons of LCFS credits in the California credit bank, significantly pulling LCFS credit prices down. These lower credit prices, along with lower RINs, make it harder for BBD producers to be profitable.
The significant growth we saw in BBD production in 2023 led to a banner year for all feedstocks to the BBD process. Soybean-
oil consumption reached a new record—just over 13 billion pounds—in 2023; yet soybean oil as a percentage of all feedstock used decreased to about 41 percent due to significant growth in canola-oil consumption and animal fats. Used cooking oil (UCO) also saw large growth in consumption, though it remained at about 21 percent of all feedstocks used in 2023.
Soybean growth came mostly domestically, as soybean-oil exports decreased and were pushed into the BBD production process. The other growth, however, came via increased imports. The big changes in imports came from both inedible tallow and UCO. The tallow growth was somewhat expected while UCOimport growth led by China was not expected to reach the levels it did. Chinese UCO imports rose from zero prior to 2023 to 362 million pounds in January 2024. This sharp increase in available UCO in the market has driven U.S. feedstock prices down significantly. Since LCFS markets preferentially select low-CI fuel sources, low-CI feedstocks like UCO are preferred for producers selling into those markets.
There is significant enthusiasm in new markets, such as rail and marine, in reducing their corporate greenhouse-gas emissions, and both biodiesel and renewable diesel fit perfectly into their corporate structures. Biodiesel sales in marine markets are growing rapidly throughout the world, and these companies would like to increase their uptake in biodiesel and renewable diesel blends in the U.S.—but the inability for ocean-going vessels to get the benefits of RINs remains a hurdle. Meanwhile, multiple Class I railroad companies have been setting lofty goals for biodiesel use in their engines as early as 2030. Demand for BBD is going to continue to grow as the benefits of our fuels continue to reach new markets. It will be up to the industry to make that market come to fruition—even if we have to weather yet another storm to get there.
Author: Jonathan Martin Director of Economics and Market Analytics
Clean Fuels Alliance America 800-841-5849
jmartin@cleanfuels.org
Growth in renewable fuels like biodiesel is unstoppable. So are your partners at Evonik – with reliable supplies of alkoxides to keep your biodiesel business up and running. And targeted technical support when and where you need it. With production facilities in all major markets, we’re never far away. Let’s talk about boosting your business in this key source of renewable energy.
Let’s talk about what Evonik can do for you. Evonik Catalysts. Let’s make a difference.
Are you interested in learning more? Please contact us at:
Evonik Corporation
Phone +1 331 666-8235 fabio.tufano@evonik.com evonik.com/catalysts
By
Production of high-quality biodiesel with low monoglyceride content is now possible with a new, elegant and economical process that can be easily integrated in existing and new biodiesel plants.
Biodiesel is a renewable biofuel that consists of fatty acid methyl esters and is typically produced by transesterification of vegetable oils or animal fats. Biodiesel (B100) has to meet minimum quality requirements that are specified in various international standards (EN 14214 and ASTM D6751). Some countries have their own national standards such as Indonesia (SNI 04-7182-2006) and Malaysia (MS 2008:2008).
Biodiesel quality parameters can be either feedstock or process dependent. Feedstock-related quality parameters such as iodine value or oxidative stability are intrinsic parameters related to the raw-material inputs and are generally not affected by the biodiesel production process.
Cold stability is another critical quality parameter that can be notably influenced by a combination of factors, including feedstock-related parameters such as sterol-glucoside content and the degree of saturation measured by the iodine value. In practice, some of these quality parameters can be improved to a certain extent by the use of additives. For example, coldflow improvers are added to improve the cold stability while antioxidants are added to get a better oxidative stability.
Process-related parameters such as ester content, degree of conversion (mono-, di- and triglyceride content) and total contamination result from the biodiesel production technology itself and can be improved by optimizing the process design and conditions.
One important parameter that determines the degree of conversion is the monoglyceride content. A high monoglyceride content contributes to poor cold-flow properties as monoglycerides tend to precipitate, causing problems in the engine’s performance.
Therefore, cold stability is an important biodiesel quality parameter as it will determine the maximum blending ratio of biodiesel in fossil diesel. Cold stability of biodiesel can be expressed by different parameters such as the cold filter plugging point (CFPP) or the cold soak filtration test (CSFT). Currently, 7 percent is the maximum biodiesel blend permitted in diesel fuel (B7) by the European Fuel Quality Directive (Directive 98/70/EC of the European Parliament and of the Council). This specific limit is established as higher blending ratios may result in clogging of fuel filters, especially in northern Europe and coldweather conditions. This issue mainly arises from the poor cold stability that biodiesel with higher saturation exhibits, such as palm-based biodiesel. In countries with a (sub)tropical climate, such biodiesel can be used without any problem and even at
higher blending ratios. Major palm oil-producing countries like Indonesia and Malaysia currently have biodiesel mandates of 30 percent (B30) and 10 percent (B10), respectively, and Indonesia is even considering increasing it further to B40.
Hence, in order to assure a better cold stability of (saturated) biodiesel, and given the increasing biodieselblending mandates, there is a trend by users and associations to implement more strict norms and quality control to avoid issues in the use of biodiesel. The European EN 14214 biodiesel standard reduced the maximum concentration of monoglycerides from 0.8 percent to 0.7 percent, while the American standard ASTM D6751 adopted a tight spec with a maximum of 0.4 percent monoglycerides for grade 1-B biodiesel. On the other hand, other countries like Indonesia, despite the higher blend, set an intermediate value of 0.55 percent for B30 blends.
Over the years, different technologies were developed to get a lower monoglyceride content in biodiesel by either pushing the conversion or removing them from the biodiesel.
Pushing the conversion during transesterification can be achieved by either dosing more catalyst and/or dosing more methanol. These conditions will give a biodiesel with lower monoglycerides with no yield loss but also with a higher operating cost. Nevertheless, due to the equilibrium of chemical reactions, there will always be a constraint on the extent to which monoglycerides can be reduced through transesterification.
Another option is to remove monoglycerides from the biodiesel. This can be achieved by distillation, which is a known process for the production of high-quality biodiesel. Less volatile components, including monoglycerides, di- and triglycerides, unsaponifiable matter and sterol glucosides, will remain in the distillation pitch, which will lead to a reduction in yield. The lower biodiesel yield together with the higher operating cost are seen as the main disadvantages of the distillation process.
Monoglycerides can also be removed from biodiesel by adsorption on specific silica-based or activated compounds. This adsorption process, however, is not widely used on an industrial scale due to a number of constraints.
Next to the different existing solutions to reduce monoglyceride content in biodiesel, Desmet developed a new, improved purification process that enables very-low residual monoglycerides at reduced capital investment.
Table 1 (caption in article)
Table 1: Results from a lab-scale trial of Desmet’s improved biodiesel-purification process. SOURCE: DESMET
Table 2 (caption in article)
Desmet currently offers a fully continuous biodiesel process with optimized transesterification conditions and low catalyst consumption. This process enables production of a final biodiesel product with 0.4 percent monoglyceride content, which covers the specifications of current European and other national biodiesel standards by a great margin.
Table 1 (caption in article)
To anticipate the biodiesel market evolution and meet the stricter demands on monoglycerides and higher blending mandates, Desmet has developed an improved biodieselpurification process, which enables a further monoglyceride reduction to a final amount of below 0.3 percent. This process is applied downstream in the biodiesel process without increasing the catalyst consumption and can be integrated in existing and new biodiesel plants with minor adjustments, limiting the capital investments required in comparison to traditional distillation columns.
The improved biodiesel purification process is an integrated post-treatment, which involves contacting the
Table 2 (caption in article)
Biodiesel
biodiesel after the different transesterification steps with a concentrated alkaline solution. Very small dosages of concentrated solution are required, which make the process more cost efficient.
After contacting the biodiesel with the concentrated solution into a nano-cavitation unit, the mixture is sent to a specially designed reactor allowing variable mixing zones, enabling selective contact between monoglycerides and the chemicals, leaving the fatty acid methyl esters intact. As a result, a high purity biodiesel is produced.
This patent-pending application has been deeply studied at laboratory scale, enabling a comprehensive understanding of the chemical interactions between the biodiesel components and the reactants (Table 1).
Additionally, the first industrial implementations have been successfully tested (Table 2) starting with variable monoglyceride content in crude biodiesel, allowing adaptation to different industrial-plant situations.
Table 2: Results from an industrial-scale trial of Desmet’s improved biodiesel-purification process.
SOURCE: DESMET
Authors:
Bárbara Sánchez González
Engineer
Dario Altera Head of Oleochemicals & Global Technology ManagerOleochemicals
Discover which units are the most suitable for coprocessing, what modifications are required and which feedstocks are best for SAF yield.
By Maria J. L. Perez and Milica Folic
As the aviation industry seeks to reduce its carbon footprint, the production of sustainable aviation fuel (SAF) has gained significant attention. One proven technology, due to its relatively low capital and operating expenditures (capex/opex) and only modest complexity, is coprocessing renewable feedstocks in conventional refineries.
With the promise of an additional revenue stream, and usually simple diversification, refiners are asking what are the most suitable units for coprocessing? What modifications are required? And which feedstock is best for SAF yield? We have the answers.
In coprocessing, fossil feedstock (e.g., crude oil) can be partly replaced with renewable feedstock (HEFA-based) such as vegetable oil, animal fat or used-cooking oil. HEFA stands for hydroprocessed esters and fatty acids. Fossil and renewable feedstocks are processed together to produce renewable fuel. Coprocessing can be conducted in several hydroprocessing units within a refinery, such as a kerosene hydrotreater, diesel hydrotreater or hydrocracker—all three will be explored in detail later.
In the coprocessing approach, renewable and fossil feedstocks are processed together, resulting in a blended product. Physical segregation of the renewable component from the fossil component in the resulting fuel is not feasible. Sustainability characteristics of each fraction, however, are
preserved in bookkeeping or mass-balance systems. These systems accurately track the amount and sustainability attributes of the renewable feedstock through the supply chain, ensuring that the renewable element and its benefits are accurately accounted for and credited.
Modifications required for a hydroprocessing unit to undertake coprocessing depend on its existing design and objectives. Several common areas may need to be addressed, however, including hydrogen availability, corrosion control, water formation and catalyst volumes.
Hydrogen availability is important as renewable feedstocks— due to their oxygen content—can consume significantly more hydrogen than fossil feedstocks (sometimes more than 31 times as much). Therefore, revamps of the make-up gas compressor and recycle-gas compressor may be needed to ensure sufficient hydrogen supply.
Renewable feedstocks can be highly acidic and may also contain chlorides (Cl), which can lead to Cl-induced corrosion. Depending on the point of injection of the renewable source, a material check may be required to assess potential acidity issues for corrosion control. The deposition of ammoniumchloride salts may also necessitate modifications in the point of injection of wash water at the reactor outlet.
Water formation also needs to be considered as triglyceridebased renewable feedstocks typically contain around 11 percent oxygen, which is converted into mostly water and small
amounts of carbon monoxide (CO)/carbon dioxide (CO2) during hydroprocessing. This increased water formation may require adjustments to the water-boot capacity.
The kerosene hydrotreater is particularly advantageous for SAF production, especially in the European Union where carbon-14 measurements are required. This unit maximizes the SAF yield, ensuring that a larger proportion of the biogenic carbon in the renewable feedstock ends up in the jet-fuel fraction.
It is the quickest and simplest method to begin coprocessed SAF production as it can be implemented without significant alterations to existing units. This approach is both a low opex and capex solution, promising a short payback period. Additionally, it provides the flexibility to select the most suitable coprocessing starting point, allowing the inclusion of renewable feed up to 5 percent volume.
Using the high selectivity TK-930 D-wax™ catalyst in an existing kerosene hydrotreater will retain the highest possible biogenic carbon in the jet fuel and ensure that it meets the demanding freeze-point specifications. The renewable fraction in the product will comply with the most stringent fuel specifications for SAF.
Renewable feedstock can be introduced directly into an existing diesel hydrotreater together with fossil feed. The product will be a combination of renewable and fossil diesel. This method offers several benefits. Firstly, it typically requires limited or no revamp of the plant, making it a cost-effective option. Additionally, renewable grading and hydrodeoxygenation (HDO) catalysts can be swiftly incorporated, either by the next turnaround or even sooner through skimming processes. This approach boasts low opex and capex resulting, again, in a short payback timeframe.
The implementation is straightforward, eliminating the need to wait for a fully renewable grassroots unit. Another advantage is the flexibility to determine the coprocessing starting point. Most notably, up to 10 volume percent of renewable feedstock can be seamlessly integrated with minimal equipment modifications. For coprocessing with more than 10 percent renewable feedstock, however, a revamp might be necessary. Nonetheless, this solution remains expedient and cost effective compared to establishing a new grassroots unit.
Hydrotreating units may be the primary choice so far for coprocessing renewable feedstock, but hydrocracking units should not be overlooked. Given their versatility, hydrocracking units are particularly suited for coprocessing renewables. We anticipate their usage will become indispensable in the future, particularly as the need to process more demanding secondand third-generation feedstock increases.
Unlike the hydrotreater, the hydrocracker offers significant process flexibility. It can be adjusted to accommodate specific feedstock availability and to produce the desired product. Coprocessing second-generation renewable feedstock like waste oils and fats, forest and food-crop waste and nonfood crops with vacuum gas oil (VGO) enables simultaneous production of various renewable fuels, including SAF, diesel and naphtha.
The preferred hydroprocessing unit to coprocess renewables would depend on the configuration of the refinery, the specific constraints of each unit and the desired product.
Hydrocrackers offer some benefits due to their larger size and increased hydrogen availability, which allow for greater quantities and more flexible selection of feedstocks. While operational challenges exist due to high oxygen content in renewables, the impact on hydrogen consumption is less compared to hydrotreaters, mitigating operational difficulties.
Hydrocrackers handle contaminants more efficiently, as they are designed to process feedstocks with considerable amounts of contaminants like VGOs and heavy coker gas oil (HCGOs), minimizing the need for extensive catalyst replacement and ensuring uninterrupted operation.
If the target products are hydrotreated vegetable oil (HVO) or SAF, coprocessing renewable feedstock in a diesel or kerosene hydrotreater will retain the highest possible biogenic carbon in the diesel or jet fuel. If a combination of renewable products is desired, coprocessing in a hydrocracker is the preferred option.
Another possibility to produce SAF is using the fractionation system in the hydrocracker to cofractionate hydrotreated renewable diesel together with the fossil product. It is required to have hydrotreater renewable diesel available.
Catalyst selection is crucial in producing efficient, high-quality coprocessed fuel. Topsoe’s catalyst selection for coprocessing, for instance, is designed to effectively address differences between renewable and conventional feedstocks, minimizing CO2 formation while optimizing cycle length, yields and coprocessing rates.
Additionally, Topsoe’s specialty guard materials and catalysts combat new contaminants introduced during renewable fuel conversion, such as phosphorus, potassium and sodium, ensuring profitable operation. Finally, dewaxing—vital for improving the coldflow properties of biofuels like renewable diesel and SAF—is facilitated by Topsoe’s state-of-the-art dewaxing catalysts TK930 D-wax™ and TK-920 D-wax™. These catalysts leverage selective isomerization to enhance cold-flow properties while minimizing yield loss to byproducts.
The operating conditions for coprocessing in a hydroprocessing unit can vary widely and are determined on a case-by-case basis. Several factors influence the optimal operating conditions, including the amount of renewable feedstock, product objectives, unit pressure, hydrogen-to-oil ratio, unit design temperature and temperature range of operation, and available catalyst volume or liquid hourly space velocity (LHSV).
Two key factors in this are obviously the desired product, whether it is SAF, renewable diesel or another product, and the volume of renewable feedstock to be coprocessed. These both dictate the operating conditions as higher volumes may require adjustments to the abovementioned conditions.
To determine the optimal operating conditions for coprocessing in a given hydroprocessing unit, a thorough evaluation must be conducted. This tailored approach, which Topsoe provides to customers, ensures the most efficient and effective conversion of renewable feedstocks into the desired end products.
Finally, it is worth mentioning that the type of feedstock used in the production of SAF via coprocessing generally has a minimal impact on the yield. However, lighter feedstocks, particularly those with a higher proportion of carbon chains below C16, tend to maximize yields.
These lighter feedstocks often have a lower molecular weight and fewer impurities, making the coprocessing procedure more efficient and resulting in a higher yield of SAF. Nevertheless, the specific yield also depends on the other factors mentioned earlier, such
as the operating conditions of the hydroprocessing unit.
Coprocessing renewable feedstocks in conventional refineries has emerged as a cost-effective and reliable technology to produce SAF and other renewable fuels. By understanding the suitable units for coprocessing, the necessary modifications, the optimal operating conditions and the impact of feedstock selection on the products yield, refiners can make informed decisions and drive the adoption of this production method, which is likely to be a key renewables pathway in the coming years.
Topsoe’s experience in coprocessing and in various SAF production pathways can be invaluable for customers entering coprocessing for the first time. A focus on proper evaluations and testing is obviously a key component in ascertaining how customer goals can be met. It also defines the optimal design of the production facility. When there are new, unique requirements, this is more important than ever.
But critically, when refiners are assessing new revenue streams, there needs to be constructive, forward-thinking dialog—this ensures that everyone is on top of the latest developments, the customer’s goals are always in sight and there is high transparency in terms of technology and design. The question, “If we change that, then how will that impact other factors?” is a recurring conversation, but one that makes sure aims are met.
This open dialog also builds customer trust for the long term, where Topsoe becomes a value-driving partner and not a licensor making a one-off sale. You could say Topsoe is onboard with customers for the long haul.
Authors:
Maria J. L. Perez Senior Product Line Director for Clean Fuels & Chemicals-Catalysts
Topsoe mlp@topsoe.com
Milica Folic Product Line Director for Clean Fuels & Chemicals-Technology Topsoe mfol@topsoe.com
The journey to cleaner skies starts now. Sustainable aviation fuel is no longer an experiment but a prerequisite for low-carbon air transport. Industry players, passengers, and the planet will benefit. And our range of proven green-energy technologies is ready to help you produce more in-demand, renewable SAF.
Turn your sustainable ambitions into a sustainable business.
Join Flight Plan Green. Find out how: topsoe.com/saf
By Brandon Day
Innovation is the lifeblood of the renewable energy industry. Biobased diesel resulted from fostering and encouraging innovation, a process that must continue.
U.S. soybean farmers supported early innovation in the biobased diesel industry. Soybean oil now comprises more than 50 percent of the feedstocks used for biodiesel production, and it has grown to more than 25 percent of the feedstocks used for renewable diesel, according to University of Illinois analysis. As the biobased diesel industry grows, that demand is expected to increase.
U.S. Soy is rising to the challenge of meeting that potential demand, reporting plans for increased crush capacity. In 2023, three soybean-crush plants expanded capacity and a new plant opened. Plans are in progress for 12 new soybean-crushing plants and five expansions to be operating by 2026.
The Soy Innovation Challenge 2023 was launched to address that growing demand for soybean oil for diesel by encouraging new and novel markets for the soybean meal also produced from crushing, as well as whole soybeans and other soy components. The Yield Lab Institute with the United Soybean Board, which wholly funded the challenge, and AWS Startups aimed to advance creative solutions that use U.S. soy to address real-world challenges.
The challenge invited entrepreneurs from around the world to share their ideas and technologies. Innovation can come from anywhere and anyone, and the 69 applicants came from five continents. They are working on soy-based solutions for everything from food to adhesives and cosmetics to petrochemicals. The applicants included six from the biofuels and energy sector.
From this group, a diverse panel of experts vetted applications. These judges selected four finalists to participate in a venture-accelerator program and compete for cash investments from U.S. soybean farmers provided through the soy checkoff.
“I know soy has many uses, but I learned about many innovative concepts I hadn’t considered as I reviewed each application,” said Shannon Tignor Ellis, a farmer from Champlain, Virginia, and a USB director who served as a judge to represent the investors. “It was eye-opening to see what ideas and applications exist. The finalists represent all the applicants well.”
The Soy Innovation Challenge 2023 finalists will drive use of soy forward as the biobased fuel industry grows, with similar themes of improving sustainability and reducing dependence on petroleum.
An innovative fermentation process from Clean Label Solution delivers high-value feed for beef and dairy cattle from soybeans and soybean meal. Soybeans provide foundational nutrients, but cattle couldn’t eat much because the oil was toxic to them. The proprietary process allows more soy to be used in this feed, replacing palm oil, a less sustainable ingredient. In trials with farmers, these soy-based products allow cattle to digest the 30 percent of soy protein that otherwise passes through the animal without being used. This boosts milk and meat production while curbing methane emissions. That improved efficiency saves farmers about 30 cents per head per day. This leads the way toward a more sustainable, efficient future for livestock agriculture.
“
The challenge invited entrepreneurs from around the world to share their ideas and technologies. Innovation can come from anywhere and anyone, and the 69 applicants came from five continents. They are working on soybased solutions for everything from food to adhesives and cosmetics to petrochemicals.
In a much different industry, Eden Concept Fill has developed a fully sustainable cushion alternative to polyurethane foam, which is the petroleum-based industry standard for soft fill in furniture, mattresses, seats in cars and planes, and much more. Its product, Cellyfill™, is a near 100 percent cellulose-based material that can be made from soy hulls, the thin shell on soybeans often removed as waste during crushing.
Cellyfill™ provides biobased cushion fill with performance equal to or better than synthetic polyfoam. It offers manufacturers and consumers a lower cost, more environmentally friendly option for soft seating and mattresses. Global industry estimates show that using an alternative like Cellyfill™ in place of synthetic polyfoam could eliminate 1.1 gigatons of carbondioxide emissions by 2050, representing 42 percent of the United Nations’ targets.
In the medical-technology field, NeuEsse is harnessing the healing power of soy by creating a human-skin substitute, OmegaSkin™, made from soy protein. This medical solution helps cover and heal serious wounds and burns with minimal scarring. The soy protein in OmegaSkin™ becomes a scaffold for the body to regrow its own skin over a wound or burn, and it is much more costefficient than current treatments like skin grafting, skin substitutes or advanced cellular therapies.
“
New markets for soybeans and soybean meal will complement the demand for soybean oil for biobased diesel.
Studies show OmegaSkin™ gradually degrades and integrates into wounds. It supports the body’s natural wound closure, allowing healing to the full thickness of the skin, while generating functioning hair follicles and sweat glands. Those wounds heal with the person’s natural pigmentation and skin color, an advantage compared to current options.
is making plastics and polymer building blocks from soybean meal and its constituents to improve the sustainability of some plastics. The company aims to become a plastics supply house that makes soy-based plastic beads and plastic additives that customers can melt and mold into a variety of more sustainable plastics. While Henry Ford introduced this concept in his first cars, modern technology and techniques are advancing it.
Some plastics should be compostable, and using soy protein for much of the material can make that possible. Soybased plastics have potential for use in nondurable outdoor applications like golf tees, Airsoft BBs, string weed-trimmer
line, lawn toys and more, as well as impact-resistant packaging and rigid flame-retardant uses.
“Regardless of the U.S. Soy investment each finalist receives, I hope participation in the Soy Innovation Challenge helps keep all these companies moving forward,” Ellis says. “When they win in the market, we all will win.”
New markets for soybeans and soybean meal will complement the demand for soybean oil for biobased diesel. At the same time, we will all have access to more sustainable options for fuel, cushions and plastics; a natural, sustainable skin substitute; and a more sustainable way to produce dairy and beef products.
To learn more, visit thesoychallengelive.com, and watch for information from the Soy Innovation Challenge. It can be a complementary platform to advance the next generation of innovations for renewable energy.
Author: Brandon Day Chief Operating Officer
The Yield Lab Institute brandon@theyieldlab.com
Available this July, the all-new, third-party recordsharing portal by Reiter Software will offer a powerful solution for both parties.
By Kristof Reiter
For years, U.S. EPA has emphasized the need for detailed records that account for the point of origin of used cooking oil (UCO) to root out fraud. The original fraud problem was oil stolen from restaurants and other businesses that was not traceable. While that’s still a huge problem, now there appears to be skyrocketing import fraud, pertaining to foreign palm oil intentionally mislabeled as UCO. Investigations are taking place in the European Union at the request of Germany to identify fraudulently labeled virgin palm oil. The U.S. is following suit.
The American Soybean Association pointed out in April that the EU imported 600,000 fewer metric tons of UCO from China in 2023 than it did in 2022. At the same time, the U.S. imported over 700,000 tons more.
It wasn’t until the past few years though that this issue came to a head in a way that limited options for both buyers and sellers.
Because of the perceived fraud risks associated with UCO, many buyers/producers don’t want to assume the risk of working with sellers who are unable to provide detailed records prescribed by EPA—including the addresses, date and quantity of oil collected from each service location. This limits the number of collectors they can purchase from. Additionally, UCO collectors may be hesitant to share those records with buyers who also operate competing UCO-collection companies and have been known to request audits for the purpose of gaining commercially valuable data. In these cases, the combined buyer/collector acts as both buyer and competitor to the UCO-collection company.
In order to solve the growing problems of fraud without damaging the commercial viability of independent UCO collectors, a record-sharing platform must meet certain requirements and contain the following features:
● Records cannot be double allocated. After gallons from a particular pickup have been allocated to a particular sale, they must be locked.
● Records must be protected from those with conflicts of interest, and only shared with appropriate auditors.
● Buyers must have analytical tools to assess records quality, such as a histogram of collection volumes in the batch, GPS confirmation data, and the “age” of the included records.
● Auditors must be able to quickly review data to identify any loads that need further follow up. By making the auditor’s job easier, audit costs can be decreased.
● Sellers need access to the tools necessary to protect their data without creating a liability for buyers.
● Both buyers and auditors need access to analytical tools that make insuring compliance easy.
● It must not be possible to bulk upload records.
Route Simplified is proud to announce it is offering a solution for both parties: the all-new, third-party record-sharing portal coming this summer in July. Route Simplified will give the collector simple control and access to their collection data while making it easy to share noncommercially valuable data with the customer, and the full unredacted records with approved third-party auditors who are bound by nondisclosure and nonuse agreements.
Route Simplified is Reiter Software’s latest iteration of routebuilding software for UCO collectors. Reiter Software has always been the most powerful tool on the market for UCO collectors, capable of building the most efficient routes possible based on the predicted fill rates of each individual kitchen.
Reiter Software has been a market leader in software designed for UCO collectors since its 2017 release of the Cooking Oil Service Tier. Since the early days of COST, however, the number of users requesting to use the Reiter platform has more than tripled. This growth required Route Simplified to employ new Amazon and Google technologies to keep pace with user growth and expectations.
Ultimately, the second generation of UCO-collection software was launched under a new name: Route Simplified. Leveraging Amazon’s AWS, Microsoft’s .NET and Google’s Flutter technology positions Reiter’s latest offering—Route Simplified—to remain fast, powerful and stable for decades to come as its use expands not only in North America but around the world.
Route Simplified is not a “records-storage system.” Users cannot “upload records” from a spreadsheet into the system— this process is prone to fraud. Rather, Route Simplified is an operation platform designed to improve the operating efficiency of legitimate oil collectors, generating records at the moment of pickup. The only way to create records in Route Simplified is by running routes. This dramatically decreases the likelihood of the upload of bulk, fraudulent data.
If collectors are using Route Simplified, buyers never have to worry about liability during an audit again. All of their sellers’ collection records will be safely stored in the software at the moment of pickup, ensuring buyers know the records are complete and available. In the event of an audit, all buyers have to do is make a request for the collector to share the unredacted records directly with the auditor.
In the past, buyers could amass a year’s worth of liability before discovering that a seller did not have adequate records. Now, prospective buyers can ask the collector to share data from the very first shipment onward, substantially limiting RIN and LCFS compliance risk. Because allocating and sharing records is easy for Route Simplified users without compromising their confidential business information, there’s little friction in building new buyer/seller relationships. When the data starts flowing between parties, Route Simplified’s proprietary analysis tools make spotting risks quick and easy.
The software has consistently helped collectors maintain and organize records by collecting pickup dates, locations and volumes in the program, but now collectors will be able to instantly share that data with other parties in a simple, controlled and secure format with just a few clicks.
If collectors need to prove to a new buyer that they have the records the buyer needs without having to share all of their confidential business information, Route Simplified has an answer for that. Users can send a simplified version of their collections data that excludes confidential business information, such as the names and addresses of restaurants. The buyer can use Route Simplified’s propriety fraud-detection tools to gain confidence that the collector is maintaining high-quality, legitimate records.
With Route Simplified, collectors are in full control of their confidential business data—the names and locations of their clients—but the buyer gets a high degree of confidence that the records are, in fact, legitimate.
Author: Kristof Reiter CEO, Reiter Companies 888-428-5617
kristof@reiterscientific.com
Biobased Diesel™ conducts a Q&A with Manfred Baumgartner, CEO of BDI-BioEnergy International, about the company’s foray into renewable diesel pretreatment.
Q: What led to BDI’s desire to enter the renewable diesel and sustainable aviation fuel (SAF) refining market with its Advanced PreTreatment technology?
A: It was a logical decision for BDI to enter this market, as our knowledge about feedstock purification dates back to the beginning of our business with biodiesel [in 1996]. These days, the most sought-after feedstock for renewable diesel or SAF are waste oils. At BDI, we decided already back in the mid-1990s to focus on waste oils for biodiesel production. So, we developed technologies for biodiesel production especially designed for the properties of waste oils. If a plant is to run smoothly and without unexpected disruptions, proper pretreatment of the waste oils is necessary. We have gained extensive knowledge about this topic over the years.
Q: How does BDI’s Advanced PreTreatment system for renewable diesel and SAF differ from other available pretreatment systems?
A: There are different technical approaches on the market. BDI is able to deliver a wide range of technical solutions, which are used in a modular approach. In other words, we add specific process units, depending on feedstock, product and customer requirements.
I want to highlight two main differences. Our first process unit is called the PrePurification process, which is the key for using waste oils. This process has been proven since 1998 and has many advantages. It purifies the feedstock using a very robust technology, which is necessary for the kind of impurities in waste oils. All impurities have to be taken out in an efficient way, as they can create a gluey sludge. The system is therefore designed in a way to handle this without issue.
This process entails an initial washing stage followed by a three-phase centrifugation using a horizontal centrifuge called a decanter. If one were to use a vertical centrifuge—a disc separator—the risk of fouling inside the machine (followed by a shutdown and cleaning actions) would be increased. In addition to this higher plant availability, the yield is also higher with our PrePurification process, as there is no excess oil loss during this first process unit.
There is a second noteworthy unique selling point at BDI, which I want to highlight. We have nearly 30 years of expertise in handling waste oils. This knowledge results in a very flexible plant design and plant operation. First, we take all feedstock properties into consideration for the design. I think it can be explained by the following: If we are designing a plant for vegetable oils, where the feedstock properties and quality stay very constant, the plant design will be much more streamlined. If waste oils are the feedstock, we design the equipment to be bigger, we consider fouling in a different way and we use different technical solutions. Secondly, when it comes to plant operation, our customers value our flexible design of the process-control
system. Waste oils can be different each day and this means that plant operators have to react, change settings, optimize recipes and adapt plant operations accordingly. This flexibility, attained through years of experience with waste oils, is not only essential but also significantly pays off.
Q: Could you describe the different stages of BDI’s Advanced PreTreatment process?
A: Different feedstocks and their qualities and customer requirements result in a certain plant configuration. Our modular approach of different process units is the basis for the final plant configuration.
Let me describe a standard process. It starts with our PrePurification as explained earlier and is followed by a second acidic washing stage using a vertical centrifuge. This is important in order to reduce water-soluble components as much as possible. Afterwards, we need to dry the feedstock in a flashvacuum dryer to a level appropriate for the next process unit.
In the adsorption process, filter media are added to adsorb the remaining impurities. Special types of bleaching clay are mostly used as adsorbents, but there are also cellulosic and silica-based types available. The selection of the right adsorbents for the application is part of our expertise.
The adsorbent is added to the oil and mixed for a certain time and afterwards filtered by a so-called pressure leaf filter. The filter cake is de-oiled and discharged. The filtered oil is moved to a polishing step to get out all fine solid particles.
Aside from PrePurification, this might sound like a standard setup—however, our experience with waste oils and the BDI design, as explained earlier, result in many small details, which characterize the BDI Advanced PreTreatment process.
In addition, other process units like polyethylene removal, deacidification, a second adsorption process or a final drying stage are also necessary for certain applications.
On the other hand, we also offer so-called high-temperature processes for removing impurities. This process configuration can reduce impurities to a lower level and can be beneficial for certain feedstocks, if the higher operating costs and the gained feedstock qualities are profitable.
Q: How might the needs or requirements of a prospective client determine the layout or steps included in their particular pretreatment design?
A: It is very important to consider customer requirements, site conditions or other customer aspects in the overall plant design as early as possible. A proper “project development” in an early stage is ensuring a safe investment calculation and a short project schedule. We at BDI support our customers in this regard, not only for the core process configuration, but also for the surroundings and infrastructure. Very often we start a project with pre-engineering, during which all these aspects are considered.
One important example is the planning of the logistics on
site. It starts with parking of trucks, sampling of the shipment— very important for waste oils—route optimization and so on. Another example is the solid handling on site. We bring in adsorbents and manage the removal of solid impurities of the feedstock and spent adsorbents. The movement of these solids requires a smart layout design, which we are happy to provide and optimize together with our customers.
Q: What differentiates BDI’s basic pretreatment design for renewable diesel versus biodiesel?
A: There is a clear answer—a hydrogenation process requires a much higher purity of the feedstock in order to lengthen catalyst lifetimes. Therefore, the pretreatment process also has to be more sophisticated. Different biodiesel technologies require different pretreatment levels.
The required high quality using reasonable operating and capital expenditures (opex and capex) logically exclude some feedstock types or qualities for this business—for example, extremely degraded feedstocks such as trap greases, or split fatty acids from soapstock splitting. However, these feedstocks can be processed into fatty acid methyl esters (FAME) using the appropriate biodiesel technology, such as our RepCat process.
Q: Can you share any references for a BDI system designed for renewable diesel/SAF feedstock pretreatment?
A: First, I want to mention a few highlights, which show our extensive expertise with waste oils. Our first pretreatment unit for used cooking oil (UCO) commenced operations in 1998, followed by one built in 2002 for animal fat, and palm-oil mill effluent (POME) purification in 2014. These plants and others show how we have been forerunners in this industry and evidence our experience.
Our latest plant configuration of our Advanced PreTreatment system for the renewable diesel/SAF industry is providing outstanding results and reaching lowest impurity parameters. These projects are all currently underway and we are working with very well-known customers. However, there are nondisclosure agreements (NDAs) in place and thus we are not allowed to speak about these projects. We take this very seriously to protect the business approach of our customers.
Q: I understand it may be difficult to enter a new market like renewable diesel or SAF in which large petroleum refiners are the prospective customers versus smaller-scale, independent biodiesel producers. Can you describe to me what challenges BDI has faced in gaining traction in this market?
A: You are right, there are new challenges with these customers. During the first discussions with refiners, before starting a project, we focus on a few topics that we need to explain to our customers and educate them on.
First, we need to explain the properties of the different feedstocks and the technical possibilities to treat them. For example, it makes no sense to use a feedstock with high free fatty acids (FFA) for coprocessing, where only low FFA are allowed. Capex and opex might be too high for certain feedstock configurations. However, with blending in certain quantities, the feedstock concept might be feasible.
Another topic is refinery standards. Refineries are all designed according to American Petroleum Institute standards, and in our business, we are used to typical chemical-engineering standards. We also can build plants according to API standards, but the investment will be about 40 percent more.
The topic of standards can get even more sophisticated. Big companies—with refineries of course being very big indeed— do have their own company standards. There are topics like details of the steel-structure design, typical pump-frame design, standards for sampling, and so on. For fulfilling these standards, a lot of additional engineering hours are needed.
So, we need to clarify, first, which standards are applicable in a new project in order to consider them in our price calculation.
Most of the refineries also have a well-defined project workflow with certain milestones. The projects are divided into phases: feasibility, definition and execution. And these phases are mostly split into two parts. There is a management review after each phase and a decision for moving ahead. This concept has its advantages, but the project schedule might be lengthened to up to five to seven years. If we compare the project schedule with a standard engineering, procurement and construction (EPC) project in our previous business, we took about two to three years for a full project execution. The project schedule does of course have a big impact on the business, especially as our customers are fighting for feedstock supply. The quicker a project is completed, the earlier the feedstock can be secured for it.
Q: How might BDI’s new parent companies affect how or where you seek to gain greater market share in this sector?
A: Our new owners, EOSS, Rieckermann and KVT Technology are all bringing in different new business opportunities. This means that BDI is moving into an interesting and dynamic future. Particularly with renewable diesel and SAF—our partnership with Rieckermann marks our entry into what is, for us, a new market. Rieckermann is a group of companies with a big customer base, active in the Asian market, and we are already working on new project opportunities, which hold considerable potential for growth.
Q: Is there anything else you would like to share with me?
A: There is one topic I would like to elaborate on. The goal of processing waste oils in a pretreatment process is to achieve the lowest possible amount of impurities at the end. Low phosphorous and metal contents lengthen the lifetime of the very expensive catalysts of a hydrogenation unit. We at BDI support our customers in achieving the best product results by transferring all of our knowledge in this field to manage production in the best way. We have developed a method to run and optimize a pretreatment plant, called Analytical Management. By analyzing feedstock, standardizing lab testing of feedstock, and analyzing the results of all production units and product qualities, we optimize the plant operation in order to minimize operating costs and maximize product quality.
Furthermore, we are able to implement this system in a semiautomated way using Advanced Process Control, which uses past data, mathematical models or artificial intelligence (AI) in order to optimize the process.
With fluid-film bearings, increased speed in canned-motor pumps results in greater film stability and load capacity, providing higher and more efficient performance with a much smaller footprint and lower cost.
By Jim Hoffman
It is common practice for centrifugal-pump specifications to be based around low-speed operation—typically 1,750 revolutions per minute (RPM)—in the interest of increasing mean time between maintenance (MTBM) and failure (MTBF). This idea is rooted in the effect of rotational speed on the expected lifespan of mechanical components found in many centrifugal pumps such as mechanical seals, ball or roller bearings and couplings, which are designed into rotating equipment with a finite life expectancy.
Sealless centrifugal pumps have gained significant traction in the renewable fuels industry over the past two decades in both inside battery limits (ISBL) and outside battery limits (OSBL) services as a result of evolving regulatory requirements centered on leakage containment and controlling emissions. Available sealless pumps are either magnetically driven or hermetically sealed canned-motor pumps. While both
technologies do away with mechanical seals, the former relies on conventional ball bearings and an electric motor coupled to a ball bearing-supported shaft through a coupling, very much like its traditional, mechanically sealed counterpart. Cannedmotor pumps take reliability and realistic operating parameters to the next level by completely removing ball and roller bearings, couplings and all associated alignment from the equation and instead utilizing one single, solid rotating element supported by two hydrodynamic fluid-film bearings fed by either a slip stream of the process fluid or any other process-compatible flush fluid depending on the application.
Unlike ball or roller bearings, fluid-film bearings eliminate mechanical contact by supporting the rotating element radially with a thin, pressurized fluid film between the inside diameter of the bearing and the outside diameter of the shaft journal. These sleeve-type bearings are available in a variety of process-
compatible materials. Most importantly, the thickness of the film and therefore its stability and radial-load capacity scales with rotational speed. Such bearings have a quantifiable bearing-characteristic rating known as a Sommerfield number, which relates various factors such as viscosity, RPM and radial load to determine the film thickness for a given bearing.
Utilizing no-contact bearings provides a major advantage when considering MTBM and MTBF intervals as the technology is designed for zero wear to occur during normal operating conditions. Furthermore, the position of the rotating assembly in a cannedmotor pump is continuously monitored electronically to provide real-time indication of bearing wear and data to predict maintenance schedules based on pump operation.
Canned-motor pumps are configured considering an array of key parameters of the pumped fluid for a given application including, but not limited to, fluid viscosity, vapor pressure and motor-
cavity pressure to ensure no vaporization of the circulated liquid and that a robust fluid film can be maintained within the defined operating conditions. The fact that increased speed results in greater film stability and load capacity presents new opportunities beyond maximizing reliability, including the ability to achieve significantly higher and more efficient performance with a much smaller footprint and lower cost.
As a scaled comparison, consider a duty point of 50 gallons per minute at 80 feet of total dynamic head (TDH). At 1,750 RPM fixed-operating speed, this job can be done with a 2x1-10inch hydraulic. When speed is doubled, however, the same performance can be achieved with a 1x3/4-5-inch hydraulic, requiring less power. Increase speed to 6,000 RPM and impeller diameter is reduced to 3 inches, requiring even less
Single-stage canned-motor pump size comparison with increased rotational speed.
IMAGE: TEIKOKU USA INC.
power, and so on, while effectively moving the duty point closer to the best efficiency point.
The ability to reduce physical-equipment size and power consumption is underpinned by centrifugal-pump affinity laws, but there is even more at play behind the scenes. Consider windage, for example. A spinning disk (impeller) in a liquid is subject to a viscous drag proportional to [disk diameter]5 Therefore, if an impeller diameter is halved, viscous drag is reduced by (1/2)5 or a factor of 32x. This effect is compounded for multistage pumps using more than one impeller. Consider, for example, that a 12-stage pump at 85 hertz (Hz) can do the same job as a 16-stage pump at fixed 60Hz speed.
Multistage canned-motor pump size comparison with increased rotational speed.
IMAGE: TEIKOKU USA INC.
It is also important to note that typical induction motors for centrifugal pumps are most often designed for operating speeds up to 50Hz or 60Hz at full voltage. When a variable-frequency drive is used to increase speeds above the nominal frequency, the voltage has already reached its maximum and, therefore, as frequency increases so does current draw per Ohm’s law.
High-speed canned-motor pumps solve this issue by employing a specialized motor-winding system designed for say 120Hz at full voltage, thereby maintaining the voltage-tofrequency ratio at any frequency below 120Hz.
Inherent to its design, canned-motor pump technology encompasses all the advantages sought by rotating-equipment operators, particularly in the renewable fuels sector where containment, sustainable operation and environmental friendliness are highly valued. These advantages include dual containment, ease of operation and maintenance, extended MTBM and MTBF intervals relative to alternative technologies and significant physical-space cost savings when considering high-speed solutions that only canned-motor pumps can offer.
Representation of output power versus speed for typical 460V/60Hz induction motors versus high-speed motor design.
Author: Jim Hoffman Eastern Regional Business Manager Teikoku USA Inc. 267-485-4094 jhoffman@teikokupumps.com
Climate action is most effective at the local level, where collaboration and problemsolving take flight while world leaders remain locked in analysis paralysis as the climate crisis rages on.
By Kelly King
In my editorial series these past few issues of Biobased Diesel™, I have focused on the multitude of environmental and economic benefits of community-based biodiesel. As the longest operating community-based company in our industry, Pacific Biodiesel has become the poster child for the circular economy in Hawaii.
This issue, on the heels of two meaningful events we’ve recently hosted for our community, I am inspired to focus on the “community” aspect of our model at Pacific Biodiesel that integrates local regenerative agriculture for “food then fuel.”
This past April 22, Earth Day, our team held a traditional Hawaiian Blessing to mark the planting of our first sunflower field on the island of Kauai, following our federally funded expansion of agriculture operations we announced in the Winter 2024 issue of Biobased Diesel™. That morning, Bob (my husband and president of Pacific Biodiesel) and I felt a true sense of joy and positivity as we were warmly welcomed into this island community. It was a familiar feeling we’ve
experienced often in the 30 years since we founded Pacific Biodiesel on Maui.
Community is how Pacific Biodiesel has grown over the years. We go where we are welcomed. When we outgrew our first two biodiesel plants (on Maui and Oahu) and needed to expand and enhance biodiesel production, the community on Hawaii Island rolled out the red carpet and expressed all the reasons they wanted our company to build our next biodiesel facility on their island. Bob and I were courted by several community groups to put our new, state-of-the-art biodiesel refinery on the Big Island, and we were sincerely touched by their deep understanding of the benefits of locally produced renewable fuel.
Similarly, when it came time for our agriculture operations to increase through regenerative farming of local feedstock for our biodiesel production, community members on Kauai welcomed us with open arms. The leadership team at Gay & Robinson Inc., longtime landowners and one of the last Hawaii sugarcane
companies to close its plantation, made it easy for us to get a running start by making available existing warehouse space on their property and access to thousands of acres of land they intend to keep in agriculture.
A few weeks later, on May 4, we held our third annual sunflower farm music festival. Bob and I were thrilled to once again make our Maui sunflower fields available for this community cause—a farmers market, farm tours, and a musical gathering for our Maui community. Throughout the day, we celebrated those who are doing the hard work to grow food security on our island and throughout our state. The event benefitted three nonprofits that are working on food sovereignty in real time on Maui: Common Ground Collective, Maui Hub and Grow Some Good. All in collaboration with our widening circle of friends in the local and global music community thanks to Kerry Brown, who produced this year’s event, and his team
at Licorice Pizza Records. In a big way, it brought me back to the beginnings of the biodiesel industry when we had huge support from celebrities like Willie Nelson, Woody Harrelson, Daryl Hannah, Pat Simmons, Neil Young and others who saw the sustainability we were striving for and lent their voices to the cry for more local production.
Community-based biodiesel is the best example of the circular economy. It supports food and energy security, jobs and local revenue, which are especially important on Maui where our community is still reeling from last year’s deadly fires. All of these urgent issues are interconnected and crucial to surviving and thriving in our island state, the most isolated population on the planet.
It reminds me of concentric circles starting with me and Bob and our ‘ohana (family) outward to our 100 employees statewide, to our customers and local communities across Hawaii, and further outward to fellow renewable
fuel producers and industry groups around the nation like the Maine Energy Marketers Association, which, after reading my editorial in the Winter 2024 Biobased Diesel™, invited me to speak at its Northern New England Energy Conference this June. It is both comforting and frustrating that our country’s climate-response plans, which continue to ignore the superior greenhouse-gas (GHG) reductions of locally produced biodiesel, are of concern from coast to coast.
In a recent planning call with the MEMA CEO and leadership team, I learned what resonated with them about my editorial: that total electrification of on-road transportation is not the silverbullet solution it’s often made out to be. In fact, America’s trucking industry is pushing back, demanding to keep their existing diesel fleet and simply switch to renewable fuels like biodiesel. There are significant economic factors such as the heavier loads (with battery requirements) and reduced operating hours of electric vehicles (EVs)—all expenses that would be passed on to consumers. Also, for colder climates, biodiesel as a firm liquid fuel is preferred over EVs for states like theirs that experience extreme snow and ice storms, which can shut down power grids and make electrification unreliable. They shared that polling in their state over the past two years indicates 91 percent of registered voters want a choice on how to heat their homes and fuel their vehicles. Offering choices and promoting a mix of renewables is our standpoint as well. EVs and solar power are important options, but in addition to—and not instead of— other community solutions.
It was astonishing to me that two states in geographically opposite ends of the United States would have so many economic and environmental similarities in the nexus of renewable fuel. I found our conversation that day refreshingly collaborative as we shared resources and experiences while preparing for my upcoming presentation.
In my years as an elected Maui County councilmember, a member of the Local Government Advisory Committee to the U.S. EPA, and a board member with ICLEI USA (ongoing) that resulted in my invitation to participate in two
consecutive Conference of the Parties events as a presenting delegate, I’ve become convinced that climate action is most effective at the local level. Local communities are where collaboration and problem-solving take flight, faster than world leaders who seem locked in analysis paralysis as the climate crisis rages on.
This is why our mission statement has been the same for three decades—to promote a clean, sustainable energy future through the community-based production of renewable fuels. In the mid-1990s, when my diesel-mechanic husband Bob King saw the problem of dumping used cooking oil into the Central Maui Landfill and took the initiative nearly 30 years ago to find a solution, Pacific Biodiesel opened the first biodiesel pump in America and has been producing commercially viable renewable fuel in our state ever since. Seeing grassroots leaders like student climate activist Greta Thunberg, whose singular unwavering focus on spearheading weekly climate strikes as a peaceful means to challenge world leaders, is encouraging; however, it is really up to cities, towns and counties to take immediate action to solve the climate crisis for her generation. I have participated on panel discussions with mayors and councilmembers from across the country, and even from other countries like Brazil and Scotland, and we all agree that the actions taken locally are more meaningful, effective and can outlast any dictatorship that might try to reverse climate actions at the national level.
That Earth Day blessing at our first sunflower field on Kauai included a group of students and teachers from the STEM and agriculture programs at Kauai High School. Seeing
the students light up when Bob invited them to climb onto our innovative new tractor to view its GPS-based planting technology made us smile.
While it has been a lot of hard work, sacrifices and dedication to get to where we are today, there has never been a moment of resting on our laurels. Changing political will, logistical challenges and climate disasters such as the recent devasting wildfires that destroyed Lahaina all affect our bottom line, and we are constantly pivoting to compensate for these setbacks. But with perseverance, we managed somehow to get our kids through college and are working on the next generation now. Bob and I are proud to be pioneers in this industry and get excited when we see our future leaders step up, take interest in agriculture and renewable energy careers, and generally roll up their sleeves to demonstrate what true community is all about.
The big question to the next presidential administration is, “Are you with us?”
Author: Kelly King Co-founder, Pacific Biodiesel ktk@biodiesel.com