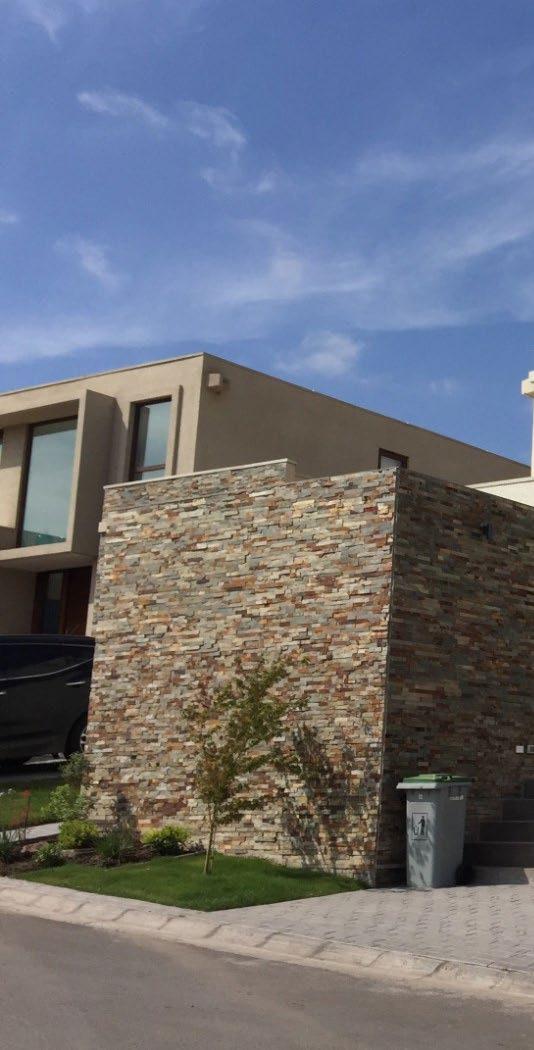
13 minute read
AVANCE EN LA CONSTRUCCIÓN VIVIENDAS REFABRICADAS DE HORMIGÓN LA EXPERIENCIA DE DETECO
Si bien su presencia en el país se observa desde hace varios años, la relevancia que toman los sistemas de prefabricación industrializados -en especial, los de hormigón- en el último tiempo, muestra cómo el sector de la construcción comenzó un tránsito desde los sistemas tradicionales “in situ” hacia aquellos en los que se usan sistemas estructurales y elementos constructivos que se producen en ambientes controlados de fábricas especializadas, con todos los beneficios que ello implica para la buena ejecución de cada proyecto.
Otro factor que aportó a esta nueva realidad dice relación con el confinamiento al comienzo de la pandemia y los protocolos sanitarios, en especial, aquellos relacionados con distanciamientos sociales y aforos. En ese sentido, los sis- temas industrializados que trabajan con prefabricados de hormigón lograron, por sus características, sortear de buena manera estas condiciones y sus actores lograron, si bien no reemplazar el volumen de proyectos, acotar su impacto y preparar el camino para futuras obras.
Advertisement
Así lo explicó Francisco Cañete Arratia, director comercial y fundador de DETECO, “Desarrollos de Tecnologías para la Construcción”, empresa especializada en el diseño, producción y montaje de paneles prefabricados de hormigón para edificaciones, quien destacó que “en el confinamiento, muchos proyectos se paralizaron y muchos dejaron de existir, entonces, hubo más tiempo para hacer una siembra que, actualmente, estamos cosechando”.
Ante esto, desde DETECO subrayan que su sistema de paneles prefabrica- dos de hormigón cuenta con todas las capacidades para realizar proyectos de corte tradicional -viviendas de uno y dos pisos, townhouses y edificaciones de hasta 4 y 5 pisos, que son los que más ven- hasta aquellos que, por características definidas por el mandante, se pueden calificar como especiales, mostrando así la versatilidad del sistema.
Un sistema industrializado, pero basado en la experiencia previa
A la hora de hablar de construcción industrializada y prefabricación, no existe un sistema único. Los hay robotizados, semiautomatizados, o con distintos grados de integración de mano de obra en fábrica. Para el caso de DETECO, su sistema actual, de producción continua semiautomatizada, nació de “los más de 10 años de experiencia que teníamos prefabricando en modalidad batch”, dijo su director comercial y fundador.
Con más de dos décadas en el mercado, el sistema industrializado de paneles prefabricados de hormigón armado de DETECO da evidencias de una muy buena salud, estando presente en una gran cantidad de proyectos habitacionales de todo tipo, con mayor relevancia en casas y townhouses de dos y tres pisos de altura. Sus principales ejecutivos comentaron las distintas posibilidades que ofrece su sistema constructivo, destacando la versatilidad y las diversas soluciones que éste ofrece.
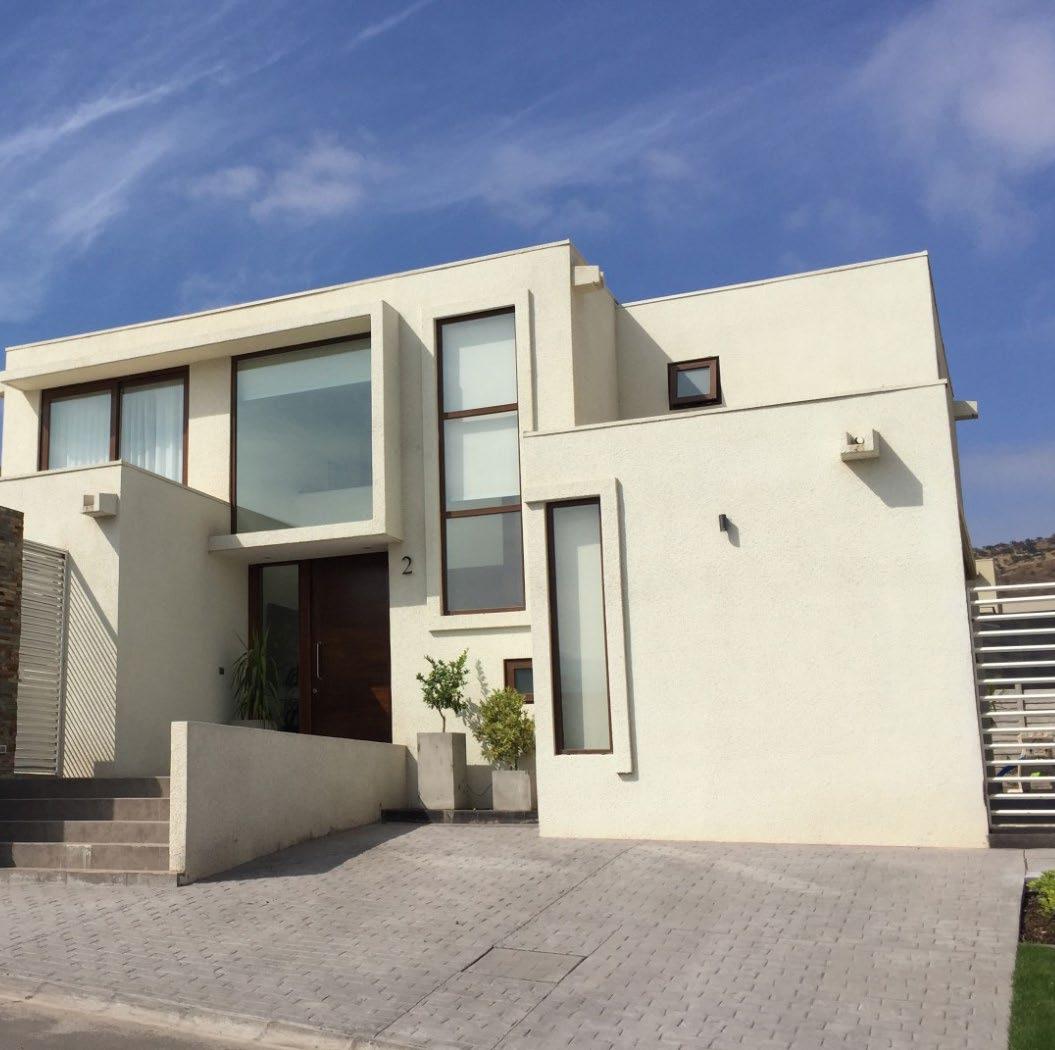
De acuerdo con el sitio web de la compañía, éste se compone de un “sistema de carrusel continuo, lo que permite contar con estaciones especializadas en encofrado, enfierradura, instalaciones eléctricas y sanitarias, permitiendo controlar la calidad en cada parte del proceso”.
Francisco Cañete puntualiza: “se trata de un sistema tipo carrusel sin robotizar totalmente la producción, pero sí mecanizar y hacer más industrial una producción que ya sabíamos cómo hacerla en batch”.
-Si bien la planta, como mencionan, no es robotizada, ¿el sistema posee un grado de automatización?
Guido Sepúlveda: Así es. La logística interna, es decir, todo ese sistema de carrusel que menciona Francisco, está dirigido por dispositivos electrónicos programables que gobiernan todos los movimientos de los paneles y de las plataformas metálicas mesas sobre las cuales éstos se fabrican, conduciéndolos a las distintas etapas del proceso, tales como moldeo, armado de enfierraduras, instalación de pre-embutimientos, hormigonado o la etapa de curado.
En esta misma línea, el gerente general de DETECO agregó que “también existe un elevador inteligente de paneles que los va a guardar cada uno a su respectivo casillero en las cámaras de curado y después, el mismo sistema los retira, bastando para ello digitar el número correspondiente. De esta manera, tenemos un sistema de logística muy interesante, con un buen estándar tecnológico”.
Además de la experiencia en el mundo de la ingeniería civil, del hormigón y del prefabricado de ambos ejecutivos, antes hubo un trabajo de investigación exhaustivo en el que se visitaron plantas de similares características en países como España y Alemania, los más aventajados en lo que respecta a producción industrializada de prefabricados de hormigón.
“Luego de estas visitas -dijo Francisco Cañete- diseñamos nuestra propia planta, que fue concebida con crecimientos programados. Se pensó para que fuese creciendo en el plazo que establecimos y hoy en día, hemos aumentado en el orden de un 30% aproximadamente la capacidad inicial y tenemos capacidad para crecer un tanto más”.
Potenciando la velocidad y la logística
Una de las cualidades que se resalta permanentemente de los sistemas prefabricados es la velocidad. Al tener los elementos ya listos, éstos sólo deben despacharse al sitio de obra para su posterior instalación, incrementando el ritmo de avance del proyecto y, por consiguiente, aumentando la productividad del proceso.
Conscientes de esa característica, en DETECO buscaron darle un valor agregado. “En la fábrica, nos gusta prefabricar no más allá de un par de días antes de montar los paneles en camión e ir a terreno. Hacer lo contrario significa tener acopios, tanto en fábrica como en obra, que no agregan valor desde el punto de vista de la productividad que brinda el sistema”, explicó Francisco Cañete.
-En ese punto, ¿de qué manera el sistema de DETECO asegura una velocidad constante para la fabricación de los paneles?
Francisco Cañete: Por condiciones de desencofrado a temprana edad, uti- lizamos un hormigón que a las 24 horas debe tener una resistencia del orden de 10 MPa, el equivalente a 100 kg/cm2 y eso es constante en todo el año. Ocupamos dosificaciones tanto de invierno como de verano para que podamos cumplir con esta meta.
“Dentro del proceso prefabricación -agregó- está la incorporación de unos racks que tienen calefacción incorporada para apurar o privilegiar que el proceso de fraguado del hormigón, que es exotérmico, no pierda el calor que genera. Eso permite un curado del concreto que a las 24 horas es posible manipular estos paneles”.
De esta manera, aseguran los ejecutivos de DETECO, mantienen un controlado programa de producción que va en directo beneficio de la velocidad del sistema, permitiendo un despacho constante de los paneles prefabricados de hormigón. “El proceso productivo es igual, ya sea trabajemos para obras emplazadas en Puerto Montt, San Pedro de Atacama o dentro de la Región Metropolitana”, aseguró Guido Sepúlveda.
-El transporte, en este caso, es crucial para mantener la velocidad del sistema. ¿Qué pasa cuando este ítem, por cualquier motivo, se retrasa?
Francisco Cañete: Ahí lo que se hace es tener elementos de almacenamiento en obra, atriles, que permiten que si el camión N tuvo algún problema y se atrasa, llega a lo mejor el N+1. Antes, estos atriles permiten ordenar las cargas y montar readecuando la secuencia constructiva. Podemos efectuar estos ajustes y usar estas flexibilidades para que la grúa no paralice producto de algún problema logístico o algún incidente mecánico en el camino.
Tecnología del hormigón para los pa-
neles de Deteco
Dada las características y la importancia que tiene la velocidad de producción dentro del sistema de DETECO, se podría inferir que los paneles prefabricados de hormigón, sean losas o muros, deben tener algún aditivo especial o una aplicación distinta para mantener la integridad del material durante el proceso.
La primera exigencia, como ya comentó Francisco Cañete, es que el hormigón tenga una resistencia a las 24 horas que sea de 100 kg/cm2, ya que así, el panel prefabricado puede manipularse en la fábrica a través de polipastos y sistemas de grúa, dijo el director comercial de DETECO.
-En ese sentido, ¿se utiliza algún aditivo especial para conseguir la resistencia temprana del hormigón que requiere el sistema?
Francisco Cañete: Ocupamos una dosificación que, con el advenimiento de los aditivos, nos deja alcanzar este requisito. Hoy en día, empleamos un aditivo súper plastificante que, a una dosis comparativamente menor de cemento, nos permite alcanzar la resistencia temprana que comentaba.
Dado que se trata de aditivos de “alta gama”, comentó Guido Sepúlveda, el gerente general de DETECO dijo que el hormigón utilizado para la fabricación de los paneles “califica con holgura como un G30, pero tiene mejores prestaciones que un hormigón convencional, dado que además utilizamos un mix de agregados que le otorga a los paneles muy buenas condiciones para su comportamiento en fase plástica y de terminación superficial”.
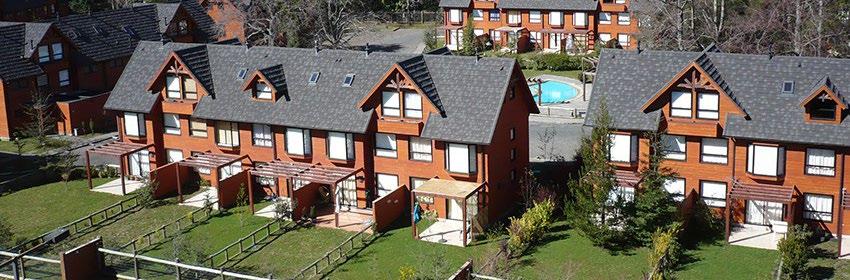
Al tratarse de hormigones con alta resistencia inicial, la fisuración por retracción del material es una condición que se está permanentemente gestionando, ya que se utiliza una menor cuantía de cemento en comparación a otros elementos fabricados con hormigón. “El tema de la fisuración -destacó Francisco Cañete- es inherente para todo prefabricador en hormigón armado”.
-¿Qué medidas tomaron en DETECO para combatir la fisuración en los paneles prefabricados por DETECO?
Francisco Cañete: Hemos incursionado en el uso de fibras. Hemos empleado distintos tipos y hoy en día utilizamos la llamada macrofibra, que es una fibra del orden de 4 a 5 cm de largo. Si bien no elimina totalmente la fisuración por retracción, sí la reduce notoriamente y es parte del proceso también, hacer un tratamiento especial en las fisuras cuando éstas superan los 0,3 ó 0,4 mm que, según nuestra experiencia, es lo suficiente para que luego la pintura o los revoques de yeso no la evidencien.
El profesional agregó que “se debe considerar que, luego de pasado el periodo fuerte de la retracción en el hormigón, la fisura es totalmente estable en el mismo y vemos, en base a nuestra experiencia, que fisuras con posterioridad a las tres, cuatro semanas, ya dejan de ser notorias o dejan de aparecer. Entonces, basta tratar aquellas que sí lograron tener un espesor que lo amerita, lo queda establecido contractualmente y no hemos tenido problemas serios por fisuración”.
Optimizando los beneficios de los paneles prefabricados de hormigón armado
Dadas las características tanto en la logística interna, la fabricación y la tecnología aplicada al hormigón, el sistema industrializado con el que trabaja DETECO brinda una serie de ventajas, más allá de las inherentes a la construcción industrializada, tales como velocidad en obra e incremento en la productividad.
En ese sentido, uno de los aspectos del sistema más interesantes es que existe una certeza en cuanto a la geometría de los paneles, ya que “todo vano del sistema queda dentro de un marco de tolerancias que es prefijado en el contrato inicial y que se cumple satisfactoriamente”, explicó Francisco Cañete.
Asimismo, el director comenrcial de DETECO destacó que, por las características del sistema industrializado de la planta, la obra gruesa se genera íntegramente con los paneles prefabricados. “Las únicas uniones frescas que demanda nuestro sistema son solamente las costuras de losas en terreno”, puntualizó.
“En rigor -complementó Guido Sepúlveda- desde el punto de vista de la obra gruesa, la constructora ejecuta solamente las fundaciones. El área de ingeniería de DETECO y el equipo de proyectistas diseñan las fundaciones, cuyos planos y especificaciones enviamos como primer entregable al cliente. Una vez ejecutados los cimientos, procedemos a verificar su conformidad con el diseño y si eso está cumplido, DETECO comienza el proceso de montaje, período en el que el cliente puede dedicarse a otras actividades.
Solamente debe incorporarse antes que DETECO vaya a efectuar las costuras de losa, asegurando que las conexiones de los conduit eléctricos entre losas vecinas son las que corresponden. Todo el resto de la construcción de la obra gruesa, las uniones y los tratamientos de junta, los hace DETECO, lo que permite muy importantes ahorros de recursos al cliente”.
-Dado que se demandan edificaciones que sean energéticamente eficientes, ¿cómo logra el sistema de DETECO al- canzar dicha eficiencia?
Guido Sepúlveda: Nuestros paneles son aislados térmicamente. Poseen prismas de poliestireno expandido en su interior que mejoran mucho el comportamiento térmico de los paneles y, por lo tanto, con la actual normativa vigente, nuestros muros no necesitan aislación hasta la región de Valdivia.
Francisco Cañete: Cumplimos holgadamente hasta la zona 5, de las 7 que subdividen a todo el territorio, sin incorporar ninguna aislación exógena, sino que la propia que acaba citar Guido, que, dicho de paso, está validada a través de un ensayo normado del Dictuc.
Con esto, comentaron los profesionales, no sólo se genera un gran ahorro energético, sino que, también, la “huella de carbono” de las casas o edificaciones construidas con el sistema de DETECO es significativamente menor. “Lo que hacen los prismas de poliestireno expandido es contrarrestar de alguna forma la transmitancia térmica potente del hormigón. Entonces, el diafragma exterior se está calentando dado el sol y esta membrana intermedia, que tiene poliestireno expandido, permite que ese calor no inunde, por así decirlo, al diafragma interno y permite una mejor habitabilidad”, explicó Cañete.
Junto con esto, el sistema de prefabricados de hormigón de DETECO también brinda una alta resistencia a sismos de alta intensidad, además de reducciones en faenas complementarias, las que se traducen en una disminución considerable de escombros, explicaron los ejecutivos de DETECO.
El camino actual de Deteco
En la actualidad, si bien la mayor cantidad de proyectos que DETECO ejecuta están asociados a casas y townhouses de hasta dos o tres pisos de altura, desde la empresa comentaron que, al estar certificados por la Ditec del Ministerio de Vivienda y Urbanismo, Minvu, pueden participar en edificaciones en altura como elemento complementario a la estructura principal.
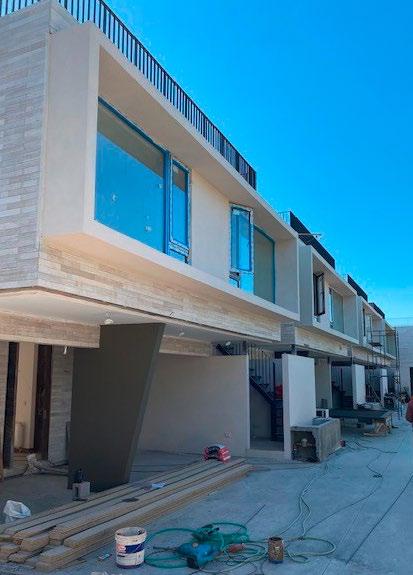
Además, el sistema de paneles prefabricados de hormigón de DETECO también se ha utilizado para edificios. “En nuestro país, desde hace mucho tiempo se ha abierto una buena veta, por así decirlo, de edificaciones de cuatro y cinco pisos. Entonces, nosotros incursionamos en ese campo y para ello, nos apoyamos y validamos nuestros diseños en importantes y reconocidas oficinas de ingeniería del país”, dijo Francisco Cañete.
En el caso de edificaciones de cuatro pisos, el director comercial de DETECO detalló que participaron en tres etapas de un proyecto y que, junto con otras pequeñas obras, llevan una cifra que bordea a los 1.000 departamentos cons- truidos con este sistema. -¿Han tenido la oportunidad de que los paneles de Deteco se utilicen en otro tipo de proyectos, más particulares?
Francisco Cañete: Sí. En nuestra experiencia de 22 años, hemos adecuado nuestra producción para hacer cosas singulares. Hemos construido templos religiosos, salas y casetas eléctricas, estanques de agua y estanques para sistemas de biolixiviación, por citar algunos. También, hicimos recientemente un mausoleo en el Cementerio General y a través de los años hemos efectuado varios proyectos de muros de contención, que son de muy ágil y eficiente instalación.
“Eso es muy interesante porque hemos roto, en cierto modo, el paradigma de que los muros de contención, de estos que son geoestáticos, necesitan una gran masa para impedir el volcamiento. Nosotros hemos hecho muros prefabricados, con contrafuertes, y muros alivianados. El diafragma vertical es un muro que tiene un diafragma, por lo tanto, es más económico y el compromiso lo toman los contrafuertes, también prefabricados”, complementó Cañete
“En ese sentido -agregó- para un proyecto en Illapel, donde hicimos 200 casas, en Illapel, hubo que ejecutar casi un centenar de terrazas, lo que conllevó a una cantidad de metros lineales enorme de muros de contención que, de haberse hecho en sistema tradicional, hubiera tardado meses. Nosotros íbamos a un ritmo aproximado de entre 10 a 20 metros lineales por día y lo hacíamos en paralelo con el montaje de las casas”.
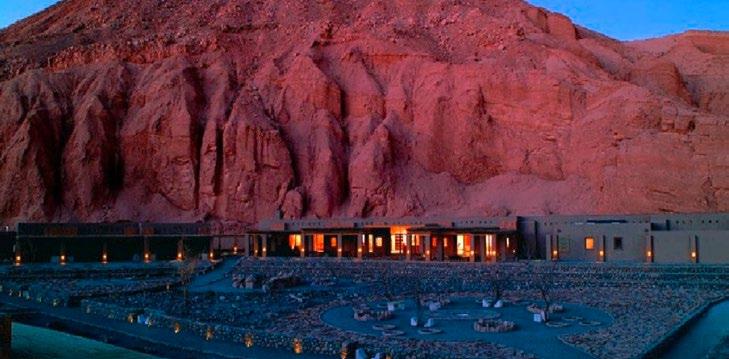
Con ello, comentaron los ejecutivos de DETECO, se puede evidenciar la versatilidad que posee el sistema industrializado de prefabricación que promueven. “Hemos sido creativos y en estos 22 años de experiencia, hemos desarrollado varios proyectos singulares, no sólo edificaciones de vivienda tradicionales”.
-En su experiencia, ¿cómo ven el crecimiento y la evolución de sistemas industrializados que trabajan con prefabricados de hormigón?
Francisco Cañete: Vemos con alegría que se han incorporado otros operadores al mercado, lo cual potencia el uso de hormigón armado industrializado. Hace 15 años atrás, éramos los únicos. De hecho, la primera planta industrializada que hubo en el país fue la nuestra, como las que existen en Alemania, España, en fin, hecha con ingeniería chilena, pero en cierto modo, asemejando a la forma de construir de esas plantas europeas. -En esa misma línea, ¿de qué manera analizan el impulso que, desde el Minvu, se le está dando a la construcción industrializada?
Guido Sepúlveda: Lo vemos como una señal positiva y esperamos que se transforme en una eficaz herramienta para reducir el déficit habitacional. También ciframos expectativas en que esto signifique una mayor apertura a estas nuevas soluciones que, como toda innovación, no han sido de fácil introducción en los procesos de revisión y permisos, los que la mayoría de las veces son muy extendidos en el tiempo. Que esta mayor apertura permee tanto a las obras privadas como de interés social también lo vemos con muy buenos ojos porque a la larga, lo que nuestro sistema ofrece son mayores certezas al cliente y finalmente también al usuario final, no sólo en costos, sino también en plazos de ejecución, lo que implica que si se planifica colaborativamente y nos integramos tempranamente, hay una gran agregación de valor, es decir, todos ganamos.
Aplicando Econom A Circular Para Un Hormig N M S Verde
Para alcanzar la neutralidad de carbono al 2050, la industria del cemento debe seguir diferentes caminos para reducir sus emisiones de CO2. Si bien las medidas convencionales deben aplicarse en la mayor medida de lo posible, se necesitarán tecnologías innovadoras como la captura de carbono para reducir las emisiones de CO2 que, de otro modo, no podrían eliminarse. La investigación sobre la captura de carbono en la industria del cemento comenzó temprano. La tecnología de postcombustión ya se encuentra en un estado maduro de aplicación potencial. ECRA, la Academia Europea de Investigación del Cemento, comenzó su trabajo sobre la combustión de oxicombustible desde el 2007. El principal desafío para la industria serán los altos costos operativos y de inversión. Desde un punto de vista técnico, queda la pregunta de cómo utilizar o almacenar el CO2 capturado.
Los productores de cemento de todo el mundo apuntan a emisiones cero netas de CO2 para 2050. Esto se refleja en las diferentes hojas de ruta para el sector, en las que se describen las palancas y medidas relevantes.
Para el sector mundial del cemento y el concreto, la GCCA (Global Cement and Concrete Association) ha desarrollado su hoja de ruta en la que se han abordado los diferentes caminos hacia las emisiones cero netas de CO2 [1]. Las principales medidas convencionales son el uso de combustibles alternativos, entre ellos la biomasa, y la reducción del factor clinker en el cemento.
A lo largo de la cadena de valor, la mejora en la tecnología del concreto, así como el ahorro de cemento y concreto en el diseño y la construcción, proporcionarán una contribución significativa a la reducción global de CO2 por parte del sector.
Todas estas medidas, incluso si se aplican en la mayor medida posible, todavía requerirán que un tercio de las futuras emisiones de CO2 se reduzcan mediante tecnología de captura de carbono. Es una tecnología emergente que hasta el momento no se ha aplicado a nivel industrial en el sector del cemento. Se ha iniciado proyectos de investigación y demostración que han concluido que, en principio, esta tecnología se puede aplicar a las plantas de cemento. En los artículos de ECRA Technology [2] se proporciona una buena descripción general de las diferentes tecnologías, su