
4 minute read
HARNESSING ZERO LIQUID DISCHARGE, BRINE MINING AND MINERAL PRODUCTION FOR A GREENER FUTURE
By Nikolay Voutchkov, Dr. Noura Chehab, Mohammed Alsindi, Hussain
Bukannan, Dr. Hyuk Soo Son, Fatima Bukhari, Ali Alghazal – ENOWA Water Innovation Center
NEOM is a new region being built from the ground up in the Northwest of Saudi Arabia and a key component of Saudi Arabia's Vision 2030. Envisioned as a future Special Economic Zone, NEOM will be a living laboratory for solutions that address global issues. Among these, one of NEOM's primary goals will be to develop and implement at-scale solutions for water scarcity and pollution, minimizing water costs and eradicating waste. ENOWA, the water and energy company of NEOM, is leading this charge and has brought together world-leading experts within the energy and water space to lead infrastructure development while investing in and testing ground-breaking technology.
ENOWA Water is designing infrastructure utilizing forward thinking technologies and in collaboration with leading international organizations. The water infrastructure is being built on circular economy principles where seawater desalination will be integrated with brine processing and 100% wastewater recycling and recovery of resources will achieve zero-liquid discharge (ZLD) by 2030.
The recently created ENOWA Water Innovation Center (WIC) focuses on the development of applied research projects that support ENOWA’s strategic plans and objectives. With a focus on seeking solutions that reduce waste, recover resources and foster environmental and fiscal sustainability. WIC develops and implements new ideas and technologies as a center of excellence in desalination, smart water technology, seawater brine mining and advanced wastewater treatment. Core to ENOWA’s strategy is the implementation of circular economic models where by-products such as brine from desalination are revalued as resources.
New Generation ZLD System
Brine generated from desalination plants and industrial production processes contains high salt content and its discharge into aquatic or terrestrial habitats can have negative environmental impacts on these habitats. To overcome this challenge, the water industry has developed technologies to recover additional water from the brine and harvest minerals in solid crystal form to achieve ZLD.
Despite their positive environmental impact however, current ZLD technologies are rarely adopted in practice because of the prohibitively-high cost of application. In addition, current technologies produce mixed salt products that have limited or no commercial value; in most ZLD plants today, crystalized salts are disposed of in landfill as solid waste at relatively high cost.
The WIC international research team has developed an innovative ZLD system for production of desalinated water with imbedded synergistic multistage brine mining technologies. Its purpose is production of commercially viable minerals (i.e., sodium, potassium, rubidium chloride, calcium carbonate, magnesium hydroxide) and elemental metals (i.e., lithium and magnesium) from desalination brine or other high salinity sources such as produced water, high salinity groundwater, mineral water from springs, wells and other natural or human-made high salinity streams with a total dissolved solids (TDS) concentration of 2,000 mg/L or more.
As a first step of fresh water and mineral production, the WIC system separates the high salinity source water (i.e., seawater entering the desalination plant) into two streams: monovalent minerals and metals naturally occurring in seawater (monovalent stream-MVS) and polyvalent minerals and metals (polyvalent stream-PVS).
conventional reverse osmosis system (i.e., SWRO) to separate the fresh water from the MVS and produce monovalent brine (MVB), followed by an ultra-high pressure reverse osmosis system (UHPRO) to produce more fresh water and concentrate the MVS. The MVS brine is further concentrated by osmotically-assisted reverse osmosis (OARO) to concentration of ~225,000 mg/L of TDS and then crystalized in membrane or thermal crystallizer to produce high purity sodium chloride (99.8% purity). The purge that contains other minerals and metals is processed by another crystallization process to produce potassium chloride, in parallel through lithium extraction system to produce lithium metal and lithium chloride, and sequentially through ion exchange system with selective resin to produce lithium chloride. All low salinity water produced from the brine valorization processes is mixed with the desalination plant permeate to produce more fresh water.
This separation of seawater into MVS and PVS uses nanofiltration (NF) membrane elements specifically designed for rejection of magnesium of more than 85% and for low rejection of monovalent minerals (less than 15%). The separation of the seawater into MVS and PVS is of critical importance to produce commercially viable pure minerals and metals because polyvalent ions contained in the MVS, such as calcium and magnesium, are considered impurities in the most monovalent commercial salt products; and vice versa.
The MVS is further processed by reverse osmosis membrane separation in two stages:
Similarly, the PVS is processed in a clarifier for softening by adding soda ash (Na2CO3) to precipitate calcium in the form of calcium carbonate (CaCO3). The supernatant from the calcium clarifier is conveyed to another clarifier (Magnesium clarifier) to precipitate magnesium in the form of magnesium hydroxide (Mg(OH)2) using sodium hydroxide, ammonium hydroxide or other regent that can precipitate over 90% of the magnesium in the PVS into Magnesium Hydroxide. Precipitated magnesium hydroxide is used to produce magnesium metal. The supernatant from the Magnesium Clarifier is processed by ultrafiltration or conventional filtration to remove fine solids, and used to crystalize magnesium chloride and sulphate, as well as sodium carbonate (soda ash), and calcium sulphate and chloride. Crystallization of the above minerals is completed by membrane or thermal crystallizer. The membrane crystallizer uses sodium chloride as a draw solution (DS) of salinity between 200,000 and 300,000 mg/L of TDS which draws the water out of the concentrated minerals and crystalizes them on the surface of the membranes. The diluted draw solution is processed through sodium chloride crystallizer to reconcentrate it and to recover all the fresh water from the PVS. The process schematic of the WIC ZLD system is shown in Figure 1.
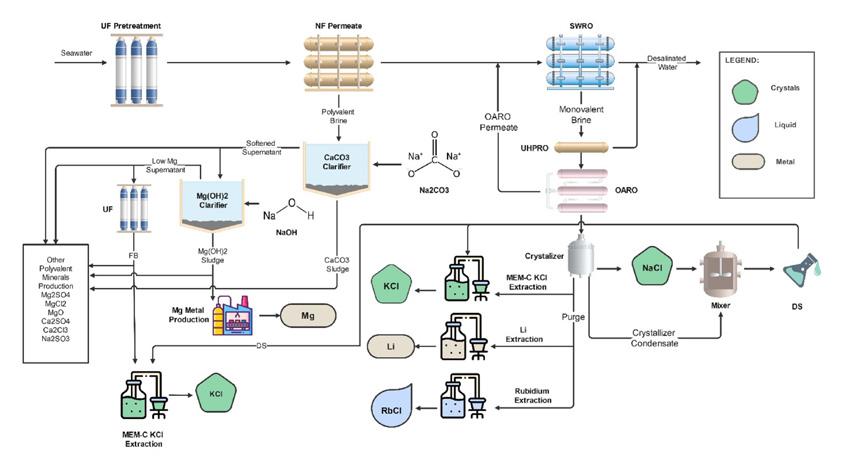
About the Author
Dr. Noura Chehab is leading the water Research and Innovation at ENOWA . Noura has been with NEOM for the past 3 years and half, where she has established multiple research projects and agreements and played a key role in attracting disruptive Water technologies to the Innovation team.
Noura holds a PhD and MS degrees in Environmental Science and Engineering from King Abdullah University of Science and Technology. She is a recipient of several prestigious awards (First prize Bayer award; Siemens Second Prize Student Award) in recognition of her innovative ideas in developing sustainable solutions to water scarcity.
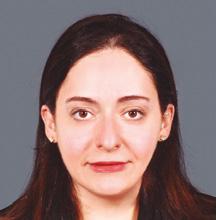
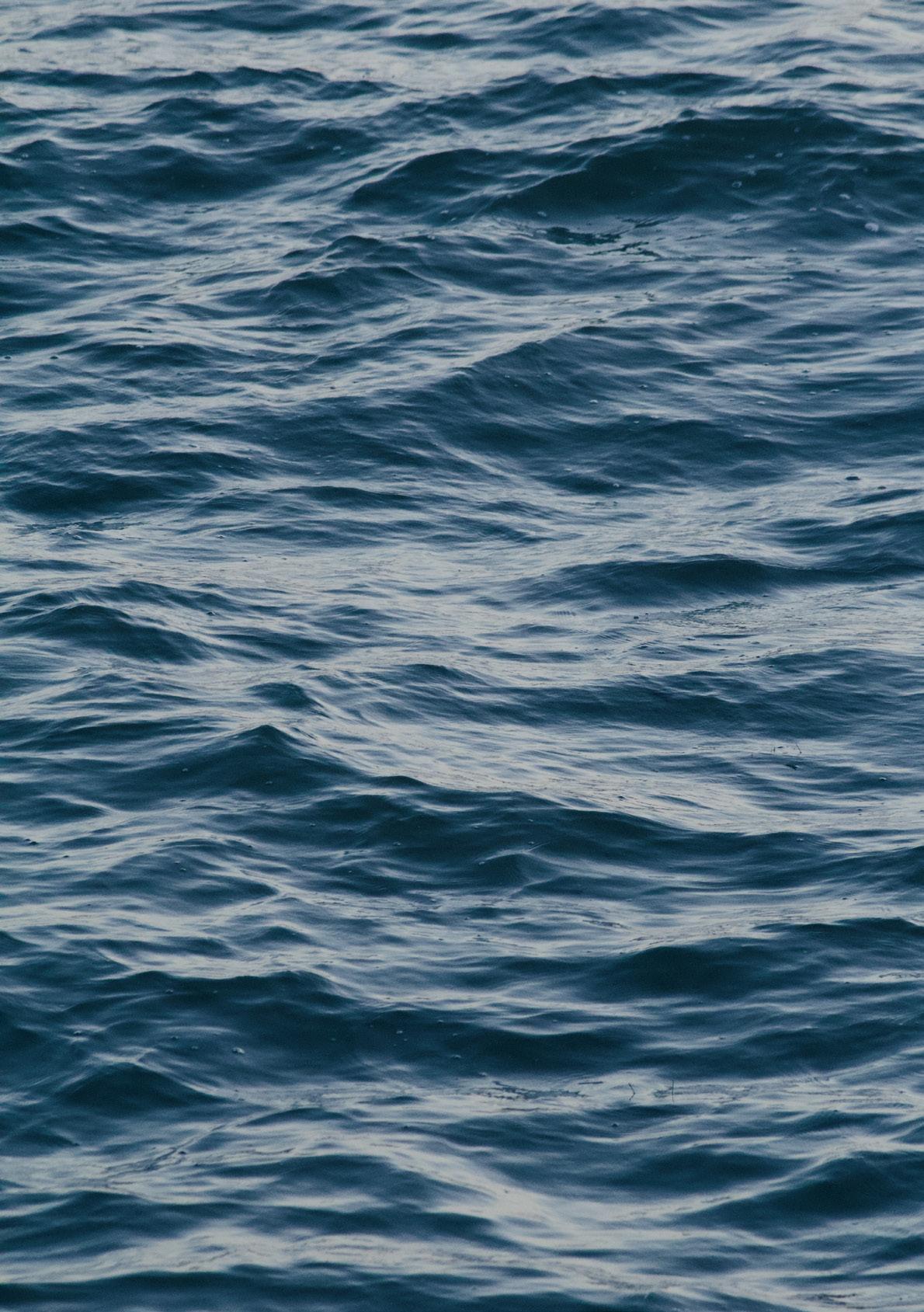