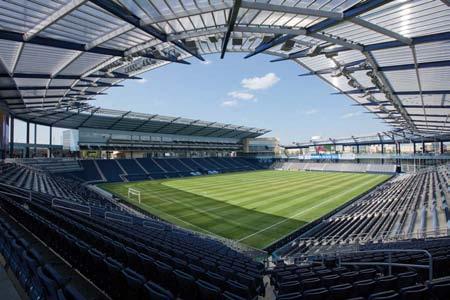
14 minute read
Canopy Adds A Kick To Sports Venue
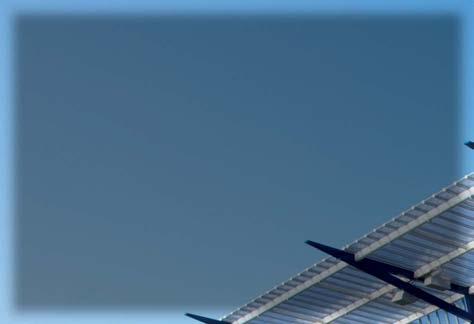
The canopy allows plenty of sunshine to keep the naturalturf playing fi eld lush and healthy.
Advertisement
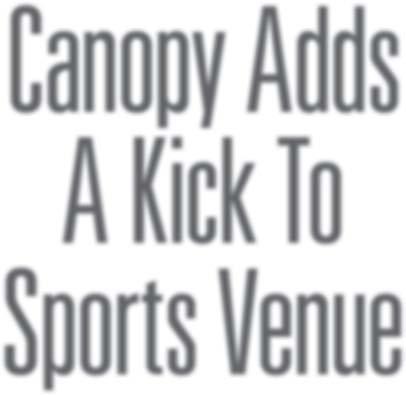
A stadium gets the world’s largest polycarbonate canopy to shade fans and enhance their experience.
The largest polycarbonate canopy in North America provides shade for fans at Livestrong Stadium, while evoking the curved path of a soccer ball.
Soccer players and fans celebrate “the beautiful game,” as superstar Pele called it, in a Kansas City, KS, stadium unsurpassed for high-tech, fan-friendly features. The crowning touch is a translucent, crystalline canopy that shades all 18,500 seats, yet allows diffused sunlight to fl ood the fi eld. It also refl ects the roar of the fans, amplifying the sounds to create, “an electric place to be,” according to Jeff Spear, AIA NCARB. Spear is lead project designer and a principal in the Kansas City, MO, practice of Populous, the architecture fi rm responsible for the leadingedge design of Livestrong Sporting Park. “The canopy is a very important part of the overall design, which wouldn’t have worked as well without it,” said Spear. “The players and the fans love it. It’s exceeding our expectations.”
Aiming for the sky
Those expectations were high for this new $200-million home of Sporting Kansas City, the soccer team formerly known as KC Wizards. After shuttling from one venue to another for 15 years, they now call home one of the world’s most sophisticated stadiums, designed to evoke the soaring curve of a soccer ball and the athleticism of the players.
The fi rm responsible for design engineering of the stadium’s canopy—the largest polycarbonate stadium canopy in North America—is Duo-Gard Industries Inc., Canton, MI. Duo-Gard specializes in custom design, engineering, and fabrication of architectural canopies, often involving high-performance-polycarbonate glazing technology and structural framing innovations.
“Meeting the architect’s demands for this unique project was a function of understanding a multifaceted challenge,” said David Miller, DuoGard’s president. That challenge included several specifi c goals for the stadium’s polycarbonate canopy, which is more than 1,800 feet long and ranges from 25 feet to 70 feet in depth. Those goals included: • aligning mullions while transitioning the canopy from 3 feet to 9 feet from one level to the next and while fl owing around the corners. At the same time, the system steadily dropped 30
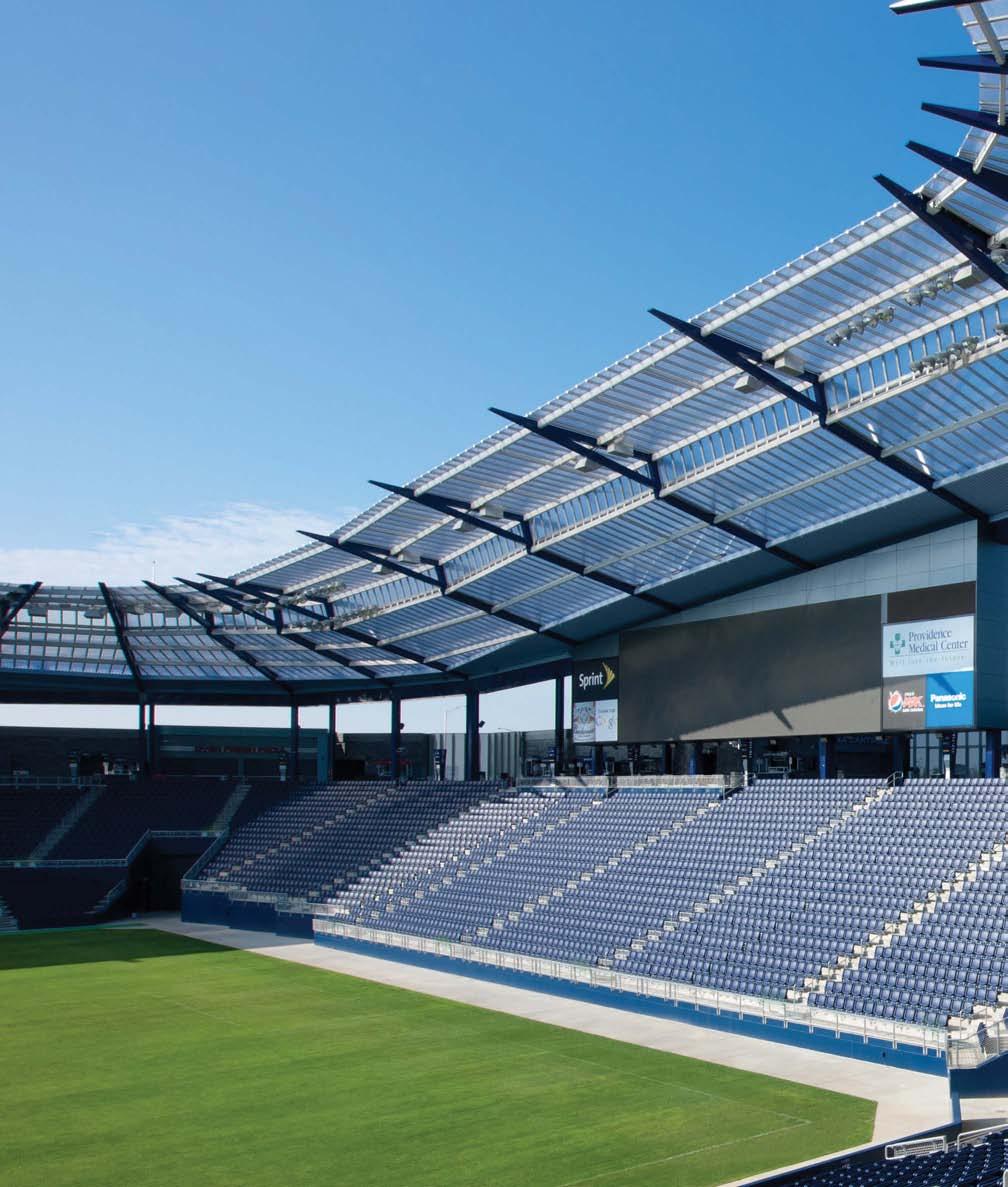
feet from one end to the other. • creating a low-profi le system to minimize shadowing and the use of a steel support structure. The project team designed a system that is 3 3/4 inches high. The previous system was 9 inches. • using a glazing that can be extruded in 41-foot lengths, meets the structural requirements of 83 PSF, and allows direct sun to support the health of the natural-turf system. The Duo-Gard team had to adapt the polycarbonate extruder to make custom panels that would meet the desired performance. • designing the system for a low-pitch application that allows free fl ow of water without pooling. A low-profi le plastic cap prohibits water pooling while allowing airfl ow to evacuate the panels of any condensation.
Shelter in the outdoors
The structural demands were extraordinary. In meeting them, Duo-Gard’s engineers created a low-profi le, long-span system with performance and savings unprecedented in the industry.
“One impetus for the canopy was
to provide an intimate resists hail and other impacts. r environment that would Plus it spans farther with less P amplify the crowd’s noise; weight than glass.” w that’s why we covered every Aesthetics also played a seat. Another factor was part. “With glass, you could see p shading the crowd without clouds and sky,” he added, “but c shutting off the sunlight we the translucent polycarbonate t needed to maintain the natural adds a sparkle that switches a grass that Major League Soccer between the sunlight and the b prefers,” said Spear. He said stadium lights that makes it s they wanted to avoid grow Part of the plan for the canopy was that Part of the plan for the canopy was that more interesting.”m lights while ensuring that the it would catch the crowd noise and The green features of the grass had the best opportunity amplify it for the players on the fi eld. material were attractive too. m to fl ourish. The polycarbonate:T
The design team evaluated several • incorporates recycled and recyclable content alternatives. Fabric didn’t offer the required hard • minimizes materials while accomplishing projsurface. ETFE pillows didn’t give the desired ect goals appearance, and the weight of glass panels at the • focuses technology to eliminate unnecessary desired spans would have required signifi cantly features more-costly steel substructure. • complements and integrates with green-building principles. The polycarb solution However, Miller said, the structural Spear said the design team then considered demands of low slope and low profi le made translucent polycarbonate. “Its hard surface it more interesting—and infi nitely more accentuates sound. It disperses natural light. It challenging—for the design team, requiring a

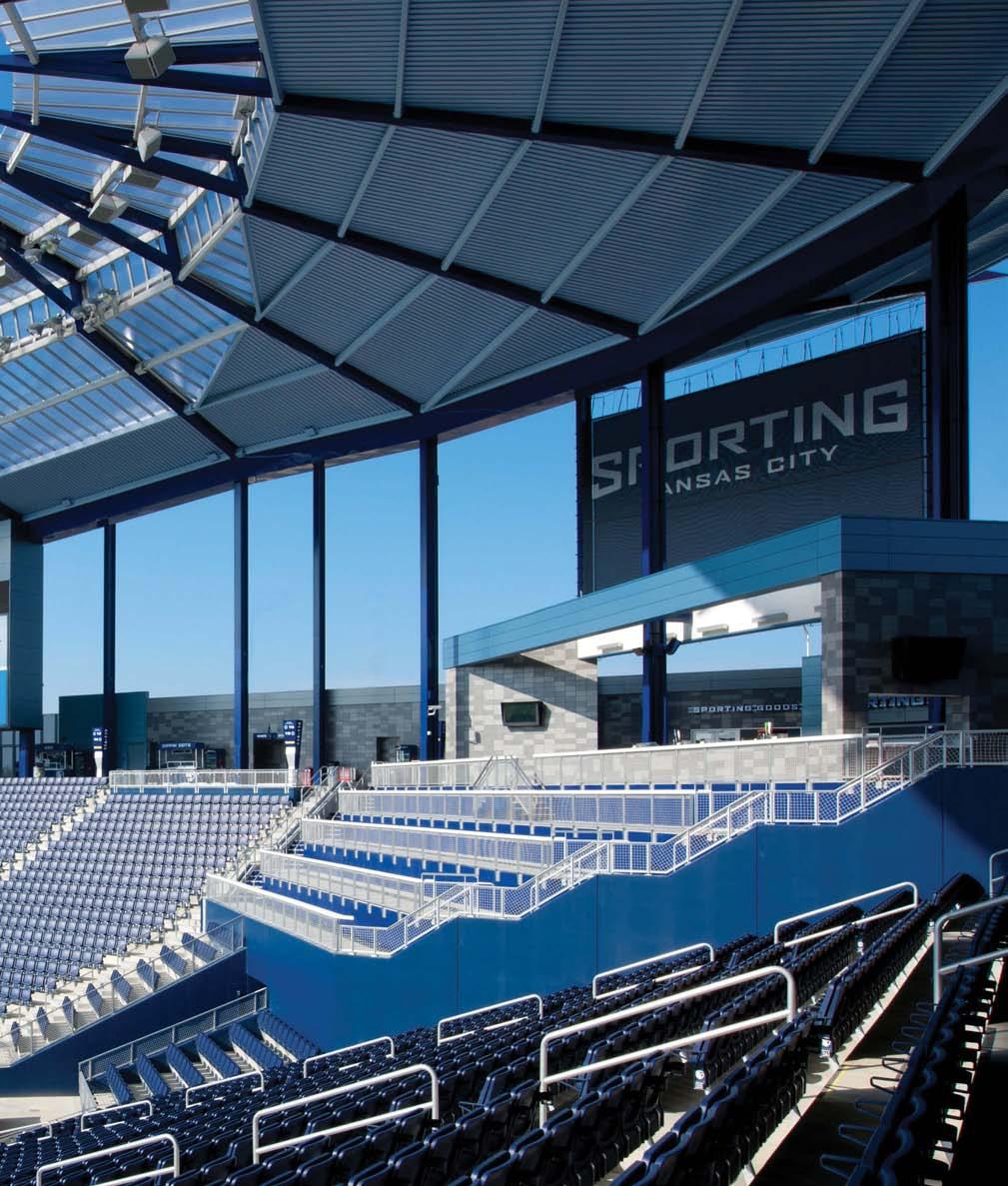
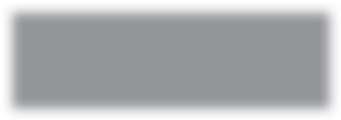
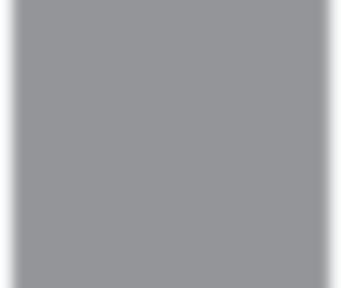

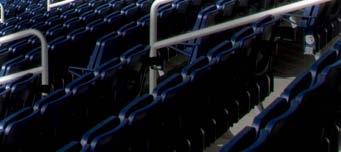


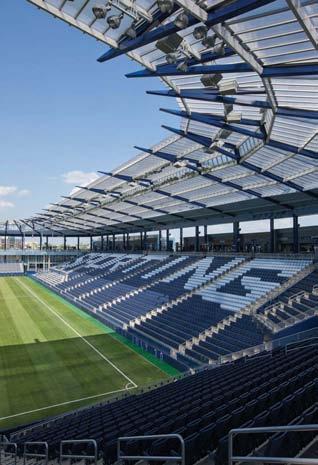
1/12 pitch, a 12-foot span between structural members, and exceptionally high loading.
“This kind of span hadn’t been done before by anyone with polycarbonate at a slight slope,” Miller said. “Our engineers broke ground with this.”
The canopy actually integrates two complementary components. The steel structure is cantilevered 95 feet and supports a metal deck that fl ows into the two-tiered polycarbonate deck cantilevered three feet off the metal. The glazing is 25-mm, triple-wall clear polycarbonate, allowing 80% light transmission. Duo-Gard’s aluminum framing system features a specially engineered base plate, pressure plate, and curved cap that conceal the fasteners.
“It sports our new 3 1/2-inch profi le in 32-inch on center to minimize shadowing and maximize sunlight transmission to the fi eld,” said Frank Kosciolek, Duo-Gard’s engineering manager. He compared it with the industry’s typical systems with a 7-inch profi le at 24-inches on center, throwing out much more shadowing and requiring an additional steel purlin.
“Our capability for 32-inches on center allowed us to eliminate the extra purlin, resulting in 35% less metal required. That’s a signifi cant savings on a project of this scope,” Kosciolek said.
He added that the company successfully tested the system at 150% of the required loading, which was more than double that for most canopies. Plastic channels at the top and bottom of the translucent panels enhance the “fl oating effect” of the canopy. Special fl ashing and expansion joints complete the system.
Tricky installation
Kosciolek said installation of the canopy involved additional challenges that required close collaboration between Duo-Gard, general contractor Turner Construction, Kansas City, MO, and installing contractor A2MG, Kansas City, MO. “Working with the long span and low slope, especially at 100 feet from the ground, was the most signifi cant challenge,” said Chris Mann, project manager for A2MG. “Yet it’s a simple system, easy to handle. It turned out great.”
Other installation challenges were: • complex geometry-mandated fi eld fabrication in some areas • handling 41-foot sheets six stories in the air with only the structural steel as support • packaging all materials by bay to minimize any material movement on the rooftop.
Duo-Gard’s David Miller said the project was the company’s largest and most challenging to date.
for free information, CIRCLE 12
or visit our digital magazine at www.cbpmagazine.com/digital/janfeb2012 and click on the icon.

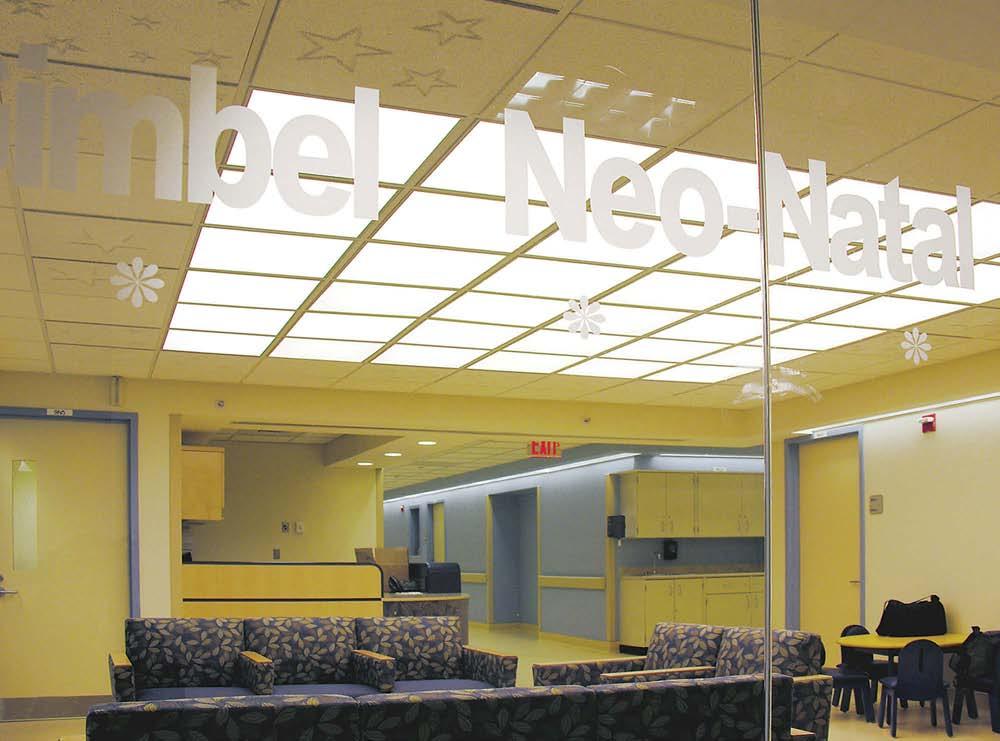

▲
Installation of LED fl at panels in the family suite of the neonatal intensive care unit at Bellevue Hospital, New York, adds bright, consistent light to the area.
▲
In the radiology department at Englewood Hospital, Englewood, NJ, LED fl at panels provide robust illumination to make it easier for technicians to read digital images.
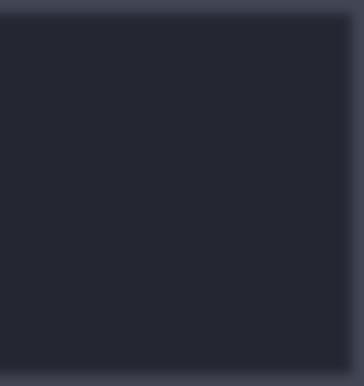
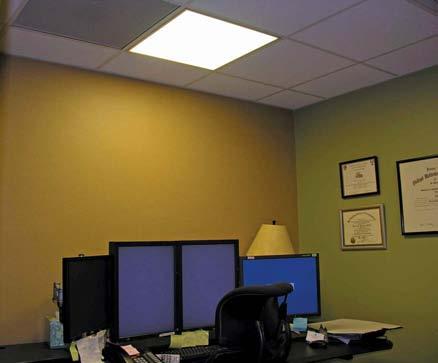
LEDs Cut Costs, Boost Effi ciency


Few buildings have greater need for excellent lighting than hospitals. From the emergency department to neonatal units to surgical suites, physicians and nurses must be able to see exactly what they’re doing as they care for patients. Hospital administrators, meanwhile, are under constant pressure to cut costs as healthinsurance companies and government programs squeeze reimbursement drier each day. Two New-York-area hospitals recently installed energy-effi cient lighting that fi lled their needs exceptionally well. MaxLite, West Caldwell, NJ, designed and produced innovative edge-lit LED MRI fl at-panel fi xtures for Bellevue Hospital, Manhattan, and Englewood Hospital and Medical Center, Englewood, NJ. The fi xtures deliver fully dimmable, energy-effi cient, high-quality lighting with even, shadow-free distribution and a color-rendering index (CRI) of 85. Part of the FlatMax line, LED fl at panels offer high performance with a documented life of 50,000 hours at L70 standards, or more than 13 years (based on 10 hours of use/day) to minimize energy and maintenance costs. The programmable panels are highly compatible with the healthcare centers’ control systems, so they can be switched on/off and dimmed to meet user preferences. Constructed as RoHS compliant, without mercury or hazardous materials, and without emitting heat,
LED MRI fl at panels create soothing atmospheres at two hospitals while reducing costs.
UV, or IR radiation, the panels also are compliant with regulations for restriction of hazardous substances. The panels even include emergency battery-backup models for safety and remotedriver models for MRI units.
Soothing light for worried families
The LED MRI fl at panels were installed at Bellevue Hospital’s family suite of the Barbara P. Gimbel neo-natal unit. The 20-bed NICU serves 500 infants annually, and all require highly specialized medical care. The 36 newly installed 3,500-K warm color temperature, state-of-the-art, lighting units enhance visual comfort for family members enduring long stretches of time at the hospital while their premature or critically ill infants receive intensive care. The wall-switch-controlled soft lighting soothes the senses and reduces stress.
To meet the challenge of the family suite’s 6-inch ceiling cavity, the ultra-thin LED fl at panels have a shallow 1.6-inch depth for easy installation with a tight fi t. Optimal general and ambient lighting are provided for the facility’s varying uses, including a space for 24-hour family visitations and child developmental classes, medical consultations, CPR training, and a private place to make phone calls or relax.
The MaxLite team worked closely with Leszek Nadler, Sr., electrical engineer for facilitymanagement design at Bellevue to specify and install the panels. Nadler said he chose the MaxLite panels, “for their even light distribution, for their dimming qualities, and for their shallow depth.”
The fi xtures’ housings and back panels are constructed of aluminum to provide maximum heat sink and thermo-control capabilities to maintain a long, cool operation. The trim also acts as a heat sink, and in keeping with the high quality of the rest of the materials, the lens is a translucent white polycarbonate.
While incandescent fi xtures are affected by the high magnetic fi eld within a medical facility and need to be replaced regularly, the LED panels are made of non-ferrous materials to ensure that the medical equipment is not affected by magnetic fi elds.
In addition, the LED panels are produced without mercury and therefore limit any unnecessary mercury exposure to patients or their families.
Easy-to-read X-rays
The needs at the Englewood hospital were much different but also were met by the same luminaire. The hospital installed four units of LED fl at panels in its radiology viewing offi ces. Controlled with an IR remote, the new 5,000-K luminaires create a visually comforting space for employees. The LED panels provide shadow-free, even illumination and smooth dimming.
“We need subdued light to view the screens for accurate readings, but with the easy capability to transition to brighter light for other tasks,” said Joseph Sudan, Englewood Hospital’s radiology administrator. Overhead LED MRI fl at panels create clear lighting that helps doctors view X-ray fi lms and imaging-procedure results on digital screens with accurate detail. Medical professionals and radiologists also can get brighter light for other tasks such as consultations, examinations, offi ce management, and administration functions.
The LED fl at panels provide optimal illumination levels for operating the instruments and equipment. The LED panels minimize re-lamping and maintenance time and effort while maintaining the facility’s uptime without unnecessary interruptions. Less downtime directly translates to higher productivity coupled with higher physician and patient satisfaction.
The panels use non-ferrous materials. Incandescent fi xtures may be limited to less than 1,000 hours of life, while LED panels have an extended life of 50,000 hours. Fluorescent fi xtures, which have a longer life than incandescent fi xtures, still do not compare to LED luminaires. Unlike LED panels, fl uorescents often generate unwanted noise in medical facilities.
The technology of better lighting
LED fl at panels deliver a signifi cant reduction in energy consumption, costs, and maintenance. The fl at panels are dimmable using four different methods: IR remote, 0- to 10-V, building controls, or 512 DMX control. The panels are pre-programmed to operate effectively within the hospital’s control system. Manufactured with high-ranked binning for color uniformity and consistency, MaxLite fi xtures and lamps turn on instantly from a cold start, dim for pleasant ambient lighting, and deliver a high lumen output and CRI. Constructed without any hazardous materials, the luminaires provide a cool operation without emitting radiation or heat while reducing HVAC costs and maintenance.
“The capability of LED to meet or exceed traditional lighting technology is amazing,” said Pat Treadway, product-marketing manager for MaxLite. “Colors appear in truer hue, people look healthier, and products appear better with high-CRI LED lighting. This is a key strength of this newer technology. When combined with the longevity of a qualifi ed light source, the lower maintenance costs, and the energy effi ciency of LED systems, LEDs can affect businesses and the environment in a positive manner that was not available a few short years ago. By incorporating MaxLite products in a few high-use indoor applications, the payback time is less than two years.”
Given the benefi ts of the latest LED technology, it makes sense that LED fl at panels are popular with progressive hospitals. In addition to eliminating mercury from lighting fi xtures and reducing maintenance and energy costs, these innovative hospitals have ensured patient safety and safeguarded their lighting systems with long-life, smoothly operating fi xtures.
for free information, CIRCLE 14
or visit our digital magazine at www.cbpmagazine.com/digital/janfeb2012 and click on the icon.
W H E N YO U R B U I L D I N G’S AG I N G O R O U T DAT E D WATER SYSTEMS CALL FOR A CURE, ZURN LISTENS.
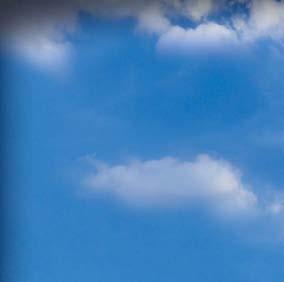
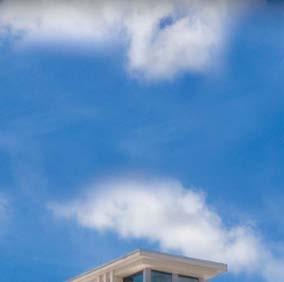
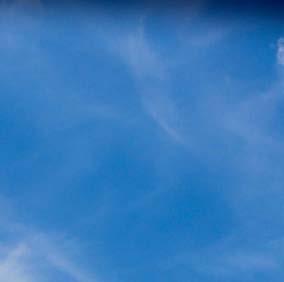


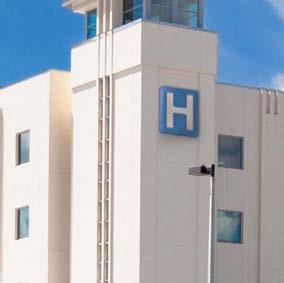
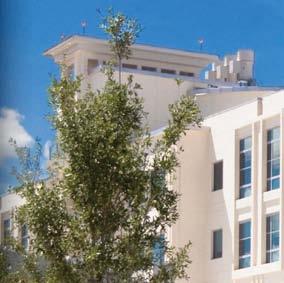
Water is said to be the key to all life. Nowhere is that statement truer than in a hospital. So when we replaced all the brass fix tures and backflow valves here, we needed the most dependable products with the fastest installation times. That’s why we called Zurn.

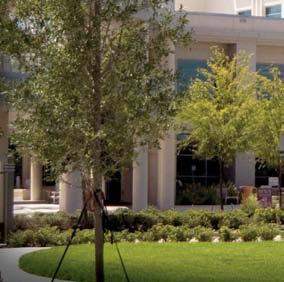
RETROFIT A N D REPLACEMENT SOLUTIONS
Lead-free backfl ow valves with the lowest lifecycle cost. High-effi ciency toilets and valves. And hands-free faucet and toilet sensors that reduce the spread of bacteria. When it comes to saving time, money, and maybe even a life, one name is the remedy to all your building’s needs. Zurn. For your next retrofi t and replacement project, give us a call. We’ll listen.
Sensor Flush Valves
375XL – Lead-Free Reduced Pressure Assembly Sensor Faucets
zurn.c m
1.855.ONE.ZURN