
12 minute read
For An Old Building
from commARCH - May 2013
by IdeaSoil
decreasing ambient air temperature • Creating a beautiful, natural environment for occupants, guests, and wildlife • Contributing between 6 and 14 points to the U.S. Green Building Council, Washington, Leadership in Energy and Environmental Design (LEED) certifi cation.
Going underground
Advertisement
A superior water-management solution goes beyond the outdated curb-and-gutter design. For instance, a gauged water-release, passive retention system—sometimes referred to as subsurface irrigation and storage—is an onsite water-management-and-reuse system that collects, fi lters, retains, and distributes water below ground. This type of system can collect and reuse nitrates, phosphates, and other pollutants as nutrients for the vegetation above ground. It also cuts down on pollutants that may enter groundwater from rainwater runoff.
Not only does the system convert pollutants to usable fertilizer for vegetation, but onsite water-management and reuse systems can also remove fl oatables, skim oil and grease, and even tap sediment before those elements are released into the ground or natural bodies of water. A geomembrane liner can help with soil erosion. When properly designed, in combination with other water-storage products, a subsurface irrigation and storage system is a great, low-maintenance water-management tool. The United States spends billions of dollars each year to build large sewer systems that can handle additional rainwater. Stormwater management can help alleviate the need and expense for those larger systems as well as control fl ooding, which contributes to the spread of pollution, contaminates drinking water, and threatens the safety of people in an affected community.
Moreover, water-management systems can create multi-functional green spaces or permeable parking with exceptional drainage and water-collection capabilities. Water captured with these technologies can result in using 50% to 80% less potable water indoors and for landscape irrigation, resulting in decreased dependence on municipal water supplies. By bringing together passive subsurface irrigation, water storage, and fi ltration, an on-site, underground stormwater-retention system makes possible adjustments to fi t a building’s footprint and help building owners and managers achieve hydrologic responsibility.
Conventional perforated-pipe systems with geotextile lining have also been a popular option as a drainage mechanism, but many eventually fail due to silt buildup in the geotextile. These systems often need to be replaced after a few years, which can become very costly and cause further damage to the property.
Real and artifi cial turf
Subsurface systems are ideal for various applications, including green spaces, athletic fi elds, parks, sidewalks, and even parking lots. Heavy rains and standing water particularly affect parks and athletic fi elds, which are costly to build and maintain. Water-management systems alleviate the stress put on these environments by heavy rains.
Subsurface systems leverage gravity to pull water down below ground, where it is stored in chambers. Capillary rise pulls the water upward to irrigate natural turf. This process provides
Installation of plants goes quickly with preplanted mats. The colorful sedum will thrive even in dry conditions with minimal irrigation.

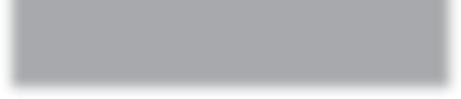

water management for natural sports fi elds and outdoor artifi cial turf.
Not only can water-management systems fertilize the natural vegetation in a park and minimize standing water, but they also alleviate a major concern: heat. With artifi cial turf, surface temperatures may exceed 180 F as a result of the sun’s ultraviolet light reacting with compounds in the synthetic turf. The excessive heat can contribute to heat-related health hazards for the athletes. Gauged waterrelease passive-retention systems may include a damp fi eld base that allows the heat to dissipate, creating a natural cooling effect that can reduce fi eld-surface temperatures on hot, sunny days. The systems can also allow moisture to enter the sandbased infi lls from below grade for optimal cooling and playability.
Hydrologic responsibility and LEED
The commercial-building community uses LEED, R-values, and other measures to build smarter, more effi cient structures. Water effi ciency is one of the fi ve core categories for LEED certifi cation. Installing a subsurface irrigation and storage system may help achieve LEED credits in the following categories: Sustainable Sites, Water Effi ciency, Materials and Resources, Innovation and Design, and Regional Priority Credits. Applying a vegetative roofi ng system to a commercial structure is another way to help achieve LEED certifi cation.
We are seeing a major shift toward standards and codes at the local, state, and national level that are more rigid, especially for new commercial construction. Codes and standards vary by state and locality. The U.S. Department of Energy, Washington, Building Energy Codes Program outlines commercial building codes at http://www.energycodes. gov/states/.
With the countless environmental problems caused by stormwater runoff, it is important to be proactive about incorporating water-management solutions into commercial-construction, facilitymanagement, and corporate social-responsibility plans. Water-management solutions and best practices are crucial to protecting the environment, ensuring a building is performing at the highest level, and complying with building and energy laws. As architects, contractors, and facility managers strive to be more environmentally conscious, water-management practices will become part of the model to construct smart, high-effi ciency buildings.
The building envelope controls the energy use, effi ciency, and performance of a facility. Regulating rainwater runoff is just as important as keeping water out of a building to avoid mold and mildew damage. Keeping water out of the facility is also crucial to maximizing the energy effi ciency of the building. There is a variety of building products that function together to protect a commercial building from rain and other environmental elements. For example, cavity wall systems made of ethylene propylene diene terpolymer (EPDM) synthetic—an elastomeric rubber membrane with a tradition of superior performance in harsh environments including commercial roofi ng and environmental containment—can help protect masonry walls from water damage by forming a barrier to moisture ingress in cavity-wall construction by directing water to a building’s exterior.
Rainscreen systems can also protect the building envelope from water and natural elements. A rainscreen is an exterior cladding product that sits away from a building’s exterior wall, forming an air cavity. This gap allows moisture to drain away from the building instead of getting trapped in the wall, where it could result in mold or infi ltrate the structure. An added benefi t: Rainscreens help improve a building’s energy use and performance.
It is important to note that building-envelope solutions vary according to facility, geographic location, and climate. There is no one-size-fi ts-all solution, which is why it is important to partner with experts to select building-envelope materials and products that are right for a project.
Bill Johnson has been with Firestone Specialty Products, Indianapolis, for 15 years. He currently serves in warranty and fi eld services and as the installation-training manager.
for free information, CIRCLE 3
and visit our digital magazine at www.cbpmagazine.com/digital/may2013 and click on the icon.

Although The Manor still looks like a farmhouse, it has been through changes that resulted in its use as an offi ce building and communitymeeting center.
Unlock New Uses For An Old Building


Acommercial structure near the historic Pennsylvania town of Lancaster claims an unusual background. Over the course of more than a century and a half, a series of transformations has seen a vintage fi eldstone farmhouse become a live-in training center for a major corporation, then be repurposed as the contemporary headquarters for a dynamic wealth-management fi rm. That most recent change also entailed a commitment by the new owners to make signifi cant spaces in the structure available to regional non-profi ts for meetings and special events. Essential to these most recent changes is a range of entrance-hardware products, developed and manufactured by a fi rm whose western hemisphere operations are based not far from the old farm homestead.
19th century roots
The much-evolved farmhouse, known today as The Manor, is the home of Rodgers & Associates. When it was built in 1866, it was known as
A 19th-century farmhouse gracefully enters the 21st century thanks to thoughtful renovations and modern technologies.

Jack Romig
Bloomington Farm, the pride of well-to-do farmer, banker, and tannery owner David P. Locher. Set on 120 acres just northwest of Lancaster, it was a spacious rural showplace, its handsome lines bespeaking the prosperity and taste of its owner. The house remained in the Locher family until 1920.
Eleven years earlier, a thriving Pittsburgh manufacturing concern, Armstrong Cork Co., decided to relocate to the quieter, airier, and less-congested environs of Lancaster. Armstrong had sited its factory at the edge of town, setting the scene for a burgeoning success. Beginning with a basic line of linoleum products, Armstrong eventually became a leading maker of fl oor coverings.
As the company grew, president Charles D. Armstrong decided to purchase Bloomington Farm. His company remade the handsome old house into living and training quarters. In what was an unusual method for the period, the company would house 24 recruits at a time while they underwent six-month training cycles. As time went by, the company developed and added to the property to create a kind of private hotel: Armstrong Manor.
For years, Armstrong World Industries (still located in Lancaster, PA) operated this unusual business center, bringing trainees and guests from across the country and around the globe to the Lancaster County countryside. Changing competitive realities, however, ultimately led Armstrong to sell the property in 2011. Continued on page 24.
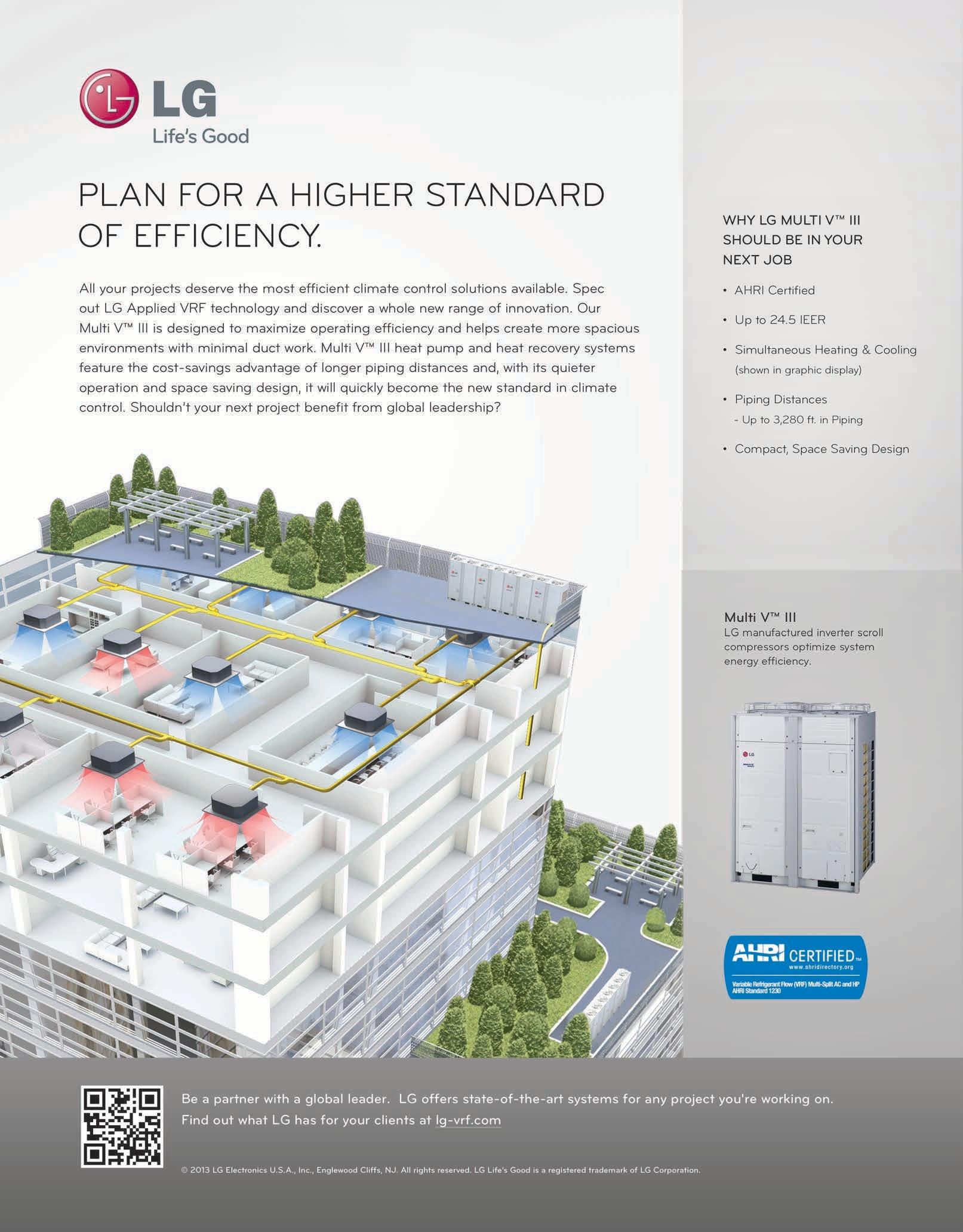
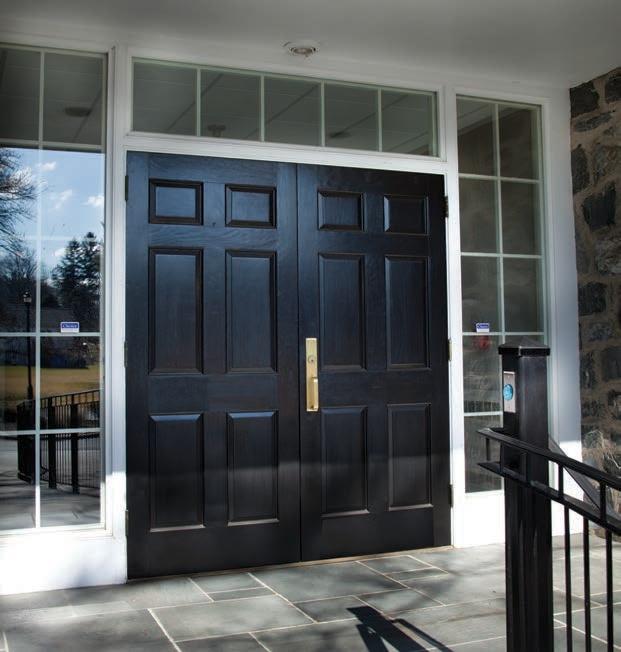


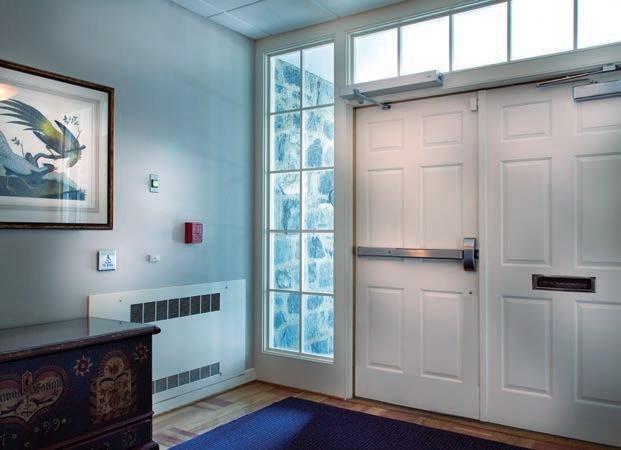



New possibilities to meet the requirements of ANSI/BHMA A156 manufactured by Dorma’s Rutherford Controls Rodgers & Associates was looking for a working 2 Series 4000 Grade 1. The Manor’s exterior International affi liate (RCI), Cambridge, Ontario. commercial property that was emblematic of the doors also feature Dorma hardware. At the front Dorma provided a customized wiring and sehigh-end market they served. More pragmatically, entrance, Rodgers opted for a quiet and easycurity integration plan that its products support they needed a new business home that offered to-use ED 900 low-energy operator that features structure-wide. For some of the entrances, access adequate parking when the fi rm held seminars for an electromechanical drive and an advanced and egress are regulated by RCI touch pads. The its clients. Armstrong Manor was the system enables remote control and right place at the right time. The fl oormonitoring of the entrances from ing manufacturer had maintained the any credentialed Internet access site well. It was almost what Rodgers point, including wireless access from needed to move into. mobile devices.
Almost. “You have to understand that this was a training and hotel Non-profi t outreach space,” said Mark Eisenberger, Rodgers’ From the time they fi rst considered director of business development. “We purchasing and reshaping the Armtook those 24 guest bedrooms and strong Manor property, the senior converted them to offi ces. The old management team at Rodgers had boardroom, dining room, and lounge an unusual plan in mind for how to were all maintained.” One distinctive use the property: sharing its fi rstfeature surviving the renovation: each class meeting areas with deservof the newly created offi ces has its own ing organizations in southeastern bathroom. Pennsylvania. The source of this
High Construction of Lancaster, charitable support originated with PA, managed the renovation. ConvertJessica Rodgers, who recognized ing the hotel rooms to offi ces was just possibilities in the Manor’s elegant the beginning. The building also needpublic spaces that reached beyond ed additional parking slots, fi re doors, the needs of her company. Now modern offi ce appointments, and wider the rejuvenated boardroom, dining entrances to the new offi ces to meet room, kitchen, and lounge are availADA requirements. Walls between able for meetings and events of local several bedrooms were knocked out to non-profi t groups. The result not only create conference space and enlarge provides direct support to the activithe offi ces. A more memorable part of ties of regional charities, but also the renovation: A family of skunks had helps to stimulate public participato be evicted from their den under the tion in those activities. front porch. Among the groups to benefi t
The actual renovation took have been the Lancaster County about 14 weeks. Although the project Council of Churches, a regional hosresulted in a repurposed building that pice organization, the Boy Scouts met the working needs of Rodgers & of America, the Boys and Girls Club Associates, it did not complete every of Lancaster, and other groups servintended element of the renovation. ing the public good. The spaces are The Manor remains a work in available to them at no charge, and progress, with more changes planned the non-profi ts have taken advantage for future development. of the offer by holding dinners, educational seminars, training sessions, Doors and hardware Throughout its various renovations, The Manor has retained the look of its origins and management retreats at the Doors and associated hardware were and a welcoming appearance despite the addition of modern devices required by Manor. In its own way, this approach pivotal to the success of the project code. The front door alone features a low-energy operator with an electromechanrepresents a corporate transformafrom aesthetic and functional points ical drive and an advanced microprocessor motion-control system. It is also tied tion as innovative as the physical of view. For this part of the work, Rodinto the overall security system. changes Rodgers & Associates made gers managers chose products from to the structure itself. a neighboring company, Reamstown, PA-based microprocessor motion-control system. Including Dorma. “We went with 24 wood-framed, frostedthe ED 900 was part of making the front entrance Jack Romig is a veteran writer for daily glass doors,” said Jessica Rodgers, company coADA compliant. Besides automatic operation, newspapers, trade journals, owner with her husband Rick. “We changed all the door can be opened manually with ease. and online publications. the hardware to a pretty brushed nickel, a nice All entrances also incorporate Dorma’s fl owing style.” integrated access-control solution, bringing all of for free information, CIRCLE 5
Each of the 24 offi ce doors is equipped the security elements of the building’s entrances and visit our digital magazine at with a Dorma C800 cylindrical lock, which is into a single, coherent plan. The hardware incorwww.cbpmagazine.com/digital/may2013 built with a high-performance cylindrical chassis porates electronic access-control components and click on the icon.