
33 minute read
A Primer on Mobile Fluid Power
A PRIMER ON
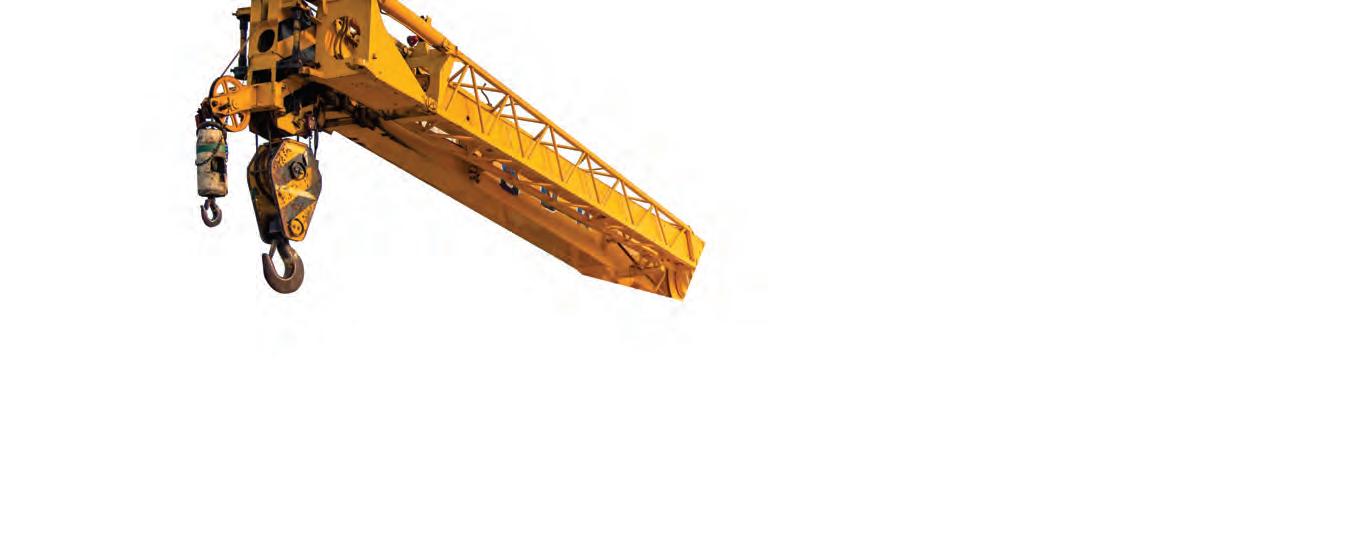
FLUID POWER By Joe Raccosta, Fluid Power Sales Manager, and Micah Taylor, Mobile Fluid Power Manager, Milwaukee Division, Motion
nce during a discussion about a mobile fluid power application, a colleague kept referring to what he called “voodoo hydraulics.” This curious phrase illustrated the many and often misunderstood differences between mobile and industrial fluid power.
As with industrial fluid power, mobile fluid power automates a machine and makes it move. Most of the time you’ll find mobile fluid power in machines with tracks or tires that are outdoors in the elements. But mobile fluid power refers not only to the type of machine, it also refers to types of hydraulic components and circuits used to control the machine. This article discusses how mobile fluid power works and how it is different from industrial fluid power. In most cases the human-machine interface between mobile and industrial equipment is very different. Many industrial applications are automated. Programmable logic controllers and programming allow the machines to run a large number of functions based on sensor or user inputs. Most of the time, with mobile equipment the human-machine interface is much more intimate. The movement of a lever or joystick or the push of a proportional thumbwheel directly affects the machine’s movement. It gives the operator the ability to get the “feel” of the machine, much like driving a car.
Another big difference between mobile and industrial equipment is the prime mover. Mobile machinery regularly uses the vehicle’s engine-driven system (its internal combustion engine) for the prime mover; in industrial applications, it’s usually powered with an electric motor. However, there is an overlap. For example, open loop pumps (vane and piston) are used in both segments but are more prevalent in industrial systems, whereas closed loop pumps are more frequently used in mobile systems. Screw-in cartridge valves are used in many manifold assemblies across both platforms as well. Both segments use cylinders, but mobile tends to use more welded and telescopic types than industrial. As far as fluid conveyance, mobile applications often operate at higher pressures and need hose with higher pressure ratings. They also require corrosion-resistant fittings for environmental protection, as well as abrasive-resistant hose because of machinery movement. Later in the article, we will describe some of the more common components found in a mobile system.
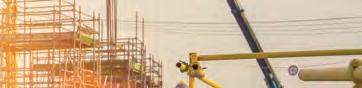
As with other segments of industry, mobile fluid power has unique characteristics and challenges. Some of those characteristics are duty cycle, environment, modular size, and noise and shock.
Duty cycle. Duty cycle is the ratio of time a load or circuit is on compared to the time the load or circuit is off. The duty cycle on hydraulic pumps is the number of minutes in each hour the pump is under load. If you place a lower-efficiency, lighter-duty pump into a higher-duty cycle application, the life of the pump is compromised. Each subsegment of mobile equipment has varying duty cycles, and some applications may require higher-duty cycles than others.
Corrosion resistance. Mobile equipment operates within a wide scope of environmental conditions. Mobile equipment must be compact yet powerful, with performance unhindered by environmental factors like rain, snow, ice, dirt, extreme heat, or moisture. These environmental factors typically don’t come into play in the design or performance of industrial equipment. With these environmental challenges, mobile hydraulic components require anticorrosion agents for preventive measures.
Size, weight, and power output. Size, weight, and power output are crucial in mobile applications. Mobile components are typically smaller, modular, and lighter compared to industrial components. Take a reservoir, for example. On an industrial system, it is usually sized around three times the flow of the pump’s output, whereas in a mobile system the reservoir size could be as small as the output of the pump or less. Producing the power output required with less space and weight is crucial. That is why power density is a major factor in mobile hydraulic circuits. Power density is the power output per unit volume, or the power output as a ratio of the actuator size. Power density is one reason why hydraulics is so important to mobile machinery. Mobile systems require high-output power combined with minimum weight.
Noise, shock, and vibration. Mobile systems tend to have higher noise, shock, and vibration challenges because of improper human operation or extreme and rugged operating conditions. Because of the environment in
which mobile systems operate, they generally do not have strict noise (dB) specifications like an industrial system and tend to operate at higher dB levels.
An example of shock occurs when a loader operator runs the bucket in “shake mode,” that is, starting and stopping the bucket’s movement quickly to break loose stuck materials. That sudden start-and-stop motion adds shock to the hydraulic system.
Vibration is another challenge from both the machine’s engine and terrain conditions. Uneven and rough terrain can cause vibration as well as pressure pulsations originating from the hydraulic system. Another factor is user error. Again, the operator can cause some of these issues by having the machine make sudden and erratic movements, leading to abrupt changes of pump displacement and actuator positions, causing additional vibration.
Now we’ll look at some common mobile fluid power components.
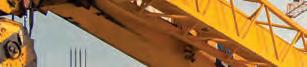
Both industrial and mobile systems use gear, vane, and piston pumps. The main drivers behind mobile-component design are weight, space, environment, and performance characteristics. Historically, noise has not been a huge factor, but more stringent regulations and exports to Europe are changing that.
Piston pumps are the most expensive of the three types but offer the most control options and highest operating pressures. In general, gear pumps fall between the piston and vane on both operating pressure and price. They can be a bit noisy depending on the gear design. Vane pumps have historically been the least expensive type. They tend to operate at a lower noise level and offer a number of pump controls.
Before discussing pump controls, there must be a basic understanding of what fixed and variable displacement means. A fixed pump always has the same displacement no matter the pressure. The input speed at which the pump turns can change the output flow, but the physical displacement of the pump always remains the same. With a variable displacement pump, the oil volume output can change based on the displacement change. This can be done in several different ways with a variety of pump controls.
By far, the most common controls in the mobile world are the pressure compensator and load sense. If a pump is outfitted with a pressure-compensator control, it sits at maximum displacement until the prime mover is turned on. As the pump immediately creates flow, pressure starts to build. As the pressure builds to a predetermined setting, the pump mechanically destrokes, or reduces the pump displacement to zero. It stays at zero until a machine function is operated. At that point, the pump flows oil to the function as quickly as physically possible. One advantage of this system is that it reacts quickly. This type of control is a good choice for a mobile machine such as a telehandler, in which the operator wants no lag between joystick operation and a function move. The disadvantage of a pressure-compensated system is that it is always at the maximum compensator pressure setting, or high-pressure standby. So if high-flow low-pressure functions are run, the net result is a high-pressure drop between the pump and actuator, resulting in heat.
Load sense is a variation of the pressure-compensator control but takes it a step further. Just as with the pressure-compensator control, when the machine is off, the pump sits at maximum displacement via a bias spring. When the prime
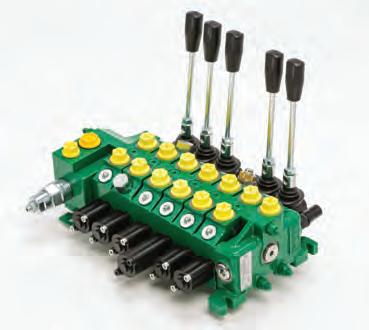
An open-center sectional valve commonly used in mobile applications.
Image courtesy Salami SpA.
mover turns on, the pump starts to create flow and pressure builds. But instead of reaching the compensator setting, the load-sense control destrokes the pump at a lower predetermined setting, referred to as low-pressure standby. A common low-pressure standby setting is 300 psi (21 bar).
The advantage of the load-sense pump is that it is very efficient if used on a machine that can see many different load conditions or pressures. The disadvantage is that you must use a load-sense valve with the pump. That adds cost and complexity to the overall system. There are many controls available for mobile equipment including horsepower limiting, electroproportional displacement, hydraulic pilot control, and more. But the load-sense system is one of the most popular on mobile equipment.
It’s not always the case, but in general it seems piston and gear pumps have taken over the mobile market. Many applications can run between 3,000 and 4,000 psi (207 and 276 bar) maximum operating pressure, with many maxing out at 3,000 psi (207 bar), making the gear pump a possibility depending on the control scheme. The outlier is the hydrostatic drive pump that routinely has a maximum operating pressure of up to 6,000 psi (414 bar).
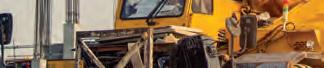
Among all the product categories, the directional control valve probably differs more than any other. It is common in that it can control the direction and flow of oil. But virtually everything else is different in size, shape, weight, corrosion-resistant options, electrical connectors, and so on. There is a gray area, because it is still common to see small industrial valves – sizes D03 and D05 – on mobile machinery.
Mobile directional control valves come in two forms: monoblock and sectional. A monoblock valve has one body but can have up to eight spools within that body. Many are available in tandem, parallel, or series circuits. These valves are less expensive but also less flexible. Monoblocks are a good choice for equipment manufacturers that use the same valve repeatedly.
Sectional valves have an individual spool in each body, or section. The sections are held together with tie rods. Typically eight to twelve sections can be stacked together depending on the particular valve’s manufacture and size. This type of modular valve allows for many different combinations of options, making it an attractive solution for end users and equipment manufacturers alike.
There are two types of mobile valve circuits: open center and closed center.
Open center. Open-center circuits consist of a fixed-displacement pump and an open-center type mobile directional control valve. The fixed pump (typically gear) creates constant oil flow, which flows through the directional control valve and back to tank at a low-pressure drop. When the valve is operated, the main spool moves and starts to cut off the flow to tank and redirect it to the valve work ports. As the spool continues to stroke, more oil flow is directed to the work port and less to tank. When the spool strokes fully, 100% of the flow is redirected to the work port.
Within the open-center valve platform, there are three common circuit options, described as parallel, tandem, and series. The schematic (Continued on page 10)
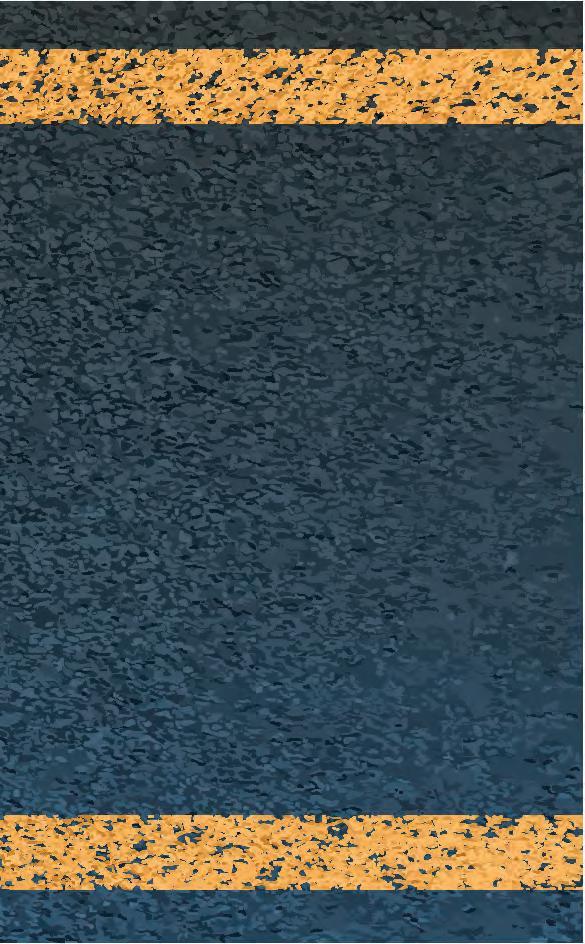
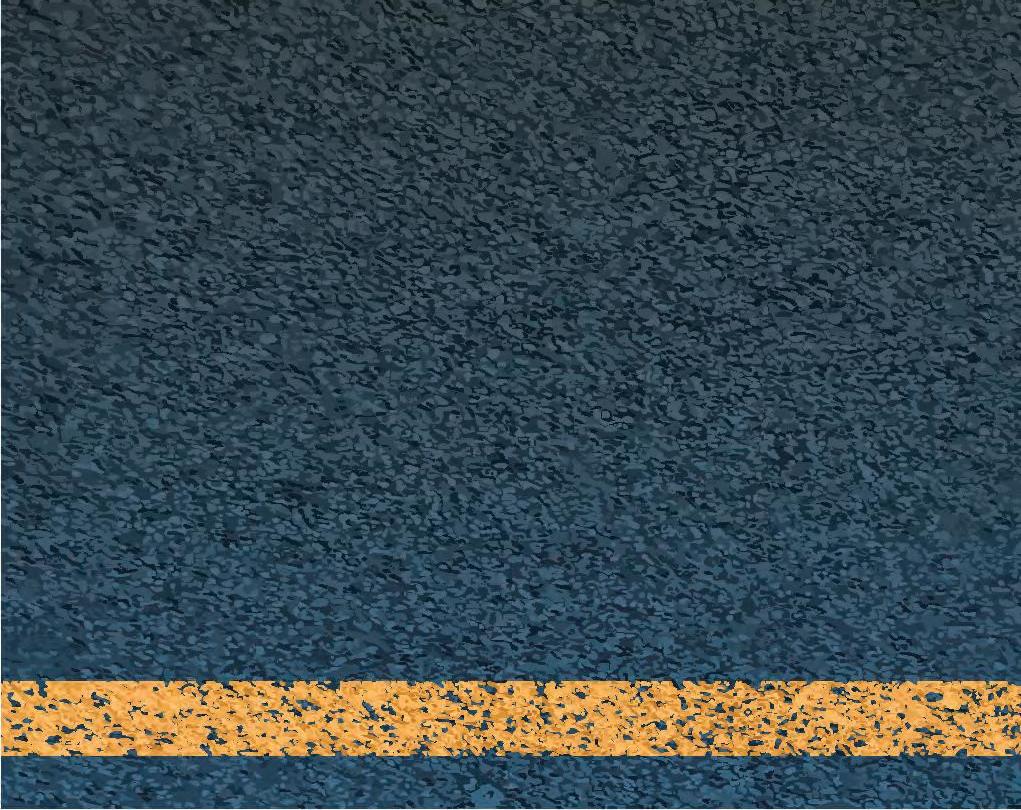
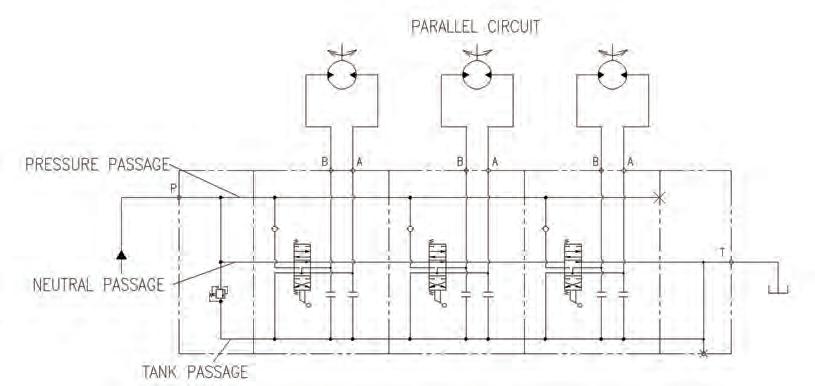
(Continued from page 9) symbols of each circuit show the pressure, neutral, and tank passages (see illustrations at right).
In a parallel circuit, the main inlet pressure is connected to all the spool, or section, P ports through one main pressure core or passage. In this case, if multiple functions are run, the oil can take the path of least resistance and cause a function to slow or stop.
In a tandem circuit, the main pressure passage is cut off between each section, allowing oil to be directed through a neutral passage only. If each section in a valve stack is tandem, the upstream section will always have flow priority. The oil coming out of the actuator (cylinder or motor) is directed by the spool back to the tank port via the tank passage.
In a series circuit, the pressure passage is cut off between each section but allows oil to run through the neutral core. After the oil returns from the actuator (cylinder or motor), it flows over the spool, but instead of going back to tank, it is routed to the next section’s pressure passage. This allows 100% of the oil flowing into the valve to go through each actuator and run them in series.
Closed center. Closed-center valves do not allow oil to flow through the valve and back to tank but will block the flow completely. In cases where this type of valve is used, a variable-displacement pressure-compensated pump is required. When the prime mover is turned on, the pump will destroke at a predetermined pressure. When a function is operating, the pressurized oil moves the actuator responsively.
Load-sense valves are more complex. They are closed center and must be used with a variable-displacement pressure-compensated load-sense pump control. The added loadsense function works like this: When the valve is operated, a load-sense signal is generated and directed back to the pump control via a separate load-sense line, allowing the pump to stroke and develop flow. This type of system is an advantage when there are varying flow and pressure requirements. The correct flow is provided at load pressure plus the set stand-by pressure.
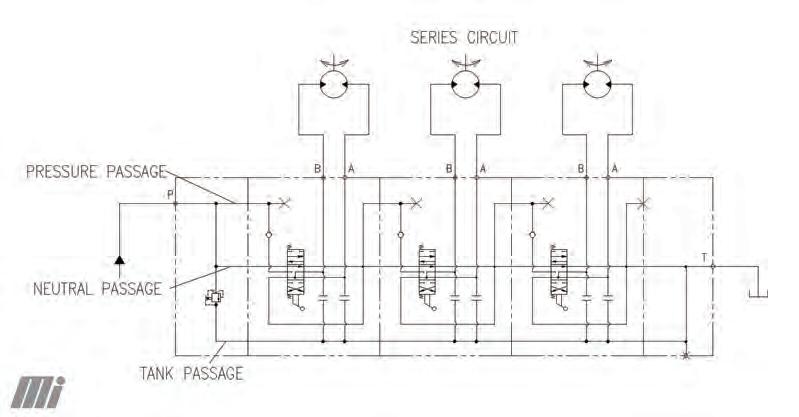
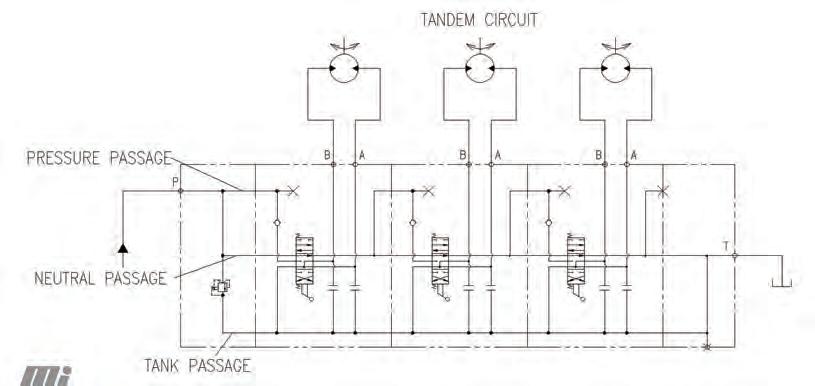

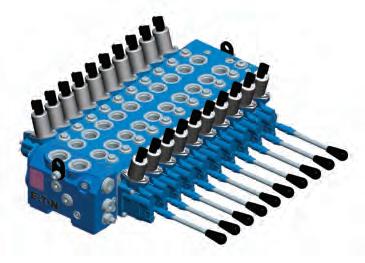
Image courtesy Eaton
Load-sense systems can be split into two technologies: precompensated and postcompensated. The precompensated valve is the original technology. The disadvantage is that when the machine calls for more flow than the pump can offer, the highest pressure function slows or completely stops (path of least resistance). The operation of the postcompensated valve is different. When the machine calls for more flow than the pump can offer, all the functions slow down proportionally. The main advantage of the postcompensated system is it does not allow any one function to stop, which gives the operator more predictive and consistent control of the machine under varying operating conditions.
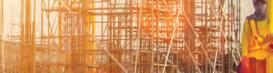
Steering control units, often referred to as steering orbitrols, are components much more frequently found in a mobile application than in an industrial application. They are used in conjunction with a column and wheel to steer a machine. Applications include lawn and garden, lift trucks, construction, forestry, agricultural vehicles, dump trucks, forklifts, and tractors.
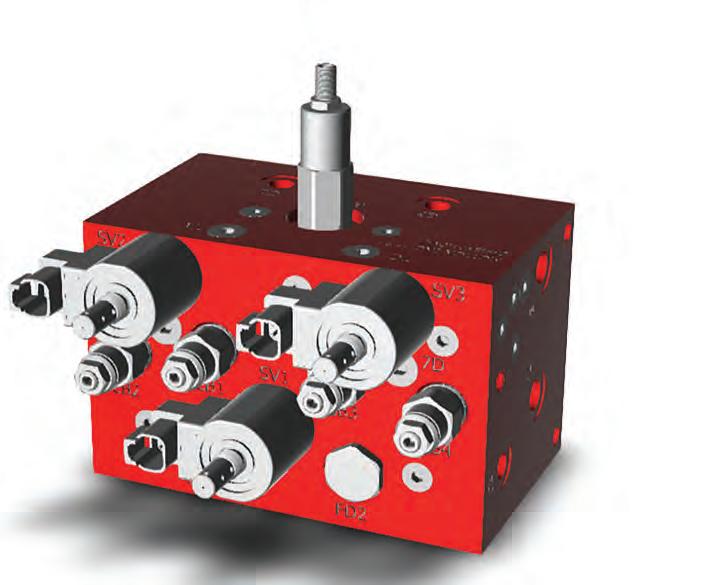

Cylinders are available in an infinite number of sizes, configurations, and complexities. There are standard “off-the-shelf” cylinders as well as customized cylinders with mounted manifolds for load holding or other hydraulic circuits. Like industrial fluid power systems, cylinders in mobile systems are very application-specific, including the telescopic cylinders used on applications such as dump trucks. Most of the cylinders that we see on mobile equipment are of a welded design, versus the tie-rod and milltype cylinders found on industrial equipment. Not to exclude the telescopic cylinders used on applications such as dump trucks.

Motors, like pumps, are available in vane, gear, and piston design. The performance and cost comparisons between them are the same as well. No matter what the technology used, hydraulic motors seem to cross over the most out of all the product categories. Motors come in several mounting configurations and are used to turn tracks, wheels, augers, mixers, swing drives, and more on a variety of mobile equipment.
Another technology attributed to mobile hydraulics is the hydrostatic transmission. Often it is used as a ground drive to propel machines but found on many motor circuits where reversing direction and variable flow is required.
The hydrostatic pump and motor both have two pressure ports, A and B. The ports are connected or “looped” together so that the oil that comes out of the motor goes directly back into the pump. The pump itself can supply oil out of
Image courtesy Motion
3D model of a custom manifold assembly.
the A or B port. That is what allows the motor to reverse. What makes the motor unique is that it often has a hot-oil shuttle built right into it that strips oil out of the loop so it can run through a filter or heat exchanger. In the hydrostatic pump, a small gear pump – referred to as the charge pump – replenishes the oil that was stripped away by the hot-oil shuttle and the case drains.
Hydrostatic transmissions are used in applications like tractors, forestry machines, golf course maintenance equipment and more.
Cartridge valves were created because equipment manufacturers demanded more flexibility in the design of their hydraulic systems and the industry demand for refinements to their line-mounted hydraulic systems to a more compact design. The result is a more simplified installation appearance of the system and fewer hydraulic hoses, fittings, and mounting brackets, eliminating many leakage problems.
Cartridge valves are commonly used to control oil pressure, direction, and flow. Valves are either spool, poppet, or ball check design. Screw-in cartridges are very compact and produce inexpensive circuits that are reliable and easy to maintain. Screw-in cartridges are most often part of a machined manifold but also are available in individual bodies. Custom machined manifolds with cartridge valves compress the overall envelope size by combining valving and plumbing into one complete package.
Installation and maintenance of custom manifolds are more simplified when compared to traditional, line-mounted valve systems. The need to connect valves by hydraulic hoses and fittings is reduced using internal passages machined into the manifold block. By designing one or more manifold blocks into a system, the time and cost of installing the hydraulic system are much less than traditional, linemounted valve systems. Advantages for OEMs using a custom manifold block with cartridges are greater design flexibility, lower installed cost, smaller package size, less external leakage, easier troubleshooting, easier maintenance, organized plumbing, and lower noise levels. Compact manifold assemblies reduce the system size and weight, allowing for smaller, more efficient mobile applications.
The differences between mobile and industrial hydraulics have evolved in response to the performance and environmental requirements of the equipment being produced. These industries are evolving with various demands of technology, flexibility of systems, cost savings, and efficiency requirements. Fluid power products and solutions specific to mobile or industrial equipment continue to evolve. Although hydraulic components serve similar functions across both segments, understanding differences between these components’ functionalities, their applications, and how the machinery operates benefits equipment users and designers alike.
Robert Sheaf has more than 45 years troubleshooting, training, and consulting in the fluid power field. Email rjsheaf@cfc-solar. com or visit his website at www. cfcindustrialtraining.com.
COIL RETRACT TO EXPAND
EXPAND SOL. A
DR A B
P T COLLAPSED SOL. B
D07 VICKERS TOP
RACINE MAIN STAGE 11 2" PIPE
New Problem
Pilot Operated Directional Valve Locks Up
30 HP 1200
By Robert Sheaf, CFPAI/AJPP, CFPE, CFPS, CFPECS, CFPMT, CFPMIP, CFPMMH, CFPMIH, CFPMM, CFC Industrial Training
1000 PSI HH9660024DNUBT PALL PRESSURE FILTER HC9600FDN16H
40 GPM
PALL FILTER HC0293SEE5
120 GAL TANK 0 - 3000 PSI VICKERS 0FM - 202
»I GOT A call to help with a problem on an aluminum uncoiling station. The customer would collapse the expander that held the coil and installed a new coil to unwrap. They would cycle the directional valve back and forth while properly positioning the coil. If they were having trouble and cycled the directional valve more than four to six times, the valve would lock up and wouldn’t shift in either direction.
They would call maintenance to troubleshoot the problem and, depending how quickly maintenance arrived, the valve would either cycle or lock up. The longer it took, the better chance the valve would then work. But if they cycled it several times, it would lock up. The directional valve and PO check were mounted close to the expander, while the power unit was about 30 feet away. The pump did supply oil to three other functions that had directly operated valves, and they worked well. They replaced the directional valve with a new one, and it would cycle 10 to 12 times and then lock up.
What could be causing the problem?
Solution to July 2021 problem: Servo System Pump Keeps Failing
After inspecting the system where the pressurecompensated pumps were failing, I wondered why there was not a spike-suppressant directly operated relief valve to keep the pressure spikes under control. The designer had used the accumulator to soften the system and control the pressure spikes. I found the bladder in the accumulator had failed.
To view previous problems, visit www. fluidpowerjournal.com/figure-it-out.
BLOW MOLDING NOZZLE CONTROL CYLINDER
DIAPHRAGM ACCUMULATOR
PRESSURE FILTER MOOG SERVO VALVE RETURN FILTER
LIFT HANDLE
EM 5
SET AT 2000 PSI HINGED TOP
IFPS Names Hall of Fame Inductees
»TO MARK FLUID Power Professionals’ Day in June, the International Fluid Power Society announced nine inductees to the Fluid Power Hall of Fame. They will be honored at an Oct. 6 ceremony during IFPS’s annual meeting in Reno, Nevada. Two inductions are posthumous.
PETER A.J. ACHTEN
Peter A.J. Achten, Ph.D., holds over 40 individually titled worldwide patents and has authored more than 200 survey reports, papers, articles, and books. He has presented speeches, workshops, and lectures around the world in several languages. Achten was awarded the Robert E. Koski Medal in 2019 and the Joseph Bramah Medal in 2008.
TIMOTHY R. BAILEY
Australian Timothy R. Bailey helped develop several of his country’s fluid power organizations and has served as president of the Western Australian Fluid Power Society, the International Fluid Power Society Australia, the Fluid Power Society Australia, and the Fluid Power Society (WA). He helped create the original WAFPS Curriculum Matrix. He has focused on safety throughout his career.
JIM BRIZZOLARA
Jim Brizzolara cofounded HydraForce in 1985. The company has won awards and accolades throughout the industry. With a strong emphasis on community involvement and student training, HydraForce has supported students, suppliers, and employees through more than $400,000 in grants, tuition support, and training programs, including full sponsorship for the Wheeling High School robotics lab.
GEORGE DOIG
After his service in the U.S. Navy during World War II, George Doig and three others founded Numatics in 1953. In the 1950s, Doig became one of 30 founders of IFPS and chapter 1 in Detroit. In 1966 he coauthored the book “Practical Air Circuitry.” He founded manufacturers’ representative Doig Associates in 1972. He holds four air control patents and was a certified fluid power engineer from 1994 to 2010.
CELEBRATING 60 YEARS
CRAIG M. FOX
Craig M. Fox served as technical editor for the Lightning Reference Handbook. He worked for Eaton Corporation in Maumee, Ohio, as a senior technical trainer and contributed to Eaton’s Industrial Hydraulics Manual. He is an active member of the electronic technology curriculum review board for the College of the Canyons in Santa Clarita, California.
MEDHAT KHALIL
Medhat Khalil, Ph.D., won the 2012 Otto Maha Pioneer in Fluid Power award and is in his 16th year as the director of professional education and research development for the Applied Technology Center of the Milwaukee School of Engineering. He has contributed to the specification and commissioning of training labs and centers for MSOE, Concordia University, Egyptian Iron & Steel Company, and the Giza, Egypt, Civil Aviation Authority. He is author of five books.
NOAH D. MANRING
Noah D. Manring, Ph.D., P.E., has served on the faculty of the Mechanical and Aerospace Engineering Department at the University of Missouri since 1997, becoming dean of engineering in 2020. He has published 44 archival journal papers, 38 conference papers, and three books on fluid power. He holds 12 U.S. patents, including one in 2018 for monitoring cardiovascular disease. He served from 2006 to 2010 as scientific advisory to the Center for Compact and Efficient Fluid Power.
HARLEY E. BERGREN (1917-2021)
Harley E. Bergren unfortunately passed away March 19, three days before his 104th birthday. Bergren founded Power Systems in Minnesota in 1966. He retired in 1982 but remained a company stockholder until the company was sold in 1998. He developed a unique lawn-mower drive system before hydrostatics was invented, using a cam, a valve, and two gear pumps. In 1967, he obtained the patent for a hydrostatic transmission.
RICHARD J. FONTECCHIO (1948-2014)
Richard “Dick” Fontecchio began his fluid power career in 1965 at Fluid Power Systems in Glenview, Illinois. In 1985, he cofounded HydraForce with Jim Brizzolara in Northbrook, Illinois. With Fontecchio’s leadership as vice president of sales and marketing, HydraForce released over 15,000 standard and proprietary valves and their electrohydraulic controls. The company grew into the world’s largest supplier of hydraulic and electrohydraulic valves, manifolds, and controls.
Fluid Power Symbology Guide
MEMBER PRICE: $12.85 • NON-MEMBER: $16.00
This 30-page guide presents fluid power symbols commonly used within ISO 1219-1 and 2 standards and illustrates the component function applied within fluid power systems. This Symbology Guide is permitted to be used during an IFPS certification test.
Note: ISO 1219 also specifies the drawing size and orientation of drawn components, which is not covered in this booklet; refer to ISO 1219 for further detailed information.
HYDRAULIC SYMBOLS
• Basic Symbols • Pumps and Motors • Pressure Controls • Logic Valves • Accumulators • Cylinders • Directional Control
Valves • Common
Directional Control
Valves • Fluid Conditioning • Sensors • Flow Controls • Flow Dividers • Accessory and
Misc. Components
ELECTRICAL SYMBOLS
• Basic Electrical
Symbols • Electrical Relay
Diagram Symbols • Logic Gate Symbols
PNEUMATIC SYMBOLS
• Basic Symbols • Air Compressor,
Air Motors and Vacuum
Components • Pressure Controls • Logic Elements • Cylinders • Directional Control
Valves • Common
Directional Control
Valves • Fluid Conditioning • Flow Controls • Sensors • Accessory and
Misc. Components
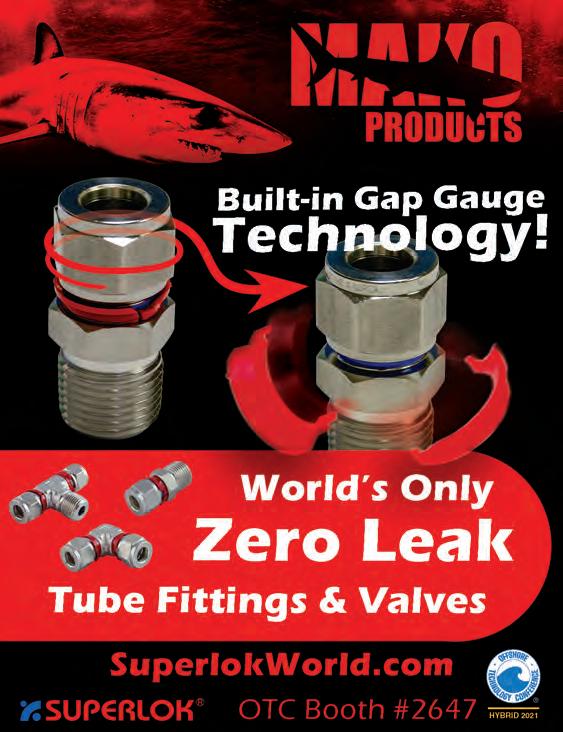
CELEBRATING 60 YEARS
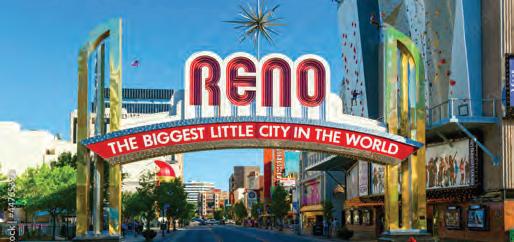
IFPS Annual Meeting Set for October
»THE INTERNATIONAL FLUID Power Society’s annual meeting takes place in person Oct. 5-7 in Reno, Nevada.
IFPS hosts the Fluid Power Hall of Fame awards ceremony on Oct. 6. Nine inductees, including two posthumous, will be acknowledged for their significant contributions to the fluid power industry. (See page 13.)
The annual meeting is a great way to network with professionals in the industry. To register, visit www.ifps.org.
SCHEDULE OF EVENTS
Monday, Oct. 4
8:00 AM - 2:00 PM............................................. Technical Workshop
Tuesday, Oct. 5
8:00 AM - 9:00 AM..............Strategic Planning Committee Meeting 9:00 AM - 11:00 AM ......................... Education Committee Meeting 11:00 AM - 12:00 PM ...................Membership Committee Meeting 12:00 PM - 12:30 PM ...................................................Hosted Lunch
12:30 PM - 1:30 AM .........Membership Committee Meeting, cont'd 1:45 PM - 5:00 PM....................... Tesla Gigafactory Tour (tentative) 6:00 PM - 9:00 PM..........................Welcome Reception & Jeopardy
Wednesday, Oct. 6
8:00 AM - 12:00 AM ..................... Certification Committee Meeting 12:00 PM - 1:00 PM......................................................Hosted Lunch 1:00 PM - 3:30 PM............................ Marketing Committee Meeting 6:00 PM - 9:30 PM Annual Dinner & Hall of Fame Awards Ceremony
Thursday, Oct. 7
8:00 AM - 9:30 AM................................Finance Committee Meeting 9:30 AM - 11:00 AM ............................... Board of Directors Meeting 11:00 AM - 12:00 PM Strategic Planning Committee Meeting Follow Up 12:00 PM - 1:00 PM.......................................... Lunch (on your own) 1:30 PM - 9:00 PM Lake Cruise & Dinner at Lake Tahoe (tentative)
May 2021
Newly Certified Professionals
AUTHORIZED JOB PERFORMANCE PROCTOR
John Popek, Perfection Servo Hydraulics Adam Smith, Controlled Fluids Inc.
MASTER OF INDUSTRIAL PNEUMATICS
holds PT, PM, and CC Certifications Steven Downey, Hydraulic Parts Source
PNEUMATIC SPECIALIST
Dylon Ackerman, Bedford Industries Isaac Frieden, Sun Hydraulics
CONNECTOR & CONDUCTOR
Ariel Garza, Controlled Motion Solutions Matthew Marquiss, Manitowoc Cranes Kurt Smay, Manitowoc Cranes Dalton Wilson, Manitowoc Cranes
MASTER TECHNICIAN
holds IHT, MHT, and PT Certifications Steven Downey, Hydraulic Parts Source
SPECIALIST
holds HS and PS Certifications Dylon Ackerman, Bedford Industries Isaac Frieden, Sun Hydraulics
ELECTRONIC CONTROLS SPECIALIST
Alejandro Hernandez, SunSource
HYDRAULIC SPECIALIST
Alex Adams, Womack
Chris Dole
Tyler Sorensen, Marmon-Herrington Nicholas Wiebelt, EMI, A Division of W&O
MOBILE HYDRAULIC MECHANIC
Enoch Abell, Altec Industries Inc. Christopher Absher, Altec Industries Inc. Francisco Armendariz, Southern California Edison Cole Blanton, American Electric Power Ryan Bruce, Altec Industries Inc. Adrian Caballero, Southern California Edison Omar Cardenas, Southern California Edison Andrew Chapa, American Electric Power Co. Jimmy Cockrell, Terex Utilities Christopher Coffee, Altec Industries Inc. Christopher Coleman, Terex Utilities Stephen Crocker, Altec Industries Inc. Charles Edwards, Terex Utilities
Robert Ellsworth
Gregory Funderburg, Altec Industries Inc. Thomas Gardenhire, Terex Utilities Morgan Harris, Terex Utilities Phillip Hernandez, Altec Industries Inc. Chad Hrnjak, Altec Industries Inc. David Kennard, Southern California Edison Dylan Lee, Altec Industries Inc. Jeremy McCutcheon, Terex Utilities Brion Myers, Southern California Edison Robert O'Neil, Altec Industries Inc. John Pettigrew, Southern California Edison Christopher Quigg, Southern California Edison John Quiles, Southern California Edison Jonathan Redden, The Illuminating Co Donald Rowe, Altec Industries Inc. Steve Sanchez, Altec Industries Inc. Heath Schultz, Altec Industries Inc. Seth Shubirg, AEP Matt Singer, AEP Jakob Spurlock, Altec Industries Inc. Daniel Taylor, Altec Industries Inc. Ryan Thomas, Altec Industries Inc.
Casey Tucker
Jackson Wagner, Altec Industries Inc. Frank Weitoish, First Energy Corp. Ethan Whitson, Altec Industries Inc. Dustin Williams, AEP
PNEUMATIC TECHNICIAN
Steven Downey, Hydraulic Parts Source
Introducing!
9S SERIES INVESTMENT CAST SWIVELS

The “9S” Series swivels represent one of the most complete range of sizes and configurations available to the industry. This series has been redesigned to incorporate a one piece barrel arrangement thus eliminating the need for braze joints. These swivels are pressure balanced with operating pressures up to 5,000 psi. All configurations are designed with a 4:1 Safety Factor and include RoHS compliant zinc plating.
P.O. Box 6479, Fort Worth, TX 76115 V. 817/923-1965 www.hydraulicsinc.com

Certification Testing Locations
Individuals wishing to take any IFPS written certification tests can select from convenient locations across the United States and Canada. IFPS is able to offer these locations through its affiliation with the Consortium of College Testing Centers provided by National College Testing Association.
Contact headquarters if you do not see a location near you. Every effort will be made to accommodate your needs.
If your test was postponed due to the pandemic, please contact headquarters so that we may reschedule.
TENTATIVE TESTING DATES FOR ALL LOCATIONS:
September 2021
Tuesday 9/14 • Thursday 9/30
October 2021
Tuesday 10/5 • Thursday 10/28
November 2021
Tuesday 11/2 • Thursday 11/18
December 2021
Tuesday 12/7 • Thursday 12/16
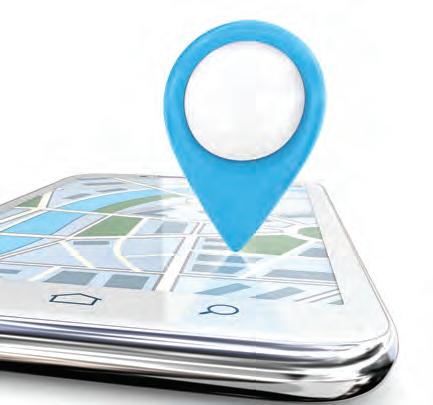
ALABAMA
Auburn, AL Birmingham, AL Calera, AL Decatur, AL Huntsville, AL Jacksonville, AL Mobile, AL Montgomery, AL Normal, AL Tuscaloosa, AL
ALASKA
Anchorage, AK Fairbanks, AK
ARIZONA
Flagstaff, AZ Glendale, AZ Mesa, AZ Phoenix, AZ Prescott, AZ Scottsdale, AZ Sierra Vista, AZ Tempe, AZ Thatcher, AZ Tucson, AZ Yuma, AZ
ARKANSAS Bentonville, AR Hot Springs, AR Little Rock, AR
CALIFORNIA
Aptos, CA Arcata, CA Bakersfield, CA Dixon, CA Encinitas, CA Fresno, CA Irvine, CA Marysville, CA Riverside, CA Salinas, CA San Diego, CA San Jose, CA San Luis Obispo, CA Santa Ana, CA Santa Maria, CA Santa Rosa, CA Tustin, CA Yucaipa, CA
COLORADO
Aurora, CO Boulder, CO Springs, CO Denver, CO Durango, CO Ft. Collins, CO Greeley, CO Lakewood, CO Littleton, CO Pueblo, CO
DELAWARE
Dover, DE Georgetown, DE Newark, DE
FLORIDA
Avon Park, FL Boca Raton, FL Cocoa, FL Davie, FL Daytona Beach, FL Fort Pierce, FL Ft. Myers, FL Gainesville, FL Jacksonville, FL Miami Gardens, FL Milton, FL New Port Richey, FL Ocala, FL Orlando, FL Panama City, FL Pembroke Pines, FL Pensacola, FL Plant City, FL Riviera Beach, FL Sanford, FL Tallahassee, FL Tampa, FL West Palm Beach, FL Wildwood, FL Winter Haven, FL
GEORGIA
Albany, GA Athens, GA Atlanta, GA Carrollton, GA Columbus, GA Dahlonega, GA Dublin, GA Dunwoody, GA Forest Park, GA Lawrenceville, GA Morrow, GA Oakwood, GA Savannah, GA Statesboro, GA Tifton, GA Valdosta, GA
HAWAII Laie, HI
IDAHO
Boise, ID Coeur d ‘Alene, ID Idaho Falls, ID Lewiston, ID Moscow, ID Nampa, ID Rexburg, ID Twin Falls, ID
ILLINOIS
Carbondale, IL Carterville, IL Champaign, IL Decatur, IL Edwardsville, IL Glen Ellyn, IL Joliet, IL Malta, IL Normal, IL Peoria, IL Schaumburg, IL Springfield, IL University Park, IL
INDIANA
Bloomington, IN Columbus, IN Evansville, IN Fort Wayne, IN Gary, IN Indianapolis, IN Kokomo, IN Lafayette, IN Lawrenceburg, IN Madison, IN Muncie, IN New Albany, IN Richmond, IN Sellersburg, IN South Bend, IN Terre Haute, IN
IOWA
Ames, IA Cedar Rapids, IA Iowa City, IA Ottumwa, IA Sioux City, IA Waterloo, IA
KANSAS
Kansas City, KS Lawrence, KS Manhattan, KS Wichita, KS
KENTUCKY
Ashland, KY Bowling Green, KY Erlanger, KY Highland Heights, KY Louisville, KY Morehead, KY
LOUISIANA
Bossier City, LA Lafayette, LA Monroe, LA Natchitoches, LA New Orleans, LA Shreveport, LA Thibodaux, LA
MARYLAND
Arnold, MD Bel Air, MD College Park, MD Frederick, MD Hagerstown, MD La Plata, MD Westminster, MD Woodlawn, MD Wye Mills, MD
MASSACHUSETTS
Boston, MA Bridgewater, MA Danvers, MA Haverhill, MA Holyoke, MA Shrewsbury, MA
MICHIGAN
Ann Arbor, MI Big Rapids, MI Chesterfield, MI Dearborn, MI Dowagiac, MI East Lansing, MI Flint, MI Grand Rapids, MI Kalamazoo, MI Lansing, MI Livonia, MI Mount Pleasant, MI Sault Ste. Marie, M Troy, MI University Center, MI Warren, MI
MINNESOTA
Alexandria, MN Brooklyn Park, MN Duluth, MN Eden Prairie, MN Granite Falls, MN Mankato, MN
MISSISSIPPI
Goodman, MS Jackson, MS Mississippi State, MS Raymond, MS University, MS
MISSOURI
Berkley, MO Cape Girardeau, MO Columbia, MO Cottleville, MO Joplin, MO Kansas City, MO Kirksville, MO Park Hills, MO Poplar Bluff, MO Rolla, MO Sedalia, MO Springfield, MO St. Joseph, MO St. Louis, MO Warrensburg, MO
MONTANA
Bozeman, MT Missoula, MT
NEBRASKA
Lincoln, NE North Platte, NE Omaha, NE
NEVADA
Henderson, NV Las Vegas, NV North Las Vegas, NV Winnemucca, NV
NEW JERSEY
Branchburg, NJ Cherry Hill, NJ Lincroft, NJ Sewell, NJ Toms River, NJ West Windsor, NJ
NEW MEXICO
Albuquerque, NM Clovis, NM Farmington, NM Portales, NM Santa Fe, NM
NEW YORK
Alfred, NY Brooklyn, NY Buffalo, NY Garden City, NY New York, NY Rochester, NY Syracuse, NY
NORTH CAROLINA
Apex, NC Asheville, NC Boone, NC Charlotte, NC China Grove, NC Durham, NC Fayetteville, NC Greenville, NC Jamestown, NC Misenheimer, NC Mount Airy, NC Pembroke, NC Raleigh, NC Wilmington, NC
NORTH DAKOTA
Bismarck, ND
OHIO
Akron, OH Cincinnati, OH Cleveland, OH Columbus, OH Fairfield, OH Findlay, OH Kirtland, OH Lima, OH Maumee, OH Newark, OH North Royalton, OH Rio Grande, OH Toledo, OH Warren, OH Youngstown, OH
OKLAHOMA
Altus, OK Bethany, OK Edmond, OK Norman, OK Oklahoma City, OK Tonkawa, OK Tulsa, OK
OREGON
Bend, OR Coos Bay, OR Eugene, OR Gresham, OR Klamath Falls, OR Medford, OR Oregon City, OR Portland, OR White City, OR
PENNSYLVANIA
Bloomsburg, PA Blue Bell, PA Gettysburg, PA Harrisburg, PA Lancaster, PA Newtown, PA Philadelphia, PA Pittsburgh, PA Wilkes-Barre, PA York, PA
SOUTH CAROLINA
Beaufort, SC Charleston, SC Columbia, SC Conway, SC Graniteville, SC Greenville, SC Greenwood, SC Orangeburg, SC Rock Hill, SC Spartanburg, SC
TENNESSEE
Blountville, TN Clarksville, TN Collegedale, TN Gallatin, TN Johnson City, TN Knoxville, TN Memphis, TN Morristown, TN Murfreesboro, TN Nashville, TN
TEXAS
Abilene, TX Arlington, TX Austin, TX Beaumont, TX Brownsville, TX Commerce, TX Corpus Christi, TX Dallas, TX Denison, TX El Paso, TX Houston, TX Huntsville, TX Laredo, TX Lubbock, TX Lufkin, TX Mesquite, TX San Antonio, TX Victoria, TX Waxahachie, TX Weatherford, TX Wichita Falls, TX
UTAH
Cedar City, UT Kaysville, UT Logan, UT Ogden, UT Orem, UT Salt Lake City, UT
VIRGINIA
Daleville, VA Fredericksburg, VA Lynchburg, VA Manassas, VA Norfolk, VA Roanoke, VA Salem, VA Staunton, VA Suffolk, VA Virginia Beach, VA Wytheville, VA
WASHINGTON
Auburn, WA Bellingham, WA Bremerton, WA Ellensburg, WA Ephrata, WA Olympia, WA Pasco, WA Rockingham, WA Seattle, WA Shoreline, WA Spokane, WA
WEST VIRGINIA
Ona, WV
WISCONSIN
La Crosse, WI Milwaukee, WI Mukwonago, WI
WYOMING
Casper, WY Laramie, WY Torrington, WY
CANADA ALBERTA
Calgary, AB Edmonton, AB Fort McMurray, AB Lethbridge, AB Lloydminster, AB Olds, AB Red Deer, AB
BRITISH COLUMBIA
Abbotsford, BC Burnaby, BC Castlegar, BC Delta, BC Kamloops, BC Nanaimo, BC Prince George, BC Richmond, BC Surrey, BC Vancouver, BC Victoria, BC
CELEBRATING 60 YEARS
MANITOBA
Brandon, MB Winnipeg, MB
NEW BRUNSWICK
Bathurst, NB Moncton, NB
NEWFOUNDLAND AND LABRADOR
St. John’s, NL
NOVA SCOTIA
Halifax, NS
ONTARIO
Brockville, ON Hamilton, ON London, ON Milton, ON Mississauga, ON Niagara-on-the-Lake, ON North Bay, ON North York, ON Ottawa, ON Toronto, ON Welland, ON Windsor, ON
QUEBEC
Côte Saint-Luc, QB Montreal, QB
SASKATCHEWAN
Melfort, SK Moose Jaw, SK Nipawin, SK Prince Albert, SK Saskatoon, SK
YUKON TERRITORY
Whitehorse, YU
UNITED KINGDOM
Elgin, UK
GHAZNI
Kingdom of Bahrain, GHA Thomasville, GHA
EGYPT Cairo, EG
JORDAN
Amman, JOR
NEW ZEALAND
Taradale, NZ
CFPAI
Certified Fluid Power Accredited Instructor
CFPAJPP
Certified Fluid Power Authorized Job Performance Proctor
CFPAJPPCC
Certified Fluid Power Authorized Job Performance Proctor Connector & Conductor
CFPE
Certified Fluid Power Engineer
CFPS
Certified Fluid Power Specialist (Must Obtain CFPHS & CFPPS)
CFPHS
Certified Fluid Power Hydraulic Specialist
CFPPS
Certified Fluid Power Pneumatic Specialist
CFPECS
Certified Fluid Power Electronic Controls Specialist
CFPMT
Certified Fluid Power Master Technician (Must Obtain CFPIHT, CFPMHT, & CFPPT)
CFPIHT
Certified Fluid Power Industrial Hydraulic Technician
CFPMHT
Certified Fluid Power Mobile Hydraulic Technician
CFPPT
Certified Fluid Power Pneumatic Technician
CFPMM
Certified Fluid Power Master Mechanic (Must Obtain CFPIHM, CFPMHM, & CFPPM)
CFPIHM
Certified Fluid Power Industrial Hydraulic Mechanic
CFPMHM
Certified Fluid Power Mobile Hydraulic Mechanic
CFPPM
Certified Fluid Power Pneumatic Mechanic
CFPMIH
Certified Fluid Power Master of Industrial Hydraulics (Must Obtain CFPIHM, CFPIHT, & CFPCC)
CFPMMH
Certified Fluid Power Master of Mobile Hydraulics (Must Obtain CFPMHM, CFPMHT, & CFPCC)
CFPMIP
Certified Fluid Power Master of Industrial Pneumatics (Must Obtain CFPPM, CFPPT, & CFPCC)
CFPCC
Certified Fluid Power Connector & Conductor
CFPSD
Fluid Power System Designer CFPMEC (In Development) Mobile Electronic Controls
CFPIEC (In Development) Industrial Electronic Controls
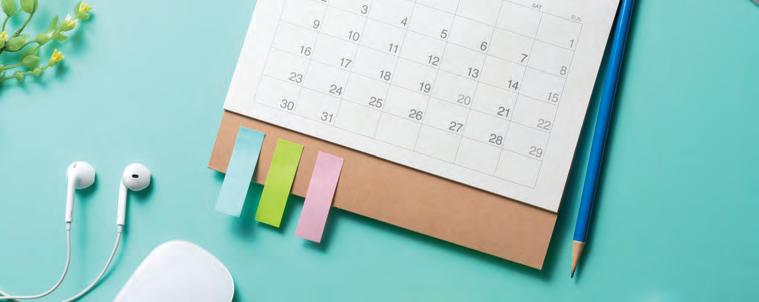
Tentative Certification Review Training
IFPS offers onsite review training for small groups of at least 10 persons. An IFPS accredited instructor visits your company to conduct the review. Contact kpollander@ifps.org for details of the scheduled onsite reviews listed below.
HYDRAULIC SPECIALIST CERTIFICATION REVIEW
September 13-16, 2021 - CFC Industrial Training, Fairfield, Ohio | Written test: September 16, 2021 September 27-30, 2021 - MSOE, Milwaukee, WI | Written test: September 30, 2021
ELECTRONIC CONTROLS CERTIFICATION REVIEW
August 9-12, 2021 - CFC Industrial Training, Fairfield, Ohio | Written test: August 12, 2021
CONNECTOR & CONDUCTOR CERTIFICATION REVIEW
November 16-17, 2021 - CFC Industrial Training, Fairfield, Ohio | Written and JP test: November 18, 2021
MOBILE HYDRAULIC MECHANIC CERTIFICATION REVIEW
Online Mobile Hydraulic Mechanic Certification Review (for written test) offered through info@cfcindustrialtraining.com. This course takes you through all chapters of the MHM Study Manual (6.5 hours) and every outcome to prepare you for the written MHM test. Members receive 20% off. (Test fees are additional - separate registration required.) August 30 - September 1, 2021 - CFC Industrial Training, Fairfield, Ohio | Written and JP test: September 2, 2021
INDUSTRIAL HYDRAULIC MECHANIC CERTIFICATION
Call for dates. Phone: 513-874-3225 - CFC Industrial Training, Fairfield, Ohio
INDUSTRIAL HYDRAULIC TECHNICIAN CERTIFICATION REVIEW TRAINING Call for dates. Phone: 513-874-3225 - CFC Industrial Training, Fairfield, Ohio
MOBILE HYDRAULIC TECHNICIAN CERTIFICATION REVIEW TRAINING
Call for dates. Phone: 513-874-3225 - CFC Industrial Training, Fairfield, Ohio
PNEUMATIC TECHNICIAN and PNEUMATIC MECHANIC CERTIFICATION REVIEW TRAINING
Call for dates. Phone: 513-874-3225 - CFC Industrial Training, Fairfield, Ohio
JOB PERFORMANCE TRAINING
Online Job Performance Review - CFC Industrial Training offers online JP Reviews, which includes stations 1-6 of the IFPS mechanic and technician job performance tests. Members may e-mail askus@ifps.org for a 20% coupon code off the list price or get the code in our Members Only area for the entire IFPS Job Performance Review; test not included.
LIVE DISTANCE LEARNING JOB PERFORMANCE STATION REVIEW
E-mail info@cfcindustrialtraining.com for information.