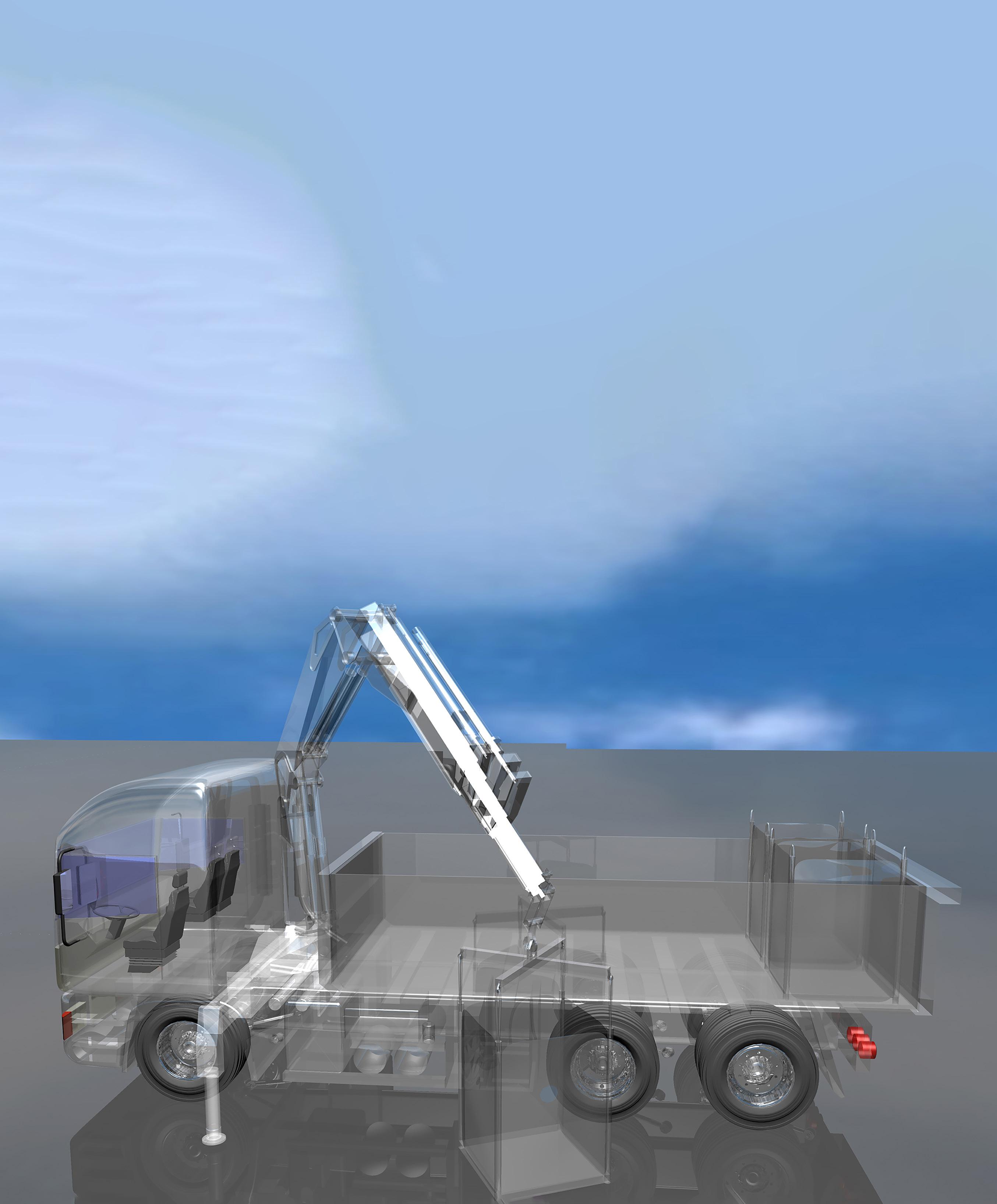
11 minute read
One for the Road: Providing Power on Demand
One for the Road
Providing Power on Demand
By Michael Pyper for Bucher Hydraulics
The compact and flexible components of a Smart PowerPack can be distributed around commercial vehicles.
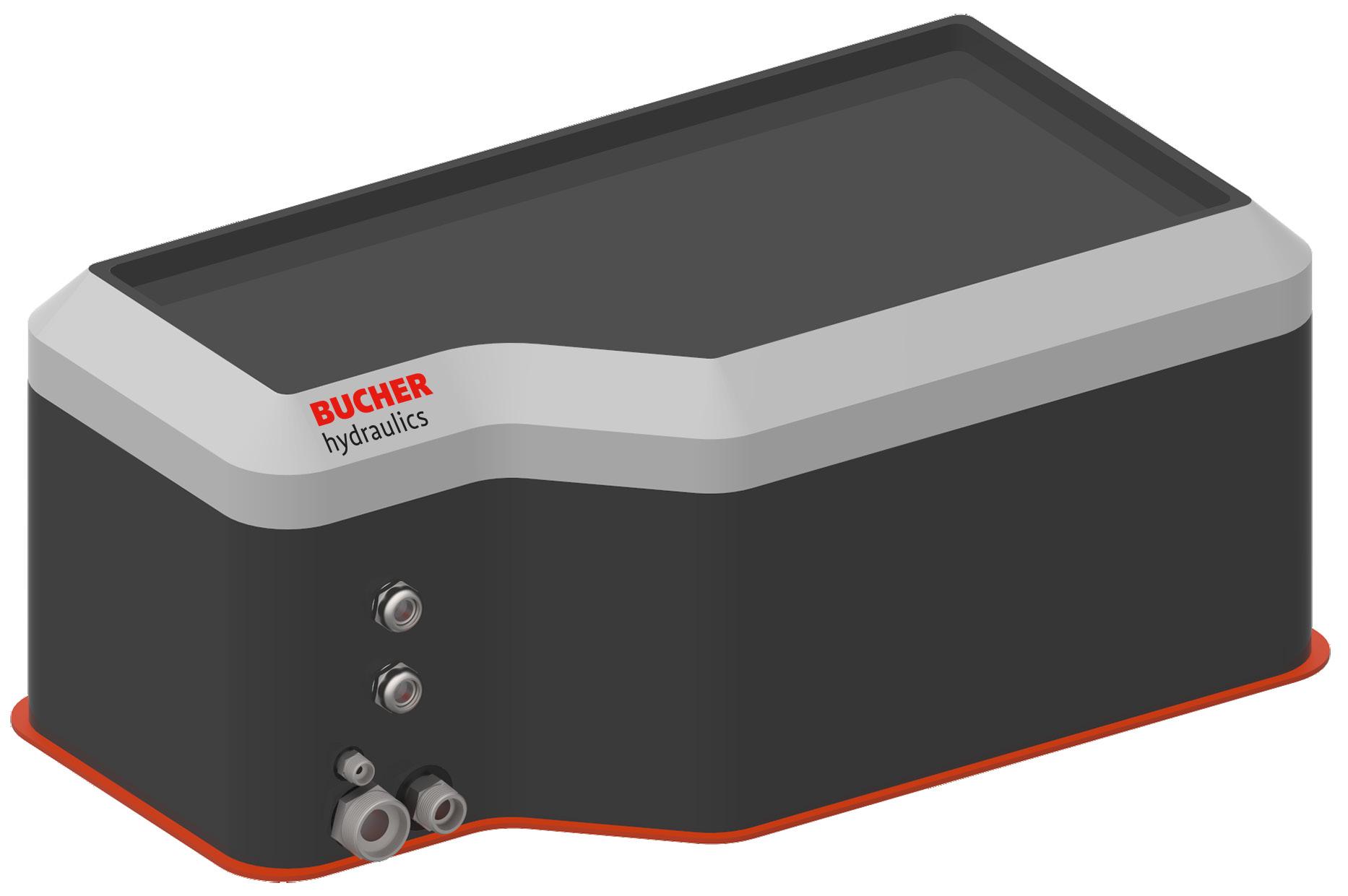
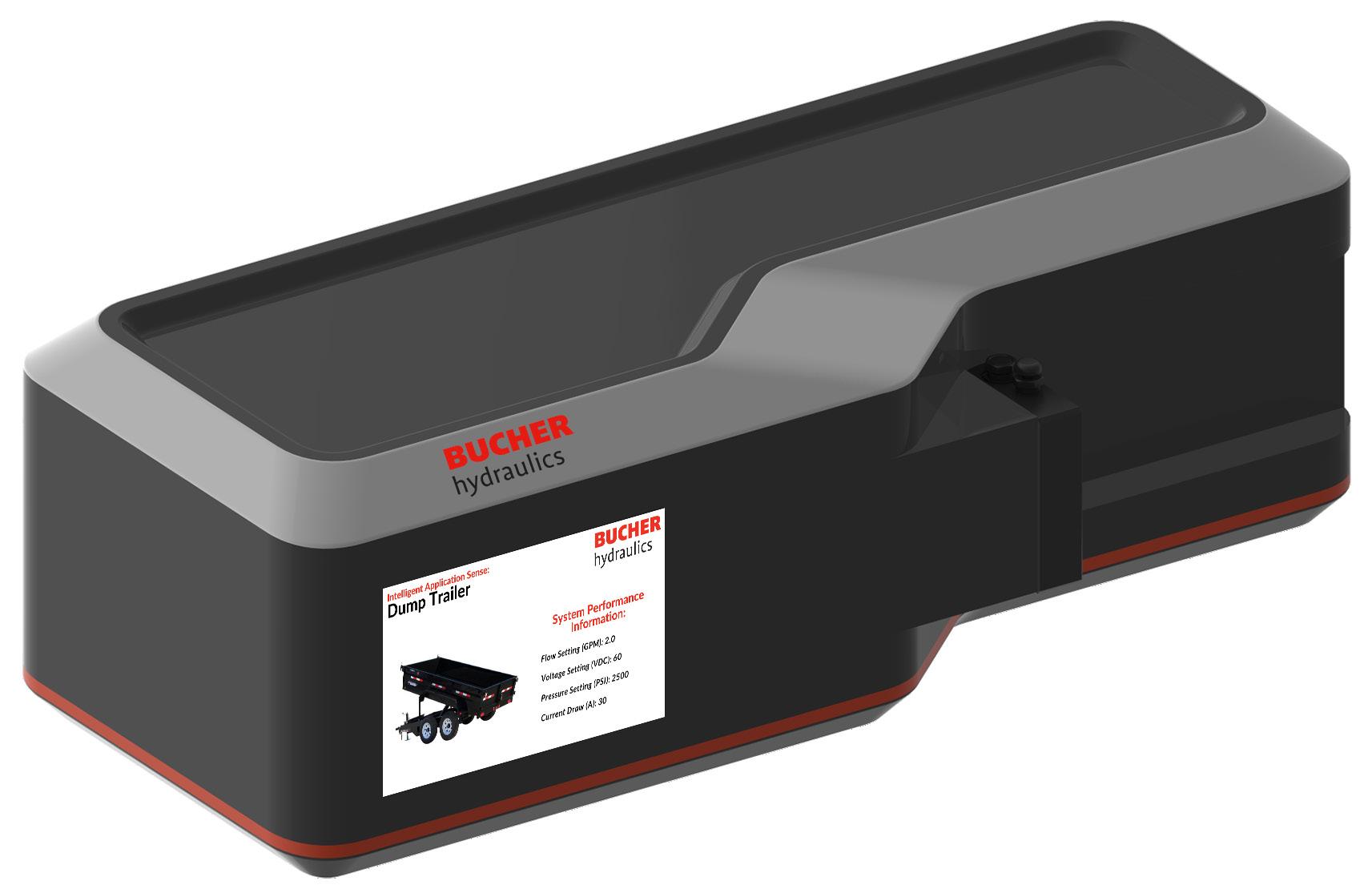
Smart PowerPack S for up to 6 kW (low voltage up to 60 VDC). Regulations for road vehicles in the European Union are becoming increasingly stringent. To reduce CO2 emissions, mechanical V-belts or power take-offs may no longer exist on future commercial vehicles. Energy-efficient electrohydraulic systems, like Bucher Hydraulics’ latest range of Smart PowerPacks, provide an alternative.
The facts are on the table. In 2019, the EU committed to reducing CO2 emissions from heavy commercial vehicles by 30% percent of 2005 levels and to achieve this by 2030. The first 15% must be achieved by 2025. Otherwise, manufacturers may face penalties of an undetermined amount that are likely to be painful. However, only on-highway trucks are affected.
Vehicles such as refuse collection and municipal trucks with loading cranes are initially exempt from the regulation. But this year, the EU Commission is scheduled to discuss how to proceed in this area, and the regulations are likely to be strict. A report called Study of the Potential for Energy/ Cost Saving in Fluid Power, commissioned by the German Federal Environment Agency, has identified and evaluated
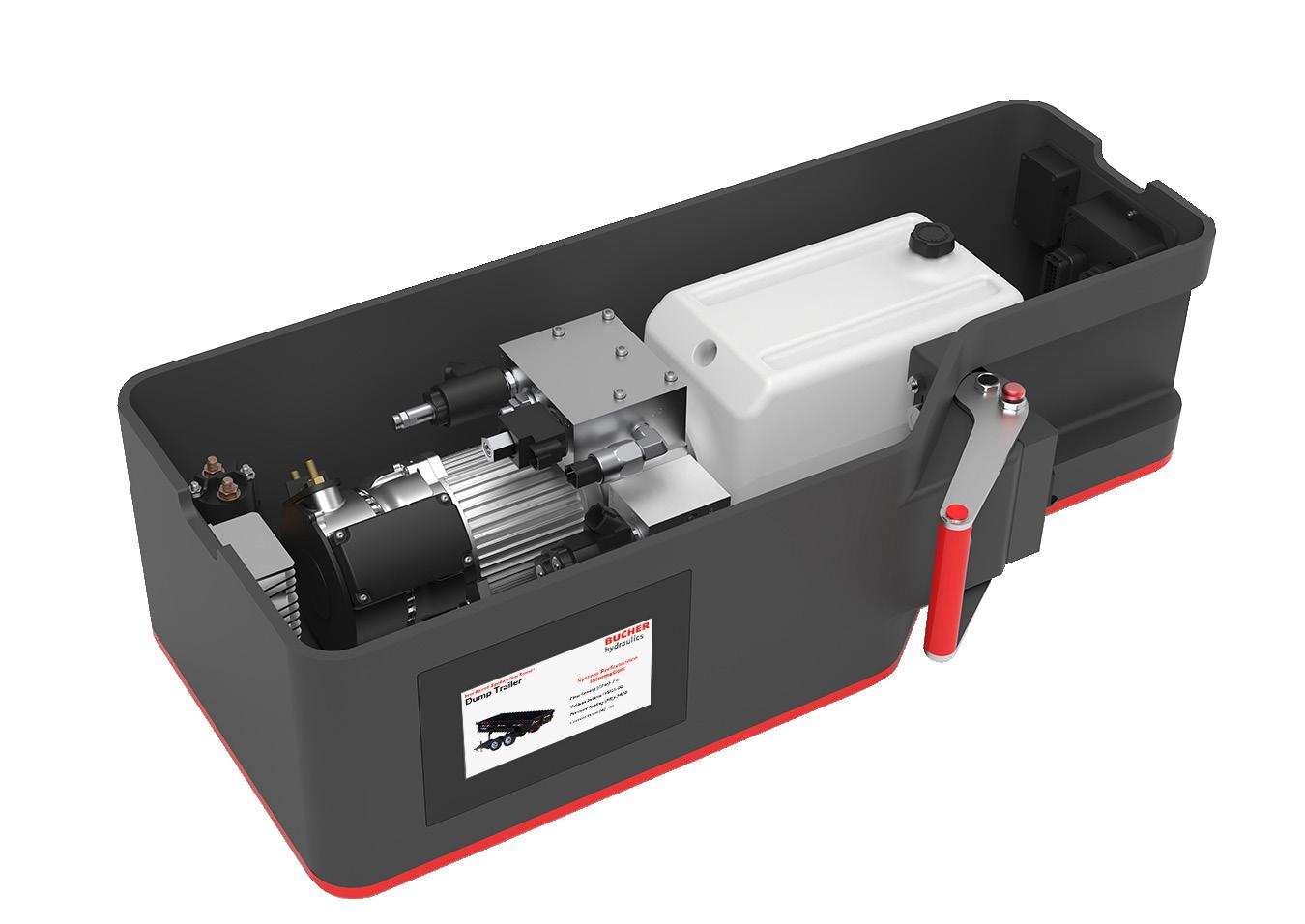
various measures for construction and agricultural machinery. Applying lessons of this report, such as the avoidance of idling periods and the demand-based control of auxiliary actuators, are particularly promising for these vehicles.
No more PTOs
If the EU regulations regarding CO2 emissions are extended to other commercial vehicles, manufacturers of auxiliary units will be particularly affected. In conventional equipment, auxiliary equipment such as cooling water pumps, air-conditioning compressors, add-on equipment for municipal work functions, and loading cranes have been driven by hydraulic pumps. These pumps are usually connected to the truck engine mechanically via a gearbox, a power take-off shaft, or a V-belt. In rare cases, they can be disconnected by couplings,
Smart PowerPack L for more than 30 kW (high voltage of 400 to 800 VDC).
The compact and flexible components of a Smart PowerPack can be distributed around commercial vehicles.
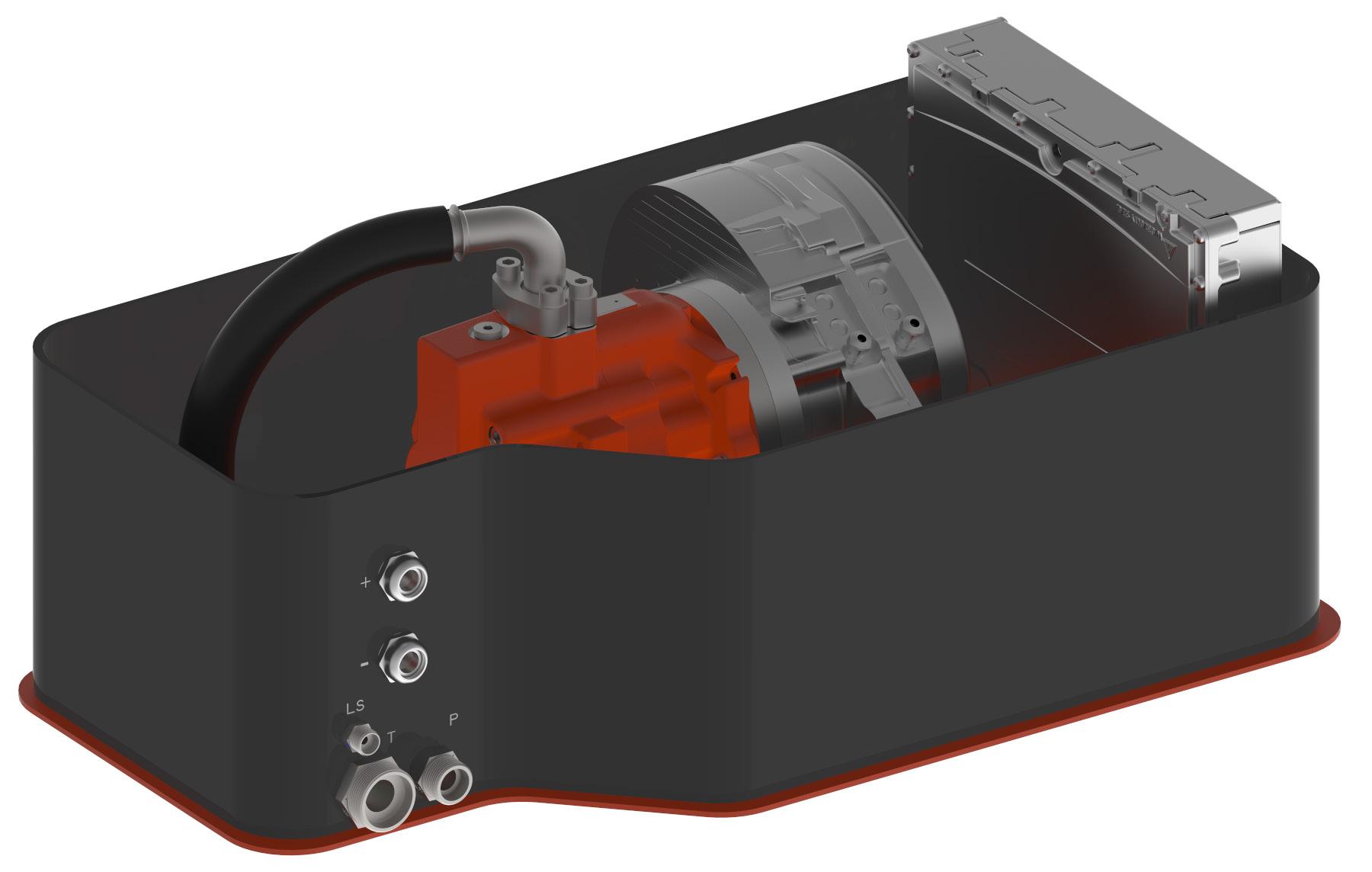
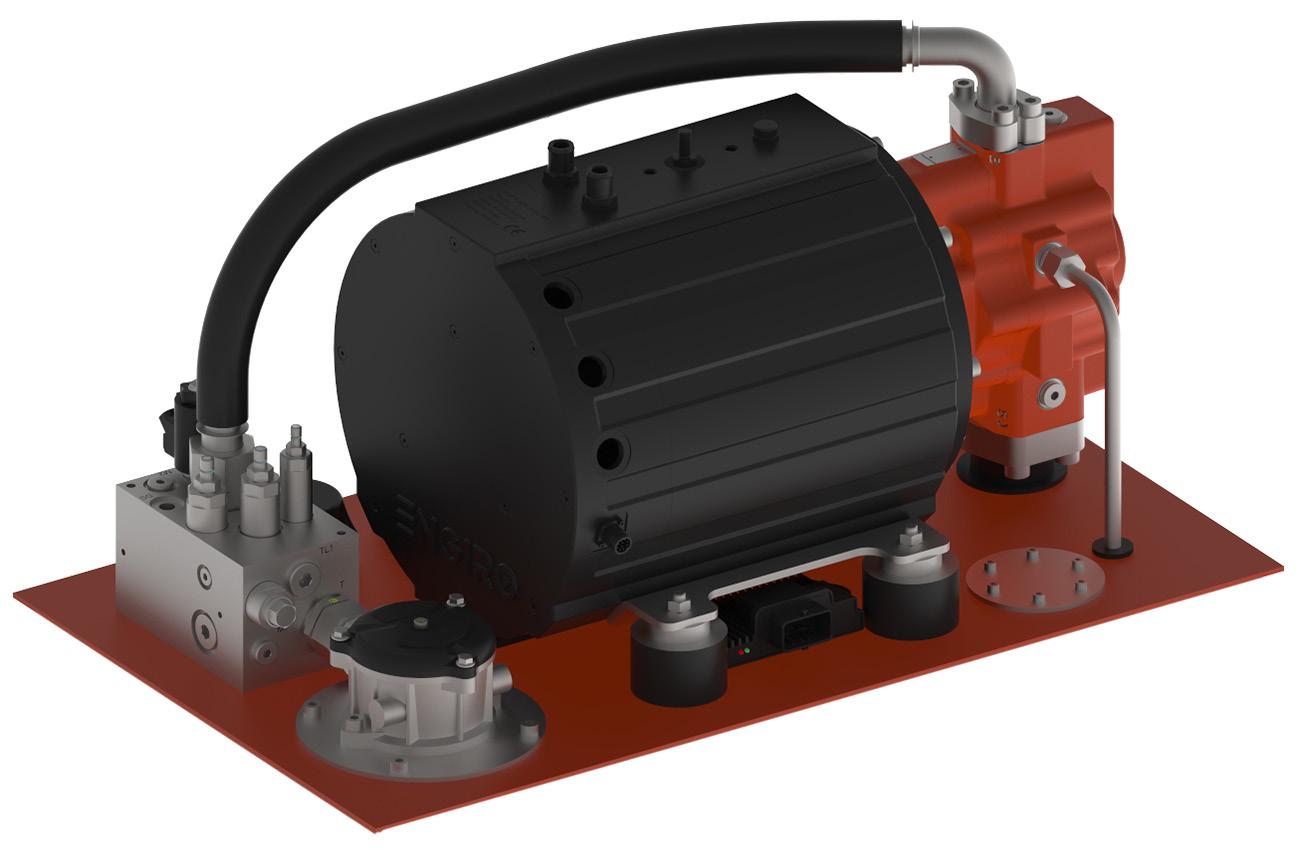
but they usually run continuously. To keep the initial cost down, less expensive pump systems with energy losses of 50% to 75% are often chosen. This is why large oil coolers are often required.
Diesel engines for trucks are optimized for driving at 80 kmh (50 mph) on the highway, where they operate efficiently at low speed and high load. Because the pump rpm is directly related to engine rpm, the engine speed must be raised to provide the high flow rate required for stationary use. This is not only noisy but inefficient, as the engine then works at an unfavorable operating point with poor combustion and high fuel consumption.
To reduce fuel consumption and thus emissions, vehicle manufacturers are removing PTOs from their future product ranges. Compressors, fans, and steering and hydraulic pumps will be driven electrically using the power-on-demand principle, with no direct connection to the engine.
Electrification of the hydraulic PTOs enables the use of power on demand exactly. Hydraulics cannot be eliminated, as it is indispensable for linear movements with high force. However, the hydraulic system must become more efficient to prevent costly energy losses.
Bucher Hydraulics developed Smart PowerPacks for utility vehicles with precisely this goal in mind. The Smart PowerPacks provide precisely the flow and pressure required and only on demand. This is the key for energy optimized operation. The Smart PowerPacks can be combined with or replace all commercially available hydraulic control systems.
Speed set point
A key component for higher performance is the AX pump. It has 24 pistons and is designed for variable-speed applications. The large number of pistons keeps pulsations very low. The wide speed range from 0 to 3,600 rpm allows for full use of the electric drive. The minimum speed limit of conventional pumps does not apply to the AX pump, which can operate from 0 with no breakaway effect. With an overall efficiency between 92% and 94%, it far exceeds the values of conventional pump solutions. The system includes a smart hydraulic block, which generates the information on the actual flow demand and integrates the pressure relief function. The system uses inverters from Bucher Hydraulics mobile drives. These calculate the speed set point internally, which keeps the installation costs low.
The Smart PowerPack is available in various sizes. In addition to the AX pump for high performance, the modular system includes external and internal gear pumps, thus covering a wide range of applications. As many body manufacturers and retrofitters do not yet have experience with such electrohydraulic drives, Bucher Hydraulics offers advice and design support.
The Smart PowerPack is configured to match the pressure and flow requirements of the application. The modular system includes various pump lines and sizes from Bucher Hydraulics, as well as the matching electric motors and inverters from Bucher Hydraulics mobile drives. Internal sensors allow the electric motor to modulate using the lowest possible pump speed to achieve the required flow and pressure.
Benefits include a reduction of fuel consumption by decoupling the PTOs, a reduction of cooling requirements, lower noise emissions, and control of battery capacity thanks to demand-based flow supply. •
New Problem
Deep Pan Forming Press Loses Operating Pressure
By Robert Sheaf, CFPAI/AJPP, CFPE, CFPS, CFPECS, CFPMT, CFPMIP, CFPMMH, CFPMIH, CFPMM, CFC Industrial Training
»A MANUFACTURER OF cooking pots and pans had a large 200-ton press in which the pressure would only go to 600 psi. They needed a minimum of 3,500 to 4,500 psi. The circuit on the right shows the basic circuit for the main ram function.
While troubleshooting, they found that the return line filters were missing their elements. The company didn’t know how long the press had run without them. They decided to drain and flush the system and install new filter elements. They confirmed that all the solenoids were shifting by manually actuating and then electrically energizing and de-energizing the coil. They also checked all the orifices shown on the drawing, and some they found that were not. The proportional valve had spool feedback that confirmed the spool did shift and return to neutral.
The system pressure would drop to 400 psi when the idle valve solenoid #7 was de-energized, compensating the pump to standby. No loud oil flow noise could be heard. The separate solenoid #6 operated control valve is used to unload the manifold mounted start-up/safety relief valve. The DCV coil #6 would energize three to four seconds after the start-up of the electric motor. (This would reduce the inrush AMP draw caused by the start-up of the electric motor.) They found that if they energized solenoid #7 and de-energized solenoid #6, there was a loud rush of oil flowing somewhere in the manifold on which the valves were mounted. Replacing the start-up/safety relief valve did not fix the issue.
What could be the problem?
SOL. 3
OPEN PRE-FILL
SOL. 6
RELIEF DCV SOL. 5
LOCK VALVE
START-UP / SAFETY RELIEF VALVE SET AT 4750 PSI SOL. 1
Solution to the July 2022 problem:
Hydraulic Motor Slows as Accumulator Discharges
Sometimes we forget that a speed control flow is determined by the pressure drop across the valve. If you increase or decrease the pressure drop without changing the valve setting, the flow will change. As the accumulator precharge drops, the pressure differential decreases, causing the flow through the valve to decrease. Changing the flow control to a pressurecompensated flow control design solved the problem and gave them constant flow.
75HP 1800 EM MAX 4500 PSI LOAD SENSE 400 PSI
80 GPM
SOL. 7
IDLE VALVE
OVERHEAD TANK
Robert Sheaf has more than 45 years troubleshooting, training, and consulting in the fluid power field. Email rjsheaf@cfc-solar.com or visit his website at www.cfcindustrialtraining.com.
DE-COMPRESSION VALVE
SOL. 4
COUNTER BALANCE
SOL. 2
Y
SLOW SPEED RETRACT
SOL. 8
H2O
SPECIAL AD SECTION
PRODUCT SPOTLIGHT
Contact us to showcase your products and services in the Product Spotlight. This special section is a high-profile area offering product-specific advertising.
Visit fluidpowerjournal.com for more information or to view our media guide.
Plastic Bodied Solenoid Valves
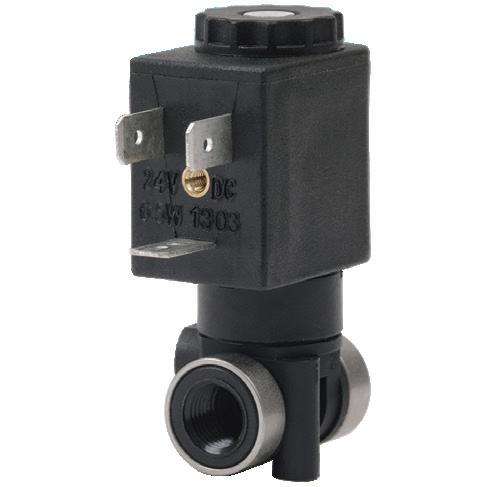
Spartan’s line of composite plastic bodied solenoid valves are used all over the world due to consistent reliability, cost-effectiveness, quick availability, and application versatility. Learn more at www.spartanscientific.com.
customerservice@spartanscientific.com 8510 Foxwood Ct, Youngstown Ohio 44514
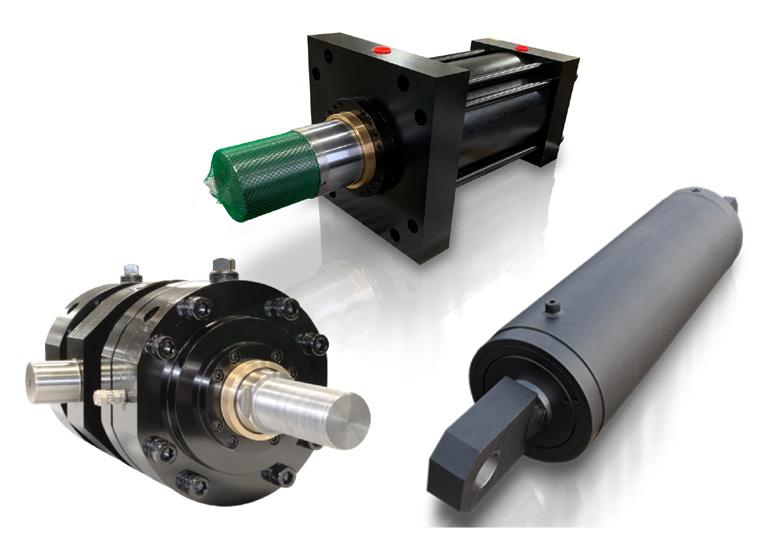
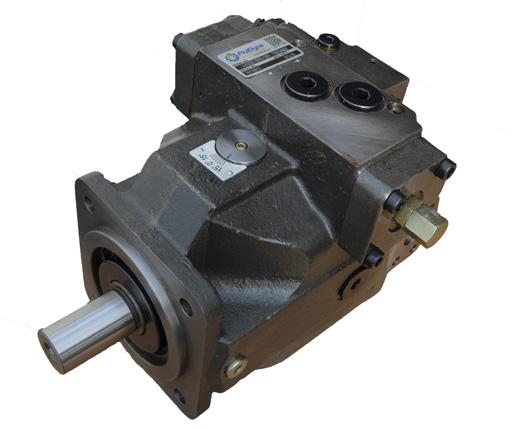
Go ahead. Push me. Ordinary heavy duty not heavy enough?
Heavy-Duty Mill Cylinders for:
• Induction-Hardened,
Chrome-Plated Rods • Heavy Wall Tubing • Replaceable Glands & Retainer Rings • High-Load Piston Design
Think indestructible and call Yates. www.yatesind.com
Yates Industries (HQ) 586.778.7680
Yates Cylinders Alabama 256.351.8081
Yates Cylinders Georgia 678.355.2240
Yates Cylinders Ohio 513.217.6777 FluiDyne Fluid Power Stocks A4V Piston Pumps & Parts
FluiDyne carries a complete line of A4V piston pumps that are available in displacement of: 40, 71, 125, 180, 250. Our units are used in many different applications: agriculture, forestry machinery, construction, on-highway, commercial vehicles, offshore, marine, wind/ocean energy, automotive and more.
Controls include: DR, DRG, FR, FRG, DFR, and LR2. They are available in SAE or metric. The versatile A4V units carry the industry leading 18 month warranty. Units are fully tested, documented and guaranteed to perform 100% to the original manufacturer’s specification.
Call, email, chat…we’re ready to help!

586.296.7200 • sales@fluidynefp.com www.fluidynefp.com
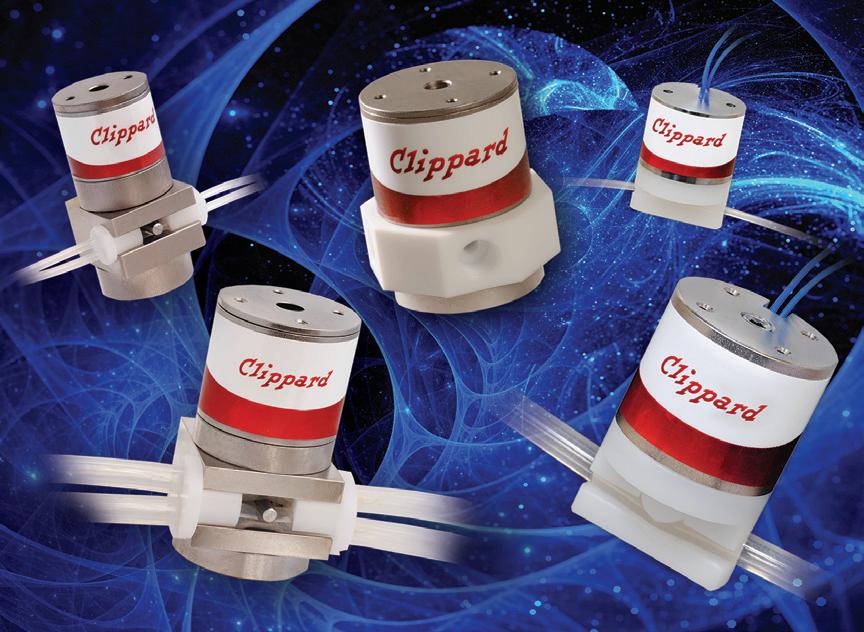
Clippard Solenoid-Operated PTFE or PEEK Media Isolation & Pinch Valves
Ideal for use with sensitive or corrosive media, this line is an excellent alternative to traditional mechanical valves when media contamination is a concern, as they interact with tubing, PTFE or PEEK, and never touch the material being dispensed! Many features include low power consumption, superior design, low dead volume, high cycle life, fast response and more. Many styles and options available. Proudly made in the USA. View more information and White Papers.
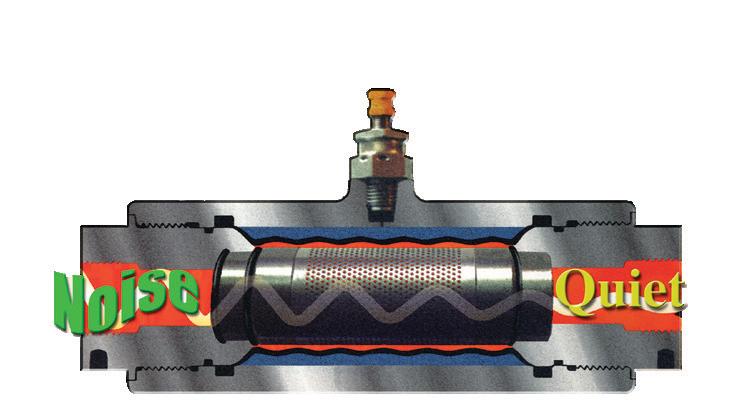
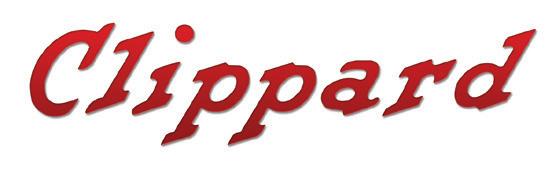
www.clippard.com New—Flat Face Design "TVF" Series Quick Disconnect
• Up to 6,000 PSI Operating Pressure—
Coupled or Uncoupled • Full 4:1 Safety Factor • Superior Flow Characteristics—Minimal
Pressure Drop • RoHS Compliant Plating • Multiple Port Options—Female NPTF,
Female SAE O-Ring, Female BSPP,
Code 61 & 62 Flange Port/Head
P.O. Box 6479 • Fort Worth, TX 76115 817.923.1965 • www.hydraulicsinc.com
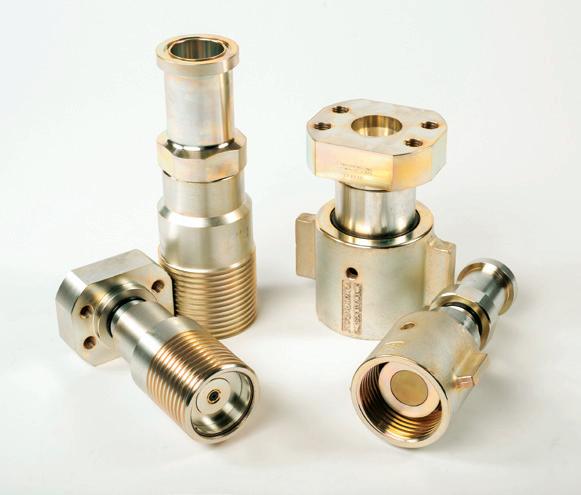
Hydraulic Noise and Shock Suppressor
Suppressor Accumulators
Wilkes and McLean manufactures an In Line Noise and Shock Suppressor for hydraulics and is a stocking distributor of Nacol Accumulators. Our suppressors eliminate pulsations, which greatly reduces noise and vibration from applications from a few gallons up to 200 gallons. We stock all of our suppressor sizes as well as Nacol Accumulators and parts from 1/5 of a pint up to 15 gallons, in our Schaumburg, Illinois facility.
877.534.6445 info@wilkesandmclean.com | www.wilkesandmclean.com
PRODUCT REVIEW
Trelleborg Launches D-Seal Design to Lower Emissions
»TRELLEBORG SEALING SOLUTIONS recently launched its enhanced double D-seal, a resilient, dual-function sealing and damping solution specifically developed to meet the needs of the automotive, truck, and transportation industry. Designed specifically for static and semidynamic powertrain applications in which vibrations can cause damage, D-seals can extend the time-to-service intervals of the engine, contributing to lower emissions through improved efficiency. Developed as an alternative to O-rings, X-rings, square-rings, and other ovalshaped seals, Trelleborg developed two main designs of the D-seal: an enhanced double D-shaped seal and an updated single D-shaped seal. The robust designs each have a customized profile that effectively absorbs vibrations and maintains strength and rigidity.
Trelleborg’s double D-shaped design includes sharper edges that ensure a tight seal fit, for example, against a cylinder lining, evenly distributing pressure to improve seal performance and eliminate the risk of leakage or cavitation damage, where water vapor bubbles form and damage metallic components.
Available in a wide choice of industry-approved materials, D-seals can be manufactured to provide specific characteristics including temperature, pressure, or media resistance, and colored to aid in identification or camera detection to support automated processes. Additional assembly coatings can also be added to D-seals to reduce assembly forces and eliminate lubrication during installation. For more information, visit www.trelleborg.com/en/seals/products-and-solutions/latest-innovations/d-seal.
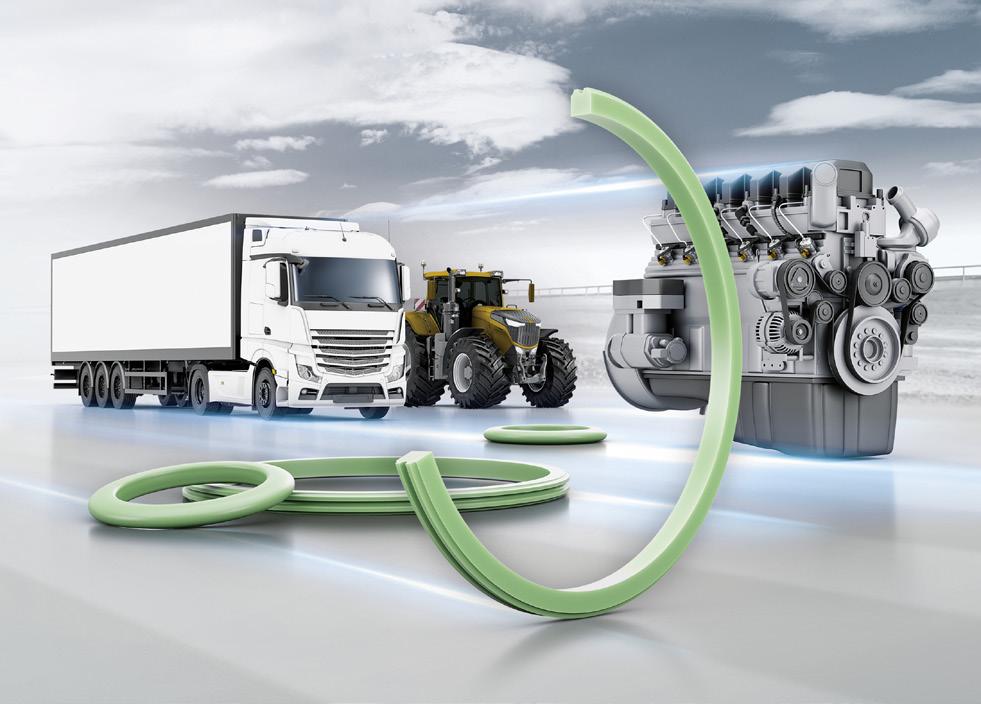