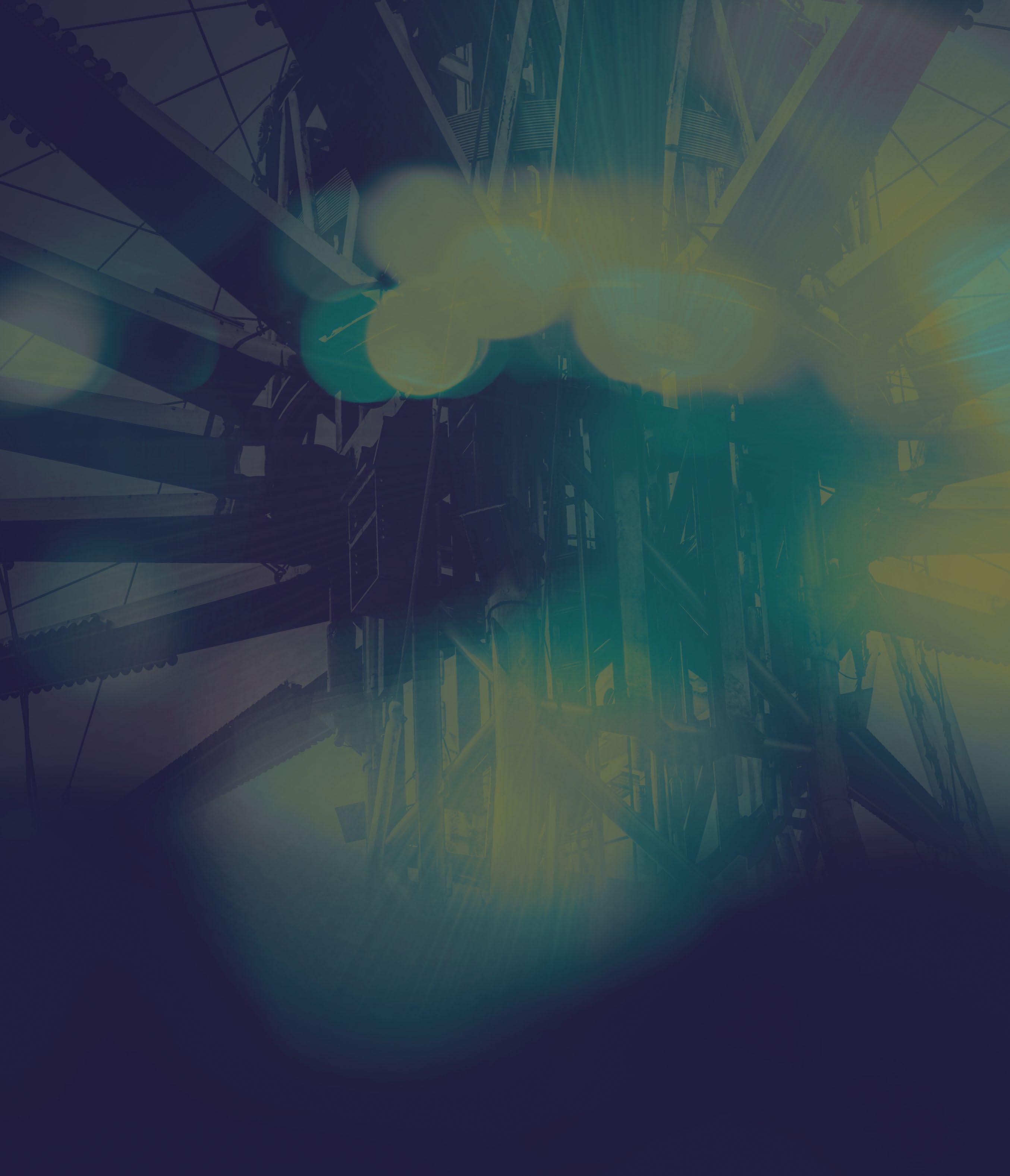
4 minute read
Stopping & Holding Loads Safely
STOPPING & HOLDING LOADS SAFELY
Whenever a cylinder accelerates, stops, or decelerates, it applies classic Newtonian laws of motion.
Considerable effort goes into designing a cylinder circuit that will accelerate a load in a specific amount of time. The same consideration should apply to safely stopping a load. Lack of planning can generate significant shock loads on the cylinder, the mechanism, or both. The compressible nature of air further complicates the deceleration once the load stops. Care must be taken that the air pressure trapped in the deceleration process is not enough to overcome friction and cause the actuator to move in the opposite direction.
Locking cylinders
When stopping a load midstroke, using pilot operated check valves or closed center directional control valves may cause a “bounce back” effect if the valve closes suddenly. The severity of the effect depends on the load inertia-to-friction and the cylinder-force ratios, and the trapped air volume. Using a valve to stop a load does not ensure holding it in place for long periods. Leakage of piston seals or valve spools can allow the cylinder to drift if an external load or force is present.
Force balance is accomplished by using a pressure-centered valve with a regulator and check in one or both of the work ports. The pressures in the cylinder ports are based on the respective piston areas and the external load being applied. This circuit holds the load, provided the load magnitude does not change.
When stopping a load, consider the allowable travel. Stopping a light load in a short distance may require a stopping force much higher than the one needed to accelerate the load.
Cylinder cushions are only useful when the machine function uses the full cylinder extension. Cushions provide more protection for the cylinder than for the load. For operations in which the cylinder does not
travel to the end of its stroke, a stopping circuit or mechanical stop may be required. The stop must be robust enough to stop the load without being damaged. Elastomeric bumpers inside the cylinder prevent metalto-metal contact of the piston and the end caps.
To safely stop a load, its kinetic energy must be dissipated in the allowable distance. This energy usually converts to heat. The decelerating device’s design must include the cycle time to ensure the heat buildup does not damage the device.
Dynamic brakes that stop a moving load differ from cylinder locks designed for static holding, which should not be used for dynamic stopping. Use static locks for an emergency stop condition, then closely inspect them for damage or wear. The load should stop before the lock is applied. If the lock activates while the cylinder is moving, it may damage the cylinder rod. Continued actuation when the rod is still moving shortens the functional life and potentially damages the rod and brake mechanism. The cylinder lock can be integrated into the housing or as an optional attachment. A cam-operated locking device that acts on the cylinder rod is usually unidirectional. It can be configured to prevent the load from extending or retracting the cylinder. A tapered-style locking mechanism prevents the load from moving in either direction. A third option uses a brake-pad style that clamps onto the rod. The recommended practice is to design the lock to have a holding force greater than the cylinder force output. Most locks are spring-applied pressure release. A separate circuit supplies the pilot to the brake mechanism at the same time the main directional valve shifts to move the cylinder.
Stop pins are intended for static holding. Cylinders can have integral stop pins that use internal porting to disengage the stop pin and require no external control. For cylinders with no integral stop pins, the common method to control a stop pin is to use a 3/2 directional valve to retract a single-acting spring-extend cylinder. If the valve is de-energized or air pressure is lost, the cylinder spring extends the stop pin into a mating hole to stop or hold the load. Lack of air pressure prevents the cylinder from retracting, even if the valve actuates. This method is preferred for holding a load and preventing it from moving, rather than stopping it midstroke.
Starting the actuator after lockup requires additional consideration. Depending on the application, pressurizing the actuator prematurely may make unlocking difficult or result in jumping when the lock releases. If the lock prevented a “fall back” condition, you may need to pressurize the actuator in the opposite direction to release the lock without dropping the load. •