
32 minute read
Cover Story
Grip on Reality
Pneumatic Tooling in Automation Robotics
By Frank Langro and Mike Guelker, Festo
As implementations of stationary and autonomous mobile robotics grows, the focus on innovations in end-of-arm tooling technology intensifies. End-of-arm tooling innovation falls into two broad areas. The first involves designing new and improved specialized tools for performing single-purpose tasks such as gluing or screwdriving. In the second, design engineers work toward solutions that expand flexibility in picking and placing, holding, and clamping. The greater the range of objects grasped by a gripper, the more a single robot can do and do efficiently.
Pneumatic- and vacuum-powered grippers are applied in numerous industries and applications due to their small-form factor and high-force capabilities as well as the lower relative cost of pneumatics compared to servo-electrics. Pneumatics and vacuum are also ideal for adaptively gripping variable shapes and delicate, easily damaged objects. Servo-electric grippers are primarily used for precision, low-force gripping and have a narrower band of applications compared to pneumatics.
In some cases, unique designs rather than force, size, and cost make pneumatics the ideal choice. In one recent customer application, a pneumatic cylinder incorporated a vacuum assist and blow-off function via a hollow through rod on the cylinder. Compressed air flowing from the through rod removed debris and protected the workpiece surface.
Demand for flexible automation
The COVID-19 pandemic has accelerated interest in flexible automation. Automation reduces worker density, lowering the risk of airborne germ transmission. Flexible automation also helps lower dependence on a labor market in which too few skilled workers are applying for open positions and serves to counteract the rising price of labor.
The development of autonomous mobile robots has moved robotics into new applications. Robots today, for example, can sanitize areas of a facility between shifts and other transition periods. The implementation of robotics for these tasks makes it possible to sanitize more often, thus protecting patients, guests, staff, and workers in hospitals, hotels, and plants. Due to the variety of tasks diverse types of grippers could be needed to accommodate different sanitizing tasks.
New materials, controls, manufacturing innovations such as 3D printing, and energy management for greater sustainability are driving innovation in robotic gripping. The ideal gripping solutions are typically lightweight and handle a variety of objects. This means that most gripping solutions no longer consist solely of heavy-duty metal parts. Today, 3D-printed and molded parts are increasingly incorporated into grippers. The speed and versatility of 3D printing allows for customized gripper fingers to handle specific objects. Companies that
can 3D print gripper fingers internally are less susceptible to supply chain disruption and better equipped to make repairs and modifications rapidly, which positively impacts uptime and productivity. A rapid prototyping capability provides companies with greater agility and can help them adapt to a rapidly changing environment.
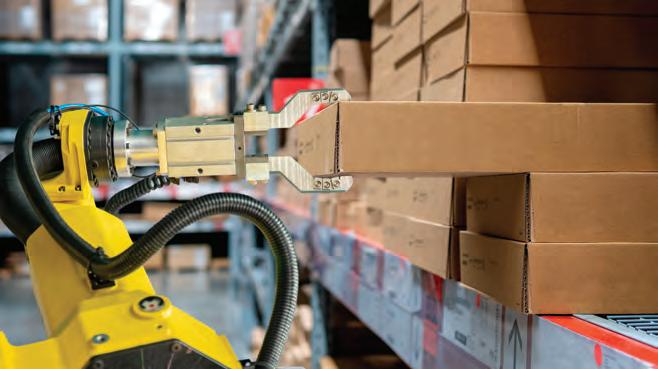
Artificial intelligence
Artificial intelligence and smart pneumatics also play a part in furthering pneumatics gripping applications. AI, smart pneumatics, and gripping are simply a natural fit. The ability to adjust and control grip force based on the attributes of the object is useful in applications in HITACHI FLANGELOCKwhich the objects being grasped can vary. As the AI system recognizes the object, with a pneumatic gripper pressure can be adjusted to apply TM Robot with parallel grippers for versatile picking and placing boxes in a warehouse.AND CAP KITS AVAILABLEthe appropriate gripping force or vacuum level to hold the part securely without causing damage.
Part numberAI and smart pneumatics are making great strides in terms of not only Part description Applicable machines Number of parts Weight (kg) adjusting force but also in the flexibility of the “grasp.” The human hand SWINGFLGLCK2062 Swing hose FlangeLockhas 27 degrees of freedom, enabling it to grasp and manipulate many TM kit EX3600, EX5600, EX8000 16 x 2062U - red FlangeLockTM 6.7 SWINGCAP2062different objects with varying force. In production environments, this Swing circuit cap kit EX3600, EX5600, EX8000 16 x 2062 - cap 4.5 level of flexibility would eliminate changeovers in tooling and prevent TRAVELFLGLCK2462 Travel hose FlangeLockTM kit EX3600, EX5600, EX8000 16 x 2462U - purple FlangeLockTM 7.7 production interruptions. In distribution centers, handlike gripping TRAVELCAP2462accelerates the adoption of robotic picking and packing. And in agri- Travel circuit cap kit EX3600, EX5600, EX8000 16 x 2462 - cap 6.4 FRONTATTFLGLCK326162culture, flexibility facilitates planting and harvesting, particularly of fruits and vegetables. Front attachment FlangeLockTM kit EX3600, EX5600, EX8000 14 x 3262U - black FlangeLockTM 4 x 3261U - black & silver FlangeLockTM 8.9
FRONTATTCAP326162 Front attachment cap kit EX3600, EX5600, EX8000Food processing and the handling of meat, poultry, and fish require 14 x 3262 - cap 4 x 3261 - cap 9.5 BOOMARCHFLGLCK3262high levels of sanitation. Soft gripping solutions made from food-safe Boom arch hose FlangeLockTM kit EX3600, EX5600, EX8000 20 x 3262U - black FlangeLockTM 9.9 materials can prevent contamination from being introduced to the food BOOMARCHCAP3262 Boom arch hose cap kit EX3600, EX5600, EX8000 20 x 3262 - cap 11.3 stream and can be easily disinfected. As soft grippers come into contact (Continued on page 14)
with these food items, they gently shape around them without harm. Pneumatics with its inherent cushioning makes this possible.
Similar soft gripping solutions for agriculture are rapidly developing successful strategies to deal with inconsistency in shape, sizes, and ripeness. Mobile robots with AI-based systems in tandem with soft gripping are learning to differentiate fruit and vegetables that are ready to pick from those that are not. Labor shortages along with the emergence of indoor and vertical farming are drivers of new robotic applications in the agricultural space, opening the door to a host of soft gripping applications.
THE ULTIMATE CONTAMINATION CONTROL TOOL

CONTAMINATION CONTROL
Routine and scheduled maintenance of hydraulic systems are vital to getting the most out of your Hitachi Mining Excavator. While maintenance plays the largest role in the prevention of unnecessary machine downtime, it can also expose the hydraulic system to high levels of contamination rapidly decreasing component longevity. The importance of contamination control is sometimes Stop the Mess overlooked when performing maintenance due to incorrect practices being used. THE FLANGELOCK™ TOOL AND CIRCUIT BLANKING CAPS The FlangeLock™ tool and caps are the ultimate contamination control tools for protecting your hydraulic system. The FlangeLock™ allows for the simple sealing of open hydraulic flanges without tools while the caps can be bolted in place of a flange connection. Easy on, easy off, they offer a leak-proof solution to hydraulic systems and environmental cleanliness. FlangeLock™ tools and caps stop the mess.
The FlangeLock™ Tool is the ultimate contamination control tool for protecting your hydraulic systems. It allows for the simple sealing of open SAE code 61, 62 HITACHI MAKING CONTAMINATION CONTROL EASY & CAT-Style hydraulic flanges without tools. Constructed from lightweight aluminum. Hitachi have packaged FlangeLock™ tool and caps specifically for Hitachi mining excavators. The Hitachi customised kits make sure no matter which component routine maintenance is being performed on, you will always have the exact Easy on, easy off. Offers a leakproof solution to hydraulic system and environmental number of FlangeLocks™* and caps to help reduce contamination. cleanliness. FlangeLock™ Tools stop the mess!*Note: FlangeLocks™ are not to be used under pressure
SAVE TIME SAVE MONEY SAVE LABOR SAVE OIL
This product is Patented, other Patents pending. • No tools required • No expensive hardware needed • No more rags stuffed into hoses • No more messy plastic caps • The ultimate contamination control tool
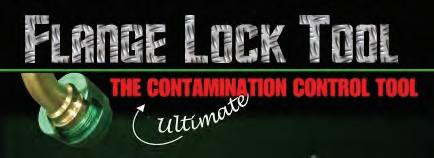
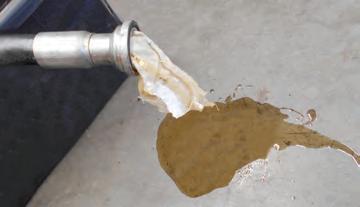
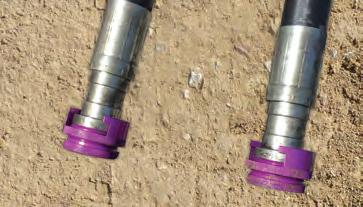
• One hand installation • Eliminate hydraulic oil spills & clean up • Quick installation & ease of usage Call you local Hitachi Muswellbrook representative or the branch on 02 6541 6300 for more information. • Safe for personnel & environment • Industry acclaimed
For more information, call (203) 861-9400 or email sales@flangelock.com. www.flangelock.com
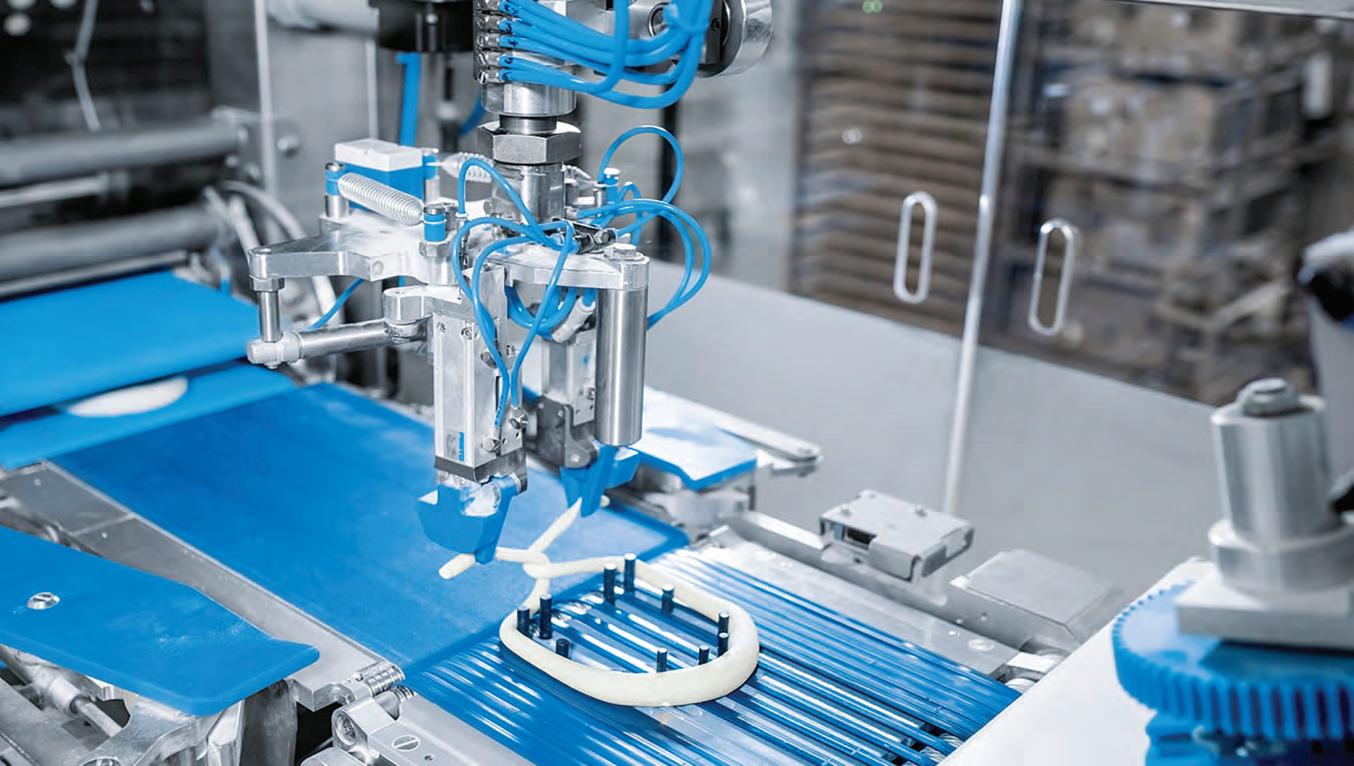
Adaptive grippers in a bakery gently grasp dough in a high-speed pretzel-making process.
(Continued from page 13)
Autonomous mobile robots
Stimulating profound change in automation is the marriage of autonomous robotic mobility with flexible gripping. In manufacturing and end-of-line packaging, work comes to the robots; the robot does not go to the work. Using autonomous mobile robots with flexible gripping, robots travel safely among humans and go to the work. This is happening in hospitals and distribution centers were people and robots safely inhabit the same environment. For these applications, innovative, compact, portable, and low energy consumption compressors are being introduced.
The most common types of industrial pneumatic robotic grippers are parallel, three-finger, angled, and vacuum. Parallel grippers, the most frequently applied, do just what their name implies: two slides either close parallel to the workpiece to grip its outside edges or open out to put pressure on inside walls.
Three-finger grippers are used to center the workpiece between the fingers, which are offset by various angles. The three fingers slide the workpiece to the gripper’s center, holding the workpiece snugly. A variation of the angled gripper is the radial gripper: The fingers open a full 180˚, which is useful where vertical space is limited. Fully open radial fingers can rest just above or below the workpiece and close when it is in position. Vacuum grippers can be as simple as a single suction cup or as complicated as a 12-x-12 matrix with different configurations of cups fed vacuum as needed to conform to various shapes and weights of the load to be grasped.
Adaptive gripping is a new class of gripper. These grippers offer flexibility in the range of objects they can grasp.
Mention adaptive grippers to anyone in manufacturing or assembly
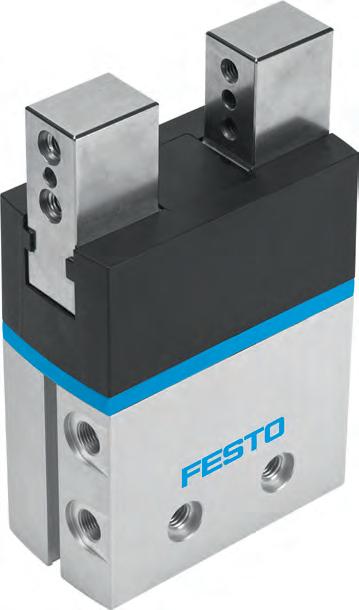
Parallel pneumatic gripper.
today and their first response will be to say adaptive grippers are being developed for collaborative robotics. They would be partially correct.
Just as important as collaborative robotics, other industries are driving development principally because the price of automation is falling, and the capabilities are rising. For example, dairy farming is a labor-intensive agricultural business with low margins and a shortage of workers. Due to technology advancements, there is a trend toward dairy farms incorporating robotic milking barns where cows learn to enter the barn to feed and, at the same time, be milked by a milking robot – all without human intervention. In the baked-goods industry, soft-adaptive grippers gently grasp breads and muffins. These flexible robotic systems can pick and pack mixed assortments to conform to each customer’s order.
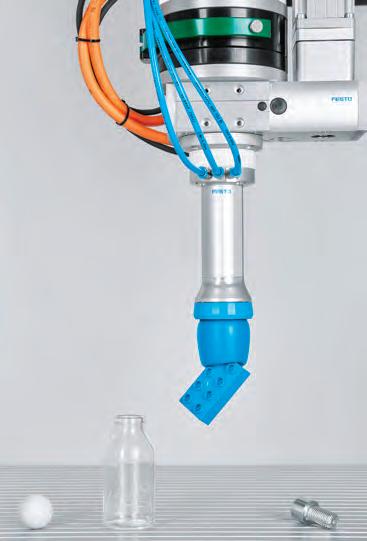
For items that are oddly shaped and not easily damaged, adaptive grippers with metal or hard plastic hinged fingers can be used for grasping. For items easily damaged, such as produce or baked goods, the pneumatic fingers are made of a flexible elastomer. Some elastomeric grippers have flexible zones and nonflexible zones. When pressurized, the flexible zones inflate and flex around the nonflexible zones, creating a nonmechanical hinge. Elastomeric fingers do not damage an item because both the elastomer and compressed air give when in contact with an object and thus offer a built-in cushioning effect. This inherent damping causes less shock during initial grasp, making these grippers ideal for baked goods, confections, fruits, and vegetables.
The continued advancement of adaptive gripping will rely in varying degrees on: • Tactile force sensors for measuring force and detecting different objects. • Flexible printed circuit board with inertial and force sensors. • Compact valve terminal with proportional piezo valves for rapidly and precisely ventilating and exhausting individual gripper fingers and swivel modules. • Inertial sensors for recording the position of the gripper fingers. • Elastic silicone skin for improving the haptics (the experience of simulated touch) and protecting the sensors. • 3D textile knitted fabric of high-strength synthetic fibers for long wear. • AI for reinforcement learning. • Vision systems for identification and location sensing.
There are drawbacks to adaptive grippers. They open and close more slowly than comparable stroke conventional grippers. Elastomeric materials wear faster than metal or hard plastic. The size and weight of objects limit what these grasping devices can manage.
The greatest area of exploration for the future of adaptive gripping will be simulating the functionality of the human hand. The reason for this is simple. The hand offers the greatest efficiency – one gripper for a wide assortment of tasks. And with sensor technology providing touch feedback there can be object manipulation, something grasping finger-based grippers cannot do.
Shorter product lifecycles, small lot sizes, and labor demographics are accelerating the need for adaptive systems. There are fluid power engineers today envisioning the possibilities and moving the industry forward. For a fluid power engineer, the opportunities for innovation in this field are endlessly gripping. •
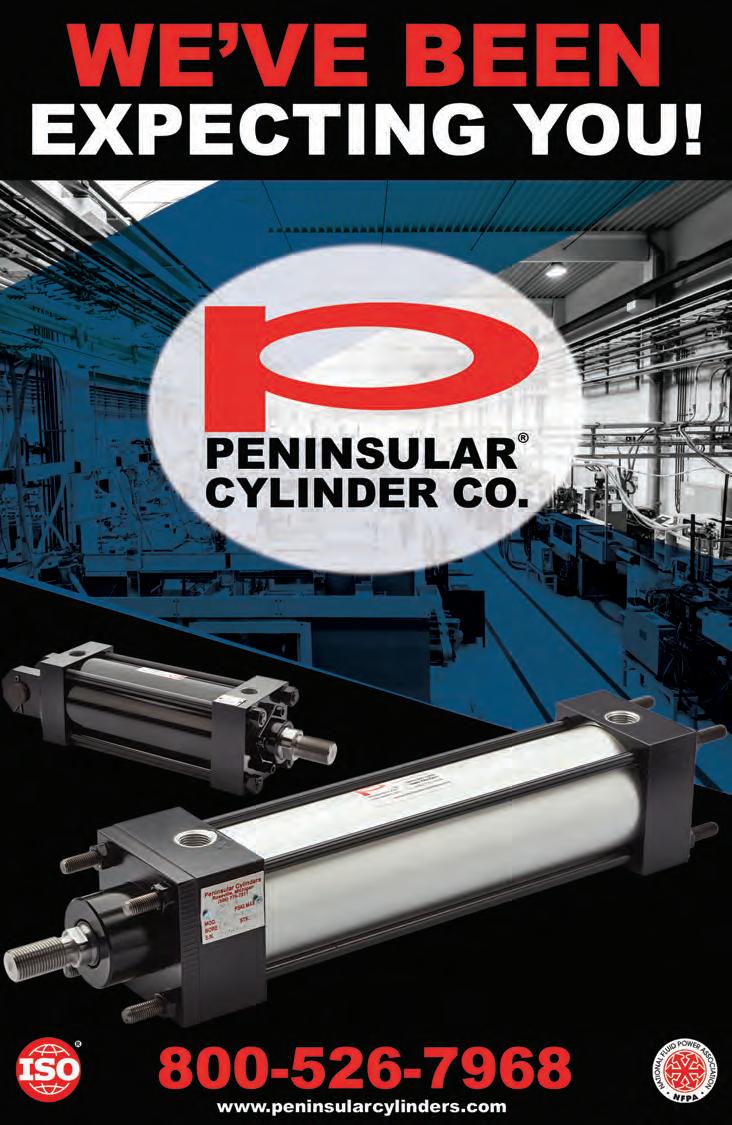
The Bionic Mobile

Assistant Prototype The SoftHand 2.0 can adapt its gripping force to a particular item.
Industrial change demands new kinds of interaction among people, machines, and data. In the future, operators and robots will interact closely together, so Festo has been working intensively on systems that can relieve people of monotonous or hazardous activities while at the same time posing no risk. Artificial intelligence plays a significant role here. The BionicMobileAssistant is a prototype of a robot system that moves independently in three dimensions and can identify objects, grip adaptively, and collaborate with humans.
The entire system, which has been developed in collaboration with ETH Zurich, has a modular design and consists of three subsystems: a mobile robot, an electric robot arm, and the BionicSoftHand 2.0. First presented by Festo in 2019, the pneumatic gripper mimics the human hand.
With its unique combination of force, dexterity, and fine motor skills, the human hand is a true miracle of nature. To enable the BionicSoftHand 2.0 to replicate the movements of the human hand, compact valve technology, sensors, electronics, and mechanical components are integrated in the tightest of spaces. The fingers and the opposable thumb are made of flexible bellows structures with air chambers surrounded by a firm yet yielding knitted fabric. This makes the hand light, adaptive, and sensitive, yet capable of exerting strong forces. The pneumatic fingers are actuated by a compact valve terminal with piezo valves mounted directly on the hand.
In order to extend the maneuverability of the thumb and index finger compared with the first version of the BionicSoftHand, the developers increased the lateral swivel range of both fingers. As a result, they now work well together and grip with great precision. Thanks to a 3D-printed wrist with two degrees of freedom, the hand can also move both back and forth as well as to the left and to the right. This means that gripping with a tight radius is also possible.
To increase the stability of the fingers, the air chambers now each contain two structural elements that function as bones. For each finger, a bending sensor with two segments determines the positions of the fingertips. The hand also wears a glove with tactile force sensors on the fingertips, the palm, and the outer sides of the robot hand. This allows it to sense the nature of the item to be held, and to adapt its gripping force to the particular item – just as people do.
In addition to the tactile sensors, the hand has a depth camera inside the wrist so it can visually detect the objects. Using it, the robot hand detects and grips a range of objects, even when they are partially covered. Once the hand has been correctly trained, it uses the collected data to assess the objects and distinguish good from bad, for example. The information is processed by a neural network that’s been trained in advance with the aid of data augmentation.
Electric arm
The BionicSoftHand 2.0 is combined with a mobile ballbot and a lightweight electric robot arm – the DynaArm. The DynaArm can carry out fast and dynamic movements thanks to its lightweight design with highly integrated drive modules that weigh just 1 kilo (2 pounds).
For the ballbot, the developers chose a sophisticated drive concept: the robot balances on a ball. This means that the BionicMobileAssistant can move freely in all directions. All the system’s energy supply is onboard: the battery for the arm and robot is located in the body; the compressed air cartridge for the pneumatic hand is installed in the upper arm. The robot is thus not only mobile but also works autonomously. The algorithms stored on the master computer also control the system’s autonomous movements. The robot orients itself independently in three dimensions using two cameras.
Hand in hand with people
The system would be perfect to directly assist people, as a service robot, as a helping hand in assembly, or to help carry out ergonomically strenuous or monotonous tasks.
It could also be used in environments where people cannot work because of hazards or restricted accessibility, such as maintenance or repair work, data measurements, or visual inspections. Imagine mobile robots carrying out simple tasks in areas of risk infection. Other future scenarios include robots bringing drinks and food to the table in restaurants or delivering medicines to hospital or nursing home patients.
Thanks to the modular concept, the BionicSoftHand 2.0 can be quickly mounted on other robot arms and is easy to commission. Combined with Festo’s BionicCobot or BionicSoftArm, the gripper can, for example, form a completely pneumatic robot system that works hand in hand with people. •
Growth in Fluid Power Shipments Continues
Data from the National Fluid Power Association shows that pneumatic and hydraulic shipments continue to grow. Year to date, shipments grew 18.6% in October 2021. Raw index data shows industrial hydraulic and pneumatic shipments for October 2021 down slightly down from September, while mobile hydraulic shipments were slightly higher. The data was collected from more than 80 fluid power manufacturers in NFPA’s Confidential Shipment Statistics (CSS) program.
Hydraulic and Pneumatic Shipments
Raw Index Data, Index: 2018=100
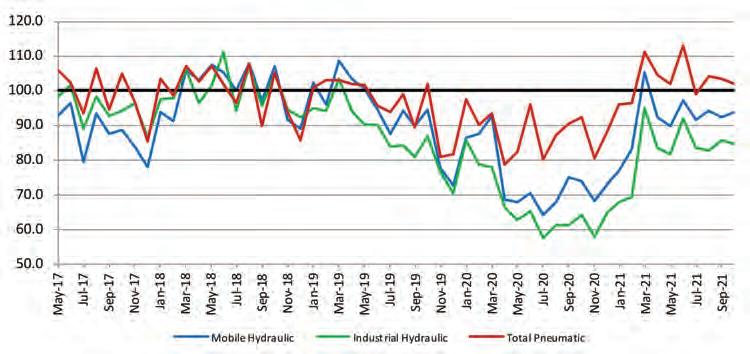
This graph of raw index data is generated by the total dollar volume reported to NFPA by CSS participants and compared to the average monthly dollar volume in 2018. For example, the October 2021 total dollar volume for pneumatic shipments is 102.1% of the average monthly dollar volume in 2018. (Base Year 2018 = 100)
SHIPMENTS
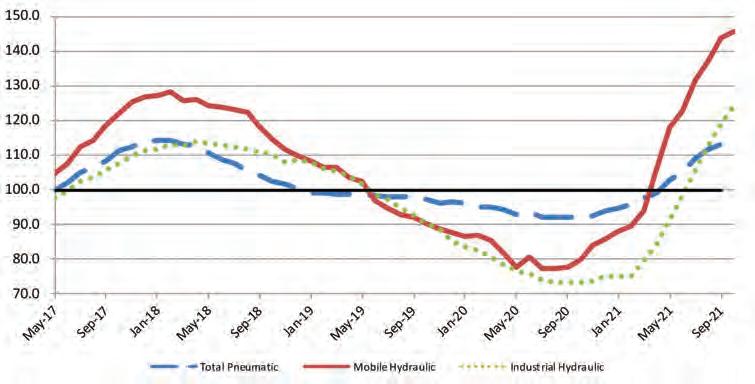
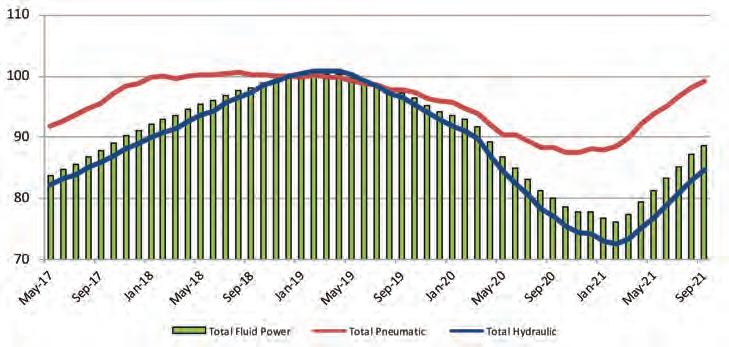
MONTH TOTAL FLUID POWER TOTAL HYD. TOTAL PNEU.
Aug. 2021 17.7 17.7 17.1
Sept. 2021 18.5 18.7 16.8
Oct. 2021* 18.6 19.3 16.1
*Preliminary data subject to revision.
Shipments – Cumulative year‐to‐date % change (2021 vs. 2020)
The table above is expressed in terms of cumulative percent changes. These changes refer to the percent difference between the relevant cumulative total for 2021 and the total for the same months in 2020. For example, October 2021 pneumatic shipments figure of 16.1 means that for the calendar year through October 2021, pneumatic shipments increased 16.1% compared to the same time-period in 2020.
Pneumatic, Mobile and Industrial Hydraulic Orders 12/12 Ratio
Each point on this graph represents the most recent 12 months of orders compared to the previous 12 months of orders. Each point can be read as a percentage. For example, 124.3 (the October 2021 level of the industrial hydraulic series) indicates that industrial hydraulic orders received from November 2020 to October 2021 were 124.3% of the orders received from November 2019 to October 2020. (Base Year 2018 = 100)
This graph of 12-month moving averages shows that in October 2021, the moving average for shipments increased across the board. (Base Year 2018 = 100)
Total ‐ Hydraulic and Pneumatic Shipments 12 Month Moving Average
Registration Open for IFPS Spring Meeting
»THE INTERNATIONAL FLUID Power Society's spring meeting is scheduled for March 7-10 in Charleston, South Carolina.
In addition to meetings with IFPS committees, attendees can take local tours. A technical workshop titled Proportional Directional Control Valves for Mobile Hydraulic Applications takes place March 7.
At the meeting, attendees meet with a fun and dedicated group of professionals who exchange ideas and discuss ways to improve and educate the fluid power workforce. IFPS members who can’t attend in person can join individual committee meetings virtually.
To register, visit www.ifps.org or contact scoleman@ifps.org.
SCHEDULE OF EVENTS
Monday, March 7
8:00 AM. - 2:00 PM............................................................................................Technical Workshop 2:30 PM. - 5:00 PM.......................................................... Board Orientation (board members only) 6:00 PM - 9:00 PM.............................................. Board of Directors Dinner (board members only)
Tuesday, March 8
8:00 AM - 9:00 AM..............................................................Strategic Planning Committee Meeting 9:00 AM - 11:00 AM. ........................................................................Education Committee Meeting 11:00 AM - 12:00 PM .................................................................. Membership Committee Meeting 12:00 PM - 12:45 PM. ................................................................................................. Hosted Lunch 12:45 PM - 1:30 PM........................................................Membership Committee Meeting (cont'd) 1:45 PM - 5:30 PM.............................................................................................Fort Sumter Tour ($) 6:30 PM - 8:00 PM............................................................................................. Welcome Reception 8:00 PM - 10:00 PM.........................................................................................Star's Rooftop Bar ($)
Wednesday, March 9
8:00 AM - 12:00 PM. ....................................................................Certification Committee Meeting 12:00 PM - 12:45 PM ....................................................................................... Lunch (on your own) 1:00 PM - 4:00 PM.................................................................................................. Carriage Tour ($) 6:00 PM - 9:30 PM....................................................................................................Dinner & Games
Thursday, March 10
8 AM - 10:30 AM...............................................................................Marketing Committee Meeting 10:30 AM - 12:00 PM. ......................................................................... Finance Committee Meeting 12:00 PM - 12:45 PM. .................................................................................................. Hosted lunch 12:45 PM - 2:30 PM................................................................................Board of Directors Meeting 2:30 PM - 3:30 PM............................................................ Strategic Planning Committee follow up
CELEBRATING 60 YEARS

Hall of Fame Nominations Open
»NOMINATIONS FOR THE Fluid Power
Hall of Fame are now being accepted and remain open until April 15.
A panel of judges reviews the applications and announces the inductees on Fluid Power Professionals Day, June 19. Inductees will be honored at an awards dinner during the International Fluid Power Association’s fall meeting in October in San Diego.
Anyone can nominate a living or deceased professional who has 25 or more years’ experience in the fluid power industry. Living nominees will be contacted and asked to complete an application.
The Fluid Power Hall of Fame was established to acknowledge individuals who have made significant contributions to the fluid power industry. To make a nomination, visit www.fluidpowerhalloffame.org.
IFPS Welcomes New Board Members
»IFPS ELECTED TWO new directors-at-large to the board of directors at the fall meeting in October. The members take office this month. Stephen Blazer, PE, CFPE, CFPS, CFPMHM/MHT, is manager of prevention and product safety at Altec Industries. Blazer earned a bachelor’s in mechanical engineering from Kansas State University in 1986 and began his career at Boeing Aircraft Company in Wichita, Kansas. In 1988 he joined Altec, where he’s worked in many different roles and with a variety of groups. In his spare time, he operates a small family farm producing corn and soybeans, along with specialty crops of Aronia berries, chestnuts, and papaws. He also tends a dozen beehives for honey production and enjoys hunting, fishing, flying, and restoring antique airplanes and classic muscle cars, including a 1965 Ford Mustang. He is married and has three wonderful children.
Ethan Stuart, CFPS, CFPECS, is an application specialist at Wainbee Limited. Stuart earned a bachelor’s in applied science from the University of British Columbia and has worked at Wainbee for nine years, designing custom fluid power systems. He is engaged to be married.

»IFPS HAS REVAMPED Hydraulic Specialist online training modules, which are helpful when preparing for the HS certification test or just to boost skills. Members have access for one year so they can learn at their own pace. Enhanced features of the modules include: • a voice explanation for each circuit • three sets of additional pretest questions not included in the print HS study manual • interactive quizzes at the end of each section • reworded complex topics for easier comprehension with additional examples and enhanced graphics • streamlined equation formulas and text describing how to compute complex formulas • “bar” added to equations involving pressure units To order, visit ifps.org/hydraulic-interactive.
IFPS Announces VFD Webinar
»IFPS WILL HOST a web seminar titled
Variable Frequency Drives in Hydraulic Applications on Jan. 20 from 12 p.m. to 1 p.m. Eastern.
Presented by Alan Froslie, CFPAI, of Airline Hydraulics, the webinar introduces the function and considerations of a VFD for a hydraulic system, providing insight into the potential benefits and possible drawbacks to this technology. From electric motor and VFD basics to an examination of two applications, the webinar presents knowledge to determine when a VFD works for an application. Register at www.ifps.org/web-seminars.
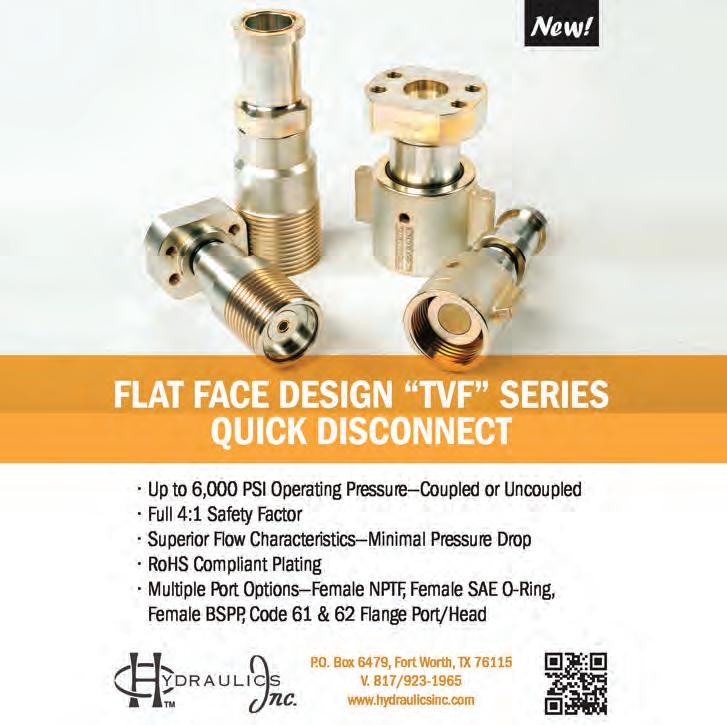
Don’t compromise!
Use MAIN Manufacturing Products, Inc. as your source for hydraulic flanges
Dependable - 60 yrs service Informed - members of SAE, ISO, & NFPA tech committees
Quick - Thousands in stock specials can be 3-4 days
Made in USA
SAE J518, JIS, DIN, ISO, standard & special adapters Socket & Butt weld, NPTF, BSPT, ORB, BSPP, 6149, ETC. In-line, el, tee, F, blind, cross, cross, flanged, reducing, flange heads, couplings
Materials: Carbon, 304L, 316L, Duplex, Cu-NI, Ductile, Aluminum, etc.
Grand Blanc, MI USA
IFPS Fall Meeting Highlights
CELEBRATING 60 YEARS
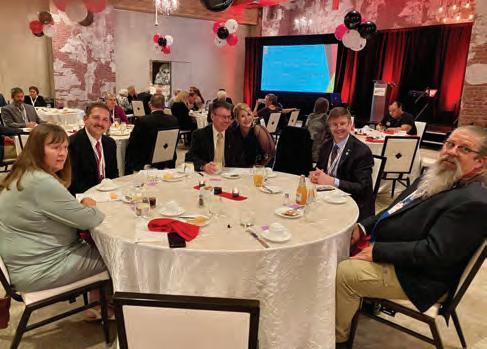
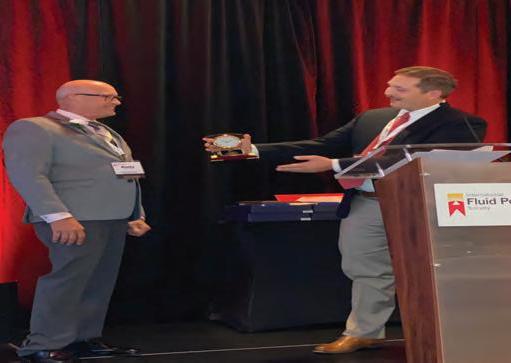
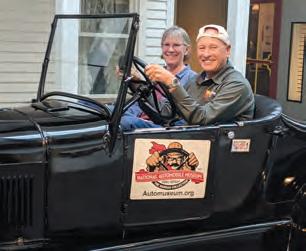
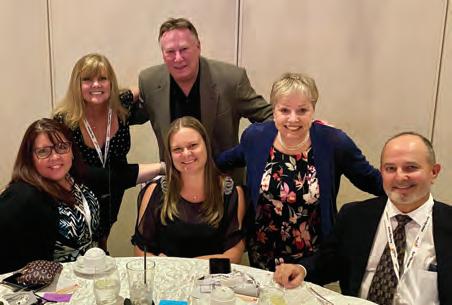
First Vice President Scott Sardina presents a clock in appreciation to outgoing Board President Rocky Phoenix.
From left: Melinda Sardina, Scott Sardina, Alan Froslie, Donna Pollander, Brian Wheeler, and Jeff Hodges. From left: Jim O’Halek, Tom Blansett, Paul Prass, Mohaned Shahin, Chauntelle Baughman, and Mark Baughman.
Rocky and Susan Phoenix at the National Automobile Museum.
Seated, from left: Lisa DeBenedetto, Elizabeth Fontecchio, and David Fontecchio. Standing, from left: Barb DeCesare, David Bates, and Jane Bates.
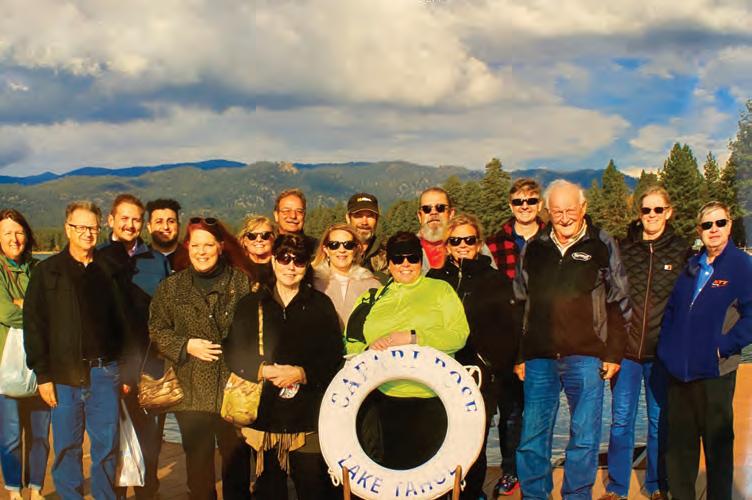
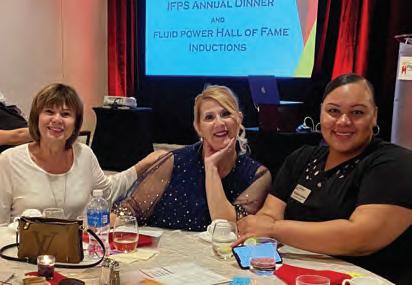
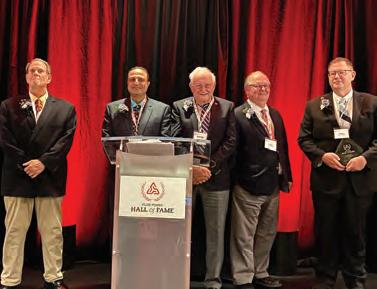
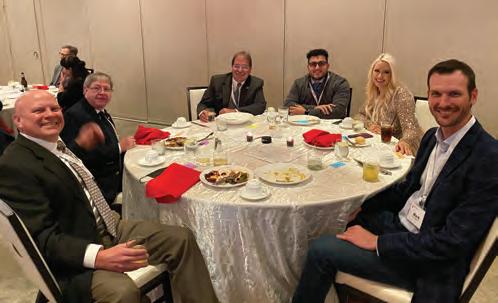
Hall of Fame inductees from left: Craig Fox, Medhat Khalil, George Beniek, Alan Hitchcox, and Peter Nachtwey. From left: Adele Kayser, Donna Pollander, and Stephanie Coleman.
Newly Certified Professionals
September 2021
SPECIALIST
(holds HS & PS certifications)
Matthias Honermeier Matt Savage
Artin Tosounian, SMC Corporation of America
HYDRAULIC SPECIALIST Seth Brokaw Matt Savage
Derrick Bohl, JWF Technologies Travis Barthalow, Manitowoc Crane Group Alfin Leo, Parker Hannifin Eric Amato, Radial Dynamics Nicholas Virostko, The Lubrizol Corporation
PNEUAMTIC SPECIALIST Matthias Honermeier
Artin Tosounian, SMC Corporation of America Jon Murray, Cross Company
CONNECTOR & CONDUCTOR
Matthew Winkleman, Controlled Fluids Gary Loving, Controlled Fluids Ronald Granger, Controlled Fluids Rocky Burks, Controlled Fluids Karl Haynes, Controlled Fluids Noe Hernandez, Controlled Fluids Daniel Nunley, Open Loop Energy Micheal Ballantyne, The Boeing Company Jordan Mazi, The Boeing Company
INDUSRIAL HYDRAULIC MECHANIC
Paul Wiggert, Paragon Technologies
MOBILE HYDRAULIC MECHANIC
Kevin Costlow, AEP Jonothan Dahlke, Alliant Energy Kenny Meisgeier, Alliant Energy Ed Schultz, Alliant Energy Corey Smith, Alliant Energy Bryce Burgett, Altec Industries Garrett Conrad, Altec Industries Carlos Contreras, Altec Industries Brandon Melvin, Altec Industries Duane Predmore, Altec Industries Isaac Salcido, Altec Industries Jason Jones, City of Tacoma Jeremy Anderson, City of Tacoma Caleb Curtiss, Clark Public Utilities Dustin Flanagan, Duke Energy Levi Gordon, Duke Energy Jason Johnson, Duke Energy William Loomis, Duke Energy Daniel Lydon, Duke Energy Randall Mann, Duke Energy Matthew Mckay, Duke Energy Nicholas Molenda, Eugene Water and Electric Board Zachary Sligar, Grant County PUD Craig Wood, Grant County PUD Justin Dalton, Idaho Power David Jackson, Idaho Power Zac Lucas, Idaho Power Jack Rupe Jr., Rupe’s Hydraulics Wayne Collins, Rupe’s Hydraulics Eduardo Flores, Rupe's Hydraulics Paul Montgomery, Rupe's Hydraulics
PNEUMATIC TECHNICIAN
James O'Halek, The Boeing Company October 2021
CONNECTOR & CONDUCTOR
Michael Vallon, Pirtek Jason Wood, Pirtek Daniel Coats, The Boeing Company Dustin Henning, The Boeing Company Michael Howard, The Boeing Company John Ildefonso, The Boeing Company Harold Wilson, The Boeing Company
SPECIALIST
(holds HS & PS Certifications) Alex Adams, Womack
HYDRAULIC SPECIALIST
Caleb Peterson, CNH Industrial Chad Wood, Genesis Attachments
PNEUMATIC SPECIALIST
Alex Adams, Womack
MOBILE HYDRAULIC MECHANIC
Michael Dill, Alabama Power Justen Hutto, Alabama Power Donovan Lewis, Alabama Power Russell Elfast, Altec Industries Edwin Rivera, Altec Industries Holden Shillingstad, Altec Industries Paul Benedetto, Benedetto Nursery Raul Aldape, Duke Energy Jon Blomberg, Duke Energy Sean Pickard, Duke Energy Brandon Pogue, Duke Energy Zachary Richardson, Duke Energy
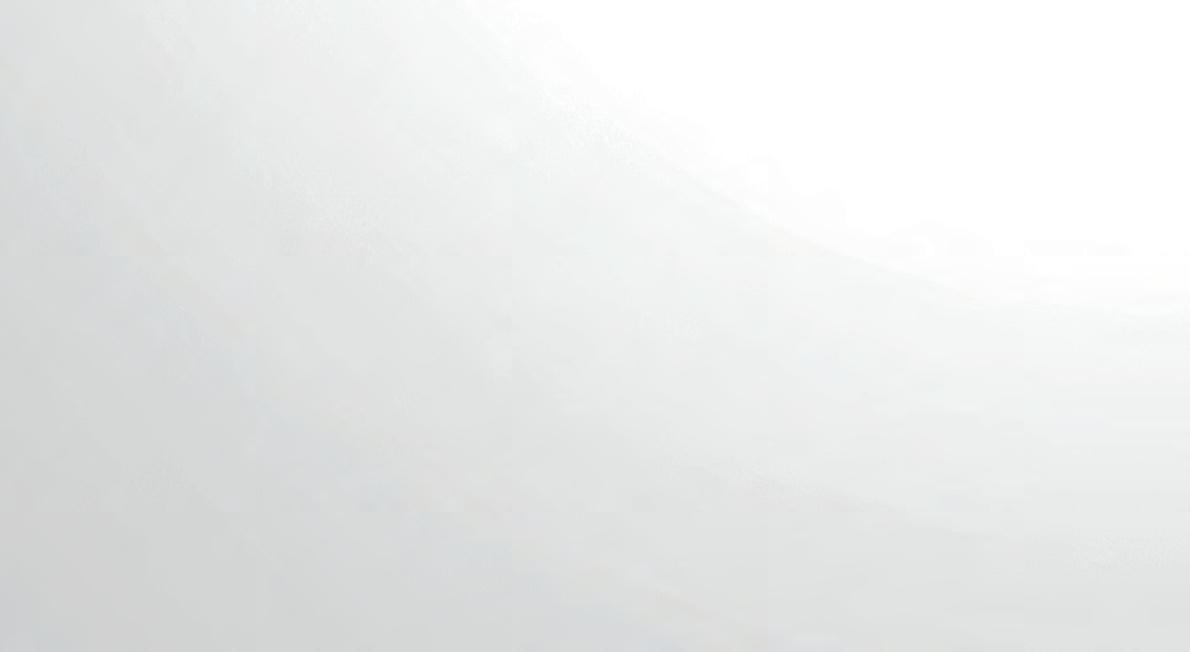
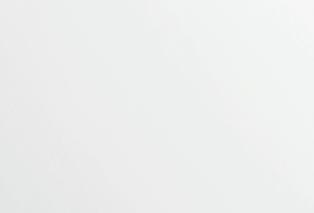
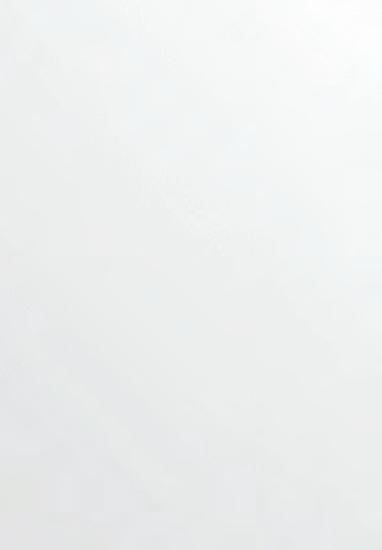
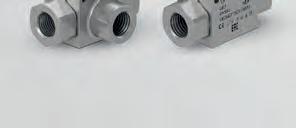


CFPAI
Certified Fluid Power Accredited Instructor
CFPAJPP
Certified Fluid Power Authorized Job Performance Proctor
CFPAJPPCC
Certified Fluid Power Authorized Job Performance Proctor Connector & Conductor
CFPE
Certified Fluid Power Engineer
CFPS
Certified Fluid Power Specialist (Must Obtain CFPHS & CFPPS)
CFPHS
Certified Fluid Power Hydraulic Specialist
CFPPS
Certified Fluid Power Pneumatic Specialist
CFPECS
Certified Fluid Power Electronic Controls Specialist
CFPMT
Certified Fluid Power Master Technician (Must Obtain CFPIHT, CFPMHT, & CFPPT)
CFPIHT
Certified Fluid Power Industrial Hydraulic Technician
CFPMHT
Certified Fluid Power Mobile Hydraulic Technician
CFPPT
Certified Fluid Power Pneumatic Technician
CFPMM
Certified Fluid Power Master Mechanic (Must Obtain CFPIHM, CFPMHM, & CFPPM)
CFPIHM
Certified Fluid Power Industrial Hydraulic Mechanic
CFPMHM
Certified Fluid Power Mobile Hydraulic Mechanic
CFPPM
Certified Fluid Power Pneumatic Mechanic
CFPMIH
Certified Fluid Power Master of Industrial Hydraulics (Must Obtain CFPIHM, CFPIHT, & CFPCC)
CFPMMH
Certified Fluid Power Master of Mobile Hydraulics (Must Obtain CFPMHM, CFPMHT, & CFPCC)
CFPMIP
Certified Fluid Power Master of Industrial Pneumatics (Must Obtain CFPPM, CFPPT, & CFPCC)
CFPCC
Certified Fluid Power Connector & Conductor
CFPSD
Fluid Power System Designer CFPMEC (In Development) Mobile Electronic Controls
CFPIEC (In Development) Industrial Electronic Controls
Tentative Certification Review Training
IFPS offers onsite review training for small groups of at least 10 persons. An IFPS accredited instructor visits your company to conduct the review. Contact kpollander@ifps.org for details of the scheduled onsite reviews listed below.
HYDRAULIC SPECIALIST
Feb. 7-10, Fairfield, OH. Contact info@cfcindustrialtraining.com. Written test Feb. 10. March 14-17, Mukwonago, WI, offered through Milwaukee School of Engineering. Written test March 17. Aug. 29-Sept. 1, Fairfield, OH. Contact info@cfcindustrialtraining.com. Written test Sept. 1.
ELECTRONIC CONTROLS
March 21-24, Fairfield, OH. Contact info@cfcindustrialtraining.com. Written test, March 24.
PNEUMATIC SPECIALIST
June 13-16, Fairfield, OH. Contact info@cfcindustrialtraining.com. Written test June 16.
CONNECTOR & CONDUCTOR
May 24-25, Fairfield, OH. Contact info@cfcindustrialtraining.com. Written test May 26. Nov. 15-16, Fairfield, OH. Contact info@cfcindustrialtraining.com. Written test Nov. 17.
MOBILE HYDRAULIC MECHANIC
April 19-21, Fairfield, OH. Contact info@cfcindustrialtraining.com. Written and JP test April 22. Oct. 10-12, Fairfield, OH. Contact info@cfcindustrialtraining.com. Written and JP test Oct. 13. Online review for written test. Contact info@cfcindustrialtraining.com. IFPS members can email askus@IFPS.org for a 20% off coupon code. Test fees not included.
INDUSTRIAL HYDRAULIC MECHANIC
July 18-20, Fairfield, OH. Contact info@cfcindustrialtraining.com. Written and JP test July 21.
INDUSTRIAL HYDRAULIC TECHNICIAN
Onsite review training for small groups. Contact IFPS for details.
MOBILE HYDRAULIC TECHNICIAN
For dates, call 513-874-3225 or contact info@cfcindustrialtraining.com.
PNEUMATIC TECHNICIAN and PNEUMATIC MECHANIC
For dates, call 513-874-3225 or contact info@cfcindustrialtraining.com.
JOB PERFORMANCE TRAINING
Online review. Contact info@cfcindustrialtraining.com. Reviews includes stations 1-6 of the IFPS mechanic and technician job performance tests. Members can email askus@IFPS.org for a 20% coupon code. Test fees not included. To register, contact info@cfcindustrialtraining.com.
LIVE DISTANCE LEARNING JOB PERFORMANCE STATION REVIEW
Contact info@cfcindustrialtraining.com for information.
Certification Testing Locations
Individuals wishing to take any IFPS written certification tests can select from convenient locations across the United States and Canada. IFPS is able to offer these locations through its affiliation with the Consortium of College Testing Centers provided by National College Testing Association.
Contact headquarters if you do not see a location near you. Every effort will be made to accommodate your needs.
If your test was postponed due to the pandemic, please contact headquarters so that we may reschedule.
TENTATIVE TESTING DATES FOR ALL LOCATIONS:
February 2022
Tuesday 2/8 • Thursday 2/24
March 2022
Tuesday 3/8 • Thursday 3/24
April 2022
Tuesday 4/5 • Thursday 4/21
May 2022
Tuesday 5/3 • Thursday 5/19
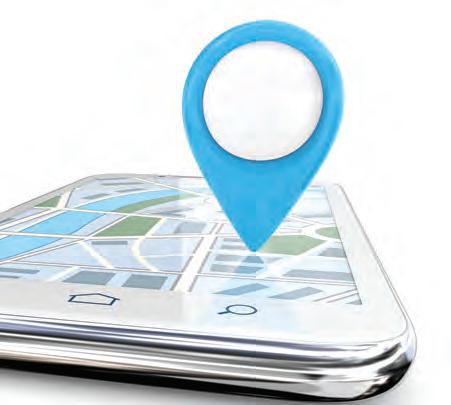
ALABAMA
Auburn, AL Birmingham, AL Calera, AL Decatur, AL Huntsville, AL Jacksonville, AL Mobile, AL Montgomery, AL Normal, AL Tuscaloosa, AL
ALASKA
Anchorage, AK Fairbanks, AK
ARIZONA
Flagstaff, AZ Glendale, AZ Mesa, AZ Phoenix, AZ Prescott, AZ Scottsdale, AZ Sierra Vista, AZ Tempe, AZ Thatcher, AZ Tucson, AZ Yuma, AZ
ARKANSAS Bentonville, AR Hot Springs, AR Little Rock, AR
CALIFORNIA
Aptos, CA Arcata, CA Bakersfield, CA Dixon, CA Encinitas, CA Fresno, CA Irvine, CA Marysville, CA Riverside, CA Salinas, CA San Diego, CA San Jose, CA San Luis Obispo, CA Santa Ana, CA Santa Maria, CA Santa Rosa, CA Tustin, CA Yucaipa, CA
COLORADO
Aurora, CO Boulder, CO Springs, CO Denver, CO Durango, CO Ft. Collins, CO Greeley, CO Lakewood, CO Littleton, CO Pueblo, CO
DELAWARE
Dover, DE Georgetown, DE Newark, DE
FLORIDA
Avon Park, FL Boca Raton, FL Cocoa, FL Davie, FL Daytona Beach, FL Fort Pierce, FL Ft. Myers, FL Gainesville, FL Jacksonville, FL Miami Gardens, FL Milton, FL New Port Richey, FL Ocala, FL Orlando, FL Panama City, FL Pembroke Pines, FL Pensacola, FL Plant City, FL Riviera Beach, FL Sanford, FL Tallahassee, FL Tampa, FL West Palm Beach, FL Wildwood, FL Winter Haven, FL
GEORGIA
Albany, GA Athens, GA Atlanta, GA Carrollton, GA Columbus, GA Dahlonega, GA Dublin, GA Dunwoody, GA Forest Park, GA Lawrenceville, GA Morrow, GA Oakwood, GA Savannah, GA Statesboro, GA Tifton, GA Valdosta, GA
HAWAII Laie, HI
IDAHO
Boise, ID Coeur d ‘Alene, ID Idaho Falls, ID Lewiston, ID Moscow, ID Nampa, ID Rexburg, ID Twin Falls, ID
ILLINOIS
Carbondale, IL Carterville, IL Champaign, IL Decatur, IL Edwardsville, IL Glen Ellyn, IL Joliet, IL Malta, IL Normal, IL Peoria, IL Schaumburg, IL Springfield, IL University Park, IL
INDIANA
Bloomington, IN Columbus, IN Evansville, IN Fort Wayne, IN Gary, IN Indianapolis, IN Kokomo, IN Lafayette, IN Lawrenceburg, IN Madison, IN Muncie, IN New Albany, IN Richmond, IN Sellersburg, IN South Bend, IN Terre Haute, IN
IOWA
Ames, IA Cedar Rapids, IA Iowa City, IA Ottumwa, IA Sioux City, IA Waterloo, IA
KANSAS
Kansas City, KS Lawrence, KS Manhattan, KS Wichita, KS
KENTUCKY
Ashland, KY Bowling Green, KY Erlanger, KY Highland Heights, KY Louisville, KY Morehead, KY
LOUISIANA
Bossier City, LA Lafayette, LA Monroe, LA Natchitoches, LA New Orleans, LA Shreveport, LA Thibodaux, LA
MARYLAND
Arnold, MD Bel Air, MD College Park, MD Frederick, MD Hagerstown, MD La Plata, MD Westminster, MD Woodlawn, MD Wye Mills, MD
MASSACHUSETTS
Boston, MA Bridgewater, MA Danvers, MA Haverhill, MA Holyoke, MA Shrewsbury, MA
MICHIGAN
Ann Arbor, MI Big Rapids, MI Chesterfield, MI Dearborn, MI Dowagiac, MI East Lansing, MI Flint, MI Grand Rapids, MI Kalamazoo, MI Lansing, MI Livonia, MI Mount Pleasant, MI Sault Ste. Marie, M Troy, MI University Center, MI Warren, MI
MINNESOTA
Alexandria, MN Brooklyn Park, MN Duluth, MN Eden Prairie, MN Granite Falls, MN Mankato, MN
MISSISSIPPI
Goodman, MS Jackson, MS Mississippi State, MS Raymond, MS University, MS
MISSOURI
Berkley, MO Cape Girardeau, MO Columbia, MO Cottleville, MO Joplin, MO Kansas City, MO Kirksville, MO Park Hills, MO Poplar Bluff, MO Rolla, MO Sedalia, MO Springfield, MO St. Joseph, MO St. Louis, MO Warrensburg, MO
MONTANA
Bozeman, MT Missoula, MT
NEBRASKA
Lincoln, NE North Platte, NE Omaha, NE
NEVADA
Henderson, NV Las Vegas, NV North Las Vegas, NV Winnemucca, NV
NEW JERSEY
Branchburg, NJ Cherry Hill, NJ Lincroft, NJ Sewell, NJ Toms River, NJ West Windsor, NJ
NEW MEXICO
Albuquerque, NM Clovis, NM Farmington, NM Portales, NM Santa Fe, NM
NEW YORK
Alfred, NY Brooklyn, NY Buffalo, NY Garden City, NY New York, NY Rochester, NY Syracuse, NY
NORTH CAROLINA
Apex, NC Asheville, NC Boone, NC Charlotte, NC China Grove, NC Durham, NC Fayetteville, NC Greenville, NC Jamestown, NC Misenheimer, NC Mount Airy, NC Pembroke, NC Raleigh, NC Wilmington, NC
NORTH DAKOTA
Bismarck, ND
OHIO
Akron, OH Cincinnati, OH Cleveland, OH Columbus, OH Fairfield, OH Findlay, OH Kirtland, OH Lima, OH Maumee, OH Newark, OH North Royalton, OH Rio Grande, OH Toledo, OH Warren, OH Youngstown, OH
OKLAHOMA
Altus, OK Bethany, OK Edmond, OK Norman, OK Oklahoma City, OK Tonkawa, OK Tulsa, OK
OREGON
Bend, OR Coos Bay, OR Eugene, OR Gresham, OR Klamath Falls, OR Medford, OR Oregon City, OR Portland, OR White City, OR
PENNSYLVANIA
Bloomsburg, PA Blue Bell, PA Gettysburg, PA Harrisburg, PA Lancaster, PA Newtown, PA Philadelphia, PA Pittsburgh, PA Wilkes-Barre, PA York, PA
SOUTH CAROLINA
Beaufort, SC Charleston, SC Columbia, SC Conway, SC Graniteville, SC Greenville, SC Greenwood, SC Orangeburg, SC Rock Hill, SC Spartanburg, SC
TENNESSEE
Blountville, TN Clarksville, TN Collegedale, TN Gallatin, TN Johnson City, TN Knoxville, TN Memphis, TN Morristown, TN Murfreesboro, TN Nashville, TN
TEXAS
Abilene, TX Arlington, TX Austin, TX Beaumont, TX Brownsville, TX Commerce, TX Corpus Christi, TX Dallas, TX Denison, TX El Paso, TX Houston, TX Huntsville, TX Laredo, TX Lubbock, TX Lufkin, TX Mesquite, TX San Antonio, TX Victoria, TX Waxahachie, TX Weatherford, TX Wichita Falls, TX
UTAH
Cedar City, UT Kaysville, UT Logan, UT Ogden, UT Orem, UT Salt Lake City, UT
VIRGINIA
Daleville, VA Fredericksburg, VA Lynchburg, VA Manassas, VA Norfolk, VA Roanoke, VA Salem, VA Staunton, VA Suffolk, VA Virginia Beach, VA Wytheville, VA
WASHINGTON
Auburn, WA Bellingham, WA Bremerton, WA Ellensburg, WA Ephrata, WA Olympia, WA Pasco, WA Rockingham, WA Seattle, WA Shoreline, WA Spokane, WA
WEST VIRGINIA
Ona, WV
WISCONSIN
La Crosse, WI Milwaukee, WI Mukwonago, WI
WYOMING
Casper, WY Laramie, WY Torrington, WY
CANADA ALBERTA
Calgary, AB Edmonton, AB Fort McMurray, AB Lethbridge, AB Lloydminster, AB Olds, AB Red Deer, AB
BRITISH COLUMBIA
Abbotsford, BC Burnaby, BC Castlegar, BC Delta, BC Kamloops, BC Nanaimo, BC Prince George, BC Richmond, BC Surrey, BC Vancouver, BC Victoria, BC
CELEBRATING 60 YEARS
MANITOBA
Brandon, MB Winnipeg, MB
NEW BRUNSWICK
Bathurst, NB Moncton, NB
NEWFOUNDLAND AND LABRADOR
St. John’s, NL
NOVA SCOTIA
Halifax, NS
ONTARIO
Brockville, ON Hamilton, ON London, ON Milton, ON Mississauga, ON Niagara-on-the-Lake, ON North Bay, ON North York, ON Ottawa, ON Toronto, ON Welland, ON Windsor, ON
QUEBEC
Côte Saint-Luc, QB Montreal, QB
SASKATCHEWAN
Melfort, SK Moose Jaw, SK Nipawin, SK Prince Albert, SK Saskatoon, SK
YUKON TERRITORY
Whitehorse, YU
UNITED KINGDOM
Elgin, UK
GHAZNI
Kingdom of Bahrain, GHA Thomasville, GHA
EGYPT Cairo, EG
JORDAN
Amman, JOR
NEW ZEALAND
Taradale, NZ