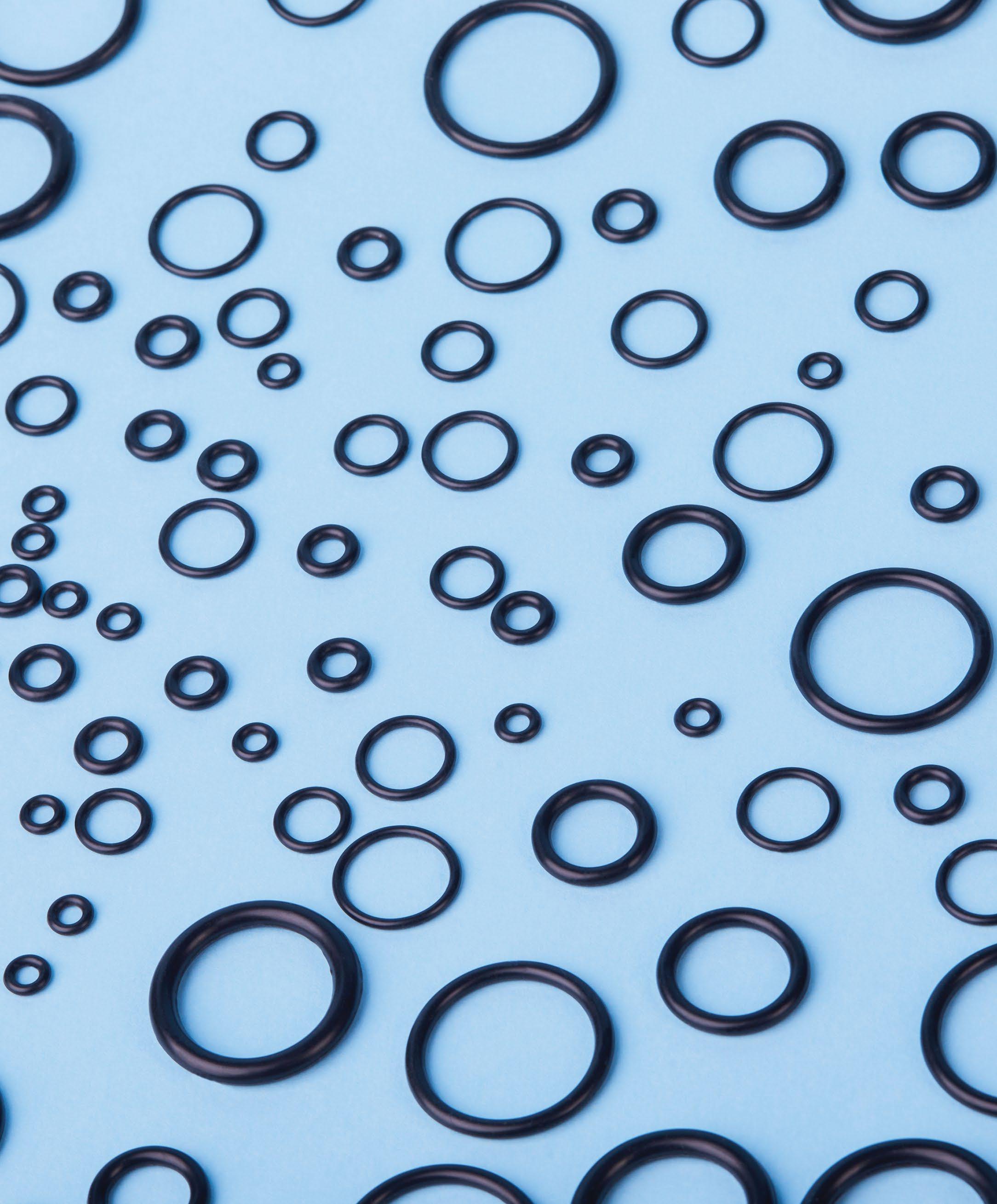
2 minute read
THE COST EFFECTIVENESS OF AN O-RING & BACK-UP RING COMBINATION
By Michael Cook, Global Segment Off-Highway and Marketing Americas Segment Manager Fluid Power
Fluid power applications present challenges for Original Equipment Manufacturers (OEMs). Not only must hydraulic seals prevent leakage, they must also withstand high pressures, extreme high and low temperatures, and transverse forces within the cylinder. That is why it is critical for OEMs to work with a knowledgeable sealing partner that offers a broad range of solutions to develop, manufacture, and supply seals to meet their unique needs. A solution that results from a true supplier partnership can help reduce assembly time and provide process automation resulting in cost savings for the OEM.
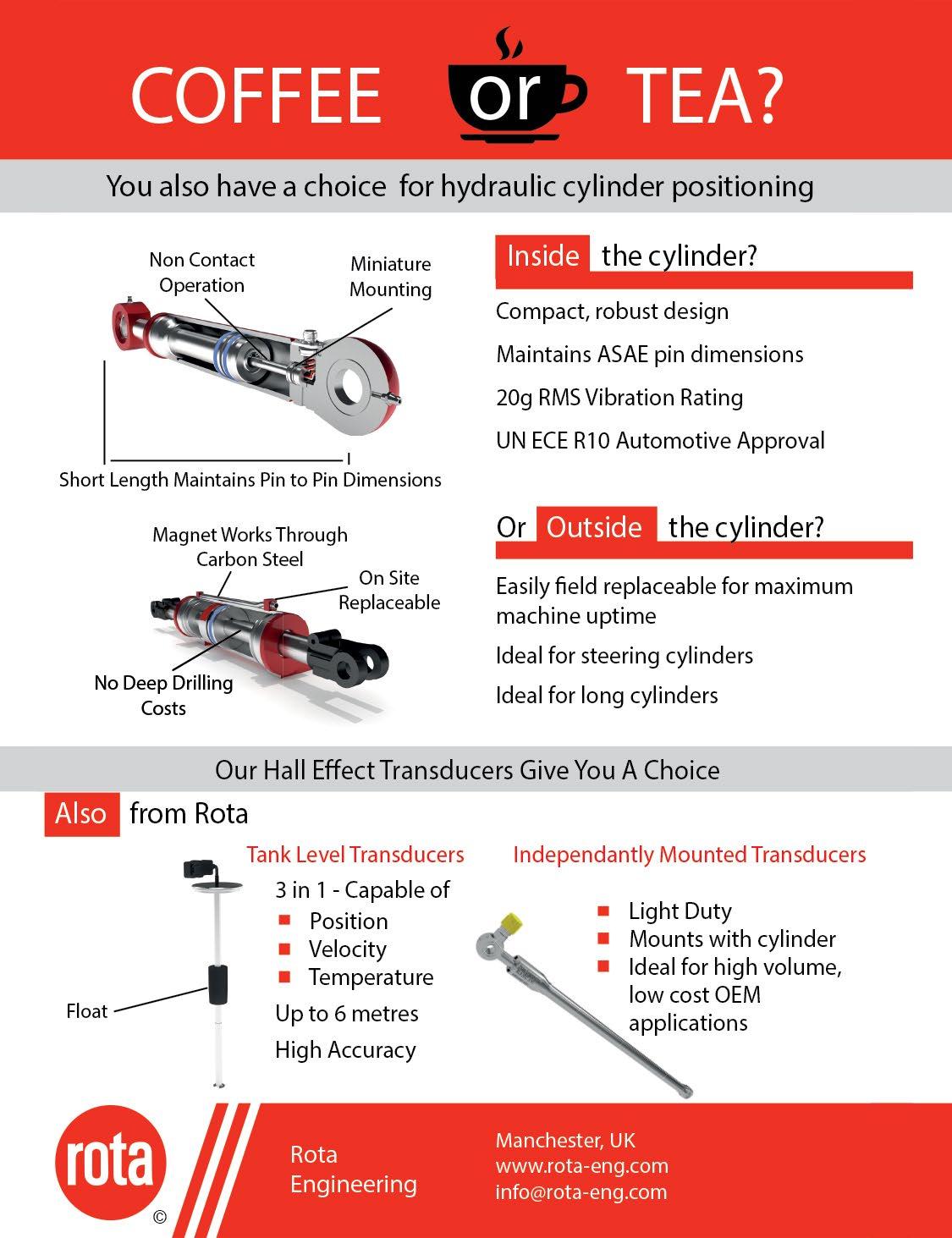
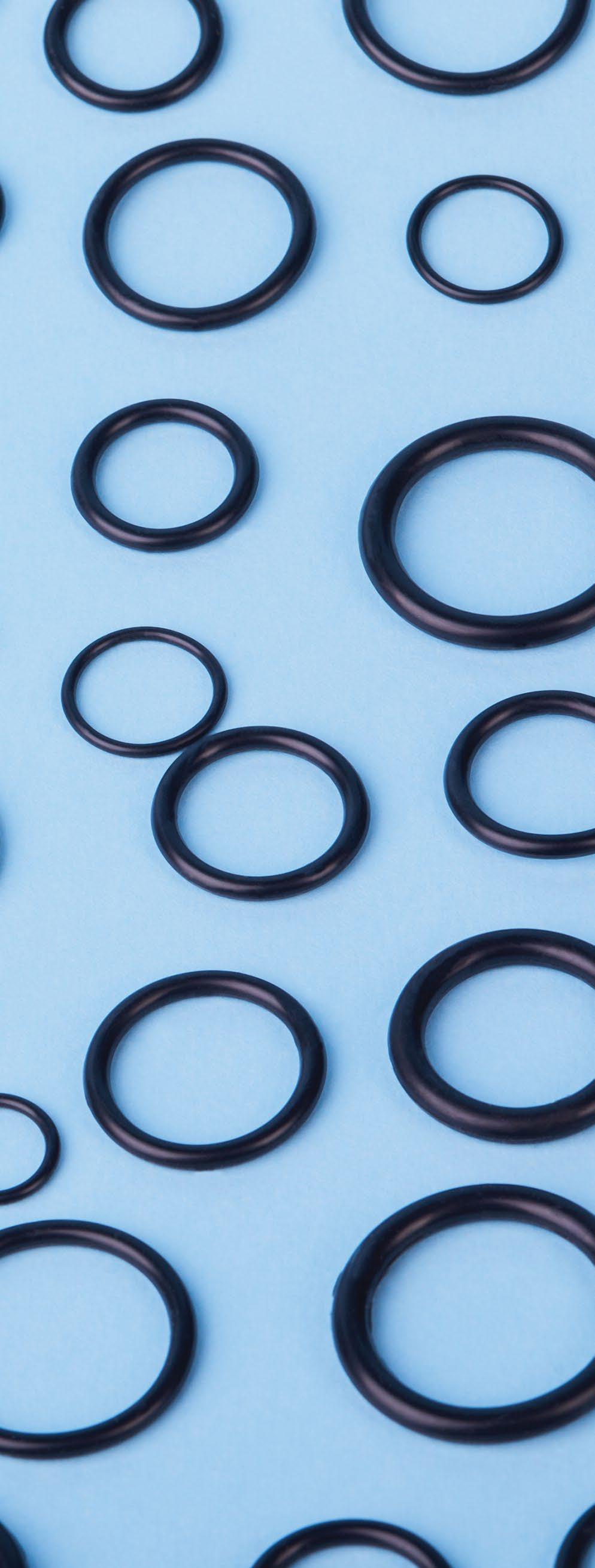
Superior testing and expertise
A full-service component manufacturer can utilize its database of compounds to help an OEM find the material formulation that performs best in their specific application. Top component suppliers have proprietary materials and products. Using these, their technical expertise and testing for non-standard hardware, they will make recommendations for the best options. They can create custom designs to meet customer-specific requirements with the aid of Finite Element Analysis (FEA) and other leading-edge technologies. If needed, seals can undergo short- or longterm testing before volume production.
Continued on page 10
Continued from page 9
Seizing a Sealing Opportunity for Efficiency

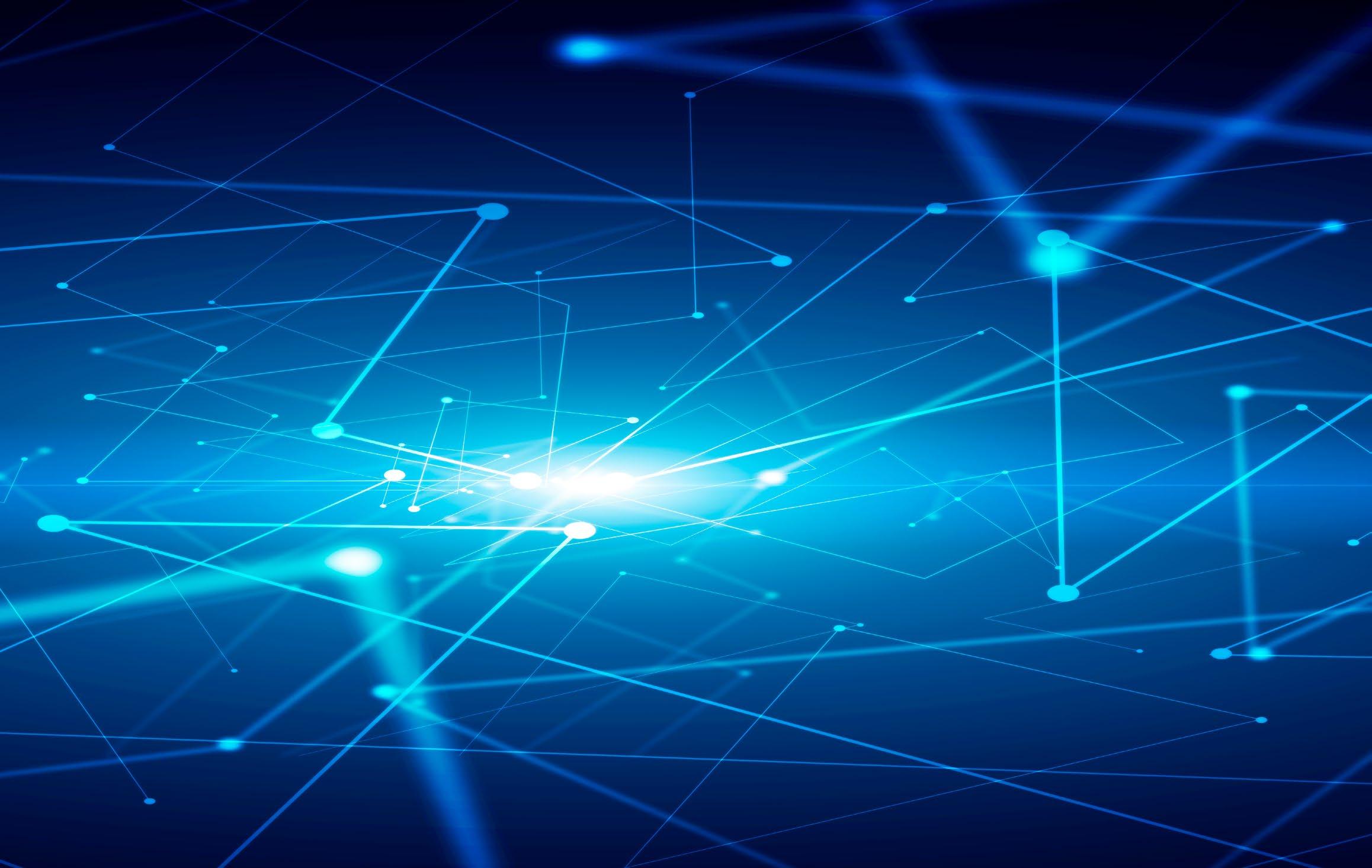
In many current hydraulic component designs, O-Ring or O-Ring and Back-up Ring combinations are mainly used as static seals. Using a single seal alternative can present significant advantages in terms of efficiency and return on investment (ROI).
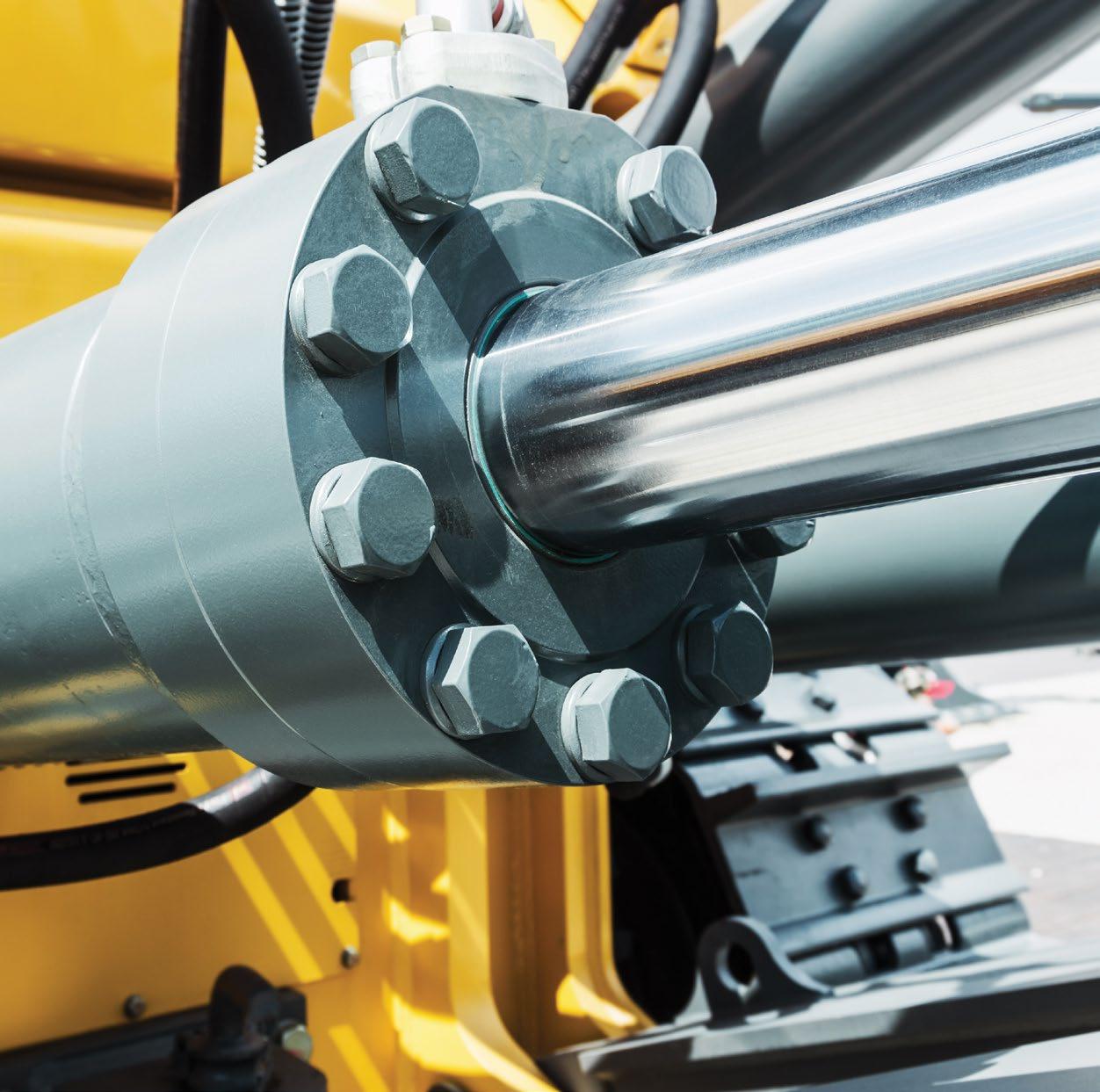
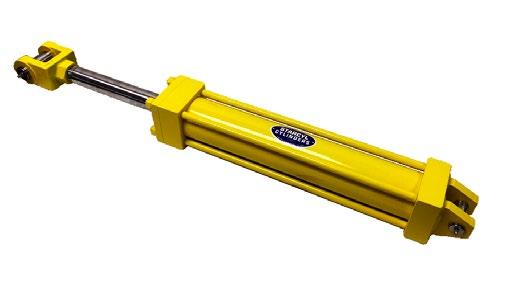

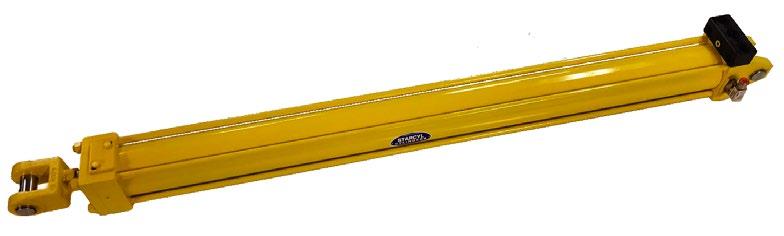
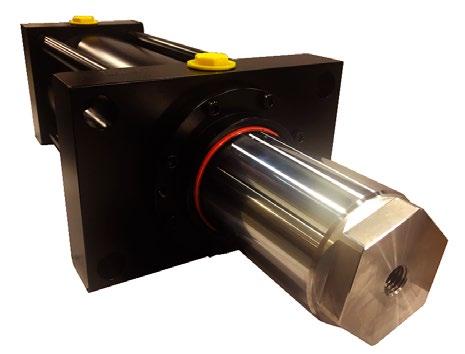

In one example, Trelleborg Sealing Solutions supplied standard static seals for a customer’s cartridge valves. Each cartridge valve required three O-Ring and Back-Up Ring combination sets, which made the assembly process very labor intensive. Seeing an opportunity to streamline operations, Trelleborg proposed that the customer switch to a single component static hydraulic seal for high-pressure applications, the Dualseal.

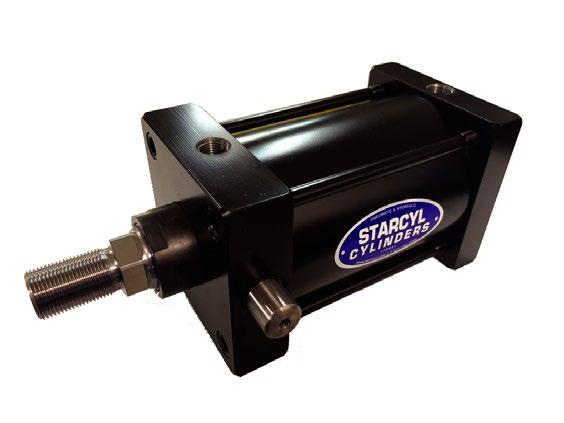
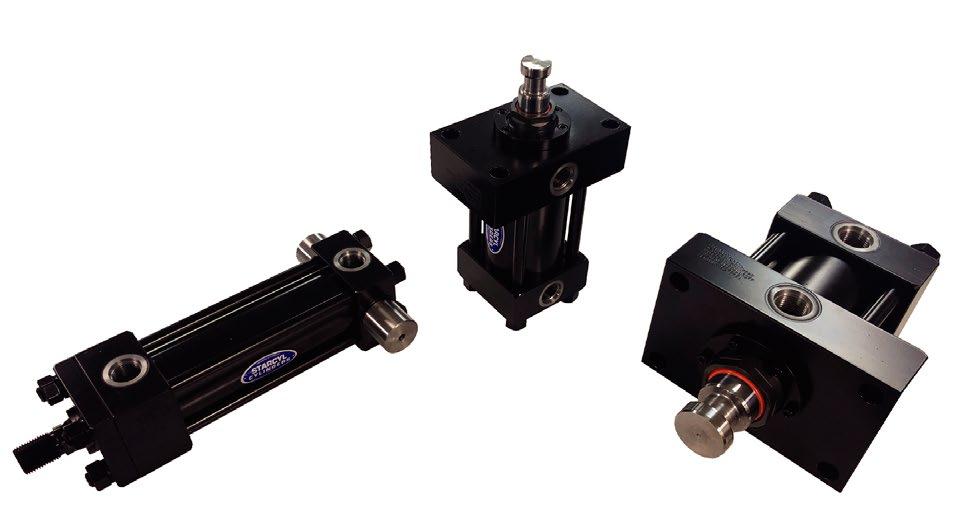
However, Trelleborg’s standard catalog Dualseal material did not offer the chemical compatibility needed for the customer’s cartridge valve application. Together with the customer, Trelleborg’s experts investigated elastomeric options, but found the available sizes were all too small for the application grooves.
A team of custom product engineers formulated a new design using FEA models and ran compatibility testing utilizing Trelleborg’s material laboratory. Having identified a suitable design and material, engineers took a standard Dualseal and created a custom profile for the customer. After testing variations of this, Trelleborg was able to design a modified Dualseal to withstand the demanding cartridge valve application.
Sometimes the Solution is Standard
Trelleborg also used its technical expertise to help Lion Hydraulics improve productivity and in-house assembly times by switching them to Dualseal for their static seals on hydraulic cylinders. Lion was using a two-piece O-Ring and Back-up Ring combination when Trelleborg introduced them to the single-piece standard Polyurethane (PU) Dualseal.
Utilizing industry-standard design profiles and sizes ensures designers and end users can easily specify sealing components, allowing the reuse of hardware designs. Standardization also supports ease of repair, refurbishment, and reuse with readily available replacement parts, to give the hardware a second or third life.
In addition to saving valuable assembly and production time, the switch to the PU Dualseal also alleviated quality issues that Lion experienced in the field with their nitrile rubber (NBR) Back-up Ring.
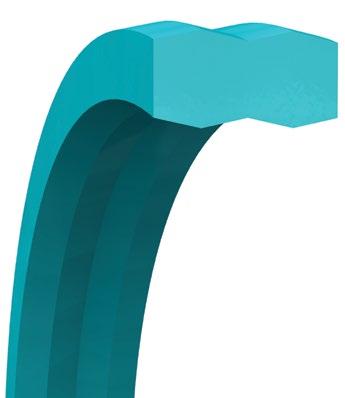
The Payoff
Both recommendations resulted in better ROI for the customer thanks to the reduced labor required to install one part instead of two and managing only one stock keeping unit (SKU). Finally, using one component greatly reduced the likelihood of incorrect installation and/or installation damage, which translates to less potential for leakage, less seal failure, and lower scrap and replacement costs.
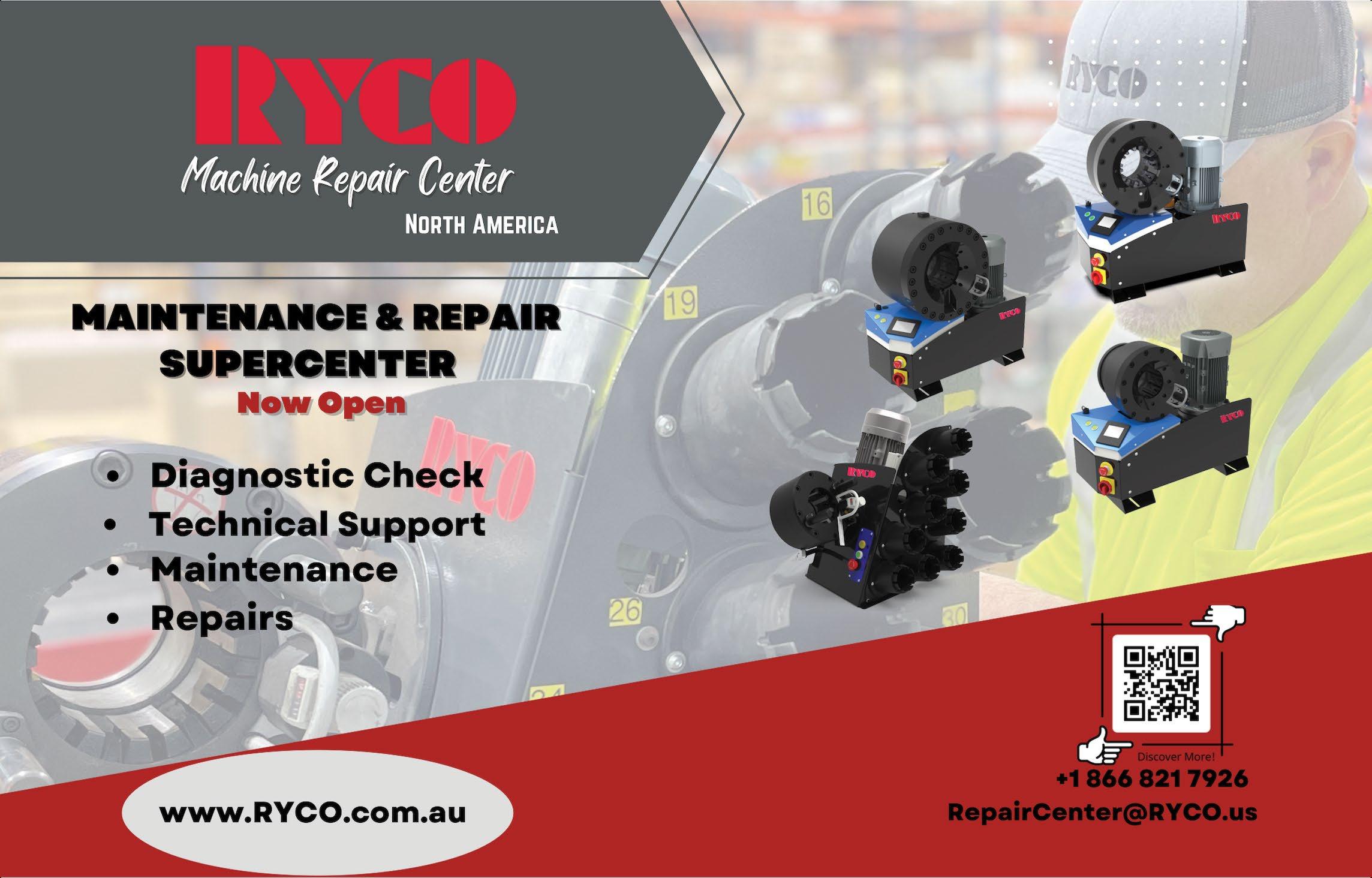
Additionally, with the Dualseal providing a virtually leak-free seal design, the customers minimize the risk of contamination to ground and water resources for the end user, protecting the environment from pollution.
Conclusion
Selecting the right seal and material in fluid power applications enables OEMs to increase efficiency and save time, which contributes positively to their bottom lines. By working with an experienced seal manufacturer, OEMs can ensure their hydraulic components incorporate the right seal in the best material for their application. •