
12 minute read
Test Your Skills
GAS-CHARGED HYDRAULIC ACCUMULATORS
Gas Valve
Bladder Nitrogen Gas
Accumulators are pressure vessels and are subject to the American Society of Testing Materials standards in addition to the International Standards Organization and the Occupational Safety and Health Administration guidelines. The use of accumulators may be subject to additional regulations, depending on location and application. Local and industry-specific standards should be investigated to confirm compliance. The accumulator manufacturer’s literature should be reviewed for additional recommendations and limitations. Because accumulators are pressure vessels, they cannot be modified in any way except by the manufacturer. Information concerning mounting and securing accumulators is also provided in the standards and guidelines. Note: Accumulators should be mounted vertically.
The precharge pressure of an accumulator is the pressure reading in the bladder when the accumulator is empty of fluid. The precharge requirement of the accumulator will vary based on the application, independent of the accumulator size. Common applications are to supplement pump flow, provide short-term back up power, absorb hydraulic shocks, or maintain system pressure. If the precharge pressure is low, the system operation will be sluggish. Low precharge in accumulators used for surge protection will allow a system with high system shocks to knock and make noise. If the precharge pressure in a bladder-type accumulator is high because the accumulator was precharged to a higher pressure than manufacturer specifications, the bladder may fail. Under normal operation, the bladder is compressed in the shell by hydraulic oil and only expands to rest against the poppet valve in the bottom of the accumulator when the system is off. Higher-than-specified precharge pressures can cause the bladder to pound against the poppet valve in the bottom of the accumulator when system pressure drops but is still within the operating range of the machine. This will make the bladder fail where it is pushed against the anti-extrusion valve.
Accumulator precharge should be checked on a regular basis. Occasionally, the precharge of an accumulator becomes low and must be reset. This requires checking the accumulator for internal and external leaks, and then recharging the accumulator with dry nitrogen. If the accumulator shows dents or obvious damage, it must be replaced. The precharge pressure of the accumulator is temperature sensitive. To accurately test the precharge pressure, it should be done immediately after the machine has been shutdown while it is still at operating temperature.
There are a number of safety precautions that must be observed when charging accumulators. Safety goggles, gloves, and other required protective equipment should be worn, and any external leaks must be stopped before charging the accumulator. In addition, ensure that the potential hazards of working with a gas in a confined space are understood and steps taken as required to keep personnel safe. If there is fluid in the precharge gas in a bladder-type accumulator, the bladder is either

Anti-Extrusion Valve Shell
Port
Port
Body Piston Nitrogen Gas
Bladder andpiston-type accumulators.
Gas Valve
passing fluid through the bladder membrane or has a leak. If the bladder is leaking, it must be replaced before recharging. If there is fluid in the precharge gas in a piston-type accumulator, the piston seal between the charge gas and system fluid is leaking.
Gas valves will vary with accumulator manufacturers and for pressures over 3,000 psi. Most manufacturers use an ISO 4570-8VI-style valve that may look like an automotive-type Schrader valve. However, it is rated for much higher pressure. The valve is used to charge the accumulator and release gas when necessary.
Steps to check and add to or reduce the precharge on an accumulator are as follows: 1. Ideally, the system will be at operating temperature. Lower all movable machine members, and block those that could move and injure personnel. Follow lock-out/tag-out procedures. 2. The system must be shut down or the accumulator isolated, and the hydraulic pressure side drained to the reservoir. 3. Before connecting the appropriate filling/testing valve and hose assembly to the nitrogen tank, ensure that all the valves are closed.
Use adequate safety precautions to ensure that accidental venting of the accumulator doesn’t render the room uninhabitable due to displaced oxygen.
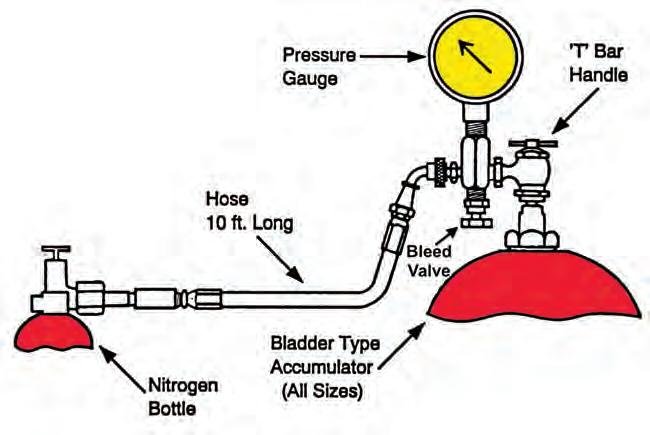
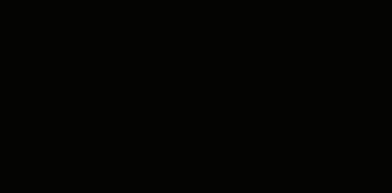
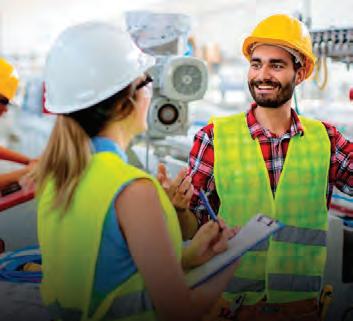
Accumulator charging valve setup.
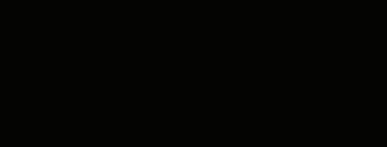
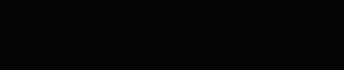

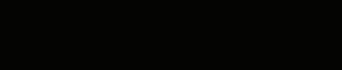
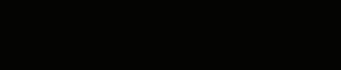
4. Verify that the precharge pressure matches the specifications for the application. 5. Remove the safety caps on both the accumulator and fill tank. 6. Gently screw in the T bar handle (CW) to open the charging fill valve to allow nitrogen gas to enter the accumulator. At this time, the actual precharge pressure will be seen on the gauge when gas from the accumulator fills the line. 7. Slowly open the fill valve from the top of the nitrogen tank to start charging the accumulator. Charge slowly and watch the pressure gauge for proper charge pressure. When the gas supply is turned off, the pressure will drop slightly. Add nitrogen as needed to reach the desired charge pressure. If overcharged, the fill valve can be closed and the bleed valve slowly opened to discharge excess gas. It will be extremely cold while venting. 8. After filling, close the fill valve on the nitrogen tank and close the fill valve on the accumulator by turning the T handle (CCW). 9. Open the bleed valve and release the trapped gas in the hose between the
accumulator and the nitrogen tank before disconnecting either end of the charge/fill kit. 10. Disconnect both ends of the charge/ fill kit, and screw the safety caps back on the accumulator and the nitrogen tank. Be sure to secure the nitrogen tank in a proper storage place.
It is a good practice to wait a few minutes and recheck the precharge pressure. If the accumulator was charged too quickly, the expanding gas can be cooled to provide an initial inaccurate reading. Remove the hose and charge valve assembly from the accumulator, and install a tag on the accumulator noting the date and precharge pressure. Install the charge valve protection cap.
Dry nitrogen is the preferred gas used to charge an accumulator. If the application requires a different gas to be used, ensure it is inert.

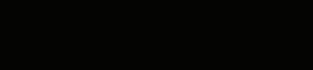
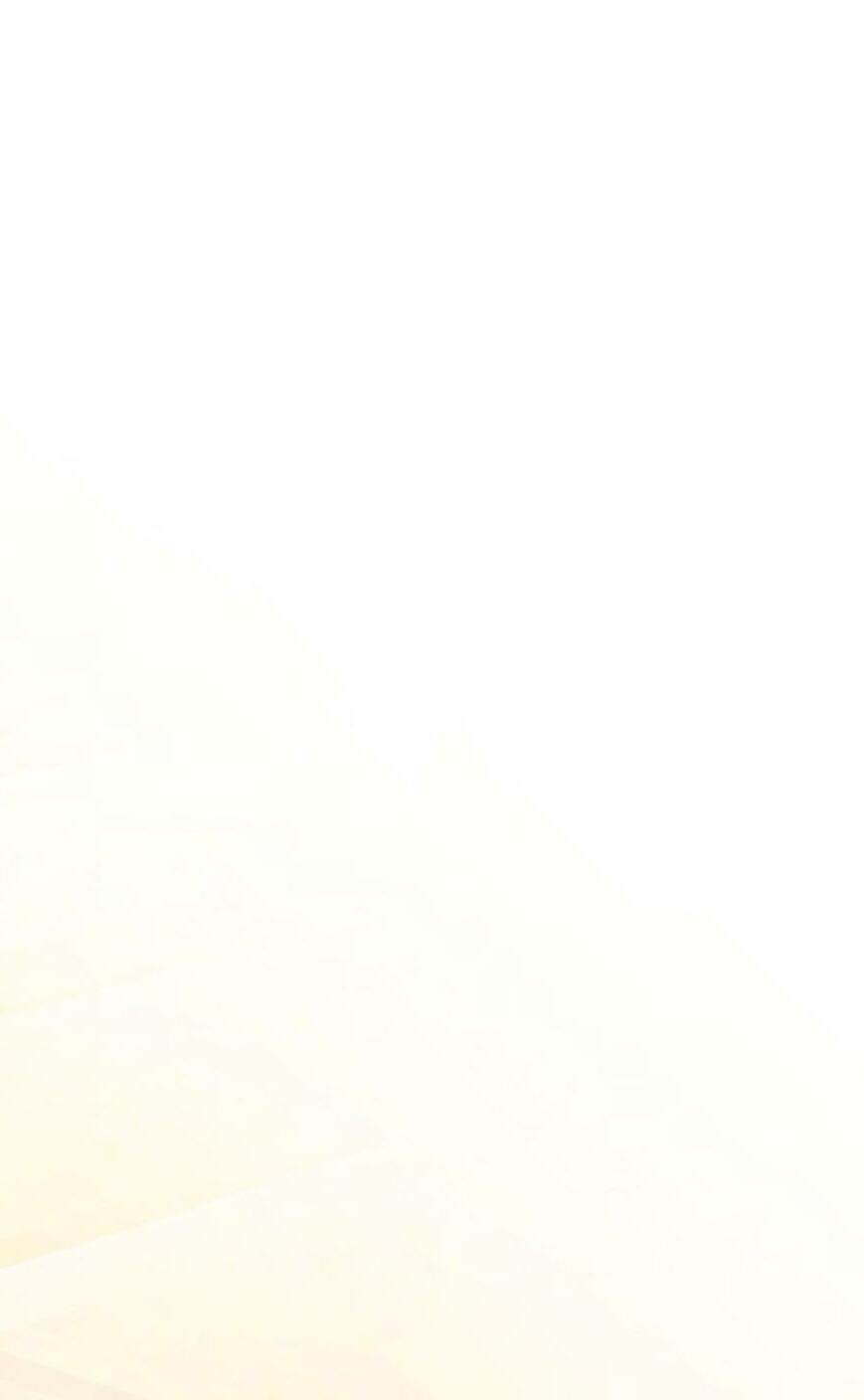
TEST YOUR SKILLS
1. Oxygen must not be used to charge a hydraulic accumulator because it:
a. Is too expensive. b. Contaminates the fluid. c. Could cause an explosion. d. Will leak through the bladder. e. Has the wrong expansion characteristics.
2. What would cause hydraulic fluid to come out of the gas valve when the precharge gas is released from a bladder-type accumulator?
a. Bladder leaks. b. Operation is normal. c. Accumulator is overcharged. d. Hydraulic pressure was not released. e. Foot valve in the accumulator is stuck open.
See page 31 for solutions.
ONSITE
TRAINING
AND CERTIFICATION FOR: Hydraulic Techs & Engineers Electrical Techs & Engineers Pneumatic Techs & Engineers Multicraft Techs & Engineers
UPSKILL YOUR WORKFORCE!
CFC provides direct, Industry and/or Machine-specific training to companies the world over. Our Hands-On Training Equipment is mobilized directly to your facility with Certified Instructors traveling on-site. This turnkey approach includes all books, materials, equipment, and travel arrangements. We have the capability to upskill your entire workforce NOW!
CFCINDUSTRIALTRAINING.com 7042 Fairfield Business Drive Fairfield, Ohio 45014 +1 513.874.3225 info@cfcindustrialtraining.com
PRODUCT SPOTLIGHT
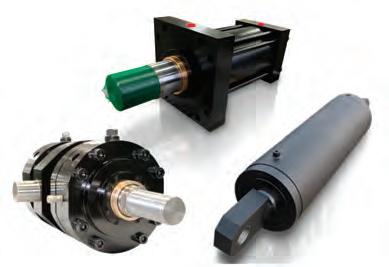
Go ahead. Push me. Ordinary heavy duty not heavy enough?
Heavy-Duty Mill Cylinders for:
• Induction-Hardened,
Chrome-Plated Rods • Heavy Wall Tubing • Replaceable Glands & Retainer Rings • High-Load Piston Design
Think indestructible and call Yates. www.yatesind.com
Yates Industries (HQ) 586.778.7680
Yates Cylinders Alabama 256.351.8081
Yates Cylinders Georgia 678.355.2240
Yates Cylinders Ohio 513.217.6777
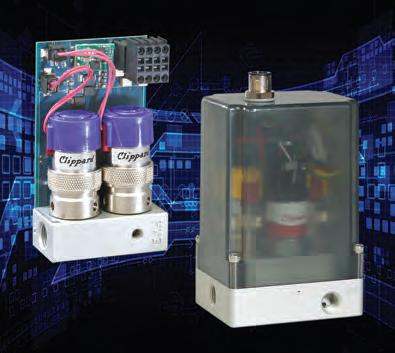

Cordis Electronic Proportional Pressure Controls
Known for reliability, innovation and focus on miniature pneumatics, Clippard’s new revolutionary micro-controllers utilize the proven EVP and DVP lines of Clippard proportional valves allowing for steady, repeatable downstream pressure as demand or processes change. The result, a precise, linear digital pressure control within a closed-loop system with ultra high resolution (≤5 mV) and repeatability. Made in the USA.

Suppressor Accumulators
Wilkes and McLean manufactures an In Line Noise and Shock Suppressor for hydraulics and is a stocking distributor of Nacol Accumulators. Our suppressors eliminate pulsations, which greatly reduces noise and vibration from applications from a few gallons up to 200 gallons. We stock all of our suppressor sizes as well as Nacol Accumulators and parts from 1/5 of a pint up to 15 gallons, in our Schaumburg, Illinois facility.
877.534.6445 info@wilkesandmclean.com | www.wilkesandmclean.com
New—Flat Face Design "TVF" Series Quick Disconnect
• Up to 6,000 PSI Operating Pressure—
Coupled or Uncoupled • Full 4:1 Safety Factor • Superior Flow Characteristics—Minimal
Pressure Drop • RoHS Compliant Plating • Multiple Port Options—Female NPTF,
Female SAE O-Ring, Female BSPP,
Code 61 & 62 Flange Port/Head
P.O. Box 6479 • Fort Worth, TX 76115 817.923.1965 • www.hydraulicsinc.com

Protection for All Things Hydraulic, Pneumatic and Fluid Power
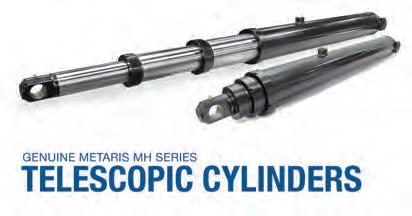
MOCAP manufactures an extensive range of protective closures to guard pipes, hoses, and hydraulic fittings from dirt, moisture, and damage to help maintain equipment reliability. Included are a variety of sizes and styles of Threaded and Non-Threaded plastic Caps and Plugs for Metric, NPT, BSP, JIC and SAE Threaded Connections, Ports and Fittings. These are in addition to MOCAP’s already extensive lines of low-cost Caps, Plugs, Grips, Netting, Tubing and Tapes for general Product Protection, Finishing and Masking. All of our stocked items are ready for immediate shipment and available in Box, Mini-Pack and Micro-Pack quantities. Free Samples are always available for testing purposes.
sales@mocap.com www.mocap.com
METARIS TELESCOPIC CYLINDERS – ENGINEERED FOR RUGGED RELIABLE OPERATION
HITACHI FLANGELOCKTM You can’t go wrong with our MH series line of telescopic cylinders. Major design improvements over competing products include a AND CAP KITS AVAILABLElow friction dual lip rod seal; and all stages chrome plated and roller burnished for smoother operation, increased scratch-, impact- and Part number Part description Applicable machines Number of parts Weight (kg)rust-/corrosion-resistance, and greater stability. Our special low friction dual lip rod seal also has many benefits including reduced SWINGFLGLCK2062 Swing hose FlangeLockTM kit EX3600, EX5600, EX8000 16 x 2062U - red FlangeLockTM 6.7running friction for smoother and faster operation, no mis-staging, SWINGCAP2062 Swing circuit cap kit EX3600, EX5600, EX8000 16 x 2062 - cap 4.5 no seal adjustments are necessary, no compression set like standard TRAVELFLGLCK2462 Travel hose FlangeLockTM kit EX3600, EX5600, EX8000 16 x 2462U - purple FlangeLockTM V-packing, longer seal life than V-packing and a better operating 7.7 temperature range. Our MH series single acting telescopic cylinders TRAVELCAP2462 are fit, Travel circuit cap kit EX3600, EX5600, EX8000form and function interchangeable 16 x 2462 - cap 6.4with other manufacturers’
FRONTATTFLGLCK326162 Front attachment FlangeLockTM kit EX3600, EX5600, EX8000cylinders in the market today. 14 x 3262U - black FlangeLockTM 4 x 3261U - black & silver FlangeLockTM 8.9
FRONTATTCAP326162 Front attachment cap kit EX3600, EX5600, EX8000Hydraulex 14 x 3262 - cap 4 x 3261 - cap 9.5
BOOMARCHFLGLCK3262 Boom arch hose FlangeLockTM kit EX3600, EX5600, EX8000 20 x 3262U - black FlangeLockTMFor more information, call us at 9.9 1-800-323-8416 or visit www.hydraulex.comBOOMARCHCAP3262 Boom arch hose cap kit EX3600, EX5600, EX8000 20 x 3262 - cap 11.3

THE ULTIMATE CONTAMINATION CONTROL TOOL
SAVE TIME SAVE MONEY SAVE LABOR SAVE OIL
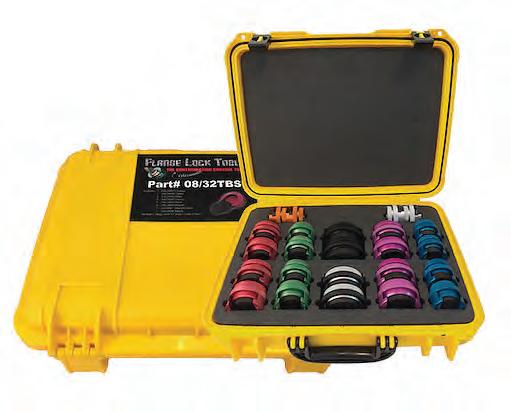
This product is Patented, other Patents pending. CONTAMINATION CONTROL
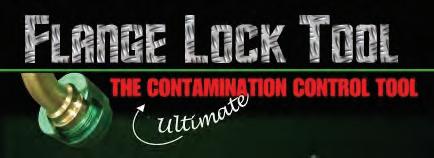
Routine and scheduled maintenance of hydraulic systems are vital to getting the most out of your Hitachi Mining Excavator. While maintenance plays the largest role in the prevention of unnecessary machine downtime, it can also expose the hydraulic system to high levels of contamination rapidly decreasing component longevity. The importance of contamination control is sometimes Stop the Mess overlooked when performing maintenance due to incorrect practices being used. THE FLANGELOCK™ TOOL AND CIRCUIT BLANKING CAPS The FlangeLock™ tool and caps are the ultimate contamination control tools for protecting your hydraulic system. The FlangeLock™ allows for the simple sealing of open hydraulic flanges without tools while the caps can be bolted in place of a flange connection. Easy on, easy off, they offer a leak-proof solution to hydraulic systems and environmental cleanliness. FlangeLock™ tools and caps stop the mess.
The FlangeLock™ Tool is the ultimate contamination control tool for protecting your hydraulic systems. It allows for the simple sealing of open SAE code 61, 62 HITACHI MAKING CONTAMINATION CONTROL EASY & CAT-Style hydraulic flanges without tools. Constructed from lightweight aluminum. Hitachi have packaged FlangeLock™ tool and caps specifically for Hitachi mining excavators. The Hitachi customised kits make sure no matter which component routine maintenance is being performed on, you will always have the exact Easy on, easy off. Offers a leakproof solution to hydraulic system and environmental number of FlangeLocks™* and caps to help reduce contamination. cleanliness. FlangeLock™ Tools stop the mess!*Note: FlangeLocks™ are not to be used under pressure
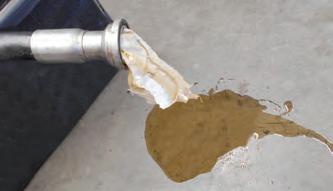
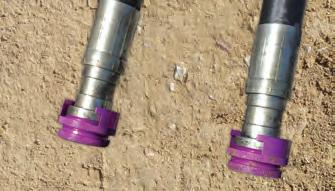
• No tools required • No expensive hardware needed • No more rags stuffed into hoses • No more messy plastic caps • The ultimate contamination control tool
• One hand installation • Eliminate hydraulic oil spills & clean up • Quick installation & ease of usage Call you local Hitachi Muswellbrook representative or the branch on 02 6541 6300 for more information. • Safe for personnel & environment • Industry acclaimed