
15 minute read
Case Study: Drop-in Solution Forces Out Extrusion Press Downtime Aluminum production increased so much that the company’s oven could not keep up
Drop-in Solution Forces Out Extrusion Press Downtime
By Michael Kramer, Press Application Engineer, and Andrew Binversie, Manager, Press Applications, Bosch Rexroth Corp.
The extrusion press is the workhorse of manufacturing. Long valued for its ability to produce high-quality parts, it can operate productively for many decades with proper maintenance and life-cycle management. However, this longevity is now leading to some issues in the industry; many extrusion presses are using outdated, inefficient, and unreliable hydraulic pumps.
Superior Extrusion found itself confronted with this situation. In 1996, the company purchased a used 1,650-ton Farrel press. In use since 1971, the 7-inch press has since produced over 200 million pounds of aluminum extrusions for the Michigan-based manufacturer. The press currently runs one 10-hour shift per day, with plans to move to two shifts in the near future.
Planning the upgrade
»In an aluminum extrusion press of this size, hydraulic components are under significant and constant wear and tear. Decades of production of light truck accessories, roof racks, commercial building products, and military materials had taken its toll on the variable-displacement legacy pumps driving the press. Maintenance of the hydraulic elements was becoming increasingly expensive.
A key, decades-old component on the press is the hydraulic pump. Like many customers using similar model pumps on other presses, repairing and maintaining these older pumps in operating condition usually required rebuilds, and doing so was becoming a challenge for Superior. Parts became obsolete, and qualified technicians became harder to find. Furthermore, rebuilds do not always deliver the same quality and service as the original unit. And, in many cases, the parts being replaced were rebuilds as well.
One major consequence of the pump’s aging condition was that hydraulic fluid leaks became increasingly problematic. Oil leaks increased costs for the company, which logged 65 to 70 hours of downtime every year to repair these leaks. From constant welding to fabricating new pipes, the cost and hassle of downtime takes its toll.
Designing a drop-in solution
»The importance of the press required careful planning that would identify the right solution and minimize downtime during installation. Superior approached Bosch Rexroth to help develop the solution since they had worked together on other hydraulic projects in the past, both for new systems and equipment upgrades.
The nature of the original pumps required an engineered solution that would match the way older components operated. The original pump sat on top of the tank, drawing oil up from the reservoir and supplying it to the system through two supply ports.
Most modern pumps operate with just one supply port, so installing a new pump would require careful planning and reconfiguration of the hydraulic system. At the same time, Superior and Bosch Rexroth both wanted to design an approach that would provide a relatively simple and straightforward upgrade solution.
Prior to working with Superior, the Bosch Rexroth team recognized that this pump style was becoming obsolete. In response, engineers in Bethlehem, Pennsylvania, collaborated with associates in Germany to develop a unique system to directly replace the old, expensive, and inefficient pumps. The initiative involved the design and engineering of a pump/manifold/controls solution and prototype construction.
The prototype underwent 150 hours of testing at the Bethlehem facility and over 2,000 testing hours in production on a customer’s 2,400-ton extrusion press. The team instrumented the test unit with many types of pressure transducers and flow meters to record data. They completed a 100-hour test at full pressure, followed by a complete teardown of the internals to document the wear and tear. The results confirmed the drop-in solution met the company’s performance and reliability standards.
Superior Extrusion’s project was the first opportunity to apply the tested drop-in concept. At the solution’s heart was a Rexroth A4VSO 500 axial piston pump. Adding a check valve at the bottom of the suction pipe and injecting a partial filling volume into the pipe ensured that the pipe inlet was full on startup or under minimal flow conditions.
The Bosch Rexroth team also incorporated a custom manifold circuit designed to replicate
A Rexroth A4VSO 500 axial piston pump was the heart of the drop-in solution. Oil is directed to the correct port with type LC and LFA two-way cartridge valves. An HACD digital electronic control was configured to take the existing analog signal outputs to control both the A4VSO piston pump and the LC and LFA valves.
the two-way function with two pressure ports in the same location as the legacy pump. Two-way cartridge valves type LC and LFA then directed the oil to the correct port. The solution conserved as much of the existing configuration as possible so that it bolted directly to the existing piping. The new Bosch Rexroth pump manifold deckplate preserved all of the existing press piping.
To control flow through the pressure ports, an HACD digital electronic control was configured to take the existing analog signals that previously controlled the legacy pumps and use those outputs to control both the A4VSO pump and the LC and LFA valves. This significantly simplified the controls challenge of swapping out the legacy pump and valves with the current generation of hydraulics.
The result was a drop-in solution that would modernize the press without the significant downtime or cost associated with a complete upgrade or replacement. In fact, the installation took place over a long weekend, with tear out happening Friday and full production by Tuesday.
Measurable results
»The hydraulic pump retrofit produced measurable results almost immediately. The most significant improvement early on was the increase in press speed. Without any fine-tuning of the controls platform or the PLC code, the change was dramatic.
“Prior to the upgrade, the press ran around 2,000 pounds per hour,” said Bradley Couture, Superior Extrusion president and CEO. “Now it runs around 2,400 pounds per hour, about a 14% increase. The metal was just flying down the table. If the press ran 24 hours a day, five days a week, that would produce 1.8 million more pounds per year.”
The speed of the press increased so much that when one particular die ran at 2,800 pounds per hour, Superior’s oven could not keep up with the production run.
Superior found the new retrofit operated more efficiently. The Bosch Rexroth pump used less energy to the extent that a few months after the retrofit, they swapped out 200-horsepower motors for new, more energy-efficient, 150-horsepower motors with no loss of performance. The oil temperature also decreased.
“Before the upgrade, it would run normally at around 110°F to 120°F (43°C to 49°C),” Couture said. “With the Bosch Rexroth pump, it operates between 105°F and 110°F (40°C and 43°C). So the press runs more efficiently and at a cooler temperature.”
Finally, it appears that oil-leak-related downtime is being significantly reduced, from 65 to 70 hours per year previously to just three hours last year. Those savings added up, especially considering that press-repair time could run up to $800 per hour.

Each year, the International Fluid Power Society and the Fluid Power Journal hold a photo contest in honor of Fluid Power Professionals' Day. This year’s contest runs from January 1 through March 31, 2021.
THE 2021 PHOTO CATEGORIES ARE:
1. New Perspective: Photos that show fluid power used in novel ways and from views not everyone gets to see. 2. Teamwork: Photos of people working together using fluid power to get the job done. 3. Fun with Fluid Power: Photos that capture the joy of using, learning, or teaching about hydraulics and pneumatics. 4. The Muscle of Fluid Power: Photos that capture the might of fluid power in action.
A panel of judges will announce three winners for each category on June 19, 2021 in celebration of Fluid Power Professional’s Day. A People’s Choice recognition will be awarded based on votes during a one-week voting period. Submit your fluid power photo by visiting www.fluidpowerjournal.com to take your shot at recognition in the Fluid Power Journal.
CELEBRATING 60 YEARS
Sheet Metal Vacuum Gripping
By Dane Spivak, Engineering Manager, Davasol Inc.
»A FLAT SMOOTH surface with plenty of area is an ideal product for vacuum gripping or pick and place. Products such as sheet metal provide easy cup sealing and plenty of area for suction cup placement. Putting together a system that works is easy enough, but designing an efficient system that is properly engineered can provide significant savings in cost, energy consumption, maintenance, and reliability.
There are specific vacuum cups designed for the steel-stamping industry that are referred to as heavy-duty metal-stamping cups, or a variation of those words. Stamping cups tend to be flat or single bellows, have an integral metal fitting for rigidity, and have internal ribs for oil channels and increased frictional gripping force. These suction cups are usually made in nitrile or polyurethane materials. Polyurethane is an ever-popular choice as it typically provides longer cup life and is nonmarking. Nitrile is adequate in these categories as well, so some users will stick with this material that they have been using for some time and that can be sourced at a lower cost. Other manufacturer-specific materials are also available. Figure 1 shows an example of conventional stamping cups and their features.
integral fitting
oil channels
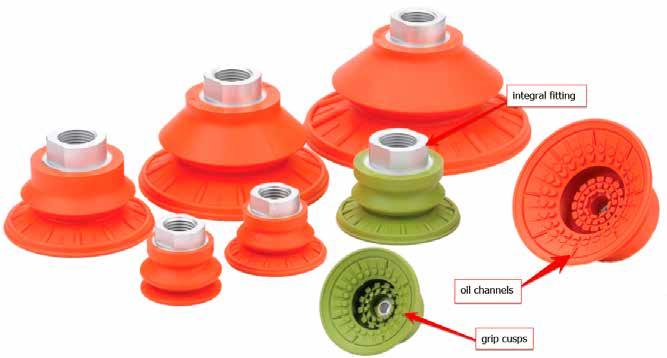
grip cusps
Figure 1: Examples and features of typical stamping vacuum cups.
Stamping cups are usually round or oval. Round is the go-to shape; oval is used for narrow points or any target areas where a round cup would not fit or seal. Because of the nature of metal sheets, which warp and bend across their surface and have manufactured curves formed from press operations, single short-bellows cups are used to provide height and angular compensation as well as allow the cup lips to conform and seal against uneven locations. Flat cups are useful when sheets are relatively level, allowing for a sturdier grip. If need be, spring-loaded level compensators can always be used as a vertical buffer, as they often are with both flat and bellowed cups.
The gripping forces in many steel-stamping applications, such as sheet pick and place, are overkill. The reason is that an array of cups spread out across the surface is required for a balanced and stable grip. When gripping large surface areas, particularly thin sheet products, it is
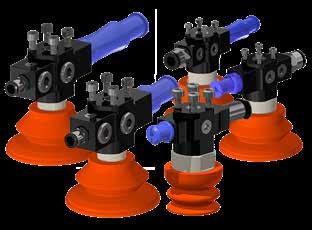
Figure 2: Stamping cups close coupled to venturis.
Figure 3: Self-closing valve components and installation. Scan the barcode with the camera on your smart phone to watch the video.

important to have many smaller cups at multiple points instead of fewer cups with bigger diameters. The goal is to spread the gripping force, but when doing so, the cup diameters should be sized appropriately so they provide a reasonable and safe gripping force without exceeding needs. Using the right cup size can save considerable cost on parts and energy use when considering the vacuum generators required.
The traditional vacuum system for pick and place in metal stamping is one air-powered venturi generator close coupled to a single suction cup, as shown in figure 2. This allows for each cup to be fully independent and simplifies installation for the user or machine builder. It is an easy, effective way to get the job done, though the approach has its challenges, including excessive air use, lack of filtration, and managing each as an individual system.
The alternative and solution to the single-cup-per-venturi conundrum is a centralized system in which a larger venturi powers and controls a set of cups, or a vacuum-pump and vacuum-valve system to do the same. Larger venturis allow for using multistaged units that use air more efficiently, allowing a reduction in their consumption. In a centralized system, the external plumbing creates room for installation of a proper vacuum filter to protect the vacuum generator. Having a single vacuum source is easier to manage and maintain with controls, sensors, and other system components. Motor-driven vacuum pumps are not the most popular in stamping since pumps cannot be mounted to the robot arm, and they require vacuum valves to control the cups. In this case there are extra pieces, adding to the work, and higher costs that are generally not worth it for many facilities with an abundance of compressed air available. Centralized vacuum systems have their benefits, but they typically require a larger variety of parts for plumbing and rely on all cups sealing properly. For cups potentially leaking in centralized systems, there are techniques to isolate them if they do not seal properly. Products such as velocity fuses, shuttle valves, or self-closing valves shut off vacuum from cups that do not seal against the product. The valves close based on the in-rush of flow from the leaking cups. Figure 3 illustrates a self-closing valve’s components and functionality. With one of these on each cup, the system becomes universal in a sense because any number of cups can
grip the product or shut independently while still achieving maximum vacuum-level pressure. These types of system designs require the cups to contact the product first before vacuum is turned on to ensure they do not close prematurely. Additionally, if the sensors are connected into the vacuum system, it can be difficult to measure lifting force and understand which cups are gripping the product. A vacuum sensor would be required on each cup between the self-closing valve and cup to get a true measurement.
Revisiting compressed-air consumption, venturis use compressed air to generate vacuum, and the total consumption is correlated to how much time the venturi runs. Vacuum gripping flat smooth surfaces creates an excellent opportunity to save air because the venturis can run to charge up the vacuum then shut off once the vacuum level reaches its set point. Then check valves and self-closing valves in the system lock in and maintain the vacuum. Should the vacuum level drop, the venturi will turn on and charge up the system. Figure 4 illustrates an example of a venturi coupled with an air energy-saving kit consisting of the switch and pilot valve. This technique allows for the venturi run time to be reduced to a fraction, as it can remain off for all the pick-movement cycle in a pick-and-place application, and much longer in a vacuum hold-down type of process. It also works well with products such as the self-closing valve. Energy-saving parts are inexpensive and easy to use, which makes them very attractive to users.
Metal-stamping vacuum gripping applications offer the convenience of a simple and reliable system. However, cup selection and the use of venturis can greatly impact cost, efficiency, and energy use. Talk to a professional to find out which design is best for your application.

New!


FLAT FACE DESIGN “TVF” SERIES QUICK DISCONNECT

• Up to 6,000 PSI Operating Pressure—Coupled or Uncoupled • Full 4:1 Safety Factor • Superior Flow Characteristics—Minimal Pressure Drop • RoHS Compliant Plating • Multiple Port Options—Female NPTF, Female SAE O-Ring, Female BSPP, Code 61 & 62 Flange Port/Head
P.O. Box 6479, Fort Worth, TX 76115 V. 817/923-1965 www.hydraulicsinc.com
pilot-operated pneumatic valve
pneumatic vacuum switch
vacuum inlet
Figure 4: Multistaged venturi with built-in check valves coupled with an energy-saving kit.
This article is the opinion of the author, Dane Spivak of Davasol Inc., an industrial brand management firm with many clients. One of Davasol’s HYDRAULIC NOISE, SHOCK clients, Vacuforce LLC, based in Indianapolis, partners with the author on AND VIBRATION SUPPRESSOthis article. Contact Dane Spivak at dspivak@davasol.com. R
HYDRAULIC NOISE, SHOCK AND VIBRATION SUPPRESSOR HYDRAULIC NOISE, SHOCK AND VIBRATION SUPPRESSOR HYDRAULIC NOISE, SHOCK AND VIBRATION SUPPRESSION
8775346445 www.wilkesandmclean.com info@wilkesandmclean.com8775346445 8775346445 www.wilkesandmclean.com info@wilkesandmclean.com www.wilkesandmclean.com info@wilkesandmclean.com

»transfluid’s t-cut tube-cutting machines promise chipless cuts of tubes with a diameter of up to 80 mm.
The RTO 628 cuts tube diameters of 6 to 28 mm (0.24 to 1.1 inches). The RTO 2080 handles tube diameters of 20 to 80 mm (0.79 to 3.15 inches).
As an all-in-one solution, the t-cut can manufacture medium and large volumes with different cutting options, using a cut-through, pull, or pull-and-break method. Changing the setup for other tube sizes or lengths takes little time.
In addition to the orbital cutting technique, transfluid also offers the familiar blade-cutting method. If needed, the cutting step can be integrated with the process on the bending machine. The bending and cutting process are easily and reliably combined, with little chip generation. For more information, visit www.transfluid.net/ en/homepage.html.
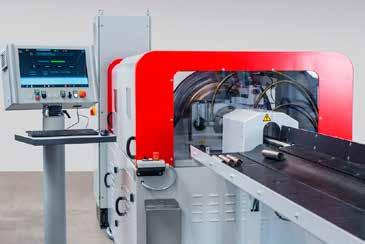

Greene Tweed Offers Wear- and Abrasion-Resistant Pump Components
»Greene Tweed, a manufacturer of high-performance elastomers, thermoplastics, composites, and engineered components, offers wear-resistant (WR) and abrasion-resistant (AR) pump components engineered from high-performance thermoplastic composite materials for centrifugal pumps and magnetic drive pumps.
Greene Tweed’s WR line offers excellent wear and friction properties, along with superior nongalling and nonseizing performance. The WR material portfolio enables extended mean time between repair and improved reliability. Offering extended dry-run performance and exceptional chemical resistance, Greene Tweed’s WR materials can often reduce running clearances by more than 50%. These reduced clearances minimize recirculation, which maximizes rotor stability, reduces vibration, and improves overall efficiency.
Greene Tweed’s AR composites are recommended when pumping in a watery media with the presence of abrasive materials like sand or sludge. Benefits include low hydrolysis/low swell of parts in water, self-lubricating material properties, and overall reduced effects of abrasion. Pump customers can increase intervals between overhauls and improve pump reliability. The composites promise to last up to five times longer than traditional materials. For more information, call (215) 256-9521 or visit www.gtweed.com.
