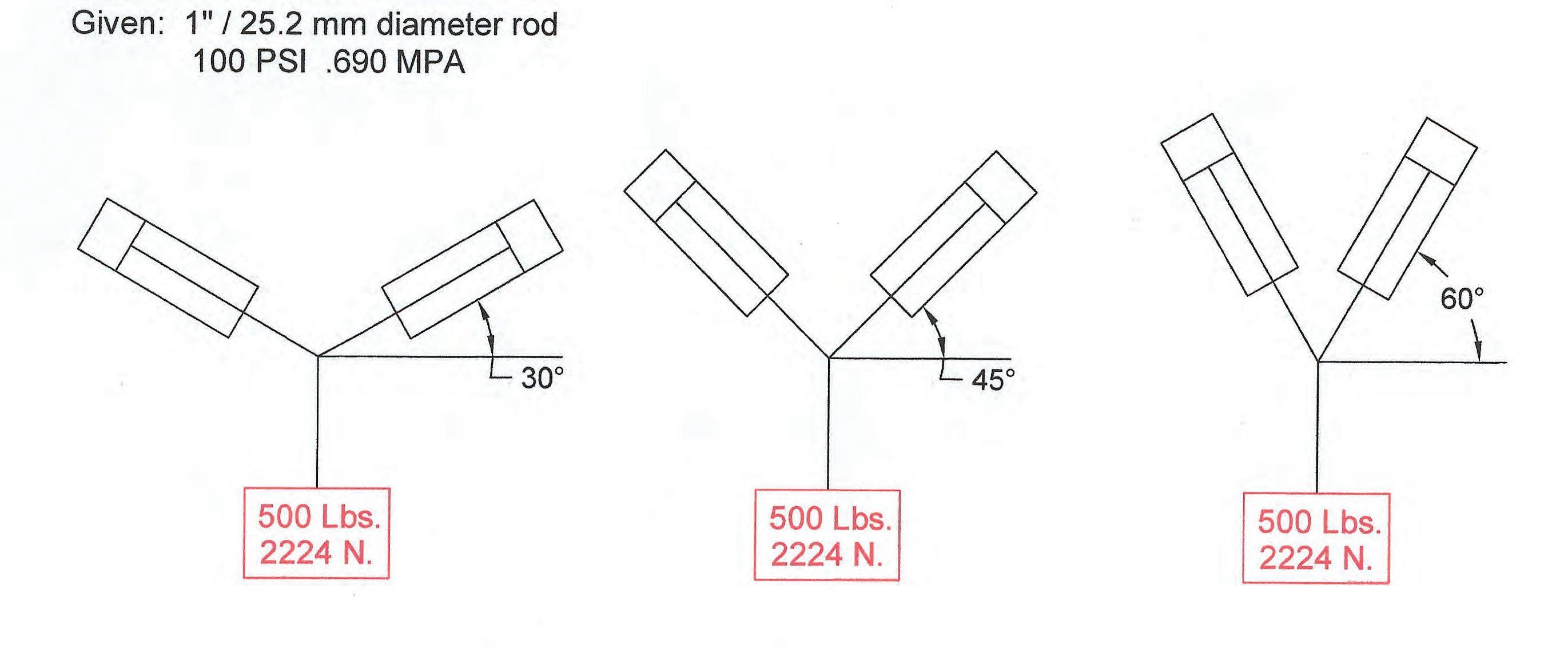
18 minute read
Air Teaser
PUBLISHER Innovative Designs & Publishing, Inc.
3245 Freemansburg Avenue, Palmer, PA 18045-7118 Tel: 800-730-5904 or 610-923-0380 Fax: 610-923-0390 • Email: Art@FluidPowerJournal.com www.FluidPowerJournal.com
Founders: Paul and Lisa Prass Associate Publisher: Bob McKinney Editor: Michael Degan Technical Editor: Dan Helgerson, CFPAI/AJPP, CFPS, CFPECS, CFPSD, CFPMT, CFPCC - CFPSOS LLC Director of Creative Services: Erica Montes Account Executive: Norma Abrunzo Accounting: Donna Bachman, Sarah Varano Circulation Manager: Andrea Karges
INTERNATIONAL FLUID POWER SOCIETY
1930 East Marlton Pike, Suite A-2, Cherry Hill, NJ 08003-2141 Tel: 856-489-8983 • Fax: 856-424-9248 Email: AskUs@ifps.org • Web: www.ifps.org
2021 BOARD OF DIRECTORS
President: Rocky Phoenix, CFPMMH - Open Loop Energy, Inc.
Immediate Past President: Jeff Kenney, CFPMHM, CFPIHM, CFPMHT - Dover Hydraulics South First Vice President: Denis Poirier, Jr., CFPAI/AJPP, CFPHS, CFPIHM, CFPCC - Eaton Corporation Treasurer: Jeff Hodges, CFPAI/AJPP, CFPMHM - Altec Industries, Inc.
Vice President Certification: James O’Halek, CFPAI/AJPP, CFPMIP, CMPMM - The Boeing Company Vice President Marketing: Scott Sardina, PE, CFPAI, CFPHS Waterclock Engineering Vice President Education: Randy Bobbitt, CFPAI, CFPHS Danfoss Power Solutions
Vice President Membership: John Bibaeff, PE, CFPAI, CFPE, CFPS
DIRECTORS-AT-LARGE
Chauntelle Baughman, CFPHS - OneHydraulics, Inc. Stephen Blazer, CFPE, CFPS, CFPMHM, CFPIHT, CFPMHT Altec Industries, Inc. Randy Bobbitt, CFPAI, CFPHS - Danfoss Power Solutions Steve Bogush, CFPAI/AJPP, CFPHS, CFPIHM - Poclain Hydraulics Cary Boozer, PE, CFPE - Motion Industries, Inc. Lisa DeBenedetto, CFPS - GS Global Resources Daniel Fernandes, CFPECS, CFPS - Sun Hydraulics Brandon Gustafson, PE, CFPE, CFPS, CFPIHT, CFPMHM - Graco, Inc. Garrett Hoisington, CFPAI/AJPP, CFPS, CFPMHM Open Loop Energy Brian Kenoyer, CFPHS - Five Landis Corp. Jon Rhodes, CFPAI, CFPS, CFPECS - CFC Industrial Training Mohaned Shahin, CFPS - Parker Hannifin Randy Smith, CFPHS - Northrop Grumman Corp.
EXECUTIVE DIRECTOR (EX-OFFICIO)
Donna Pollander, ACA
HONORARY DIRECTORS (EX-OFFICIO)
Paul Prass, Fluid Power Journal Liz Rehfus, CFPE, CFPS Robert Sheaf, CFPAI/AJPP, CFC Industrial Training
IFPS STAFF
Executive Director: Donna Pollander, ACA
Communications Director: Adele Kayser Technical Director: Thomas Blansett, CFPS, CFPAI Assistant Director: Stephanie Coleman
Certification Coordinator: Kyle Pollander Bookkeeper: Diane McMahon Administrative Assistant: Beth Borodziuk
Fluid Power Journal (ISSN# 1073-7898) is the official publication of the International Fluid Power Society published monthly with four supplemental issues, including a Systems Integrator Directory, OffHighway Suppliers Directory, Tech Directory, and Manufacturers Directory, by Innovative Designs & Publishing, Inc., 3245 Freemansburg Avenue, Palmer, PA 18045-7118. All Rights Reserved. Reproduction in whole or in part of any material in this publication is acceptable with credit. Publishers assume no liability for any information published. We reserve the right to accept or reject all advertising material and will not guarantee the return or safety of unsolicited art, photographs, or manuscripts.
New Problem:
Calculate Diameters of Load-Holding Cylinders
By Ernie Parker, CFPAI, CFPSD, CFPS, CFPMM, CFPMT, CFPMIP, CFPMMH, CFPMIH, CFPE
»CALCULATE THE REQIRED diameter and standard diameter needed for the cylinders to hold the load shown below.
The solution will be published in the February 2022 issue of Fluid Power Journal.
Solution to the June 2021 problem:
Find the Cylinder Rod
We need to find a solution where the resistance would produce a pressure of 1 psi for each hp. 60 mph = 88 feet / sec. 1 hp = ? lbs. of pull x 88 / 550 1 hp = 6.25 lbs. of pull 3” diameter cylinder = 7.068 sq. in. Since 1 hp = 1 psi, then 6.25 lbs. requires 6.25 sq. in (effective rod-end area) 7.068 – 6.25 = .818 sq. in. of rod A = D² x .7854
Working backward, rod diameter = 1. inches.
Visit www.fluidpowerjournal.com/air-teaser to view previous problems.
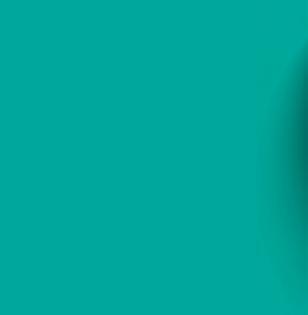

Wise UpWISE UP
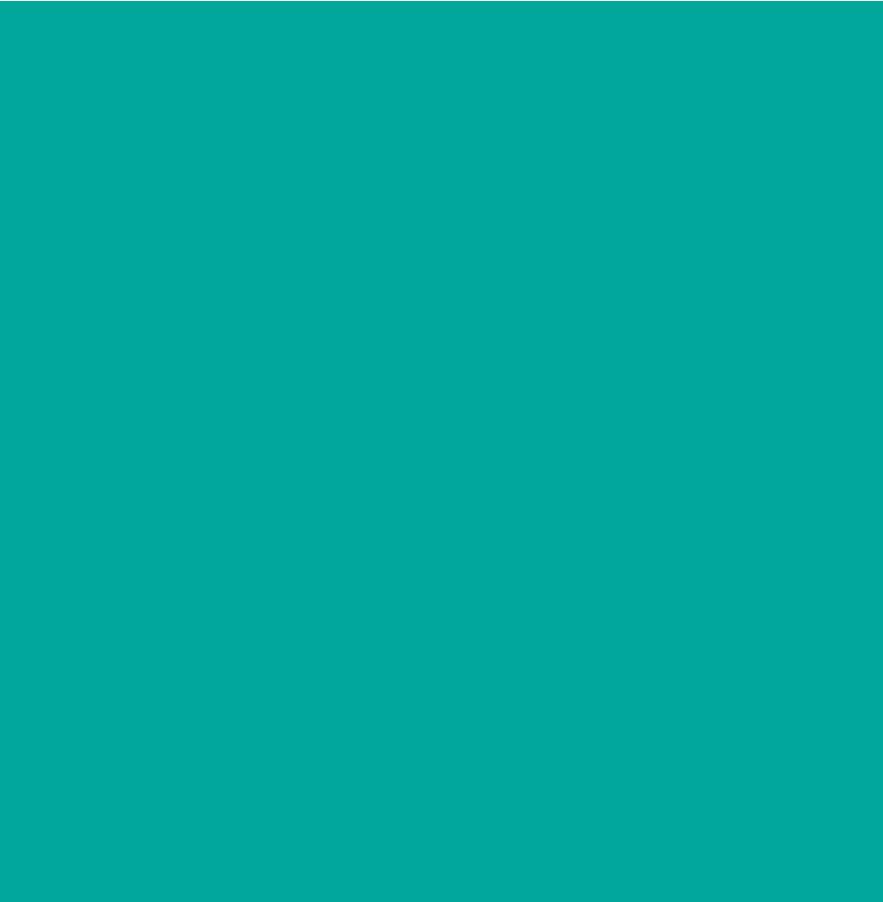
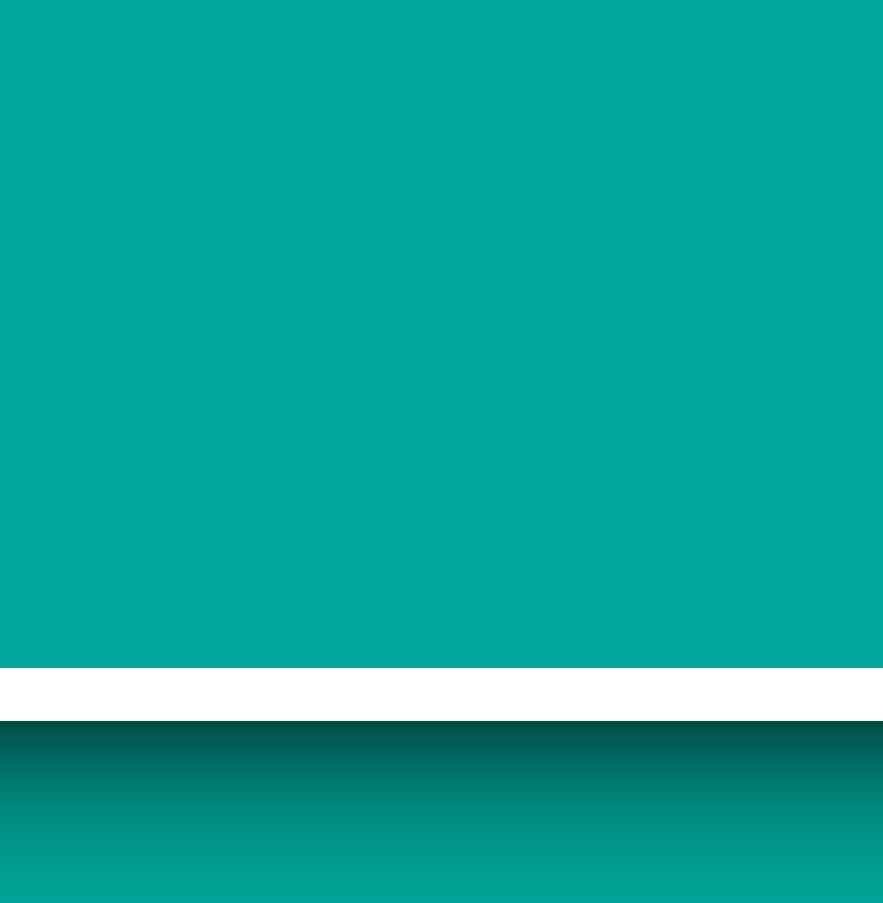
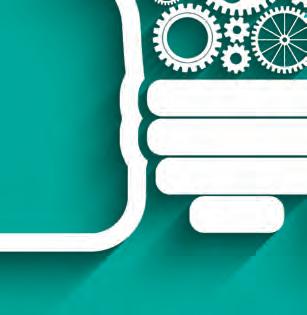
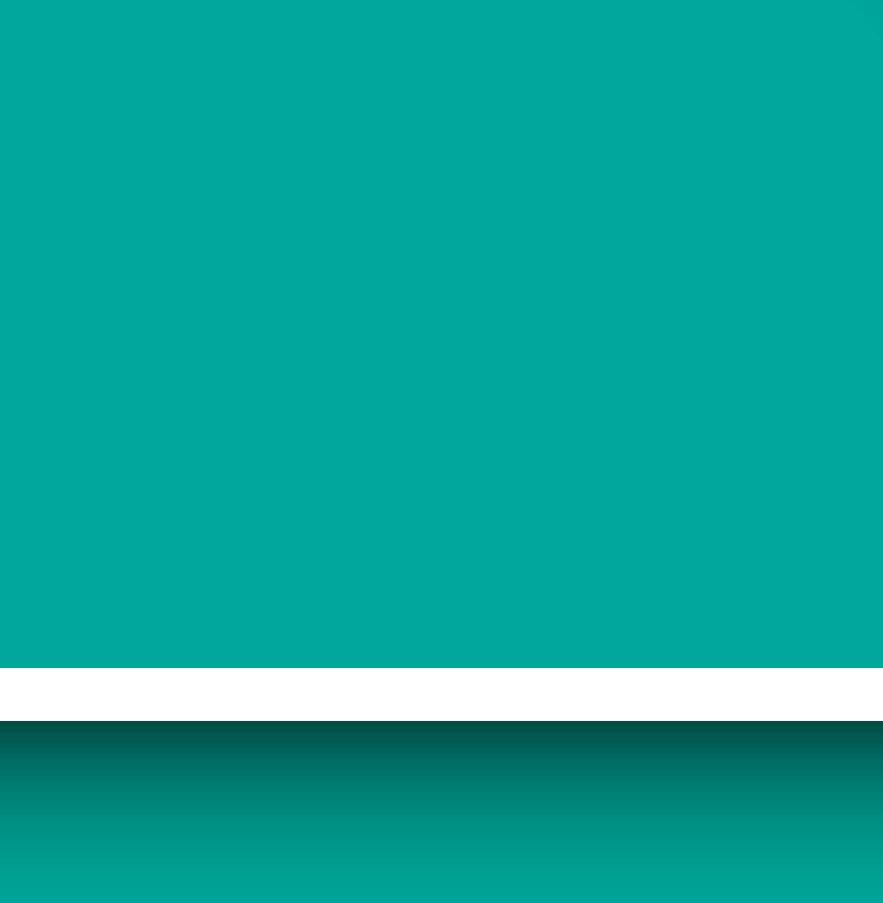
The Future of Fluid Power Is Smart
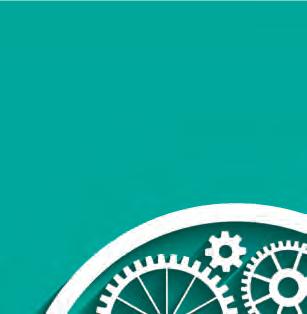

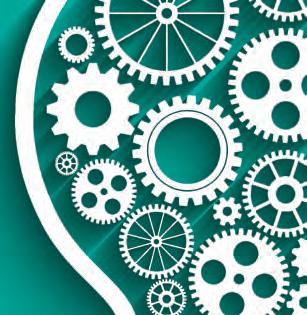
By Kevin P. Vanderslice, Director of Sales, ifm efector
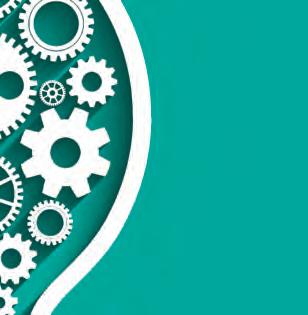
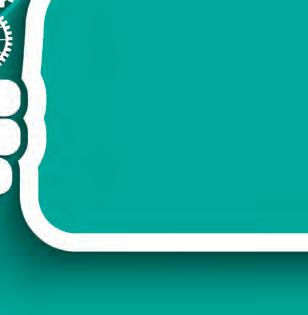
Digital transformation and Industry 4.0 are common buzz words these days. They focus on real-time data and auto- mation. But how should we approach this?
The manufacturing industry generates more data than any other sector of the economy, and because of all this data, companies are making analytics a priority. In a recent General Electric survey, 42% of manufacturers have said “big data” is the top priority, and another 45% said it is one of the three highest priorities. Digital transformation is happening in three waves.
Wave 1. The waters that most of us have navigated in recent decades are in wave 1. It is the classic ownership model, i.e., a customer pays a one-time price for a machine or after-sales service. As the OEM, you provide a warranty for a limited amount of time, and any service work beyond that follows the classic model of dispatching a technician or bringing in the vehicle for maintenance or repairs.
Wave 2. In wave 2’s usage-based model, a customer pays to use a machine but does not own it. Uptime becomes more critical. The customer simply may not pay you if the machine is not performing 100%. Insight into the machine’s operation to detect early wear and tear becomes a necessity. With that information, you can plan maintenance and repairs during scheduled downtime.
Wave 3. In this final stage, wave 3 evinces an outcome-based model in which the customer pays only for the finished product. Frankly, he could care less which machine you used to get there. But as you are responsible for the final product, so a full understanding of machine health and product quality is critical. The classic consumer example of this third wave is the ride-sharing service Uber. Suddenly, owning a car is not necessary; getting from A to B is all that matters, which also testifies to the impact that Uber’s transformation has had on the automotive industry. How does digital transformation apply to industry?

Here are some examples.
1. Aircraft deicers at airports have a serious impact on airline operations. To avoid bottlenecks, stops to refill trucks with the deicing fluid are staggered. This requires a real-time view of current liquid levels in each truck. Additionally, tracking the usage per aircraft may be mandated by the FAA.
2. Refuse collection vehicles are constrained by weight and cycle time. Improving the speed of pickups and optimizing capacity enables trucks to pick up more refuse in less time. This is only possible by accurately measuring key body data and preventing unplanned maintenance.
3. Mobile drill rigs are a good example of highly complex on/off highway vehicles that utilize a large number of sensors and actuators. The operator must manage the drill operation as well as the safety zone of the drill head. Using
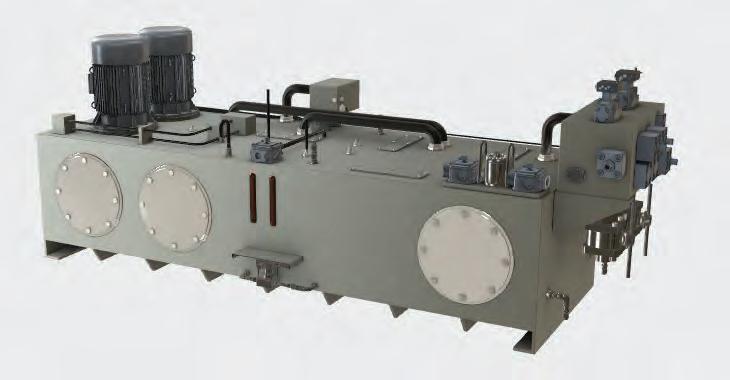
area surveillance to assist the operator with these tasks and display the parameters in the cab significantly improves the working conditions and safety of the job site.
4. What if farm equipment automatically identified weeds or pests and eradicated them? Besides efficiency and cost reductions, the decreased use of crop-protection chemicals and reduced emissions into the environment show the advantages of this technology, which could ultimately eradicate harmful substances from farming.
5. The traffic of cargo vessels in ports is tightly scheduled. There is little time to load or unload cargo. Automated guided vehicles have simplified and quickened the transportation of containers by knowing where and when to pick up the freight. Automated machines are helping the fast-growing needs of the ship-to-shore industry. The smart factory
Industry 4.0 is often referred to as the fourth industrial revolution and represents a new stage in the organization and control of the industrial value chain. In manufacturing, Industry 4.0’s modern control systems and smart sensors have resulted in what is often called the “smart factory.” IoT devices in smart factories lead to higher productivity and improved quality. With minimal investment, quality-control personnel can monitor manufacturing processes from virtually anywhere by connecting a smartphone to the cloud. By applying machine learning algorithms, manufacturers can detect errors immediately, rather than at later stages when repair work is more expensive.
In the industrial world, while Industry 4.0 is influencing overall equipment effectiveness, there are multiple areas where there could be improvement, including: • Machine availability – reducing planned and unplanned stoppages. • Machine performance – eliminating slow cycles and small stops. • Product quality – reducing levels of scrap, defects, and rework. • Energy optimization – preventing air or vapor leaks. •Environmental impact – improving pollution control. Let’s look at two examples.
Air compressor
• Machine availability. Vibration sensors monitor the pump health to prevent catastrophic failure and loss of availability. You can monitor five key areas of machine problems: impact, fatigue, friction, severity, and temperature. Monitoring this data in real time allows the sensors to predict pending failures and limit catastrophic damage. • Machine performance. Compressed air leaks cause compressors to work harder and produce more air than needed. Flowmeters reliably measure compressed air flow, pressure, temperature, and total consumption, alerting users to leaks that reduce compressor performance. • Product quality. Using sensing elements that measure accurately, users can attain precise control of the compressed air system, maintaining quality. • Energy optimization. Vibration analysis sensors allow for monitoring compressor performance and provide alerts when pumps are operating inefficiently and wasting energy.
Hydraulic power unit
• Machine availability. Particulate contamination in hydraulic oil can lead to sticking or accelerated mechanical wear of system components. Reliable oil-cleanliness sensors can measure particle size and distribution and alert users before the particle contamination reaches a critical level. • Machine performance. As a hydraulic pump wears over time, more hydraulic oil leaks past the pump seals to the case drain. Flowmeters can reliably measure the flow of case drain oil, providing real-time feedback on diminishing pump performance. • Product quality. Over time, water can get into a hydraulic system, causing corrosion, increasing oxidation, and leading to the inaccurate position of system components like valves. Humidity sensors can monitor the level of moisture in hydraulic oil and alert users when it reaches a critical level. This eliminates improper positioning of hydraulic devices, ensuring quality output. • Energy optimization. Vibration sensors monitor pump performance and provide alerts when pumps are operating inefficiently, wasting energy. • Environmental impact. Without accurate sensing technology, false levels may fail to indicate overflowing hydraulic oil that can potentially impact the environment. Capacitive point level technology with no moving parts can provide reliable detection of overflow conditions. What does the future look like?
Consider some predictions. • With real-time maintenance, data from machine sensors predicts which maintenance activities should be performed on the machine and when. This can be as simple as time-based maintenance decisions or as complex as using powerful analytical models to predict component wear and tear. • Instead of operator fatigue being measured in hours of work or jobs completed, performance is measured based on operator alertness with the assistance of camera technology. • An operator score card allows for increased safety, efficiency, a drop in insurance rates, and should, at the same time, increase overall job satisfaction. • Tracking technology verifies that the correct tool is used for its purpose and location. Additionally, it ensures that expensive assets are not left on the job site and that the machine with the proper tools is deployed to a job site. • Real-time diagnostics eliminate the need to deploy service technicians with laptops. Instead, critical data empowers an operator or engineer to evaluate, analyze, and troubleshoot problems. Making history
Digital transformation allows machine builders to reimagine how they design, manufacture, and service equipment. While Industry 4.0 is still evolving, companies that are currently adopting new technologies realize its potential. These companies upskill their workforce to take on the responsibilities made possible by IoT, and they recruit new employees with the right skills.
We might not have the complete picture until we look back in 30 years. But for now, we’re making history! •
The
Factor
By Tony Casassa, Engineering Manager, Aggressive Hydraulics WOW
Hydraulic Cylinders in Entertainment
When thinking about hydraulic cylinders, typically the first applications that come to mind are construction equipment like excavators and dump trucks or industrial applications like presses. However, a relatively unknown hydraulic application is entertainment. Except for fluid power enthusiasts, most people would not buy a ticket simply to watch a hydraulic cylinder extend and retract. However, hydraulic cylinders work behind the scenes to provide linear motion for amusement parks, animatronics, live shows, and other entertainment venues. These cylinders have much in common with their more utilitarian cousins, but they often have unique features to meet the requirements of the entertainment industry.
One common requirement is the need for reliability. If the hydraulic cylinder on a dump truck fails, the owner of the dump truck loses revenue during the time the truck is inoperable and not hauling loads. In the same way, if an entertainment venue must cancel a show because of cylinder failure, there is a loss of revenue from ticket sales. So cylinders for entertainment must be designed for a high level of reliability because, as the old saying goes, “the show must go on!” Welded-type cylinders provide a high level of integrity through numerous pressure cycles, even in high-vibration environments. They can also be easily disassembled to replace the seals or perform other service work, a task that is even simpler with bolted head glands.
One specific area of reliability is the rod sealing system. Although rod-seal leaks are never desirable, some users of mobile and industrial equipment tolerate a certain amount of leakage on a machine that may already be greasy or dirty. At an entertainment venue, cleanliness has a high level of importance to the patrons and, by extension, the owner. So there is little tolerance for unsightly leaks that may form a puddle on the ground, create an oil slick on the water, or become a collection point for dust and debris. The cylinder must be designed with highly efficient seals that endure many cycles and wipe the rod clean before it extends. The rod wiper must keep out contamination that may damage the rod seal. In some cases, a buffer seal may be added to dampen any pressure spikes from reaching the main rod seal, extending seal life. A leak detection port may be added to indicate if the rod seal has been compromised. This port could be used for a visual sight gauge, electrical pressure switch, or drain tube to a holding reservoir. Any of these methods can be used to alert maintenance personnel when it is necessary to schedule repair downtime. The leak detection port is especially valuable when the cylinder is used in or around water.
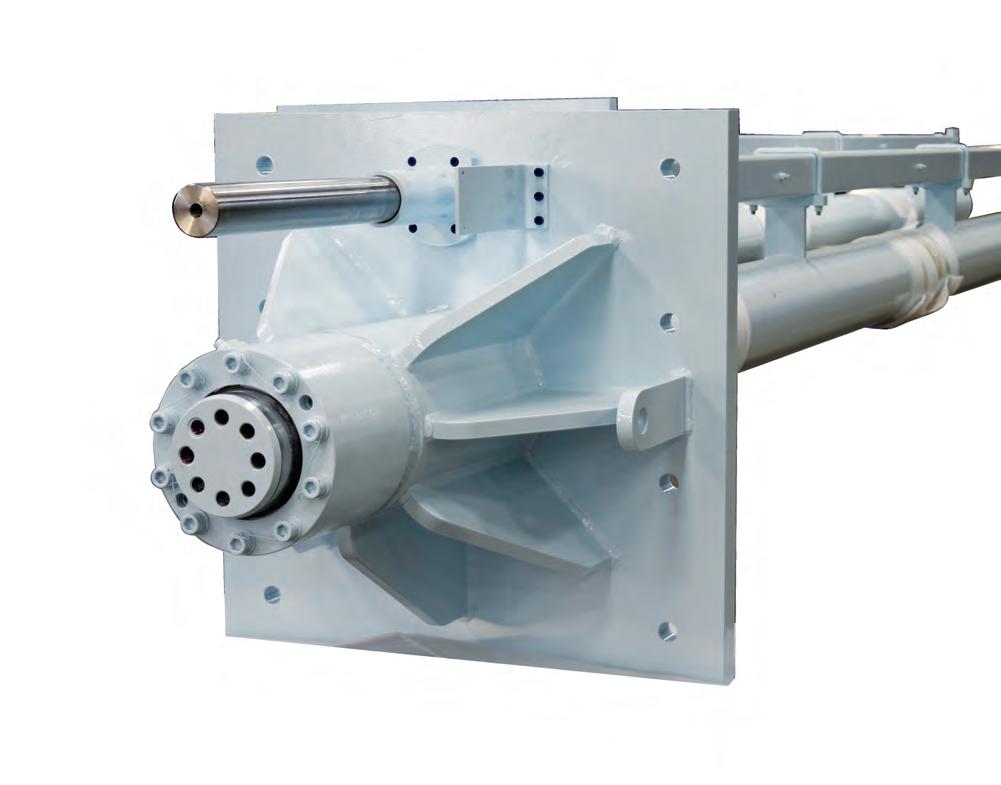
Hydraulic cylinder for an underwater stage.
Challenges presented by water
Seventy-two percent of the earth is covered by water, and water is also a common feature in the entertainment world. From fountains to water features on rides to wave pools, H2O is ubiquitous because people find water fascinating. Water poses two primary threats to hydraulic cylinders: corrosion and water ingression. Carbon steel or ductile iron, common raw materials for cylinder components, are prone to rust in the presence of water. This rust is not only unsightly, over time it weakens the material and can result in failure. Fortunately, there are solutions to combat this problem. For the barrel or body of the cylinder, corrosion can be slowed by special paint finishes, for example, inorganic zinc primers or two-part marine-grade epoxy. If that is not adequate, nickel plating the exterior components provides an even more robust barrier than paint. Although typically not viable on large cylinders due to cost and material availability, smaller cylinders can be manufactured from stainless steel and bronze to inhibit corrosion.
Closeup of the hydraulic cylinder developed for an underwater stage.
Animatronics cylinder engineered by Aggressive Hydraulics.

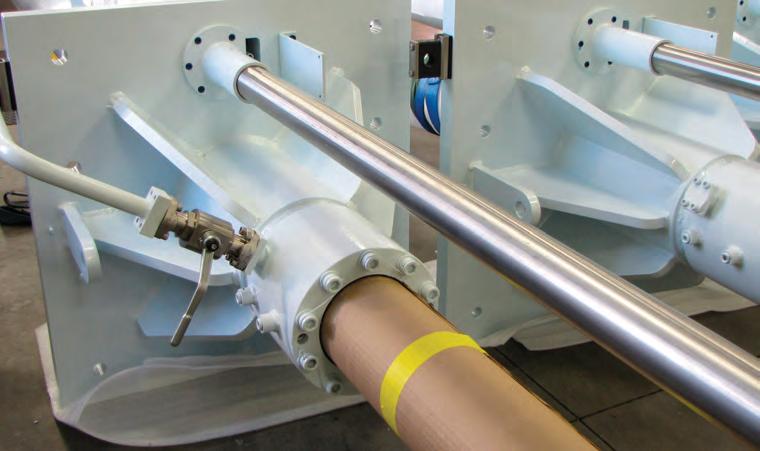
The cylinder rod, which is typically chromeplated carbon steel, presents a unique challenge for corrosion protection. Chrome is a hard surface that is compatible with the rod seals, and chrome also provides a limited amount of corrosion protection. Chrome itself is resistant to rust, but it has microscopic cracks that let moisture penetrate to the base material, allowing it to rust and lift off the chrome plating. The options for the cylinder case are not viable for the rod; paint would strip off when the rod cycles, and nickel plating is too soft. There are viable solutions, including chrome application methods that significantly reduce the microcracks and form a stronger barrier to protect the base material. A different option is to plate the rod with a layer of nickel plating below the chrome, as the nickel provides corrosion resistance, and the chrome provides a smooth, hard surface for the seals. Instead of trying to protect the base material, yet another strategy is chrome-plated stainless steel, in which the chrome only provides the surface for the seals and the base material is resistant to corrosion. Although 300-series stainless steel provides more corrosion resistance, 17-4 stainless is typically used for the combination of good corrosion resistance and high tensile strength. The drawback of stainless steel, whether for the barrel or the rod, is higher cost and lower material availability, especially in larger diameters.
Corrosion is not water’s only threat to hydraulic cylinders, which are typically designed only with seals to keep in the high-pressure fluid. If the cylinder is submerged or splashed, water can find a way inside the cylinder and mix with the hydraulic fluid. This contamination can result in fluid breakdown and internal rust of the cylinder and other hydraulic system components. Special seal configurations prevent this water ingression. An additional rod seal turned outboard to seal against the rod can prevent water from entering the rod gland. Because the seal material typically used for hydraulic fluid often swells or softens when exposed to water, the outboard seal should be a compound compatible with water. Protecting electrical sensors
Watery environments can also pose a threat to the linear position sensors that are often integrated in cylinders. There has been a significant trend in all types of machines and equipment to add electrical sensors and controllers, and hydraulic cylinders for entertainment reflect the same trend. One application is multiple cylinders working together to raise and lower an underwater stage. An integral linear position
(Continued on page 10)
Don’t compromise!
Use MAIN Manufacturing Products, Inc. as your source for hydraulic flanges
Dependable - 60 yrs service Informed - members of SAE, ISO, & NFPA tech committees
Quick - Thousands in stock specials can be 3-4 days
Made in USA
SAE J518, JIS, DIN, ISO, standard & special adapters Socket & Butt weld, NPTF, BSPT, ORB, BSPP, 6149, ETC. In-line, el, tee, F, blind, cross, cross, flanged, reducing, flange heads, couplings
Materials: Carbon, 304L, 316L, Duplex, Cu-NI, Ductile, Aluminum, etc.
Grand Blanc, MI USA
Rendering of an animatronics cylinder.
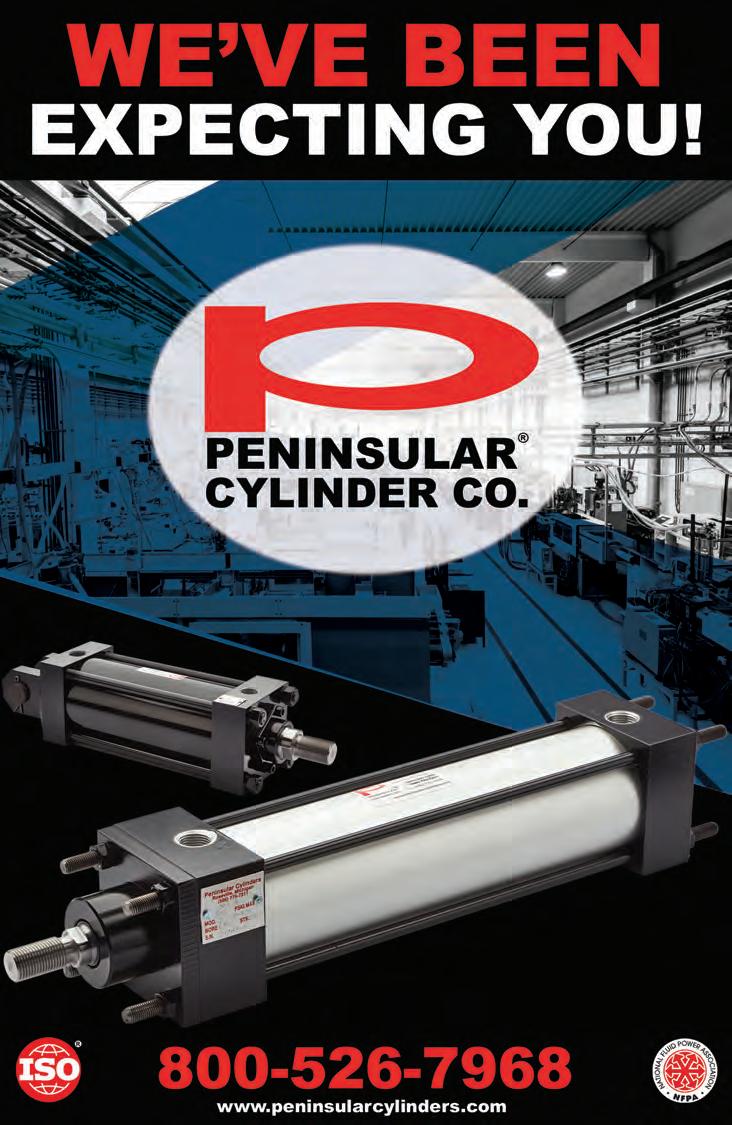
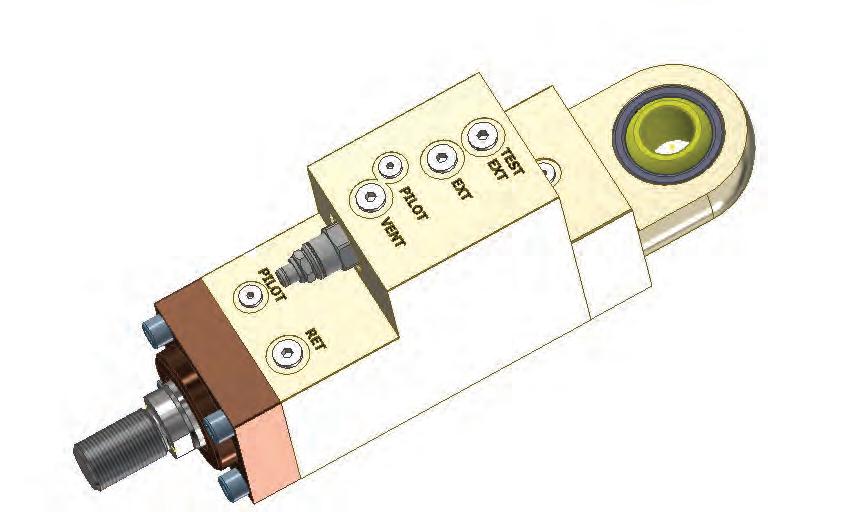
sensor can enable synchronization of the cylinders and provide an alarm notification if the stage is out of position. Although current standard sensor offerings have reasonable water ingression protection for most environments, severe or submerged applications require nonstandard configurations. In the example of the underwater stage, the sensor is protected by a custom-designed sealed enclosure with a cord grip for the terminating cable. In another example, that of animatronics cylinders that bring full-sized characters to life, specialized connectors designed for subsea environments are used to maintain electrical reliability. The job of these connectors is to transmit the output signal from the sensor integrated in the cylinder. Sometimes these outputs are common analog or digital outputs, but other cases require unique outputs. Often the controllers are highly specialized, as they go beyond typical motion control and also manage lighting and sound for the ride or show. They may require special sensor outputs like PWM – pulse width modulated. In other cases, the system may have been designed years ago with a specific type of resistive sensor that is no longer available. Because of the cost and the high level of integration, changing the electronic controller is not a viable solution. So a replacement cylinder must be designed with a sensor to provide the same feedback. This level of customization is not limited to the sensor.
Hydraulic cylinders range from standard offthe-shelf products to catalog options and highly customized types. In the case of an off-the-shelf cylinder, the customer must design the machine around the standard product or modify as needed. Catalog cylinders provide more options but are still limited to the predetermined configurations offered by the manufacturer. Custom-welded cylinders provide a high level of design flexibility, which is very important in many entertainment applications that require unique solutions. One example is a cylinder to generate waves in a pool at a water park. The duty cycle demand is high, as the cylinder operates continuously every day from open to close, and the tolerance for leakage of oil into the pool water is low. Therefore, the cylinder is designed to prevent fatigue failure and includes a dual seal and leak-detection port configuration. Although not submerged, the proximity to water requires corrosion protection features, including chrome-plated stainless steel rod, epoxy paint, and salt bath nitride head gland.
The next time you visit an amusement park, live show, or even a sports event, keep your eye out for hydraulic cylinders at work behind the scenes to entertain the audience. •