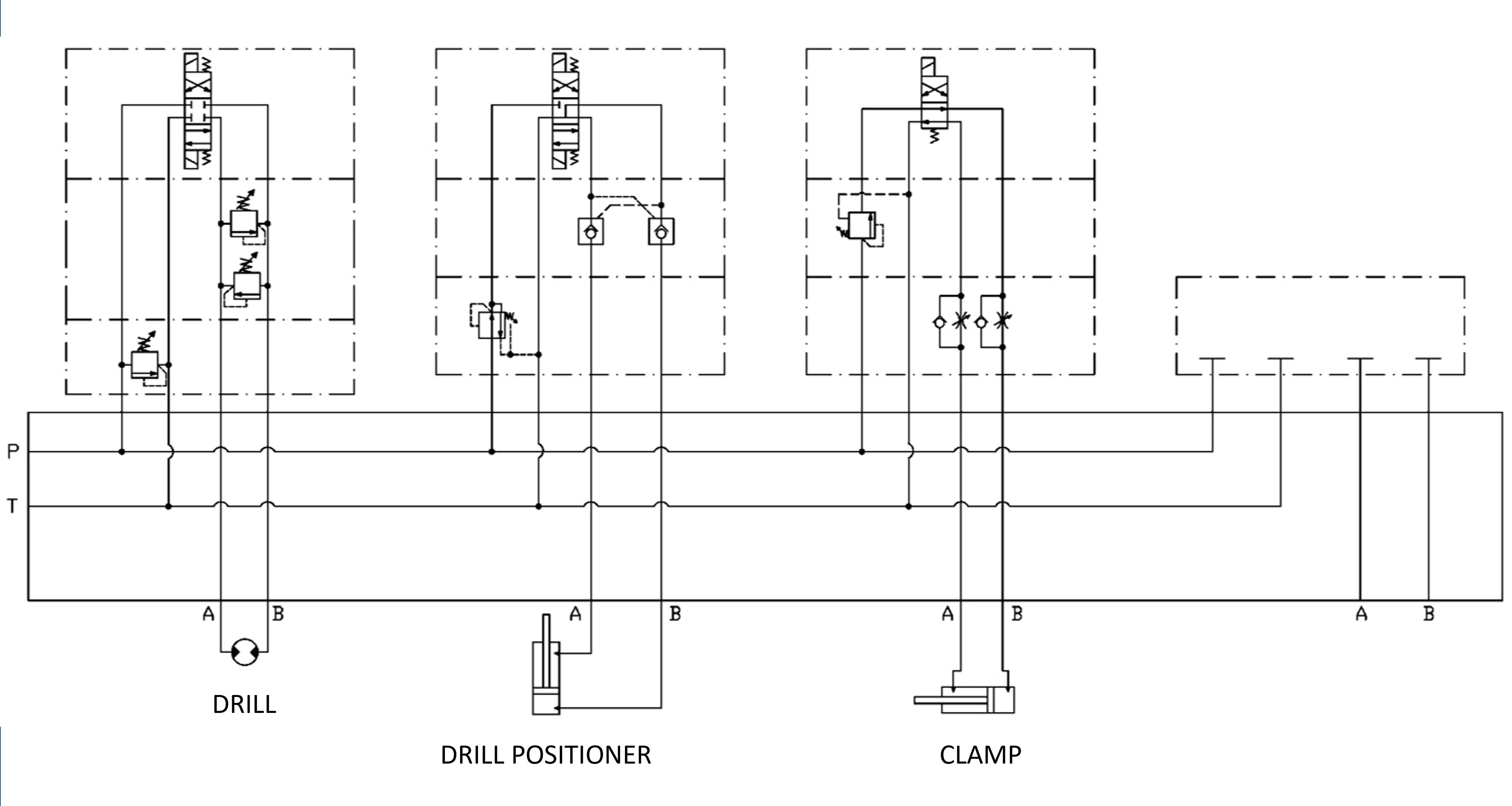
23 minute read
Figure It Out
PUBLISHER Innovative Designs & Publishing, Inc.
3245 Freemansburg Avenue, Palmer, PA 18045-7118 Tel: 800-730-5904 or 610-923-0380 Fax: 610-923-0390 • Email: Art@FluidPowerJournal.com www.FluidPowerJournal.com
Founders: Paul and Lisa Prass Associate Publisher: Bob McKinney Editor: Michael Degan Technical Editor: Dan Helgerson, CFPAI/AJPP, CFPS, CFPECS, CFPSD, CFPMT, CFPCC - CFPSOS LLC Director of Creative Services: Erica Montes Account Executive: Norma Abrunzo Accounting: Donna Bachman, Sarah Varano Circulation Manager: Andrea Karges
INTERNATIONAL FLUID POWER SOCIETY
1930 East Marlton Pike, Suite A-2, Cherry Hill, NJ 08003-2141 Tel: 856-489-8983 • Fax: 856-424-9248 Email: AskUs@ifps.org • Web: www.ifps.org
2021 BOARD OF DIRECTORS
President: Rocky Phoenix, CFPMMH - Open Loop Energy, Inc.
Immediate Past President: Jeff Kenney, CFPMHM, CFPIHM, CFPMHT - Dover Hydraulics South First Vice President: Denis Poirier, Jr., CFPAI/AJPP, CFPHS, CFPIHM, CFPCC - Eaton Corporation Treasurer: Jeff Hodges, CFPAI/AJPP, CFPMHM - Altec Industries, Inc.
Vice President Certification: James O’Halek, CFPAI/AJPP, CFPMIP, CMPMM - The Boeing Company Vice President Marketing: Scott Sardina, PE, CFPAI, CFPHS Waterclock Engineering Vice President Education: Randy Bobbitt, CFPAI, CFPHS Danfoss Power Solutions
Vice President Membership: John Bibaeff, PE, CFPAI, CFPE, CFPS
DIRECTORS-AT-LARGE
Chauntelle Baughman, CFPHS - OneHydraulics, Inc. Stephen Blazer, CFPE, CFPS, CFPMHM, CFPIHT, CFPMHT Altec Industries, Inc. Randy Bobbitt, CFPAI, CFPHS - Danfoss Power Solutions Steve Bogush, CFPAI/AJPP, CFPHS, CFPIHM - Poclain Hydraulics Cary Boozer, PE, CFPE - Motion Industries, Inc. Lisa DeBenedetto, CFPS - GS Global Resources Daniel Fernandes, CFPECS, CFPS - Sun Hydraulics Brandon Gustafson, PE, CFPE, CFPS, CFPIHT, CFPMHM - Graco, Inc. Garrett Hoisington, CFPAI/AJPP, CFPS, CFPMHM Open Loop Energy Brian Kenoyer, CFPHS - Five Landis Corp. Jon Rhodes, CFPAI, CFPS, CFPECS - CFC Industrial Training Mohaned Shahin, CFPS - Parker Hannifin Randy Smith, CFPHS - Northrop Grumman Corp.
EXECUTIVE DIRECTOR (EX-OFFICIO)
Donna Pollander, ACA
HONORARY DIRECTORS (EX-OFFICIO)
Paul Prass, Fluid Power Journal Liz Rehfus, CFPE, CFPS Robert Sheaf, CFPAI/AJPP, CFC Industrial Training
IFPS STAFF
Executive Director: Donna Pollander, ACA
Communications Director: Adele Kayser Technical Director: Thomas Blansett, CFPS, CFPAI Assistant Director: Stephanie Coleman
Certification Coordinator: Kyle Pollander Bookkeeper: Diane McMahon Administrative Assistant: Beth Borodziuk
Fluid Power Journal (ISSN# 1073-7898) is the official publication of the International Fluid Power Society published monthly with four supplemental issues, including a Systems Integrator Directory, OffHighway Suppliers Directory, Tech Directory, and Manufacturers Directory, by Innovative Designs & Publishing, Inc., 3245 Freemansburg Avenue, Palmer, PA 18045-7118. All Rights Reserved. Reproduction in whole or in part of any material in this publication is acceptable with credit. Publishers assume no liability for any information published. We reserve the right to accept or reject all advertising material and will not guarantee the return or safety of unsolicited art, photographs, or manuscripts.
New Problem
Valve Flaw Leads to Faulty Pressures
By Robert Sheaf, CFPAI/AJPP, CFPE, CFPS, CFPECS, CFPMT, CFPMIP, CFPMMH, CFPMIH, CFPMM CFC Industrial Training
»THE CIRCUIT BELOW was working for several years when the pressure-reducing valve on the clamp cylinder started leaking oil into an assembly bolt cavity. It appeared that a casting flaw finally failed after thousands of pressure cycles. The company purchased and installed a new module. However, the cap end would see full system pressure crushing the product while the rod side pressure would see reduced pressure as designed.
Maintenance returned the valve and replaced it with a new one, but it had the same problem. They examined the old valve and confirmed the new ones had the same model number as the failed one.
What was the problem?
Solution to the September 2021 problem:
Regenerative Circuit Drops Out
The regen circuit that did not work properly until the hinged fixture arm was about halfway up was caused by the spring drain line connected internally. Any pressure in the spring chamber of pressure controls is additive to the valve’s pressure setting. The pressure needed to lift the hinged fixture continually decreased as the fixture was raised. Externally draining the rod side counterbalance valve solved the problem. To view previous problems, visit www. fluidpowerjournal.com/figure-it-out.
M
Robert Sheaf has more than 45 years troubleshooting, training, and consulting in the fluid power field. Email rjsheaf@cfc-solar.com or visit his website at www.cfcindustrialtraining.com.
By Tom Fistrovich, OEM and Mobile Market Business Development Manager, Des-Case Corporation
DAMAGE CONTROL
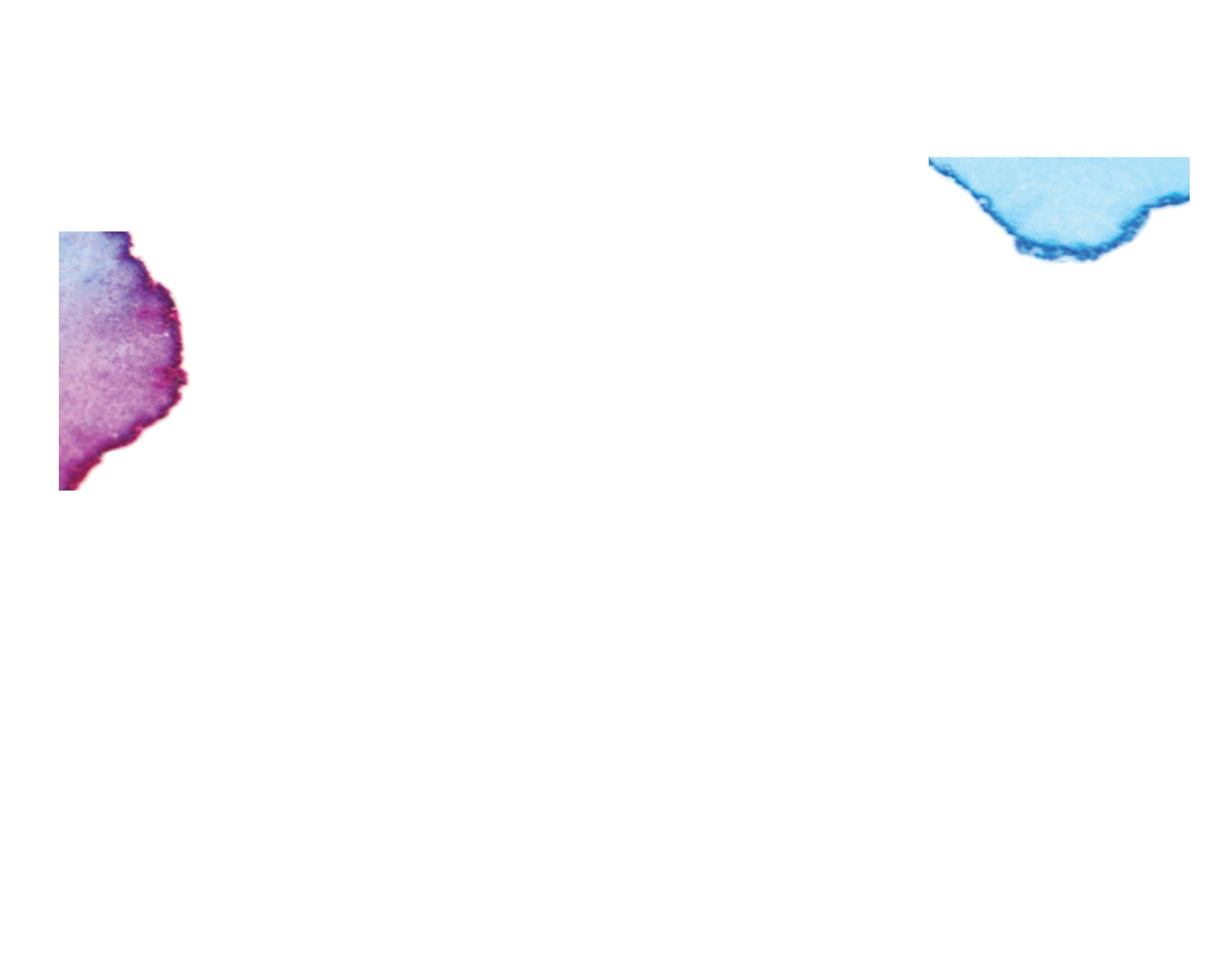
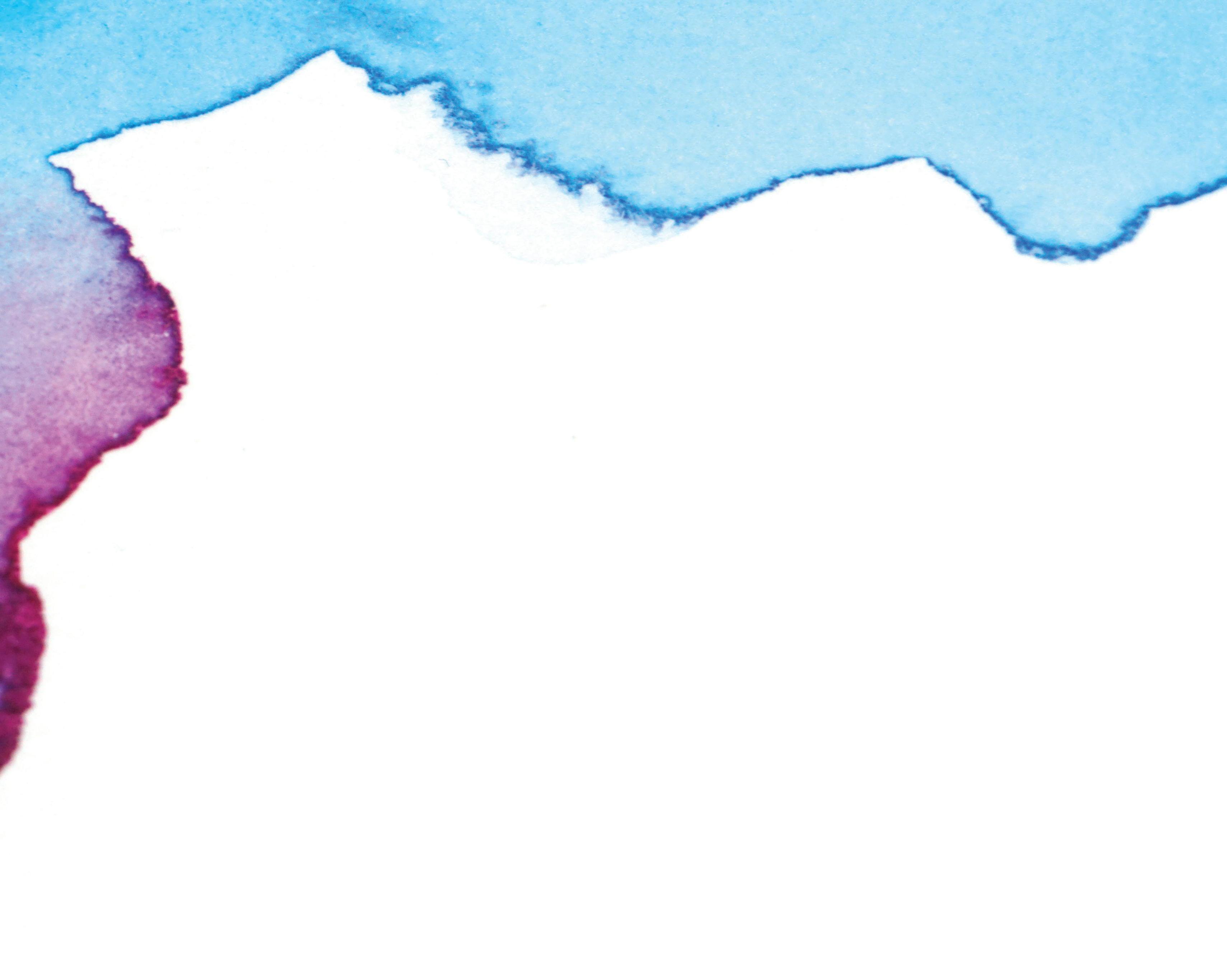
For companies that rely on mobile equipment as part of their normal operations, reduction in both downtime and overall maintenance costs is imperative to maintaining fleet efficiency and profitability. The harsh environments in which mobile equipment is typically used can make these reductions extremely challenging. On the drive side, there is an increasing trend toward electric drive versus conventional diesel powered. However, hydraulic systems continue to be a critical component in mobile equipment. While there are many aspects to maintaining a reliable hydraulic operation, contamination ingression in the form of particles and moisture is a major source of poor reliability, leading to underperformance, component damage, and hydraulic system failures.
Mobile equipment can be used and operated in some of the most challenging and contaminated working environments, including mine sites, agricultural plots, steel mills, oil fields, and many other applications. They all have one thing is common: unplanned downtime due to contamination affects operational efficiency and throughput, ultimately reducing the bottom line. Unfortunately, operating in these contaminated environments is unavoidable. Consumer demand for natural resources and products manufactured on these work sites continually increases.
But there is a way to reduce the negative impact of contamination on hydraulic systems in mobile equipment.
Most fluid power experts recognize that particle contamination is responsible for as much as 80% of mechanical machine wear in hydraulic systems. In light of these challenges, improving overall system cleanliness reduces hydraulic system failures, helping to increase equipment reliability while reducing the costs associated with maintenance and downtime. Fortunately, there is a surefire way to achieve this. Proactive maintenance of hydraulic fluid can extend the system life as much as five times. Extending hydraulic fluid and system life extends the time the mobile equipment is in use and doing its job.
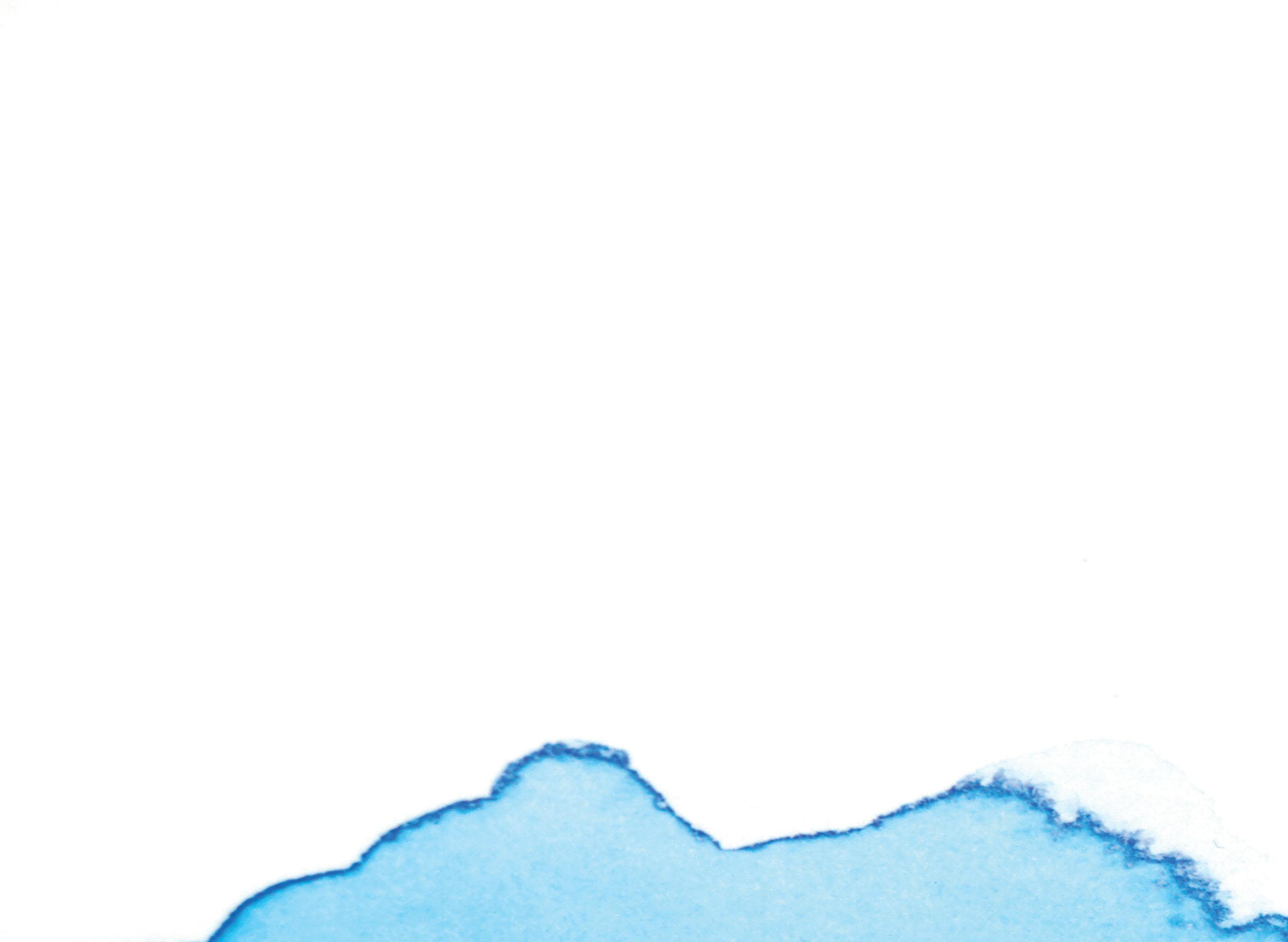
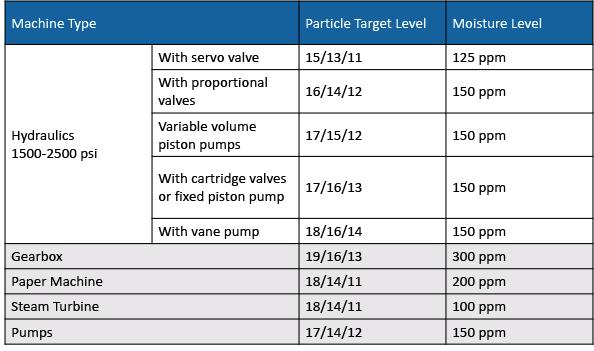
Figure 1: Fluid cleanliness target levels. (Recommended testing methods: optical particle count [ISO 11500] for both hard and soft particle counts; Karl Fischer method for moisture level.)
Figure 2: Measuring particle contamination in an oil.
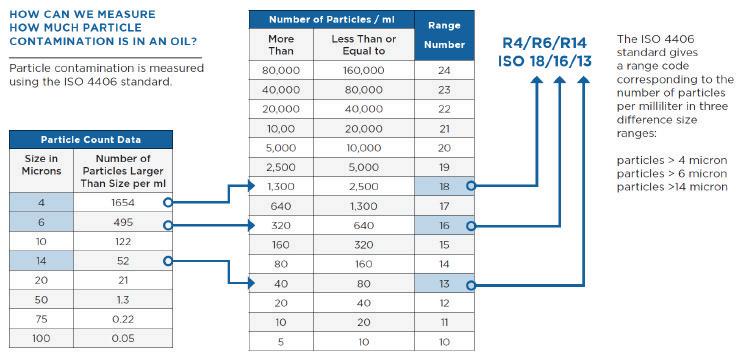
Setting a strategy
The first step is to establish a maximum target for fluid cleanliness using ISO 4406 or a similar fluid-cleanliness standard. Based on the sensitivity of hydraulic components like pumps and valves, different components can tolerate varied amounts of contamination. Knowing the sensitivity level allows equipment manufacturers and users to set target cleanliness levels. In fluid power systems, hydraulic pumps, motors, and valves typically drive the cleanliness requirements of the system, as these components are very sensitive to contamination and deposits. As shown in figure 1, a hydraulic system using a vane pump is less sensitive to the concentration of particle contamination than a system using a variable volume piston pump. Furthermore, the addition of servo valves to the system makes it even more sensitive to particle contamination. Knowing which components exist in your hydraulic system allows you to set a baseline cleanliness level at which the system should operate. A precision fluid contamination control strategy strives to achieve and maintain these baseline contamination levels.
Once the user determines a target cleanliness level, the next step is to consider a strategy to control the contamination and maintain system cleanliness to the target levels. A precision fluid contamination control strategy is the most holistic method to achieve and maintain the target levels. This method of proactive maintenance revolves around four areas: • Contamination prevention – sealing and protecting the system • Contamination removal – cleaning and purifying the fluid system • Fluid assessment – visual assessment and review of the fluid during operation • Fluid monitoring – using condition-based monitoring to diagnose fluid condition and contamination levels
Contamination prevention. Studies show that contamination exclusion in a system can cost 10 times less than contamination removal in the same system. This is one driving factor for implementing the first state of a precision strategy: contamination prevention. Mobile hydraulic systems have many points that potentially allow contamination ingression into the system. Common ingression points include the hydraulic cylinders and reservoirs. While contamination ingression at the hydraulic cylinders typically happens during operation or washdown, it is common for the hydraulic reservoir to experience contamination ingression during operation and service intervals.
Contamination prevention in a hydraulic system starts with assuring that the system’s hydraulic fluid meets the recommended ISO 4406 target cleanliness level. Hydraulic fluids can become contaminated even before they arrive on site. In fact, every transfer of the fluid can double its contamination level. New hydraulic fluid should be filtered prior to adding it to a system because most new hydraulic fluids are up to 16 times dirtier than typical cleanliness targets (see figure 2). Users should verify that they are adding the correct fluid to prevent cross-contamination. Whether the hydraulic fluid is stored in bulk tanks, left in drums, or stored into intermediate bulk containers, the storage system and dispensing equipment should
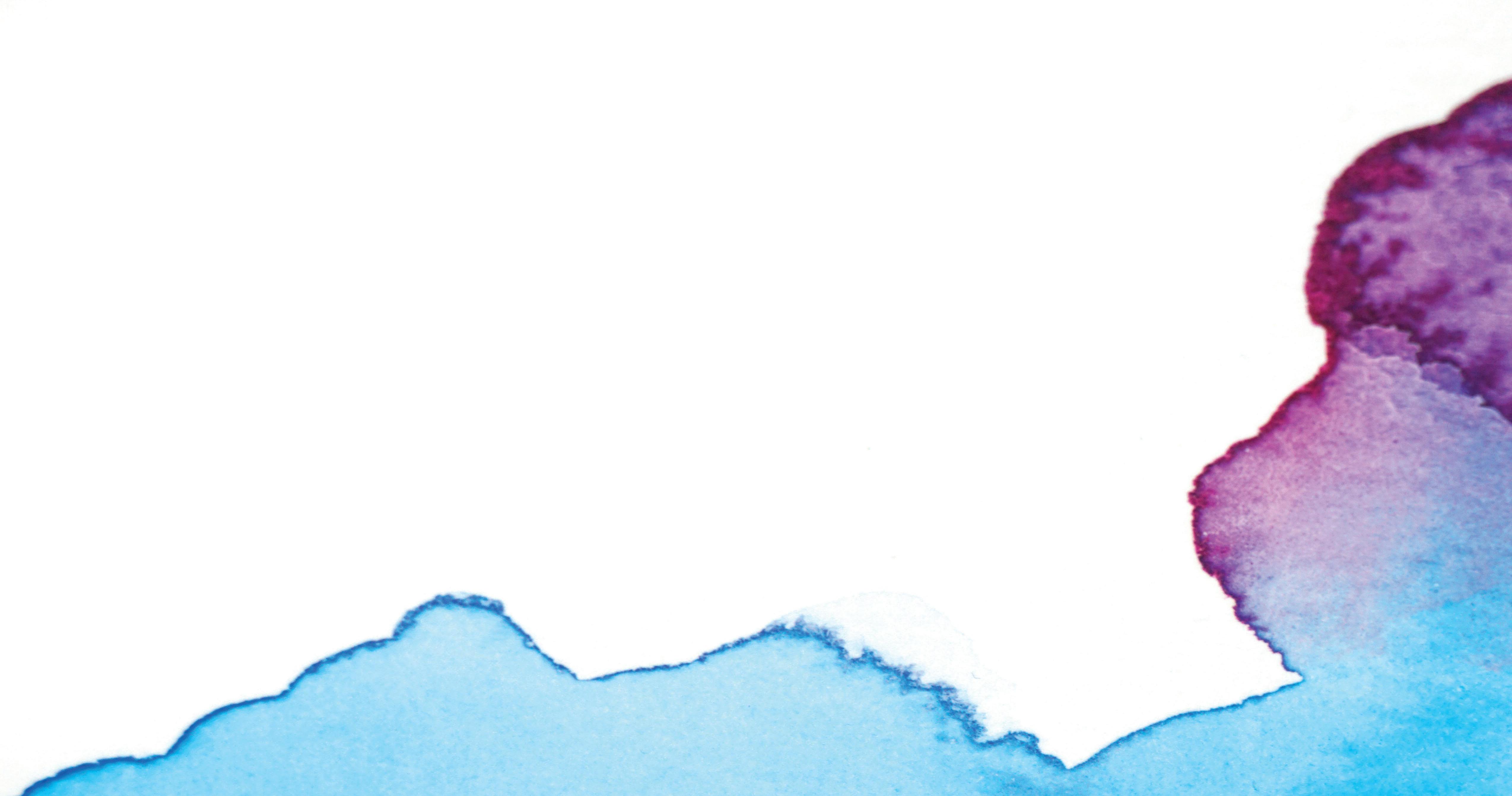
Figure 3: Airflow of a desiccant breather.
be equipped with some level of loop filtration to continually clean the fluid when filling, recirculating, and dispensing it. Mobile filtration carts are an excellent choice for servicing on-site mobile equipment hydraulic fluids, as they offer the necessary fluid filtration and the convenience of mobility.
In a hydraulic system reservoir, one common point of contamination ingression is the breather. Breathers are a necessary component in many hydraulic systems to allow air to freely flow in and out of the system as fluid levels change or thermal expansion or contraction causes air exchange. Most standard breathers offer a pleated filter to prevent particle contamination. These breathers are generally limited to exclusion of contamination particles of about 20-40 microns absolute. Some hydraulic components can experience damage from particles under 2 microns. Additionally, standard pleated breather filters do not typically address the risk of moisture ingression, which can enter through the breather due to moisture or humidity in the operating environment. It can also develop in the reservoir’s headspace due to repeated changes in relative humidity.
To address moisture and particle contamination during operation, users should consider desiccant breathers for all hydraulic reservoirs. Desiccant breathers work by filtering particle contaminants and absorbing moisture when the breather inhales air (see figure 3). Desiccant breathers also help remove moisture from the reservoir’s headspace through designs that keep the desiccant in constant contact with it.
Contamination removal. Even after taking the proper steps to prevent contamination, it will inevitably enter a hydraulic system at some point in the operational life. This is why hydraulic systems on mobile equipment typically employ some level of filtration through the pressure and flow of the system. Common filtration setups consist of an in-tank strainer or suction filter screen, filtration on the system’s pressure side, and a return-line filter to clean the fluid as it returns to the reservoir. However, these components by themselves are often insufficient to maintain optimum levels of fluid cleanliness.
One very efficient and effective way to improve cleanliness levels is with a kidney loop filtration system, which is typically set up as an off-line system and consists of its own motor, pump, and filter elements. Off-line kidney loop systems can be set up on mobile filter carts and incorporated into a work site’s preventative maintenance. While the kidney loop is one of the most efficient ways of removing contamination, mobile equipment is typically limited to using it when the equipment is idle or being serviced. But the goal of precision contamination control strategy is to reduce mobile equipment’s idle and service time. Kidney loops also do not clean the fluid in the hose cylinders and valve blocks as the machine sits idle.
There are, however, options that function as a kidney loop filtration system and are specifically designed for mobile equipment. An example is a bypass filtration system. Bypass units take advantage of hydraulic system pressure and flow by bleeding 5% to 10% of fluid from the main hydraulic system, often via a pilot circuit, and passing it through one or more filter elements before the clean fluid returns to the reservoir (see figure 4). Since a bypass filter is not part of the main fluid flow path, bypass filters can be installed with high filtration efficiency, often exceeding a filtration beta rating of 2,000 at 3 microns.
Assess and monitor. To ensure that contamination control measures are effective, regular routine fluid analysis is critical. Sampling oil monthly or
(Continued from page 7) every 1,000 operating hours – whichever comes first – should include not just basic oil analysis but also confirmation that contamination levels are meeting the ISO 4406 standard. Users should investigate levels above the defined targets and take corrective action as soon as possible.
Another tool is condition-based monitoring, which provides feedback on sudden changes in the fluid and indicates a need for service or

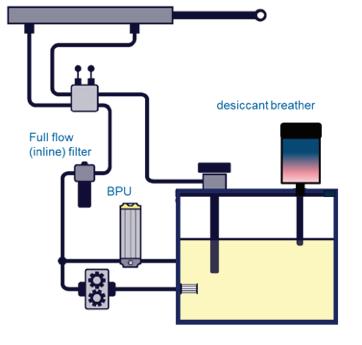
Figure 4: Bypass filtration system. replacement. For example, users can integrate an oil-quality sensor into the hydraulic system to alert for oil degradation and provide the amount of remaining useful oil life. Pairing condition-based monitoring with an oil-sampling strategy can extend maintenance intervals, improve equipment reliability, and reduce the need for costly fluid changes, unplanned downtime, waste-fluid costs, the carbon footprint, and the overall cost of ownership. Many condition-based monitoring sensors are now available as connected IIoT solutions, allowing for remote monitoring and diagnostics of mobile equipment.
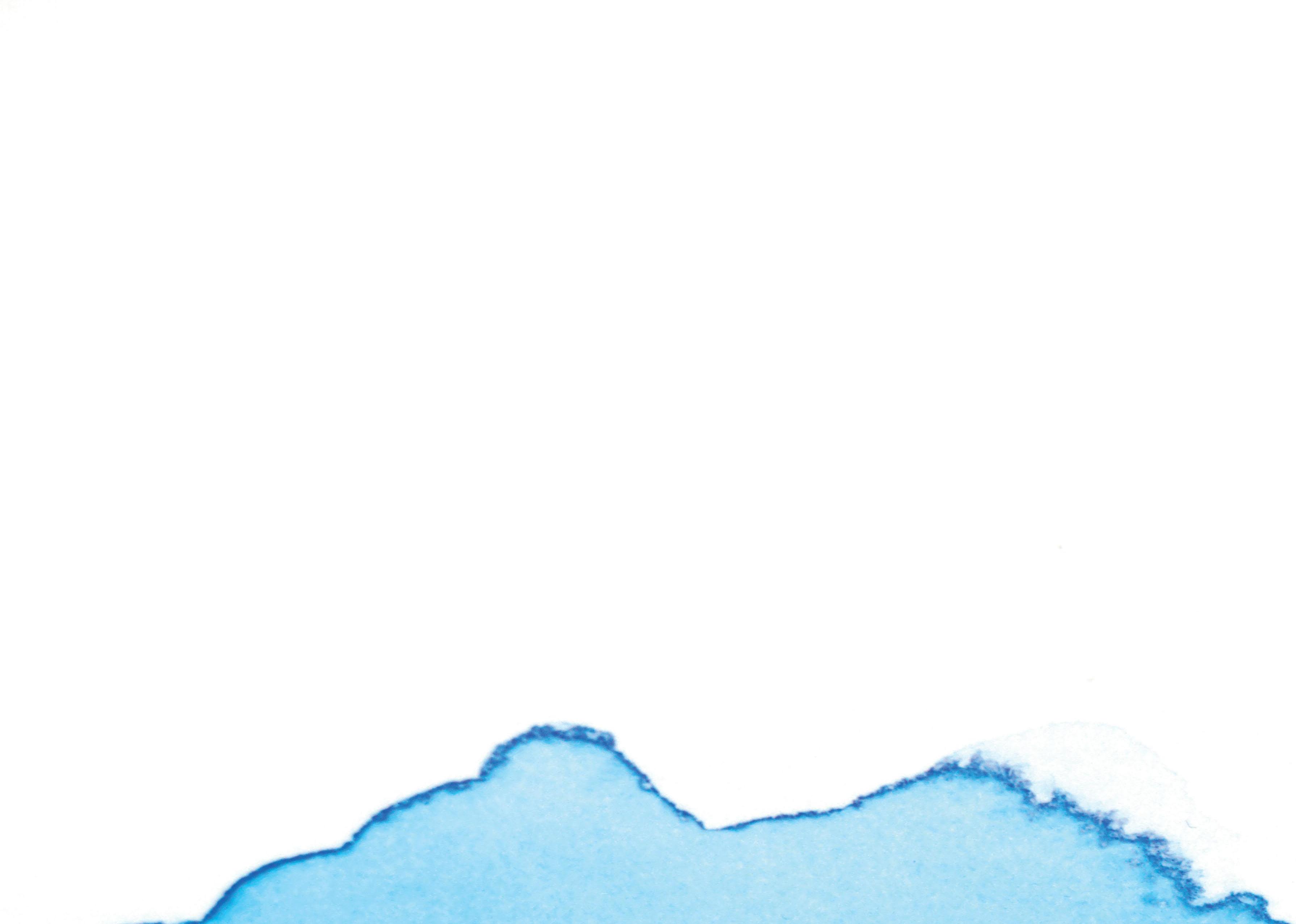
Maintaining the strategy
As you develop and implement a precision fluid contamination control strategy, it is extremely important to document it. Documenting the strategy and how to carry out the maintenance and inspection for each step helps create uniformity and consistency in the process. It provides the framework for work instructions to which team members can refer and ensures they are maintaining the strategy. Teams can then take the following steps to set the precision fluid contamination control strategy in place. • Set the ISO 4406 target cleanliness levels. • Prevent contamination from entering the hydraulic system. • Remove contamination that may have entered the hydraulic system during operation. • Visually assess the hydraulic fluid and overall system condition during operation and idle time. • Monitor the hydraulic fluid in real time with condition-based monitoring.
Documenting a process associated with each of these steps improves the reliability of mobile equipment hydraulic systems, reduces unplanned downtime, and ultimately increases operational efficiency and throughput. Committing to a precision fluid contamination control strategy with proactive maintenance should improve the bottom line. •
LAUNCH YOUR NEXT MARKETING PROJECT
Whether you are in need of some assistance that will build your brand through traditional media, or are looking for some non-traditional solutions, we are here to help. Simple to complex—we will work with you to clearly understand your project and translate those creative concepts into effective solutions. Let us launch your project forward and help bring your business to new heights.
idpcreative.com | Easton, PA | 610.923.8000
The Unvarnished Truth
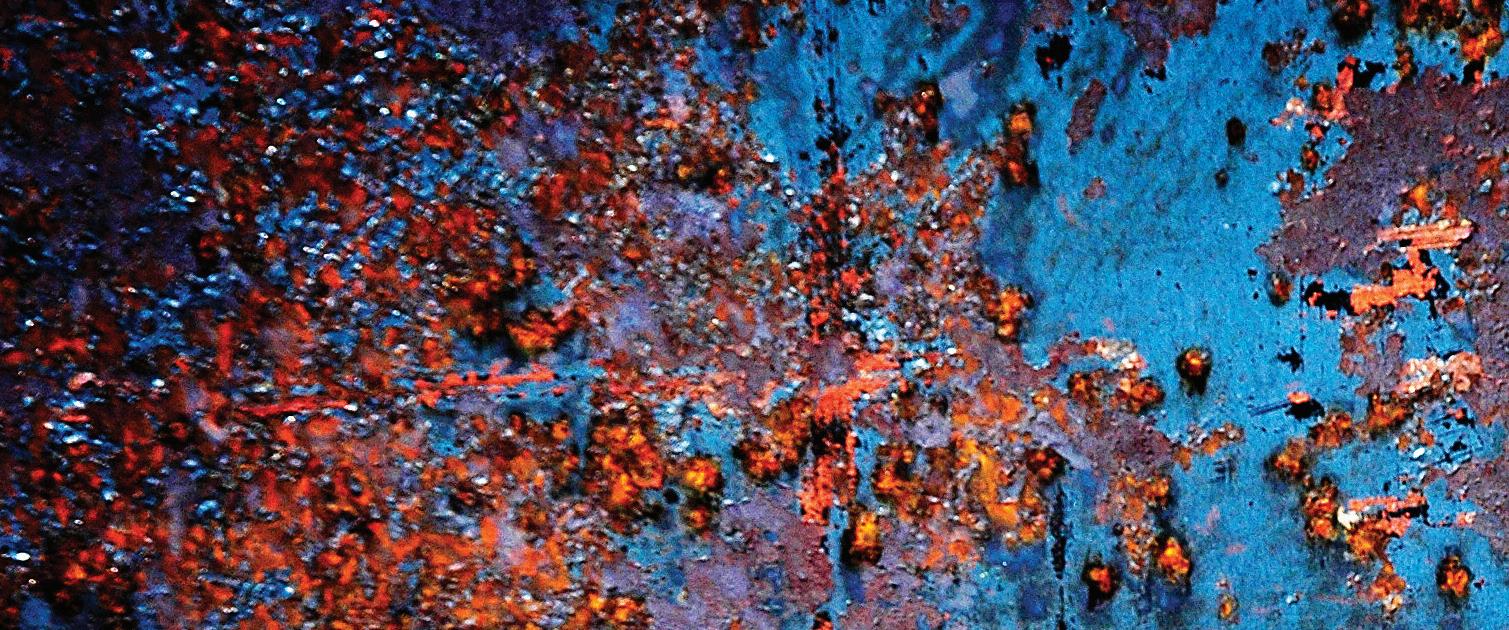
Contamination Control Makes Servo Valves Click
Richard Trent, Regional Sales Manager, and Raymond Weaver, CFPHS, District Sales Manager, Hy-Pro Filtration
Tissue paper is manufactured by various companies across the globe by complex machines that use hydraulic systems. In most cases these systems contain servo valves. As most fluid power professionals are aware, servo valves have a low tolerance for contaminants and require the cleanest fluid of all hydraulic components. This is due to tight clearances between the various internal parts of the valve. Particles that may be too small to cause issues with most hydraulic components can cause servo valves to operate erratically, which leads to premature failure. Failures with these valves is costly in downtime and valve replacement and repair.
In the spring of 2018, a tissue mill experiencing weekly machine trips that resulted in downtime on one of their machines contacted Hy-Pro. The cause was attributed to issues within the hydraulic control system, which contained multiple servo control valves. Each trip led to hours of troubleshooting and sometimes valve replacement before the machine could be brought back online and into production. The mill was looking for a solution to the trips and valve failures, which were impeding operations and increasing production costs. Their prior efforts of implementing an offline electrostatic filtration system and replacing various components within the system had not produced the desired results.
At the first onsite meeting, we reviewed the root-cause failure analysis of the failed servo. The reports, which were supplied by the valve manufacturer, showed contamination as the root cause of valve failure. The reports also noted the presence of varnish. We also reviewed an oil analysis, which showed elevations in the membrane patch colorimetry (MPC) value and the ISO cleanliness codes. We also learned at this meeting that the hydraulic-fluid manufacturer had recommended that the system be converted from using AW32 to AM68 oil. Further, the oil manufacturer recommended flushing the system with a system cleaner prior to installing the new hydraulic oil to remove as much residual varnish from the system as possible.
After viewing the hydraulic system, the discussion turned toward contamination control. Reducing contamination within the system should result in a reduction of system failures and machine trips. The company wanted a total contamination control regime to achieve a lower operating ISO cleanliness code and also to deal with varnish.
The mill had installed an offline electrostatic filtration system onto the system sometime in the past to combat varnish. ASTM International uses ASTM.D02C.01 to define varnish, and ASTM D7843 covers MPC. The MPC test has become known as the varnish potential test. Essentially it involves diluting 50 ml of in-service oil with 50 ml of a nonpolar solvent. The dilution occurs after the sample has been heated to 150°F (65°C) for 24 hours and then aged at 70°F (21°C) for 68-76 hours. Once it is diluted, the fluid is drawn across a filter patch, and filtered solvent is drawn across the patch to remove any residual oil. The patch is allowed to dry and then placed onto a sheet of aluminum foil along with a clean white patch. A device called a spectrophotometer then determines the delta E between the two patches, with the white patch being used to calibrate the spectrophotometer. The delta E values can range from 0 to > 100. The higher the delta E, the higher the potential for varnish to form.
Note that the results are not yes or no for varnish. We’ve seen systems with the same lubricant exude no evidence of varnish even though they had delta E values greater than systems with lower delta E values that were also experiencing varnish-related failures. It is our opinion that MPC should be held as low as possible, with the trend being constant as opposed to increasing over time.
Oxidation by-products
In short, varnish is the result of oxidation by-products precipitating out of solution with the fluid itself. Lubricants and hydraulic fluids oxidize over time. Oxidation can be described as the loss of an electron in the presence of oxygen. Mineral-based lubricants and hydraulic fluids contain antioxidant additives (AO) to arrest oxidized molecules and decrease the rate of oxidation. Other things that lead to increased oxidation include excessive heat as well as water and other contaminants.
As oxidation continues to occur, it creates more by-products. Eventually a point can be reached where there are more oxidation by-products present than the fluid can hold in solution. These oxidation by-products precipitate out of solution and begin to plate onto various metal surfaces. At this point varnish begins to form in the system. If the situation continues unchecked, it shortens the life of the components and the fluid itself.
Areas that generally collect varnish first are areas of low flow (reservoir), areas of tight clearances (servo valves), and cooler areas of the system (heat exchangers). Varnish has an interesting relationship with temperature. Fluids can maintain more oxidation by-products at higher temperatures versus lower temperatures. This explains why varnish appears where it does, as precipitation can more easily occur in these locations.
Varnish formation within hydraulic fluid is a broad and complicated subject. We discuss it in this article for simplicity and expediency, since varnish was a major factor in the machine trips and servo valve failures in the tissue mill’s hydraulic control system. We now look at varnish mitigation and the subsequent results at this mill.
We now know that varnish is the result of oxidation and that oxidation within mineral-based lubricants and hydraulic fluids accelerates at temperatures higher than 150°F (65°C). As water and other contaminants accelerate oxidation, a good first step is to keep the fluid clean, dry, and cool. Minimizing oxidation increases the time before a fluid becomes saturated with by-products.
Varnish mitigation
Even with a system operating under the clean-dry-cool parameters above, oxidation will occur. For that reason, varnish mitigation should be considered. There are many types of varnish mitigation systems available. Offline electrostatic filtration was one of the first systems marketed to control varnish. There are multiple manufacturers of electrostatic filtration systems, and Hy-Pro is one of them. These types of systems have been applied to lubricants and hydraulic fluids for a couple of decades. Most of these, including Hy-Pro’s, incorporate a pump that produces flow through the skid. The fluid flows through filter housings installed with collector elements. High-voltage DC current is applied to metal plated within the collectors, and insoluble oxidation by-products are “collected” onto the plates. The drawback of electrostatic filtration units is that they can only remove insoluble oxidation by-products. This leaves the fluid saturated at the temperature at which the fluid is processed. At any point that the temperature decreases, insoluble by-products can precipitate out of solution, and varnish can form. We do not apply electrostatic filtration to mineral-based fluids for this reason.
Other forms of varnish mitigation systems include ion exchange or ioncharged bonding (ICB) resins. Our experience is that resins achieve the lowest MPC values of in-service fluids. We have been supplying offline systems using 1 micron in size when they precipitate out of solution. That is much smaller than typically mechanical filters can capture. Also, they are most often still in a liquid state at that point. Properly designed depth media provides a place to capture these insoluble by-products. To keep it simple, the by-products plate to the various fibers and stay within the media. Depth media mostly targets insoluble oxidation by-products, but our VTM has shown the ability to decrease acid, leading to the theory that it removes a small number of soluble by-products. VTM and other types of depth media can remove water as well.
Installing VTM
After discussing these points with the mill, the company decided to install VTM onto its hydraulic system. Since the system already contained an offline filter cooling loop, the mill installed a larger filter housing within the loop using this media. After installation, MPC decreased from > 20 to 5.1, and the ISO cleanliness code was 16/13/9 on a sample taken May 22, 2019. Previous samples showed it as high as 21/20/17, with the lowest showing 19/17/12. In June 2019, the oil manufacturer’s recommended cleaning fluid was installed and the system operated for a couple of days. Samples taken on June 20, 2019, showed that MPC had increased to 10.1, indicating the cleaning fluid was doing what it was supposed to do. The June sample showed that ISO cleanliness had increased to 20/18/12.
Results of fluid tests before and after installing VTM
DATE MPC # New from barrel 3.6
April 2018 from lab report 5.22.2019
5.1 6.20.2019 during flush 10.9 7.25.2019 3.1
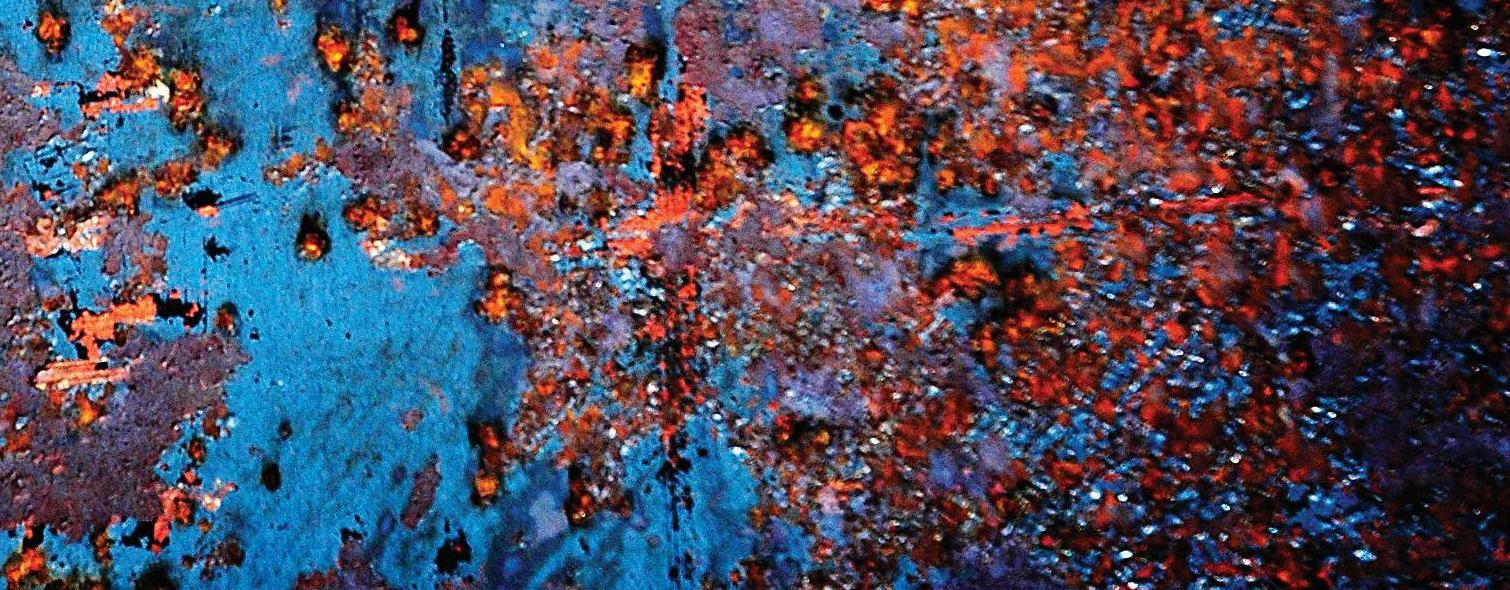
8.29.2019 10.24.2019 5.2 6.1
12.19.2019 6.7
1.30.2020 10.29.20 2.8.2021 7.6 5.4 5.4
ISO CODE 4U 6U 14U MEDIA WATER PPM
19/17/13 4904.27 Upper Limit 16/14/11 >4m/ml 1055.20 >6m/ml 50.93 >14m/ml 136.78
21/20/17 16304.00 5837.00 1084.00 Incumbant 24184
16/13/9 20/18/12 14/11/7 16/13/9 13/9/3 12/9/5 11/9/<3 11/9/<5 11/9/<3 348.00 8203.00 83.07 411.13 55.47 22.60 12.93 11.80 11.80 53.00 1422.00 19.40 50.53 4.80 3.93 2.67 3.73 2.53 4.00 38.00 0.87 3.00 0.00 0.20 0.00 0.20 0.00 VTM Only VTM Only
39 68 VTM and 6M 116.35 VTM and 6M 68.05 VTM and 6M 101.51 VTM and 6M 78.32 VTM and 6M 78.08 VTM and 6M 129.09 VTM and 6M 101.93
ICB resins for around 15 years and have achieved great results. These systems work by removing oxidation by-products that are still in solution with the fluid. Once they are removed, the fluid regains solvency and can dissolve almost any existing insoluble oxidation by-products back into solution. From there the resin removes those. We prefer the use of resin technology for R&O fluids, like turbine and compressor oils as well as most synthetic fluids. Resin, however, is not recommended for all fluids, especially most antiwear (AW) hydraulic fluids. In most cases AW additives are polar, and most resins try to remove them while also removing oxidation by-products. There are some exceptions to this, but we recommend never applying a resin to AW oils unless the fluid is tested with the proposed resin. During this type of test, the AW additives in the new fluid are measured pre- and post-treatment to determine if AW additives are being removed.
A third type of varnish mitigation is the use of depth-filter media. This is not the same as typical glass-filter media that most filter manufacturers produce today. This style of depth media can be produced using different types of fibers, both natural and synthetic. Hy-Pro produces a depth media known as VTM. Other manufacturers also make this type of depth media. This style of depth media does more than act as a mechanical filter, and that is an important distinction. As a rule, oxidation by-products are well below
A sample of the new fluid installed into the system after the flush showed ISO cleanliness as 19/17/13. The next sample, pulled on July 25, 2019, showed MPC at 3.1 and ISO cleanliness at 14/11/7. The most current sample from this system, pulled on Feb. 8, 2021, showed MPC at 5.4 and the ISO cleanliness at 11/9/<3.
From a contamination control point of view, these are great results. The operation results of the system and improved reliability of the hydraulic control system tell the story that matters the most. Since the installation of VTM media, the mill went from experiencing unscheduled downtime of four to six hours per week to a single occurrence as of Feb. 8, 2021. The company applied the same solutions to the other tissue machines onsite.
Arguably, contamination causes most hydraulic component failures. We have reviewed articles that claim that as many as 75% of failures can be attributed to contamination. And it is widely accepted that servo valves have the lowest tolerance for contamination of all hydraulic components.
However, by understanding contamination and developing a clear solution for it, even servo valves can operate for long periods of time. First, work on clean, dry, and cool. Second, implement a control plan that covers all contaminants, including oxidation by-products. It will save money and valuable time. •