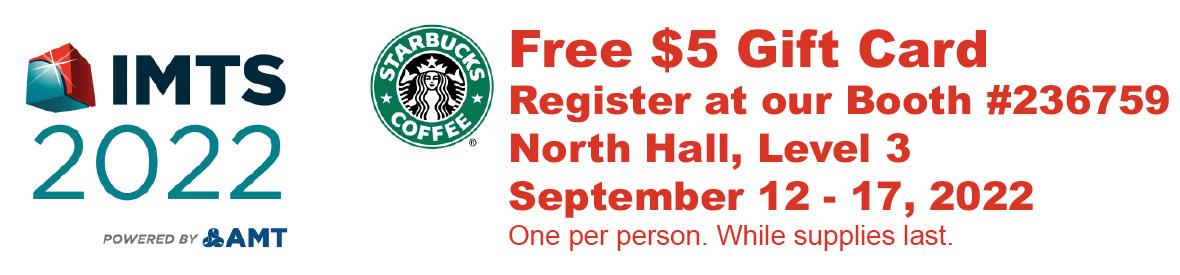
7 minute read
Test Your Skills
Considering Component Compatibility
Some fluids with very good lubricity and viscosity characteristics may prove caustic to the material in pumps, actuators, or valves, especially when hot.
There are three areas of component compatibility that the designer needs to consider. The first is within the circuit, the second is chemical reaction, and the third is temperature.
Chemical compatibility is an important consideration when choosing the hydraulic fluid for the system. The inner tube of the hydraulic hose must not react chemically with the fluid. The same can be said of the seals within the components. Water is a chemical that can adversely affect the seals, so special seals must be applied where high water-content fluid is used. Water-glycol fluids attack zinc, cadmium, and aluminum, so these elements must not be located anywhere in the circuit in order to prevent contamination and deterioration of the hydraulic system. It is important that the designer be aware of the composition of the parts that make up the system components.
SEAL MATERIAL COMPATIBLE FLUIDS TEMPERATURE RANGE
1. Metallic piston rings Petroleum base and synthetic fluids, phosphate esters – for high pressure and severe conditions Low to 500°F (260°C)
2. Leather Petroleum base and some synthetics, phosphate esters – for medium-to-high pressure -65°F to 225°F -54°C to 107°C
3. Neoprene rubber General purpose industrial use, Freon 12; weather and salt water resistant -65°F to 300°F -54°C to 149°C
4. Nitrile rubber (Buna N) Petroleum base fluids and mineral oils – used for some rotating seals, extrusion resistant
5. Silicone rubber
6. FluoroElastomers (Viton and Fluorel) Water and petroleum base fluids, phosphate esters; low tensile strength and tear resistance recommended for static seals only
Petroleum base, synthetic, diester, silicate ester, and halogenated hydrocarbon fluids – for high-temperature fluid applications -65°F to 225°F -54°C to 107°C
-80°F to 450°F -62°C to 232°C
-20°F to 400°F -29°C to 204°C
Many seals are manufactured in a process that includes heat to cure the product in the mold. This process is very specific and provides the Duron rating of the seal. Exposing seals to heat beyond their rating will result in continued curing, making the seals brittle and without proper elasticity.
The designer must be familiar with the chemical and temperature compatibility charts for both seals and metal parts (see chart) so that proper choices can be made.
Seals prevent internal and external leakage in a hydraulic system. Static seals are used for pump housings, valve bodies, and reservoir covers, and between cylinder ends and the cylinder tube, where there is no relative movement between the parts to be sealed. Dynamic seals are used between moving parts, for example, between the piston and cylinder bore, and between the cylinder rod and the rod bearing. About 80% of seal applications use static seals.
The starting and operating temperatures of the machine are also used to select hydraulic seals that retain their sealing properties in ambient and hot conditions. Neoprene, a general-use sealing material, has a temperature range of -65°F to 225°F (-54°C to 149°C). Neoprene is satisfactory for static gasket seals and O-rings with petroleum base fluids, but is not as well suited as Nitrile rubber (Buna N), urethane, and even leather, for dynamic applications. Extremely cold and hot conditions require a sealing material that is more tolerant of heat. Viton and silicone compounds are the sealing material of choice for applications with temperature extremes.
The ability of a sealing material to prevent leakage is tested by measuring the durometer (indentation hardness), creep, and compression set after deformation. The sealing compound must be hard enough to resist wear and extrusion for the clearance gap and pressure that will be encountered, yet still be soft enough to maintain a seal during continued use. Seals have a tendency to swell in the presence of hydraulic fluid. Some swelling is permissible, and even somewhat desirable, in maintaining a fluid-tight seal. But excessive swelling and accompanying softness of dynamic seals increases friction and the tendency to abrade. Twenty percent swelling is considered the maximum allowable swell; swelling by a factor of 40% to 50% is allowable for confined static seals. •
TEST YOUR SKILLS
1. Referring to the chart, which seal material has the widest temperature range? a. Polyurethane. b.Leather. c. Neoprene. d. Silicone rubber. e. Fluoro-elastomer. 2. What is the reason for knowing the chemical compatibility?: a. Avoiding bad chemical reactions. b. Choosing the correct seals. c. Matching the fluid to the pump and/ or motor. d. Applying appropriate components. e. All of the above.
See page 31 for the solutions.
COMPONENT SHOWCASE
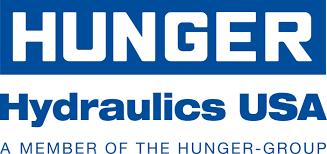

THE ULTIMATE CONTAMINATION CONTROL TOOL
SAVE TIME SAVE MONEY SAVE LABOR SAVE OIL
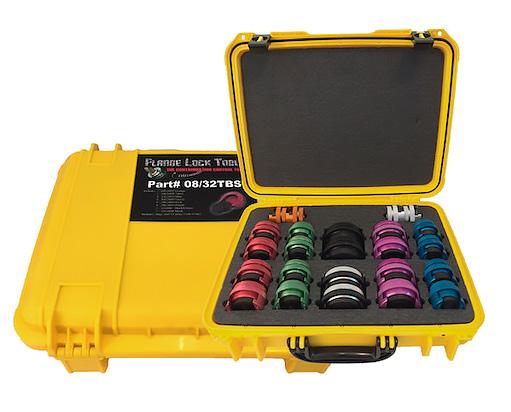
This product is Patented, other Patents pending.
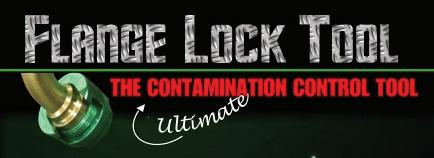
SO, YOU PURCHASED YOUR LAST HYDRAULIC CYLINDER BASED ON PRICE?
Don’t worry, you are not alone in this decision. But, do you know what your real costs are? Failure + Downtime + Repair = $$$ far more HITACHI FLANGELOCKTM than you signed up for. We pride ourselves on partnering with our customers to ensure they get the life and performance they desire. AND CAP KITS AVAILABLEFrom small to large, and with our experience and expertise, Hunger Hydraulics Group has not only produced the world’s largest hydraulic cylinders – over 260 tons! – but is also, proudly providing extensive Part number Part description Applicable machines Number of parts Weight (kg)manufacturing and repair in NW OHIO since 1981. Ask about our SWINGFLGLCK2062 Swing hose FlangeLockTM kit EX3600, EX5600, EX8000 16 x 2062U - red FlangeLockTM 6.7 lifetime warranty – Hunger Hydraulics USA. #HOWBIGDOYOUWANTIT SWINGCAP2062 Swing circuit cap kit EX3600, EX5600, EX8000 16 x 2062 - cap
OVER
TRAVELFLGLCK2462 Travel hose FlangeLockTM kit EX3600, EX5600, EX8000 16 x 2462U - purple FlangeLockTM 4.5
7.7
TRAVELCAP2462 Travel circuit cap kit EX3600, EX5600, EX8000 16 x 2462 - cap 6.4
FRONTATTFLGLCK326162 Front attachment FlangeLockTM kit EX3600, EX5600, EX8000 14 x 3262U - black FlangeLockTM 4 x 3261U - black & silver FlangeLockTMYEARS 8.9
FRONTATTCAP326162 Front attachment cap kit EX3600, EX5600, EX8000
14 x 3262 - cap Hunger Hydraulics 4 x 3261 - cap BOOMARCHFLGLCK3262 Boom arch hose FlangeLockTM kit 1-800-248-9232 EX3600, EX5600, EX8000 20 x 3262U - black FlangeLockTM
BOOMARCHCAP3262 Boom arch hose cap kit EX3600, EX5600, EX8000E-mail: info@hunger-hydraulics.com 20 x 3262 - cap
hunger-hydraulics.com
9.5
9.9
11.3
CONTAMINATION CONTROL
Routine and scheduled maintenance of hydraulic systems are vital to getting the most out of your Hitachi Mining Excavator. While maintenance plays the largest role in the prevention of unnecessary machine downtime, it can also expose the hydraulic system to high levels of contamination rapidly decreasing component longevity. The importance of contamination control is sometimes Stop the Mess overlooked when performing maintenance due to incorrect practices being used. THE FLANGELOCK™ TOOL AND CIRCUIT BLANKING CAPS The FlangeLock™ tool and caps are the ultimate contamination control tools for protecting your hydraulic system. The FlangeLock™ allows for the simple sealing of open hydraulic flanges without tools while the caps can be bolted in place of a flange connection. Easy on, easy off, they offer a leak-proof solution to hydraulic systems and environmental cleanliness. FlangeLock™ tools and caps stop the mess.
The FlangeLock™ Tool is the ultimate contamination control tool for protecting your hydraulic systems. It allows for the simple sealing of open SAE code 61, 62 HITACHI MAKING CONTAMINATION CONTROL EASY & CAT-Style hydraulic flanges without tools. Constructed from lightweight aluminum. Hitachi have packaged FlangeLock™ tool and caps specifically for Hitachi mining excavators. The Hitachi customised kits make sure no matter which component routine maintenance is being performed on, you will always have the exact Easy on, easy off. Offers a leakproof solution to hydraulic system and environmental number of FlangeLocks™* and caps to help reduce contamination. cleanliness. FlangeLock™ Tools stop the mess!*Note: FlangeLocks™ are not to be used under pressure
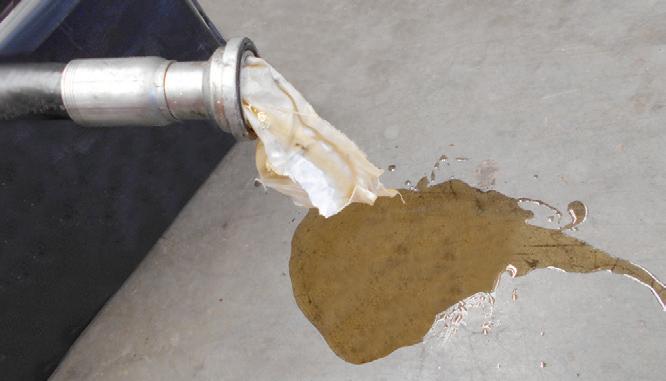
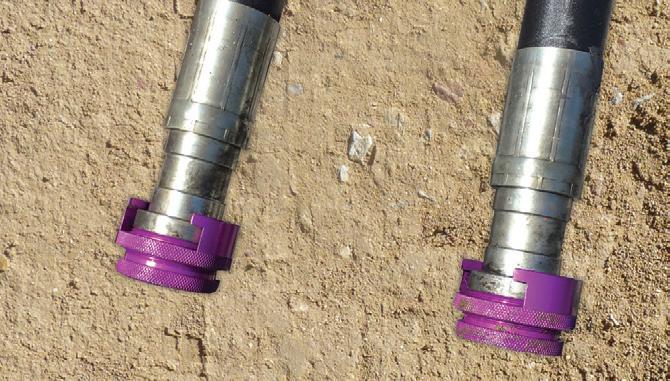
• No tools required • No expensive hardware needed • No more rags stuffed into hoses • No more messy plastic caps • The ultimate contamination control tool
• One hand installation • Eliminate hydraulic oil spills & clean up • Quick installation & ease of usage Call you local Hitachi Muswellbrook representative or the branch on 02 6541 6300 for more information. • Safe for personnel & environment • Industry acclaimed