
8 minute read
Edge-located HMIs drive new wave of Industry 4.0
Unifed HMIs installed at the automation edge effectively connect users to their data by bridging OT plant data with workfows and IT tools. Advances will improve machine performance, reduce downtime, enable greater proftability, and fuel connected enterprises through the Industry 4.0 revolution.
THE RISING TIDE OF INDUSTRY 4.0 IS MARKED by surging data and cloud connectivity demands, as machine builders and manufacturers expect their plant foor process data to be available at all times from anywhere. While digitalization and connectivity SOURCE: SIEMENS INDUSTRY has always been viewed to be competitive advantages in manufacturing, they are now imperatives for achieving proftability, longevity, and responsiveness to rapidly evolving market trends.
Fortunately for machine builders, connected components are in abundance, and it is easier than ever to equip machines with smart sensors, variable frequency drives, and other intelligent components. However, transmitting data effectively from these devices to the cloud remains a challenge.
Unifed human-machine interfaces (HMIs), located at the automation edge on the plant foor, are positioned to address this issue. Equipped with modern IT capabilities, unifed A single device offers a wide variety of apps and dashboards for machine visualization and analysis. HMIs make it easy to effciently transfer data, enabling machine builders to deploy apps Bandwidth and security issues applications where an edge controller is not and centrally monitor one machine or a feet. Internet of things developments are making present. However, in a plant setting with Availability of these IT capabilities in the it possible to connect remotely to numerous potentially hundreds of devices and sensors, industrial operations technology (OT) space smart devices. Direct connection from device direct connection to the cloud is usually not accelerates machine effciency improvement to cloud is often favorable in the consumer advisable due to bandwidth constraints and efforts. electronic space or for remote industrial security concerns. SOURCE: SIEMENS INDUSTRY While a wide array of these devices in the industrial space support direct cloud connectivity, many machine components still require an intermediary device for pre-processing raw sensor data and converting it to cloud-friendly packets. Additionally, hundreds of sensors on a plant floor simultaneously broadcasting their data for external consumption can clog up the network, creating bandwidth and latency issues. Even if data flows smoothly in both directions between plant floor and cloud, communication must be encrypted to ensure safe operation and protect sensitive information. Moreover, most modern plants require a PC-based solution to collect, store, and interpret historical performance data for optimizing production. If all sensor data moves directly to the cloud, data aggregation must take place outside the confnes of the plant foor, introducing more data integrity risk than is present while the data is closer to Each app has its own container, hosted by a unifed HMI’s docker. its original source.
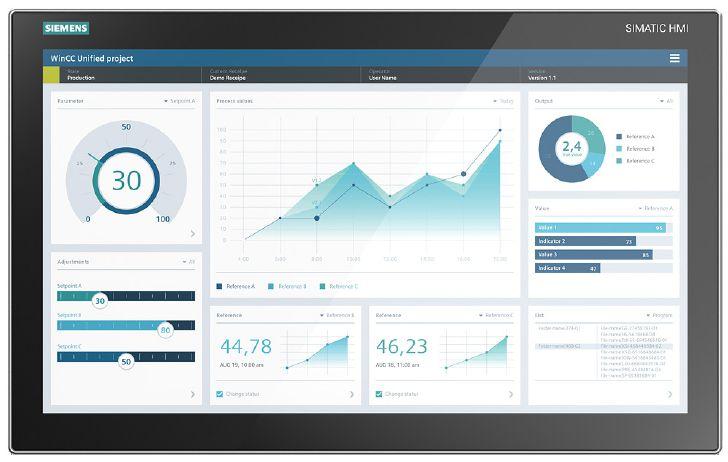
SOURCE: SIEMENS INDUSTRY • Automating workfows • Managing inventory • Analyzing machine and drive health, and calling out predictive maintenance • Analyzing performance and creating insights • Creating notification pipelines and sending alerts • Simulating production with digital twin Furthermore, unifed HMIs are repositories for data collection, analysis, storage, and forwarding. With the right apps, users can connect to automation controllers, drives, OPC UA devices, and other edge devices. Using the MQTT protocol, these devices can effciently publish data to the cloud, consuming minimal network resources. Due to their multilingual properties, unifed HMIs perform well as interfaces for establishing key performance indicators (KPIs) Machine builders can simulate proposed production changes prior to implementation. and measuring actual production output from multiple machines. Unifed HMIs also eliminate the need for PCs in many applications because Modern HMIs provide solutions built-in, scalable edge apps. they can execute many of the IT functions To address these concerns, manufacturers need In light of the headache-inducing challenge performed by PCs within their industriallyan edge device on the plant foor to make of managing application dependencies and hardened HMI housing. effcient use of bandwidth in communications compatibility across devices, unifed HMIs outside the plant, and to ensure secure data use docker and container structure to alleviate Device and app management transactions. By processing data on the this issue, freeing developers to focus on app Adding another IT characteristic increasingly plant foor closer to its source, this type of logic and functionality. This makes unifed making its presence known in OT, unified component improves data integrity compared HMI apps heavily confgurable, as opposed HMIs include enterprise management. to processing in the cloud. to programmable, because the underlying Machine builders and manufacturers can
Though essential, the reliable movement infrastructure is already vetted. centrally manage devices and apps from on of data from plant floor to cloud is only Containerization wraps up all dependencies or off premise through a web-based interface part of the need. Engineering, operations, for an app into a single package, allowing independent of the HMI automation project and maintenance staff alike must be able to it to be deployed to any device, without fle. This can be done from any device capable effectively visualize, analyze, and interact the need for a checklist of external resource of hosting a web browser, such as a laptop, with machines to keep the plant running in requirements on the target. It is similar to smartphone, or tablet. an effcient manner, and unifed HMIs at a virtualization of a personal computer (PC)— This model provides the fexibility to store network’s edge facilitate these functions. where an operating system (OS) and its apps and licenses on servers, remotely deploy
Unifed HMIs provide different capabilities entire fle system are stored in a directory, or update apps without modifying machinethan standard edge controllers with built-in and can be run without extensive external level functionality, apply security patches, and apps for managing edge devices and data, dependencies—though containers require manage content of all unifed HMIs across the and they bring advanced IT capabilities to lower overhead than virtual machines (VMs). enterprise. Communication among devices is the machine level in a cost-effective manner. A docker engine running on a device’s OS encrypted, and HMIs can be confgured for When implemented, they serve as a central enables the storage and execution of multiple automatic system backup to prevent data loss. repository for data across the plant foor, containers. As a container is to a VM, so an Apps run in the background fulltime with enabling direct visualization and analysis of HMI’s docker is to a host PC’s hypervisor. their hooks in the docker—independently of machine health and performance through a In addition to using pre-built apps, the OS running the classical HMI automation single interface. Compared to direct cloud machine builders can develop their own apps project also present on a unifed HMI—so a connection of individual sensors, unified utilizing a unifed HMI’s docker engine. The change in app confguration does not impact edge HMIs are less complicated to implement docker incorporates security intrinsically, HMI runtime execution. This provides the and more feature-rich out of the box, adding another advantage enabling focus on app fexibility to update apps on a regular basis capabilities to plant-foor data processing. development and less time spent on building without concern of modifying the automation and maintaining infrastructure. program fle. Confguration and usage For machine builders and end users short Acting as a bridge between OT and IT, unifed on time, there is likely already ‘an app Results HMIs are automation infrastructure agnostic, for that’. Native and third-party apps are For an industrial heater manufacturer, and their applications can scale as plant available for purchase to run on unifed HMIs, struggling to keep up with growing demands foor layouts evolve. This is largely in part accomplishing tasks such as: from its stakeholders, implementing Siemens to a wide variety of applications available • Performing advanced production WinCC Unified HMI software and panels for managing and interacting with machines. algorithms and calculations enabled it to deliver greater functionality and While developers have a host of tools available • Connecting to data from multiple sources performance to its users. for custom app creation on unifed HMIs, they over multiple protocols This empowered the manufacturer to develop are also equipped with a wide selection of • Visualizing data its own apps for machine and performance
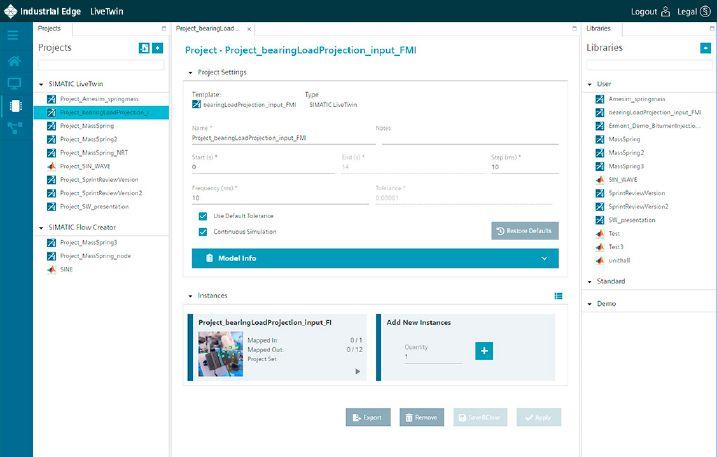
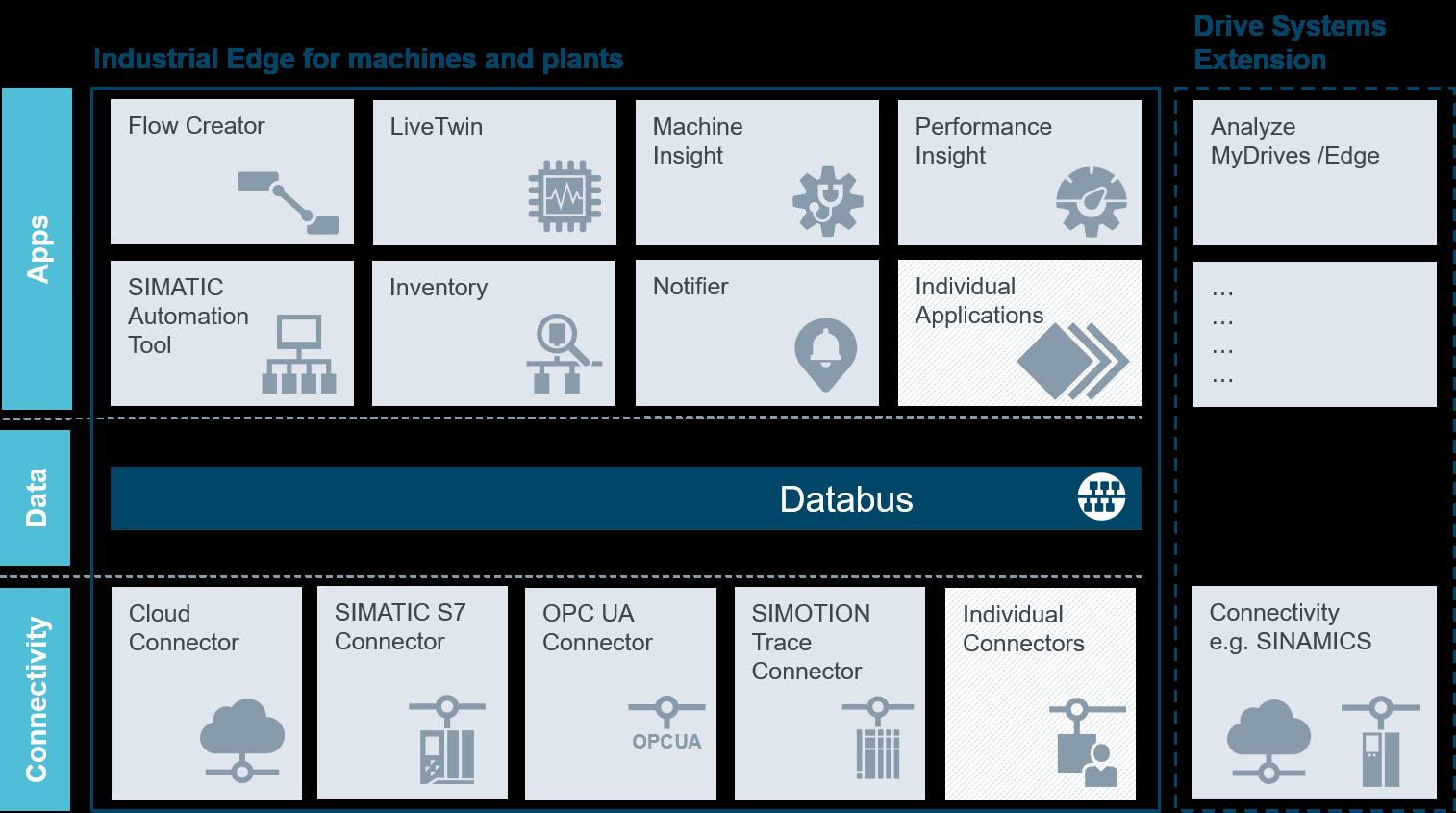
The right industrial apps ease connectivity between the cloud and plant-foor devices.
analysis, and for maintenance support. The HMI’s docker ensured app security, and it saved development time because the pre-built container infrastructure allowed attention to be placed on app functionality.
Using unifed HMIs’ remote management capabilities, the machine builder was able to remotely push updates to machines around the world whenever they released a new revision, comparable to app updates on a smartphone or patches on a PC.
Unifed HMIs’ native support for MQTT made cloud connectivity possible, while OPC UA protocol support enabled users to connect their new machine with other machines in their facilities, and with intelligent devices.
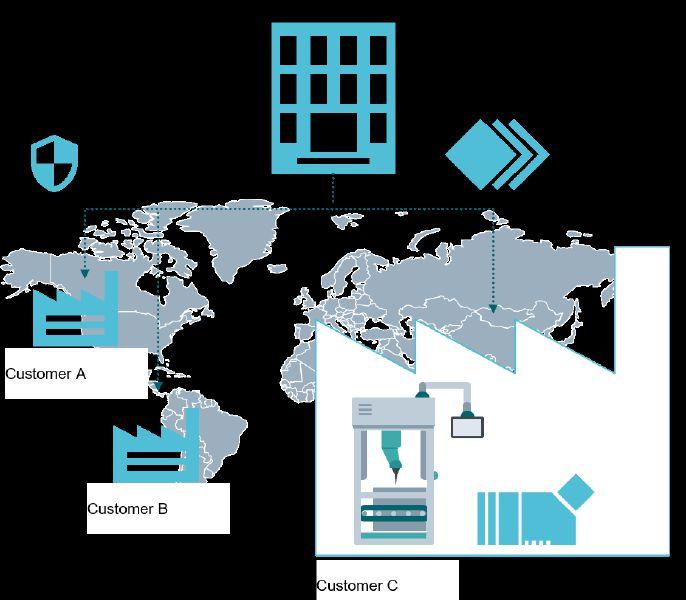
SOURCE: SIEMENS INDUSTRY
Continually improving
While industry grows more agile and geographically dispersed, machine builders are pursuing always-on access to data. Unified HMIs installed at the automation edge effectively connect users to their data by bridging OT plant data with workfows and IT tools, phasing out the need for industrial PCs in many applications.
This consolidation of functionality is already driving Industry 4.0 as machine builders are empowered to: • Connect to their data from anywhere • Consolidate traditionally separated OT and IT devices for data processing and access into a unifed HMI • Integrate machine performance data directly with business process workfows • Deploy out-of-the-box or customized apps for interaction with their data • Utilize app containers to streamline functionality and security, and alleviate OS and frmware compatibility issues
As unified HMIs evolve and continue to simplify hardware infrastructure, more and more manufacturers are relying on these devices to branch out further, supporting an increased breadth of factory-floor communication protocols.
These advances will improve machine performance, reduce downtime, enable greater proftability, and fuel connected enterprises through the Industry 4.0 revolution.
Ramey Miller, the HMI/Edge product marketing manager, Siemens Industry.