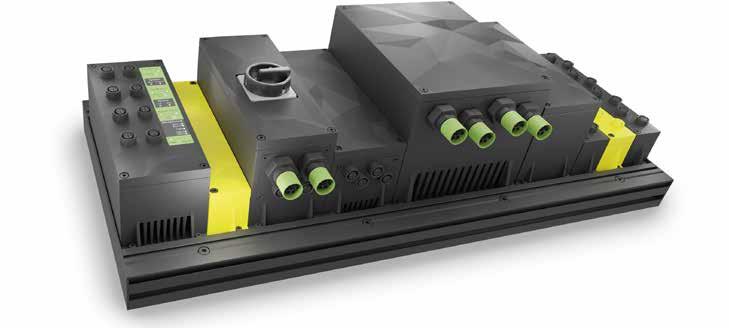
6 minute read
Decentralized automation eliminates control cabinet
Vario-X technology offers a solution for cabinet-free, decentralized automation. The platform ensures modular and transparent processes, higher added value, greater cost-effectiveness and competitiveness. Its integrated installation concept shortens machine installation time by around 40 percent.
Vario-X is a modular, highly flexible automation platform that, for the first time, allows all automation functions to be implemented completely decentrally, i.e. without control cabinet architecture.
THE VARIO-X AUTOMATION PLATFORM BRINGS sensors and actuators into the field without control cabinets and in a decentralized manner. A digital twin saves costs and time in planning, installation, operation and service. Growing digitization, shorter development cycles, higher customer requirements and an increasing shortage of skilled workers - the world of automation is changing at breakneck speed. Pretty much everything that used to be reliable in production is now being put to the test. What used to be a glimmer on the horizon: modular, standardized and digitally supported planning, simpler and faster installation and commissioning, more flexibility in production with shorter lead times, safer machines and more efficient service and maintenance processes, has become a concrete target in a very short time. All of this should also be highly digitized so that the data from the machine can be accessed at any time from any location. Has the time come for a digital twin? Murrelektronik has the answer to all these problems and presents Vario-X, a modular, highly flexible automation platform that, for the first time, allows all automation functions to be completely decentralized (without control cabinet architecture). Vario-X brings sensor and actuator technology directly into the machine environment and ensures reliable voltage, signal and data management during the seamless integration of decentralized servo drives.
At the heart of Vario-X are our IP65 rated, robust, waterproof and dustproof housings that contain the power supply, controller, switches, safety technology and IO modules. They can be easily snapped side by side onto a no less robust backplane with integrated machine construction profiles.
This allows the entire station to be easily attached to all common profile systems with no further protection required and, in extreme cases, it can even withstand stepping loads. Equipped with a multi-core CPU, Vario-XController is up to all requirements and can be integrated into all higher-level Industrial Ethernet networks as an open control platform.
The plant automated with Vario-X comes with a digital twin. A moving 1:1 image of the real plant, which contains all functions and configurations of the later system. This is available right from the start in the project phase before the first mechanical component has been ordered or assembled.
For this purpose, Murrelektronik kinematics the design files of machines and systems in special software, in which the later movements and processes can then be simulated. For this purpose, the same control program runs on the virtual model as later on the real machine. The plant can be "placed" directly in the later production hall via augmented reality using an app on the cell phone or tablet.
This allows the subsequent process sequences to be simulated even before the plant is set up and potential collision hazards or assembly problems to be identified at an early stage. The planning of subsequent cable routing and possible attachments is also noticeably simplified. On the one hand, because planning can increasingly run AI-supported and is thus less prone to errors.
Predictive maintenance
The digital twin also makes an important contribution to condition monitoring and predictive maintenance during operation. The use of artificial intelligence, in combination with the Vario-X digital twin, makes it visibly easier to use. If the data is read into corresponding software and analysis tools, anomalies in the process flow can be detected and work can begin to eliminate them at
earlier stages. Vario-X measures the accuracy of field automation processes in accordance with the lab-to-field approach.
Since the twin knows the necessary components at the same time, they can be outsourced or ordered in advance. In the best case, machine failures are completely avoided by replacing parts only when needed. Long-term analysis of the collected data also allows statements to be made on energy efficiency and simulations of various process changes can be run to gain information on possible savings potentials.
The fact that Vario-X, with its digital twin, can keep a virtually constant eye on the machine during operation also provides valuable information about the mechanical and thermal influences the machine is exposed to. This is a huge advantage in view of new business models, in which machines are increasingly being leased instead of sold, where the plant owner has an interest in knowing how his machine is being treated.
Easy control via app
Thanks to smartphones and smartwatches, everyday life is now unthinkable without apps, voice-controlled assistants and gesture control. Why shouldn't machines be controlled just as easily? Thanks to Vario-X, commissioning can be carried out via an app, and robots can be controlled by gestures or speech.
This is an effective tool for shortening commissioning times and making the work of machine installers and operators a whole lot easier. Configuration instead of programming is the new motto allowing companies retain their ability to act despite a shortage of skilled workers.
Vario-X thus transfers the planning, simulation and subsequent operation monitoring as well as the maintenance management of a plant completely into the digital world, and with the possibilities available there it can become the key to future-proof automation technology. Because: The industrial world is turning faster and faster. Digital disruption, shorter development times and a growing focus on individual customer needs require sustainable and agile solutions. The classic sequential product development process can no longer meet these requirements. It lacks transparency and flexibility, while at the same time lead times are too long - all of which inevitably leads to rising costs.
Electronics instead of pneumatics - for the sake of the environment
True to the motto "less is more": Vario-X is driving forward the consistent electrification of manufacturing processes and opposes pneumatics with a significantly more efficient alternative. With an efficiency of only around ten to 20 percent, air as an energy source literally wastes a lot of energy.
Replacing pneumatics with electrics - for example, clamping units in body-in-white production - has advantages for everyone. The manager can reduce the inefficient, poorly controlled, and relatively expensive pneumatics in his factories. The production planner can now focus on one power source - electricity. The employees can finally work in a noticeably quieter environment.
Last but not least, the environment as energy consumption or CO2 emissions of an average production facility with twelve units are significantly reduced after the conversion from pneumatics to electrics. Additionally, the power supply in the Vario-X system is regenerative, so that energy can be recovered from the system and fed back into the grid. Vario-X is an important building block on the way to a CO2-neutral factory.
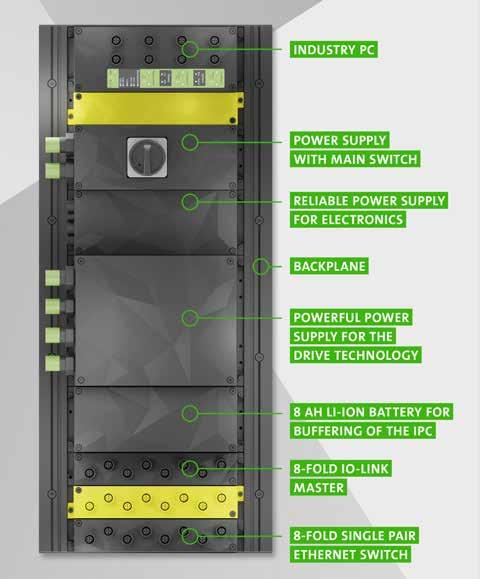
At the heart of Vario-X are IP65 rated robust, waterproof and dustproof housings, in which the power supply, controller, switches, safety technology and IO modules are installed.
100% automation without control cabinets - 40% faster installation
With Vario-X, device installation and cabling works off of the “plug-and-play” principle. By using pre-assembled, error free M12 and MQ15 connectors installation happens in a much shorter time frame. Expensive M23 connectors are no longer needed.
The pre-assembled connectors also eliminate the need for time-consuming and expensive installation work (stripping, setting wire end sleeves and clamping) on the control cabinet. If one station is not sufficient for the entire machine control system, additional stations, like an additional power supply, can be placed on the machine and interconnected without any problems. Individual IO modules can also be installed directly on the devices without a backplane in order to collect signals directly. This slims down the machine attachments and streamlines the cable architecture enormously.
Technology article by Murrelektronik.