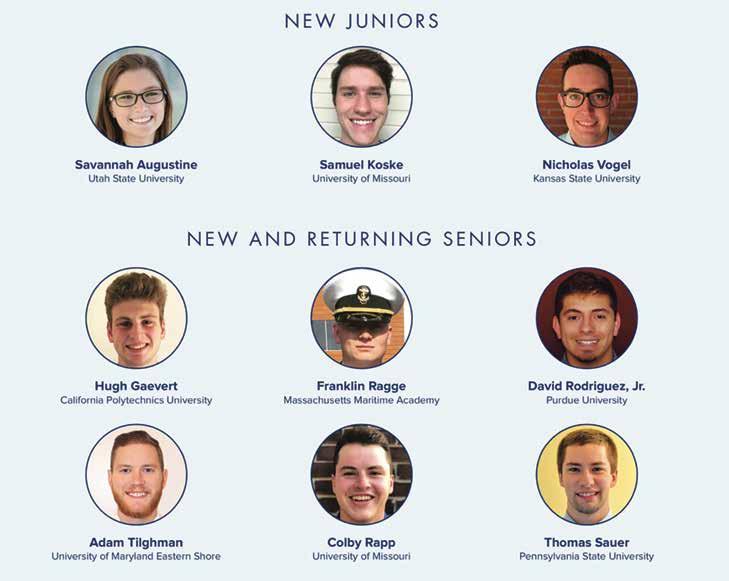
6 minute read
Lesson Learned
As Port sees it, the conference invitation is one of the biggest benefits of the scholarship program. Students have a direct connection to the industry they Ultimately, the scholarship program keeps momentum going in the industry. “The long-term benefit,” Mandato said, “as the scholarship program expands…
Bob Port, IIAR Scholarship Subcommittee Chair
are studying and to meet with industry professionals one-on-one. “I tell everyone to bring a stack of resumes with them” Port laughed. “I haven’t met a kid yet that wasn’t blown away.” as the list [of recipients] grows and there’s greater awareness within academia about the industry, those people who are responsible for the placement of graduating students from their various universities will be more likely to introduce the industry to them.”
The students who receive these scholarships are impacted positively, and their gratitude is apparent. “The IIAR Founders Scholarship has made an incredible impact in my career as an engineering student. By receiving this award, I am under less pressure to work extensive hours on top of my studies, and have avoided taking out student loans,” Samuel Koske, a junior at the University of Missouri who received a scholarship this year, said in a statement. “This scholarship has also given me an incredible opportunity to connect with companies and learn more about the natural refrigeration industry,” Koske added. “After I graduate, my hopes are to eventually make cheaper and safer ways to make ammonia/natural refrigeration a more widespread technology throughout the world.”
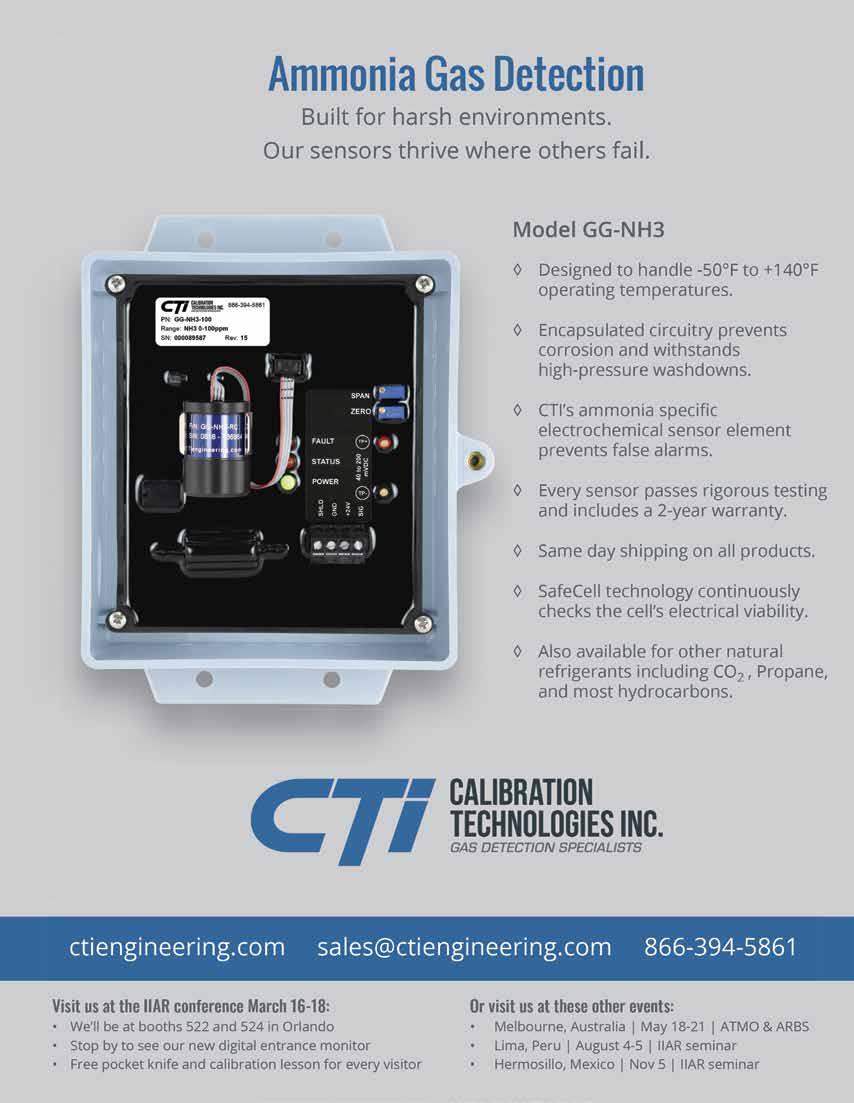
What? I didn’t know that BY KEM RUSSELL
LEARNED? LESSON recently read an article about a man that spent a considerable amount of time tromping through the wilderness back in the early 1900s. In his journal he made a statement that I found interesting. He wrote, “I don’t know where I am, but it doesn’t matter.” I am concerned when someone doesn’t know where they are or what is going on, and they think it “doesn’t matter.” I think it can matter a lot where you are, and what you know when you are there. On this man’s last trip in the wilderness it certainly did matter to him. He was found some weeks later after drowning in a river. This man’s statement got me thinking about something I have run into numerous times, where people don’t know something and they also don’t realize it really does matter.
If you are in the design and construction field of industrial ammonia refrigeration, you have probably experienced this. You design most, if not all, of the ammonia refrigeration system. You properly size equipment for the intended load(s), properly size and configure piping, correctly select control valves as well as hand valves, properly size vessels, etc. You do everything needed for the ammonia system to function correctly. However, there are some items and work associated with the ammonia system that you may not do, but you are aware of what is required. Those items and that work may be done by a General Contractor, or some other contractor or sub-contractor. If the items are not done correctly the facility owner, who is relying on more knowledgeable people to do the right thing, may have serious challenges. The “Authority having Jurisdiction” may not agree with what was or wasn’t done, and require corrective action. Or at a later date, OSHA and/ or EPA may site the missing items for corrective action, along with a fine. The issues involve the ammonia machine room, and what should be part of the machine room design. I have run into this many times over several decades of design and construction, and I experienced this same issue again just recently when a knowledgeable refrigeration operator asked me what should be included in the machine room design. For industrial ammonia refrigeration the standard for safe design is ANSI/IIAR 2-2014 Addendum A (2019). I have been surprised time and again at how many people do not know about some of the key safe design standards in this document. Here are some of those key safety items that we should all know and understand: • Ammonia detection and alarming. Almost everyone, but not all, realize there should be ammonia detection in the machine room. Beyond that, understanding of what should be in place gets fuzzy. ANSI/IIAR 2 2014 Addendum A, paragraph 6.13.1 states: 6.13.1 General. Machinery rooms shall be provided with ammonia detection and alarm in accordance with Sections 17.2–17.6 and the following features: 1. At least one ammonia detector shall be provided in the room or area. 2. The detector shall activate an alarm that reports to a monitored location so that corrective action can be taken at an indicated concentration of 25 ppm or higher. 3. Audible and visual alarms shall be provided inside the room to warn that access to the room is restricted to authorized personnel and emergency responders when the alarm has activated. Additional audible and visual alarms shall be located outside of each entrance to the machinery room. I am guessing that many do not read, or have access to the information stated in 6.13.1.3, which states that “… audible and visual alarms shall be located outside of each entrance to the machinery room.” • Next, I think that most of the people involved in the design and construction of ammonia refrigeration machine rooms understand that there should be a ventilation system in that room, and that an ammonia detector should activate the emergency ventilation system. Beyond this, it seems knowledge and understanding are lacking, and it is not generally understood that there is more to be done. Paragraph 6.13.4 states: “Detection of ammonia concentrations that exceed a detector’s upper detection limit or 40,000 ppm (25% LFL), whichever is lower, shall activate visual indicators and an audible alarm and shall activate emergency ventilation, where required, in accordance with Section 6.14.7. Once activated, emergency ventilation shall continue to operate until being manually reset by a switch located in the machinery room. In addition, the following equipment in the machinery room shall be automatically de-energized: 1. Refrigerant compressors 2. Refrigerant pumps, and 3. Normally closed automatic refrigerant valves that are not part of an emergency control system.” Many ammonia machine rooms may have this high-level detection. Some may shut compressors down on activation of the high-level PPM. More rare are systems that shutdown other equipment and controls in the machine room. • Most machine room designs include “Emergency Control Switches”, but what that switch does can vary considerably from one facility to another. It is common that the switch shuts down the compressors, but often that’s all. As stated in paragraph 6.12.1 that switch should do the following: I


A roof-mounted, insulated penthouse air cooler for industrial applications
3 Standard Configurations:
► Complete unit
► Coil, base, fans, structural frame
► Coil with drainpan and legs only
Options:
● Fan discharge ducts
● Ammonia detection

● Custom curbs
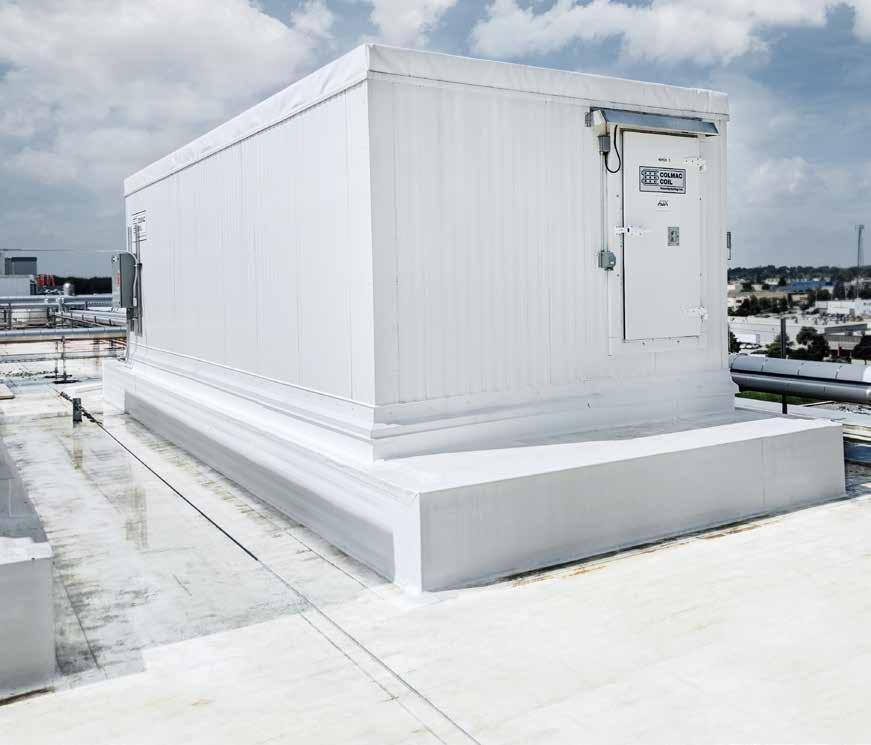