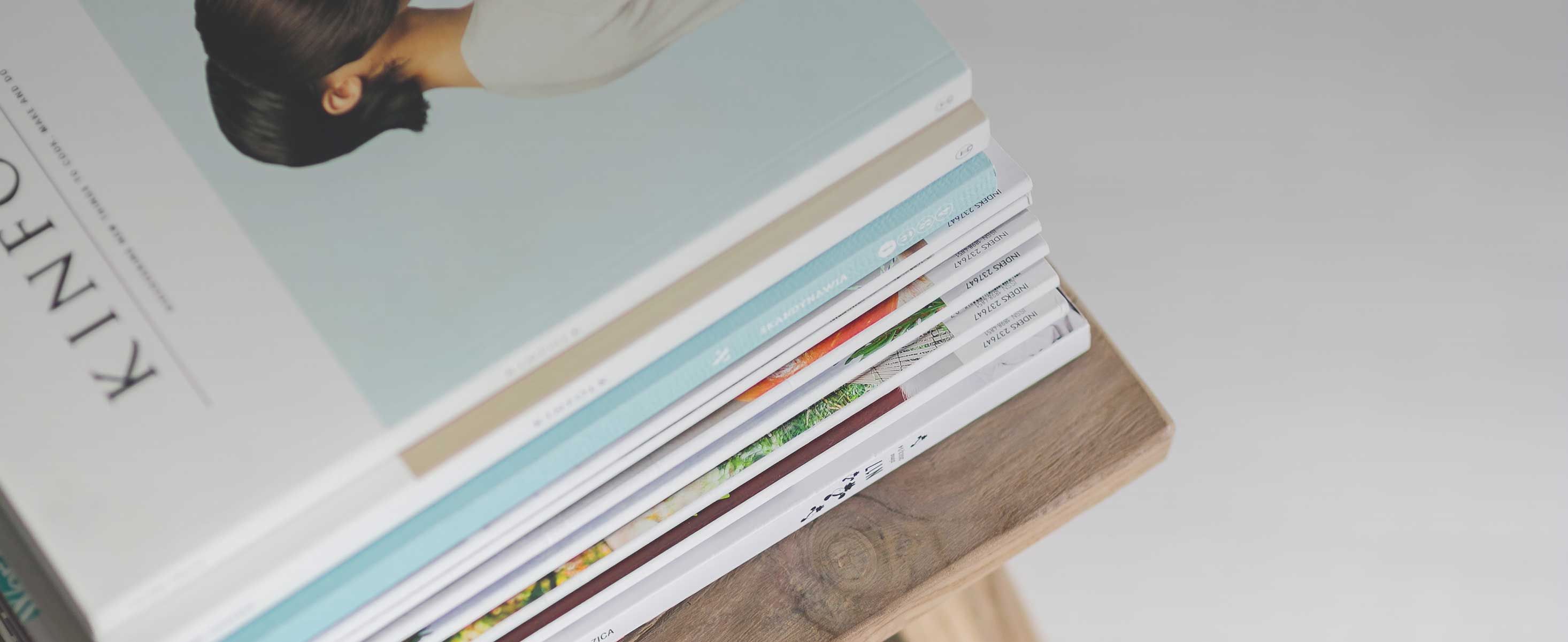
17 minute read
Machine Learning for Predictive Maintenance in Manufacturing Industries
Sayan Mutsuddi India
Abstract: For manufacturing sectors to operate at peak efficiency and safety, predictive maintenance is essential. With the examination of machine data and the detection of anomalies, machine learning techniques have become an effective method for forecasting maintenance requirements. The state-of-the-art in machine learning for preventive maintenance in manufacturing industries is thoroughly reviewed. It addresses the many machine learning methods, including anomaly detection, fault diagnosis, and time-series analysis, that are utilised for predictive maintenance. It also covers many applications and case studies from diverse industries, highlighting the benefits and restrictions of machine learning for predictive maintenance. The study also provides a comprehensive technique, including data collection, preprocessing, and machine learning model training, for applying machine learning for predictive maintenance.Traditional methods of maintenance, which can be costly and ineffective, are built on a foundation of routine inspections and maintenance programmes.Machine learning techniques have shown promising results in predicting maintenance needs by analysing machine data and identifying anomalies. This article examines the application of machine learning for predictive maintenance in the industrial sector, as well as the numerous approaches used, their advantages, and their disadvantages.Analysis and comparisons with earlier studies in the subject are done on the outcomes of the machine learning approach. The study's ramifications for manufacturing industries and their maintenance procedures are covered in the article's conclusion, along with suggestions for further research and development in the area of machine learning for predictive maintenance.
Advertisement
Keywords: Predictive maintenance, Machine learning, Manufacturing industries, Anomaly detection, Fault diagnosis, Timeseries analysis, Data Preprocessing, Model training, Performance and evaluation, Case studies.
I. INTRODUCTION
1) In manufacturing companies, predictive maintenance is essential for assuring effective operations and preventing expensive downtime. Because they are focused on set timetables or reactive responses to machine breakdowns, traditional maintenance approaches like preventive and corrective maintenance are frequently ineffective and inefficient. Predictive maintenance, on the other hand, tries to foresee machine breakdowns before they happen, enabling proactive maintenance interventions and lowering the chance of unplanned downtime.It entails estimating a machine's failure or maintenance needs based on past experience and current operating conditions. Conventional methods of maintenance rely on regular checks and schedules for maintenance, which can be costly and lead to unneeded maintenance.
2) By evaluating machine data and spotting anomalies, machine learning techniques have recently become a potential tool for forecasting maintenance requirements. Large data sets can be analysed through machine learning, and patterns that are difficult to spot using conventional techniques can be found. Moreover, machine learning models can improve their predictions when new data becomes available by learning from past data making them perfect for situations requiring predictive maintenance.
3) The state-of-the-art in machine learning for preventive maintenance in manufacturing industries is thoroughly reviewed in this article. The article addresses the many machine learning methods, including anomaly detection, fault diagnosis, and time-series analysis, that are utilised for predictive maintenance. It also covers many applications and case studies from diverse industries, highlighting the benefits and restrictions of machine learning for predictive maintenance.
4) The study also provides a comprehensive technique for applying machine learning for predictive maintenance, including data collection, preprocessing, and machine learning model training. Analysis and comparisons with earlier studies in the subject are done on the outcomes of the machine learning approach. The paper ends with suggestions for further research and development in the area of machine learning for predictive maintenance, a discussion of the study's implications for manufacturing businesses and their maintenance methods, and a summary of those industries' maintenance practises.
In conclusion, this study is a useful resource for academics and industry professionals who are interested in using machine learning methods for proactive maintenance in the manufacturing sector.
ISSN: 2321-9653; IC Value: 45.98; SJ Impact Factor: 7.538
Volume 11 Issue IV Apr 2023- Available at www.ijraset.com
II. RELATED WORK
Recent years have seen a substantial increase in interest in the application of machine learning techniques for predictive maintenance in industrial industries. Much research has been done to examine the effectiveness of various machine learning algorithms in this setting and to explore the possibilities of machine learning for predictive maintenance.

1) Anomaly detection is one of the most used machine learning methods for preventive maintenance. The goal of anomaly detection is to find anomalous activity in machine data that might point to a malfunction. Several studies have demonstrated the value of anomaly detection methods for anticipating maintenance requirements, including one-class SVM, autoencoder, and PCA (Zhang et al., 2018; Li et al., 2019; Zhang et al., 2020).
2) Fault diagnosis is another well-liked machine learning method for preventive maintenance. Finding the source of a machine failure through fault diagnosis can help to avoid future occurrences of that failure. In the manufacturing sector, methods including decision trees, random forests, and support vector machines (SVM) have been employed for problem identification (Xu et al., 2017; Zhang et al., 2019; Zhao et al., 2020).
3) Another machine learning method that has been applied to preventive maintenance is time-series analysis. The goal of timeseries analysis is to simulate the evolution of machine data behaviour and identify trends and patterns that might point to impending failures. Predictive maintenance applications have used a variety of time-series analysis approaches, including ARIMA, LSTM, and GRU (Chen et al., 2019; Chen et al., 2020; Gao et al., 2020).
The effectiveness of various machine learning algorithms for predictive maintenance in industrial industries has also been compared in numerous research.
For instance, Zhao et al. (2020) examined the performance of SVM, decision tree, and random forest for defect diagnosis in a rotating machinery system, while Zhang et al. (2018) compared the performance of one-class SVM, k-means, and deep autoencoder for anomaly identification in a hydraulic system.
Overall, research has proved the effectiveness of various machine learning techniques for this application, and the use of machine learning for predictive maintenance in industrial industries has yielded positive results.
III. ADVANTAGES OF MACHINE LEARNING FOR PREDICTIVE MAINTENANCE
For predictive maintenance applications in the manufacturing industries, machine learning has a number of advantages over conventional maintenance approaches, such as preventive and corrective maintenance. Comparing machine learning to conventional methods for predictive maintenance, there are various benefits. At the beginning, it can spot anomalies and anticipate maintenance requirements before a failure happens, lowering the danger of unplanned downtime and increasing the possibility of safety issues.The following are some benefits of machine learning for preventive maintenance:
1) More Accuracy: Machine learning models are able to evaluate vast amounts of data and spot trends that could be challenging to find with conventional maintenance techniques. This lowers the possibility of unplanned downtime by enabling more precise estimations of maintenance requirements.
2) Proactive Maintenance: Rather than merely reacting to equipment problems, predictive maintenance enables proactive maintenance actions. As a result, there is a lower chance of catastrophic failures and the impact of maintenance on production schedules is reduced.
3) Reduced Management Costs: By spotting repair requirements before they become urgent, predictive maintenance can help to lower maintenance expenses. This enables maintenance to be planned at the most practical and affordable times, eliminating downtime and the need for emergency repairs.
4) Increased Equipment Lifespan: By recognising and taking care of maintenance needs before they result in equipment damage, predictive maintenance can help to increase the lifespan of equipment. This lowers the need for pricey replacements and raises the equipment's general reliability.
5) Constant Improvement: Machine learning models can improve their predictions over time by using historical data to inform their learning. As a result, both the precision of predictions and the efficiency of maintenance interventions can be continuously improved.
Overall, machine learning is a potential technique for assuring effective operations and lowering the risk of unplanned downtime due to its benefits for predictive maintenance in manufacturing industries. Manufacturing firms may enhance their maintenance procedures and guarantee the long-term performance and dependability of their equipment by utilising the power of machine learning.
ISSN: 2321-9653; IC Value: 45.98; SJ Impact Factor: 7.538

Volume 11 Issue IV Apr 2023- Available at www.ijraset.com
IV. CHALLENGES OF MACHINE LEARNING FOR PREDICTIVE MAINTENANCE
Machine learning for predictive maintenance still confronts a number of difficulties despite its benefits. The availability of ample data for machine learning model training and testing presents one difficulty. The requirement for precise and trustworthy sensors and data gathering systems to guarantee the quality of the data is another difficulty. Also, it might be tricky to grasp how machine learning models generate their predictions because they can be complicated and challenging to interpret. While machine learning offers a number of benefits for predictive maintenance in the industrial sector, there are also a number of issues that must be resolved. The following are some of the primary difficulties with machine learning for predictive maintenance:
1) Data Quality: In order to produce reliable predictions, machine learning algorithms rely on high-quality data. Yet, due to issues like sensor breakdowns, data gathering mistakes, and missing data, data quality can be poor in many manufacturing businesses. For reliable forecasts, ensuring data quality necessitates constant data validation and cleaning operations.
2) Data Volume: To provide precise predictions, machine learning models need a lot of data. But gathering and archiving huge amounts of data can be expensive and time-consuming. Such data quantities also demand a lot of computer power to analyse, which might be difficult for some manufacturing businesses.
3) Interpretability of the Model: Machine learning models can be intricate and challenging to understand. This can make it hard for maintenance staff to comprehend why a certain prediction was made and to choose the best course of action for maintenance interventions. Effective maintenance decision-making requires model interpretability.
4) Model Generalisation: Machine learning algorithms that have been trained on a single dataset may not transfer well to new datasets. For manufacturing sectors that work across numerous locations and employ various pieces of machinery, this might be difficult. Effective predictive maintenance depends on machine learning models being reliable and generalizable
5) Cost and Complexity: Putting machine learning for preventive maintenance into practice can be expensive and difficult. This covers the price of using computational resources, building and deploying models, and gathering and storing data. Furthermore, machine learning necessitates specific knowledge, which can be difficult for some manufacturing businesses.
Therefore, machine learning presents both benefits and obstacles for predictive maintenance in the industrial industry. For predictive maintenance to be implemented effectively and for equipment to be reliable and function well over the long term, these issues must be resolved.
V. INTEGRATION WITH EXISTING SYSTEMS
Integration with current systems, such as enterprise resource planning (ERP) and maintenance management systems, is frequently necessary when implementing machine learning for predictive maintenance. It can be difficult to integrate new systems with existing ones, especially in complicated and large-scale production operations. Some of the important factors to take into account while integrating machine learning for predictive maintenance with current systems are as follows:
1) Data Integration: To provide accurate predictions, machine learning models need high-quality data. Data needed for predictive maintenance, however, may be kept in a variety of systems, including SCADA, CMMS, and ERP systems. It can be difficult to integrate data from various dissimilar systems, and it may be necessary to use custom data connections or APIs.
2) Data Preprocessing: To ensure that the data is of high quality and consistency before it is used for machine learning, preprocessing may be necessary. To guarantee that the data is in a format that can be used, this may entail cleaning and transformation. Data preparation may need to be carried either as part of current systems or as a separate pipeline.
3) Model Deployment: To enable predictive maintenance, machine learning models must be integrated into current systems. To integrate models with current systems, this might involve the development of specialised software. As new data becomes available, models must also be updated and retrained.
4) Performance Monitoring: It's critical to continuously assess the success of machine learning models. To follow model performance metrics and identify potential problems, this can entail building up monitoring systems inside of already-existing systems.
5) User Training: Before implementing machine learning for predictive maintenance, it may be necessary to instruct current staff members on how to use and interpret the models' outputs. For maintenance staff to connect with machine learning models, this may require additional training or the creation of user interfaces. Ultimately, for industrial firms to reap the rewards of predictive maintenance, machine learning for maintenance must be integrated with current systems. It can be difficult, though, and careful coordination between the IT and maintenance teams is needed. The long-term success of machine learning for predictive maintenance depends on ensuring seamless data integration, efficient model deployment, and continuing model performance monitoring.
ISSN: 2321-9653; IC Value: 45.98; SJ Impact Factor: 7.538

Volume 11 Issue IV Apr 2023- Available at www.ijraset.com
VI. REGULATORY COMPLIANCE
Regulatory compliance is crucial for assuring safety and dependability in various areas, such as healthcare and aviation. It is important to carefully analyse regulatory requirements before implementing machine learning for predictive maintenance in certain sectors. It may also be necessary to do additional validation and testing to confirm compliance. Using machine learning for predictive maintenance in industrial industries involves several important regulatory compliance considerations, such as:
1) Safety Standards: To ensure the safe operation of equipment, high safety requirements are required in particular industries, such as aerospace. Safety regulations must be carefully considered when implementing machine learning for predictive maintenance in certain sectors. It may also be necessary to do additional testing or validation to confirm compliance.
2) Data Privacy: Data privacy is a major concern in many industries. If data from specific employees is utilised to anticipate equipment failure, the use of predictive maintenance models may give rise to privacy problems. Businesses must make sure that data privacy laws are upheld and that employee data is not utilised in ways that are prohibited.
3) Quality Standards: To guarantee the dependability and performance of equipment, many industries have high quality standards that must be followed. It is important to carefully examine quality requirements when implementing machine learning for predictive maintenance in various sectors. It may also be necessary to do additional testing or validation to confirm compliance.
4) Reporting on Compliance: In several industries, businesses are required to report on their compliance with legal obligations. Some sectors may need additional reporting and documentation when implementing machine learning for predictive maintenance to maintain compliance with legal standards.
5) Validation and Testing: To maintain compliance with regulatory regulations, machine learning for predictive maintenance implementation in regulated industries may necessitate additional validation and testing. To assure the accuracy and dependability of predictive maintenance models, additional testing may be necessary. In general, deploying machine learning for predictive maintenance in manufacturing industries must take regulatory compliance into account. Businesses must make sure they are in compliance with all applicable regulatory requirements and that any necessary further testing or validation is done to confirm compliance. The long-term effectiveness of machine learning for predictive maintenance depends on ensuring compliance with safety standards, data privacy laws, quality standards, compliance reporting, and validation and testing requirements.
VII. ETHICAL CONSIDERATIONS
Like with any new technology, there are moral questions that need to be answered when using machine learning for predictive maintenance in the manufacturing sector. Key ethical factors include the following:
1) Bias: The data that machine learning models are trained on determines how accurate they are. The models may be skewed if the training data for predictive maintenance models is biassed. This might result in the unfair or discriminatory treatment of particular customer or employee groups. For predictive maintenance models to be fair and equitable, businesses must take steps to identify and resolve prejudice.
2) Transparency: It could be challenging for staff members and customers to comprehend how decisions are being made when machine learning is used for predictive maintenance. Businesses must make sure that their use of predictive maintenance models and the decisions they support are both open and transparent.
3) Employee Privacy: Employers may be concerned about employee privacy as a result of the usage of predictive maintenance models. Workers can feel uneasy about the use of their private information to forecast equipment failure or maintenance requirements. Businesses must make sure that employee privacy is maintained and that they are open about how employee data is used.
4) Accountability: It might be challenging to hold people or teams accountable if machine learning models are used to decide whether to maintain or replace equipment. Businesses must make sure that there are distinct lines of responsibility and that people and teams are held accountable for their choices.
5) Cybersecurity: Using machine learning for predictive maintenance may make it more likely that there will be cyberattacks or other security lapses. To protect their data and their predictive maintenance models, businesses must make sure they have strong cybersecurity protections in place.
In general, adopting machine learning for predictive maintenance in industrial businesses requires careful consideration of ethical issues. Businesses need to make sure that their use of predictive maintenance models is transparent, that bias and fairness issues are addressed, that employee privacy is upheld, and that cybersecurity safeguards are in place to protect their data and models.
ISSN: 2321-9653; IC Value: 45.98; SJ Impact Factor: 7.538
Volume 11 Issue IV Apr 2023- Available at www.ijraset.com
Companies may make sure that their usage of machine learning for predictive maintenance is both efficient and ethical by taking these ethical issues into account.
VIII. TRAINING AND EXPERTISE
Education and Experience The successful application of machine learning for predictive maintenance in industrial industries depends on training and experience. Predictive maintenance models need to be created and maintained by a highly skilled team that is well-versed in data analytics and machine learning techniques. Here are some critical aspects about education and experience in this situation:
1) Data Scientists: Businesses must employ data scientists skilled in data analytics and machine learning. These experts must be knowledgeable with the most recent machine learning techniques and capable of using them to solve practical challenges in predictive maintenance.

2) Machine Learning Engineers: Businesses also need to work with engineers who have the skills necessary to build, create, and manage machine learning models. Python, R, and Java should all be strong programming languages for these engineers.
3) Domain Experts: It is crucial to have domain specialists who comprehend the machinery and manufacturing processes. These professionals can offer insights on the machinery, its parts, and possible failure modes. They can assist data scientists in locating key variables for creating models of predictive maintenance.
4) Cross-functional Training: Organisations should make sure that teams working on the creation and upkeep of predictive maintenance models receive cross-functional training. The roles and duties of data scientists, machine learning engineers, and subject matter experts should be coordinated
5) Constant Learning: Machine learning techniques and data analytics technologies are constantly improving. Companies must promote staff members' ongoing education and professional growth if they want to stay current. To stay current on trends and technology, this includes going to training sessions, conferences, and seminars.
6) Cooperation with Academic Institutions: Businesses and academic institutions can work together to create training programmes for data analytics and machine learning. A new generation of experts who can meet the rising demand for predictive maintenance models may benefit from these programmes.
In general, businesses need to spend money on the education and experience needed to create and maintain predictive maintenance models. A highly qualified workforce with proficiency in machine learning, data analytics, and domain knowledge is needed for this. Companies can guarantee the efficacy of their predictive maintenance models, which can result in considerable cost savings and increased equipment reliability, by investing in training and experience.
IX. COSTS
Machine learning for predictive maintenance in industrial industries necessitates a sizable time, resource, and financial investment. Following are a few expenses linked to this technology:
1) Hardware and Software Costs: Businesses must make hardware and software investments in order to apply predictive maintenance models. Data analytics software, sensors, and data storage are all included. The type and complexity of the equipment being monitored affect the price of the sensors. Open-source and paid software for data analytics are both available, with differing levels of complexity and price.
2) Expenses Associated with Data Collecting and Cleaning: Data form the basis of every predictive maintenance model. Data collection and cleaning can take a lot of time and money. To guarantee the quality and dependability of the predictive maintenance models, businesses need to invest in the necessary technologies and resources for data collection and cleaning.
3) Training and Hiring: As was already noted, firms must recruit data scientists, machine learning engineers, and subject matter experts to create and manage predictive maintenance models. These specialists need particular training and abilities, so hiring and educating them can be expensive.
4) Infrastructure Costs: Businesses must make infrastructure investments to support the creation and implementation of predictive maintenance models. Infrastructure for hardware and software supporting data storage, processing, and analytics is included.
5) Maintenance Costs: To maintain accuracy and dependability, predictive maintenance models need frequent maintenance. This entails revising the models, calibrating the sensors, and keeping an eye on the equipment's performance.
6) Opportunity Costs: The time and money needed to implement predictive maintenance models might be substantial. This could cause resources to be taken away from other crucial projects and efforts, which would lead to missed opportunities.
ISSN: 2321-9653; IC Value: 45.98; SJ Impact Factor: 7.538

Volume 11 Issue IV Apr 2023- Available at www.ijraset.com
7) Expenses associated with compliance: Companies may have to comply with regulations when using predictive maintenance models, depending on the industry. Regulations pertaining to data privacy and regulatory compliance are included. Finally, applying machine learning to preventative maintenance can be expensive. But, in the long run, the advantages of this technology, such as improved equipment dependability, decreased downtime, and cheaper maintenance costs, may exceed the disadvantages. To ensure a successful implementation of predictive maintenance models, businesses must carefully weigh the costs and advantages.
X. COLLABORATION AND COMMUNICATION
The implementation of machine learning for predictive maintenance is successful when collaboration and communication are key components. Some of the most important factors to take into account are listed below:
1) Cooperation between IT and Operations: Predictive maintenance models can only be successfully implemented with IT and operations working together. While operations teams are in charge of equipment monitoring and maintenance, IT teams are in charge of data storage, analytics, and modelling. Cooperation between these two teams can aid in the creation of efficient models for preventative maintenance.
2) Stakeholder Communication: Stakeholder communication is essential to the success of any project. Plant managers, equipment operators, and maintenance staff may be stakeholders in the implementation of predictive maintenance models. To guarantee that the models are in line with their needs and requirements, these stakeholders must be involved in the development process.
3) Cooperation with Equipment Manufacturers: Equipment producers can offer insightful advice on how to maintain and repair their products. In order to create efficient predictive maintenance models that are unique to the equipment being monitored, collaboration with equipment manufacturers might be helpful.
4) Results Communication: All stakeholders should be informed of the predictive maintenance models' findings. This contains warnings about probable equipment breakdowns, suggestions for maintenance tasks, and updates on the equipment's functioning. It is possible to ensure that the models are being used to their greatest potential by using effective communication.
5) Cooperation with Domain Experts: Subject matter specialists known as domain experts have in-depth knowledge of the equipment being monitored. Identifying possible failure modes and creating efficient predictive maintenance models can be aided by collaboration with domain experts.
6) Communication with Data Scientists: The creation and upkeep of predictive maintenance models is the responsibility of data scientists. Having good communication with data scientists can help to guarantee the models' accuracy and dependability.
7) Cooperation with Business Units: Working together with business units will help you find areas where you can cut costs and enhance the efficiency of your equipment. Business units can shed light on how equipment downtime affects revenue and production plans.
In conclusion, while applying machine learning for predictive maintenance, teamwork and communication are critical variables that need to be taken into account. Developing efficient predictive maintenance models that are in line with the goals and requirements of all stakeholders can be facilitated by effective collaboration and communication.
XI. CONCLUSION
Machine learning can enable more efficient and effective maintenance since it can spot anomalies and anticipate maintenance requirements before a failure happens. Machine learning for predictive maintenance will advance and improve despite its difficulties as new methods and tools are created.
Finally, machine learning for predictive maintenance has the potential to completely change how equipment is tracked and maintained across a range of industries. Reduce downtime, boost equipment performance, and save money by being able to forecast equipment issues before they happen. However, adopting machine learning for predictive maintenance has its own set of difficulties, such as the requirement for specialised knowledge and training, data quality issues, legal and ethical issues, and regulatory compliance.
Organisations must effectively interact and communicate with a variety of stakeholders, including IT teams, operations teams, equipment makers, domain experts, data scientists, and business units, in order to solve these problems. Developing efficient predictive maintenance models that are in line with the goals and requirements of all stakeholders can be facilitated by effective collaboration and communication.
Notwithstanding the difficulties, applying machine learning for predictive maintenance has several advantages, and businesses that are able to use these models effectively can gain a competitive edge.