Multi Axis Electric Motion
What to know, what to consider

Norgren – Breakthrough Engineering
The challenges and problems the world faces grow ever more complex. Businesses demand fresh thinking and new approaches to successfully tackle fundamental issues such as climate change, rapid population growth and using technology to improve the quality of lives.
Breakthrough Engineering is at the heart of Norgren’s offering and is an integral element in driving the essential systems we all rely upon.
From improving speed, productivity, reliability, and efficiency of equipment, to generating significant energy and cost savings, or lowering total cost of ownership across many industries - Norgren’s solutions are designed to help customers pursue progress, achieve new goals, and overcome problems.
Norgren offers insight, technical excellence, and a true collaborative approach to help organisations forge a brighter future by breakthrough engineering for a better world.

Breakthrough Engineering for a Better World
Introduction
When it comes to motion control and the need to move, place, and position components as part of an automated response, linear and multi axis electric motion solutions* complement traditional pneumatic-driven options.
The growth in electric motion is set against a background of heightened application complexity. Demand for cost-efficient, but customised products are growing, addressing the need for flexibility within manufacturing processes. Furthermore, the need for data insight and system connectivity influenced by Industry 4.0, is intensifying.
Inherently, configurable, and flexible, multi axis electric motion systems are utilised across a diverse set of industrial sectors, including material handling, packaging, food production, chemical processing, and pharmaceuticals, as they seek the most efficient and effective way in which to move, position, and drive fundamental parts of their processes.
With its wide spectrum of potential solutions, multi axis electric motion has the flexibility to satisfy the often-disparate needs of individual applications, whether as part of an OEM machine build project, or enhancing the efficiencies and output of a busy production line.
For this reason, it is important to correctly identify and specify electric motion solutions based on specific needs and decide upon a standard or more customised response according to the application requirements. This whitepaper highlights the key application and specification objectives facing engineers for whom multi axis electric motion solutions are potentially attractive.
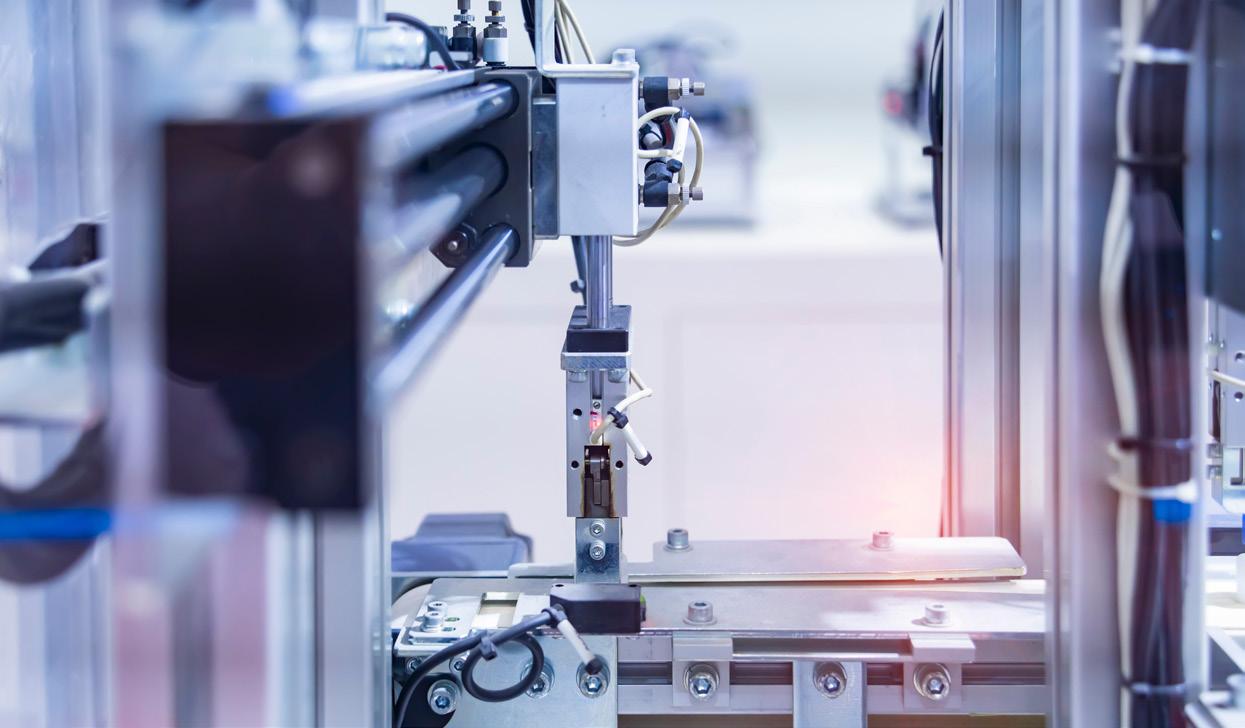
Automation plays a vital role across many of today’s industrial applications, offering operational efficiency, accuracy, reliability, repeatability, speed, cost-effectiveness, and improved safety benefits, as well as control and monitoring of machine and manufacturing performance.*Multi axis systems, alternatively referred to as cartesian robots or TTT Robots refer to mechanical movement systems normally operating across 2 (xy) or 3 (xyz) axis. For this white paper, these are referred to as Multi Axis Electric Motion.
Benefits of multi axis electric motion systems
They include:
Moving heavy loads
General purpose industrial robots often carry a limited load compared to equivalent multi axis systems because they carry the load on an outstretched arm. For machining centres that lift loads above 100 kilograms, this can be an issue. Multi axis electric motion systems offer the capability to move larger and heavier loads over longer distances.
Orientation / mounting position of the system
If the application only requires movement in a few axes, multi axis electric motion solutions can be mounted overhead and out of the way, making the best use of tight installation spaces.
At the same time, the system can be equipped with additional components such as grippers or rotary modules to obtain more axes of motion and meet the requirements of the application.
Dynamics
An important consideration for pick-and-place applications is acceleration times over long distances. Multi axis electric motion solutions can accelerate at 5 m/s2 or more, rivalling the performance of SCARA and six-axis robots. They are also useful for long-span applications where systems can be converted and extended to 20m lengths. Finally, speed, force and distance requirements can be further customised by selecting a belt, linear motor, or ball screw solution as appropriate.
Accuracy and precision
End users and specifiers can achieve or change the level of multi axis system accuracy by selecting the appropriate actuator. Ball screw driven axes provide positional repeatability of 0.02mm, but if lower repeatability of 0.1mm is acceptable, users can save costs by changing to a toothed belt driven axis. For some applications, a pneumatic solution may provide the best value solution.
Precision is key in high-end applications such as machine tools. Multi axis electric motion solutions with high-precision linear bearings are an ideal fit as they offer a balance of high performance characteristics across key parameters such as repeatability, load capacity, acceleration and cycle time.
When compared with industrial robots, multi axis electric motion systems offer several operational benefits that can help with appropriate specification choices.
Key multi axis electric motion specification considerations
The decision to opt for a pneumatic or multi axis electric motion solution depends upon operator needs. Increased complexity of motion tasks and system monitoring requirements is seeing electric motion emerge as a preferred specification route.
Some common industrial issues and potential Norgren multi axis electric motion solutions include:
Environmental conditions should determine the combination of drive and guide component specification for a multi axis electric motion system. Application machinery can often be subject to contamination and adverse environments and in such cases, linear axes with robust roller guides and toothed belt drives are particularly well suited for this purpose. An appropriate product solution here is the ELZ series.
I
with component weight
The mass to be moved often determines the dimensioning of the axis system and has significant influences on the overall machine size. The handling of small and light components, for example, requires fast and reliable movement and products from the ELZI series with toothed belt drives are efficient in such cases. Conversely, heavy loads and/or high moment forces would be better served with the heavy duty DSZ series.
The type of application in question determines the speed and the required precision. For simple handling of components for transfer to the next production process, highly dynamic linear units can be used to ensure high output levels. Compact and fast drives such as the LLZ series are a popular choice in such cases.
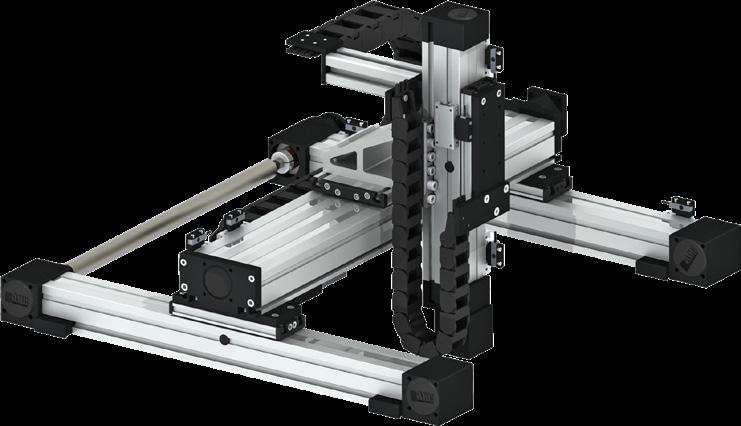
Precision and accuracy are my key concerns
The machining of sensitive electrical components or filling in pharmaceutical production may require high-precision applications. For this purpose, the systems used must operate with maximum accuracy. Here, many applications rely on very precise ball screws in combination with rail guides such as seen in the QSK series for low to medium loads, or DSK series where heavier loads are a requirement.
If short distance travel and highly precise adjustment of a workpiece are required, short spindle drives offer the best solution. Depending on the application, linear axis such as the QST/QSK series can be equipped with trapezoidal or ball screw spindles to provide the most accurate positioning over short distances.
A sustainable production process needs to address energy consumption and energy costs. Some manufacturers are replacing pneumatic components with electric linear units, including multi axis capability to support this objective. Due to the comparatively high efficiency and lower energy costs, electric linear units are generating much interest in automation applications.
I have a challenging operating environment
I need a speedy and repeatable solution
I only have to move components a short distance
I would like to address my energy consumption and look for energy cost savings
must deal
and loading parameters
Collaboration with Norgren
Norgren’s collaborative and expert team of application engineers offer in-depth and sector-specific experience, allowing them to quickly identify customer challenges and recommend the correct solution. Through a partnership approach, priority identification is speedy and the product solution selection process is rigorous and proven.
Norgren’s recently expanded range of multi axis electric motion solutions now offers a comprehensive portfolio of standard mechanical linear cylinders that can also be customised for custom application needs.
Taking a ‘solution agnostic’ viewpoint, Norgren’s engineering team will always match the best solution to meet the primary application requirement as identified.
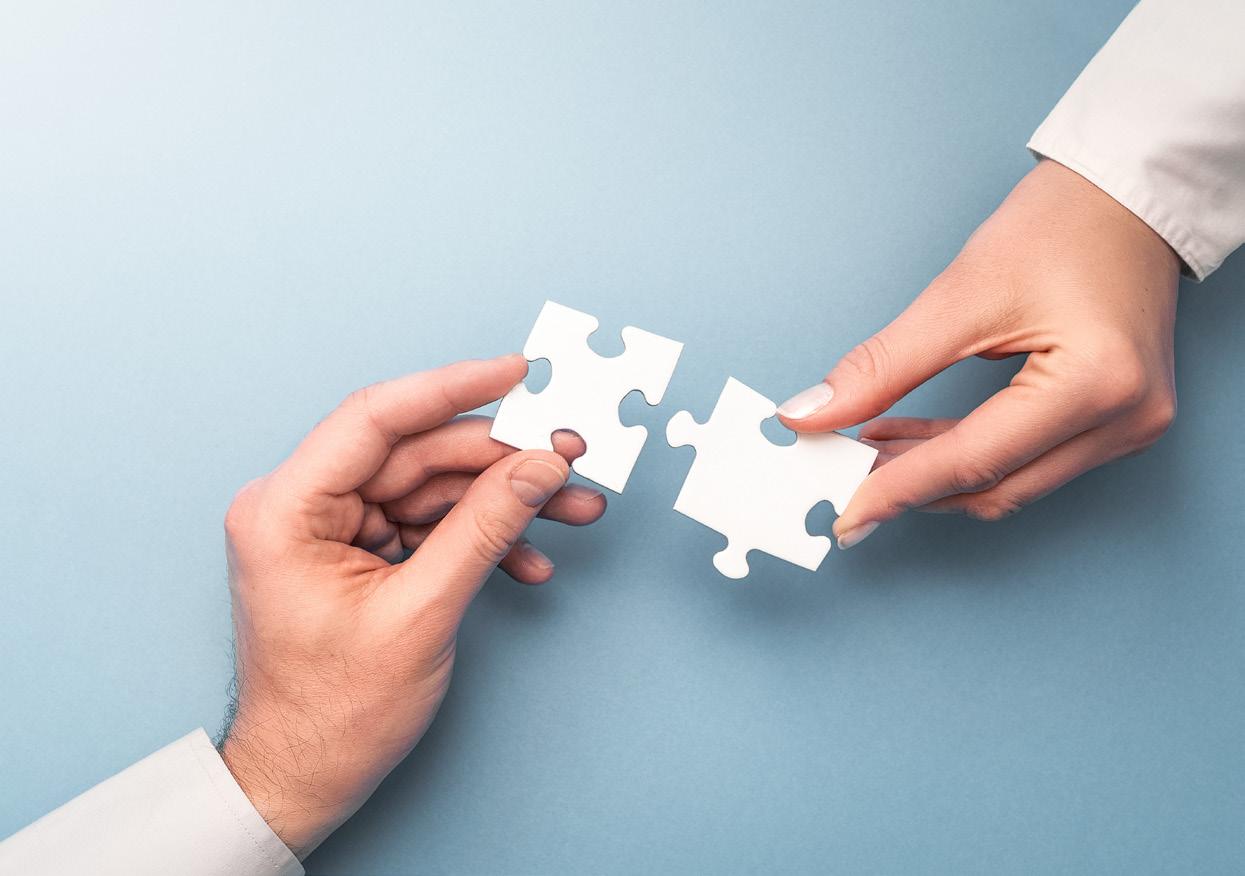
By providing 1,000 standard electric motion components resulting in over 100 million linear and multi axis configurations, Norgren can cater for every identified automation application need.
To see how Norgren’s expanded range of multi axis electric motion solutions can help meet your automation application requirements, however small, intricate, large scale, or complex, please visit www.norgren.com
Identifying challenges and delivering the best multi axis electric motion solution from a newly expanded range.
Norgren operates four global centres of technical excellence and a sales and service network in 50 countries, as well as manufacturing capability in Brazil, China, Czech Republic, Germany, India, Mexico, UK and the USA. For information on all Norgren companies visit www.norgren.com
Supported by distributors worldwide.
Norgren, Bimba, Buschjost, FAS, Herion, Kloehn and Maxseal are registered trademarks of Norgren companies.
Due to our policy of continuous development, Norgren reserve the right to change specifications without prior notice.
z10110WP en/08/23
Selected Images used under license from Shutterstock.com
For further information, scan this QR code or visit www.norgren.com
