
2 minute read
Application: Pneumatic Cylinder
Applications
Pneumatic Cylinder
Pascal Series K's User Interface streams pressure data from both sensors every millisecond and temperature data every second providing a deeper understanding of how the system is performing and guiding enhancements to the efficiency of your machine by optimising air usage.
What does Pascal Series K detect?
Presence of Cap End Seal Leakage
» Pressure Leakages would be detected by sensor 1. » The Pascal K also has the capability of measuring extent and retract time. » As leakage is present at the cap end seal, extension time is slower and retraction time is faster
Presence of Rod End Seal Leakage
» Pressure leakages would be detected by sensor 2 » Leakage at Rod end seal causes slower retraction time and faster extension time.
Presence of Piston Seal Leakage
» Pressure leakages would be detected by both sensor 1 and sensor 2. » Leakage at Piston seal causes slower retraction time and slower extension time.
Pressure inlet
Sensor 1
Sensor 2
Quick disconnect coupling
Quick disconnect coupling

Case Study #1
Leakage detection in construction production line
Leakage in production lines is common in manufacturing productions, and results in long-term operating costs and inefficiencies. To prevent this, our customer, a lead in construction supply, started to utilise Pascal Series K to detect any leakage from cylinders installed in their plant. This will also help to test for leakage from any existing cylinders prior to installing them back into the operation line.
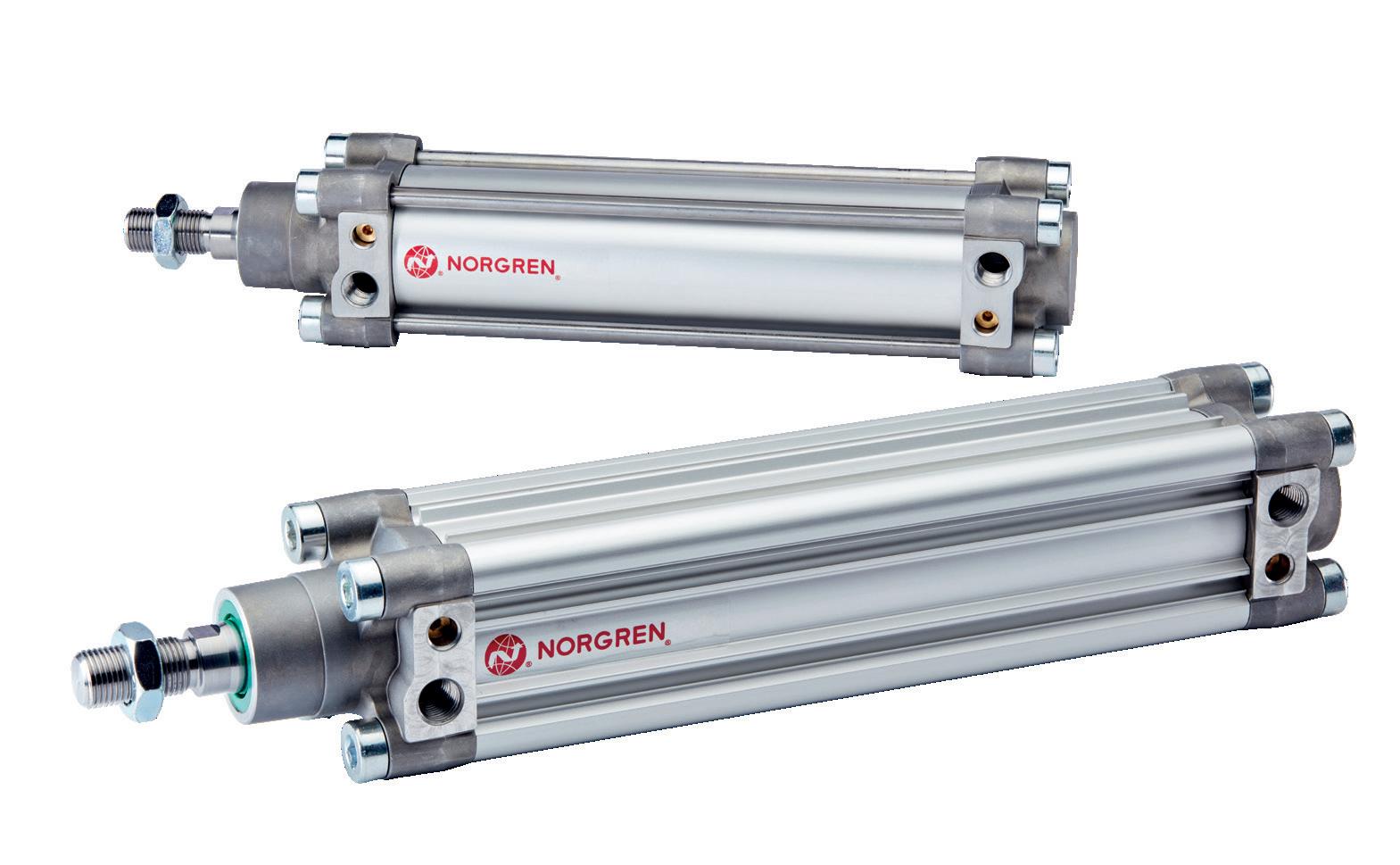

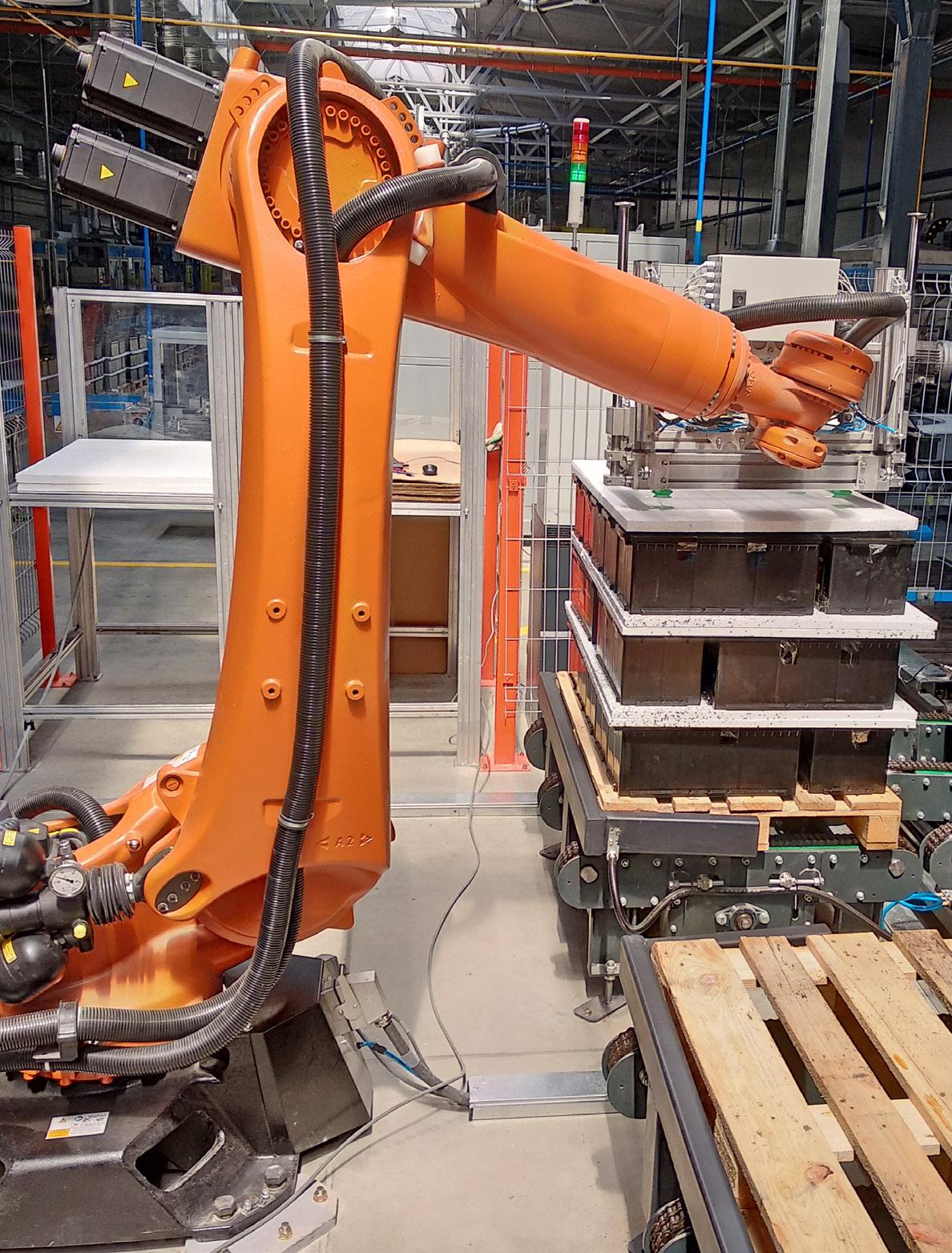
Case Study #2
Downtime reduction in packaging line
At a manufacturing plant owned by our customer, a robotic palletizer resides at the end of a packaging line. Two pneumatic actuators are used to open and close the end of the arm tool to move cases of oil. As actuators tend to wear down overtime, the gripper does not open fast enough during the packing process and this results in misplaced cases. If this situation is left undetected in time, the palletizer will drop cases creating an oil spill. This would create significant downtime to repair the pallitizer and to clean the oil spill in the plant.
To prevent downtime situations in the future, our customer equipped the use of Pascal Series K to monitor the actuators controlling the gripper. By monitoring the stroke time, they can now replace the actuators prior to failure.