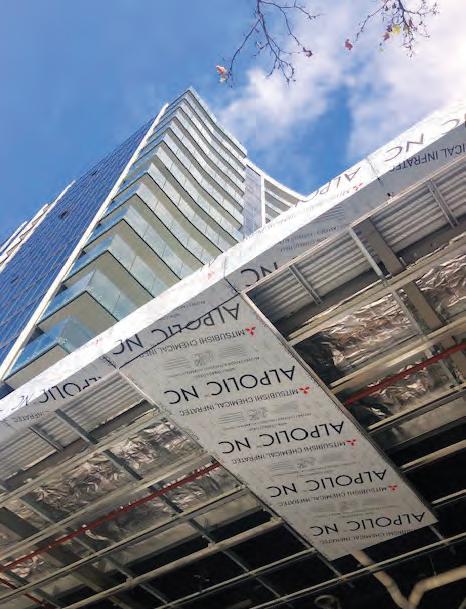
2 minute read
Comprehensive fire safety remediation project with Mitsubishi’s ALPOLIC™ NC/A1
As high-rise buildings continue to transform Australia’s skyline, fire safety remains a crucial concern for architects, construction professionals and building owners alike. While the use of combustible materials in the construction industry is still a significant issue, there is a greater awareness of the safety risks associated with non-compliant products – and this large residential complex in the nation’s capital exemplifies successful remediation projects that are shifting the status quo.
An upmarket apartment block in Canberra was reviewed by Risk Assessor Benjamin Hughes-Brown from Vortex Fire. The investigation aimed at verifying whether the lightweight cladding was non-combustible, and found that the product didn’t meet stringent Australian Safety Standards.

Following an independent review of two lightweight alternatives available in the market, the aluminium composite panel Mitsubishi ALPOLIC™ NC/A1 was selected as a replacement for the non-compliant cladding. This outstanding product was specified not only because of its DtS non-combustible, compliant profile, but also because of its industry-leading
Mitsubishi-backed full-cover warranty, as well as the product’s outstanding durability.
Widely considered as the most extensively tested cladding product both locally and world-wide, ALPOLIC™ NC/A1 meets the strict Australian Safety Standards, while a broad range of colours enabled the project team to select a shade that would match the complex’s existing palette.
Wainwright Facades were engaged to remove the flammable cladding product, and replace it with Network Architectural’s product. We found it very good to work with,” enthuses Joseph Wainwright, Director at Wainwright Facades. “It cuts well, we find it is easier on our drill bits, it is great to handle, and product performance is exceptional.”
Project Coordination Australia, who commissioned Wainwright Facades, had similar feedback: “Because of the ease of manufacturing, cutting, and handling of ALPOLIC™ NC/A1, the project has run much smoother and more swiftly with short-term logistics,” says Project Coordinator Alex Shaughnessy. “Because we are dealing with 330+ units and an existing client base, we’ve had to be reactive in some situations, and the ease of ALPOLIC™ to run through the machines has allowed us to respond to these issues easily.”
In addition, Network Architectural assisted with a sustainable disposal of the old, removed cladding. “Part of the requirement of the project was that the old cladding had to be removed and it needed to be recycled rather than go into landfill,” explains Joseph. “Network Architectural was fantastic in assisting us with the best solution for this and offered a returning truck to Sydney to take the removed material back to the PanelCycle Recycling Centre. This ensured the project was better for the environment and streamlined the process.”
This high-profile ACT project not only highlights the importance of thorough, independent evaluations – it’s also a testament to Mitsubishi’s ALPOLIC™ NC/A1’s unmatched fire safety credentials, outstanding quality and remarkable performance. In addition, it’s yet another course-corrected construction endeavour that advances Australia one step closer to more enduring, sustainable and safer high-rise buildings and, perhaps most importantly, cities.