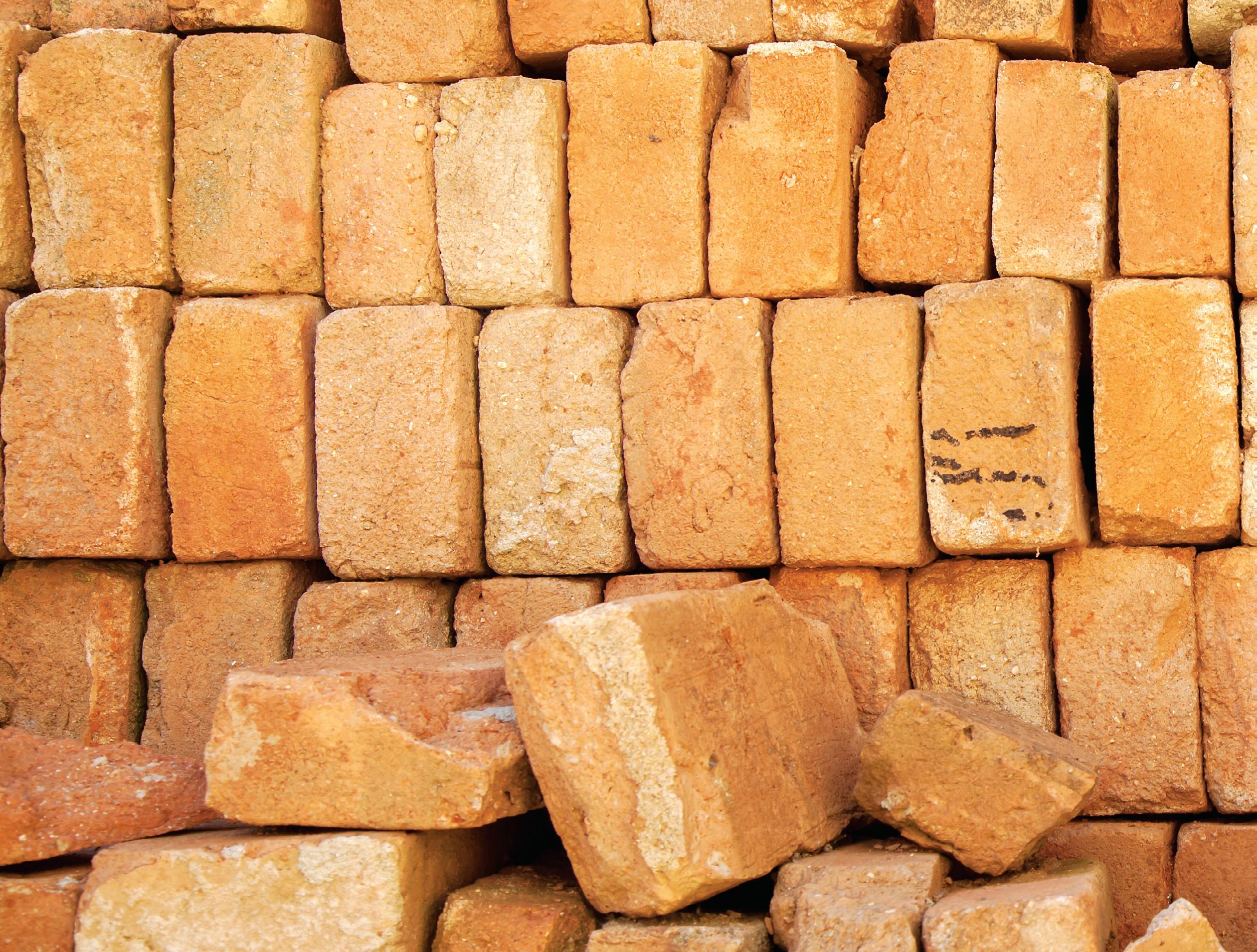
10 minute read
RECYCLING PROGRAMS
/ OCT-DEC 2022 PRACTICAL ARCHITECTURE & DESIGN / Reduce, Re-use, Recycle – waste management in the construction sector
WORDS MATT MCDONALD

While it is true that construction is a major contributor to Australia’s waste management problem, the high rates of recycling across the sector are providing grounds for optimism.
According to the Circularity Gap Report 2021, globally the mining industry extracts around 100 billion tonnes of raw material from the earth annually. As the EU notes, about half of these raw materials are used within the built environment which, in turn, contributes to more than 30% of the world’s annual waste.
Here in Australia, as the National Waste Report 2020 finds, the construction and demolition sector’s relative contribution to total waste is even higher. During 2018-19, the industry generated 27 million tonnes of waste (or 44% of the nation’s total).
Thankfully, amongst all these extraordinary figures, there is a silver lining. The report also found that, across the same period (201819), 76% of the waste generated by the local construction and demolition sector was recycled. In other words, 76% did not end up as land fill. While a figure closer to 100% would be preferable, one take-away from this is that many within the sector are already on the right track. THE SCALE OF THE WASTE PROBLEM
Equitone, a manufacturer of lightweight building solutions for the cladding of ventilated façades, is one such company.
Equitone Sustainability Product Manager, Maarten Milis openly acknowledges the scale of the waste problem. “Rather than talk our way out of it, we acknowledge the need for change and embrace it by strengthening the bridge between science and industry and connecting ideas, people, businesses and resources,” he says.
In concrete terms, the company has committed to the production of light impact materials and of zero waste to landfill by 2030.
“We’re working on developing a new generation of fibre cement by shrinking our environmental impact throughout all processes from design to production. We’re targeting zero potable water use, zero landfill, low carbon emissions and are exploring ways to increase the recycled content of our materials.
PREVIOUS TacioPhilip, iStockphoto.com RIGHT wsfurlan, iStockphoto.com
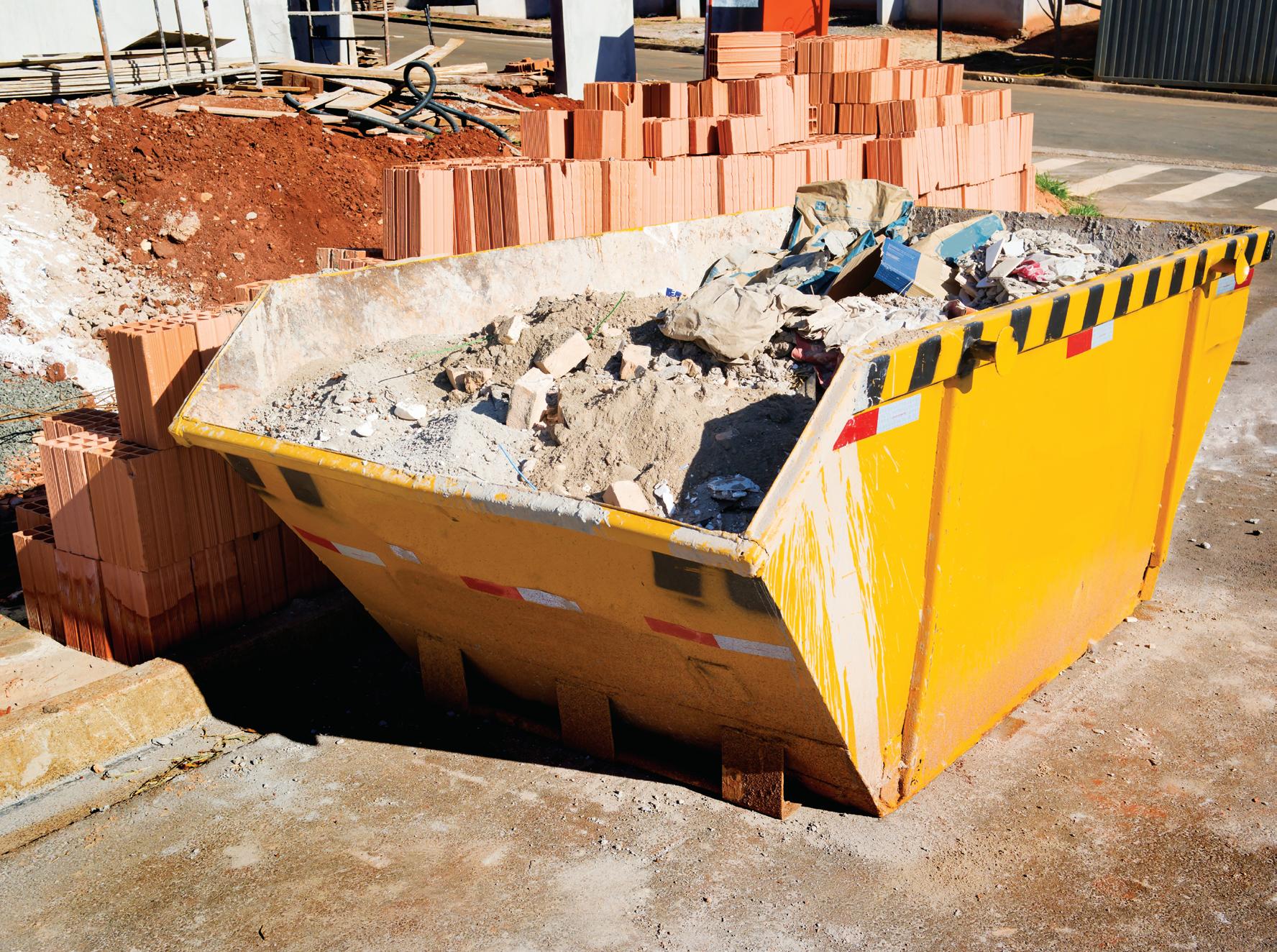
By 2030, our panels will have minimal impact on the environment and maximum durability, without compromising quality,” says Milis.
In addition, where these initiatives are concerned, the company is committed to what it calls “Radical Openness and Collaboration”. Aware of the scale of the environmental challenge, Equitone is sharing its progress and actively seeking innovative partnerships with experts in the field, including architects, academics, fabricators, and installers. The company has also organised several sustainability sessions with architects to identify the most urgent needs of its customers and define its new global sustainability commitment.
“We want to relieve architects by cutting through the spaghetti of information and give them the tools to transform the industry, one building at a time,” says Milis.
MEASURABLE WASTE REDUCTION TARGETS
In a similar vein CSR Gyprock, the manufacturer of plasterboard products, already has measurable waste reduction targets in place and recycles 95% of its manufacturing waste either back into the production process or through conversion to by-products such as soil conditioners for use in agriculture. Gyprock plasterboard products are manufactured from gypsum, paper, and a small number of additives. The paper liner board used for plasterboard and cornice is made from 100% recycled newspapers and cartons and the additives are benign materials such as gypsum, starch, and detergent. As the Investor Group on Climate Change (IGCC) pointed out in its 2007 report, Potential Earnings Impacts from Climate Change: Construction, the energy used in the manufacture of plaster products is amongst the lowest of any building product. This means that, apart from those associated with its natural gas consumption, the emissions from CSR Gyprock’s plasterboard manufacturing operations are limited to water vapour.
In terms of recycling, the company recommends that builders and contractors consider recycling their plasterboard waste. This helps the environment by reducing landfill and lowering tipping fees and site clean-up costs; and, through better resource management, also helps improve site safety.
Significantly, CSR Gyprock practices what it preaches. Its manufacturing plant in Wetherill Park, NSW features an on-site recycling service which takes clean offcuts of Gyprock Plus, Standard 13mm and Supaceil, removes the paper, and returns the crushed core back into the fabrication process. THE CIRCULAR ECONOMY
For floor covering specialist, GH Commercial the concept of a circular economy is a key influence. Interestingly, the reason for this focus extends beyond environmental considerations to economic and community concerns. According to this thinking, the handling of waste and recycling is a proven way to benefit the local economy by creating jobs and reducing reliance on supply chains that are dependent on virgin materials. As such, the company is intent on increasing the recycled content in its flooring products. For example, it is aiming to achieve 70% recycled content on average across all its carpet tiles by 2030. As it stands globally, GH Commercial’s product range already includes more than 500 items that include recycled content.
Several yarns used in the company’s products include recycled materials. For example, the Duracolor yarn, which is used in many of its premium tile products includes 30% recycled content; and the Envirobac Plus and Quickcomfort backing systems are made from recycled PET.
The company aims to use renewable fibres like wool and its Sorona fibre, which is made from over 30% biopolymer, where possible. Beyond their environmental benefits, both these fibres provide built-in stain protection, look better for longer, and deliver many other benefits to the end user.
As part of Mohawk Industries, the largest recycler in the flooring industry, GH Commercial is connected to some truly significant operations, like the plant in the US that recycles over 3 billion plastic bottles per year to be used in carpet fibre. At the same time, however, the company retains its commitment to waste reduction efforts of all types and sizes.
It already bales and recycles its finished carpet waste and is committed to developing the capacity to further process and reduce factory waste, for example by stripping remnant yarn from cones so that both the cones and fibre can be recycled. All guided by the circular economy principle, such initiatives have become commonplace at GH Commercial.
REDUCE, RE-USE, RECYCLE
It’s worth remembering that recycling is only part of the waste management story. As the case of The Brick Pit attests, whoever came up with the slogan ‘Reduce, Re-use, Recycle’ was onto something, because while it may be known as Australia’s oldest brick ‘recycler’, the company is actually more involved in the second part of the process, the ‘re-using’ of products: in this case, bricks from demolished buildings.
Another way to put that is ‘upcycling’. When pre-1950s brick structures are demolished, the bricks are rescued (instead of being crushed as demolition waste), and then upcycled for reuse in new projects. Because it does not involve the destruction of an original product to produce something new, upcycling is more energy efficient and more sustainable than recycling.
To ensure the suitability of the recovered bricks, each of them undergoes the proprietary ‘Brick Rescue’ automated cleaning process. Unique to The Brick Pit, this process ensures quality assurance and a product that is easily specified by architects and designers.
Established in 1975, The Brick Pit is still passionate about its place in the industry and continues to lead the market with its internationally patented automated brick processing system. Today, the company sits at the centre of Australia’s love affair with recycled bricks, as an authority and supplier of products that are regularly included in high profile and award-winning projects.
RECYCLED CLADDING
Façade cladding specialist, Fairview has published data on the recycling of combustible cladding at its custom-built factory in Lithgow NSW, with the impressive topline that it has diverted 309 tonnes of cladding rectification waste away from landfill projects in NSW, Victoria, and the ACT.
The Ecoloop recycled cladding plant, which is the first facility to receive and process problematic ACP material, was also able to offset 2.254 tonnes of CO2. It can repurpose any brand of at-risk or unsafe combustible cladding.
Another key statistic revealed that Ecoloop diverted a full 100% of received materials away from landfill destinations across all types of combustible cladding collected from several leading cladding brands and products.
While the facility only opened in January 2021, the report shows the valuable and very encouraging results that were attained in the premises’ first full year of waste recovery. Ecoloop became just the fifth organisation to be accredited under the Federal Government’s Voluntary Product Stewardship Scheme, for its commitment to ensuring combustible cladding components are given new life. Sustainability is becoming an important part of construction and ESG requirements for governments and for private developers alike, which makes Ecoloop a very timely initiative.
After one full year of cladding waste recycling and repurposing, the $1.6 million Ecoloop facility is demonstrating that the processing of ‘non-compliant’ cladding waste from façade rectification projects can produce tangible benefits and results.
PRECAST CONCRETE PRODUCTS
Acknowledging the civil and landscape construction sector’s increased emphasis on sustainability and the circular economy SVC Products, a specialist manufacturer and supplier of precast concrete products, has resolved to target carbon neutrality and to increase its use of recycled materials.
One example of this is the development of the company’s Ecoblox product, which involved turning the excess concrete left over from concrete mixes into modular outdoor blocks that are suitable for retaining applications or for use as weights.
In addition, almost all concrete products manufactured by SVC now include a percentage of supplementary cementitious materials (SCMs). This reduces the ratio of cement in the products and lowers the carbon emissions associated with cement production (which currently accounts for roughly 8% of global CO2 emissions). SCMs include fly ash and slag, which are byproducts of steel and iron ore production and are toxic to the environment in their natural state. Using them as a cement replacement has the dual benefits of reducing greenhouse emissions, and removing these harmful materials from circulation.
SVC has also committed to using recycled soft plastics across its civil product range. Specifically, these products will soon feature Polyrok, a lightweight aggregate that replaces natural stone aggregate, and which is made from 95% consumer-grade plastic bags collected by Coles and Woolworths. Once up and running, SVC forecasts that this initiative will prevent approximately 107 tonnes of soft plastic ending up in landfill every year. The company intends to investigate the possible roll-out of the program across its full product range.
ENGINEERED STONE SURFACES
Established in 2002, Smartstone is a leading supplier of engineered stone surfaces. Made from quartz, the second most abundant mineral on earth, these surfaces are suitable for countertops, backsplashes, walls, and so on.
Acknowledging sustainability and product responsibility as priorities, the company developed a new surface that not only reduced the quartz or silica content to a maximum of 28% but also uses recycled glass sourced from demolished buildings.
As part of its ongoing commitment to environmental responsibility products, Smartstone recently launched the low silica ‘Ibrido’ collection that sets an industry standard on many levels. Apart from its new low silica formulation, all products in the collection contain 56% recycled material.
In addition to recycled content, Ibrido also marks a turning point for Smartstone in terms of product sampling. Recognising the environmental impact of sample wastage, the company introduced Ibrido eco-sample sets with precise surface reproductions on 100% recycled cardboard and presented in bio-based recyclable vacuum pouches made using carbonnegative laminates derived from renewable plant materials.
Smartstone surfaces are highly durable, which means they last longer and need to be replaced less frequently than alternatives. In cases where a home is being renovated and a surface needs to be removed, the material can be cut and repurposed to create smaller benchtops, vanities, and so forth.
SUPPLIERS Equitone architectureanddesign.com.au/suppliers/equitone CSR Gyprock architectureanddesign.com.au/suppliers/gyprock The Brick Pit thebrickpit.com.au Fairview architectureanddesign.com.au/suppliers/fairview-architectural SVC architectureanddesign.com.au/suppliers/svc-products Smartstone architectureanddesign.com.au/suppliers/smartstone GH Commercial architectureanddesign.com.au/suppliers/gh-commercial