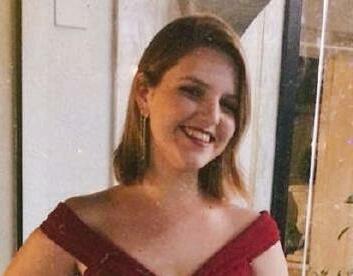
7 minute read
MARINA STOIEV & ANDRE ANDRADE
[ 152 ] | COLUMN
DIGITAL TWIN: THE KEY TO AN EFFICIENT, NET-ZERO FUTURE FOR CHEMICALS & PETROCHEMICALS
Advertisement
MARINA STOIEV
MARKETING ANALYST VIDYA TECHNOLOGY
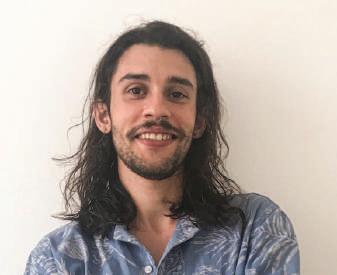
ANDRE ANDRADE
MARKETING ANALYST VIDYA TECHNOLOGY
The Chemical and Petrochemical industries are always investing in innovation. Responsible for a wide range of products used in everyday life, they manufacture products for urban, rural, and industrial use. From insecticides to medicines and even personal care, chemical industrial processes are crucial for our everyday lives. In its turn, the petrochemical sector is responsible for the production of industrial raw materials, such as natural gases and oil refinement.
As both sectors work with oil as raw material for their operation, they have on their path, difficult challenges regarding the future need for a net-zero operation. Among the main difficulties faced, there is the high dependence on oil as an input for the manufacture of its products and the combustion as an important process in the operation, culminating in the liberation of Greenhouse gases (GHG) in the atmosphere.
According to the EPA (the United States Environmental Protection Agency), the industrial sector is responsible for at least 23% of the emissions in the whole world. This data, combined with the need to mitigate climate change, culminated in international agreements, such as the Paris Agreement and the UN (United Nations) Sustainable Development Goals (SDGs). The last one is composed of 17 targets related to poverty eradication, global sustainability, improving the quality of life, and the need to zero carbon emissions up to 2050.
In spite of those challenges, the COVID-19 pandemic of 2020, culminated in significant advances in the field of biotechnology. Through research developments in this area, the chemical sector can have the opportunity to take advantage of new techniques that undermine the dependence on oil for manufacturing.
Besides this opportunity, the sector can implement technologies from digital transformation, such as Digital Twins, Artificial Intelligence, and IoT (Internet of Things) in its operation to optimize the industrial processes and comply with the goals to decarbonize its operations.
According to McKinsey & Company, operation optimization is one of the best methods to achieve net-zero emissions.
“We observe, on average, that a 10 percent increase in production efficiency
COLUMN | [ 153 ]
delivers a 4 percent reduction in emissions intensity, all else being constant [...] Predictive Maintenance and automated condition monitoring can reduce planned interventions and extended runs”
Therefore, the use of Digital Transformation technologies can generate greater control, performance, flexibility, integration, and optimization while complying with energy efficiency and sustainability goals.
CHEMICAL AND PETROCHEMICAL PROCESS AND ITS CHALLENGES
For natural resources such as water, minerals, and organic products as raw materials used to be transformed into marketable products, they need to pass through a long process of chemical transformation within the industrial plants of this sector.
The main chemical process within this industry is combustion. It is from the burning that the chemical transformations occur and give form to the non-renewable products mentioned above. However, this process is very aggressive to the environment and actively compromises decarbonization targets.
The result of this is that the sector is responsible for 7% of the world’s energy consumption and 4% of carbon emissions.
In the current economic scenario, climate change is a central issue for leading experts and investors. The subject is a matter of great debate, and its relevance has led many industries to think about strategies that change their operation towards a sustainable model, with conscientious use of natural resources, renewable energies, and good practices aligned with ESG (Environmental - Social - Government) concepts.
The sector must find ways to transform its operation to keep it running for the long term. Finding renewable energy sources is critical to reducing greenhouse gas emissions and complying with energy transition targets.
Advances in biotechnology, along with the application and development of Digital Twin technology for the O&M phase with the aim of better process control, greater energy efficiency, and accident prevention, have the potential to be the path for the reinvention of the segment.
According to data collected by Deloitte, a reference company in research: “Many chemical companies are expected to increase investment in research and development (R&D) resources and take advantage of advances in decarbonization and recycling technologies to reduce their impact on the environment and that of their customers, as well as reduce plastic waste. As a result, 2022 should see more industry players create goals and plans around reducing emissions and monetizing waste.”
This data reinforces the importance and potential that the Digital Twin has for changes in the industrial sector with the objective of decarbonization. Through development, research and innovation, industries will have the opportunity to change extremely unfavorable scenarios to carbon-free operations and processes.
But how can Digital Twin deliver greater energy efficiency with less environmental impact?
This is the question that many industries in the industrial sector have been asking lately. The answer to it is not simple, but Digital Twin technology has proven to be a great ally in the search for an increasingly sustainable operation and zero carbon.
The Digital Twin is a kind of cyber-physical system that consists of a continuous flow of data between physical elements and their digital replica.
Initially conceived by Michael Grieves in 2002, the concept is the result of a search
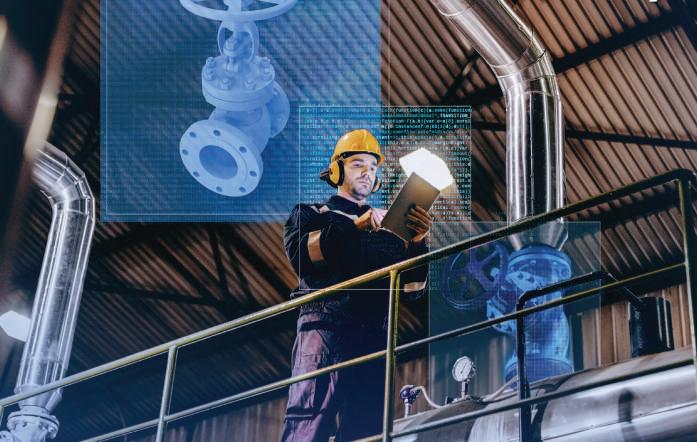
[ 154 ] | COLUMN
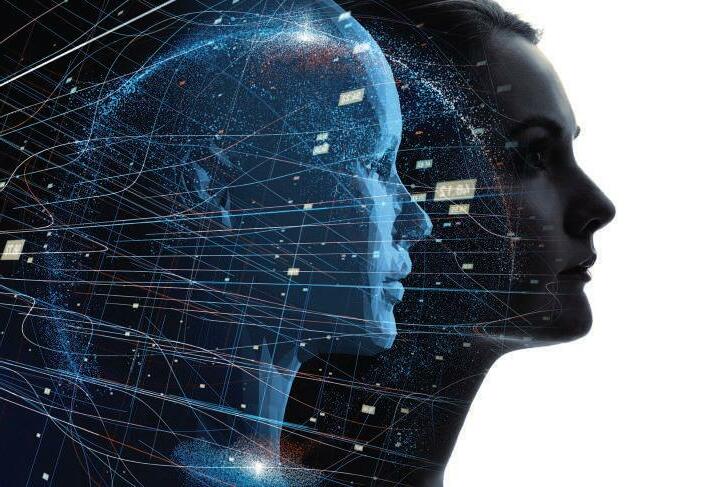
for continuous improvements in the development of projects, products, and engineering activities. It is worth mentioning that the model proposed by Grieves aimed at the possibility of satisfactory management through all phases of Product Lifecycle Management (PLM).
Although Michael was the pioneer, the first practical example of a digital twin emerged by NASA after attempts in 2010 to perform simulation testing on its spacecraft vehicles. Due to the high applicability of the technology in all phases of PLM, many industries, from manufacturing to Chemical and Petrochemicals, can take advantage of the Digital Twin for process improvement, project and product development, and even programs related to the operation and maintenance phase of a plant.
The technology uses multiple data sources as input into the system. This means that plant data is being collected and contextualized within a platform that allows managers to have easy access to critical and valuable information for decision-making and performance analysis.
Through the Digital Twin, industrial plant managers have greater control over the many variables involved in the process. Access to relevant and contextualized data can generate: • performance loss analysis • early flaw identification • asset life-cycle durability prediction • energy efficiency and consumption • the measure of the amount of gas released into the atmosphere • scheduling teams according to demand
Digital Twin: the key to a sustainable and efficient future in the Chemical and Petrochemical industries.
The Digital Twin created great opportunities for the industrial sector. Elected as a top technology by Gartner in 2019, Digital Twin has been gaining more relevance in the industrial sector thanks to the great benefits generated by its implementation.
The implementation trend is growing, and according to a report by markets and markets, the Digital Twin market was estimated to be worth $3.1 billion by 2020 and is expected to grow to $48.2 billion by 2026.
Certainly, the tendency is that more industries will implement the technology in the medium term, making it an essential tool for industries in the digital transformation movement.
NEW OPPORTUNITIES GENERATED
Digital twins can be implemented at any stage of the asset lifecycle (PLM). There are models for the design and construction phases, most common in the construction and project development industry. Another kind of application is for the operation and maintenance phase, with more attractive purposes for process industries.
This technology has a great advantage in the opportunity of total control in an industrial plant. From the implementation of this technology, industries can integrate and centralize their processes, generating greater assertiveness in the execution of activities and less time spent.
Another attractive benefit of the technology is the possibility of implementing Artificial Intelligence algorithms that along with the Digital Twin will provide insights into possible scenarios, budgets, and can also generate important information about possible failures within the operation.
Besides the benefits mentioned above, one of the great advantages of the Digital Twin is the data contextualization provided by the technology. Perhaps this is the most important benefit generated by the technology since digital processes and operations have huge amounts of data that need to be processed to be used as a generator of knowledge by decision-makers.
It is now up to the Chemical and Petrochemical sector to use the technology to improve its energy efficiency, prevent accidents and have total control over its operation and emissions. n