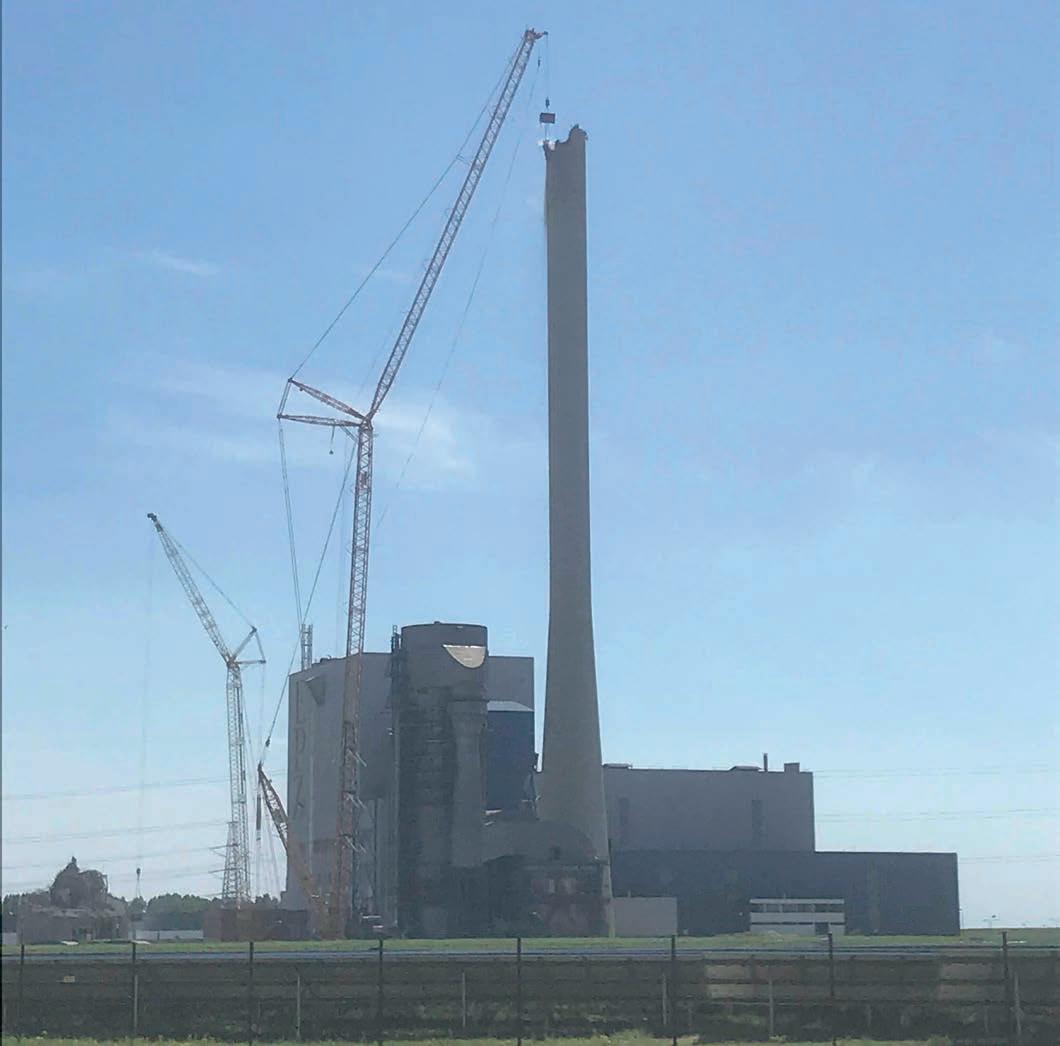
11 minute read
PROJECT Kolencentrale EPZ transformeert tot grondstof
from ILQS08-2021
Kolencentrale EPZ transformeert tot grondstof
De ontmanteling van de kolencentrale van EPZ in Borssele is in volle gang. Met een klein aantal medewerkers wordt de centrale stukje bij beetje met de grond gelijkgemaakt. Een uitdagende klus voor de sloper die op een klein terrein moet werken, direct naast een kerncentrale.
Advertisement
Dagmar Aarts
Historie kolencentrale
1969: Naast de geplande kerncentrale verrijst ook een op olie en gas gestookte elektriciteitscentrale.
1971: De bouw van een tweede olie- en gasgestookte centrale start.
1974: De oliecrisis maakt duidelijk dat olie voor elektriciteitsopwekking geen blijvende keuze kan zijn.
1983: Na tien jaar olie te hebben gestookt, stapt de exploitant (toen PZEM) over op kolenstook. Er komt een grote ombouw- operatie op gang.
1987: De kolencentrale wordt in gebruik genomen.
Jaren 90: De impact van de kolencentrale op het milieu is steeds meer een issue.
1998: Start met bijstook van biomassa.
2014: De Nederlandse politiek wil kolencentrales sluiten. Ombouw naar een volledige biomassacentrale blijkt niet haalbaar.
2015: De centrale wordt een maand eerder dan gepland uit bedrijf genomen na enkele ernstige bedrijfsongevallen, waarvan één dodelijk ongeval. Nog maar twee gebouwen staan overeind: het ketelhuis en de machinehal met daarin turbines, generatoren en transformatoren. Eerder al sneuvelden onder meer een paar blikvangers in het landschap van Zeeland. Zo is de 170 meter hoge schoorsteen, tot vorig jaar het hoogste punt van de provincie, van boven naar beneden ‘afgeknabbeld’ met een fl inke hydraulische betoncrusher. En de kenmerkende kolenbandbrug is in delen naar een sloopterrein vervoerd. Eind volgend jaar moet er alleen nog maar een groene weide over zijn. Vanuit milieuoverwegingen moest de kolencentrale van EPZ in Borssele in 2015 sluiten. Toen dat bekend werd, kwamen er volgens plantmanager Martin Oosterveld allerlei vragen om de centrale te demonteren en vervolgens ergens anders weer op te bouwen. ‘We hebben die vragen voorgelegd aan de aandeelhouders. Die hebben toen heel expliciet gezegd dat de centrale moet worden gesloopt. Anders verplaats je het probleem.’
Sloopgereed
Oosterveld werkt al sinds de start van de kolencentrale in Borssele en na de ontmanteling gaat hij met vervroegd pensioen, tenzij er nog iets anders leuks op zijn pad komt. ‘Het is alsof hij voor mij is gebouwd.’ Van de 115 mensen die EPZ in 2015 nog in dienst had, zijn er naast Oosterveld nog maar vijf over. Ook allemaal zestigers. Twee collega’s zijn inmiddels met pensioen maar werken nog in deeltijd. De anderen moeten aan het eind van dit project laten weten of ze nog willen blijven als er werk is, kiezen voor een baan buiten EPZ of met vervroegd pensioen gaan. Toen de kolencentrale uit bedrijf werd genomen, heeft EPZ eerst de tijd genomen om de ontmanteling voor te bereiden. De installatie is sloopgereed gemaakt. Olie en andere chemicaliën in de proces- en hulpsystemen zijn afgevoerd. Ook is de installatie zoveel mogelijk gereinigd. Daarnaast ging veel aandacht uit naar het ontvlechten en loskoppelen van de infrastructuur rond de kolencentrale. Zowel de kolencentrale als de kerncentrale maakten gebruik van een aantal hulpsystemen die op het terrein van de kolencentrale waren geplaatst zoals water, riool en elektra.
Niks meer waard
De aannemerscombinatie Schotte/Meuva helpt met de verdere ontmanteling. Schotte sloopte eerder al de kolenvergassercentrale in Limburg. In 2019 begon de combinatie aan de centrale in Zeeland. ‘Het is wel eens raar als wij komen’, vertelt hoofduitvoerder Ad Vermeulen. ‘Mensen
De 170 meter hoge schoorsteen, tot vorig jaar het hoogste punt van de provincie Zeeland, is van boven naar beneden ‘afgeknabbeld’ met een hydraulische betoncrusher.
hebben duizenden uren doorgebracht om zo’n fabriek netjes te houden. We hebben hier in de kolencentrale bijvoorbeeld een elektroman lopen, die heel erg begaan is met de installatie. En dan knippen wij een turbine of elektromotor kapot. Hij zit daar dan naar te kijken en zegt: ‘Weet je wel wat dat waard is?’. Ja, niks meer. Mensen vragen ons wel vaker of we weten wat we weggooien. Maar voor ons worden die materialen weer grondstoffen.’
Gebouwen als buffer
Het was voor de slopers best wel een klein gebied om in te werken, vertelt Vermeulen. ‘We hebben een route uit moeten stippelen. Wat we eerst gingen slopen zodat we materialen konden afvoeren en bij een volgend stuk konden komen. Als we op het ene stuk slopen, kunnen we een ander gedeelte voorbereiden op ontmanteling. Denk daarbij aan asbestsanering en het verwijderen van andere gevaarlijke stoffen.’
AD VERMEULEN HOOFDUITVOERDER SCHOTTE/MEUVA
Door gebouwen zo lang mogelijk te laten staan en eerst alles eruit te slopen, vermijden de slopers zoveel mogelijk geluid- en stofoverlast. Vermeulen: ‘Vervolgens halen we de hoogtes weg en verkleinen we alles. Uiteindelijk komen we dan bij de fundaties uit. Het is een heel doordacht systeem om op te kunnen schuiven.’ ‘We werken eigenlijk naar de kerncentrale toe’, vult Oosterveld aan. ‘De gebouwen die nu nog staan, hebben we de hele tijd mooi als buffer gehad. Sowieso moet alles veilig, maar er mag ook geen hinder ontstaan richting de kerncentrale. Een aantal hulpsystemen staan maar een paar meter van onze gebouwen af. Dus je moet afspraken maken over de bereikbaarheid daarvan. Ook staat er een kantoorgebouw deels tussen de te slopen gebouwen. In sommige situaties moeten de medewerkers uit de ondersteunende afdelingen van de kerncentrale daarom ergens anders werken.’
Radioactiviteit
Daarnaast was ook het verwijderen van radioactieve besmetting een uitdaging. Door de verbranding van steenkool en het gebruik van ongebluste kalk zijn er op twee plaatsen in de installatie natuurlijke radioactieve stoffen achtergebleven. ‘In kolen zit een toefje radioactiviteit’, legt Oosterveld uit. In het proces werden de kolen fijn vermalen en de vuurhaard ingeblazen van wel 1.300 tot 1.500 graden Celsius. De onverbrande deeltjes worden dan vloeibaar en nemen de radioactieve deeltjes op en hechten zich op de wand van de vuurhaard.’ Het team van Vermeulen moest externe specialisten erbij vragen om te helpen bij het saneren van de vuurhaard met radioactiviteit. Uiteindelijk is er een hele tent omheen gebouwd. Toezichthouder ANVS (Authoriteit Nucleaire Veiligheid en Stralingsbescherming) zag erop toe dat het werk goed werd uitgevoerd. In delen is de vuurhaard naar een aparte locatie gebracht waar met staalstralen de radioactieve laag is verwijderd. Daarna kon het staal pas worden afgevoerd naar de hoogovens. Vermeulen: ‘Dat was een behoorlijke uitdaging. Van vijfhonderd ton vervuild materiaal zijn we naar misschien nog geen twee ton gegaan. Het kost heel veel inspanning, maar hoort bij het proces.’ Wat niet helemaal vrij kon worden gemaakt van radioactieve besmetting is naar een speciale stort gebracht.
25 tot 50 man
‘Met hoeveel mensen denk je dat we hier werken?’, vraagt hoofduitvoerder Ad Vermeulen. Hij moet lachen bij de gok van tweehonderd mensen van de redacteur, die haar gok baseert op de enorme aantallen extra medewerkers die bij een onderhoudsstop aanwezig zijn. ‘We werken met 25 tot 50 mensen. Bij een onderhoudsstop ligt alles stil en wordt er gewerkt aan installaties, worden ze schoongemaakt en zijn er veel inspecties.’ Het aantal medewerkers is weinig, omdat er nooit boven of onder elkaar kan worden gewerkt. ‘We breken van boven naar beneden af of andersom. Er is altijd gevaar dat iemand wordt geraakt. We doen veel zwaar hijswerk. Overal waar we hijsen moeten we het gebied afzetten. We werken steeds in kleine teams. Daarom proberen we wel steeds in andere zones bezig te zijn met anderen en daar voorbereidende werkzaamheden te doen. Veiligheid garanderen is superbelangrijk.’ Daarbij maken de slopers gebruik van veel machines die spullen klein kunnen knippen en stukken kunnen sorteren. ‘We proberen een groot deel machinaal te doen. Dan hoeven er geen mensen tussen te lopen, wat weer minder risico betekent.

Plantmanager Martin Oosterveld (links) en hoofduitvoerder Ad Vermeulen (rechts).
Twee kerncentrales
Eind volgend jaar is de ontmanteling klaar. Op een deel van het voormalig kolenpark is al een zonnepark gebouwd van 21 megawatt. Een ander gedeelte van het terrein is overgedragen aan het havenschap en daar heeft een grondstoffenbedrijf een uitbreiding op gedaan. EPZ wil op de rest van de ruimte twee kerncentrales bouwen, maar zover is het nog niet.
Horizontale scheiding belooft
forse energiebesparing
Het scheiden van twee vloeistoff en met een dicht bij elkaar liggend kookpunt, kan een behoorlijke uitdaging zijn. Voor verticale scheidingskolommen dan. De RevSep-technologie van John Gommers legt de scheidingskolom echter op zijn kant en krijgt daar een zeer energie-effi ciënte scheiding voor terug.
David van Baarle
RevSep
RevSep-technologie maakt een omkeerbare scheiding mogelijk. De confi guratie bestaat uit een gesloten thermische cyclus, met een warm en een koud uiteinde. Het koude gedeelte van de cyclus vindt plaats in het bovenste gedeelte van de horizontale kolom, terwijl het warme gedeelte in het onderste gedeelte plaatsvindt. Een pakkingsectie tussen het onderste en het bovenste gedeelte verbetert de scheiding. Een binair mengsel (vloeistof) wordt toegevoerd in de onderste sectie waarna totale refl ux mogelijk is. Verdamping in de onderste sectie wordt gevolgd door condensatie in de bovenste sectie, hetgeen geleidelijk leidt tot een dynamisch evenwicht van de zware kern component aan het hete eind en de lichte kern component aan het koude eind. Een kleine energielift aan beide uiteinden is voldoende om een dynamische energiebalans te handhaven en het volgende mengsel te scheiden. Soms zou je bijna vergeten dat de chemische industrie is gebaseerd op de klassieke kunst van het scheiden, oftewel scheikunde. Wie naar het energieverbruik van deze scheidingsprocessen kijkt, kan ze echter niet over het hoofd zien. Zo’n veertig procent van de energie die chemische fabrieken gebruiken, gaat namelijk naar destillatiekolommen die mengsels verwarmen om de individuele producten te kunnen scheiden en verwerken. Helaas werken die nog niet zo effi ciënt dat alle energie daadwerkelijk wordt gebruikt voor het scheidingsproces. Sterker nog, de thermodynamische effi ciëntie van een gemiddeld systeem komt niet verder dan tien tot twaalf procent. Het fysieke ontwerp zorgt er namelijk voor dat veel warmte direct na de condensatie van de lichtste fractie de lucht in gaat. Dit gegeven zat John Gommers al een tijdje dwars. De voormalig Dow-ingenieur ontwierp in zijn werkzame leven heel wat installaties die vandaag de dag nog steeds draaien. Maar in zijn achterhoofd wist hij dat horizontale separatie mogelijk moest zijn. ‘De voordelen van een dergelijke confi guratie zijn legio’, zegt Gommers. ‘Met name doordat condensatie van het lichtste medium in een indirecte tegenstroom de warmte voor een groot deel terugwint.’
Damprecompressie
Gommers heeft schriften volstaan met berekeningen, schetsen en uitwerkingen van de horizontale scheider die offi cieel de RevSep heet, een afkorting van reversible separation. Om zijn berekeningen te staven en de ontwikkeling verder te brengen, nam hij Anton Kiss in vertrouwen. Ook Kiss heeft een lang trackrecord achter zijn naam van waardevolle innovaties bij zijn voormalig werkgever AkzoNobel. Sinds vorig jaar is Kiss hoogleraar Process Systems Engineering bij de afdelingen Biotechnologie en Chemische Technologie van de TU Delft. ‘Ik publiceerde in het verleden al artikelen over potentiële verbeteringen in destillatieprocessen’, zegt Kiss. ‘De lage energie-effi ciency was lange tijd blijkbaar geen issue. Inmiddels is de focus bij bedrijven wel verschoven naar energie-effi ciency. Zeker nu de industrie steeds meer wordt belast voor zijn CO2-uitstoot. Het mooie van RevSep is dat het benodigde temperatuurverschil zo klein is dat bijvoorbeeld damprecompressie met behulp van groene stroom een optie is. Ook het gebruik van laagwaardige restwarmte uit andere processen is een mogelijkheid.’
Drie keer effi ciënter
De energie- en grondstoff entransitie versterkt ook op een ander vlak de aandacht voor scheidingstechnologie, denkt Kiss.

De RevSep-technologie is in theorie minstens drie keer efficiënter dan de conventionele destillatiesystemen.
‘Als de industrie overstapt op biologische grondstoffen, krijgt ze daar ook een grote hoeveelheid water en andere stoffen bij. Het is zonde als je aan de ene kant CO2-uitstoot vermijdt, terwijl je met een inefficiënt scheidingproces alsnog veel energie verspilt.’
Gommers berekende dat de technologie in theorie minstens drie keer efficiënter is dan de conventionele destillatiesystemen. ‘Wel moeten bedrijven rekening houden met een iets hogere kapitaalinvestering’, zegt Gommers. ‘Maar die hogere kosten verdien je ruimschoots terug in de operationele fase. Niet alleen door de energiebesparing, maar ook doordat je zuiverdere producten krijgt. De technologie is met name heel interessant voor moeilijk te scheiden vloeistoffen waarvan het kookpunt dicht bij elkaar ligt. Dat is bijvoorbeeld het geval bij ethylbenzeen en paraxyleen. Ethylbenzeen kookt bij een temperatuur van 136 graden Celsius en paraxyleen bij 138 graden Celsius. Dankzij het ontwerp van RevSep zijn deze stromen veel eenvoudiger te scheiden dan in een verticale destillatiekolom. Juist bij dit soort toepassingen kan de energiebesparing oplopen tot zelfs negentig procent.’
ANTON KISS HOOGLERAAR TU DELFT
Opschaling
Nu alle berekeningen zijn gemaakt en bijna zijn geverifieerd in het laboratorium, willen Gommers en Kiss snel opschalen naar de volgende stap. Daarvoor willen ze een werkend systeem bouwen van ongeveer drie meter lang en twee meter hoog. ‘Ik verwacht geen fundamentele problemen’, zegt Gommers. ‘Maar we willen toch een aantal uitdagingen in het ontwerp in de praktijk beproeven en oplossingsrichtingen uitwerken. Daarvoor hebben we financiële steun nodig van de industrie, de overheid of liever nog beide. De impact van deze nieuwe scheidingstechnologie kan het energieverbruik van de chemische industrie significant terugdringen. Nu is het zaak zo snel mogelijk een werkend model te kunnen presenteren zodat we ook de praktische inpassing in bestaande systemen kunnen testen.’