
5 minute read
Shaping the future of rail technology
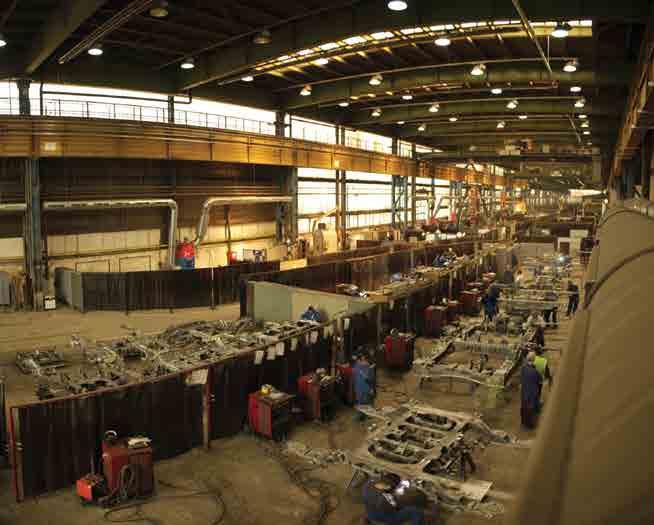
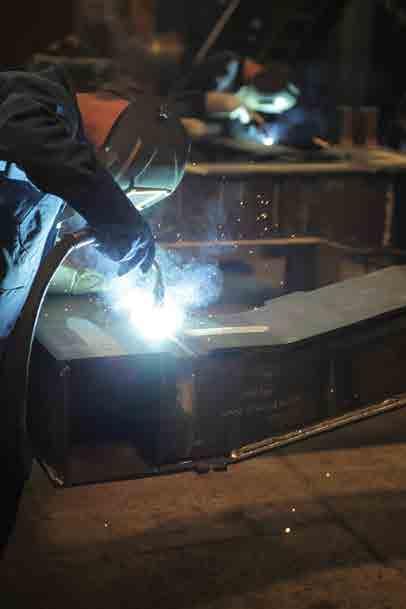
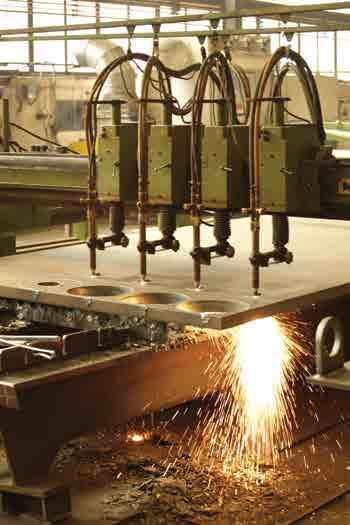
SHAPING THE FUTURE
OF RAIL TECHNOLOGY
Bombardier Transportation is the global leader in the design and manufacture of rail vehicles. Philip Yorke talked to Kurt Lievens, the managing director of the Bombardier plant in Matranovak, about their innovative, energy-efficient products and latest advanced mechatronic solutions.
Bombardier is a truly global transportation company and unique in that it is the only company in the world that operates in two distinctly different industry-leading businesses: Aerospace and Rail Transportation. Bombardier operates 69 manufacturing and engineering sites in 23 countries and employs more than 65,000 people worldwide. The company manufactures the widest range of world-class products in its two chosen disciplines, avionics and rail transportation. This includes the design and manufacture of commercial and business jets and the manufacture of rail transportation equipment as well as systems and services. The Bombardier Group is headquartered in Montreal, Canada, and its shares are traded on the Toronto stock exchange.
In the fiscal year ended 31 January 2011, the company posted revenues of over €17.7 billion.
Delivering unique mechatronic solutions
Bombardier Transportation is a major contributor to the Bombardier Group with 59 production and engineering sites in 23 countries and more than 40 service centres located at its customers’ premises worldwide. The company employs more than 40,000 people and covers the full spectrum of rail solutions ranging from complete trains to subsystems, maintenance services and system integration and signalling. To date it has manufactured more than 100,000 rail cars and locomotives worldwide which include automated people movers, monorails, light rail vehicles, advanced rapid transit vehicles, commuter trains and highspeed trains and locomotives. In addition, the company has a complete portfolio of propulsion controls for applications ranging from trolley buses to freight locomotives and the most comprehensive of bogies covering the entire range of rail vehicles: the BOMBARDIER™ and FLEXX™ bogie families.
Mr Lievens said, “At our manufacturing facility in Matranovak in Hungary, we produce over 80 per cent of all the bogie frames designed for Bombardier trains. Bombardier Transportation has always pioneered advanced rail systems and our commitment to R&D has produced some remarkable technological firsts. Our BOMBARDIER FLEXX Tronic WAKO™ is a good example. This innovative mechatronic solution was designed to compensate the natural roll movement of a rail car body and is integrated into the train’s existing secondary suspension. This unique system allows for a speed increase in curves of 15 per cent which in turn means shorter journey times without the need for significant investment in infrastructure.
“Another good example of our innovative technologies is Primove City. This technology provides contactless power transmission for trams. This means that no catenary is needed. Today Bombardier has taken this technology one step further and applied it to cars and commercial vehicles as well. Bombardier continues to shape the future of rail technology and improve comfort for passengers and energy efficiency. As always, safety, efficiency and flexibility are the guiding principles throughout all of Bombardiers product development programmes.”
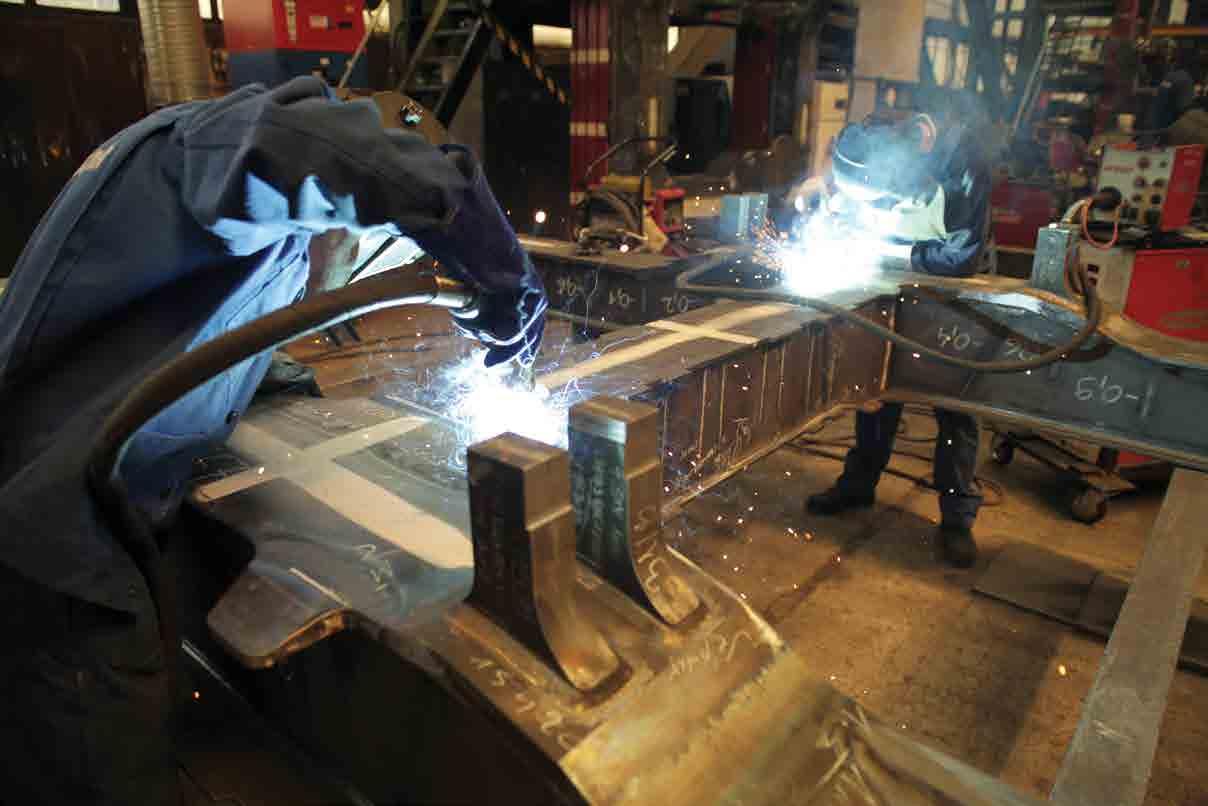
Investing in energy efficiency
Continuous investment in facilities and technology keeps Bombardier one step ahead of its competitors. In the last few years significant investments have been made in the Matranovak site in Hungary, which is located 130km from Budapest. This site specialises in manufacturing frames and primary parts for FLEXX bogies. The investments include the installation of a welding robot and new welding machines as well as advanced, welding fume exhaust systems in the main production hall. In addition, the company invested heavily in an entirely new production hall with the installation of the latest energyefficient machinery. Thanks to these investments, Bombardier’s Matranovak site has reached an annual capacity of more than 2,500 bogie frames per year and continuously improved its manufacturing processes, as well as the working environment of its employees.
All the bogie frames produced in Matranovak are delivered to the Bombardier sites in Siegen, Germany and to Crespin in France for the final assembly of bogies for rail vehicles destined for world markets. Some of these will return to Hungary once they are installed under the TRAXX locomotives ordered by the Hungarian Railways (MAV).
Revolutionary energysaving technologies
In 2008 Bombardier introduced its revolutionary ECO4™ energy-saving technologies, which are designed to be readily customised to suit any rail vehicle fleet. These eco-active technologies have advanced sustainable mobility in many different ways. This includes the optimisation of the use of energy, decreasing energy waste,

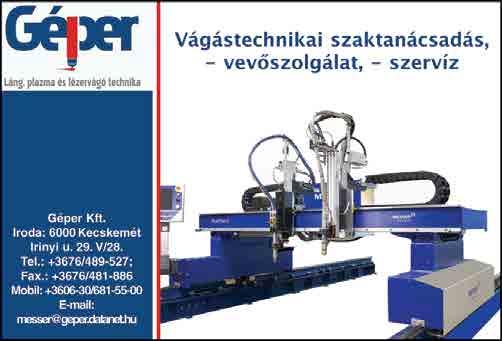
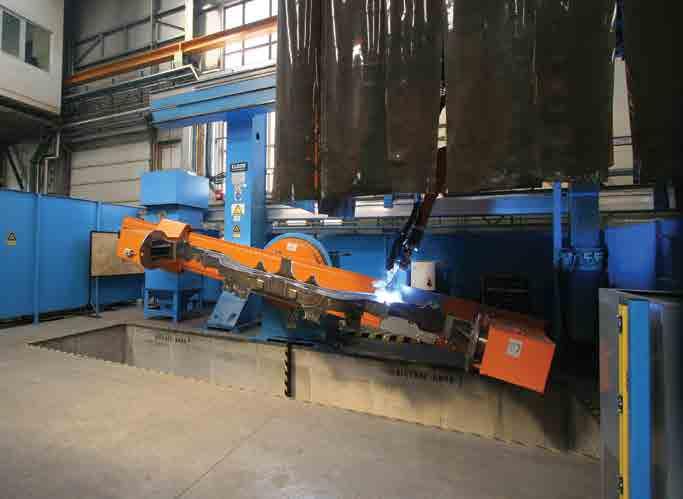
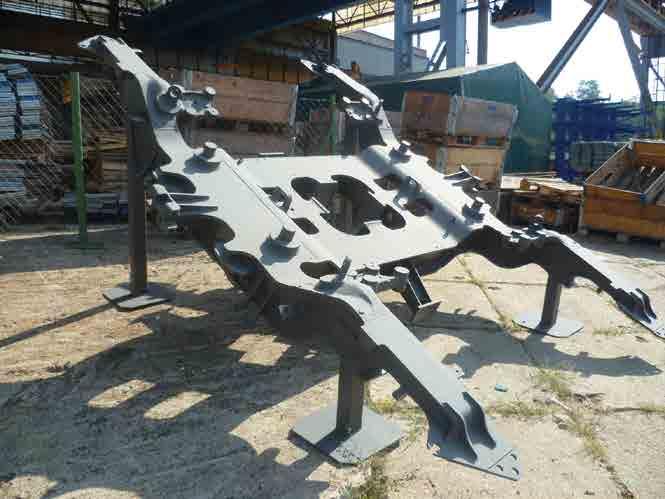
minimising CO2 emissions and increasing economic value by improving total train performance. By implementing these solutions, operators can achieve an overall energy saving of up to 50 per cent.
Bombardier’s modular suite of ECO4 technologies include its EnerGplan simulation tool, MITRAC™ energy saver, CLEAN Diesel Power Pack, FLEXX Tronic technology and EcoEfficient Optimised Environmental Performance, among many others. This energy-saving technology represents one of Bombardiers’ major sustainability initiatives.
Mr Lievens added, “Bombardier Transportation offers one of the most comprehensive rail vehicle portfolios in the world. Our strategy is one of continuous development and we are dedicated to providing the most effective, ecofriendly and cost-efficient rail solutions. Today we are delivering rail vehicles and optimal rail vehicle systems to new markets such as the Middle East where we have received contracts from Saudi Arabia and more recently in South America. We are very proud to have received a substantial contract from Sao Paulo, where we will build a monorail system to provide improved public transport in the city.” n
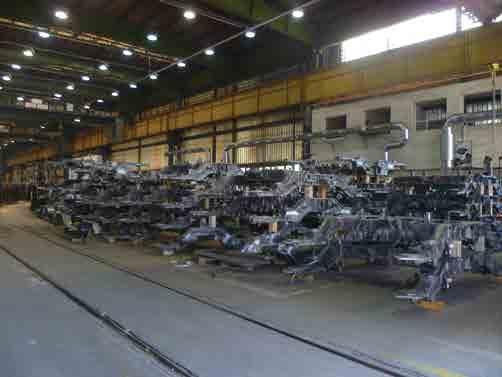

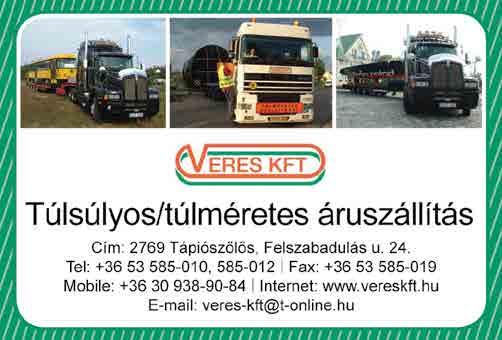
