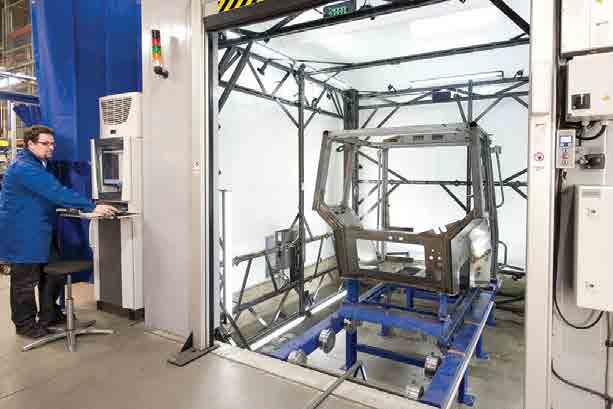
6 minute read
Fast and flexible Maaseudun Kone
3D fully automatic measurement system. We are measuring 100 per cent of all cabin frames and the system is based on camera technology. Two pairs of robots are welding floors and both side walls for final assembly welding Waterproof testing
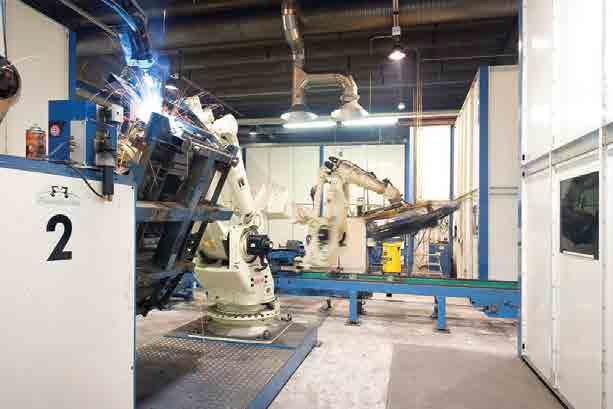
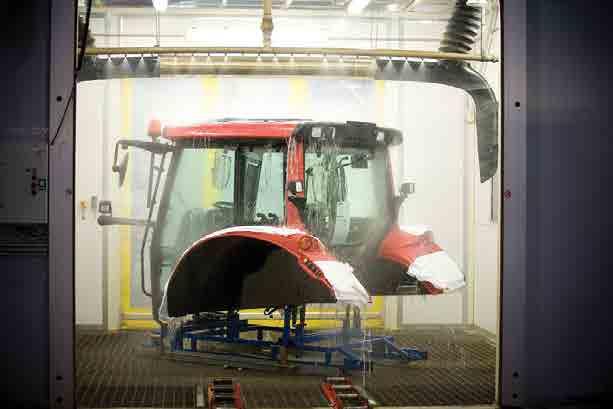
FAST AND FLEXIBLE
Maaseudun Kone is a market leader in the design and manufacture of tractor cabins and components. Philip Yorke takes a closer look at a company that spearheads a group of highly specialised manufacturers covering farming, forestry and transportation.
Starting point for the 150 metre long assembly line End of the assembly line
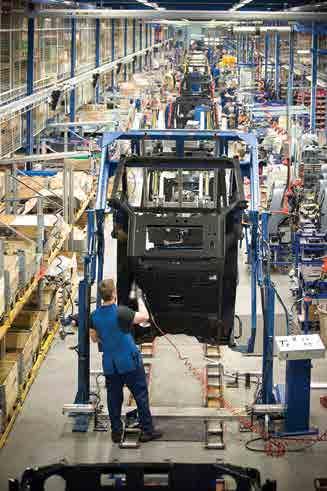
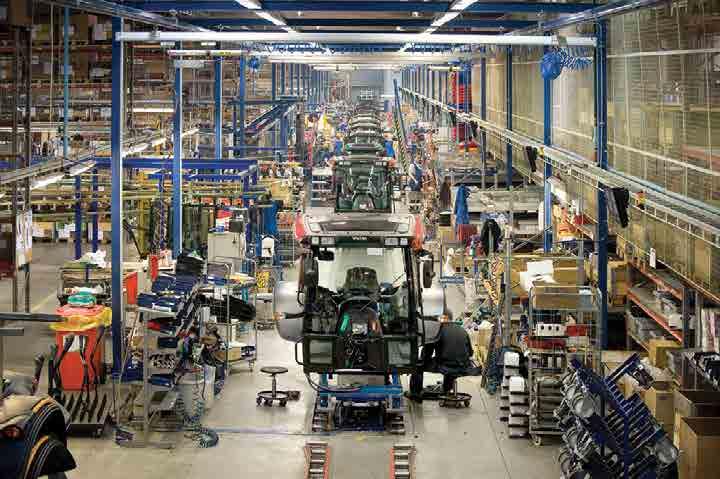
Factory in Kauhava
For over 50 years Maaseudun Kone has been designing and manufacturing safety cabins for tractors and agricultural equipment.
The company is part of the independent Finnish MSK Group and has its headquarters in Yliharma, Finland. Maaseudun Kone Oy employs more than 200 people and is backed up by a wide network of suppliers and distributors. The company has a large research and development department which focuses on designing customized safety cabins for leading Scandinavian brands such as Valtra Tractors and Ponsse Rural Machinery. Since it was founded, the company has led the way in the design of highly efficient, dust-proof, sound-proof, airconditioned and ergonomic tractor cabins. The privately owned MSK Group comprises Maaseudun Kone Oy, Junkkari Oy, Junkkari Muovi Oy and Juncar Oy.

Fully robotised welding
Masseudun Kone has continued to invest in new plant and technology, which has resulted in a factory that is one of the most efficient and modern of its kind. All welding processes are fully ‘robotised’. For example, the first robotic stage welds the main components of the tractor cabin together to produce the subparts. This is carried out by a pair of specially designed robots. The first bigger robot offers the charged welding jig for the smaller robot to weld the seams and then returns the part back onto the production line conveyorbelt. In the production cell is two pairs of robots for the pre-welding phase. The final welding of the cabin is carried out by another two robots, both served by two high-tech handling devices that keep turning the cabin frame in order to locate the ideal welding position each time.
The finishing of the cabin frame and of other components takes place along two painting lines, where pre-treatment is based on a special zinc ‘bonderising’ process. The painting is then executed by two robots spraying the powder onto the surface of the selected parts automatically. The final corrosion- resistant surface quality paint is cured in the production line’s oven at over 200°C.
Maaseudun Kone’s CEO, Matti Palo added, “We have an operations management system that meets all the latest standards and manages the plant with optimal efficiency. This cutting-edge system helps us to manage around 5000 purchased or manufactured components daily and provides constant, updated information on all key production indicators. Throughout our stateof- the-art assembly lines, our dedicated technicians furnish each single cabin with the equipment that the customer has ordered specifically for that particular cabin.
“Our lines produce a perfect tractor cabin every few hours, from where it is removed for testing and pre-delivery inspection. The final test stage ensures that the customer will receive a cabin that enables the tractor’s driver to work efficiently and in comfort, come rain, wind or blizzard. In addition, our flexible, automated production methods and advanced product planning techniques, guarantee the fastest possible manufacturing processes and our ability to meet short lead times cost-effectively.”
Professional partnerships
As an integral part of the MSK Group, Maasuedun Kone Oy benefits from the technical and production know-how that exists within the Group. The ‘descriptor’ used across all MSK companies, is: “Partnership between professionals”. In practice this means that

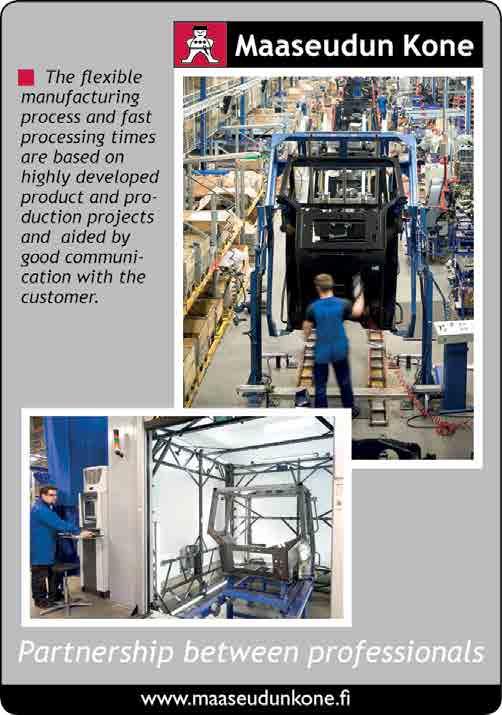
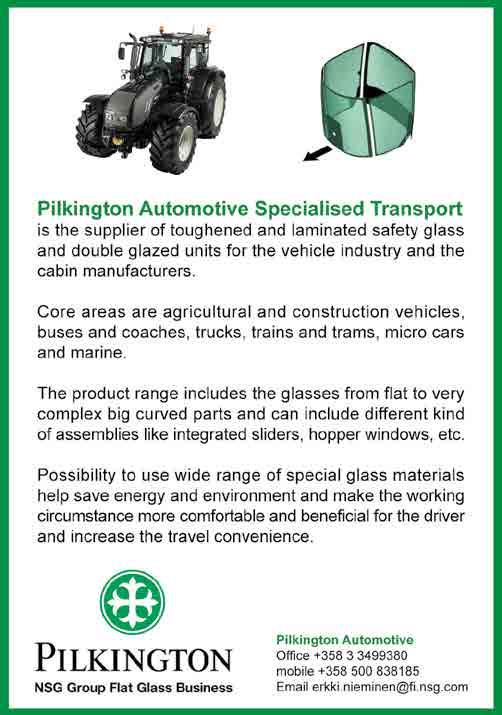
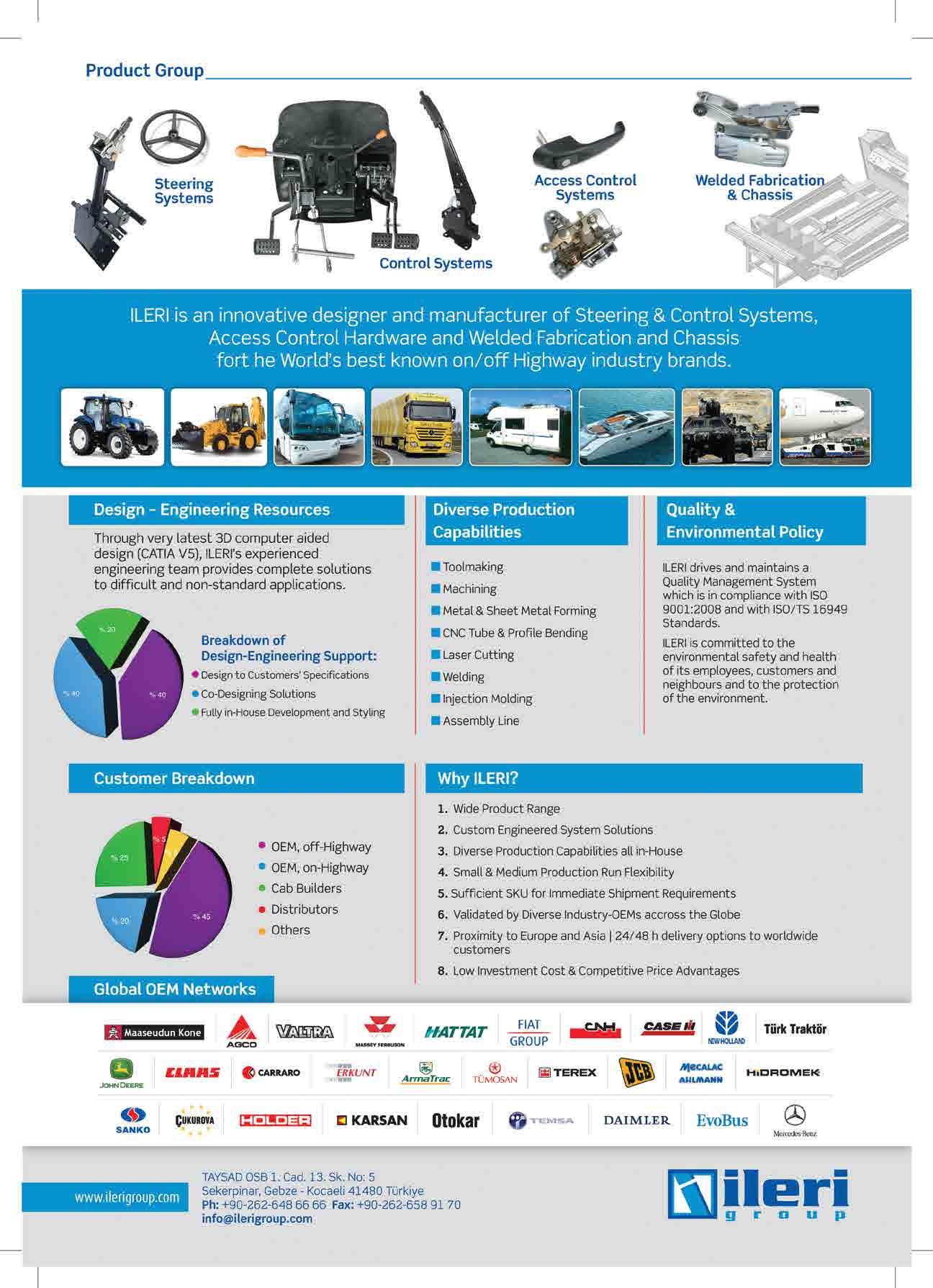
Winter time photo of the entrance to factory office
there is a common goal to provide optimised services for customers and a sharing of technological expertise and production know-how. Junkkari Oy is Maasuedun Kone’s sister company and is a leading Finnish designer and manufacturer of agricultural and forestry machinery for sowing, transportation and forestry. The company culture is the same as that of Maasuedun Kone in that its customer-orientated approach relies upon a continuous investment in research and technology, all of which is driven by the requirements of its clients. Listening to the experiences and needs of the farmer is still a fundamental principle of the company’s business culture. Junkkari also employs the latest robotic welding technology and other advanced automation techniques such as laser cutting and computer-aided quality monitoring. As a result, many of Junkkari’s innovative solutions improve the handling and operational convenience of their products in a unique and practical way.
Another key player in the MSK Group is ‘Juncar Oy’, which is the largest trailer manufacturer in Finland with over 30 years experience in the field. Juncar’s boat and car trailers are all top quality products, and attention is paid to the smallest detail in manufacture to achieve optimal results. The steel plates used in its trailers are hotgalvanised dipped, in a continuous process for a durable, corrosion-resistant finish that will withstand the harshest conditions.
Junkkari Muovi Oy is the final piece in the MSK company portfolio, which offers advanced injection moulding, reaction injection moulding and mould manufacturing services for the manufacture of subassemblies and individual products. The company has in-depth knowledge of plastics technology and employs a broad network of partners and distributors for its diverse range of high-quality plastic products.
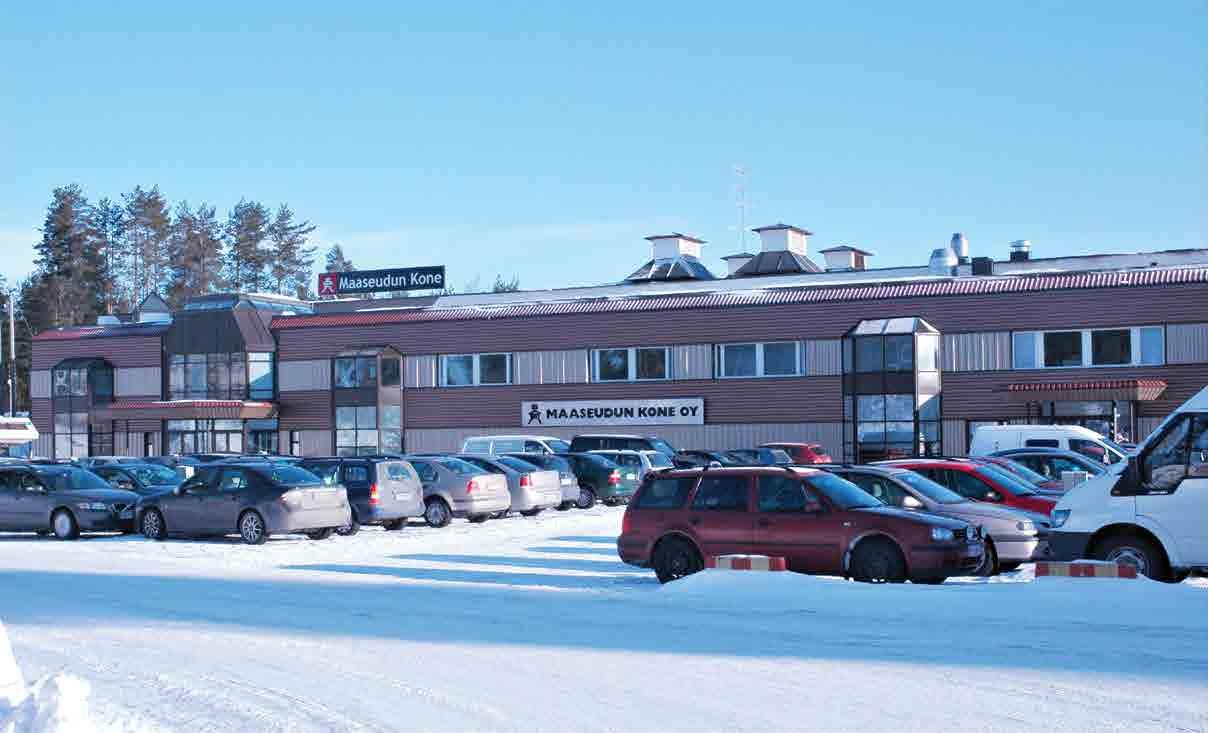
Quality by design
Maaseudun Kone is committed to on going investments in production technology and uses the latest CAD tools in the designs of its tailor-made tractor cabins. The company plans the tools required and the manufacturing processes needed for serial production at the product design stage. The prototype testing functions and dedicated project management controls ensure that production can commence quickly and flexibly for each tailor-made, quality product.
The company is also environmentally focused and is certified to ISO 9001 and ISO 14001; it was the first company in this field in Finland to achieve these two important quality assurance certifications. n
Novoplastik
Novoplastik has more than 35 years experience of Vehicle Cabin Interior trims. This includes Sportcars, Coaches, Minibuses, Tractors, Work machines, boats, Trucks etc.
Maaseudun Kone is one of the most important Customers of ours. We have successfully worked with Maaseudun Kone since early 90’s.
Newest at Novoplastik is our totally new material which we have developed for 5 years, It’s called Novofrux. It’s 100 % biodegradable nature fiber composite.
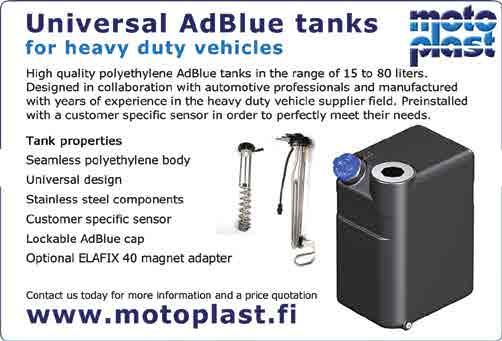
Pilkington Automotive Specialised
Pilkington Automotive Specialised Transport is the supplier of toughened and laminated safety glass and double glazed units for the vehicle industry and the cabin manufacturers. Core areas are agricultural and construction vehicles, buses and coaches, trucks, trains and trams, micro cars and marine. The product range includes the glasses from flat to very complex big curved parts and can include different kind of assemblies like integrated sliders, hopper windows, etc. Possibility to use wide range of special glass materials help save energy and environment and make the working circumstance more comfortable and beneficial for the driver and increase the travel convenience.