
5 minute read
Masters of ‘cutting-edge’ technology ESAB
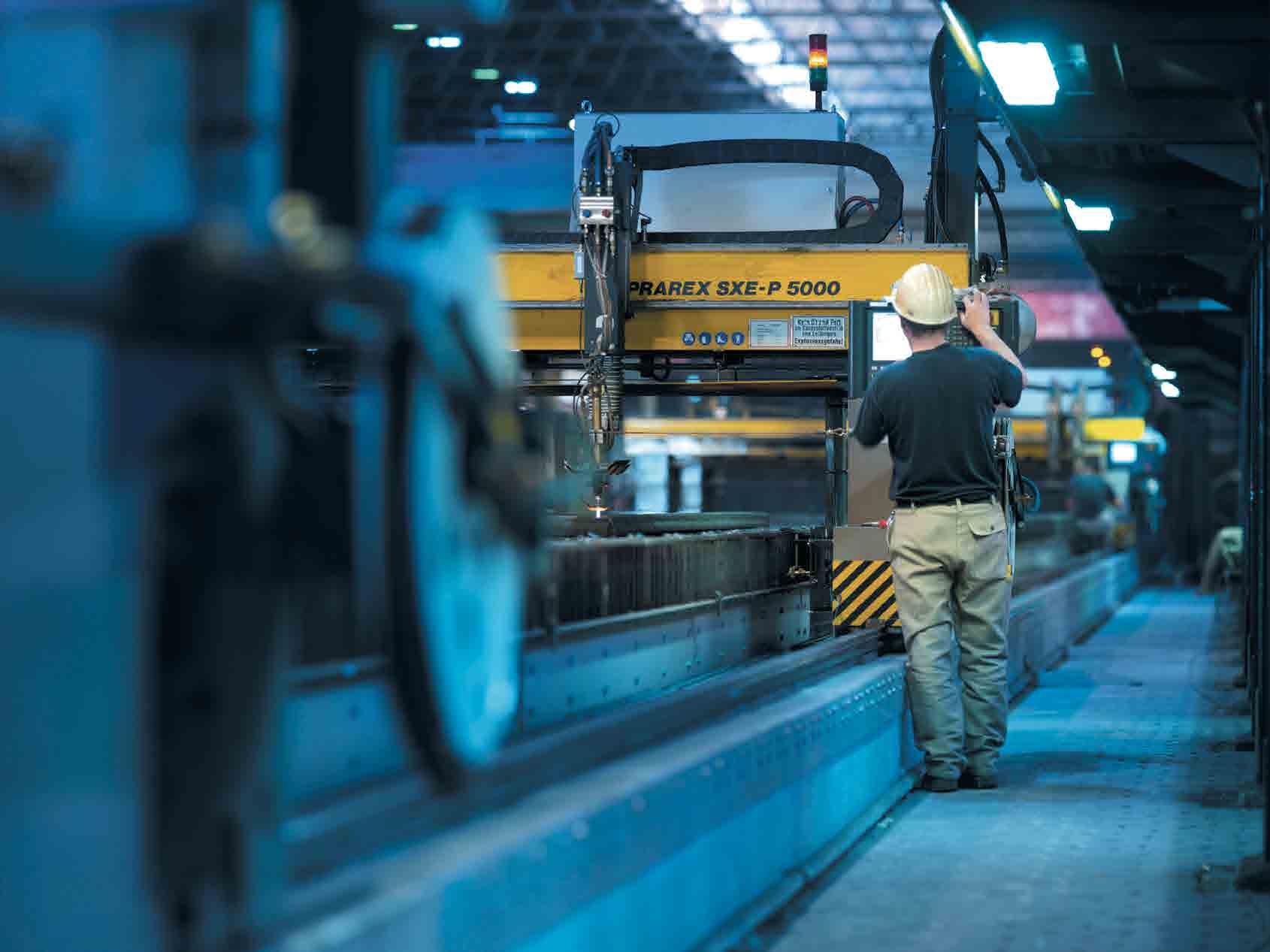

MASTERS OF TECHNOLOGY
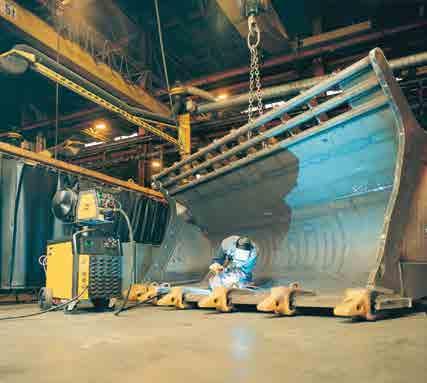
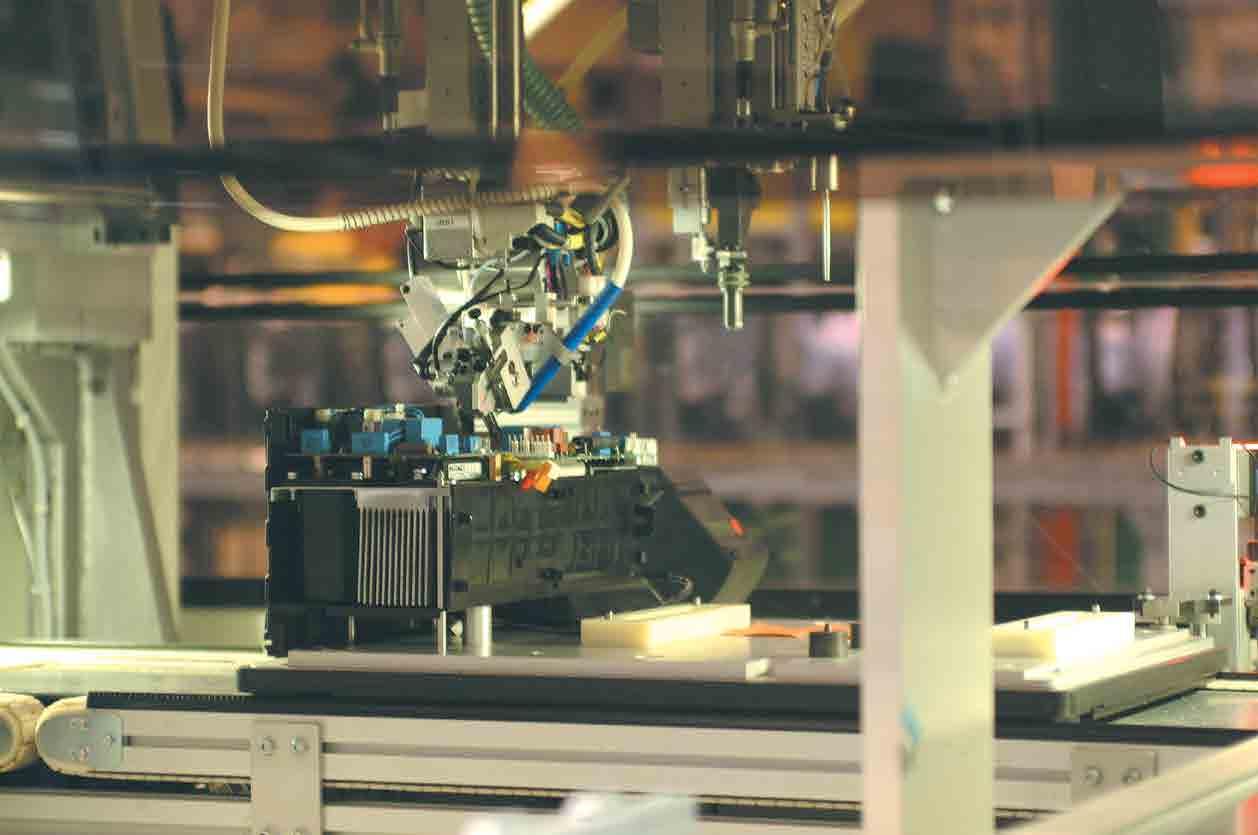
ESAB is a global leader in the field of welding and cutting processes for industry. Philip Yorke explores the secrets of ESAB’s success and looks at its latest ‘breakthrough’ technology.
ESAB was founded in 1904 by Oscar Kjellberg in Sweden following his invention of the ‘covered welding electrode’. Since then the company has seen steady growth, constantly improving on its existing technology and production methods. Today ESAB produces a wide range of consumables and equipment for virtually every welding and cutting process and application in manufacturing industry. More than 100 years of continuous research, development and manufacture has made ESAB a world leader in welding and cutting processes, with an unmatchable depth of knowledge and an enviable range of services. Innovative technology driving sales
ESAB is justifiably proud of its innovative track record, which has helped to define the industry and continues to shape the future of welding and cutting, as new materials emerge and advanced technologies present new challenges. The company offers cutting-edge, innovative technology designed to serve the vast needs of the modern welding and cutting industries. Its commitment to customer service and its energy to deliver results has kept ESAB at the forefront of its industry for many generations and continues to drive it forward today. ESAB offers a complete line of equipment for all types of processes, as well as a comprehensive range of related consumables, from cored wires to covered electrodes. The company specialises in producing a wide range of cutting equipment from small hand-held plasma units to large gantry cutters used to construct very large structures, such as aircraft carriers.
For each discipline, continuous development of methods, materials and technology combine to meet the challenges posed by a diverse range of industry sectors. Every day ESAB’s worldwide customers serving the transport, offshore, shipbuilding, power, process and aerospace industries rely on it
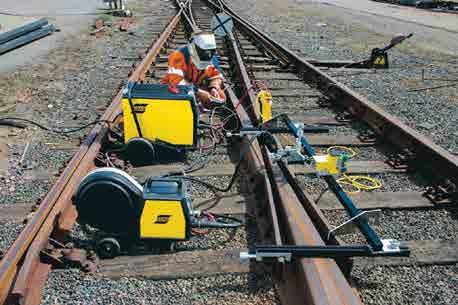
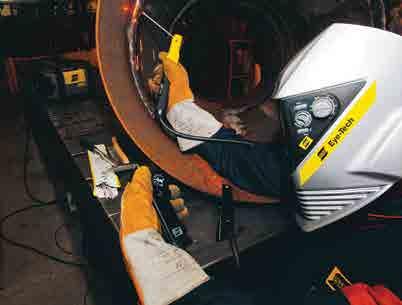

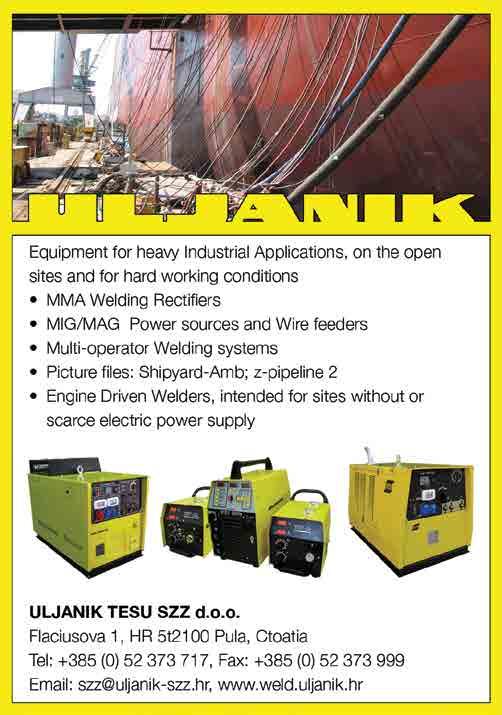
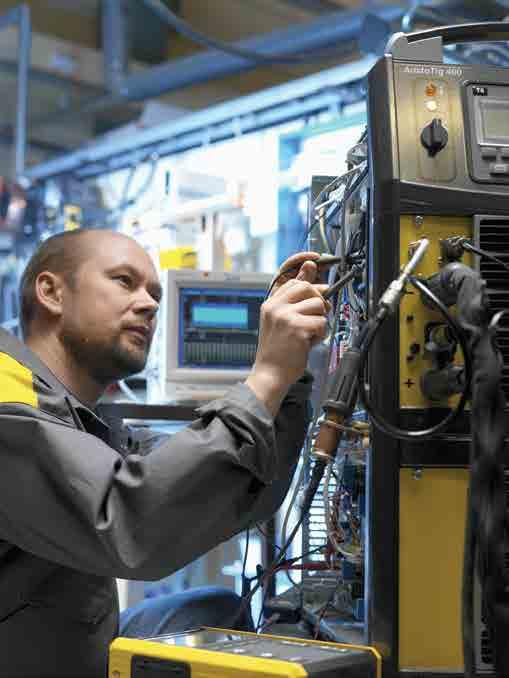
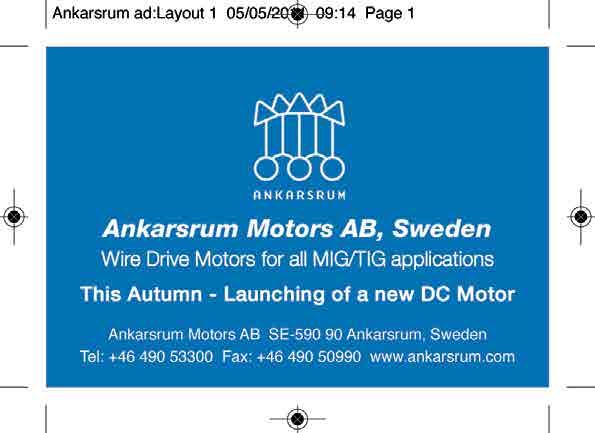
for technical and practical support.
A company spokesman said, “Our customers’ experience of our products is key to us and often provides our most valuable source of information, especially when it comes to improving our products’ performance. Our process and application support teams serve our customers at a local and global level. We also employ specialists with a comprehensive knowledge of different welding and cutting processes and techniques as well as their applications. In addition, we work actively with manual, mechanised and automated processes and have robotic cells that are available for any of our customer’s diverse applications”. Advancing hybrid laser technology
In April 2011 ESAB completed its purchase of the Master Process Controller (MPC) from Applied Thermal Sciences Inc. (ATS) for use in its hybrid laser arc welding process. This advanced technology provides a patented, real-time control system for laser management involving MIG/MAG welding equipment and the motion system that carries the laser and welding heads.
ESAB’s Hbrio TM hybrid laser welding equipment can be used on thicker materials as well as larger work pieces and joints with wider gaps. With its improved tolerance of gap variations, the hybrid laser arc welding process enables customers to reduce the time and costs associated with joint preparation, post-weld operations and re-working.
ESAB’s Hybrio TM hybrid laser technology combines the deep weld penetration and low heat input associated with laser welding, with the excellent weld properties and superior gap tolerence of GMAW. This has created a radically new welding alternative. Laser welding produces very narrow, deep welds at very high speeds. This reduces heat input to the part and the associated weld shrinkage and distortion that can make post-welding fit-up unpredictable and costly to repair.
Hybrio TM technology represents the most advanced automated laser welding system available worldwide and is capable of welding at three to ten times the speed of
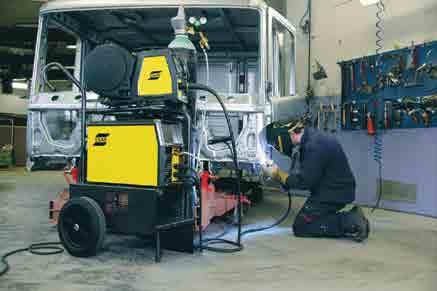
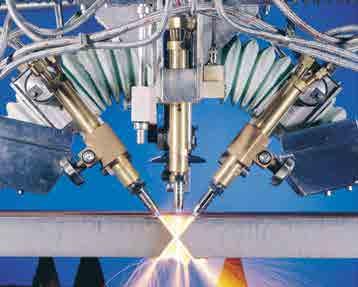
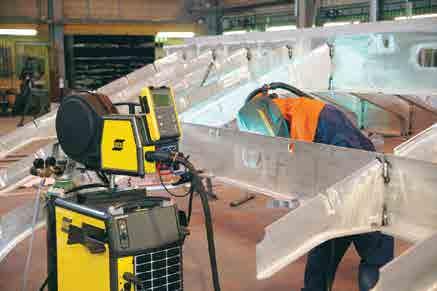
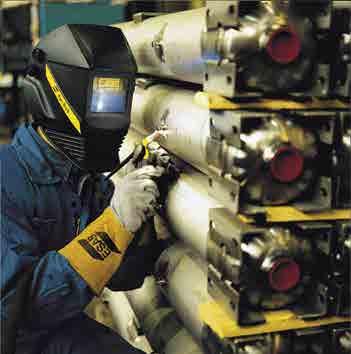
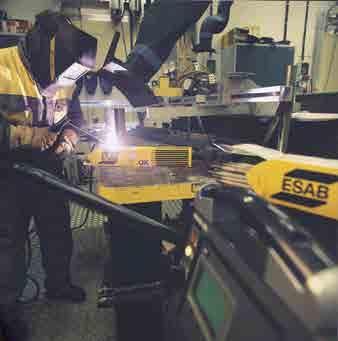
conventional welding processes. In addition, the process offers a saving of between 80–90 per cent less heat input, which in turn offers a step-change in welding performance.
ESAB’s latest Hybrio TM technology is available for use in gantry, robotic and specialised automated systems as well as a diverse range of industrial applications.
Furthermore, ESAB’s patented adaptive control system permits monitoring of the weld joint in real time, modifying the process to accommodate gaps and possible mismatch. This next-generation, intelligent control system broadens the welding performance envelope by a factor of five compared to hybrid laser-welding with conventional controls. This breakthrough in welding control technology enables the use of hybrid welding on large structures and complex assemblies without excessive reliance on very expensive pre-processing, machining and fixturing.
Exclusive US partnership
The North American division of ESAB recently announced a new partnership with a leading US custom motorcycle shop known as ‘Orange County Choppers’ (OCC). ESAB will be the exclusive welding equipment provider for OCC, supplying all the welding and cutting equipment as well as filler materials used in the shop.
Andrew Masterman, president and CEO of ESAB North America said, “OCC is the premier custom motorcycle design shop with a long history of excellence in its workmanship. Like ESAB, OCC has been praised worldwide for its innovation and leadership. Like ESAB, OCC is dedicated to providing top-quality products and exceptional customer service”.
The ESAB brand is synonymous with world leading expertise in four key areas: manual welding and cutting equipment, welding automation, welding consumables and cutting systems.
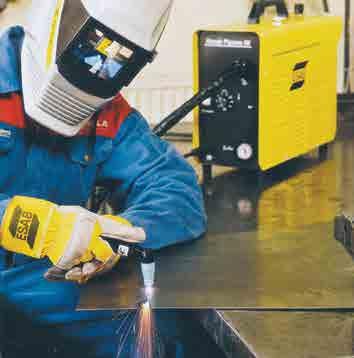
n
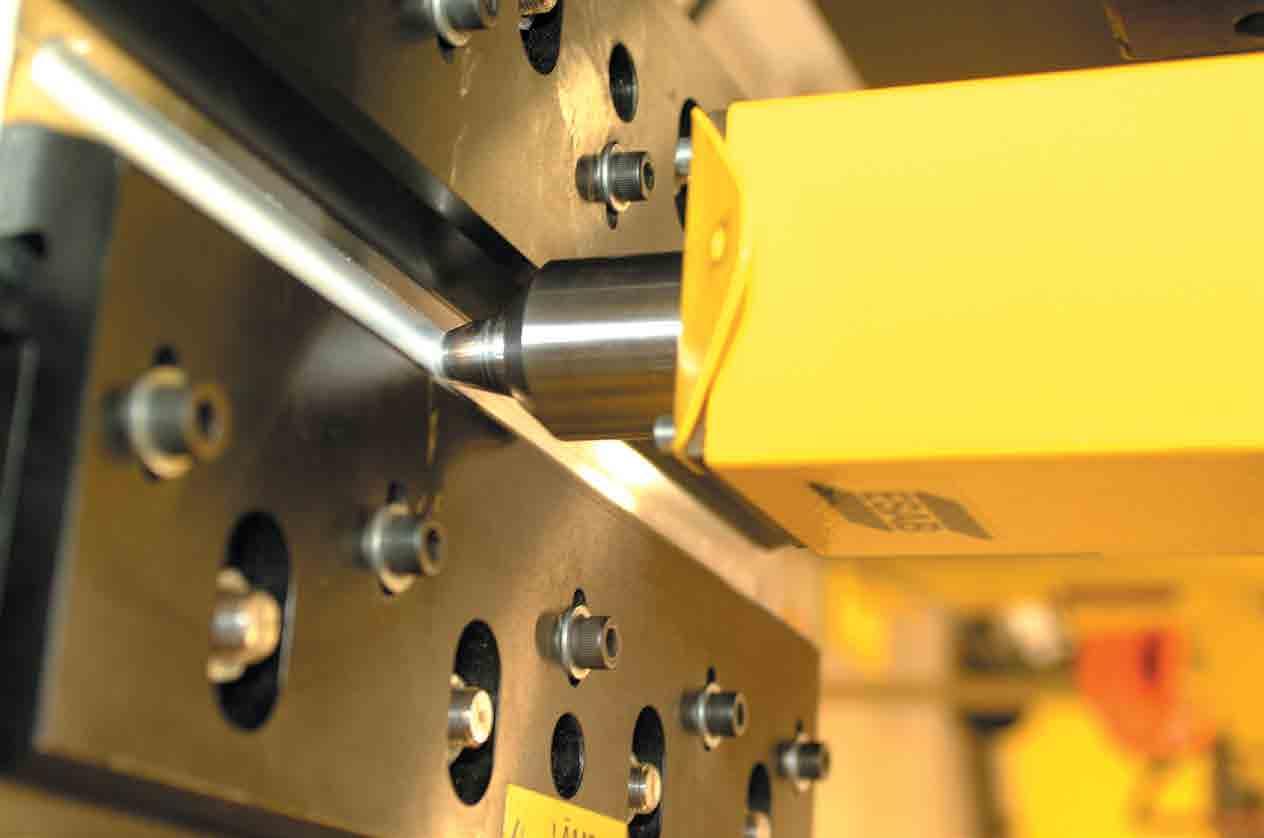
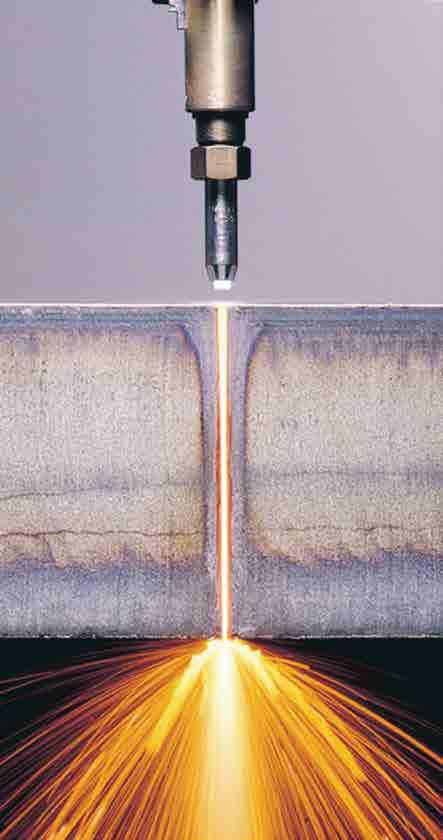