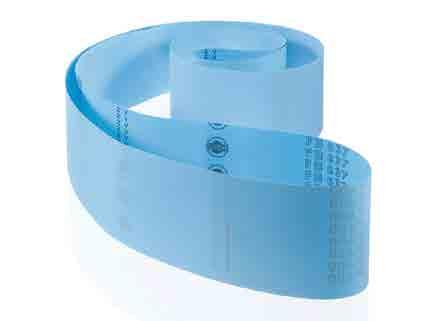
6 minute read
Advancing surface technology
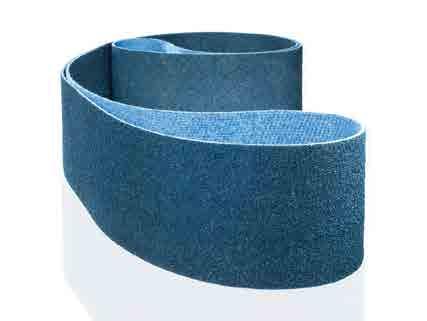

Hermes Schleifmittel is a global leader in the field of coated abrasives technology. Philip Yorke talked to Dr Jan Cord Becker about the company’s ground-breaking ‘engineered abrasives’ and its plans for future growth.
Hermes Schleifmittel was founded in Hamburg, Germany, in 1927 and has risen to become one of the largest suppliers of coated and bonded abrasives in the world. Hermes abrasive tools are used to produce precision, functional parts as well as visually attractive surfaces. The company is a market leader in many important industrial sectors, including steel, automotive, furniture, wood and glass. Hermes operates eleven major production sites, as well as numerous sales offices throughout the world. The company is fully represented in all the main industrialised and emerging industrial nations with offices and facilities in more than 100 countries. This international presence guarantees a high level of customer care and service, regardless of where the company’s clients are located.
The Hermes Group is dedicated to developing grinding solutions for a wide range of customer needs. These include coated abrasives, nonwoven abrasives and bonded abrasives. At its headquarters in Hamburg, Germany, the company’s R&D department develops new application engineering technology. From this on going commitment to innovation, the company has developed a new generation of abrasives that it calls, ‘engineered abrasives’.
Dr Jan Cord Becker, who was appointed chief executive of Hermes Schleifmittel in January 2010 after leaving his role as head of electrics engineering at Airbus Industries’ A380 programme, explains: “We have taken our engineered abrasive tools to a new level with our latest products. There have been three major, innovative developments in our new abrasive technologies. The first is a new development of the well-known ‘Hermesit®’ grinding belt, which performs five times longer than a standard belt and gives a perfectly constant finish. We have designed different versions of this belt with two special grain types. These special abrasive grains are applied to the hollow sphere bodies to ensure a very long grinding life and a consistent, high-quality finish.”
For the very popular brush finish business, Hermes developed a cork finishing belt to achieve a brush finish on a wide belt grinder. This cork belt performs like an abrasive brush, but as a belt, and gives the customer a satin brush finish like a super deburred surface. It is not only the unique surface quality that is a real advantage but the grinding ability is also enormous. It is possible to carry out a brush finish design with a feed speed of 70m/min with this cork belt on a wide belt grinder, instead of 10m/min on a brush roller unit.
“Finally, for very high pressure grinding, we have developed micro-crystalline ceramic grain, known as Sapphire Blue®.” The company owns the patent for this special Sapphire Blue® grain type and offers several belt executions with this high-tech grain. Another brand new development is the application of Sapphire Blue® grain to a paper backing, which is ideal for applications such as stainless and titanium sheet grinding. In turn, this product offers a clear price performance advantage for our customers.
“It’s premium products like these that are driving the abrasive market. However, in the mature and increasingly in the emerging markets in which we operate, there is clearly an increase in demand for ‘high end’ products such as ‘engineered abrasives’.”
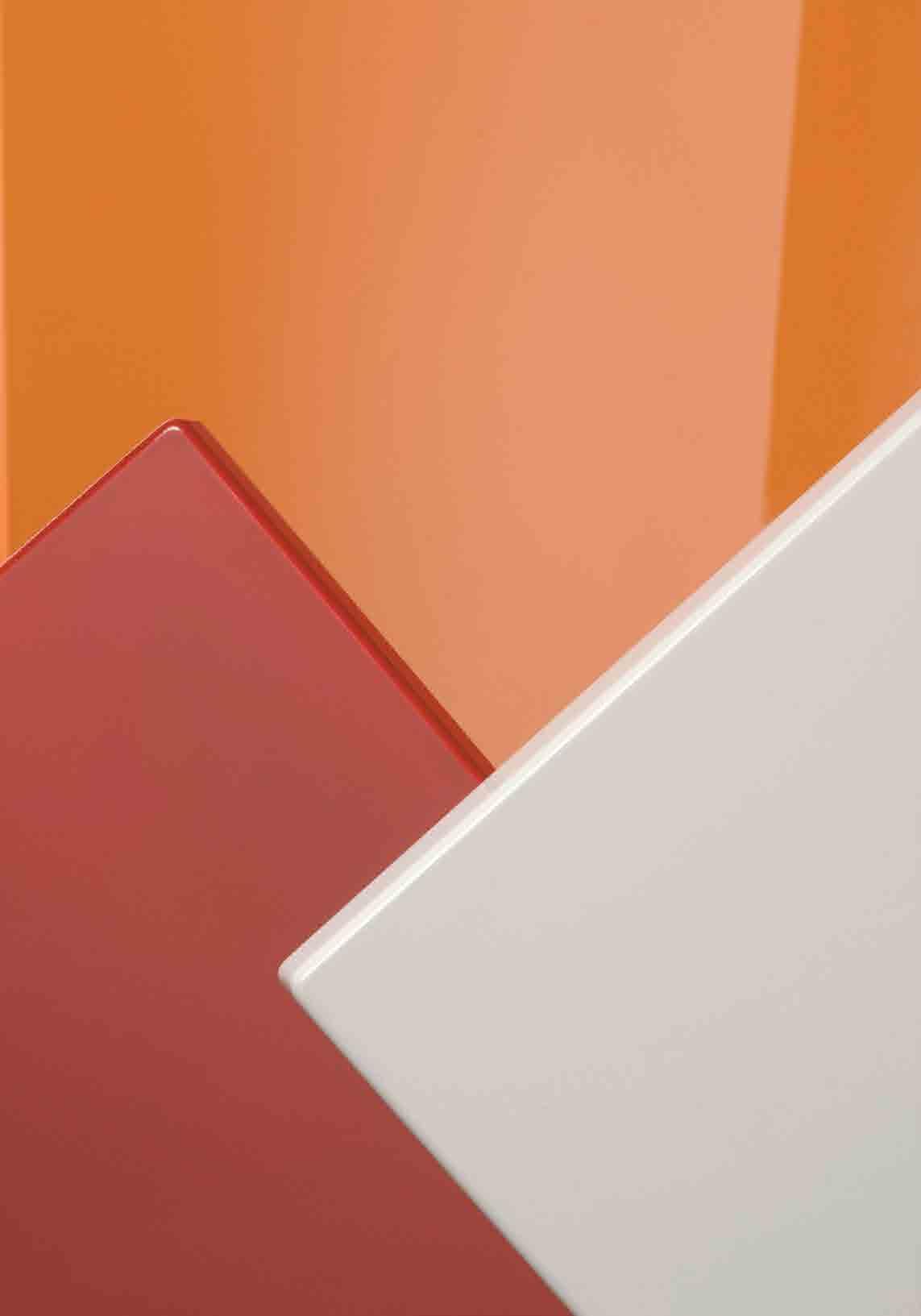

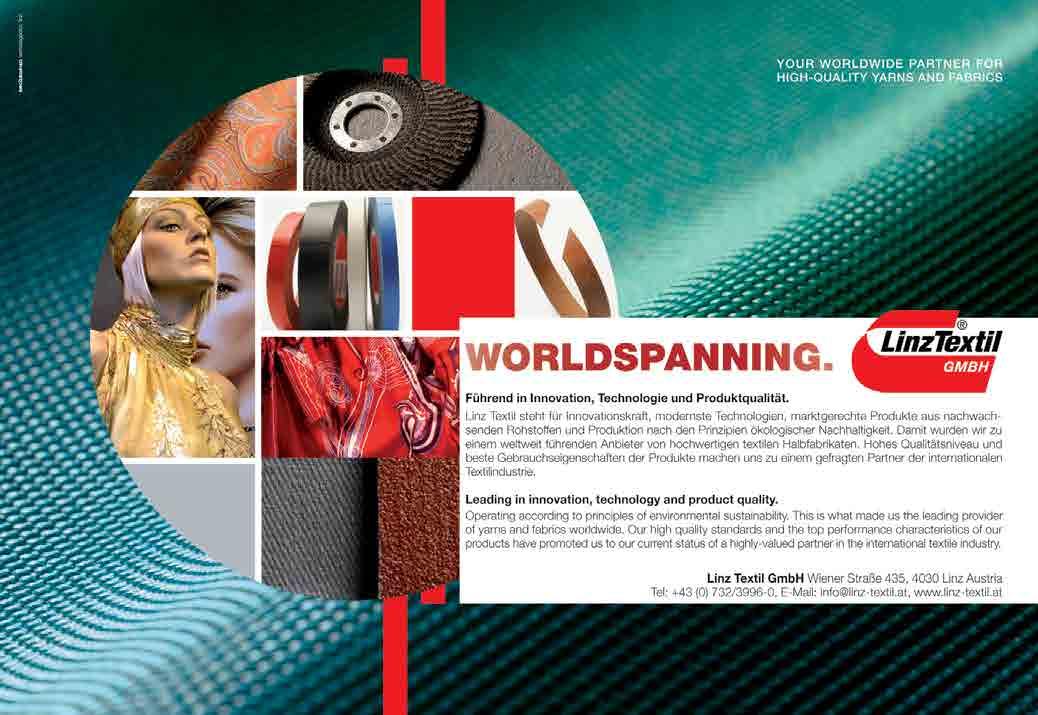
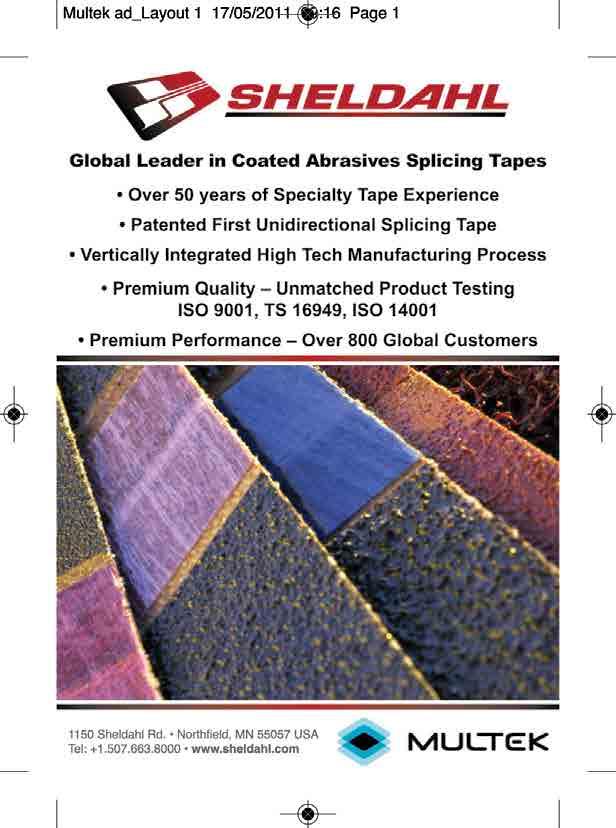
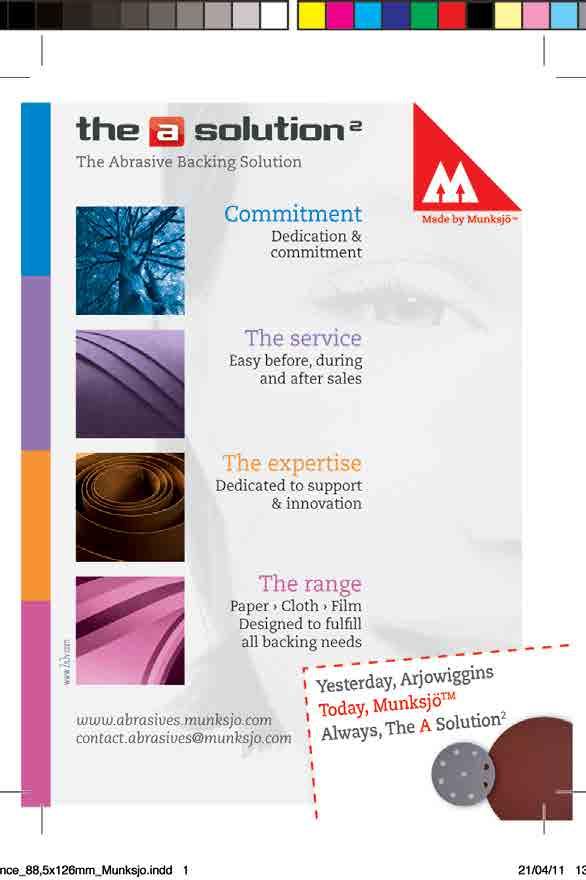
Multek/Sheldahl


Global leadership in the field of coated abrasive technology requires strong technical partnerships. The Sheldahl Materials group patented unidirectional tape technology more than 20 years ago and continues to be the world recognized leading supplier of coated abrasive belt splicing products. Hermes has a rich tradition of producing high quality products. Hermes recognizes that their innovative abrasive belts require the highest quality splicing tapes available. Hermes preferred tape supplier is Sheldahl Materials.
Michael R Truax, Product Manager Multek/Sheldahl, 507-663-8363 office, 507-261-0813 cell
Optimising production and workflow

Hermes has invested heavily in product development over the years as well as in its organisation of work-flow procedures. The LEAN production principles that the company has adopted have helped it to see the recent economic downturn as an opportunity to improve production efficiency and rationalise its structure and work-flow. As a result, it has been able to reduce complexity in its production procedures and increase its efficiency significantly.
Hermes operates six main production plants in four locations, as well as running another five converting facilities worldwide. As part of its ongoing commitment to LEAN principles, Hermes modified its production plants and derived many benefits and advantages by doing so. The know-how concerning new technologies is being developed constantly at the company’s R&D centre in Hamburg.
Dr Becker commented, “In order to produce high-end products, our philosophy is to keep all key production technologies inhouse. Recent notable advances have been achieved with entirely new products, such as our conglomerate grain for long belt life called Mercurit®, our latest non-woven abrasives called webrax® and the expansion of our production capability. We have opened up an entirely new abrasive converting facility in Shanghai, China. This enterprise gives us the opportunity to achieve fast growth in this dynamic, emerging marketplace.”
Besides the traditional markets that Hermes serves, the company is always looking out for new challenges. This applies to new markets, as well as niche markets, such as wind power station producers which have a high demand for finishing paper discs to finish fibre glass and carbon fibre composite materials. For composite sanding, Hermes offers a comprehensive portfolio of advanced products with newly developed, high-performance finishing discs. These discs are developed with sharp aluminium oxide grain and a special non-loading layer that is designed for anti-clogging, long-life sanding and is known as the Longlife brand.

Expanding global reach
Hermes continues to see Europe and North America as its principal markets. In 1980 the company decided to establish a major production facility in Virginia, USA and has since become a market leader in the supply of coated and bonded abrasives in North America. During the past few years the company has also invested in China and in South America and is currently seeing growth in these markets of more than 50 per cent per annum.
The fact that Hermes is present in all the main industrial countries today is in itself a clear advantage for its customers. Dr Becker added, “We will see continuing organic growth in the foreseeable future, with growth coming from the sales of our new, engineered abrasives products and we will continue to enhance our strengths in our R&D applications and in our application engineering technology.
“Our technology partnerships with grinding machine builders often lead us to develop new products and new machine systems. This is a service that we offer to customers and demonstrates our willingness to cooperate with all our partners on a technical basis.” n