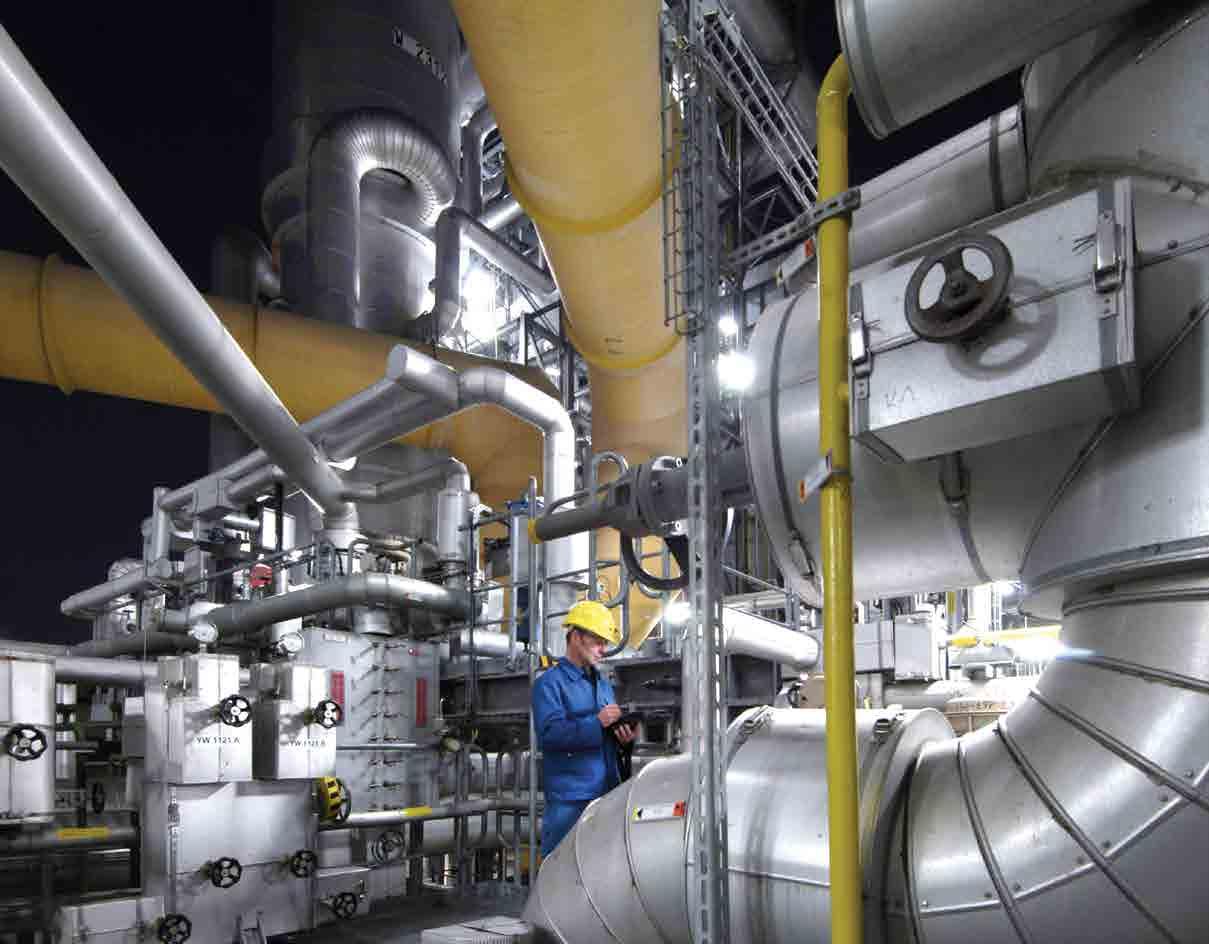
8 minute read
Strong year for European chemicals
© All images credited to press photo BASF
Most chemical producers in Europe have enjoyed a remarkably good twelve months of strong prices, margins and profits, as Nigel Davis, Insight Editor, ICIS, reports.
Some parts of the chemical industry have remained under pressure as European demand has recovered only slowly following the 2008/09 financial crisis and deep recession. But inventories have re-filled and supply chains become much more robust. The key driver for many products has been emerging market demand. China particularly has sucked in imports of chemicals and polymers. China’s stimulus programme has driven demand as has the money pumped by governments into economies in other parts of the world. And as China has boomed, so chemicals demand growth has rebounded strongly in countries like Brazil and India. The combination of returning domestic growth and rapidly expanding overseas markets has pushed up sales and helped lift earnings. Chemical firms in Europe, and indeed globally, coped well with the downturn. Production plants were shuttered at the end of 2008 and in the early part of 2009. Companies hunkered down, cut costs and stocks as they sought to reduce the demand for working capital. Only slowly did capacity come back on-stream dictated by recovering downstream markets.
By 2010, most players in the sector found they were responding to better times. The first half of the year was good and while demand growth in Europe appeared to level off in the third quarter, the year produced record results. Industry giant BASF, the world’s largest chemical company, posted record 2010 financial results and entered 2011 in confidence. The situation was similar across the sector. Match-
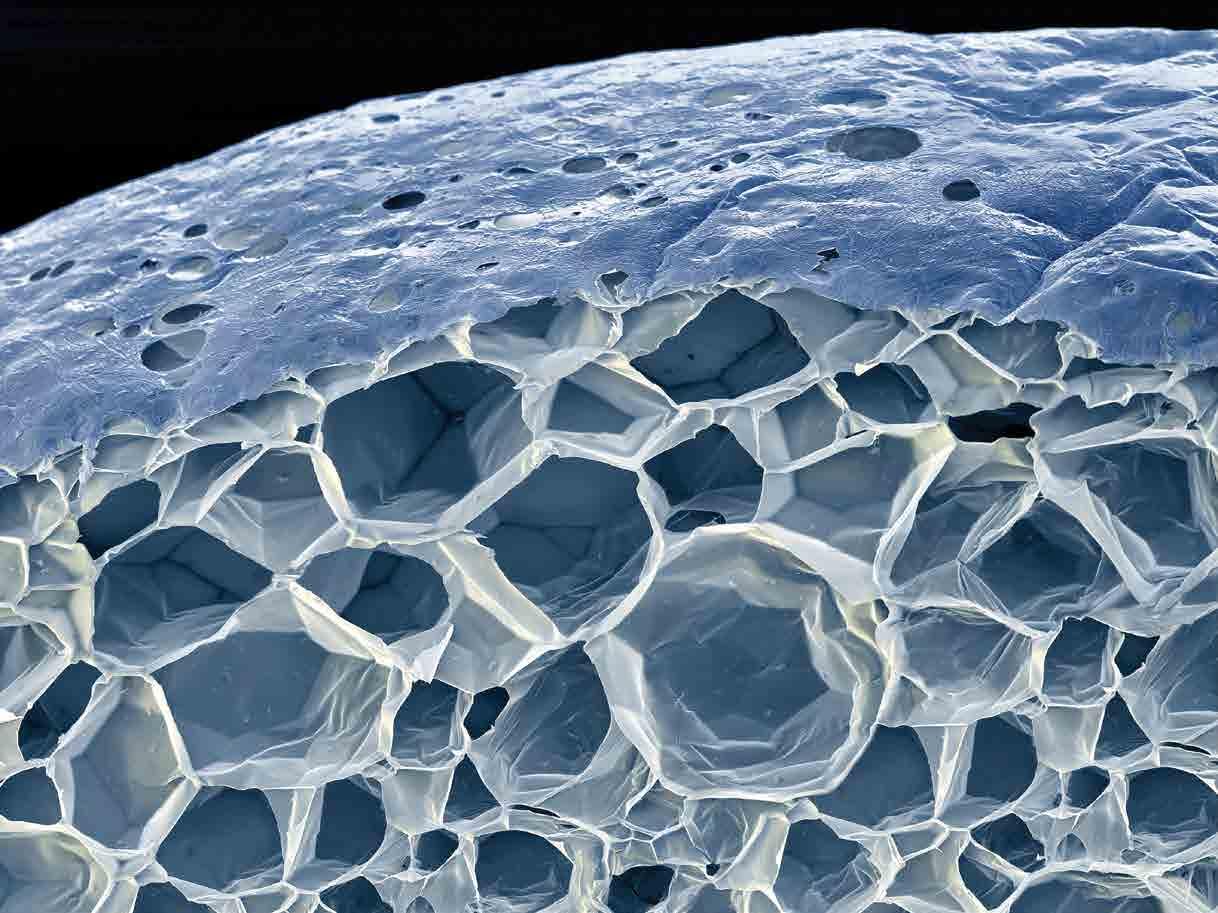
ing output to demand had paid dividends. Upstream, particularly, producers were on a roll. Demand for commodity chemicals had surged as China and some smaller fast growing markets sucked in more volumes. China’s imports of polyethylene, as just one example, increased by more than 50 per cent between 2008 and 2010. Worryingly, the rate of growth of imports has declined markedly in 2011.
Prices in Europe were successfully pushed higher to cover rapidly increasing oil-based raw material costs. Pricing power remained largely with the upstream producer. But, that having been said, even downstream, in market segments for more specialised chemicals, booming demand – into fast growing Asia electronics and automotive markets, for example – was helping lift prices to cover costlier (chemical) raw materials. Recovery was stronger than many had dared hope.
Particularly important in polyolefins and some of the high volume ethylene chain derivatives was the fact that the expansion of supply had matched demand growth. The industry has fretted for long about the addition of significant new low-cost production plants in the Middle East – in countries like Saudi Arabia and Iran. But large-scale units based on cheap gas have not always started up on time or run at planned capacity. Saudi Arabia’s reduced oil output – of 8m bbl/day in 2010/11 – has reduced the availability of ethane gas feedstock for ethylene and polyethylene production for example. China’s demand for polymers has helped soak up output from some of the new facilities.
Not having been depressed by a wave of new capacity, petrochemical and plastics markets have recovered strongly. European producers of ethylene have been able to match output to demand and cover higher oil-based feedstock costs – their primary feedstock is naphtha from the oil refinery. The Brent crude price rose from $75/bbl to more than $110/bbl from the start of 2010 into mid 2011. European naphtha prices climbed as a result. Upstream chemicals prices marched upwards with the price of oil.
The sharp recovery in chemicals produc tion is shown in the official EU statistics. European chemicals production grew by 10.1 per cent in 2010 following the 11.3 per cent year-on-year decline in 2009. The data includes all chemicals sub-sectors apart from pharmaceuticals. Petrochemical production, or output, increased by 8.1 per cent in 2010 while that of inorganic chemicals, some of the most basic chemicals used in industry and commerce, rose by 13.1 per cent, Production of plastics was 15 per cent higher and of speciality chemicals 6.5 per cent ahead. Petrochemicals, plastics and inorganic chemicals, many of the building block materials for the rest of the sector and for important big industrial end-use markets, have clearly led the way out of the downturn. Benefiting at first from strong demand from China and other parts of Asia and to a lesser extent from other emerging market economies, they improved in the latter part of 2010 and the first half of 2011 alongside European manufacturing industry.
And while there was some concern in the third quarter of 2010 that a slowdown was imminent, the output from these sub-sectors continued to grow in the second half and into 2011 as European and North American inventories filled.
Growth continues in 2011
When industry economists came to make forecasts for production growth at the end of 2010, the outlook for 2011 was muted. The European chemicals trade federation
Cefic, for instance, forecast EU chemicals production growth of only 2.5 per cent for the coming year. Concerns about the possible rate of European economic growth hung heavy in the air. As it turned out, however, EU chemicals growth expanded much more strongly in the first half of 2011 than initially expected. Industry forecasts are for annual production growth for the year of 4.5 per cent. EU statistics show a slight slowing of growth in April but the strength of the manufacturing rebound in Germany and other chemical industry in good stead.
“Strong orders from EU durable goods manufacturing, especially light vehicles and machinery and equipment, have led to bottlenecks that now appear in chemicals subsectors as demand outstrips supply,” the chemicals federation said in a statement on 23 June 2011. “Construction, an important chemicals customer, remains depressed but shows early signs of turning the corner,” it added.
Chemicals output in the EU is not yet back to its pre-crisis peak but is expected to reach that level in 2012.
The industry clearly, however, has had to contend with rising oil based raw material costs and with higher energy costs over the past year. Petrochemical producers particularly, however, have been able to manage output to demand extremely well through the period and pass on upward movements in the naphtha price and that of other crude-related feedstocks. For the majority of companies rising demand and still healthy prices have helped buoy profits and margins.
Many producers also benefited from still strong export demand driven by the fiscal stimulus packages still in place in China and indeed, the US. China demand remained particularly strong for most of the period until steps were taken by China’s government in the spring of 2011 to curb inflation and tighten controls on easy credit.
The draw of China’s demand and that from India, for example, was not confined to petrochemicals and the primary plastics. Export demand for speciality and other chemicals helped drive top line growth and profits for producers across the sector upstream and downstream.
Following a strong first quarter Europe’s chemical companies were more convinced that growth had returned to the sector although that confidence wasn’t always apparent in firms further down long chemical chains and those much closer to end-user markets.
Companies upstream talked of improved market conditions although they remained concerned that new capacity additions could work to depress margins later in the year.
Midstream chemical makers, the producers of specialities, coatings and other products reliant on petrochemical feedstocks, eyed recent price rises with some concern even though most of them had produced good first quarter financial results.
And many companies expected the economic recovery to remain fragile while acknowledging their reliance on strong Asian demand.
But a company like Dow Chemical, a diversified chemicals maker and the largest chemicals producer in the US, was able to talk about demand growth returning in developed world markets.
Strengthened consumer spending in electronics, appliances and automotive markets was lifting chemicals demand. Demand growth was returning in developed markets, with strengthened consumer spending in areas such as electronics, appliances and automotive. These positive developments were offsetting weak construction market demand and sovereign debt issues in southern Europe.
Germany based chemicals giant BASF saw little to be too concerned about although it acknowledged that geopolitical uncertainty could have a negative impact on business later in the year.
The second quarter appears to have been just as strong, if not stronger, for some firms although concerns are growing at the end of June 2011 that the end of quantitative easing in the US and China’s efforts to curb inflation will have a very real effect on business in the second half. Eurozone instability, the still high oil price and the unknown China conspire to make outlook particularly uncertain
That market uncertainty has not stopped chemical companies taking advantage of the improved situation to make the strategic merger and acquisition (M&A) and capital investment decisions that will characterise the future shape of the sector.
BASF, for instance, said in May 2011 that it would build the world’s largest single-train polyurethane intermediate TDI plant in Europe. So much investment has flowed to Asia in recent years that the decision was particularly welcome. In the first quarter, Belgium based chemicals and plastics maker Solvay said it intended to acquire France’s Rhodia in a deal that had the sanction of the Rhodia board. The intended acquisition is seen as a good strategic fit and one that will enhance the competiveness of important parts of the European chemicals industry.
Having emerged from an extremely difficult period Europe’s chemical companies remain cautious but optimistic. The coming quarters could be difficult as economies globally continue to struggle with the aftermath of the financial crisis. Chemical producers too have to contend with the longer-term trends related to the de-industrialisation of Europe and the rising global importance of new competitors from the Middle East, South, North and South East Asia. Burdened with high costs and a difficult regulatory environment they have to develop robust strategic models to compete successfully in an increasingly global business environment. n
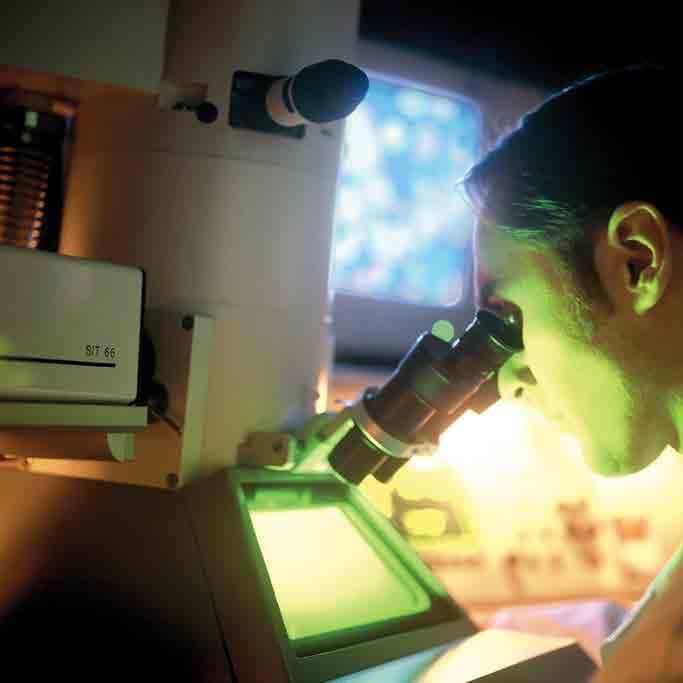