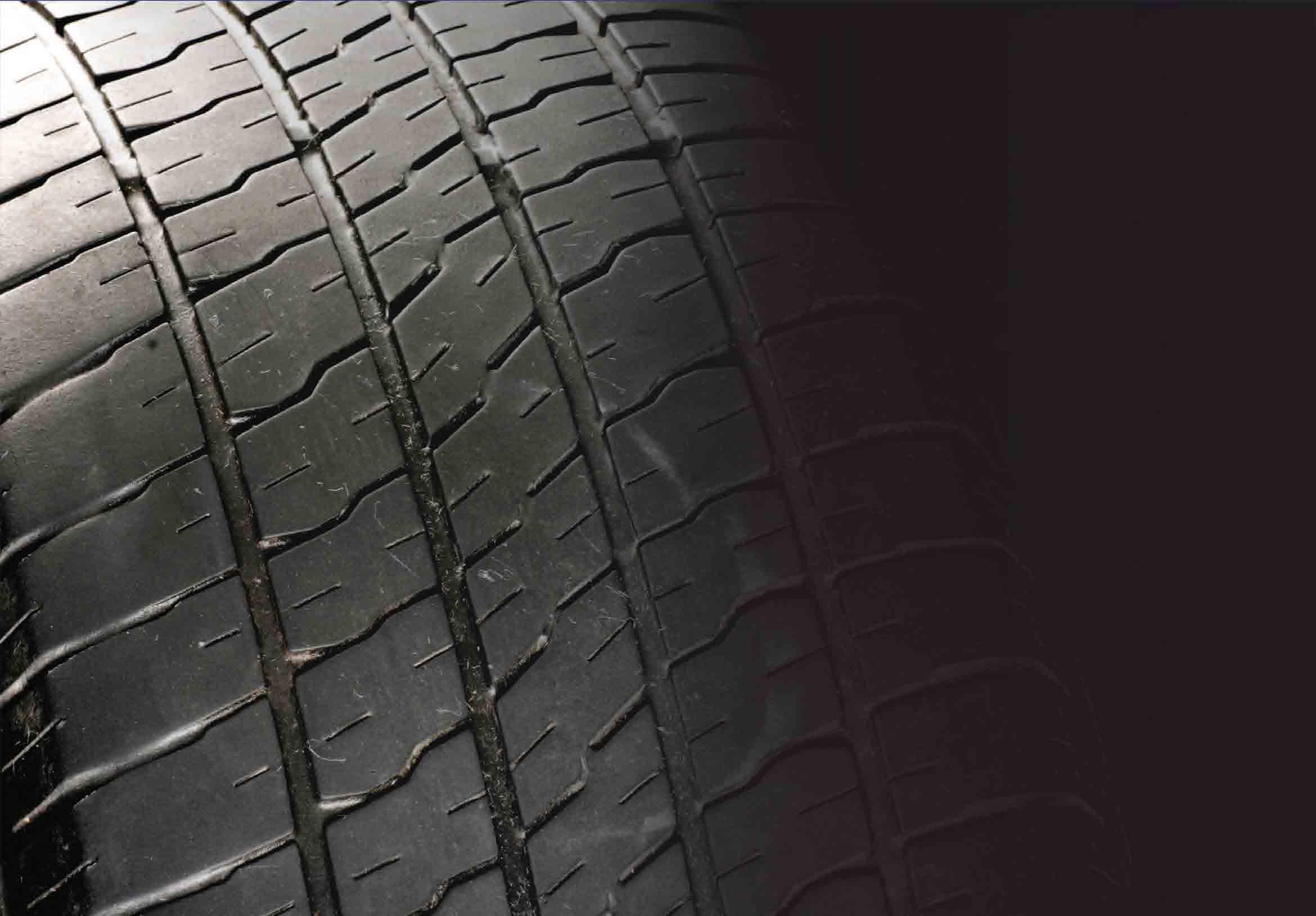
5 minute read
Driving the tyre industry forward
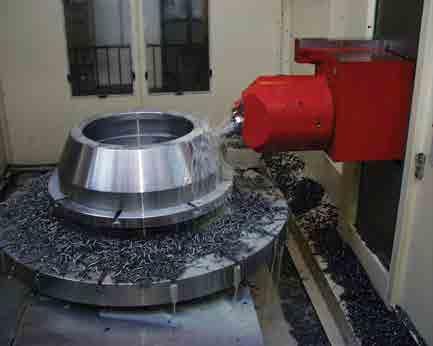
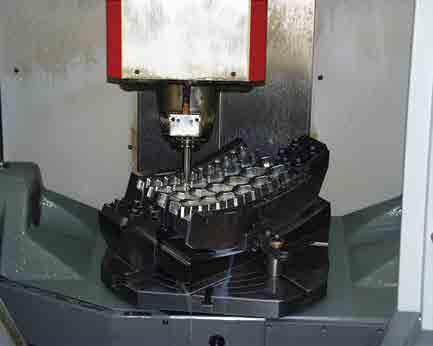

DRIVING THE TYRE
INDUSTRY FORWARD
Herbert Maschinenbau is a global leader in the design and manufacture of moulds for tyres starting with the size for passenger cars up to the largest size for earth movers. Philip Yorke talked to Martin Grosch, Herbert’s managing director about the company’s continuing investment in automation and its plans for future expansion.
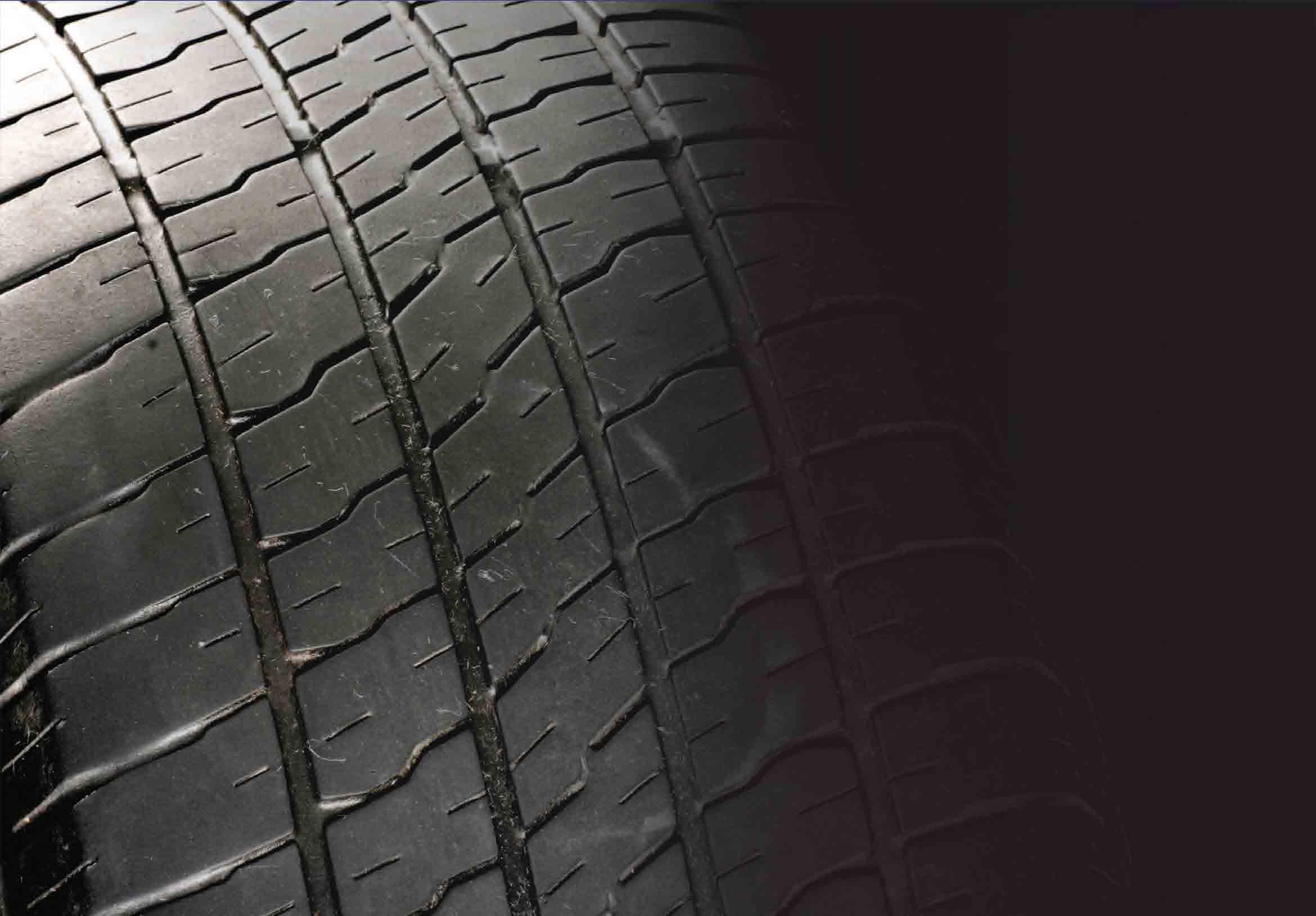
Herbert Maschinenbau was founded in Germany in 1905 in Frankfurt/Main by Leonhard Herbert for the purpose of producing tyre moulds. Later the company moved into the manufacture of vulcanising machines for tyres and tubes and subsequently into the production of prefabrication machines and tyre vulcanising presses. After a number of takeovers in the late 1980s the company was acquired by Mr M Walter in 1991 and a new programme of investment began. Today it has two major business sectors: tyre moulds and containers, and machines and equipment manufacturing.
Meeting new global demands
With the increasing globalisation of the automotive and truck markets, Herbert continues to extend its network of worldwide branches and service facilities. This is to ensure that the company’s customers will continue to receive dedicated support globally and products within the shortest possible time frame. In addition, Herbert has developed a process of standardisation to the point that its global network of branches perfectly matches the high standards set by its headquarters in Huenfeld, Germany. The company says that nowadays the time factor is the most decisive criteria for its customers next to quality and precision: Herbert is able to offer both with its state-of-the-art production methods. The company’s manufacturing facilities utilise engraving and eroding machines as well as multi-axle milling and CNC lathing machines.
Grosch said, “We are constantly developing new tooling and moulds to extend our manufacturing capabilities. The difference is that in the old days, say 15 years ago, moulds were made of cast aluminium and when you cleaned them with powder or chemicals it would reduce the life of the mould. Nowadays we make moulds out of steel and our moulds will last as long as the customer requires. Furthermore, our range of tyres today is enormous compared to the range offered just a few years ago. What’s more, we are in the process of moving into other areas and recently took over a mould shop in Ohio, USA for passenger car and truck tyre moulds.
“However, our customer base is small compared to the one of other manufacturers and includes the world’s most famous brands, such as Michelin, Pirelli and Continental. All the smaller manufacturers have been swallowed up by the big players. Today the emphasis is on providing faster services and clients expect to start a project immediately and have a mould back in the press within four or five days. Lead times for new products for passenger car moulds, motorbike tyre moulds and truck moulds have all shrunk significantly. We have adapted our workflow and management systems accordingly and meet these new deadlines without compromising quality.
“Also, we are the only manufacturer in the world who can offer customers the entire manufacturing process from the design to the final product for the complete range of tyre sizes, whereas our competitors are
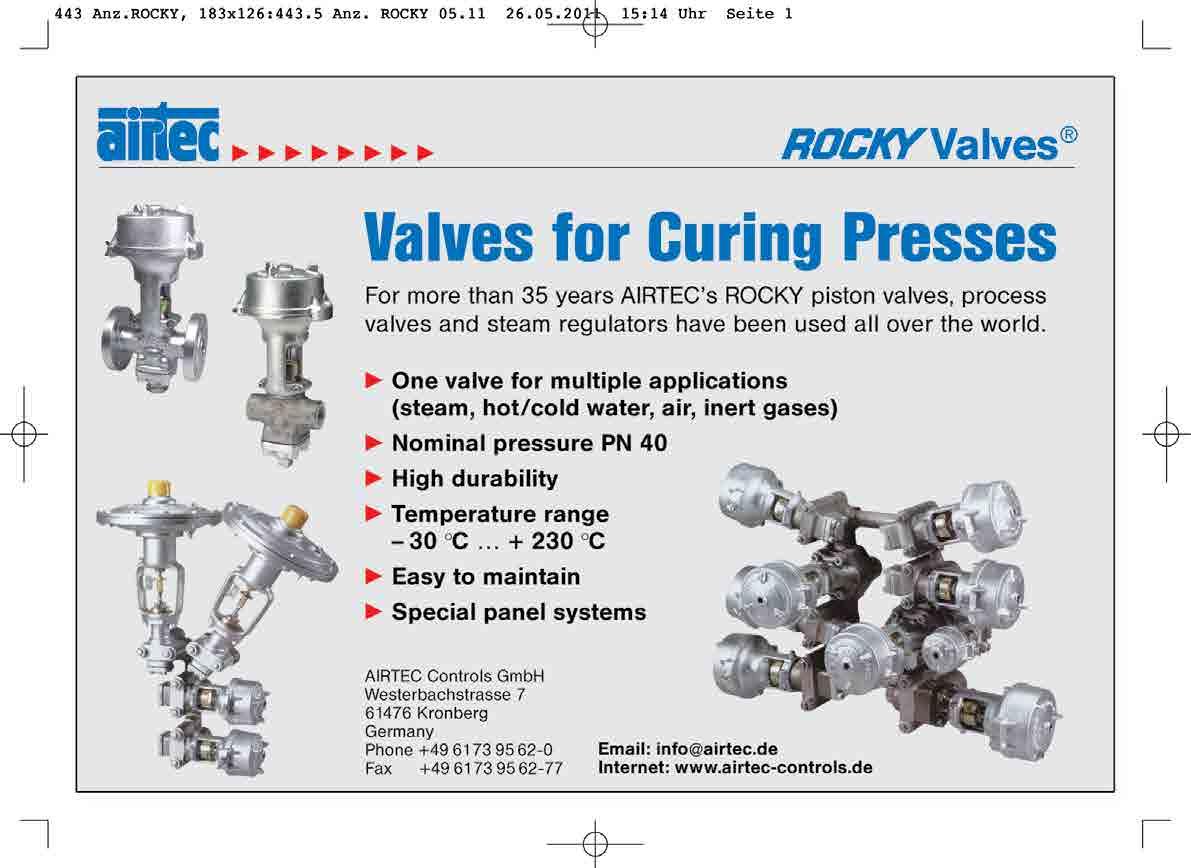
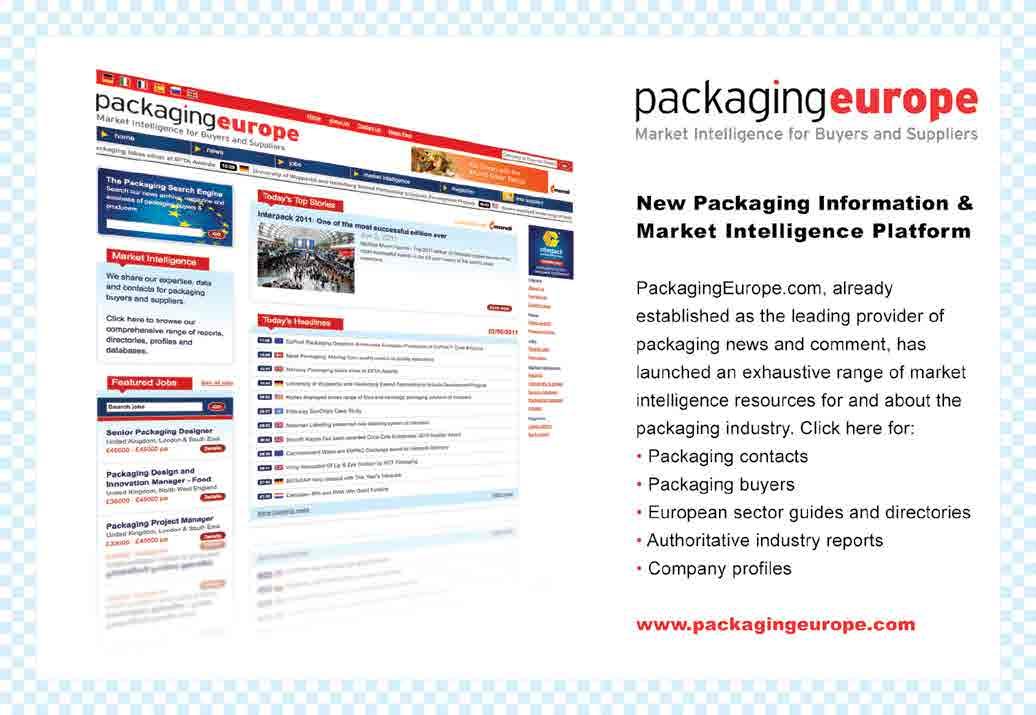
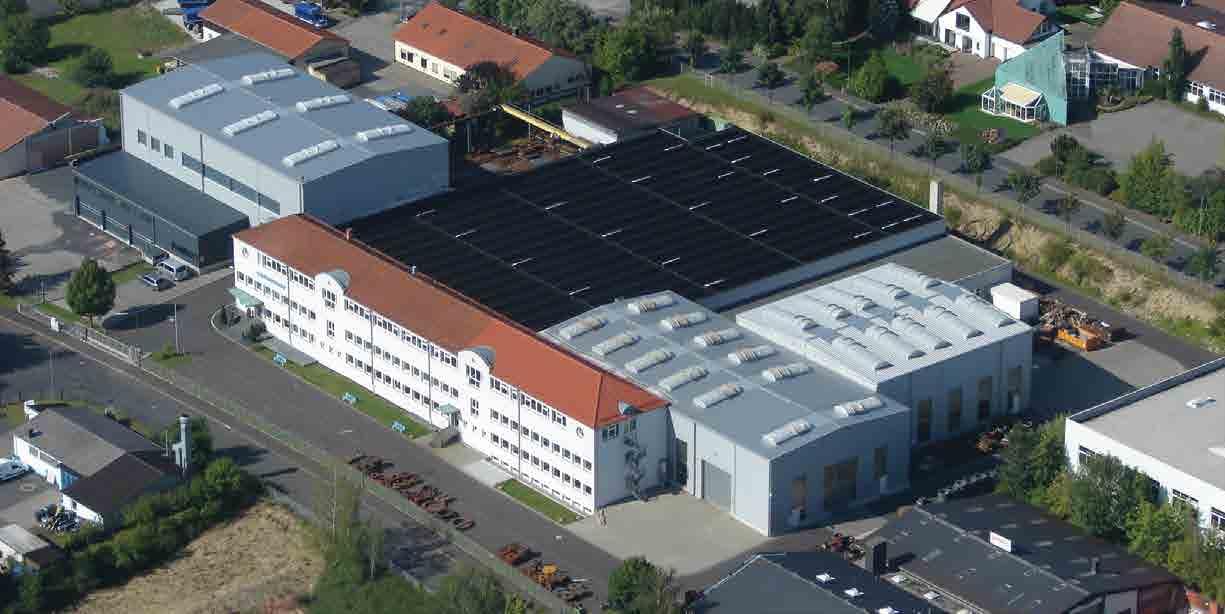
only structured to produce either moulds or containers, or if both, then only certain sizes and not the complete range of sizes.”
Strategic alliances strengthen global services
Herbert is an international company that has always been customer-focused and as a result ensures that it is always located in close proximity to its client’s manufacturing centres. The company’s quality policy objective is to ensure that its customers receive top quality, reliable and cost-effective products on time.
Grosch added, “In order to further strengthen our customer service focus we have entered into a strategic alliance with BPS Engineering Tennessee, with offices in the USA, to extend our manufacturing capabilities for tyre building tooling. They were searching for a partner to cover the EU and Asian markets. In return they have taken over our sales in the US markets and we in turn took over their sales in South America, Europe and Asia.
“Today we are facing competition from a range of niche players, but since we are able to do everything in-house, we can guarantee secrecy and confidentiality. However, we know how strong China is, so we have to be careful. We have also entered into a strategic alliance with an Argentinean supplier and recently took over a leading tyre mould shop in Russia, which employs more than 160 people. This new facility became fully active for us on the first of April this year and we consider Russia as a very interesting growth market.”
Leading the way in moulds and equipment
Manufacturing tyre building equipment has always been a major business sector for Herbert and a contributor to the company’s enviable reputation in the tyre industry. This is in addition to providing a significant contribution to its global sales performance. The company manufactures a wide range of tyre manufacturing products, from advanced curing presses to tyre building drums and transfer rings. In the tyre curing sector alone, Herbert offers a wide range of products to meet a variety of application-specific solutions. These include hydraulic frame-type tyre curing presses, hydraulic column-type curing presses and hydraulic curing presses for truck L/T tyres.
Herbert’s range of moulds is equally diverse with moulds with cast tread patterns, bladder moulds for longer bladder durability, moulds with engraved tread patterns, moulds with inserted tread ribs and sipes and ‘puzzle’ moulds, which provide a completely smooth surface directly after curing. n
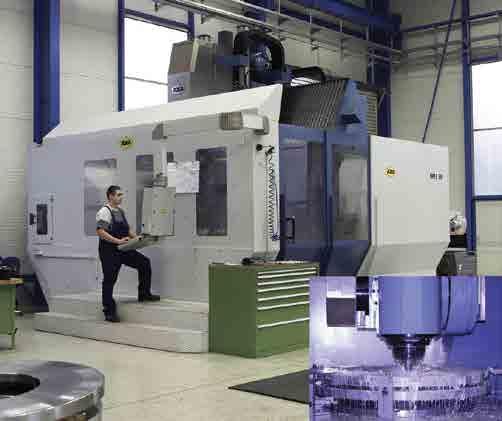
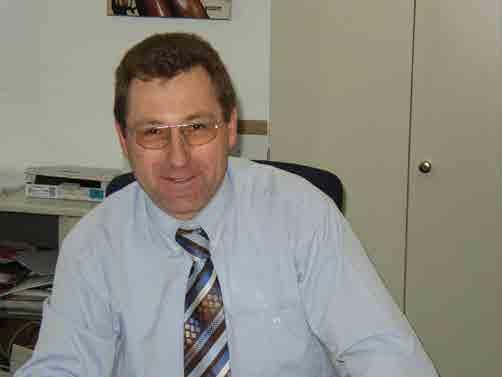