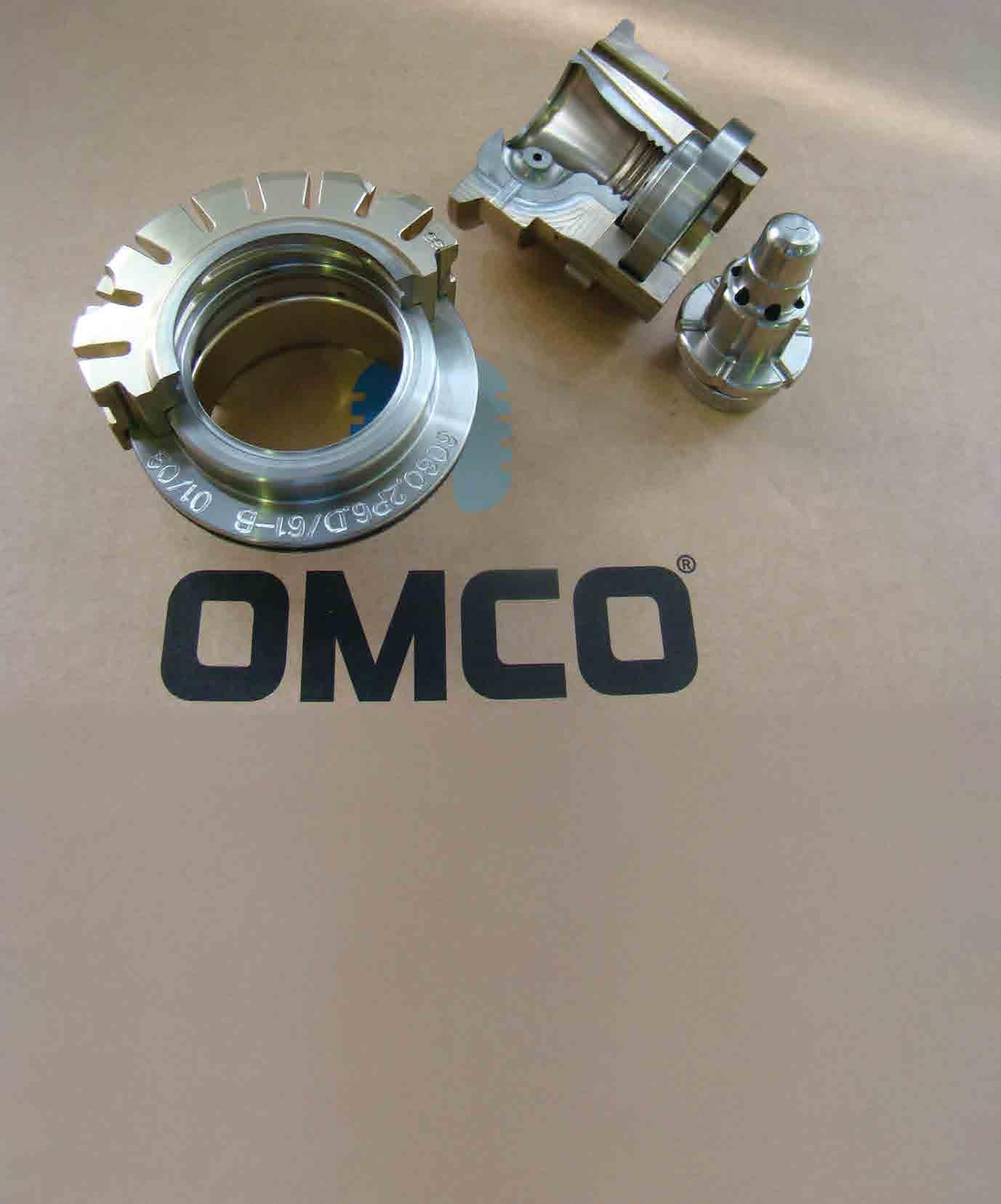
5 minute read
The new Bronze Age Omco
THE NEW BRONZE AGE
OMCO is a global leader in the manufacture of moulds for the Glass Container industry. Philip Yorke talked to Peter Dean, the company’s international sales director, about Omco’s latest aluminium bronze products and its move into new world markets.
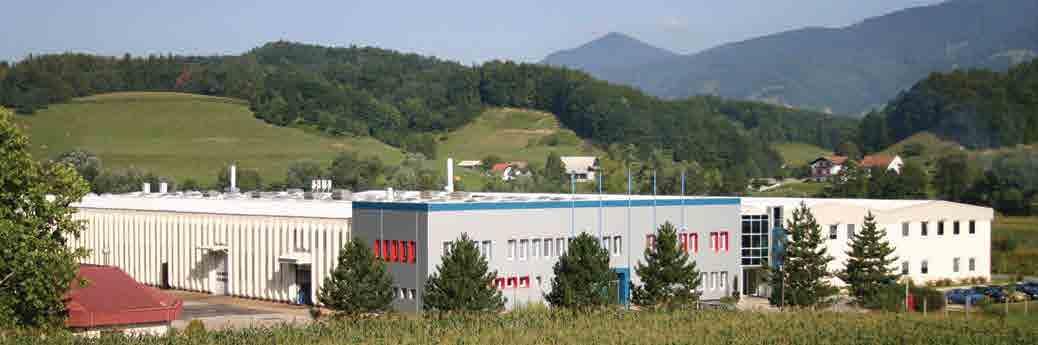
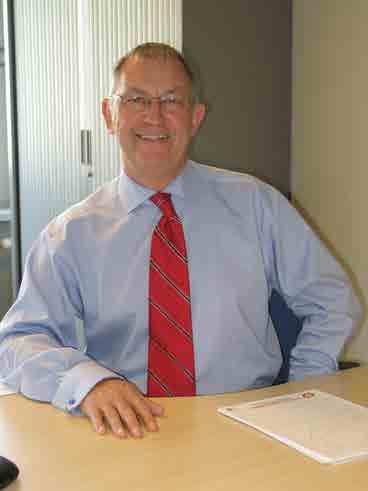
Omco was founded in Aalter, Belgium in 1964 and as a result of consistent organic growth and acquisitions is now Europe’s leading mould manufacturer for the glass container industry. The Omco Group now has seven major production facilities in Europe and a Head Office in Belgium. In 1974 it acquired a foundry in Hamme, Belgium in order to supply in-house castings to a very high standard in varying grades of cast iron and bronze. In addition, the company acquired a second foundry in Slovenia in 2001; this enhances the group’s needs for speciality castings.
The Omco Group has achieved several other milestones since 2001 with the foundation of Omco Istanbul (a 50/50 joint venture with the Sise Cam Group), the establishing of Omco Romania and most recently EMCO in the USA. Today the BMT/Omco Group has a turnover of €270 million and employs approximately 3200 people. The Omco glass mould division represents approximately one third of the group’s turnover and human resource capability.
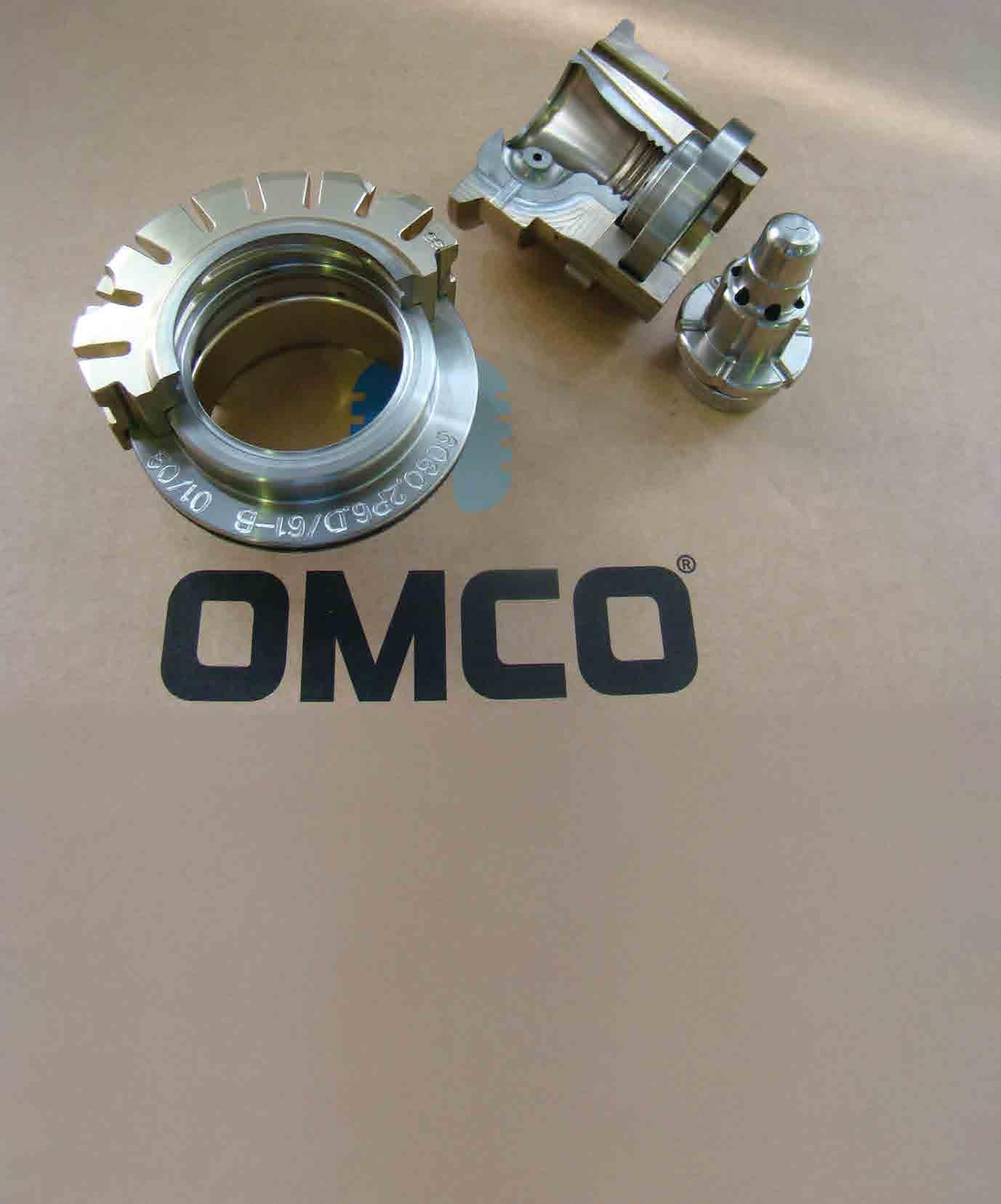
Meeting new demands
Omco offers products for the hollow glass industry based on specially developed castings in grey flake and nodular iron as well as in aluminium bronze. The company supplies globally to the glass container producers whose key markets are food, beverages and pharmaceuticals. While glass container producers face tougher demands from consumers as well as rising energy costs and increased competition from alternative packaging, Omco has evolved to provide its customers with higher quality products and shorter lead times, whilst at the same time offering increasingly competitive price levels.
Peter said, “The biggest market sectors being served by our customers are food and beverages, the beverage part of the business is high volume for the soft drink, wine, beer and spirit markets. With Omco’s customers needing to save energy at every stage and compete with alternative packaging the demand for lightweight glass without any loss of integral strength became crucial. As a result of these changing market forces, we assisted our customers process changes with the introduction of special ‘aluminium bronze’ moulds with an expensive copper based material which increases the mould life and allows the glass bottle maker to increase his productivity.
“The quality of the basic material that we use is key to the quality of the final product, which must be polished to a mirror finish.The latest ‘Individual Section’ (IS) machines can produce in excess of 600 hollow glass bottles a minute and one single mould can manufacture up to one million glass containers. We apply a nickel coating to protect the cavity edges so that no ‘break-away’ occurs during the production process and creating an ease of repair.
“However, despite the enormous advances in modern manufacturing techniques, there are certain critical elements that often require old fashioned craftsmanship. For example, on the Johnny Walker spirit bottle, the striding man logo is also depicted in the shoulder of the bottle. This image is created by our highly skilled craftsmen to form part of the final mould. To achieve the highest standards of mould manufacture we invest heavily in the latest state of the art CNC machinery sourced in the main from Japan.”
Continuous investment programme
Whilst the ongoing demand for advanced, high-tech glass products grows, many bottle makers are experiencing strong growth. In answer to the surge in demand for glass packaging products, partially caused by the need to use sustainable and 100 per cent recyclable materials, Omco has announced further expansion at three of its European facilities Croatia, Romania and the UK. In addition, it has entered into a new joint venture with the leading Indian glass container producer, Hindustan National Glass (HNG). This joint venture will be a 50/50 shareholding arrangement with the first major manufacturing facility operational by the autumn of 2011. This follows a significant investment in advanced foundry technology and the latest CNC mould-making equipment. Initial production is expected to reach over 4000 ‘cavities’ per month, along with their ancillary parts.
The company’s largest investment will be at the Iasi plant located in Romania’s second city, which will provide an increase in manufacturing capacity of more than 25 per cent. As global bottle manufacturers strive for lighter, stronger containers and faster machine speeds, Omco has added a varia-
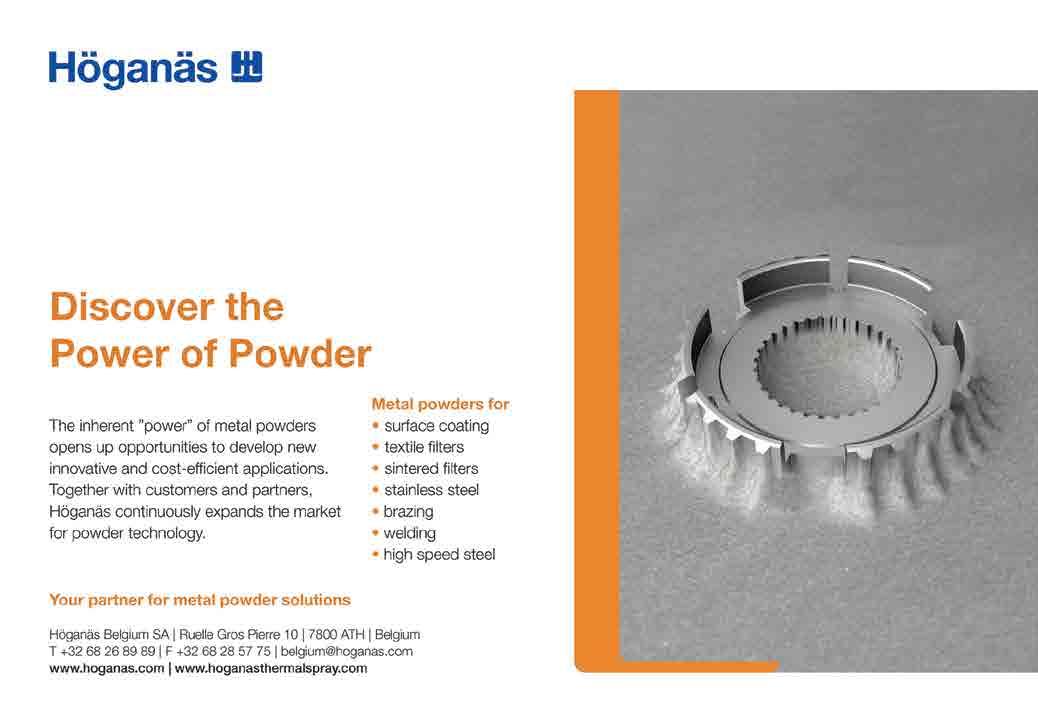

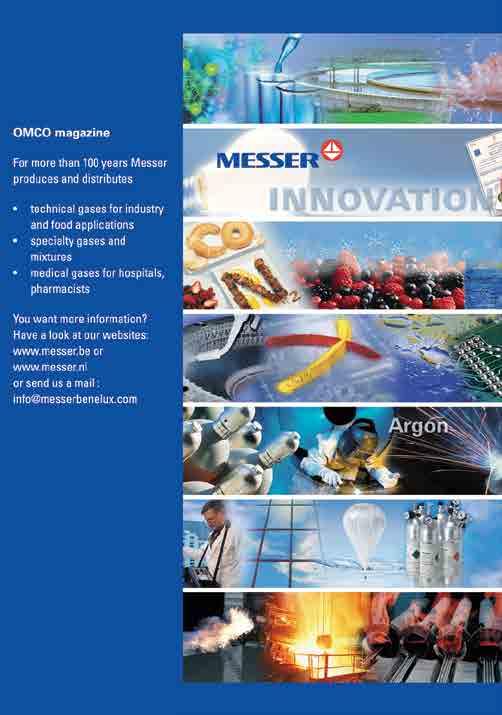
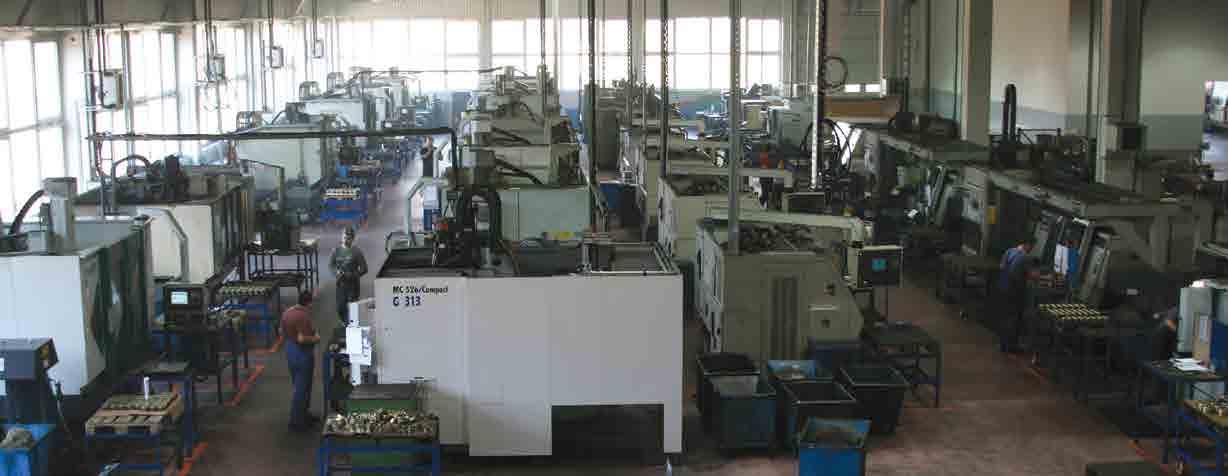
tion to its tried and tested aluminium bronze (OMX) for cavity production only. With its continuous commitment to research and development, Omco is working closely with industry partners to explore the potential benefits of laser hardening for some of its critical components. To underscore its dedication to quality, the Omco Group achieved ISO 9001 certification at all seven of its mould-making facilities in 2010.
Increasing global reach
Omco International and its subsidiaries are part of the BMT Group, which is active in a diverse range of industries. These include the glass mould-making division, which is comprised of nine companies in eight countries; the industrial gears and transmissions division, which is present in four countries with four companies; the aerospace division with three companies in three countries; and the glass engineering division which includes three companies active in two countries.
Peter added, “The investment we are making in India will ensure our high European standards are maintained for the Asian market. We have become truly global with in excess of 100 customers including the emerging markets. In Russia for instance we are now the biggest supplier. In 2011 we will invest over €9 million in new equipment to increase our manufacturing capacity and meet the growing global demand for energy efficient, recyclable glass containers.” n

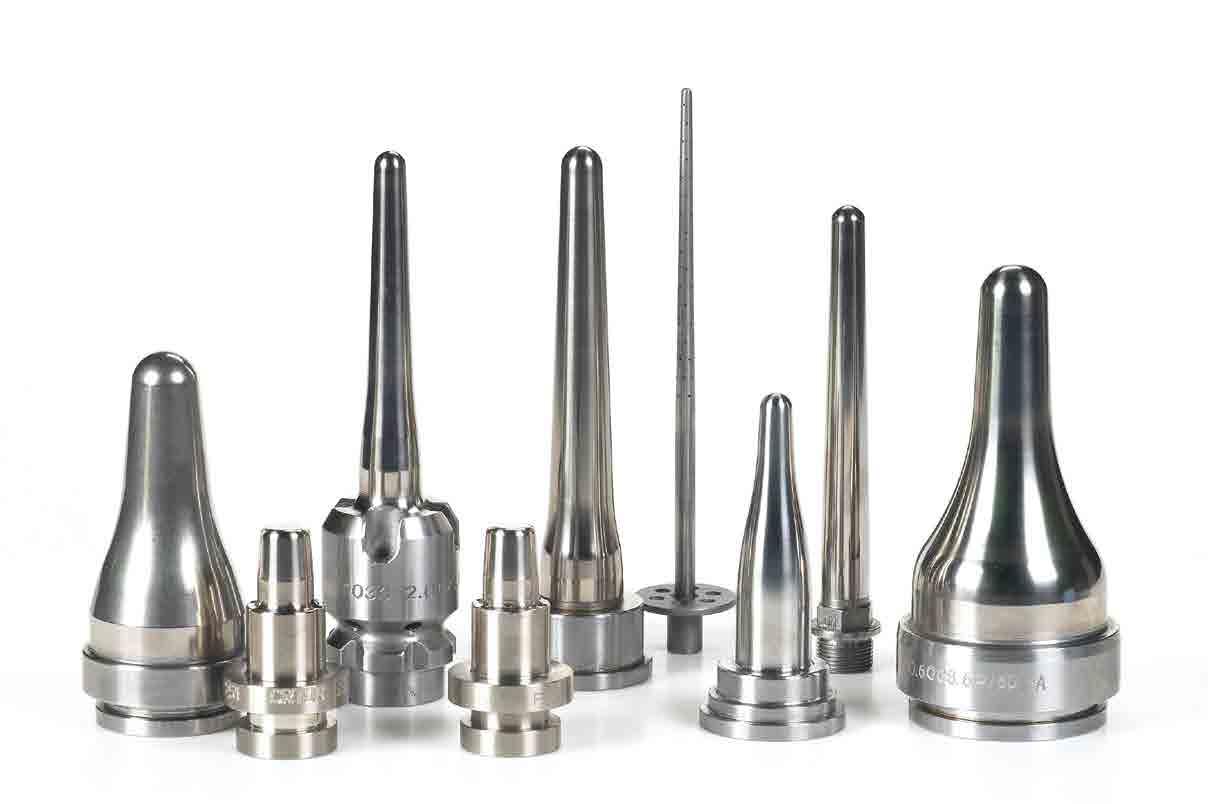