
8 minute read
The future of steel Acciaieria di Rubiera
THE FUTURE OF STEEL
Rubiera Steelworks, headquartered in Casalgrande in the Italian province of Reggio Emilia, is a familyrun manufacturer of ingots for rolling and forging, and continuous casting billets. Eugenia Fiusco looks at its operations, recent investments and plans for the future.
Rubiera Steelworks was founded in 1965 by two men, Mr Testi Sr and Mr Cima Sr, at a time when the market for machining steels was experiencing strong growth. “The company’s founder is Mr Cima Sr, who has now retired,” says current company director, Mr Franco Testi. “He and I have run the company for the past decades, so the future is now in the hands of our brave young men,” he says, referring to their two sons Mr Mario Cima and Mr Claudio Testi.
At first, the business was characterised by the mass production of common steel, such as ingots for rolled rods and
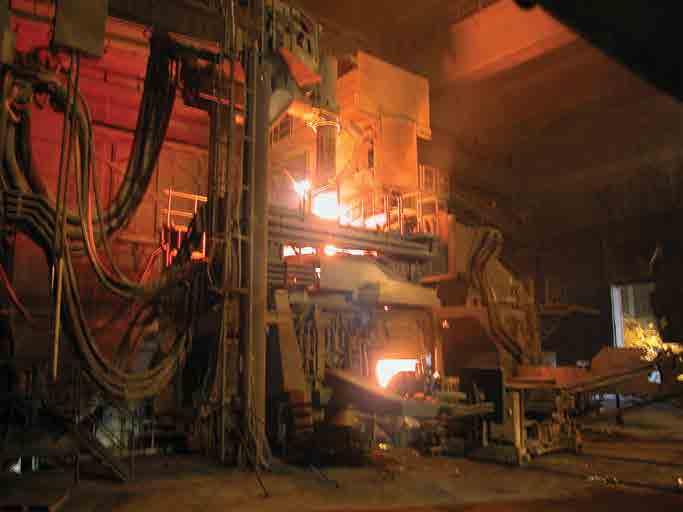
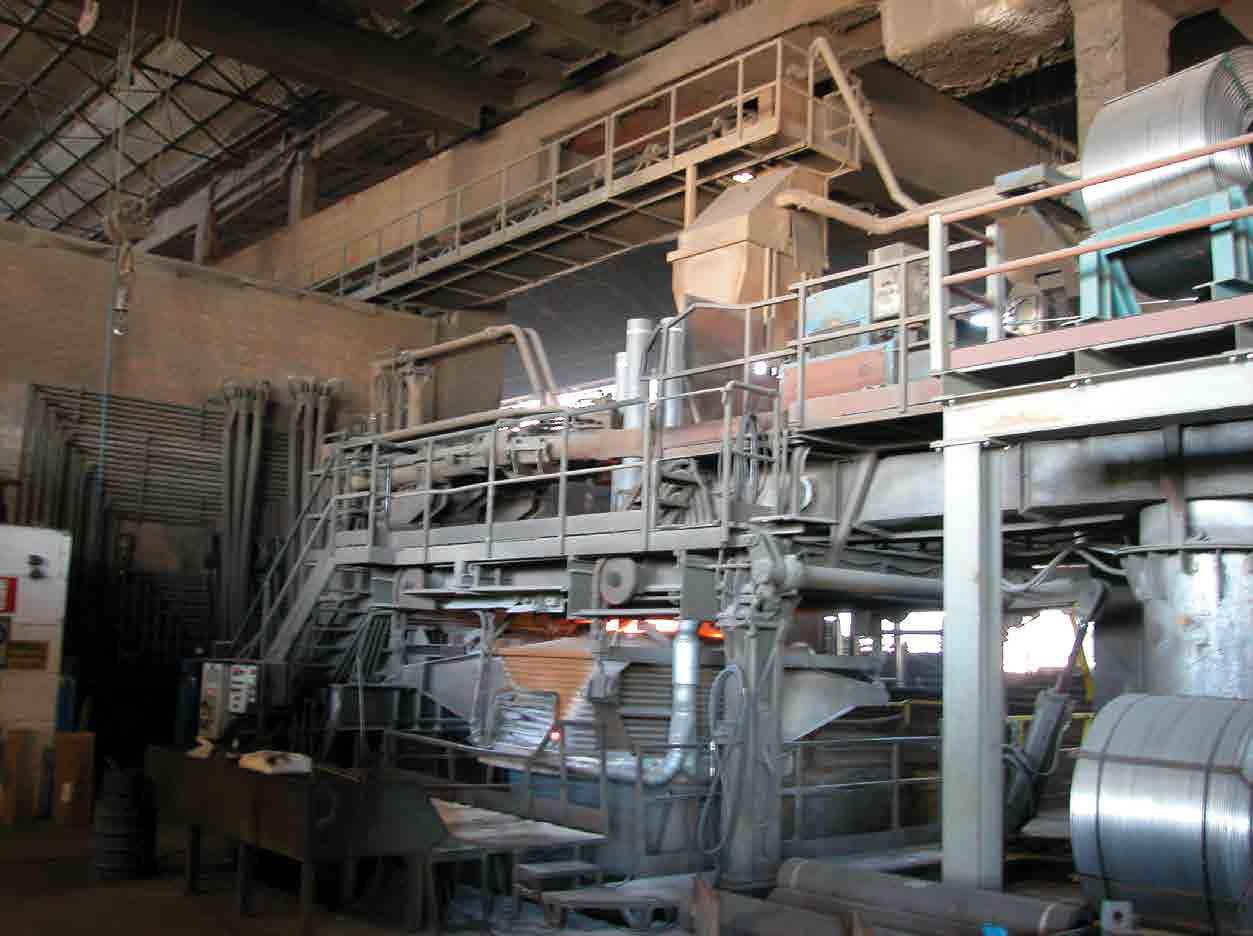
reinforced concrete rebar. However, the company grew year-on-year along with the available technology, making it possible for it to offer increased quality and more refined products. In particular, the casting department was expanded and two electrical furnaces, as well as a continuous casting plant for billet production, were installed. In the early 1990s, Rubiera Steelworks was the first Italian company to use DC arc furnaces – a technology which improved product quality and reduced power, electrode and refractory consumption in comparison to the existing technology.
Products and applications
Rubiera Steelworks’ production profile falls into two main categories: ingots for rolling and forging (round, square and polygonal bars from 1 to 120 tonnes) and continuous casting billets (square and round bars with cross sections of 100, 120, 145, 160 and 180mm). The former represents twothirds of production. The latter, meanwhile, accounts for one-third and is used mainly in the automotive industry for the manufacture of gear levers. The steels used include manganese, chrome and low or medium carbon.
“The main applications of our products are in the energy and the oil and gas markets,” explains R&D manager Mr Cima Jr. “In the energy market we are particularly prominent in wind power. We produce gas and steam turbines, wind tower shaft generators and coupling fringes. In the oil and gas market we provide steels which are used to manufacture tools to carry out methane extractions in Italy and abroad. Rubiera Steelworks also supplies steels for nitriding and tool steels, which are employed in industrial processes such as aluminium or steel extrusion. The energy market is both the most profitable and the most challenging – thus, it is the most rewarding.”
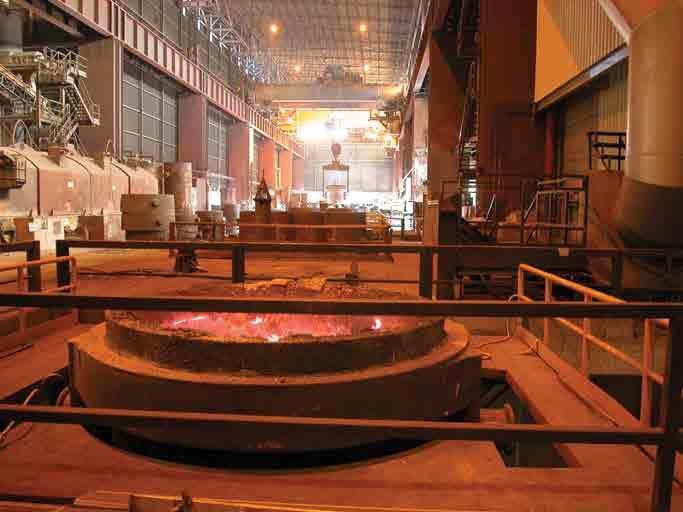
Nuova Fonderia di Castenedolo S.p.A. supplies best quality cast iron ingot moulds. For over 60 years Nuova Fonderia di Castenedolo S.p.A. have been dealing with cast iron ingot mould. Over a surface area of 120.000 sq. m., of which 20.000 covered, Nuova Fonderia works with cast iron and makes ingot mould with an important quality certification.The yearly output of about 25.000 t is obtained with the following equipment:n°1, 50-t electric induction smelting furnace for cast iron and ingot mould n°1, 65-t electric induction smelting furnace for cast iron and ingot mould n°1, electric crucible furnace of T25 for cast iron and ingot mould Equipment of appropiate size for production of cast iron and ingot mould, working and handling the products used and obtained.
Certifications Nuova Fonderia di Castenedolo S.p.A. got its UNIISO9002/ today ISO 9001:2000, quality certification in 1998.
Nuova Fondera di Castenedolo products: Ingot moulds, slag pots, plates, counter plates, tundish covers, sprues, hot tops, grounds, hematite cast iron fly doheels up to 100 T/each and spheroidal cast iron up to 30 T. Nuova Fonderia di Castenedolo cast iron production includes: round ingot moulds, square ingot moulds and polygonal ingot moulds for slabs up to a maximum lenght of 5.7 m.
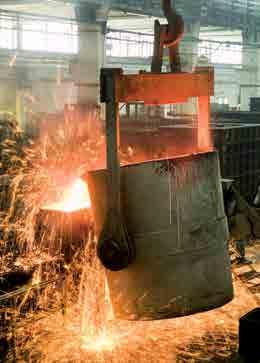
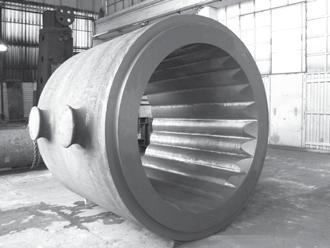

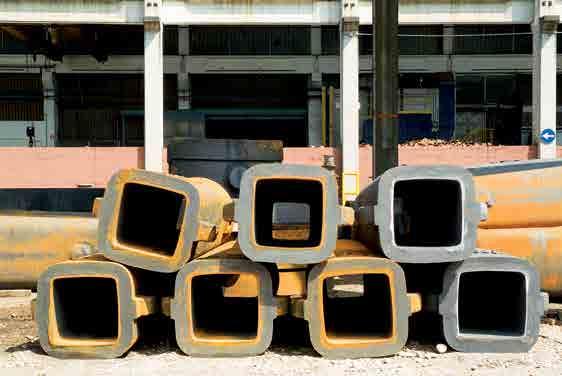
25014 Castenedolo (BS) ITALIA Via Patrioti no118 Tel. 030 2731137 - Fax 030 2731839 E-mail commerciale@nuovafonderia.com info@nuovafonderia.com
C.C.I.A.A. Brescia no348817 iscr. Trib. BS no53314 P.IVA 03261190171
Via S. Zeno 388, 25124 Brescia, Italy Tel: +39 / 030.2160622 Fax: +39 / 030.2160592 Web: www.fonderiesanzeno.it E-mail: info@fonderiesanzeno.com
Sales manager: Eng. Carlotta Antonini E-mail: carlotta.antonini@fonderiesanzeno.com
Fonderie S.Zeno covers 32.000 square metres, 12,000 of which are covered. It was founded in 1960 as a foundry for the production of ingot moulds and hematite casting for steel plants. In the 70's, Dr. Silvano Antonini, the Company's young owner, perceived the importance of the introduction of continuous casting in steel production and decided to diversify the product range by adding rolling mill roll to ingot mould production destined mainly for the Italian hot rolling mills. In the 80's, roll production reached ingot mould production levels with exports to Europe, Latin America, the USA, Asia and Far East. At the end of the 80's the company adopted a personnel qualification and production reorganisation strategy that led to ISO 9001 certification. In the new millennium, when the second generation of the Antonini family joined the Company, the Fonderie S.Zeno took courageous steps towards technological and computer innovation which could employ materials to improve product quality thanks to the new production processes. The Company's mission is the customer satisfaction, which is achieved through continuous material improvements and flexibility derived from a streamline and well-organised structure, characterised by the direct management of key positions by the owners. Customers are assisted throughout the process, from grade choice to post-sales, thus guaranteeing delivery schedules and constant product quality.



Ca.m.i. Depurazioni s.r.l. performs its activity since 1970 in environmental protect plant.
Working out feasibility studies, plant design and construction in environmental field of industrial processes, our company operates mainly in the following sectors: Steel plant, foundry ferrous and non ferrous, Ceramic tile, sanitary production, brick-works, dye stuff production and preparation, cement factories etc.
Our most frequent produced and commercialized equipments are: ● Filtering systems: efficient aspiration of volatile solids from working places prevents dust proliferation in the establishment improving clean working conditions for machinery and operator. We supply: filter units (either dry and wet systems) for dust collection and fume filtration (with pollutant elimination), aspiration hood design and construction, pneumatic cleaning, odour control (active-C filters), VOS elimination. ● Waste water treatment plants: water has become a more and more precious resource both for human and industrial purposes. We supply: waste water treatments for recycling and/or disposal purpose together with sludge management systems for industrial processes (both chemical/physical and biological), inverse osmosis, ionic exchange resins, water de-hardening and potabilization plants. ● Energy recovery: energy can be recovered and reintroduced into the production process. We supply: air/fume and water/fume heat exchangers, economizers. ● Sound proofing systems: for realizing healthy working conditions around noisy equipments. We supply: Sound proofing cabinets, acoustic isolation of rooms, silencers. ● Pneumatic transport: high speed and clean transportation of solids across the establishment. We supply: high and low pneumatic pressure plants. ● Special equipments: spray cabins with wet film or dry (our patent) with centralized or autonomous aspiration system, double clapet discharge valve, actuated butterfly valves, sludge agitation tanks, polielectrolite preparation stations, etc. ● Engineering: design and construction of metallic carpentry and piping based on our proper know how and our own drawings. We are able to realize turnkey plant supplies.
CA.M.I. Depurazione S.r.l., Via XX Settembre, 18 Fraz. Ubersetto, 41042 - Fiorano Modenese (MO) Tel.: +39 0536 843 861, Fax: +39 0536 845 670, +39 0536 927 350, P.Iva: 00251340360, info@camidepurazioni.it, www.camidepurazioni.it
A promising investment
The company is particularly proud of its recent investments which, according to Mr Testi Sr, will be able to guarantee a significant profit when the global economy has recovered. “We have invested €60 million in a project aimed at implementing our production. As part of this project, we have equipped our production unit with four remelting plants to improve the quality of steel, a VAR plant (vacuum arc remelting) and three ESR plants (electro-slag remelting).”
Thanks to these investments, Rubiera Steelworks is one of the few companies in Europe, if not the only one, that is able to melt 100 tonnes of ingots. At the moment, the company operates almost exclusively in the Italian market; however, the implementation of the new equipment may increase the number of sales abroad. An important part of its future business may come from the nuclear energy market, which is currently expanding throughout Europe and is constantly in need of remelted steel. “However,” says the commercial director, “we will not set up subsidiaries abroad in the near future. We invest in quality, and this business philosophy has proven to be rewarding, especially during the difficult times the economy has undergone these last two years.”
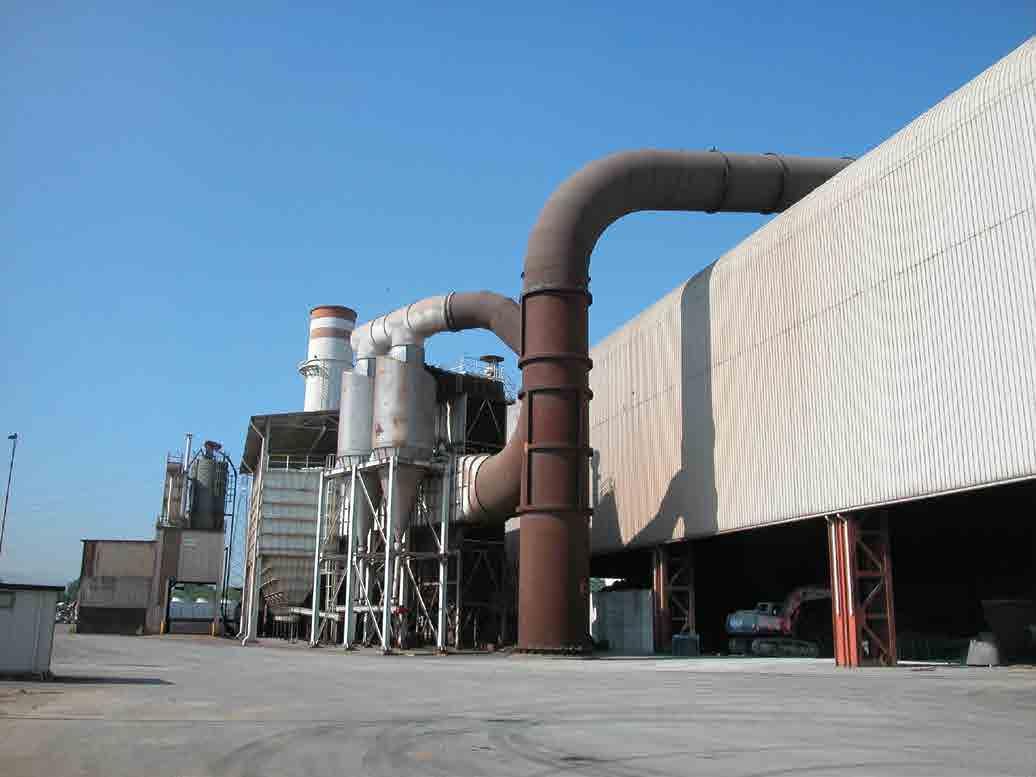
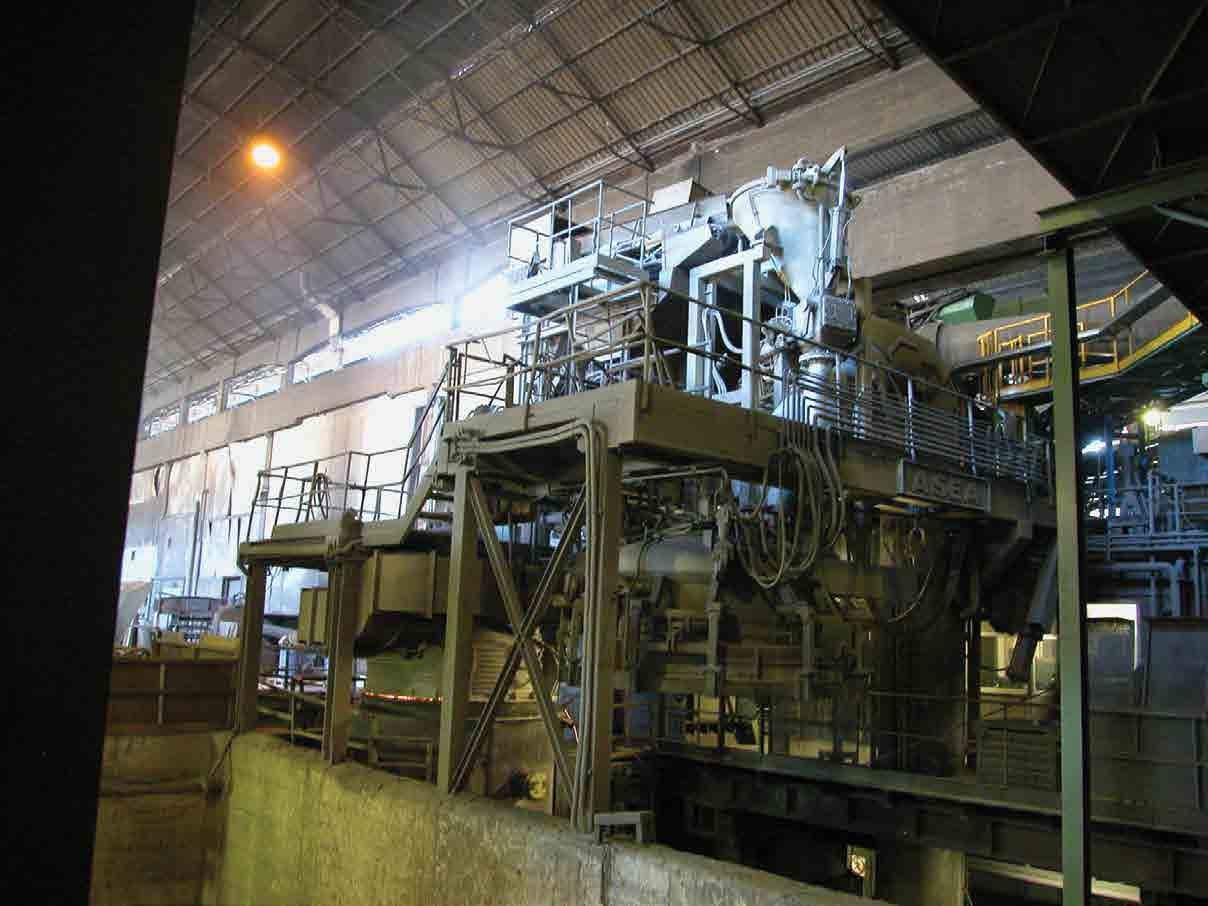
Health & safety and future goals
Rubiera Steelworks was awarded the ISO 9000 quality certificate more than 10 years ago. As for environmental issues, it was certified according to ISO 14001 last year. This was a huge step forward, as it is one of the very few steelworks in Italy to be EMAS certified. “This is very important to us, because in our industry environmental issues are a delicate matter and have to be taken into serious consideration,” says Mr Testi Jr. The company is also hoping to achieve ISO 18000 certification as soon as possible.
Rubiera Steelworks has invested in the quality of its steels and in exclusive equipment, such as a 100-tonne capacity oven. “Once a goal has been achieved, the entrepreneur has to have another one ready,” says Mr Testi Sr, “and we do have many other goals, ideas and projects for our company. However, at the present time we have to wait for the outcome of the recent investments.” n
Metallurgical equipment from Poland: Ingot Moulds – Bottom Plates – Slag Pots
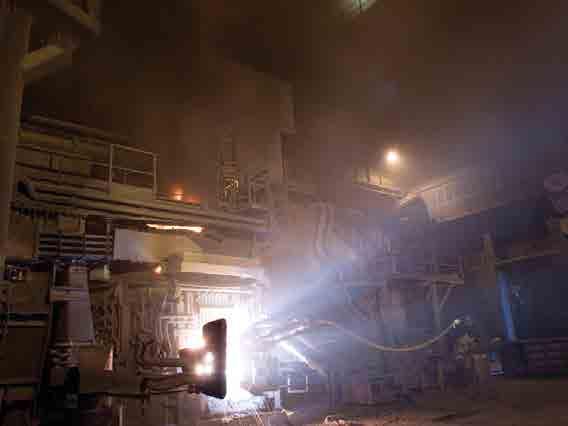
KRAKODLEW S.A.
Ul. Ujastek 1, 30-969 Krakó w, Poland Tel: +48 12 378 76 25, www.krakodlew.com.pl