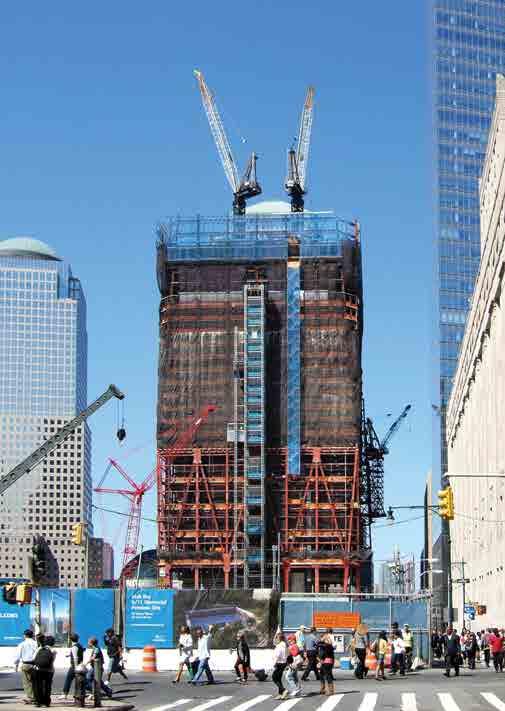
4 minute read
Cutting edges Stainless steel for One World Trade Center

CUTTING EDGES
Stainless steel from Germany is being used to edge the corners of New York’s ‘One World Trade Center’.
Ten years after the destruction of the Twin Towers of New York’s World Trade Center the centrepiece of the redevelopment of the site is already more than half built. One World Trade Center – previously known as the Freedom Tower – is a 105-storey skyscraper that stands to the side of the site of the original Twin Towers. When completed, probably in the middle of 2013, the tower will be the tallest building in the USA. Earlier this year it was announced that the main tenant of the new building will be publishing giant Conde Nast, which will move some 5000 staff into floors 20 to 41. That news itself marked a new chapter in the development of Lower Manhattan, which for more than two centuries has been almost exclusively a financial district.
One World Trade Center is owned by the Port Authority of New York & New Jersey and its construction is being managed by Tishman Construction Corporation of New York. Work on the project began in 2006. The building will have 2.6 million square feet of rentable space, the gross square footage is 3.5 million square feet. The high-rise itself will be 417 metres tall, topped with a 124-metre antenna. The total height of 541 metres corresponds exactly to 1776 feet, a reference to the American Declaration of Independence in 1776. Adjacent to the tower will be a museum and memorial to the victims of September 11, 2001.
The final architectural design of the building now under construction was drawn up in the New York office of the international architectural firm Skidmore, Owings & Merill. The outer facade of the skyscraper will be made of glass. Above the 60-metre-high base, the metal frames surrounding the glass panes will be clad with stainless steel panels. The outstanding architectural feature of the design is that the edges of the building rotate through an angle of 45 degrees from the base upwards. All the corner elements therefore have to be made in a tapering form in line with this axial rotation. High-tech solution
These corners of the skyscraper’s facade will be edged with stainless steel made in Germany. ThyssenKrupp Nirosta (Krefeld) produced the material at its Dillenburg plant using a customised rolling and heat-treatment process. Partner company Christian Pohl GmbH (Cologne) fabricated this high-quality material into complex facade elements for the corners of the One World Trade Center – some 250 tons in total.
The 1 by 4 metre (40 by 160 inches) facade elements are being made from the corrosionresistant chromium-nickel-molybdenum stainless steel alloy Nirosta 4404 with a textured finish ‘LASER’ specially designed for this project. “Our material meets the extremely high requirements for uniform surface quality with no streaking or shadowing from any angle regardless of light conditions,” says Gert Weifl, head of product service at ThyssenKrupp Nirosta. And Heinrich Robert Pohl,

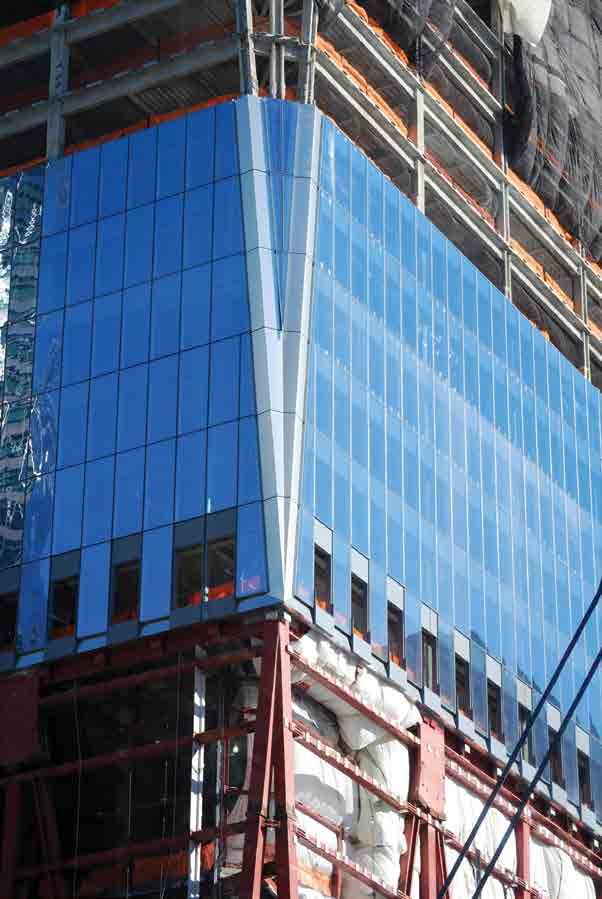
managing director of Christian Pohl GmbH, adds: “Such complex jobs call for supreme technical competencies and a wealth of manufacturing experience. With a high-tech solution we were able to win our extremely demanding customers over to this jointly developed, high-quality German product.”
With its rolled surface texture, LASER is ideal for facades which are intended to reflect light uniformly and diffusely. This design finish is in fact characterised by a complete lack of design – at least if design is understood to mean a uniform pattern. LASER has a completely random texture. Unlike regularly aligned surface patterns, which reflect light differently depending on the angle of incidence, LASER provides for diffuse reflection.
Like other design finishes from ThyssenKrupp Nirosta, LASER is produced by cold rolling the stainless steel using appropriately patterned rolls, permitting continuous, high-yield, cost-effective production. Previously high-pressure glass bead blasting was required on stainless steel to achieve the same effect as LASER.
LASER is the result of a joint project between ThyssenKrupp Nirosta and Wetzel Processing Group, a leading manufacturer of printing and embossing rolls. The two partners developed a method of transferring randomly textured surfaces to patterned rolls and from there to stainless steel strip. The challenge lay in the fact that completely random textures are far more difficult to produce on rolled surfaces than regular patterns. The conventional approach is to design lots of individual, irregularly shaped microfigures on a computer – a complex process – and then combine these tiny elements into larger areas which are then reproduced until the entire roll surface is covered. The design is transferred to the surface of the roll using a computer-controlled combination laser and etching process. The disadvantage of this method is what specialists call pattern repeat: Depending on what angle they are viewed from, and especially from further away, the patterns can be seen to recur – which is exactly the opposite of what is required.
In the new approach, the shapes making up the microelements are no longer random but right-angled. That makes it possible to digitise the elements and then, via a random generator, spread them randomly over the surface of the roll using a new direct laser technology developed by Wetzel. From the distance at which building facades are observed, it is not possible to see that the individual microfigures are no longer completely random.
“The quality of our product helped us to win the contract for this out-of-the-ordinary project. Ultimately we regard it as an accolade to be a part of this globally known project in the heart of New York which means so much to so many Americans,” emphasise ThyssenKrupp Nirosta and Christian Pohl GmbH. n