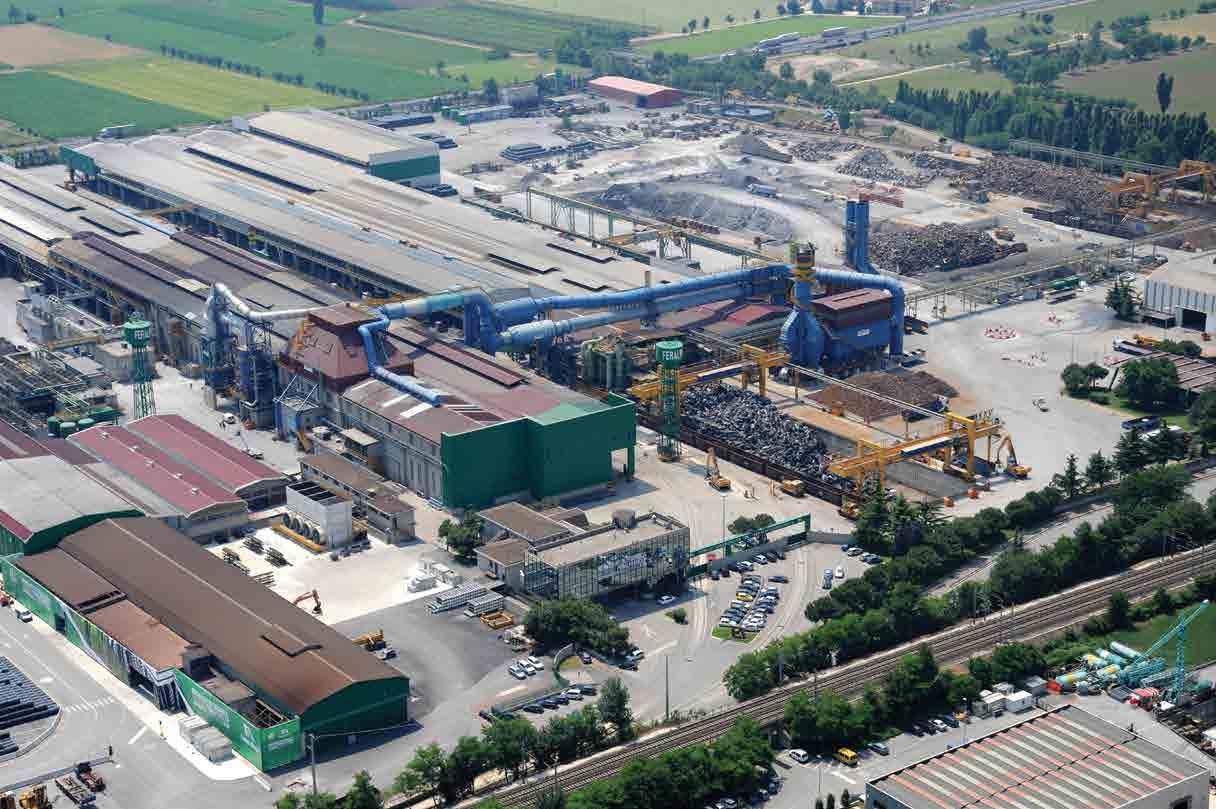
7 minute read
Sustainable growth The Feralpi Group
SUSTAINABLE GROWTH
The Feralpi Group is a major player in the Italian iron and steel industry. Isabella Manfredi, the company’s communications director, discusses its developments over the past few years, stressing the importance of factors such as production process optimisation, energy saving, emission reductions and product innovation. Barbara Rossi reports.
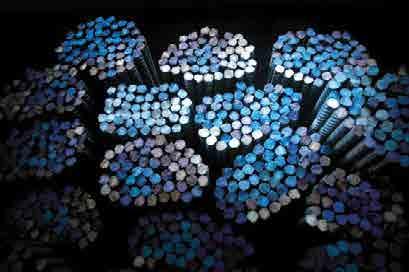
The growth achieved by the Feralpi Group over the past 10 years has developed along three paths: the first is in terms of size; the second is in terms of quality; and the third is linked to the everincreasing closeness between the iron and steel manufacturing activity and sustainable development standards.
Iron and steel manufacturing experienced a golden period between 2004 and the end of 2008. During those years the iron and steel industry changed radically, owing to aggregation and acquisition processes resulting in the creation of real giants. The Feralpi Group’s main production output consists of rebar, wire rod and electro-welded mesh. In addition to these it also manufactures cold roll reinforced steel, lattice girders and spacer bars.
Over the past few years it has grown a lot owing to its efforts to manufacture large volumes suitable for several markets. For this reason, over the years it has established plants in Germany such as ESF (Elbe-Stahlwerke Feralpi GmbH) and EDF (Elbe-Drahtwerke Feralpi GmbH), in the Czech Republic and in Romania where it has added to the already existing Lonato del Garda and Acciaierie di Calvisano facilities. In Italy the group also owns other companies such as Dieffe, which carries out cold processing, and Nuova Defim, which specialises in the manufacture of electrowelded mesh for construction, industrial fences and professional, industrial and civil railings.
Technological innovation and sustainability
Technological development and the maximisation of production efficiency are two musts for an iron and steel company – particularly in a country which doesn’t offer effective support to increase the competitiveness of its industrial players. For this reason, Feralpi has made large investments in technologies in order to optimise its production processes and to reduce raw material consumption to
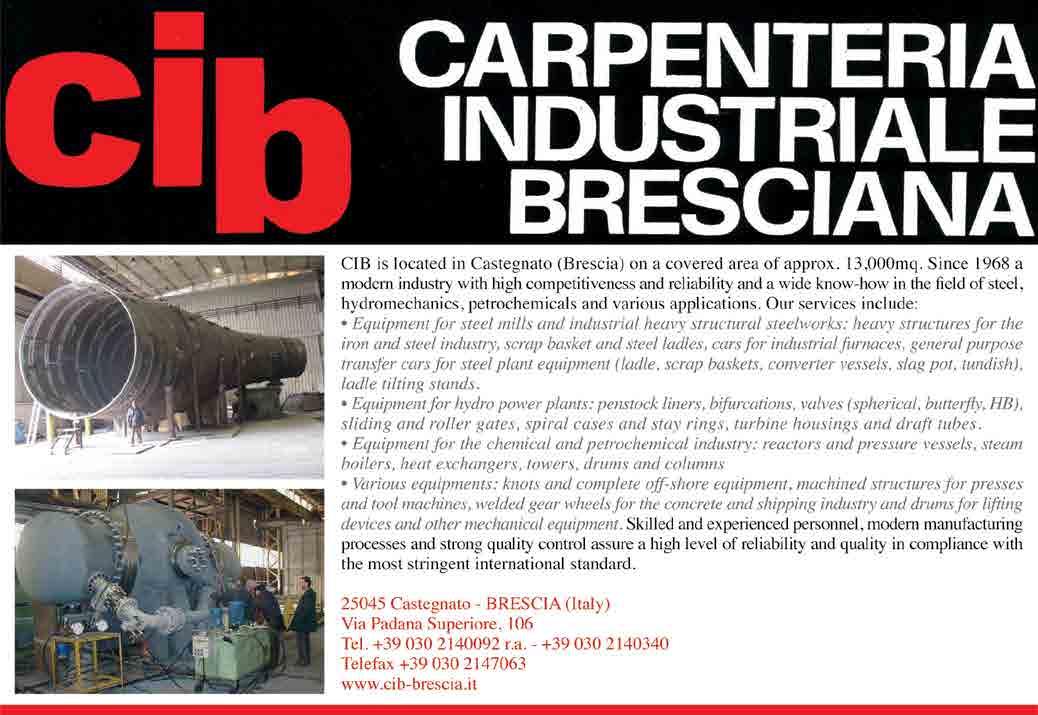


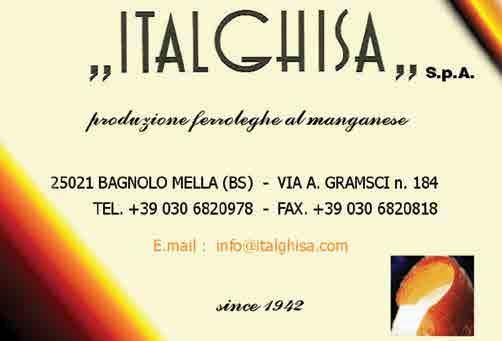
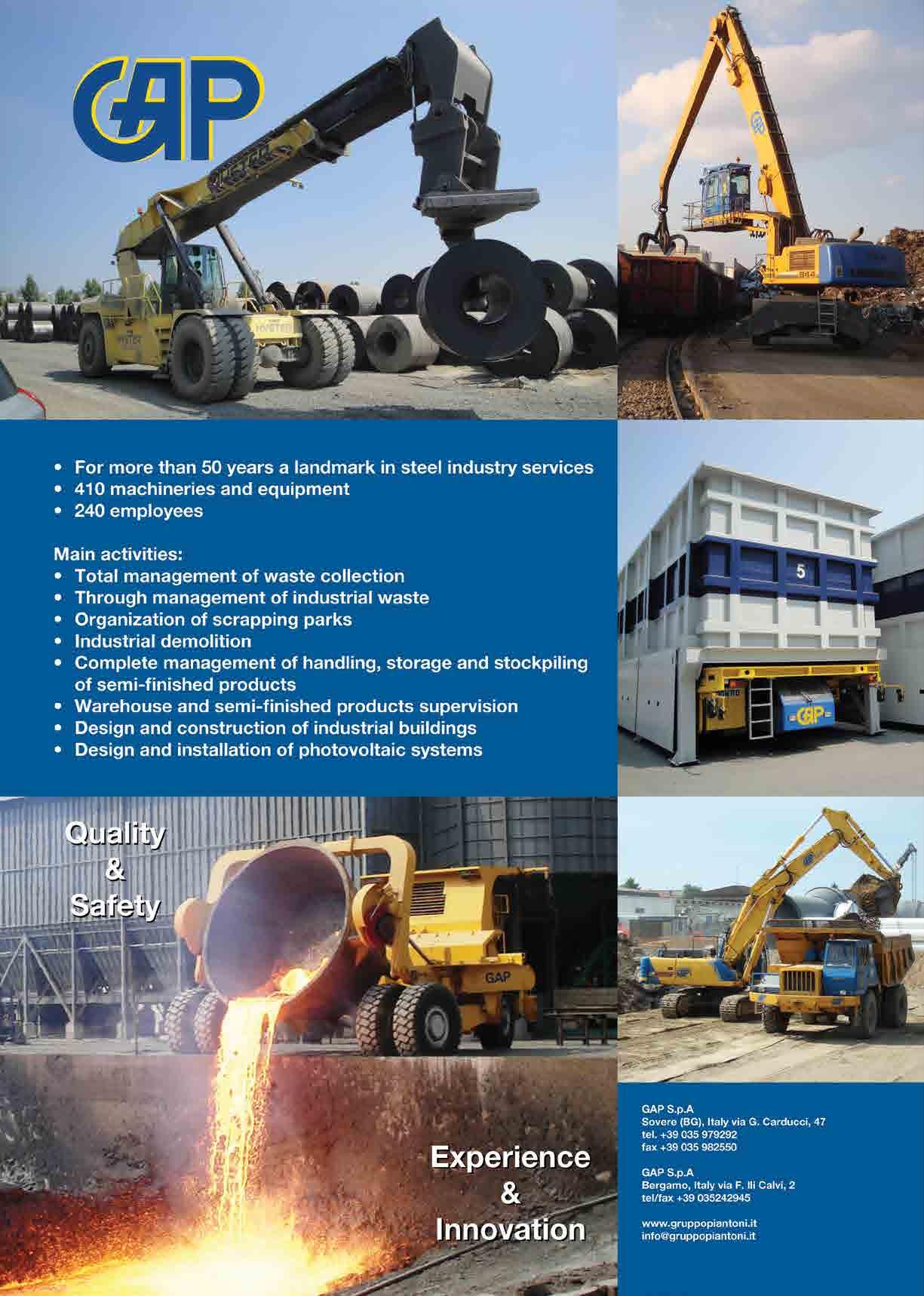
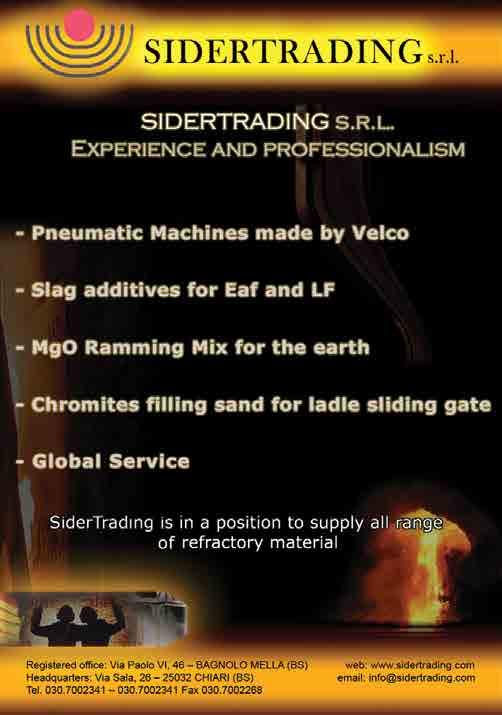
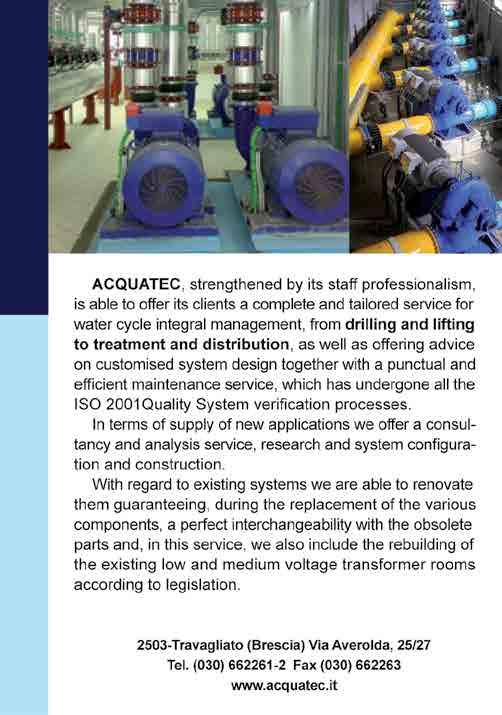
a minimum. Energy is one of the main costs for the company as so much is used in the production of iron and steel, which is why so much time and resources have been spent on this issue.
The Feralpi Group has been evaluating its environmental activities for years and periodically produces a sustainability balance sheet to measure its achievements in this area, as well as to help it map out a path for future advancements.
At the beginning of 2011 the group opened a new foundry furnace and photovoltaic system at the Lonato del Garda site, which will aid its mission to reduce production costs and improve process innovation. These facilities allow for energy savings and a reduction in greenhouse gas emissions.
The right skills
The iron and steel industry is increasingly reliant on highly skilled human resources and the current training available is not always suitable to the needs of the Feralpi group. It has tried to rectify this problem by setting up a professional apprenticeship programme to bring together school and working environments and to solve turnover issues within its departments. This project has been realised thanks to the active contribution of various business partners, creating three two-year courses in which several high school graduates with a technical/industrial specialisation have participated. Encouraging results have been achieved, demonstrating that the iron and steel sector is still appealing to new generations as long as it affords them the opportunity to grow and develop.
Feralpi is also involved in the Comenius Regio project, which connects two different EU regions for two years and allows them to take part in a common project with the aim of achieving objectives which are usable within the EU – such as comparative studies, and training courses for teachers and for apprentices. The objectives also
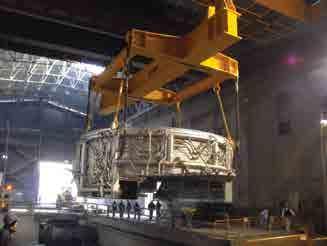
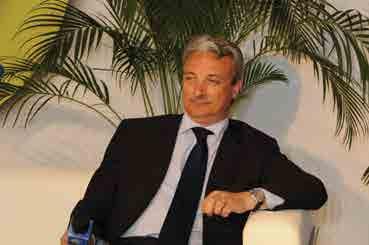

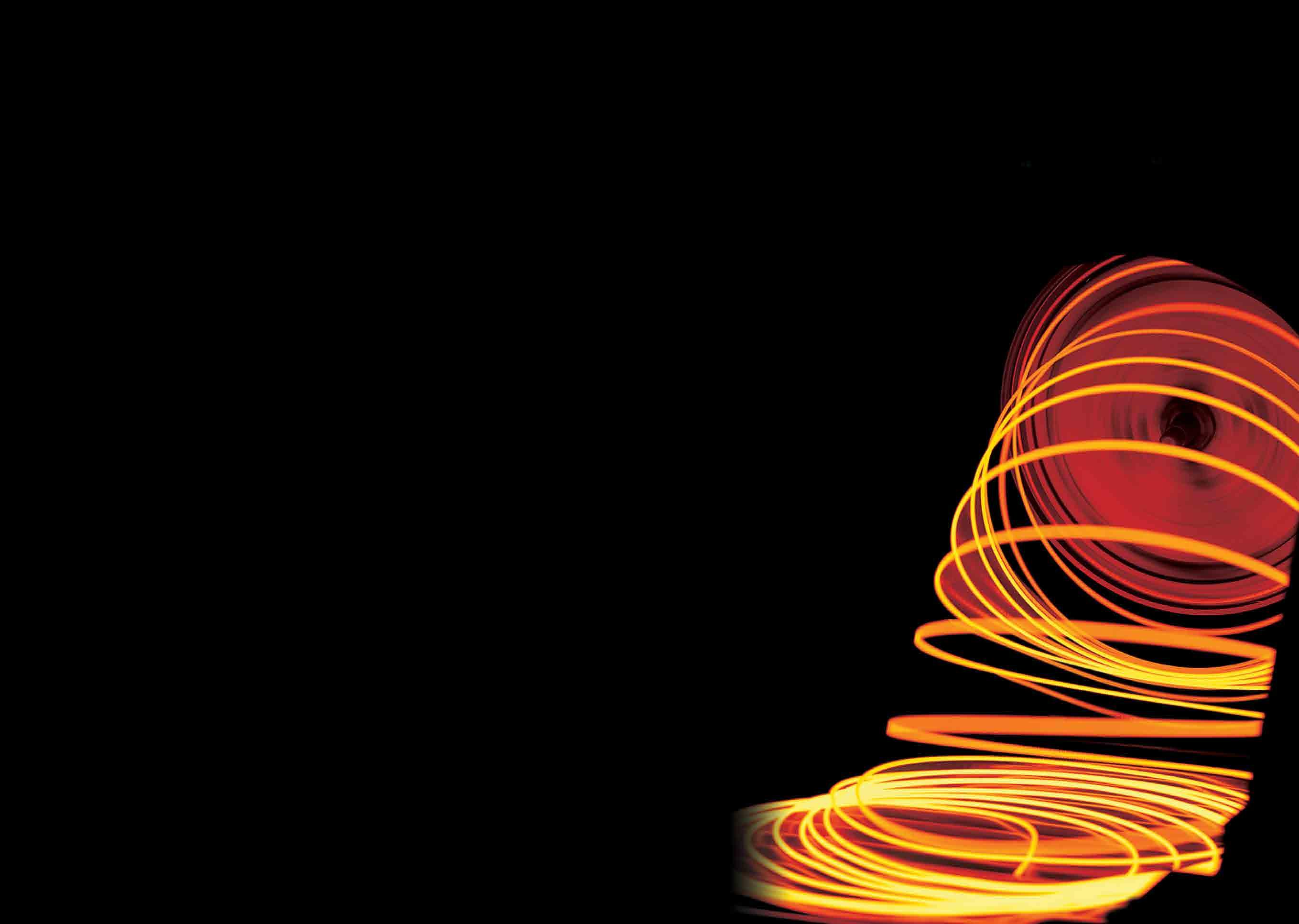
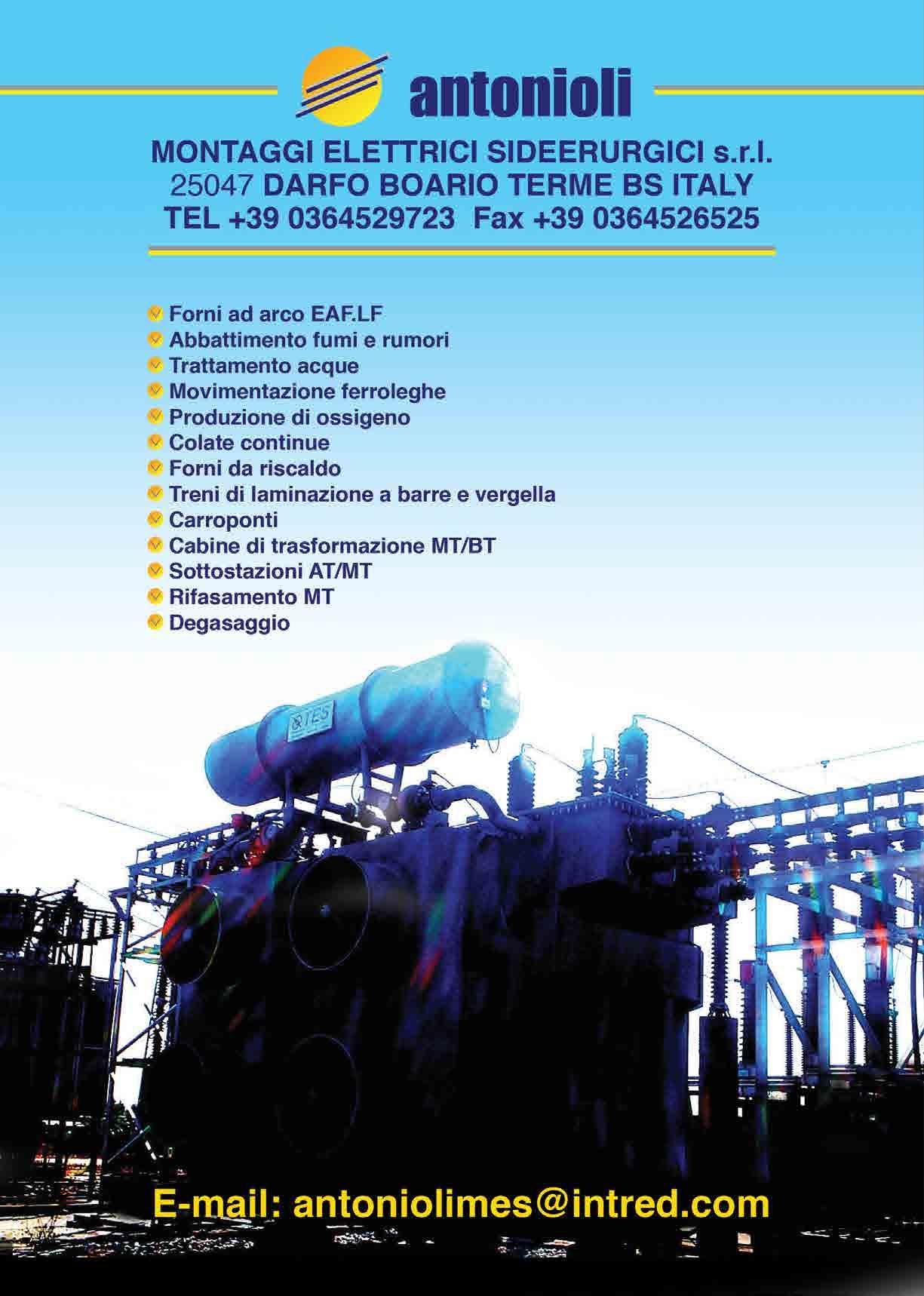
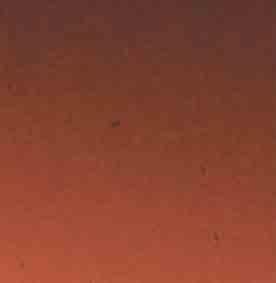
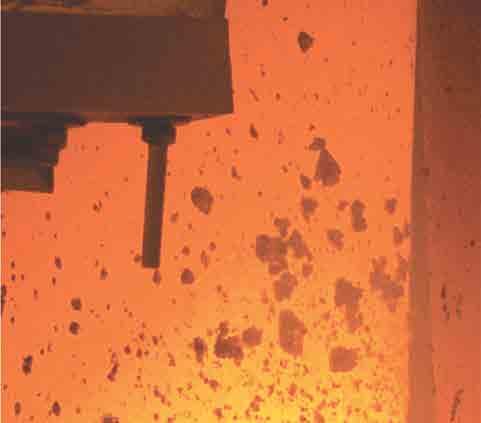

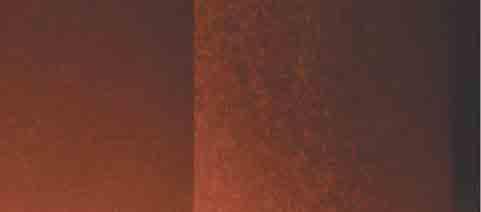
SanGregorio, a Private Shareholder Company located 40km north-west of Milan, was established in 1963 on the site of an old foundry which had been producing mainly devices for the textile industry as crane wheels. It subsequently set up a new line for the production of cast iron rolls for hot rolling mills, serving only the domestic market.
In the 1970s a new and larger workshop was built and new machine tools were set up to speed up roll machining. During the latter part of this decade the old casting line for textile tools and crane wheels was dismantled and all production became focused on cast iron rolls with the intention of conquering foreign markets, beginning with Spain.
Today more than 75% of SanGregorio’s products are exported, reaching most of the European countries, the Americas, some African countries such as Egypt, Morocco, Cameroon and the Ivory
Coast; Middle Eastern countries such as Lebanon, Jordan and Palestine; Far Eastern countries such as Taiwan, Thailand, Malaysia, Philippines, Indonesia and India. A wide network of customer service agents was also built to address customers’ needs.
SanGregorio’s production is certified according to the highest standards. It achieved the ISO 9001:2008 Quality System Certifi cation, and the ISO 14001:2004 Environmental Management System Certifi cation.
SanGregorio’s production covers an area of 18,000m2 over three buildings: Foundry, Workshop and Administration. The Foundry is equipped with a 35t medium frequency induction melting furnace and ladles able to cast a 27t one-piece roll. The Workshop is equipped with CNC horizontal & vertical turning lathes, CNC milling and grinding machines, capable of producing roll diameters up to 1500mm and rolls barrels up to 5000mm. Finally, the Administration facilities are entirely computerised and a website supports customers’ needs.
SanGregorio specialises particularly in the production of nodular/ductile cast iron rolls for the rolling of long products such as rails, beams and merchant bars. Also, following the development of Universal Stands for the rolling of rails and heavy beams, SanGregorio also specialises in the shrinking and disassembly of large sleeves onto and from steel shafts.
SanGregorio’s organisation is based upon maintaining close contacts between Customers and Company management to satisfy technical or other questions they may have. A fast-response philosophy is essential to maintain a high level of customer care!
Fonderia Officina Meccanica CILINDRI PER LAMINAZIONE I - 21010 S. Macario di Samarate (VA) Italy Viala Europa, 62 Tel: +39.0331.235353 | Fax: +39.0331.235328 Email: infocentre@sangregorio.com | www.sangregorio.com
ISO 9001:2008
ISO 14001
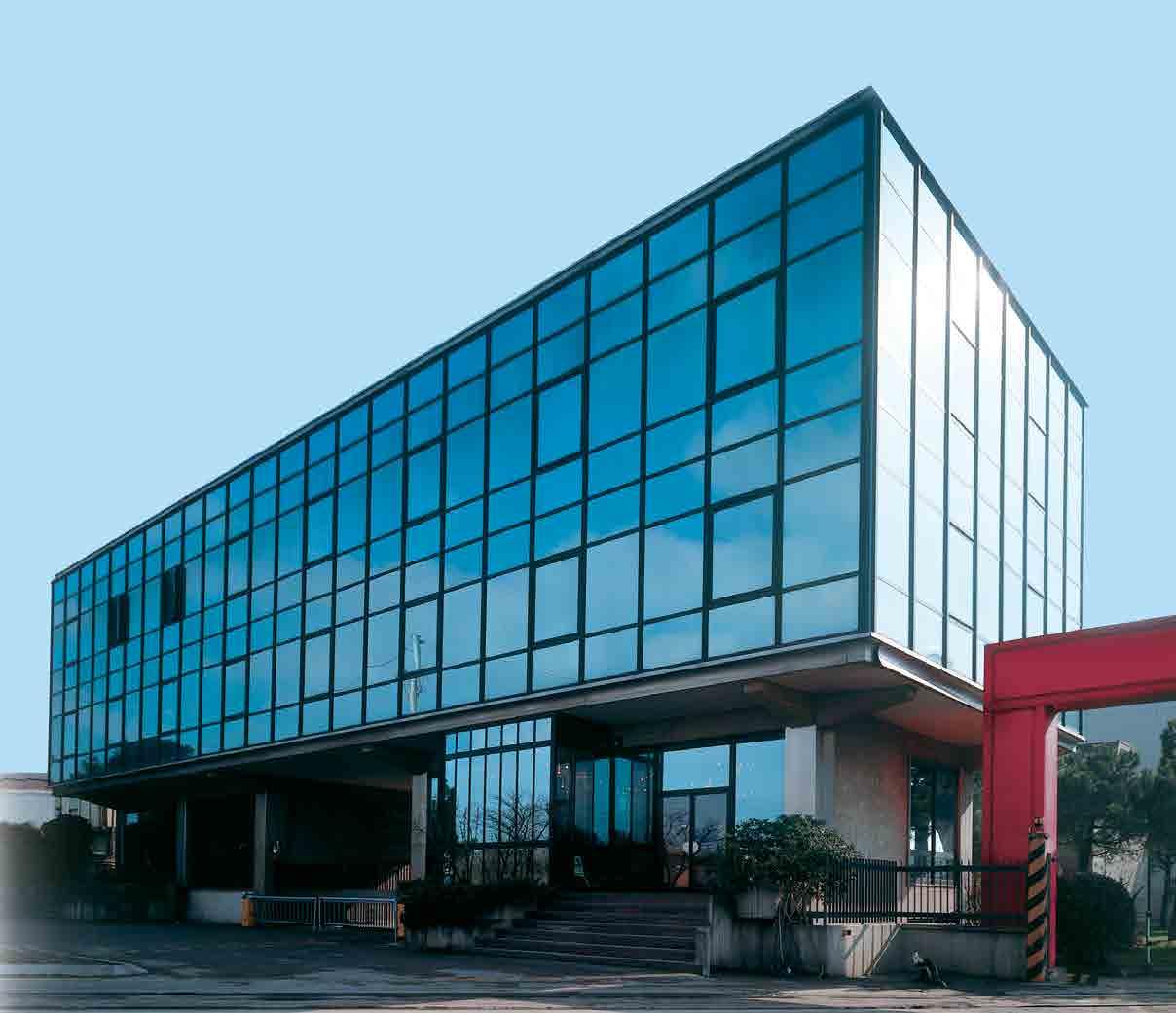
include the distribution of the results of the study and the creation of a bilingual (Italian–German) iron and steel industry glossary. In this instance the two regions involved are Lombardy, Italy, and Saxony, Germany, where the Feralpi Group is currently present. Through the Comenius Regio project the partners wish to complete a comparative study and offer a training path which will lead to European-level qualifications, respectively carried out by the Riesa-based Elbe Stahlwerke Feralpi and the Lonatobased Feralpi Siderurgica.
For many years Feralpi has been active in CSR (corporate social responsibility) in social, environmental and economic terms. These three aspects are certainly different in terms of approach and method, but they meld into a single policy which is integrated in each of the group companies.
Raw material supply
In terms of the iron and steel sector as a whole, one of the key factors to affect competitiveness is the availability of raw materials. In this context raw materials can mean a variety of elements, ranging from minerals to scrap, including human resources and energy.
For Feralpi, the challenge is that Italy is a country which is basically lacking in raw materials, and the steel industry pays a high price for this lack of energy, minerals and scrap iron. The price-increasing tendencies of the latter are an issue affecting the whole world, owing to the fact that this sector operates as an oligopoly composed of three mining companies which manage it at a global level, while the energy problem is specific to Italy owing to its lack of energy policies which has seen bills skyrocketing. The lack of infrastructural projects to push the economy often means that Italian companies find themselves alone in facing the challenge of recuperating competitive margins in the face of rising energy bills and lack of raw materials. n