
5 minute read
A local force Dirostahl

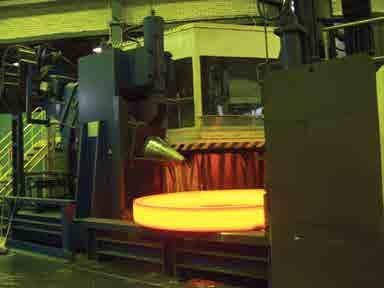
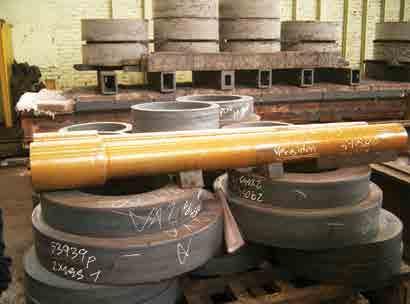
A LOCAL FORCE
Forged steel of the highest quality is called for when machines have to withstand exceptionally strong forces, and Dirostahl’s product quality satisfies the most demanding requirements in mechanical engineering. Julia Snow reports on the ongoing programme of investments.
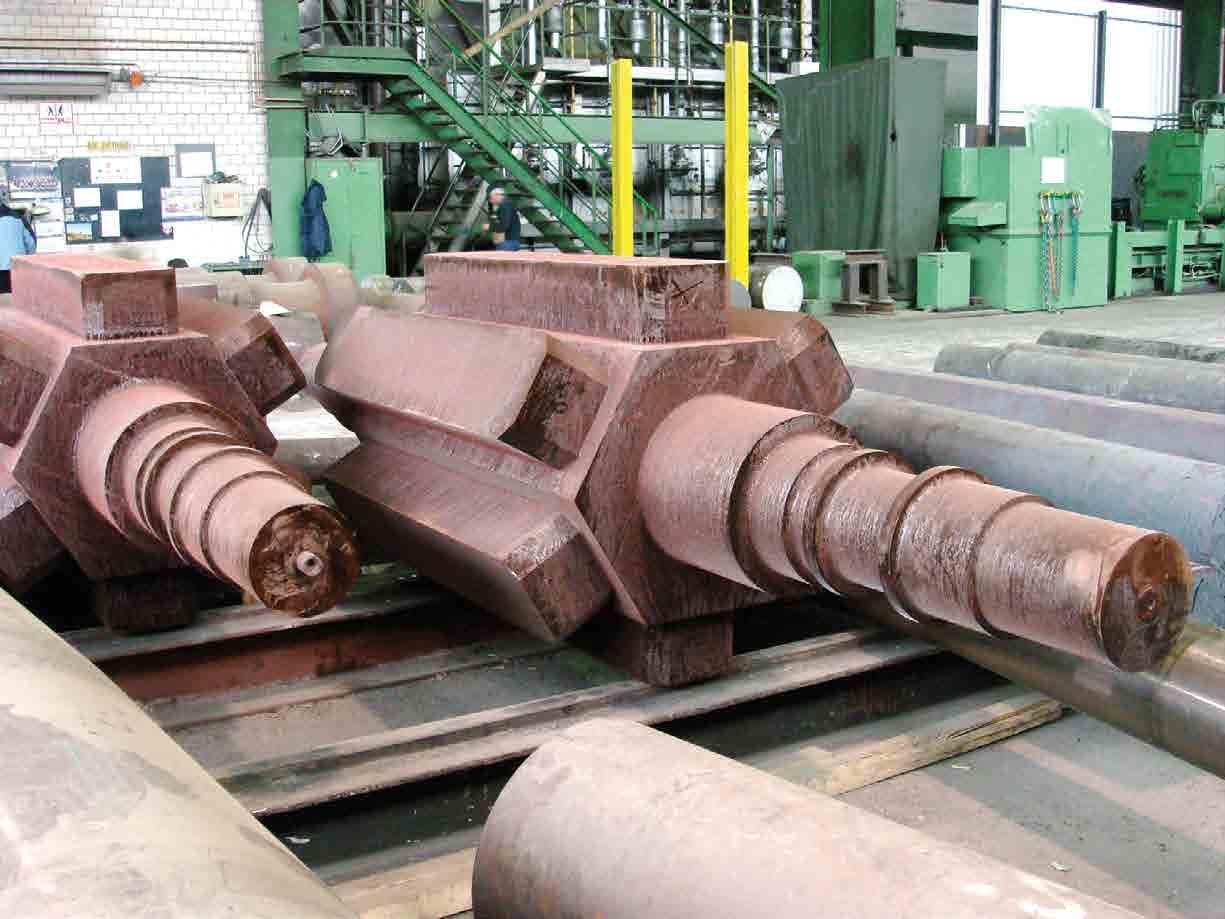

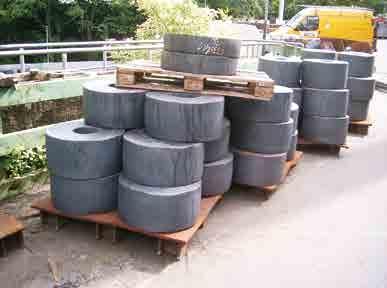
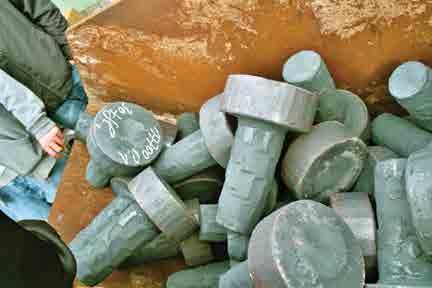
With over 400 years of tradition, and located in the heart of Europe in Germany’s Bergisches Land, Dirostahl has made a name for itself as a provider of first-class steel bars and other types of forgings for the entire machine tool industry, for the fabrication of gears, of heavy tools, synthetic, textile and paper machines, power plants and shipbuilding as well as the off-shore industry.
The company employs 480 staff, and has strong roots in the local community. Whether it’s a visit from a local politician, the use of the works as a set for a TV production or one of the many seasonal and social activities the company arranges for its apprentices, employees and retired staff members Dirostahl is proactively involved in supporting social aims and furthering the well-being of local people and strengthening the local economy.
The production facilities include open-die steam hammers and presses, rolling mills, heat treatment and machining. The product range stretches from open-die forgings from 10kg up to 35,000kg, seamless rolled rings up to 3500mm OD, forged bars up to 850mm OD/ square and up to 15 m in length in alloyed and unalloyed steel grades. In order to guarantee the highest quality of raw steel, Dirostahl works with select suppliers and purchases are made in accordance with the company’s analysis specifications. To guarantee availability and allow cost management, around 20,000t of an assorted range of raw steel is held at any time. The company has domestic and international representatives, and highly qualified engineers and technicians can provide technical and metallurgical support from the company’s base in Remscheid. Material inspections are offered at laboratory facilities and forging inspections can be carried out by destructive and nondestructive tests.
Automated logistics centre in operation
Owing to a steady expansion of the facilities, the production area has nearly doubled from 40,000m2 to 78,000m2 in the last three years. Today Dirostahl’s activities are spread across three main works and a brand new state-ofthe-art logistics centre.
In December 2009 a new 3000t press took up production after only three weeks of construction time, and the same year saw the installation of a new gantry crane to make the handling of raw steel blocks easier and safer. The highlight of 2009, however, was the opening of the new high rack storage facility. With dimensions of 50m by 17m and
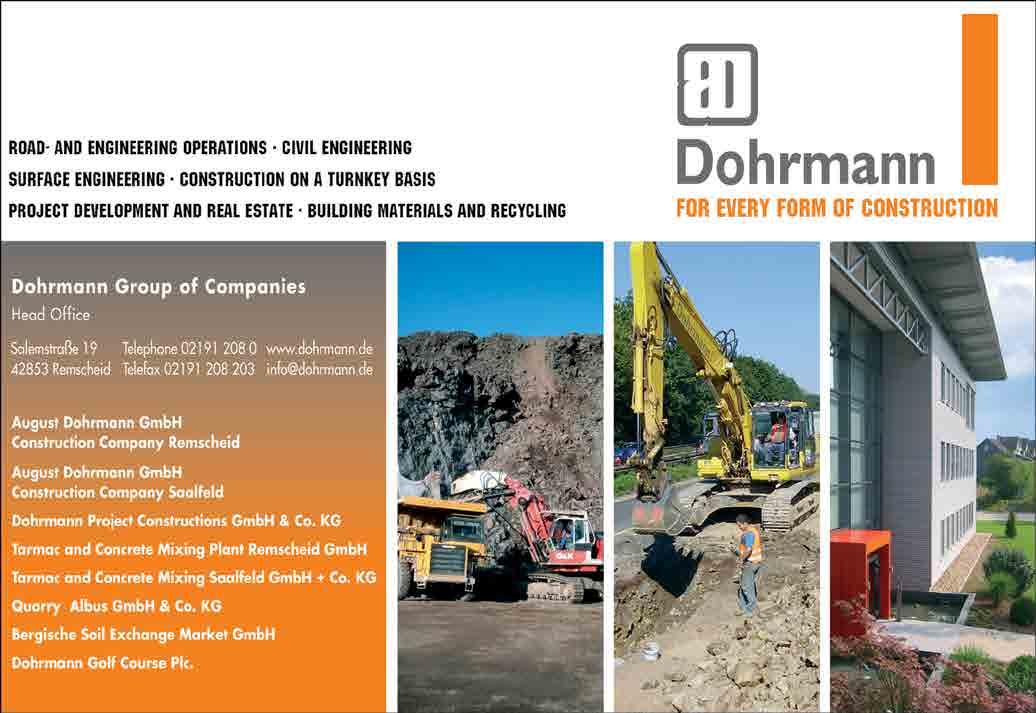
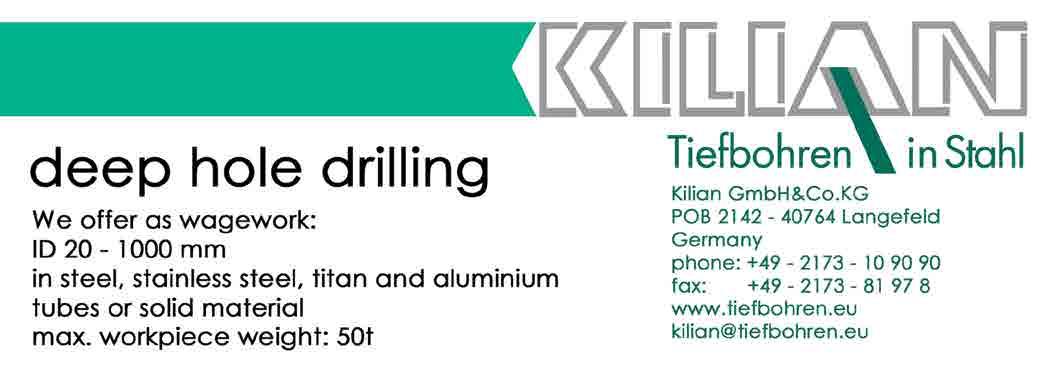
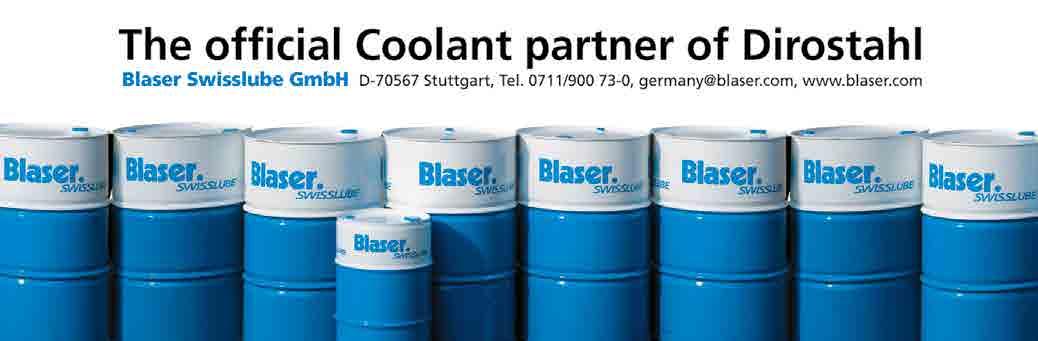
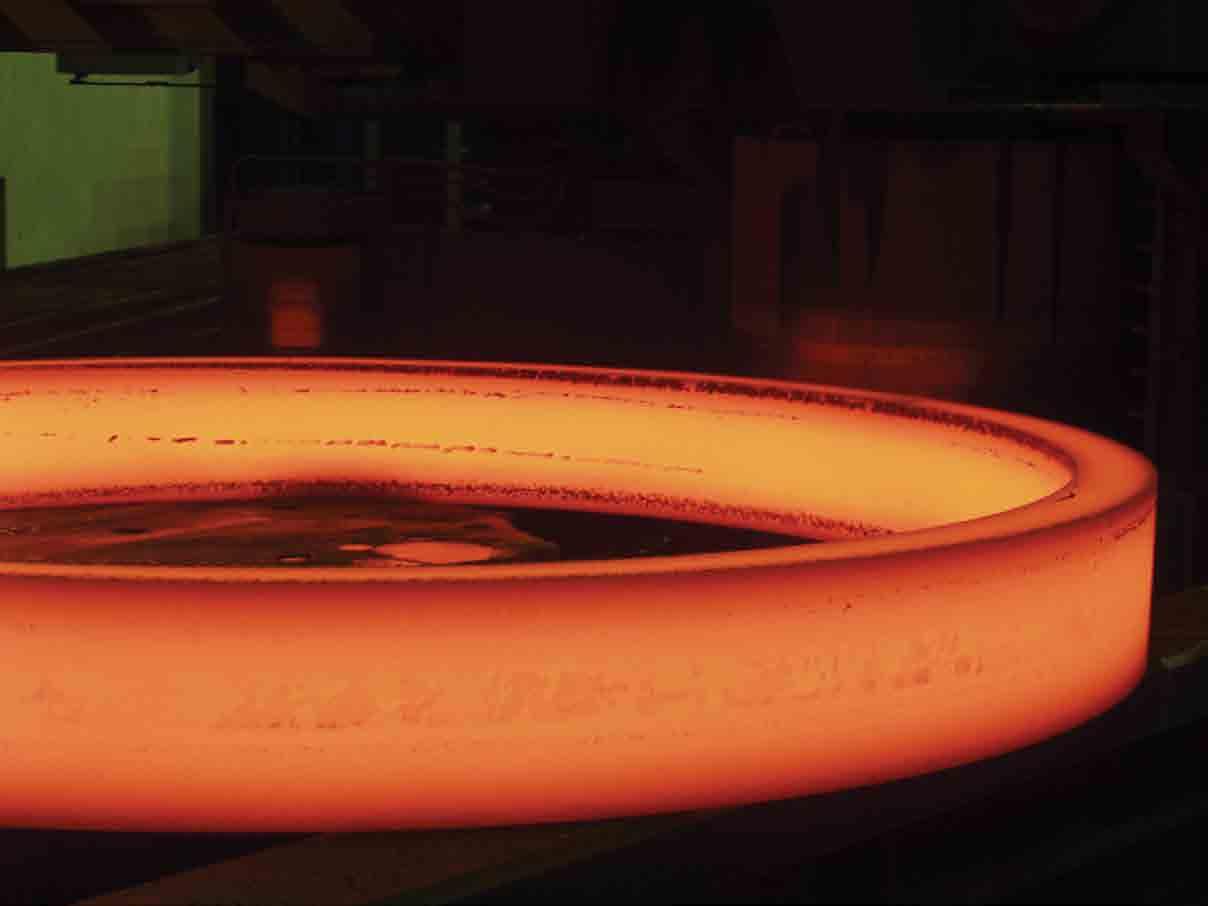
a height of 21m, the new building offers space for 2860 pallets with up to 2000kg load per pallet. Inside there are six rows of shelves with 14 – 22 floors each, depending on the shelf dimensions, and all filling and picking of pallets is handled by three fully automated shelf-rack servicing units. In the adjacent 500m2 quality control and packaging hall the forged parts can be US-, HB- and VP-tested, and a measuring protocol will be issued for each item that is then loaded onto pallets and secured safely for transport. Outside of the testing hall there is a covered area of ca. 500m2, where pallets are loaded onto lorries. The storage system places the pallets onto six loading bays, where individual displays show the order numbers of the assignments stored in each bay. Dirostahl has its own fleet of articulated lorries that take care of around a third of all deliveries, while with a range of other logistics channels, delivery reliability and flexibility are ensured all over Europe New turning shop
Last year a rotary hearth furnace was installed for the new piercing press of the ring rolling mill, and more recently Dirostahl started using a new cold circular saw (KKS 1250), as a block saw for pre-materials. The teeth of this circular saw blade are fitted with carbide, which permits a higher cutting performance compared with belt saws, halving the sawing time. The machine is equipped with an automatic stock feed unit, which allows high precision, and employs a ‘minimum quantity lubrication’ technology that reduces cooling lubricant consumption.
The biggest investment project, however, is the construction of a third turning shop, adjacent to the Luckhausen workshop II, which was started in 2008. The new facility means that heavy forged pieces don’t have to be transported across the motorway anymore, bringing a huge improvement in workflow. The new hall is now home to a range of machines, including a modernised and refurbished ‘Russenbank’, Dirostahl’s largest turning machine, a high-end portal milling machine, centre lathes and the new Tacci heavy duty lathe. The Tacci has already been used to work on a shaft weighing 21,500kg – commissioned by a Serbian customer for open-cast mining.
Into the future with optimism
During the festivities on the occasion of his 70th birthday in December last year Managing Director Dr Diederichs confirmed the positive outlook for the future of the company. He reported a rise in orders from the previous year and stated that he was optimistic for the year 2011. And certainly, the sheer volume of continuing investments – both in the company’s people and its facilities – gives a very good indication about how well-founded his optimism is. n
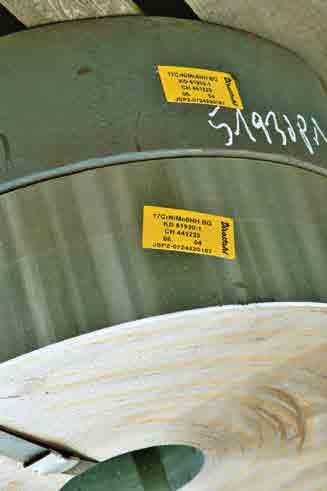
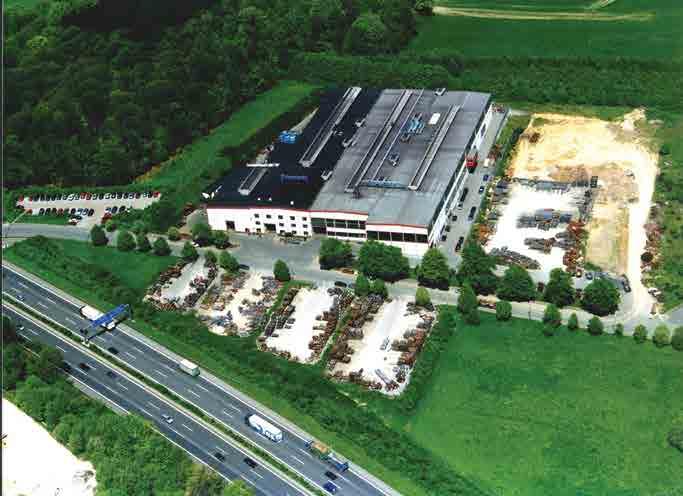