
4 minute read
Opening up a better future SIBO
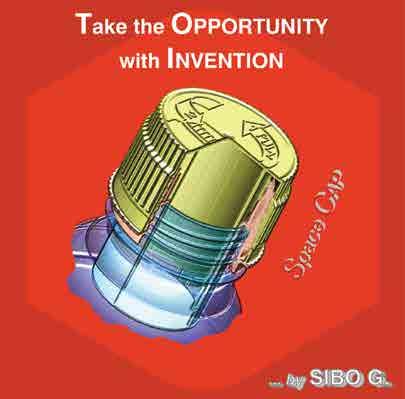
OPENING UP A BETTER FUTURE
The Slovenia-based company SIBO specialises in injection moulding for technical plastics as well as caps and closures. It serves a wide range of industry sectors, including pharmaceuticals, cosmetics, food, household products and many more. Industry Europe looks at its history of success in the market, current capacity, its latest products and plans for growth.
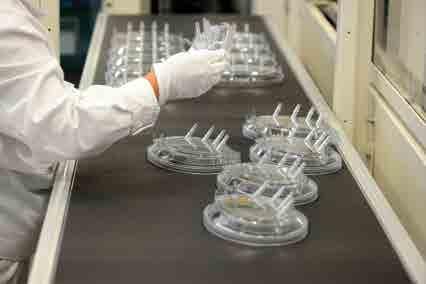
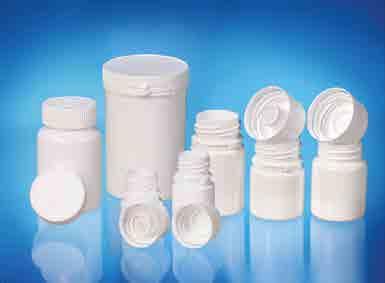
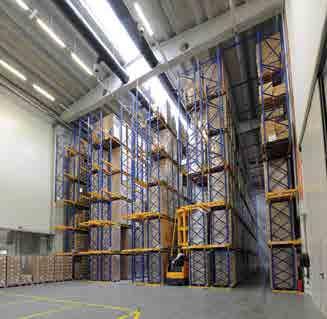
SIBO was founded in 1967 by Franc Sifrar and initially only produced plastic closures for the cosmetics industry. In 1993 the company was taken over by his son Boštjan Šifrar and moved to a larger factory and expanded its activities to include tool manufacturing. Over the years it branched out into food, household products, automotive and finally injection blow moulding technology for the pharmaceutical sector.
Today the company has two manufacturing facilities, both based in Slovenia, with four production halls covering an area of 16,700m2 . All production is based upon GMP (Good Manufacturing Practice) principles. In total, the company owns 90 different machines for injection moulding and processing. It also has Class 8 clean room, which is equipped with seven fully-electric machines with clamping forces ranging between 50 and 380 tonnes, and linear robots. All its production is certified according to the ISO 9001 quality standard.
An investment of €20 million was made in 2008 into the establishment of hi-tech and modern technology. A representative from SIBO explained: “Gaining new business and signing contracts with new customers has allowed us to invest further in machines, technology and people. On average we invest around €1 million per year in these areas.”
SIBO is a truly worldwide player. Its products are currently sold in 43 countries and it has more than 130 long-term customers. In all, around 90 per cent of its production is destined for export markets.
SIBO company structure
The SIBO Group is organised into six divisions: Tool Shop, Pharmacy, Medicine, Technical Parts, Assembling and R&D. The Tool Shop is where the construction and manufacturing of tools for the injection-moulding of polymer materials takes place. It uses the latest CAD/ CAM computer technology (Catia, SolidWorks etc.) and state-of-the-art CNC processing

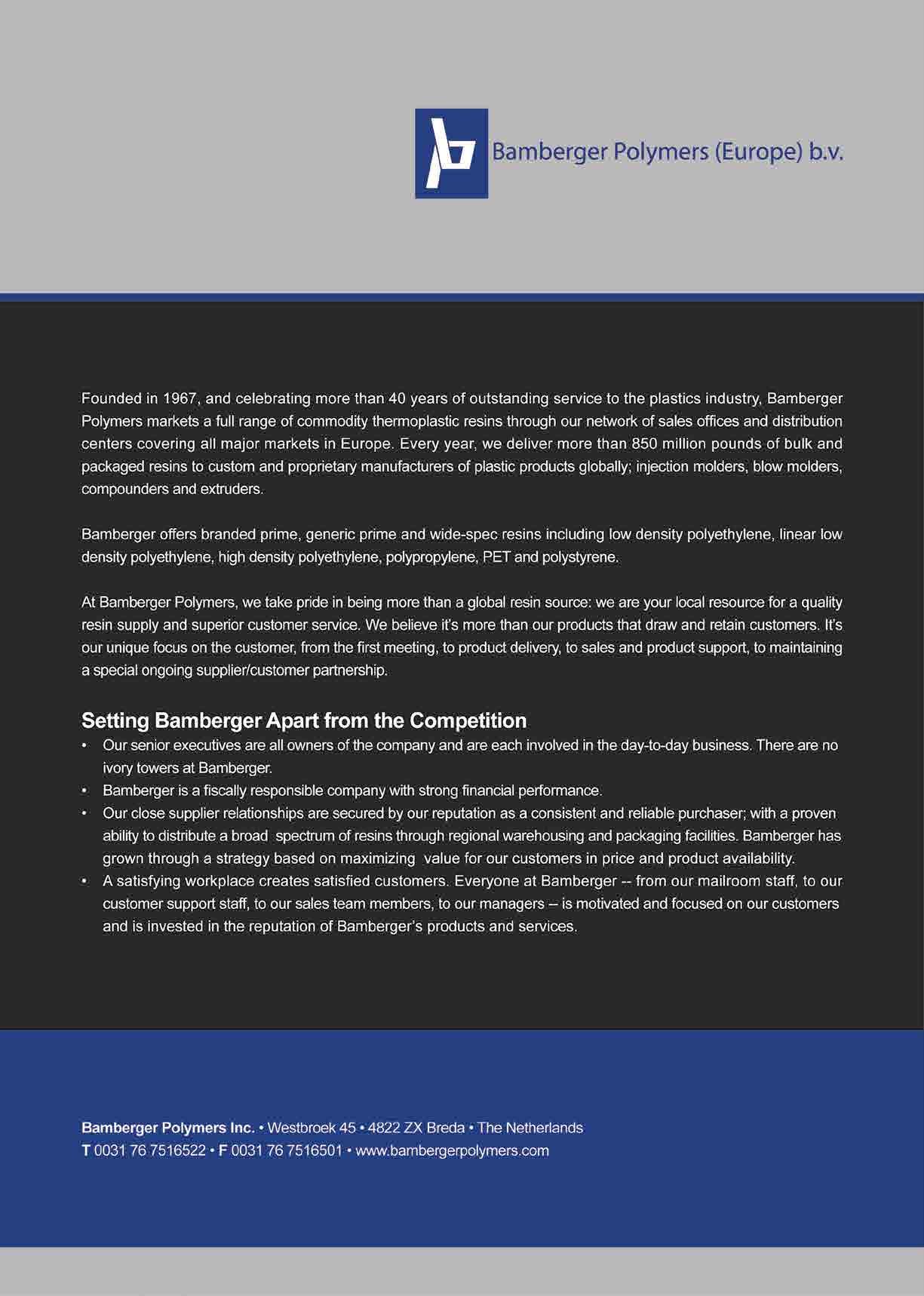
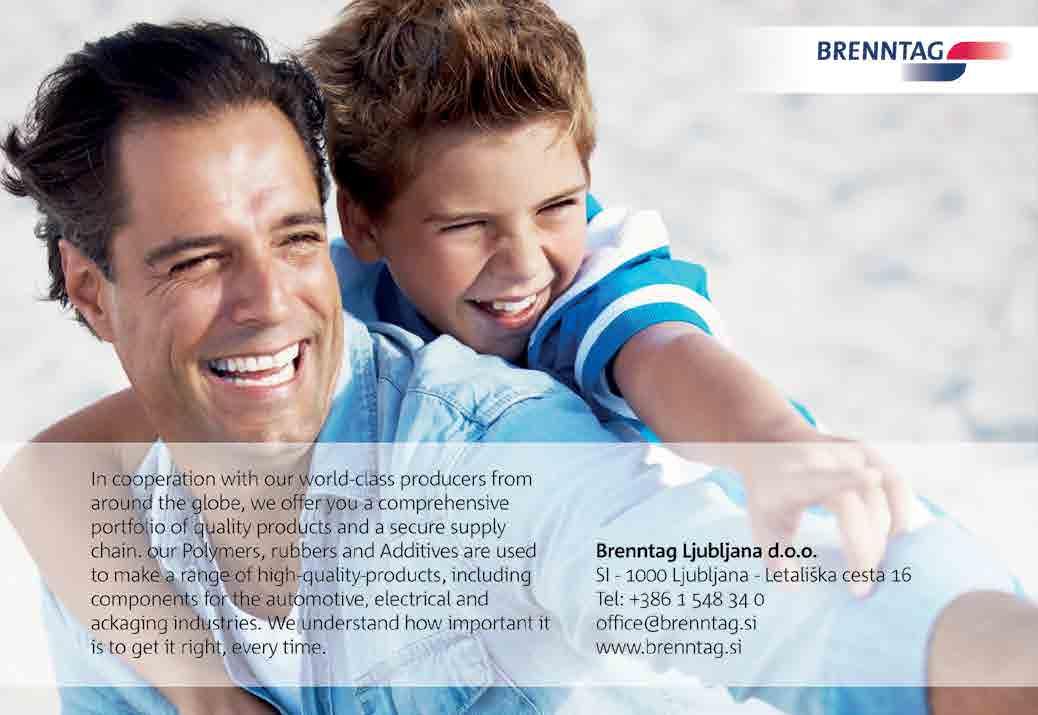
machines. Here, SIBO can create a 3D model of a tool, construct it and then carry out a review and make adjustments if necessary.
The group’s injection moulding activities also cover more than 200 varieties of caps and closures, for areas such as household products, pharmaceuticals, food etc. Production for its Pharmacy and Medicine divisions takes place in a clean room environment which has been certified according to the ISO 14644 Class 8 standard. Its Pharmacy products include closures for aluminium tubes, laminate tubes and plastic tubes.
New product development
SIBO’s R&D department focuses on packaging development for the needs of the personal care industry (such as caps and shoulders for toothpaste), the food industry (such as caps for mayonnaise), the cosmetic industry (including various flip-top caps) and the pharmaceutical industry. The latest innovation to come from this was the ‘container cap’ – a unique solution for the caps of bottled water. It can hold substances like powder supplements or pills, keeping them fresh until their release into the water.

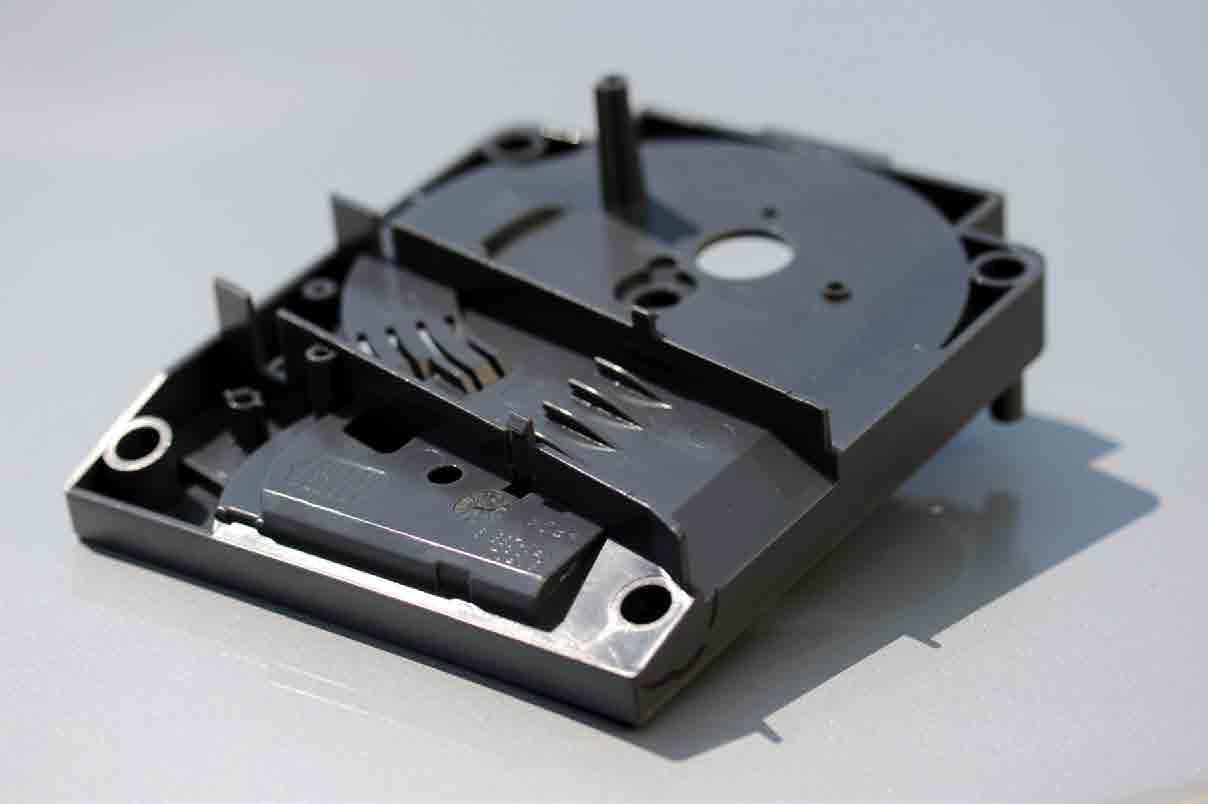
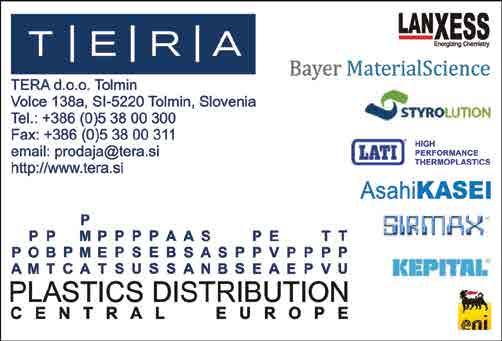
The company feels it offers a number of competitive advantages when it comes to product development. It is able to offer complete solutions with a combination of mould design, tool production and thermoplastic production. It is able to adapt to individual customer needs and is always open to exploring new ideas or technologies. All of this, plus state-of-the-art equipment and its reputation for quality and reliability, make it the ideal partner.
Plans for growth
A representative from the company discusses the ways in which it intends to move forward: “There are plans to move closer to our customers in the future or to buy some of our smaller competitors in some of the markets where our customers are present. We would like to establish the same hi-tech production facility and offer excellent service and further benefits to our customers.” SIBO is particularly focused on developing its pharmacy business and stepping up its activities in the Middle East and Asia.
In addition to acquisitions, growth will also be of an organic nature. “In the past 10 years the average SIBO growth in terms of turnover was 20 per cent and in the past five years it was around 30 per cent. We would like to continue this trend of expansion in the next five to 10 years.” n

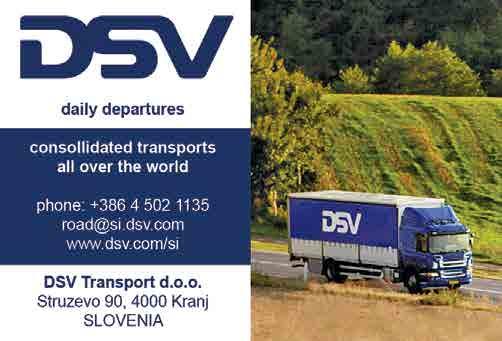