
4 minute read
An ideal partner for cast iron and bronze

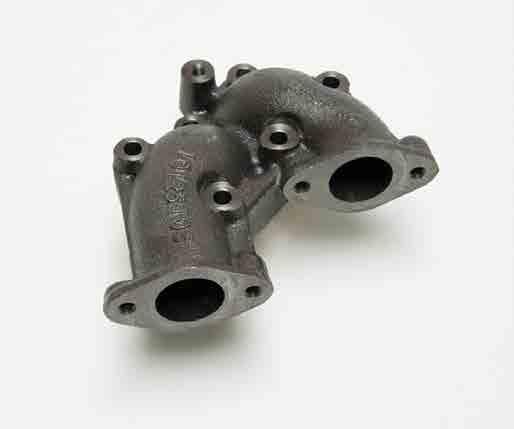
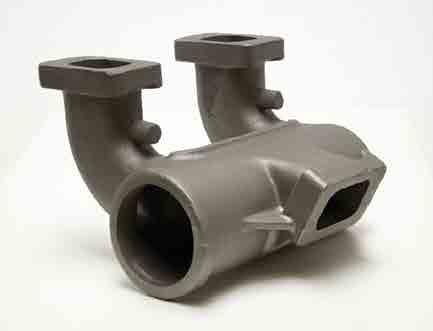

Omco (Overmeyer Mould Corporation) Metals, located in Hamme in Belgium, offers its customers maximum flexibility and delivers a wide-ranging offer of cast iron and bronze metals. Piotr Sadowski reports.
Back in 1964, Omco, as a leading producer of glass moulds in the USA, founded a division in Aalter in Belgium, in order to improve the company’s market position in Europe. The glass moulds were made from specially alloyed cast iron and bronze. Omco did not, at that time, own a foundry, so the rough castings were made by third parties. However, in the early 1970s the need for castings became so high that it was decided to establish its own foundry. In 1971 the foundry belonging to the company Bekaert in Hamme, only nine months old at the time, became available for sale and was immediately bought. Since then castings for both the glass industry and general engineering have been produced there.
In 1984 Omco found itself in financial difficulties and decided to sell off its European division, Omco NV. This was done by a management buy-out, carried out by the Regional Investment of Flanders, together with the Seyntex Group. From then on Omco NV became a Belgian company. In 1990, after 19 years of the foundry’s operations, the facility proved to be technologically out-of-date and therefore a brand new foundry was introduced. A year later Omco NV merged with BMT NV and became a publicly traded company. In 2000 a second foundry was acquired, in Slovenia, and from then on the glass moulds for the division in Croatia and Austria have been produced there, while the foundry in Hamme has been increasingly focused on customers outside of the group.
Activities today
Luc Willems, the Hamme foundry manager, explains that while 10 years ago Omco Metals was operating as a local foundry, with around 60–80 per cent of products distributed locally
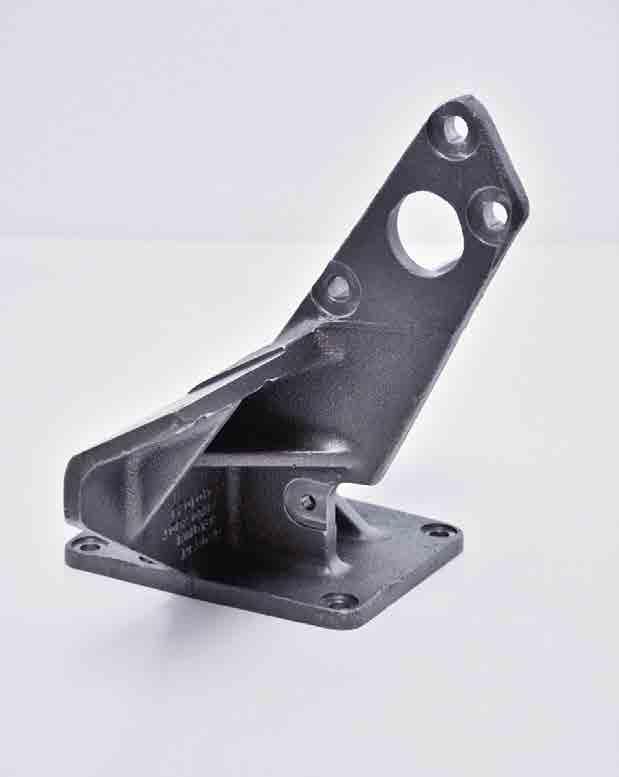
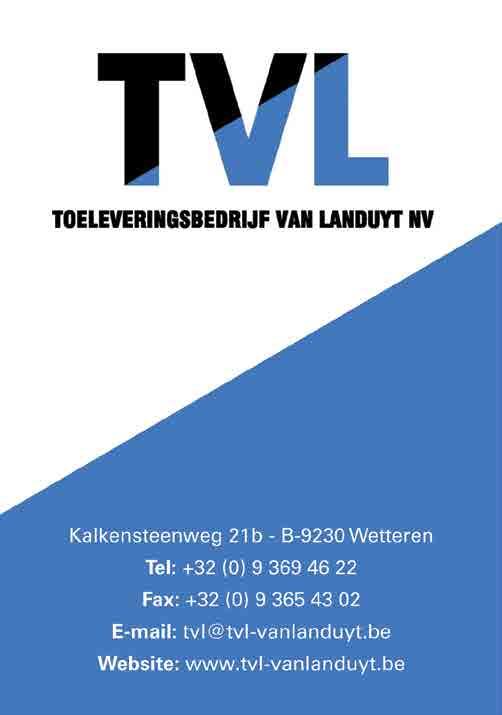
to Belgium and southern Netherlands, today the company’s spread is much wider. “Today only around 20 per cent of products are sold in Belgium; the rest goes to export markets which include Italy, Spain, Germany and Switzerland,” says Mr Willems. “Despite the economic downturn we have also been able to secure increases in turnover of around 20–30 per cent a year. This year’s turnover will be in the region of €24 million while five years ago it was approximately €14–16 million.”
The company expands not through securing more volumes of products, but through focusing on even better serving its market segment, which includes shorter, low and ultra-low series more complicated castings and alloys. “The turnover increases not as a result of more kilograms of metals produced, but from the added-value of our products,” adds Mr Willems. “We focus on Europe, glass moulds, metals-based products for the automotive sector, but also deliver specific alloys and castings tailored to direct needs of customers in other areas, including agricultural machines, earthwork machinery, pumps, incinerators and general engineering. We look to the markets to identify new trends and expectations, and respond with excellent solutions. We are a small foundry, but we do our job very well.” Technology, offer and quality
The foundry in Hamme has three induction furnaces for iron (1800 kg/furnace), an induction furnace for bronze (500 kg/furnace) and an automated core making for cores up to 30kg, as well as an automated horizontal moulding line for box size 650 x 650 x 500 mm (with a capacity of 60 moulds per hour). The facility is also equipped with two grinding robots for automated grinding, its own pattern shop with CAD/CAM capabilities and five furnaces for heat treatment.
The offer includes pieces with weights 0.1–100kg, prototypes and small- and medium-sized repetitive series (from tens to hundreds per order line). The company offers all types of cast iron: lamellar iron, ductile iron, low alloyed cast iron, vermicular iron, stainless iron (Ni-Resist), wear-resisting iron (Ni-hard), heat-resisting iron (SiMo and high Cr), bainitic iron and ADI. “We also deliver core-intensive pieces with complex geometry,” adds Mr Willems. “The foundry also offers aluminium bronze, as well as machining, painting, galvanising, pressure testing and other services associated with our activities.”
The quality at Omco Metals is assured by an ISO-TS standard certified by Lloyds. A range of other specialist provisions guarantee that the highest quality is achieved. They include CAD design of castings, digital transfer and manipulation of customer drawings (in any format), simulation software for mould-filling and solidification, spectrometric analysis, digital measuring equipment and microscopic examination. The company is able to perform all necessary mechanical tests and provide the relevant certificates.
Planning for the future
Although Omco Metals has not recently carried out any major investments, nevertheless a lot of effort has been put into identifying areas where investment is needed in order to further strengthen the company’s operations. “These include HR as well as a very important investment in a brand new IT system,” says Mr Willems. “We have opted for the Glovia solution and will be implementing it from January 2012.” There will also be a major investment in new logistics systems, including a new warehouse which will support us in maintaining stocks of products, primarily to serve automotive clients. Omco Metals will grow organically and focus on delivering the best in what it does, thereby nurturing the relationships with existing customers and acquiring new ones, across many different European markets. n