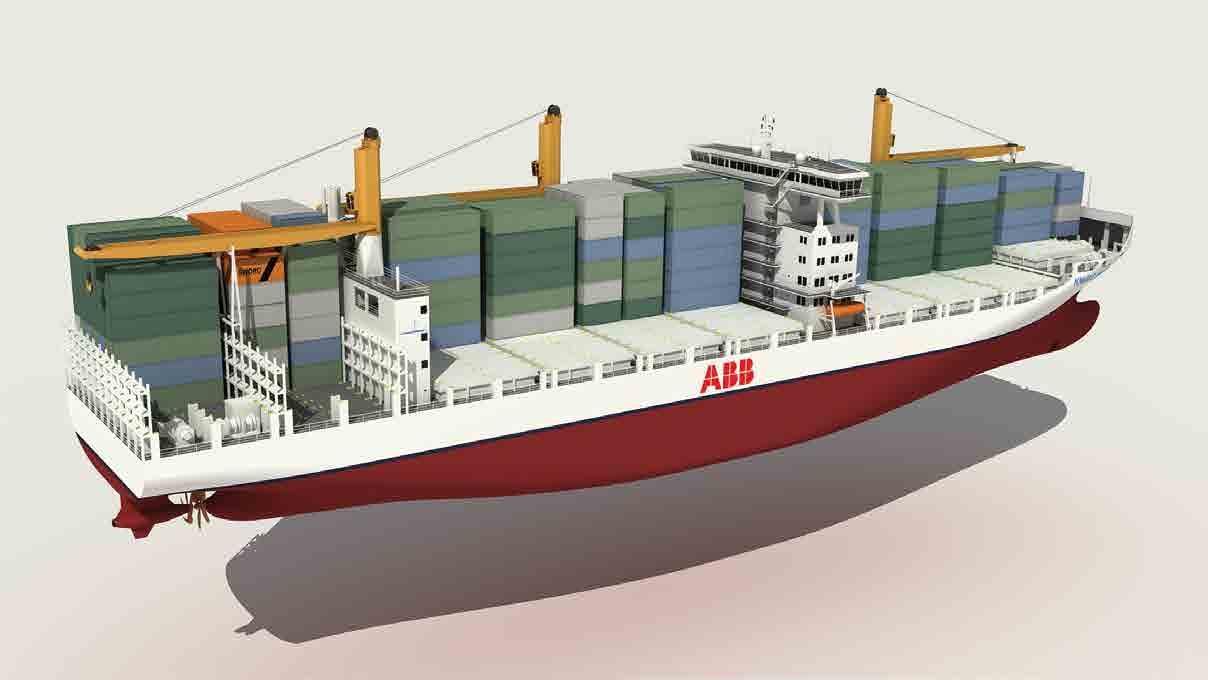
7 minute read
Saving energy and costs ABB Marine
SAVING ENERGY AND COSTS
The world’s shipping industry is under tremendous pressure – environmentally and economically. And it’s those factors that top the agenda when ABB’s Marine & Cranes business unit develops its products.
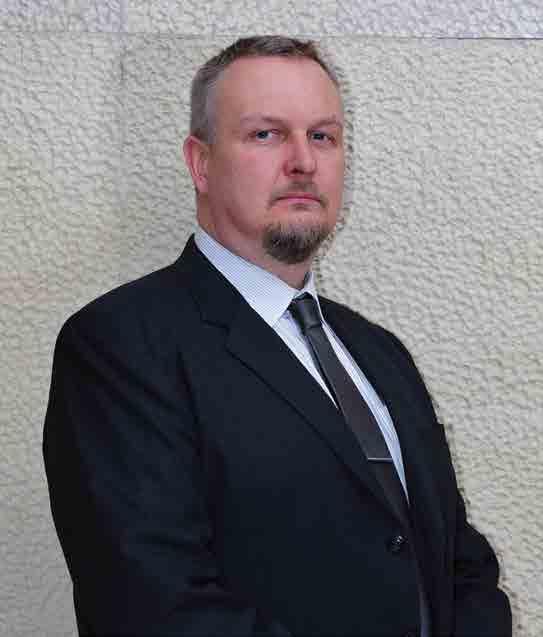
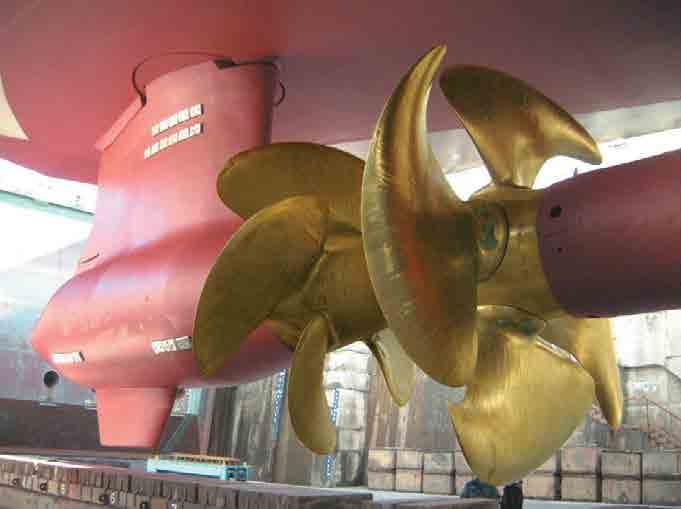
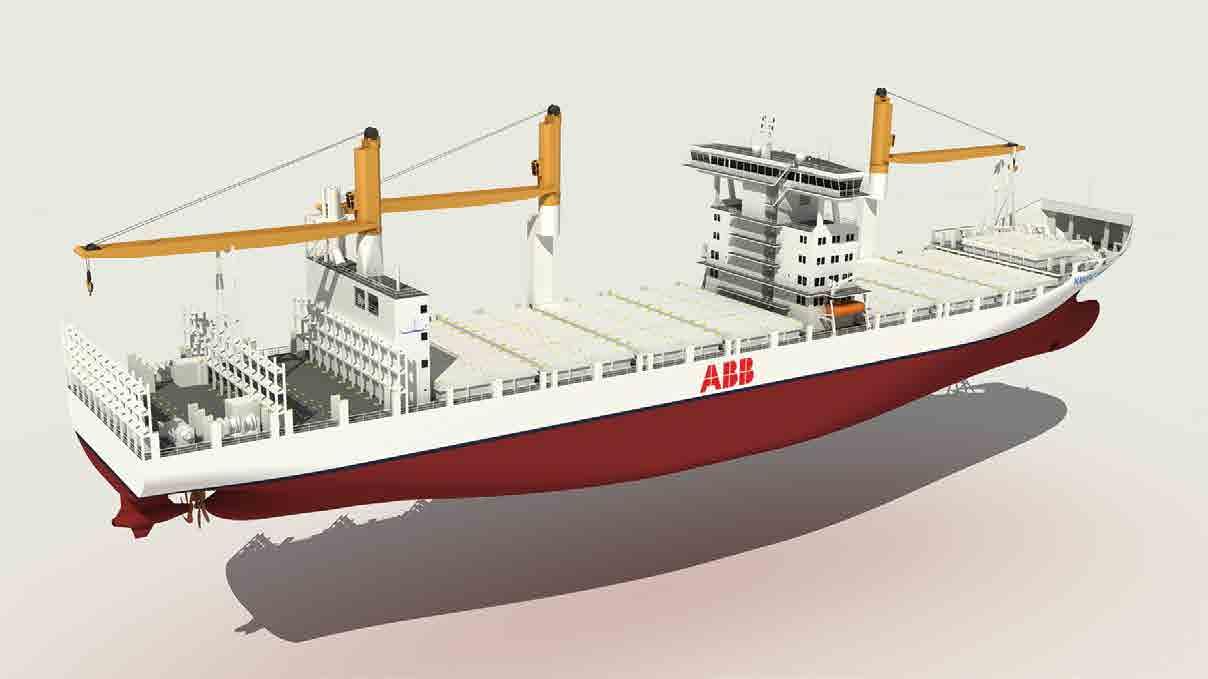
Some tough regulations are already in place – and tighter regulations are on the way for the global shipping sector, which must not only battle to remain profitable in the current economic climate, but must also reduce fuel consumption and emissions dramatically to meet environmental targets.
“By 2020, we will have a much stricter landscape when it comes to emissions from the shipping industry – the regulations are coming,” says Eero Lehtovaara, senior vicepresident of ABB’s Marine & Cranes business unit. It’s not as if the shipping sector can just shut up shop tomorrow. More than 90 per cent of global trade is carried on the water and it’s generally accepted that without shipping, half the world would starve and the other half would freeze. Hence ABB Marine’s range of products, from its unique Azipod® vessel propulsion units to its electrical, vessel information and control systems, are much in demand for their ability to reduce fuel consumption, emissions and costs for ship operators.
“We focus on energy-efficient solutions which meet the requirements of modern society; we are moving more and more into technologies that pollute less, or offer the option to use less polluting methods of propulsion or energy usage – including, for example, in big city ports,” says Mr Lehtovaara.
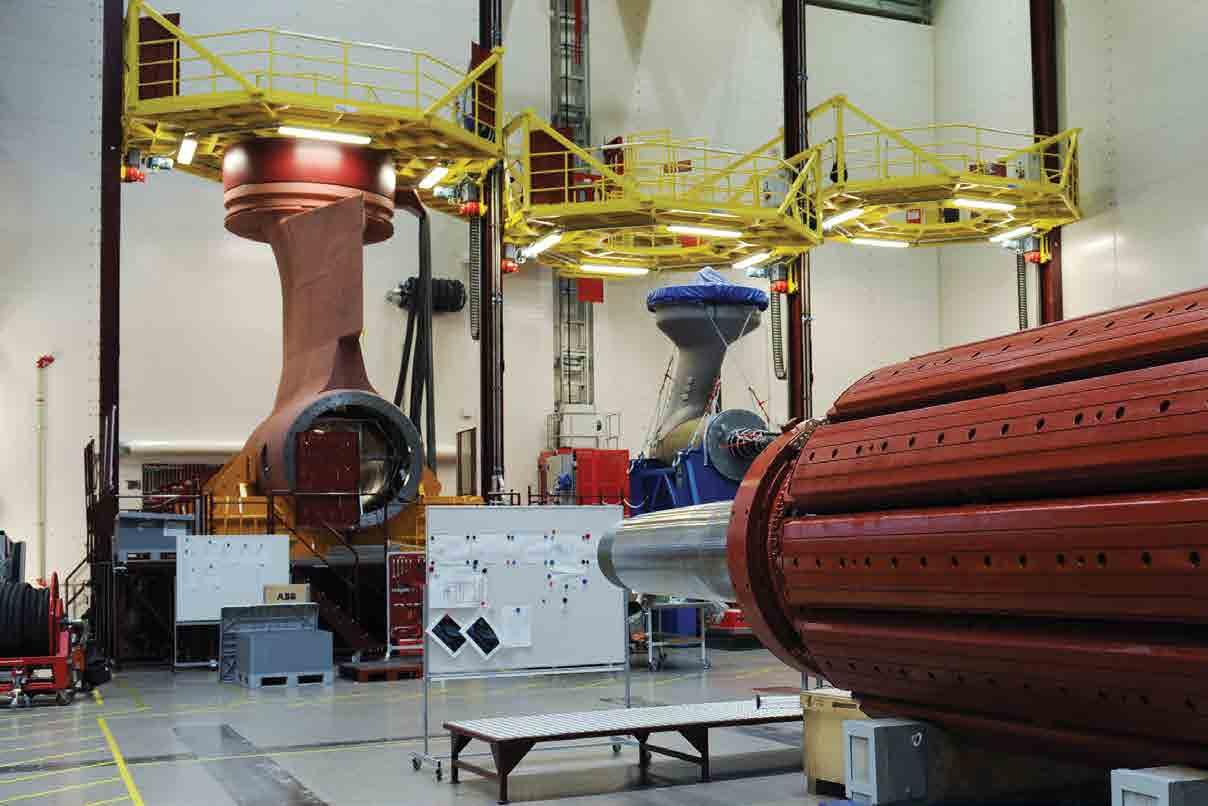
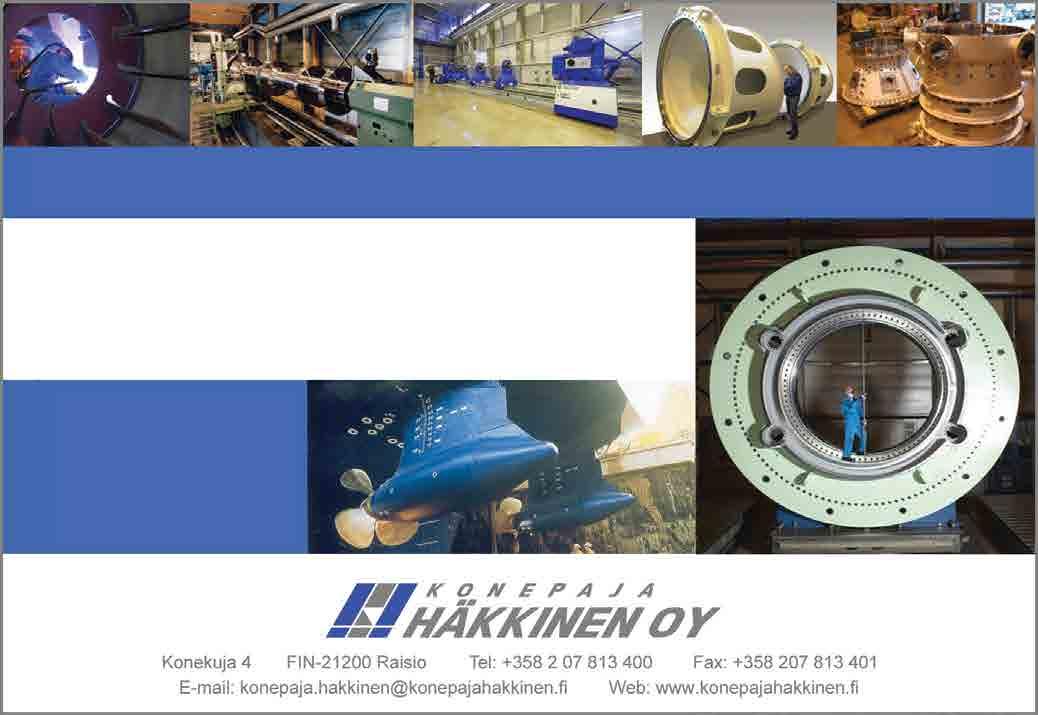
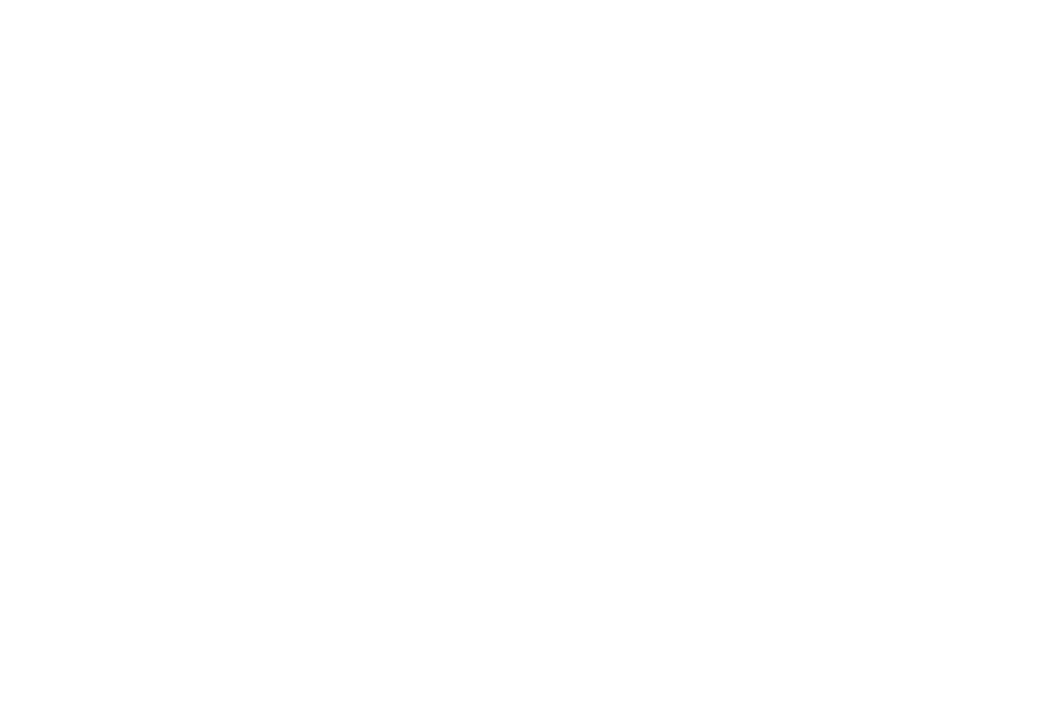
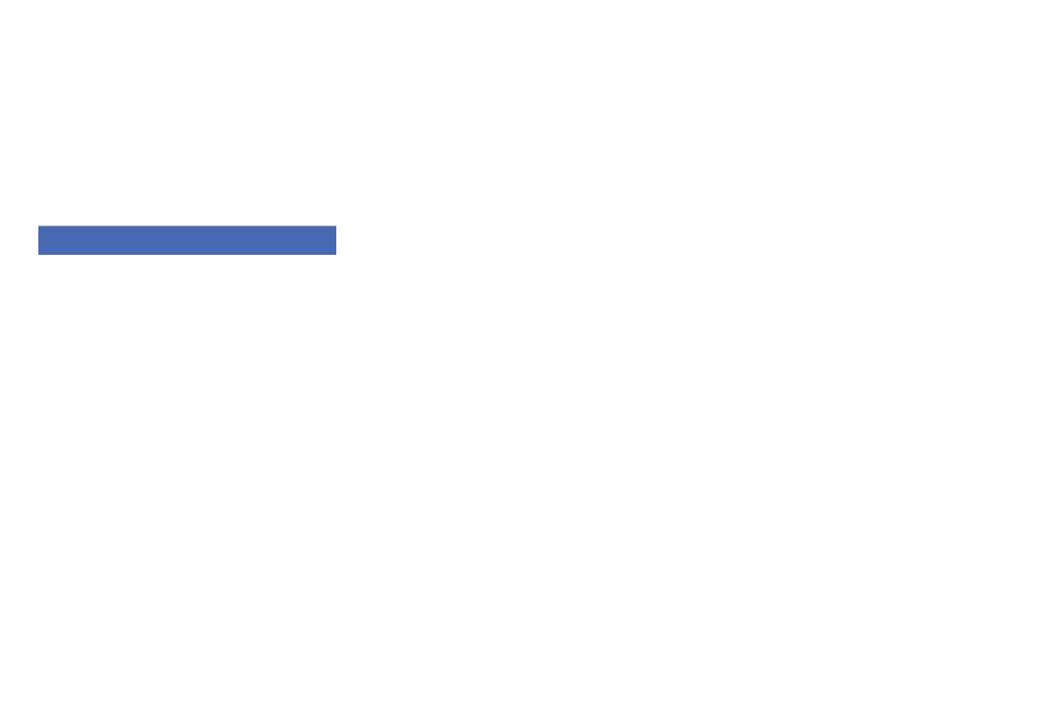


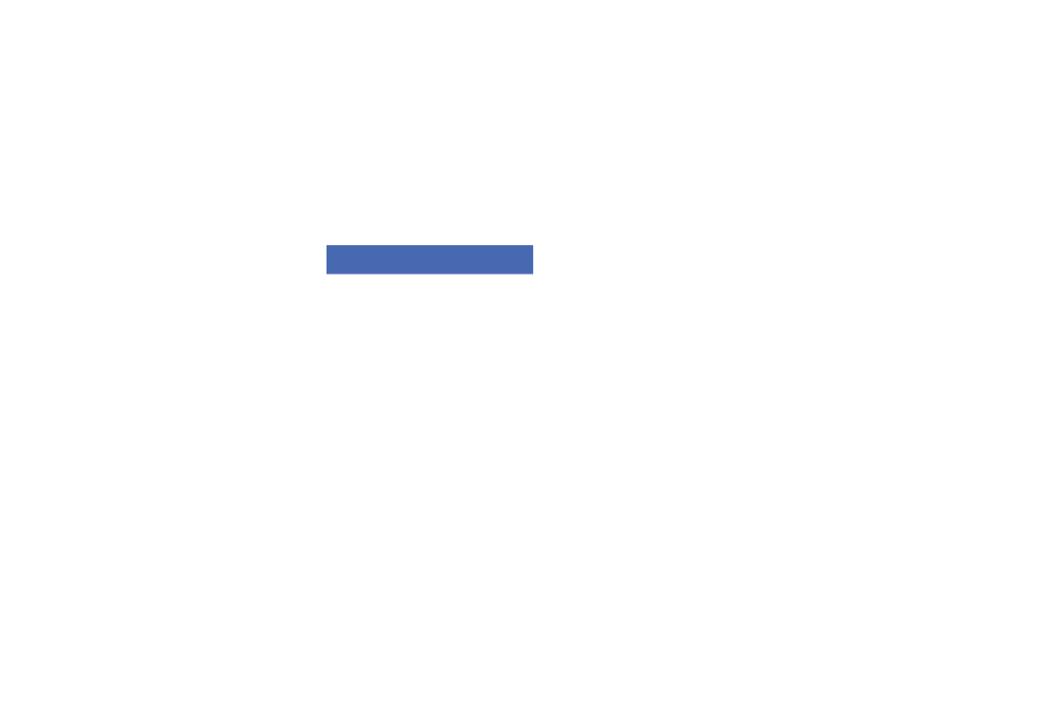

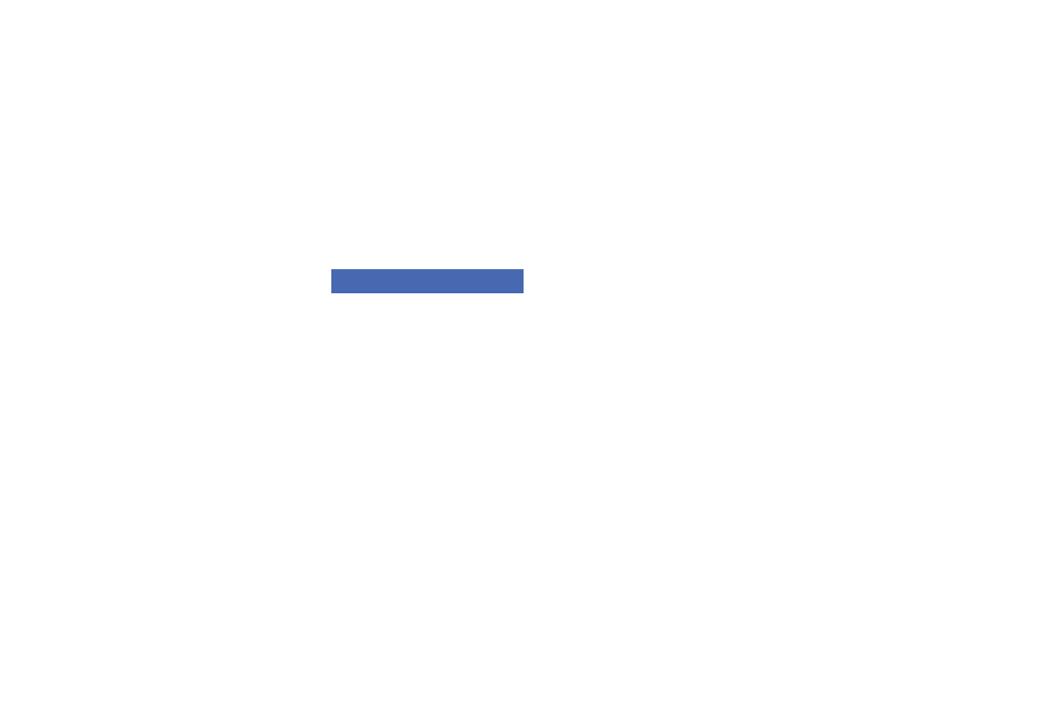

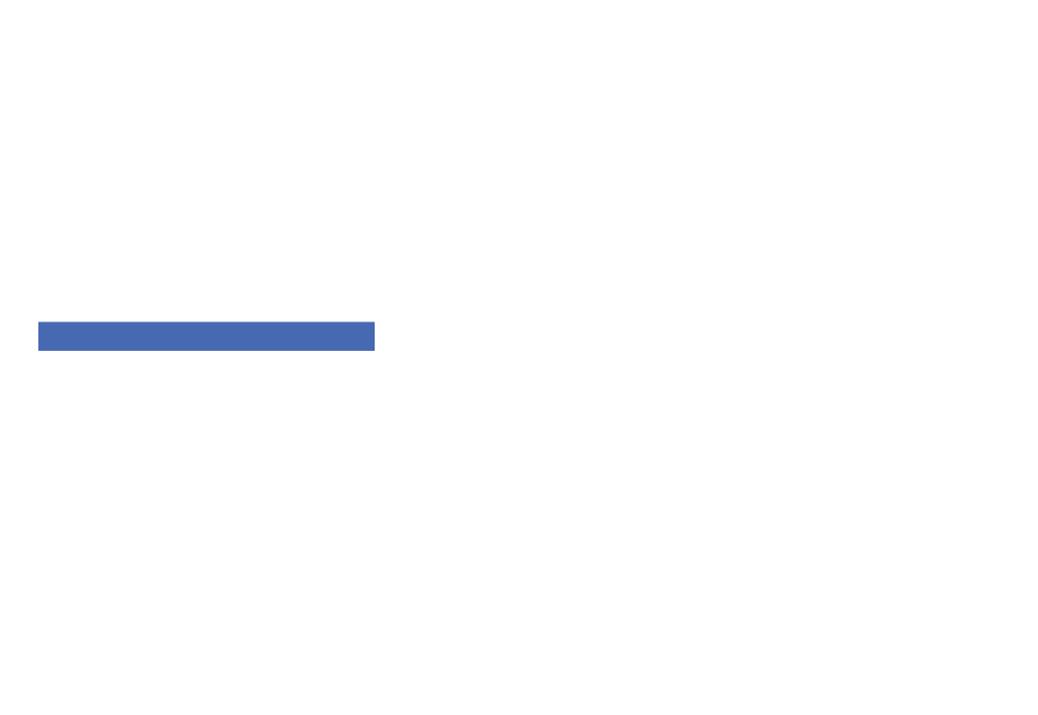
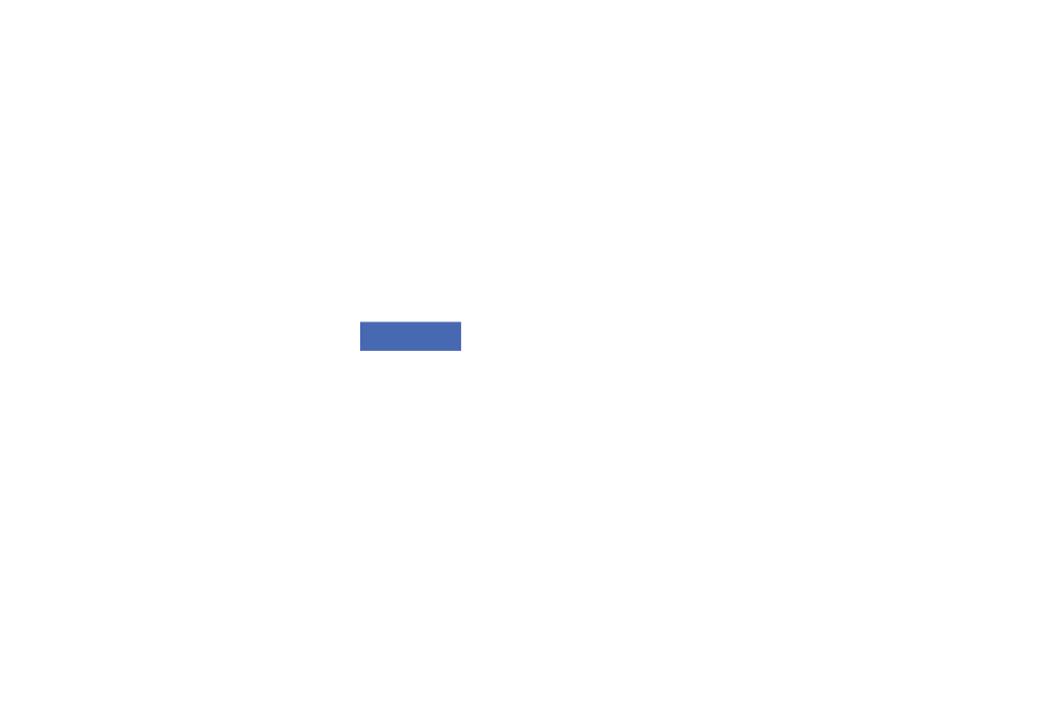
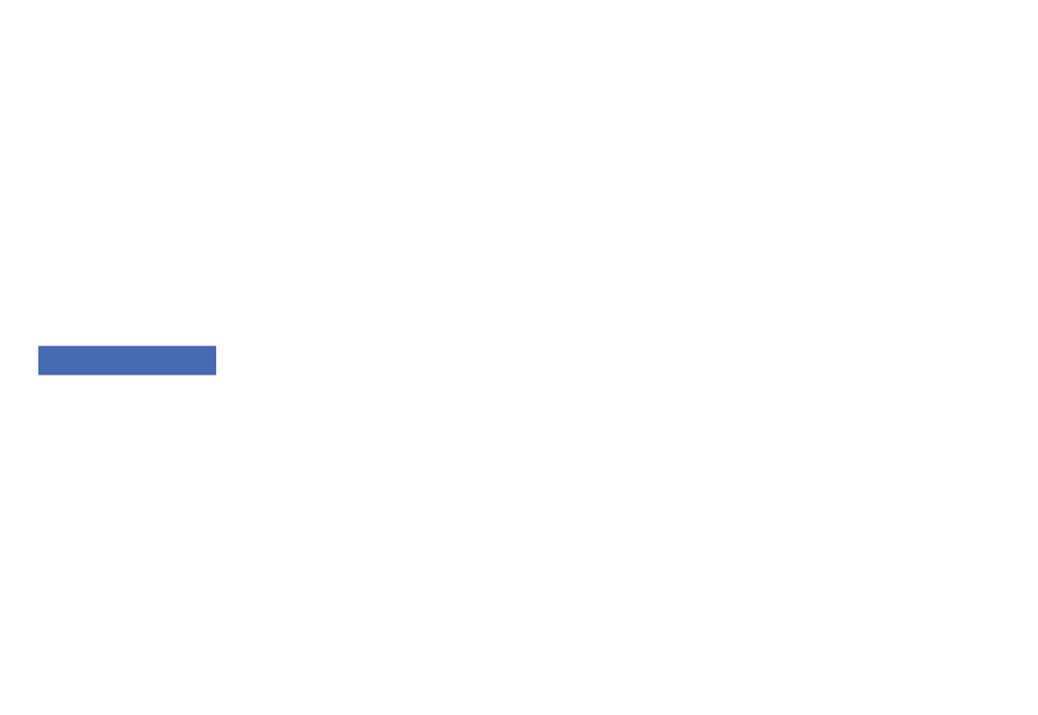


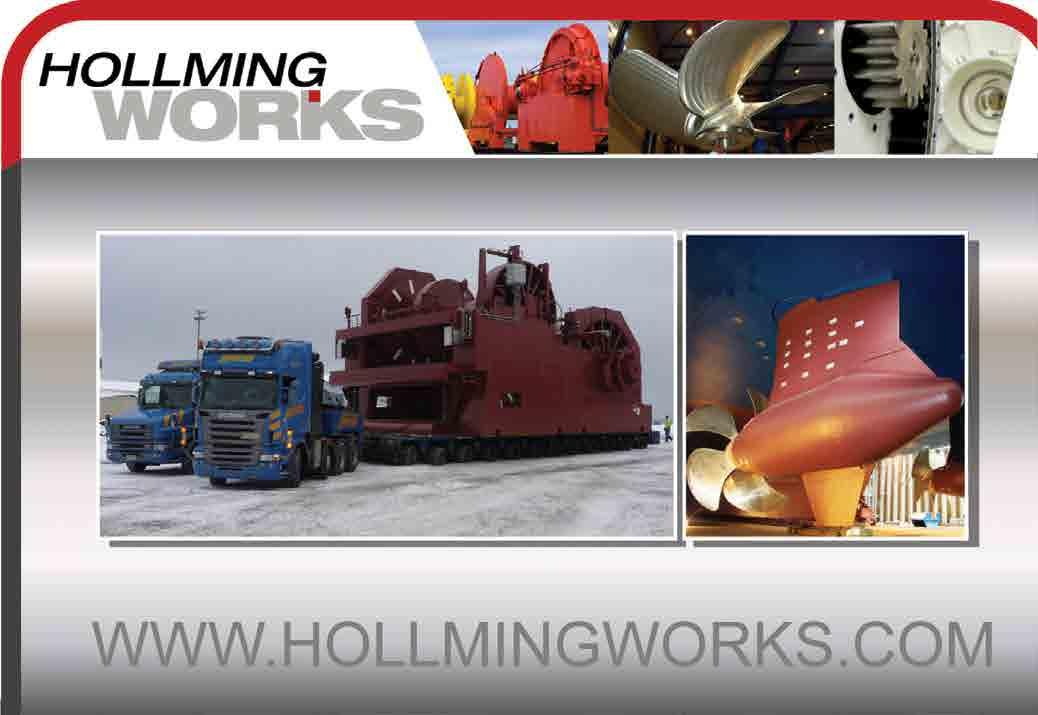
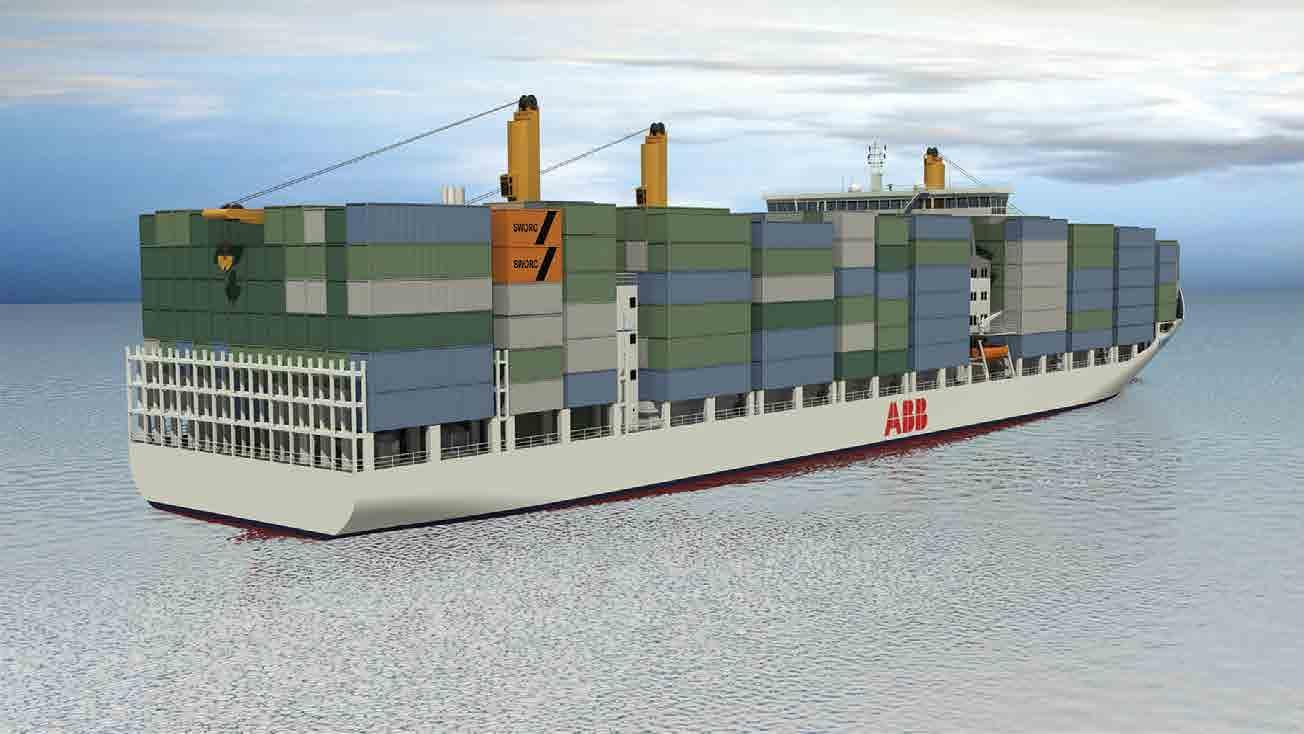
The Marine & Cranes business unit is a systems integrator within ABB’s process automation division, making heavy use of components and systems provided by different product units within the ABB Group. The business unit is involved in five main elements: propulsion units; electrical systems (its biggest revenue generator); vessel information and control systems (including automation), where there is a particularly strong emphasis on increasing the product range; cranes and terminals, where many customers are the same as in other segments; and, finally, services ‘a very important area’, says Mr Lehtovaara.
Azipod
The Azipod family takes many of the headlines – it is the key product being promoted, and the range is continuously being improved, he says. The Azipod is now designed, manufactured and classified to give five-year main service intervals, to tie in with drydocking intervals. “We are working on extending the range and scope of delivery of the Azipod system, with new products and improved features. These new features can be used even to improve the energy efficiency of existing ships with Azipod propulsion.”
Modifications to the Azipod in 2011 included a newly optimised fin shape and a new pod cap structure called X-tail; the altered fin shape receives water flow from the propeller at a less acute angle and its curved design redirects the flow more efficiently, while the X-tail strengthens water flow on ejection from the Azipod propulsor, minimising water swirling. These modifications have improved hydrodynamic efficiency by more than two per cent.
Also last year, ABB worked with the Danish naval design and marine consultancy Knud E. Hansen to develop a highly fuel-efficient 2000 teu (twenty-foot equivalent unit) container feeder vessel. Compared to a containership with a conventional diesel-direct propulsion system, the main engine has been considerably downsized, and a range of other design features offer improved efficiency in terms of speed and fuel consumption.
This is ABB’s first move into container shipping with the Azipod solution – to date the 250 Azipod units delivered have been largely into the offshore oil & gas and passenger ships segments.
“We intend to go into new segments of merchant shipping, like containers, where until now we haven’t been strong,” says Mr Lehtovaara. “We are looking at how best to address that part of the market; we feel that we need to be everywhere where our customers are and find new, highly energy efficient products suitable for those segments.”
Based on upcoming and expected environmental regulations, a key aim is to produce a ‘zero emission’ port call vessel – where a hybrid propeller solution would enable the ship to use traditional heavy fuel oil for the main voyage, switch over to diesel for slow steaming, and connect to onshore renewable sources when in port – avoiding the use of either diesel or heavy fuel oil, with
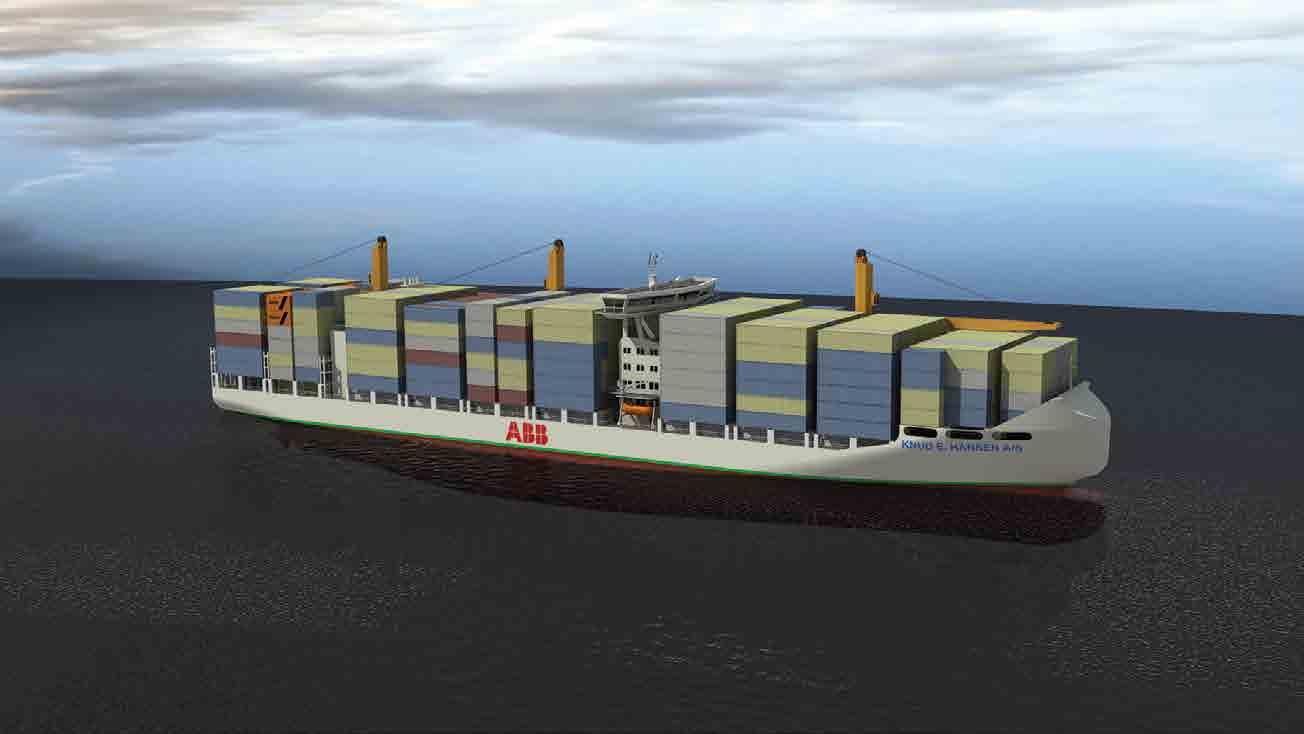
associated emissions, when moored in the centre of a city, for example.
Other recent developments have included the introduction of a new onboard DC grid system (direct current distribution for marine applications) – designed for ships with lowvoltage onboard power systems, such as offshore support vessels, tugs, ferries and yachts, it can reduce fuel consumption and emissions by up to 20 per cent.
Global expansion
The Marine and Cranes business unit employs about 1100 people across 20 countries. There are main system engineering centres in Oslo, Helsinki, Shanghai and Singapore; Azipod production/assembly takes place in Helsinki and, since mid 2011, Shanghai.
The new 37,000m2 manufacturing based in Shanghai was officially opened in August 2011 and is concentrating on production of the Azipod C, which is the compact pod range. “The factory is working well; we are very pleased with the quality and efficiency we have achieved there,” says Mr Lehtovaara. “The new facility is meeting all targets in terms of scheduling and quality.”
Two years ago, ABB announced that it was looking to strengthen its marine business presence in Brazil, in order to serve the growing market in Latin America; a key part of this will include the establishment of an Azipod C factory, marine service centre and specialised Azipod service centre, to help ABB serve Brazil’s fast-growing shipbuilding and offshore industry and also meet the statutory requirement for local content as set down by the Brazilian government.
“A production plant in Brazil is still in our plans – but the plans have not moved forward to the timetable we hoped,” says Mr Lehtovaara. “Discussions continue, with the Brazilian authorities and others and we are hoping for a positive development very soon.”
Despite the general doom and gloom of the shipping industry and wider economy, 2011 was a very good year for ABB Marine & Cranes, and 2012 is looking positive with good revenue and bookings. A key advantage for ABB is that its products offer a lower through-life cost, compared with products from other market players that are cheaper to buy at the start, but have higher lifecycle costs.
Although it is generally the shipyards that place the orders and pay the invoices, ABB is finding itself increasingly in direct contact with the end user of its products – “in a lot of cases when we are being chosen for the project, the reason is the owner’s preference”, says Mr Lehtovaara.
“In the long run, we offer energy-efficient and high-quality services and products that are cost-efficient. We support our customers with products that are reducing emissions, reducing fuel consumption, increasing energy efficiency and lasting longer, with lower lifetime costs. We are one of the few companies in the world that covers all the areas that involve shipping. And we know that one plus one can definitely be more than two.” n