
7 minute read
Solid foundations HeidelbergCement
SOLID FOUNDATIONS
HeidelbergCement is the world market leader in aggregates, and a prominent player in the fields of cement, concrete and other downstream activities – making it one of the world’s largest manufacturers of building materials. A series of capacity expansions and investments have increased its output still further.
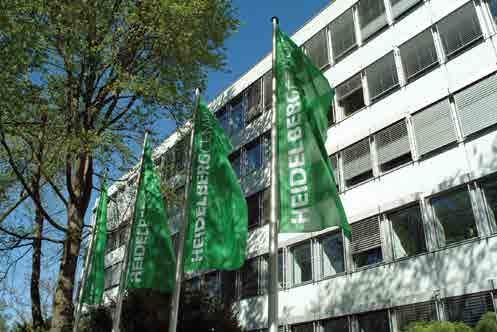
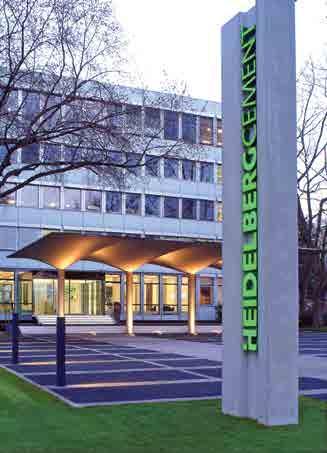

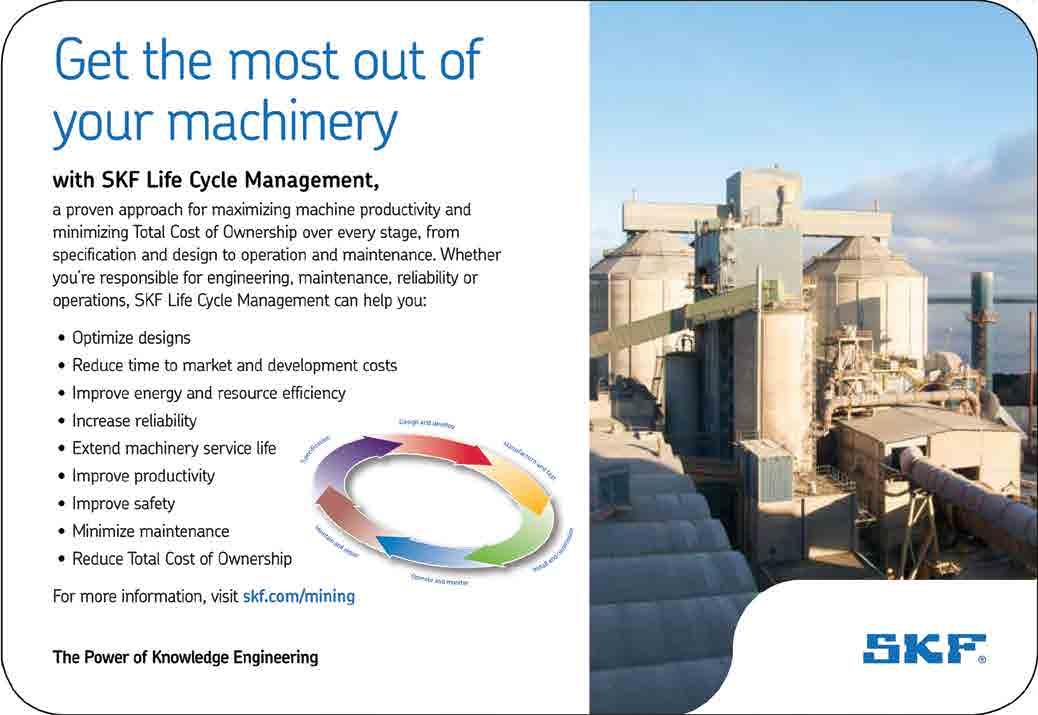

Headquartered in Heidelberg, Germany, HeidelbergCement has operations in more than 40 countries around the world. It operates in two core lines of business: cement and aggregates (sand, gravel and crushed rock), in both of which it is acknowledged as one of the global leaders. Even throughout the global financial crisis of the past few years, its turnover has continued to climb.
With an already impressive global presence, over the past few years the company has continued to expand its operations throughout Asia-Pacific and the AfricaMediterranean Basin, as well as maintaining its strong position in Europe and North America. In 2010 it restructured its operations to consolidate its global position. It is now divided into six group areas: Western and Northern Europe; Eastern EuropeCentral Asia; North America; Asia-AustraliaAfrica; Asia-Pacific; and Group Services.
Within the Eastern Europe-Central Asia division alone Heidelberg has 18 cement plants, three grinding plants, 28 cement terminals, 70 aggregates operations, 208 ready mix concrete operations and three concrete products plants across 11 countries. In Western and Northern Europe, meanwhile, it operates across 11 countries with 21 cement plants, six grinding plants, three ground granulated burning slag plants, 53 cement terminals, 176 aggregates plants, 39 asphalt plants, 596 ready mix concrete plants, 34 concrete products facilities and 22 brickmaking facilities. With these capabilities in Europe and Central Asia alone, it is easy to see why it remains a world leader. Strong in cement and aggregates
HeidelbergCement’s overall strategy was ‘reoriented’ a few years ago. In order to ensure its long-term position, it adjusted its strategy in order to focus equally on its core business of cement (previously its biggest focus) and its aggregates business. This change in strategy was strengthened by the acquisition of the Hanson, one of the world’s leading aggregates companies, in 2007. This company has extensive raw deposits in North America, the UK and Australia so it has allowed Heidelberg to strengthen its raw material base considerably.
Alongside aggregates, cement is one of the essential components of concrete. The company offers various kinds of cement using different additives for a range of applications. These include: white cements; high
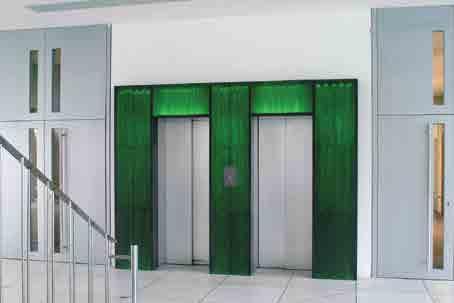
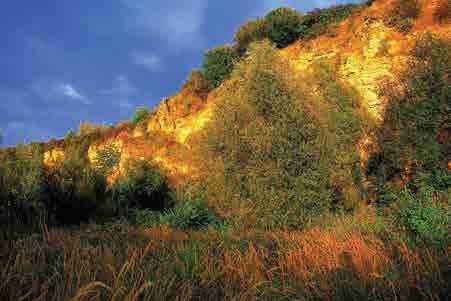
sulphate resisting Aquament and Portland cement for hydraulic engineering; anti-sulphate for sewage works construction; microcem, which is extremely fine cement for soil injection and masonry repair; and Depocrete and Procrete for waste dump sealing.
The varieties of aggregates cannot be controlled in the same way as cements. Their features as high quality raw material for ready mixed concrete and concrete products depend on the specifications of the quarries from which they are derived.
As the market leader in the Netherlands; Vliegasunie delivers mineral raw materials to the construction industry. By-products of the production of electricity in Power Stations, such as fl y ash, bottom ash and fl ue gas desulphurization gypsum.
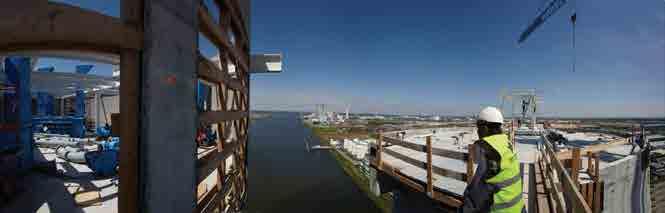
Providing an essential contribution to a sustainable building chain and the reduction of the depletion of surface minerals. We focus on reliability, quality and challenging logistic concepts.
Our new silo station for the storage and distribution of fl y ash in the Moerdijk Harbour in the South of the Netherlands and the new Power Plants under construction assure a reliable and sustainable position; now and in the future.
MORE INFORMATION?
Vliegasunie BV. The Netherlands. Belle van Zuylenlaan 3, 4105 JX Culemborg | Postbox 265, 4100 AG Culemborg Tel: +313 45 50 99 88 | Fax: +313 45 50 99 80 | E-mail: info@vliegasunie.nl

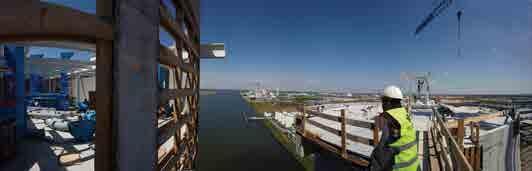
SKF
At SKF our vision is to equip Heidelberg with our knowledge, which in turn ensures that plants become more efficient, effective, competitive, and profitable. Working as collaborative partners, SKF & Heidelberg have developed an indepth relationship over many years to share ideas and experiences globally. This mutually beneficial relationship provides information on asset management, maintenance and reliability best practices, e-learning training modules and interactive maintenance tools. Through this relationship, the expertise is quickly and conveniently shared between employees, creating new possibilities to solve and troubleshoot plant problems, share best practices, and maximize operational effectiveness and lower overall costs. SKF is committed to helping Heidelberg optimize plant effectiveness and move from “Maintenance & Repair” environment to a “Maintenance & Improvement” environment through Life Cycle Management.
ATD
More then fifty years
is a long time to be on the job; but that is how long the ATD-Pressure Gas System is specialized in the removal of build-up and cross-sectional obstructions in a wide range of industrial applications. Experience like this teaches you important things. That is how ATD have been able to continually develop new products, new procedures and safety features to make the ATD-System the safest, most reliable and most effective system of its kind world-wide.
24 hours a day,
seven days a week our clients have to keep their material moving. But: at every stage of their operation, build-up and chokes can shut them down. Changing raw material conditions and the rising amount of secondary fuel components are leading to more unwanted deposits and build-up. Productions losses and downtimes can be the expensive consequences.
The ATD-Pressure Gas System
is especially engineered to reach the requirements for its use during the production with none or minimum shut-down time and feeding reduction; it offers the online-removing of build-up under heat.
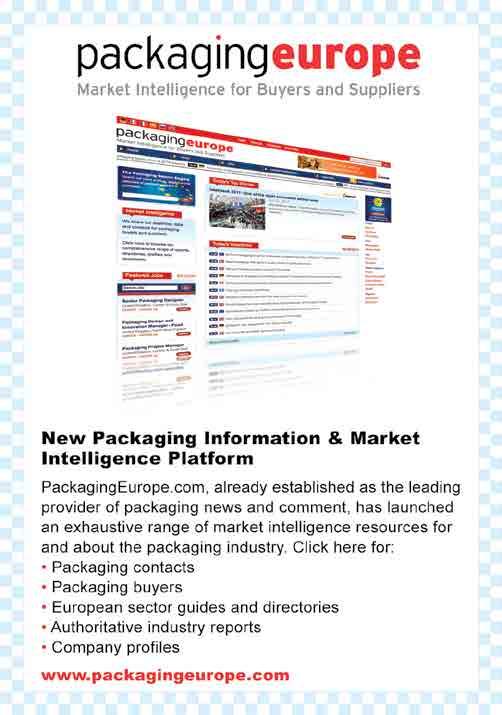

In addition to their function as an essential component of concrete, aggregates are also used for structural fill, road base, railway ballast and others.
In addition to these two main areas, Heidelberg offers concrete products such as building blocks, pavers, prefabricated ceilings and walls, and building materials such as limestone aggregates, sand-lime bricks and products and services for waste stabilisation or landfill construction.
Continued investment
Heidelberg continuously invests in new plant to improve its capabilities and maintain its position as a global leader. In July 2011 it opened a modernised kiln in its Polish cement plant Górazdze. This involved the expansion of the clinker capacity to 6000 tonnes per day. This has confirmed Górazdze’s position as HeidelbergCement’s most advanced cement plant in Europe.
Later that month, Heidelberg opened a brand new cement plant TulaCement, in Great Moscow. Located around 150km south of Moscow in the city of Novogurovsky, the plant has a production capacity of two million tonnes of cement. Investment in this facility, which employs around 400 people, amounted to around €300 million. The entire production site is spread over 100 hectares and is equipped with the latest most environmentally friendly technologies. Heidelberg has also constructed several kilometres of road and railway lines to ensure that logistics run smoothly.
Promoting biodiversity
Like the majority of globally operating companies today, HeidelbergCement recognises the part it must play in reducing the environmental impact, both of its activities and of other companies along the supply chain. As an example of one of its sustainable initiatives, in September 2011 Heidelberg and Birdlife International became cooperation partners in order to jointly preserve biological diversity at quarrying sites. In fact, the group was the first company in the international building materials industry to issue a binding guideline on biodiversity management.
But what will this particular initiative involve? At the signing of the agreement Dr Bernard Scheifele, chairman of the managing board at HeidelbergCement, said: “Together, we will analyse and optimise our existing work and define new activities in order to promote the preservation of biodiversity at our quarrying sites more effectively.
“We will give Birdlife insight into the workings of our quarries and sand and gravel pits throughout the group and implement biodiversity management projects at these sites together. These projects should make our impact on flora and fauna transparent, assess the effects and deliver improved approaches that will allow us to give back to nature more than we have taken.”
The cooperation will initially last three years. In the first year the two organisations will jointly develop a biodiversity strategy for the partnerships. The strategy will also include goals for the protection of species and habitats. In the second year, joint biodiversity projects will be formulated in different countries. From the third year, the first pilot projects in Europe will be implemented and documented. This project will hopefully pave the way for a more transparent and streamlined approach to biodiversity across the European building materials industry. n