
5 minute read
Continuously optimising its customer’s processes Alfa Laval
CONTINUOUSLY OPTIMISING ITS CUSTOMER’S PROCESSES
Alfa Laval is a global leader in separation, heat transfer and fluid handling technologies. Philip Yorke talked to Richard Kelly, the company’s UK managing director, about its new comprehensive operations centre in Aberdeen and two recent strategic acquisitions, strengthening Alfa Laval’s position in the Environment and Marine markets.
Alfa Laval is a Swedish engineering company that has remained a pioneer in its field since it produced and patented its first product, the ‘de Laval Cream Separator’ back in 1877. This laid the foundations for the company to become the global player it is today.
These days, Alfa Laval applies innovative thinking and engineering know-how to all types of process-led activities relating to their core technologies of separation, heat transfer and fluid handling. These provide the wherewithal to heat, cool, separate, pump and control the flow of liquids and semiliquids throughout the process cycle.
Alfa Laval’s worldwide organisation continues to provide high quality products and services to its customers in more than 100 countries worldwide in order to help create better everyday conditions for people. The company operates 37 major production facilities internationally with 20 in Europe, 12 in Asia, four in the USA and one in Latin America and employs just under 15,000 people worldwide. This is further complemented by the company’s extensive network of technical support through its locally based service engineers.
Delivering innovative new products
Alfa Laval’s products are particularly topical in today’s world, where increasing focus is being placed on identifying ways to save energy and protect the environment. This


involves treating water, reducing carbon emissions and minimising water and energy consumption as well as heating, cooling, separating and transporting fluids – all areas that impact us all in various ways.
Alfa Laval products are used extensively in the food, chemicals, pharmaceuticals, starches, sugars and ethanol industries. In addition, they are also employed in nuclear power, shipping, engineering, mining and the refinery industries, as well as for treating waste-water and creating comfortable climates within homes and offices.
Innovation remains at the heart of Alfa Laval’s business culture and it’s for that reason that Thompson Reuters named the company as one of the world’s top 100 innovators in 2011. To that end, Alfa Laval continues to make major investments every year in R&D, all designed to strengthen and develop the company’s global market leadership position. Currently Alfa Laval holds more than 300 patents and invests more than 2.3 per cent of its sales in research and development annually, resulting in the launch of between 35 and 40 new products every year.
Richard Kelly said, “We are a true example of a global company with a local presence and knowledge. The UK and Ireland operation is a prime example of how we are dedicated to providing quality, ‘lifetime’ service and support for our customers. We have two comprehensive workshop/service centres in the UK with the most recent one being opened in Aberdeen in June this year. By increasing our service centre capability with this new, purpose-built facility, we can provide a more dedicated service to our customers in the local markets. Furthermore, it will reduce the
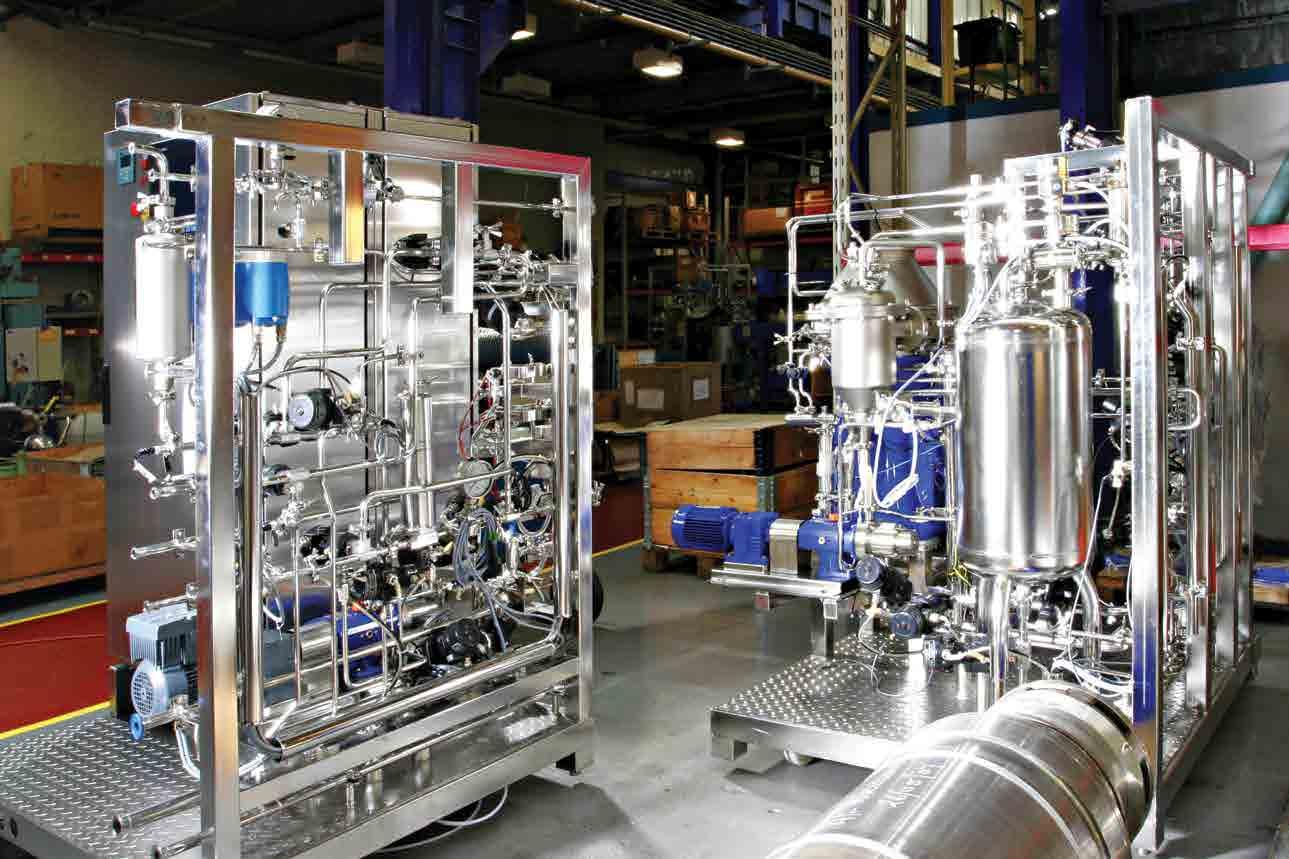
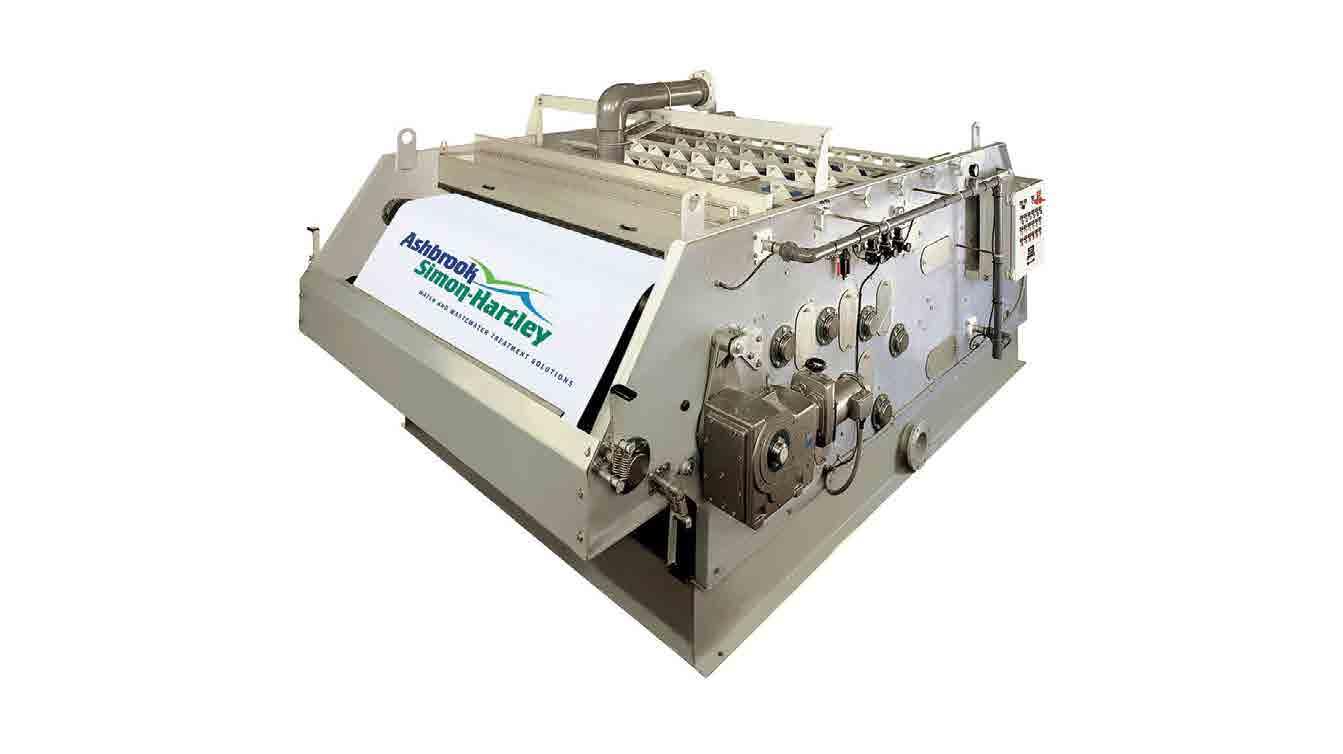
transportation distances and in turn minimise the time and cost required for equipment that is currently coming to our facility in Camberley Surrey. In addition, this will improve turnaround times and provide local support for industries such as those involved in the oil and gas, distillery, brewery and marine markets that operate in the Aberdeen area.”
Mr Kelly added, “We will mainly be servicing companies involved in the mud-cooling and drilling operations in and around the North Sea area. These products are required to consistently perform under very high pressures and who rely on our advanced heat exchanger systems to maintain operational working temperatures.”
In a separate strategic move the company has made two acquisitions over the last 18 months. Aalborg Industries, a Danish company that is a leading manufacturer of marine equipment, and Ashbrook SimonHartley, an American company with UK roots specialising in water and waste water treatment solutions.
Aalborg is a very successful, global company which supplies the marine industry with all types of boilers and employs more than 2,000 people. This important addition to our group has resulted in the establishment of a new Alfa Laval division: Marine and Diesel Division. This newly acquired expertise fits in well with our growing ambitions in the marine and offshore oil and gas industries.”
Ashbrook Simon-Hartley is an international organisation headquartered in Texas employing 230 people globally, 90 of whom are
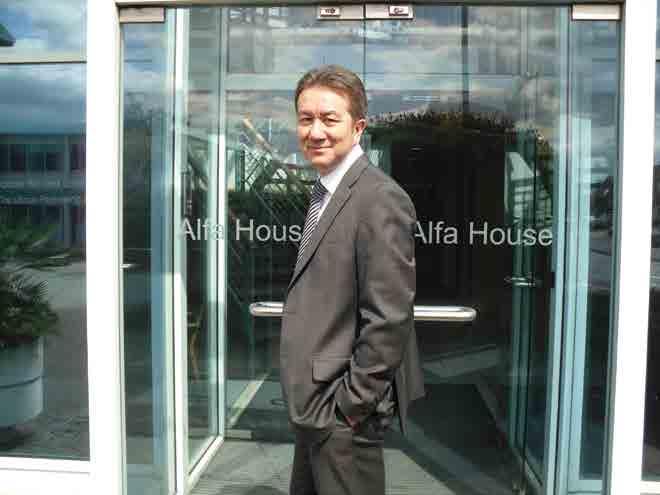

in the UK. The UK operation includes two manufacturing sites and a HQ office in and around Stoke. This acquisition enhances Alfa Laval’s existing technology within the water and waste water treatment division for Environmental applications, and it will see the UK becoming one of the Alfa Laval manufacturing sites for these solutions globally.
Optimising life-cycle performance
Alfa Laval has a well-earned reputation for unmatched reliability, optimal performance and sound operational economy, as well as for the ease of availability of its products and support services. Minimising equipment down time is a priority at Alfa Laval and the company’s timeliness when it comes to the fast delivery of spare parts and prompt on-site assistance from its specialised service engineers, sets it apart from its competitors. Today over 50,000 unique spare parts are readily available through the company’s strategically located distribution centres around the world. Furthermore, Alfa Laval has for many years helped its customers to optimise their manufacturing processes and extend life-cycle performance. This is based upon its unparalleled practical experience and industry know-how. The company is able to advise its customers on how to get the most from its installed equipment. In addition, upgraded equipment from the company not only introduces the latest technology and software to its customers’ processes, but can also increase production capacity and significantly reduce energy costs in the process. n
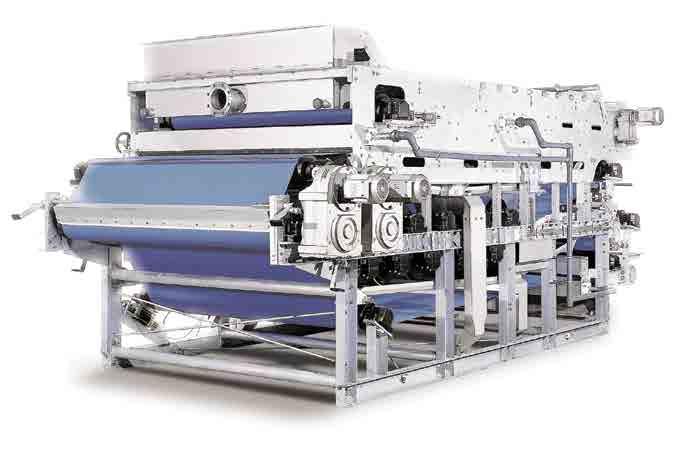
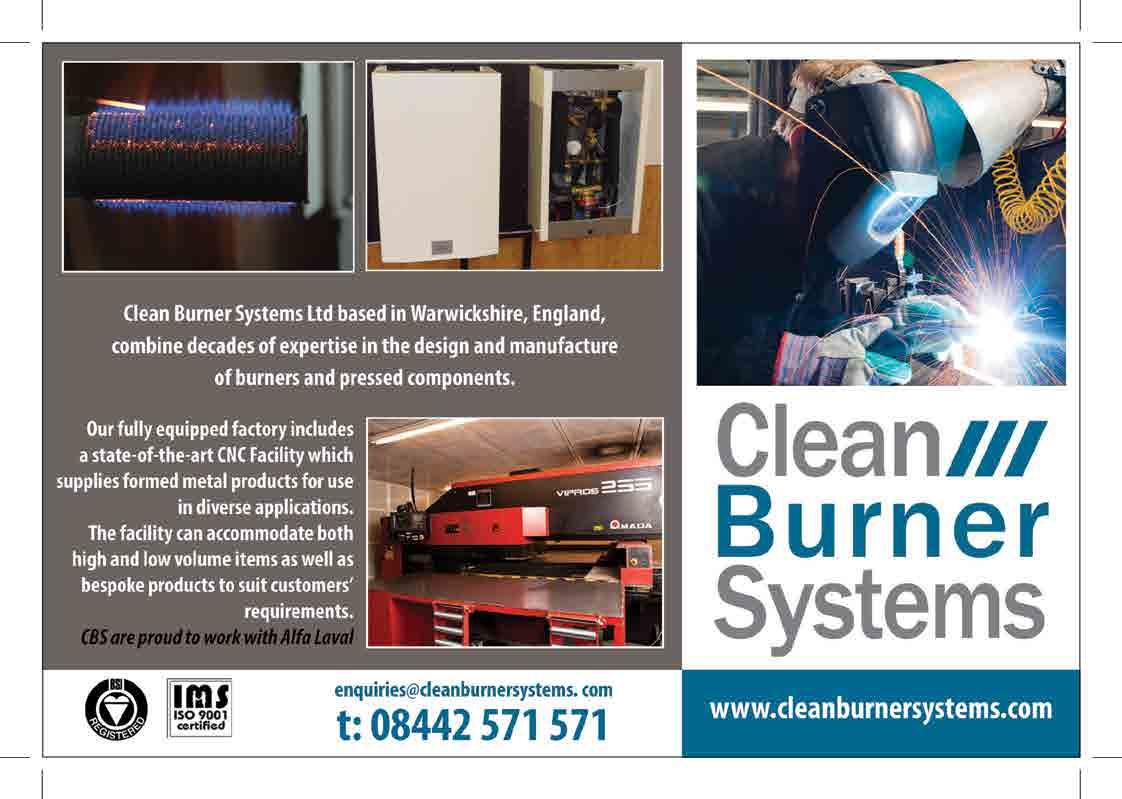