
6 minute read
Technological edge in strip cutting and finishing SALICO
TECHNOLOGICAL EDGE IN STRIP CUTTING AND FINISHING
SALICO, formerly SALMEC, of Spain, is renowned in the industry for being a reliable supplier for the engineering, manufacturing, delivery, start-up and service, throughout their entire lifetime, for slitting lines, cut-to-length lines, tension levelling lines, cleaning and packaging lines for metal strips. Piotr Sadowski reports.
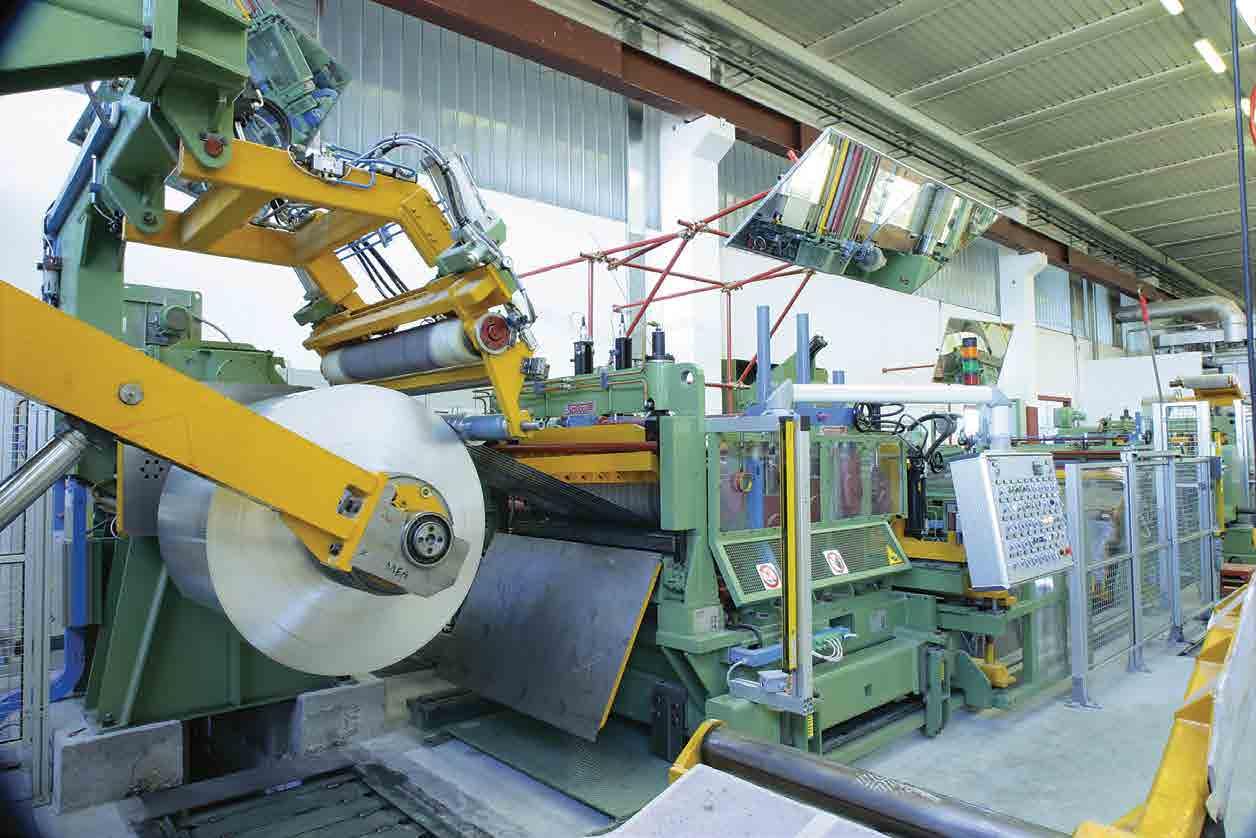
INDecember 2011, the Gerbolés family, majority shareholder in SALMEC, took a 25 per cent stake in the Italian Group SALICO. After this transfer of shares, the ownership of SALICO SpA in Italy became divided in four equal parts belonging to the Italian families Salvioni, Colombo and Molteni, and the Spanish family Gerbolés. José María Gerbolés, formerly chief executive of SALMEC, became the CEO of SALICO, while Carlo Salvioni remains as President of the Board of Directors. “We also furthermore decided to change our Spanish company’s corporate name from SALMEC to SALICO HISPANIA,” explains Mr Gerbolés. “It was a decision based on our agreement that it is much better to market just one, strong brand, SALICO.”
As a result of these important developments, the SALICO Group of companies is now composed of a number of entities. SALICO HISPANIA, S.A., in Madrid, is the mechanical engineering office, which is further strengthened by an automation company SALMEC AUTOMATION, set up three years ago. “At the beginning of June this year we launched a new engineering and production plant here, with 1000m2 of covered manufacturing space,” says Mr Gerbolés. SALICO SpA in Molteno, Italy, acts as the headquarters and also operates a mechanical engineering office and a construction plant. Another automation plant with an office, called SISTEL, a similar set-up to the one in Madrid, is located in Cremella, Italy. A further business entity is FUMAGALLI in Barzago, also in Italy, a mechanical construction plant for small items, including spare parts, which operates on just-in-time basis and is dedicated to service activities. In addition, a UK-based mechanical engineering company focuses on cleaning lines mainly for aluminium strips. All in all, over 180 highly qualified professionals offer top technology and service to SALICO customers throughout all areas of the operations.
Strong R&D activities and exports
For SALICO it is absolutely clear that in order to survive in the market and effectively compete with other players, R&D is crucial. “We have a dedicated R&D budget and a specifically allocated team which works on exploring new technologies and developing cutting-edge products,” explains Mr Gerbolés. “R&D specialists at SALICO work very closely with our customers so as to ensure that our solutions fully meet their needs.” This strong focus on delivering the best possible products has, over the decades of its operations, allowed SALICO to gain a much respected position on the market for slitting lines, cut-to-length lines, tension levelling lines, cleaning lines, blanking lines and packaging lines. With these products the company supplies customers who deal with aluminium, carbon steel and stainless steel, and in turn ultimately supply the automotive industry (including the largest names such as PSA, VW, Renault Nissan and Mercedes), the construction sector and the aluminium sector (particularly in the area of packaging).
While the company’s sales in Spain and Italy, its domestic markets, are only small, export activities are major. “We export 90 per cent of all of our products,” says the SALICO CEO. “They are distributed very widely, all across the world. We are very active in South America, particularly in Venezuela, Brazil and Argentina; in the Far East, in Indonesia and India; in Northern Africa, in Egypt; also in Europe where, amongst many other activities, we are currently involved in big aluminium plant projects in Romania and an automotive plant project in Germany. We
have three main new export targets as well: they include China, where we have been attending many trade fairs and engaging in exhibitions, Russia and the Anglo-Saxon market – the US, Canada and the UK.”
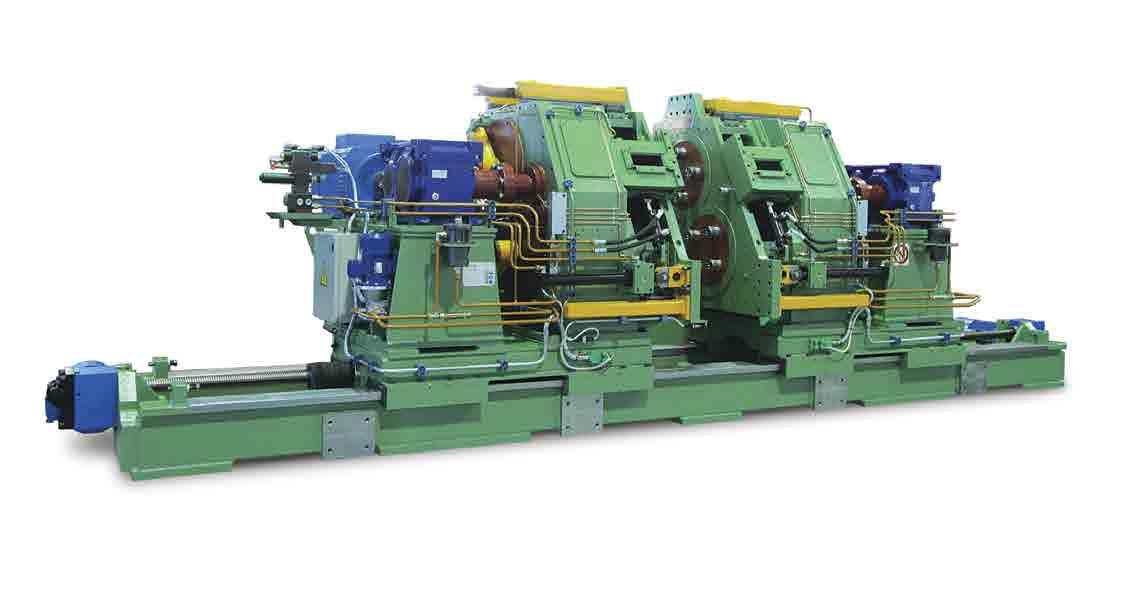
Products
One of the strategic objectives of SALICO is to supply its customers with technical solutions tailored to their needs, targets and resources, to ensure an optimum yield from their investment. The highest quality equipment manufactured by SALICO ensures low breakdown rates, ease of maintenance and, most of all, safe and ergonomic operation. Its offer of slitting, cut-to-length, tension levelling and cleaning and degreasing lines for metal strips (made from carbon steel, stainless steel, aluminium and other non-ferrous materials) is aimed at rolling mills and service centres. Slitting lines are processed within a thickness range from 0.1 to 20mm, width up to 2500mm and speed up to 800m/min. Cut-to-length lines on the other hand are processed within a thickness range from 0.1 to 25mm, width up to 2500mm and speed up to 120m/min. In the tension levelling lines offer, these are processed within a thickness range from 0.08 to 4mm, width up to 2500mm and speed up to 400m/min.
SALICO’s cleaning and degreasing lines, in turn, are processed within a thickness range from 0.15 to 6mm, width up to 2200mm and speed up to 300m/min. “There is a wide range of cleaning technologies available and their selection depends upon the characteristics of entry strip and requirements for output product, mainly in terms of productivity, oil and metallic fines content,” explains Mr Gerbolés. “Particularly for aluminium strips, there is a clear difference between strips produced in a hot mill or by means of continuous



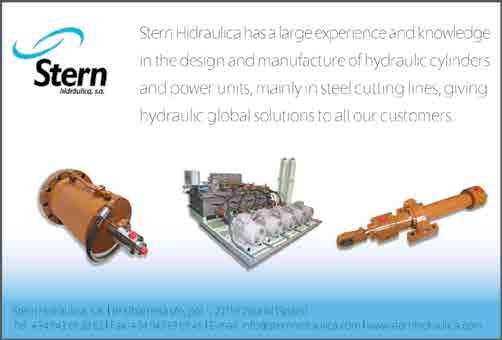
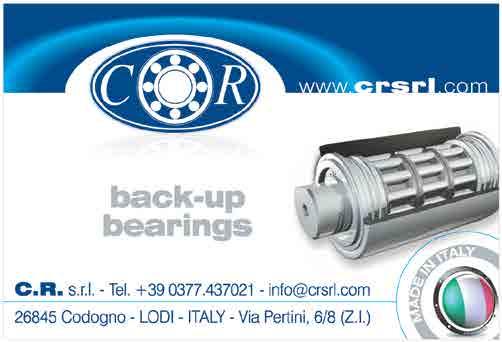
casting process and even among different alloys to be processed. Taking into account parameters such as entry dirt content, productivity and exit cleanliness requirements, to be defined by customers, our technicians will propose the solution that will best suit each situation.”
In the sector of blanking lines, these are mainly supplied to the automotive industryoriented service centres. Typically, strip thickness ranges from 0.4 to 4mm, maximum width being 2000mm and speed up to 100m/ min. SALICO also supplies packaging lines for complete coils, slit coils or packages of sheets either as final section within a new or existing slitting or cut-to-length line, or as independent stand-alone facilities.

Ensuring further growth
Most of the company’s future development will be coming from organic growth and a strategic expansion into the three new export destinations, China, Russia and the Anglo-Saxon market. SALICO expects to be fully operational there, in terms of supplies, in the next three to five years. “In July we aquired KCS HERR VOSS UK, who are based in the West Midlands in the UK” concludes Mr Gerbolés. “R&D will continue to be most crucial for us, so that we are able to develop new technologies that effectively compete with solutions coming from lowcost regions of the world. The only way to survive is to innovate.” n
